Gießöfen und Gießeinrichtungen – Stand der Technik und Entwicklungsziele
Teil 1: Gießöfen
Von Dietmar Trauzeddel, Simmerath-Lammersdorf
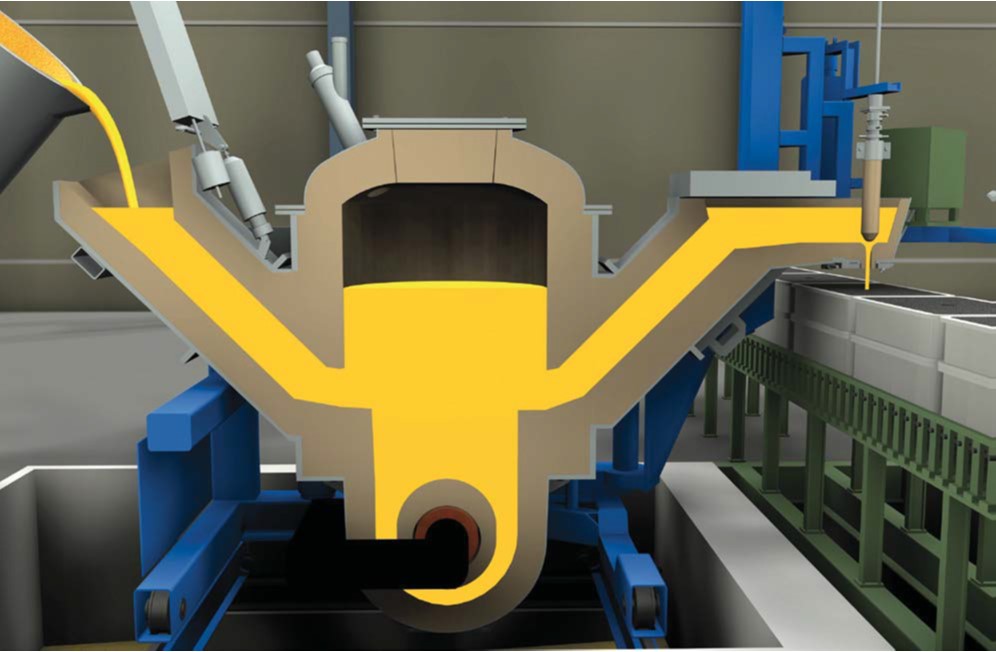
Erschienen in GIESSEREI 05/2015
Der nachstehende Beitrag befasst sich mit Gießöfen und Gießeinrichtungen für Gusseisen, die ein integrierter Bestandteil von Formlinien sind und damit im Wesentlichen ortsfest und nur begrenzt an der Formlinie verfahren werden können.
Die Notwendigkeit der Entwicklung und des Einsatzes automatisch arbeitender Gießöfen bzw. Gießeinrichtungen für den Formguss ergab sich aus folgenden Anforderungen: Zum einen ist beim manuellen Gießen mit der Gießpfanne der Gießvorgang von dem individuellen handwerklichen Können des jeweiligen Gießers und seiner Tagesform abhängig, daher ist eine Reproduzierbarkeit kaum gegeben und die erreichbare Gewichtsgenauigkeit ist nicht ausreichend, nach [1] liegt sie bei ca. 5 %. Zum anderen kommen die fertigungstechnischen Bedingungen hinzu, die sich aus der zunehmenden Automatisierung der Formherstellung ergeben. Bei Hochleistungsformanlagen, die bei der Großserienfertigung überwiegend zum Einsatz kommen, beträgt die Taktzeit teilweise nur 6–15 s. In diesem Zeitraum hat das Anfahren der Gießposition und das Füllen der Form zu erfolgen.
Dabei ist eine dem Schluckvermögen der Form entsprechende variable Gießleistung zu erreichen und eine hohe Reproduzierbarkeit und Genauigkeit der optimierten Gießkurve zu gewährleisten. Die jeweilige Position des Eingusstrichters der Form ist exakt innerhalb des kurzen Zeitfensters anzufahren.
Hinzu kommen die Forderungen nach der Einhaltung enger Toleranzen in Bezug auf Gießtemperatur und Analysengenauigkeit sowie die Erfordernisse einer zeitlich begrenzten Speicherung des flüssigen Metalls.
Mit der Entwicklung und dem Bau von induktiv beheizten Gießöfen mit Druckluftentleerung für Gusseisen in den 1960er-Jahren und der später zum Einsatz kommenden Dosierung mittels einer Stopfensteuerung wurden die oben genannten Anforderungen zufriedenstellend erfüllt und dieser Typ eines Gießofens hat auf Basis weiterer Verbesserungen und Optimierung seinen festen Platz in der Gießerei gefunden. Die Gießeinrichtungen – darunter werden alle Aggregate verstanden, die keine Beheizung aufweisen – lassen sich nach der Art des Gießvorganges in folgende Grundtypen einteilen:
- Gießen durch Kippen über den Ausguss,
- Gießen mittels Stopfenentleerung, drucklos und
- Gießen mittels Stopfenentleerung, druckbetätigt.
Die Gießeinrichtungen haben das Programm der Gießöfen ergänzt und werden bei bestimmten Anforderungen vielfach eingesetzt. An dieser Stelle soll noch darauf hingewiesen werden, dass bei den Gießeinrichtungen mit Stopfenentleerung, die drucklos arbeiten, ein sinkendes Badniveau im Ausgussbereich zu verzeichnen ist. Bei der Druckbeaufschlagung ist dies nicht der Fall und daher sind diese Gießeinrichtungen vom Grundprinzip dem Gießofen, bis auf die Beheizung, ähnlich. Wie später berichtet wird, gibt es auch Ausführungen dieses Typs, die eine spätere Nachrüstung mit einem Induktor zur Beheizung ermöglichen. Zu erwähnen ist noch, dass der Einsatz elektromagnetischer Kräfte für die Förderung und Dosierung des flüssigen Metalls in die Form– bis auf einige Ausnahmen im Bereich der ehemaligen Sowjetunion – keine industrielle Nutzung gefunden hat.
In Bezug auf die eingesetzten Verfahren zur Regelung und Kontrolle der Gießleistung des flüssigen Metalls unterscheiden sich Gießofen und Gießeinrichtung, bis auf den Gießvorgang, nicht grundsätzlich.
Die Regelung kann durch Nachfahren einer gespeicherten Gießkurve, nach dem Gewicht, der Zeit oder dem Niveau im Eingusstrichter erfolgen. Auch eine Kombination ist möglich, z. B. von gespeicherter Gießkurve und Zeit.
Vergleich Gießofen und Gießeinrichtung
Der Vergleich wurde für die beiden prinzipiell unterschiedlichen Anlagensysteme, die Gießeinrichtung mit Kippentleerung (Pfannenprinzip) und dem induktiv beheizten Gießofen vorgenommen. Die Tabelle 1 fasst den technischen Vergleich zusammen.
Tabelle 1: Technischer Vergleich Gießofen/Gießeinrichtung.
Gießofen | Gießeinrichtung | |
Fassungsvermögen | 2–50 t | 0,6–3,2 t |
Chargendauer | 30 min | 5–10 min |
Temperaturverlust | 0,5 °C/min | 5–10 °C/min |
Temperaturgenauigkeit | +/- 5 K | 25–50 K |
Gießleistung | 1–40** kg/s | 2–20 kg/s |
Legierungswechsel | 4–5 h | 1 min |
Gefäßwechsel | 12–16 h | 1 min |
Gleichzeitiges Befüllen und Abgießen | ja | nein |
Einsatz als Zwischenspeicher | begrenzt | nein |
Automatisches Dosieren und Abgießen | ja | ja |
Schlackefreies Abgießen | ja | ja |
Speicherung von Mg-behandeltem Gusseisen | ja | nein |
Einsatzkriterien Formanlagen: Abgussgewicht Taktzeiten große Breite | große Breite große Breite | klein bis mittel*** lang bis mittel*** |
* Gießeinrichtung: Pfannen-Kippsystem
** in Abhängigkeit vom gewählten Düsendurchmesser
*** bei Einsatz von zwei Gießeinrichtungen erweitert sich das Spektrum
Für die Gießeinrichtung spricht insbesondere die Möglichkeit eines schnellen Legierungs- und Gefäßwechsels und die einfachere feuerfeste Zustellung. Das Fassungsvermögen ist so ausgelegt, dass – bedingt durch Temperaturverlust – nach ca. 10 min ein Pfannenwechsel erfolgen muss. Da dieser Wechsel ca. 1 min dauert, kann in dieser Zeit nicht abgegossen werden, es sei denn man arbeitet mit zwei Gießeinrichtungen.
Eine derartige Gießeinrichtung ist vorrangig für den Einsatz an Formanlagen mit längeren Taktzeiten und mittleren oder niedrigeren Abgussgewicht geeignet.
Hinsichtlich der erreichbaren Dosiergenauigkeit gibt es keine belegbaren Zahlen oder Bewertungen, um einen derartigen Vergleich vornehmen zu können.
Die Vorteile eines Gießofens sind natürlich der geringere Temperaturverlust und die durch die Beheizung erreichbare konstante Temperatur, die Analysengenauigkeit, die längere Speicherung des flüssigen Metalls und der Umstand, dass das Befüllen mit frischem Metall ohne Unterbrechung des Gießprozesses erfolgen kann. Hierdurch ist es möglich, kontinuierlich abgießen zu können.
Wie bereits in einer früheren Veröffentlichung in dieser Zeitschrift berichtet wurde [2], ist hinsichtlich des Energieverbrauchs – bezogen auf einen Mehrschichtbetrieb – der Gießofen im Vorteil. Dabei wurden die Verbrauchswerte für die Kompensation der Temperaturverluste berücksichtigt.
Gießöfen für Gusseisen
Baugrößen
Das Konzept eines druckbetätigten Gießofens mit Stopfensteuerung wird als bekannt vorausgesetzt, sodass nachstehend nur auf einzelne Neuentwicklungen eingegangen wird.
Die Grunddaten realisierter Gießofenprojekte (Bild 1) zeigen das breite Spektrum in Bezug auf das Fassungsvermögen und die Leistungseinspeisung.
Betrachtet man den Warmhaltwert, so zeigt sich, dass im Vergleich zum Rinnenofen die Gießöfen im Durchschnitt mit einer höheren Überhitzungsleistung ausgeführt werden. Üblich ist die Guslegung so, dass eine Überhitzung von 90 – 110 K in einer Stunde möglich ist. Dies ist dadurch begründet, dass beim Einsatz eines Gießofens in manchen Einsatzfällen – wenn die Eingießtemperatur zu niedrig ist – in kurzer Zeit eine Überhitzung vorgenommen werden muss, um möglichst schnell nach dem Füllen mit frischem flüssigem Metall die gewünschte Gießtemperatur wieder erreichen zu können. Das geringe Speichervolumen – insbesondere wenn der Gießofen bis auf den Sumpf entleert ist – ist ür den benötigten Temperaturausgleich nicht ausreichend.
Aber es gibt auch Aufgabenstellungen, bei denen eine wesentlich höhere Überhitzungsleistungen erforderlich ist. So wurde eine 5-t- Gießofenanlage mit einer 1000 kW Schaltanlage ausgerüstet, um in ca. 4 min eine Temperaturerhöhung von 90 K zu erreichen. Damit ein schneller Temperaturausgleich zwischen dem Eisen im Eingusssiphon und im Ofenkessel erfolgt, wird der Ofendruck erniedrigt und anschließend wieder aufgebaut, vergleichbar mit einem Pumpvorgang.
Das man beim Gießen von magnesiumbehandeltem Gusseisen (zur Herstellung von Gusseisen mit Kugelgrafit) eine etwas höhere Überhitzungsleistung anstrebt, soll nicht unerwähnt bleiben. Die Induktorleistung ist ca. 50 kW höher auszulegen, um die Bildung von Ansätzen aus Magnesiumoxidschlacke zu vermeiden [3].
Die Grafik (Bild 1) zeigt außerdem, dass der spezifische Warmhaltewert naturgemäß mit steigender Ofengröße deutlich sinkt.
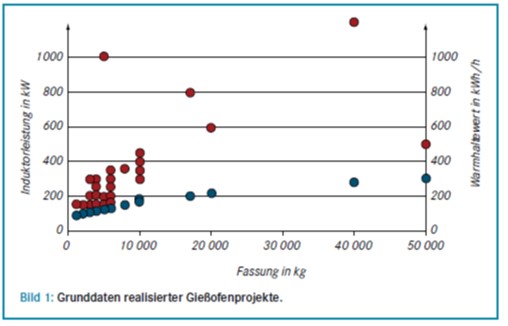
Beheizung
Wie bekannt, dient ein Rinneninduktor mit U-förmiger Rinne, der an der Seite oder am Boden angebracht ist, dem Warmhalten und Überhitzen des flüssigen Metalls. Dabei geht der Trend in Richtung der Anordnung des Induktors am Boden des Gefäßes, insbesondere beim Einsatz für Gusseisen mit Kugelgrafit.
Der Einsatz von kernlosen Induktoren in Tiegelform (Tiegelinduktor) versprach, mit Ausnahme des etwas höheren Energieverbrauches, verfahrenstechnische Vorteile, vor allem hinsichtlich der Reinigung. Allerdings hat sich diese Bauform nicht so wie erwartet durchgesetzt.
Die Abführung der Verlustwärme der Spule und die Kühlung des Induktors erfolgen i. d. R. durch eine Wasserkühlung des Aggregates. Da der Leistungsbereich der Induktoren von 150 kW bis 1200 kW reichen kann, muss die Konstruktion und insbesondere die innengeometrie auf den jeweiligen Leistungsbereich zugeschnitten sein. Dazu gehören auch Überlegungen, die Induktoren des unteren Leistungsbereiches so zu gestalten, dass mittels einer Luftkühlung die erforderliche Abführung der Wärme erfolgen kann. Insbesondere die Vergrößerung der wärmeabführenden Oberfläche des Induktors steht dabei im Mittelpunkt. Diese konstruktiven Änderungen werden zurzeit in einem Projekt eines 4-t-Gießofens mit einem luftgekühlten 250 kW Induktor umgesetzt. Daraus kann allerdings keine generelle Tendenz für die Induktoren des unteren Leistungsbereiches abgeleitet werden, es bleibt bei projektbezogenen Einzelentscheidungen und damit dem Abwägen der Vor- und Nachteile. Es erübrigt sich darauf hinzu weisen, dass luftgekühlte Induktoren für Gießofen keine Neuheit darstellen.
Die elektrische Leistungsversorgung der Gießöfen erfolgt hauptsächlich durch robuste Netzfrequenzschaltanlagen. In Einzelfällen werden aktuell auch Umrichteranlagen auf Basis der IGBT-Technik eingesetzt, wenn die technischen Bedingungen, insbesondere die stufenlose Leistungsregelung, dafür sprechen. Ein entsprechendes Beispiel stellt der bereits erwähnte 5-t-Gießofen dar, der – um in kürzester Zeit eine deutliche Überhitzung von 90 K zu ermöglichen – mit einer IGBT-Umrichteranlage mit maximal 1000 kW ausgerüstet wurde. Dabei ist zu bemerken, dass die Warmhalteleistung bei 150 kW liegt und eine übliche Leistungsversorgung eines 5-t-Ofens im Bereich von 200– 300 kW liegt. In diesem Fall sprach die erforderliche exakte Regelung der Leistung für das Überhitzen in Abhängigkeit von dem Ofenparameter für den Einsatz einer IGBT-Umrichteranlage.
Die weiteren schaltungstechnischen Möglichkeiten der IGBTUmrichtertechnik – Beispiel: variable Frequenz oder gemeinsame Leistungsversorgung für zwei unterschiedliche Öfen – haben bisher keine praktische Anwendung für Gießöfen gefunden. Es kann daraus geschlussfolgert werden, dass der Einsatz von Umrichteranlagen nur in begründeten Einzelfällen erfolgen wird.
Prozesssteuerung und- regelung
Standard ist inzwischen der Einsatz eines PC-basierten Prozesssteuerungs- und Visualisierungssystems für die Überwachung, Kontrolle und Bedienung aller Aggregate des Gießofens und deren Funktionen. Darüber hinaus ermöglichen diese Systeme auch die Speicherung und Verwaltung der Betriebsdaten und deren Weiterleitung. Die Mensch-Maschine-Schnittstelle besteht aus einem TFT-Monitor mit Maussteuerung und einer Folientastatur zur Eingabe von alphanumerischen Zeichen und Steuerkommandos. Aktuell erfolgt die Umstellung auf Systeme mit Multi-Touch Displays. Bild 2 zeigt das vorbereitete Hauptmenü für den Einsatz dieser neuen Generation.
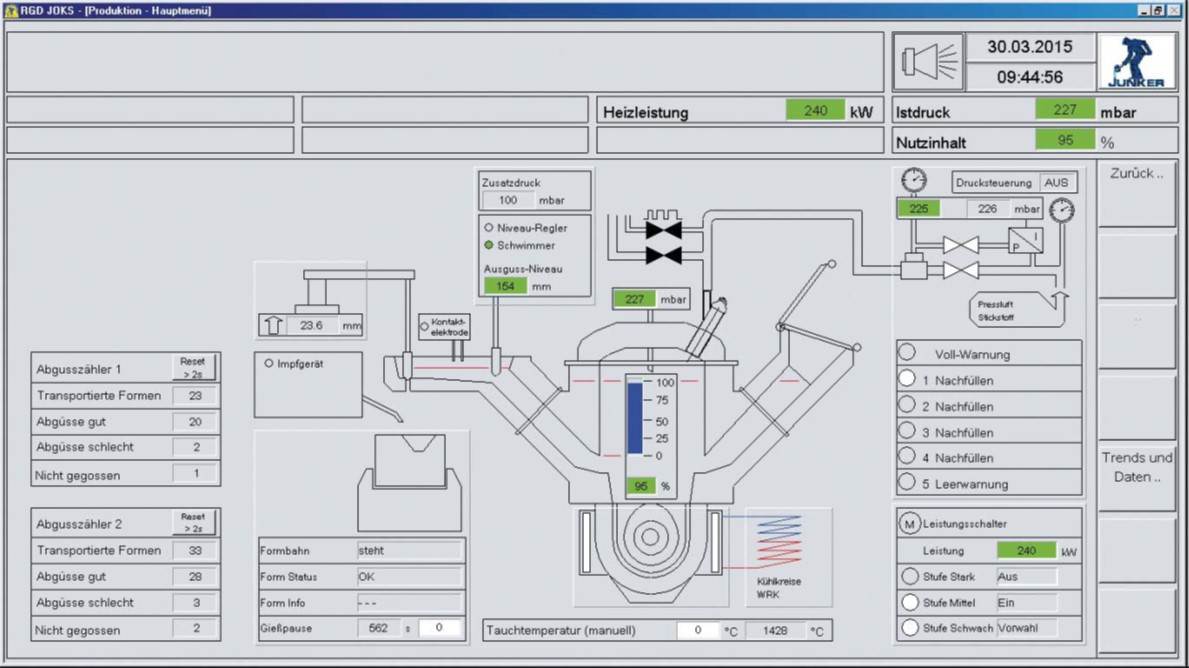
Die Dosiergenauigkeit wird unter anderem von den technischen Merkmalen der Stopfensteuerung und des zugehörigen Antriebs bestimmt. Für das präzise Arbeiten des Stopfenantriebes sind daher vor allem eine hohe Stellgeschwindigkeit und Genauigkeit gefragt. Eine einstellbare, geregelte Schließkraft des Stopfens, eine automatische Korrektur des Düsenverschleißes sowie Einrichtungen zur Düsenreinigung und zum Einreiben des Stopfens sind weitere Anforderungen.
Der von Otto Junker aus Simmerath-Lammersdorf entwickelte neue elektrische Stopfenantrieb (Bild 3) erfüllt diese Anforderungen mit hoher Zuverlässigkeit. Bei der neuen Stopfensteuerung wird der Stopfen urch einen echten Linearantrieb mittels Magnetkraft bewegt. Einziges bewegliches Bauteil ist das Schubrohr (Sekundärteil) mit spiralförmig gedrehter Nut. Zwischen diesem und einer Statorhohlwelle (Primärteil, 2-polig gewickeltes Blechpaket) befindet sich ein definierter Luftspalt. Damit arbeitet dieser Antrieb praktisch verschleißfrei.
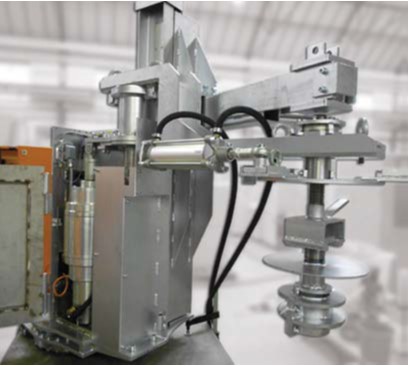
Bei einem eventuellen Stromausfall fällt der Stopfen aufgrund der geringen Selbsthemmung des Linearantriebs durch sein Eigengewicht nach unten und verschließt die Ausgießdüse. Mittels einer integrierten Hebelvorrichtung kann der Stopfen sehr einfach manuell in eine mechanische Schnapphalterung gehoben werden.Beim Abschalten der Stopfensteuerung nach Produktionsende hebt der Linearantrieb den Stopfen ebenfalls in diese Schnapphalterung. Anschließend wird der Leistungsteil des Antriebs automatisch abgeschaltet. Beim Einschalten der Stopfensteuerung wird der Leistungsteil eingeschaltet und der Linearantrieb fährt den Stopfen selbsttätig aus der Schnapphalterung bis in die Ausgussdüse. Zusätzlich zur eigenen Gewichtskraft des Stopfens wird dieser dabei mit einer einstellbaren, geregelten Anpresskraft in die Ausgussdüse gepresst. Verschleiß an Stopfen und/ oder Düse wird auf diese Weise bis zu einer einstellbaren Verschleißgrenze automatisch korrigiert.
In Verbindung mit der Entwicklung des neuen Stopfenantriebes wurde auch der Einsatz eines neuen Kamerasystems zur Messung des Füllstandes im Eingusstrichter und der darauf basierenden Regelung der Gießleistung erprobt. Bild 4 zeigt eine entsprechende Versuchseinrichtung, bestehend aus dem neuen Stopfenantrieb und dem Kamerasystem. Der Aufbau des Ausgießsystems einschließlich eines kompletten Bedienpults ermöglichte in der Entwicklungsphase eine realitätsnahe Erprobung des Systems.
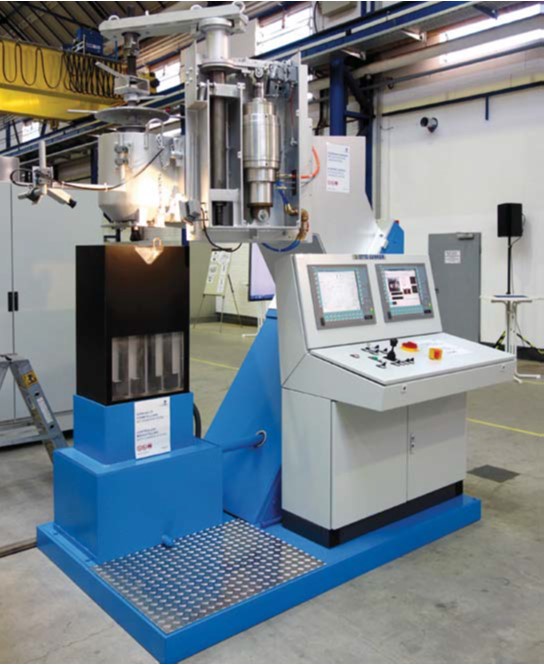
Im Ergebnis weiterer Versuche unter industriellen Bedingungen wurde eine hohe Dosiergenauigkeit erreicht und das vorgegebene Niveau im Eingießtrichter wird mit einer Abweichung von wenigen mm zuverlässig eingehalten. Der neue Stopfenantrieb wurde nach erfolgter Langzeiterprobung in Verbindung mit dem neuen Kamerasystem inzwischen in einigen Projekten erfolgreich eingesetzt.
Für die optimale metallurgische Wirkung einer Gießstrahlimpfung ist die geregelte Zugabe einer festgelegten Menge Impfmittel in den Gießstrahl während des gesamten Gießprozesses erforderlich. Die Qualitätskontrolle erfordert, dass die zugeführte Impfmittelmenge erfasst und dokumentiert wird. Da die vorhandenen Impfeinrichtungen diese Anforderungen nicht optimal erfüllen und die Dosierung nicht ausreichend genau ist, wurde das Konzept einer neuen Gerätegeneration entwickelt und erprobt. Die neuartige Impfeinrichtung (Bild 5) arbeitet wie folgt:
Ausgehend von einer Vordosierung in einen Zwischenbehälter erfolgt die Feindosierung mittels eines frequenzgeregelten Schneckenantriebes auf eine Feinwägeeinrichtung zur exakten Kontrolle und Registrierung der Impfmenge. Mit diesem System kann die Impfrate geregelt werden und die gewogene Impfmittelmenge jedes Abgusses wird gespeichert. Für die Steuerung und Regelung kommt eine SPS zum Einsatz und die Visualisierung und Bedienung werden über ein Touch Panel oder das Junkereigene JOKS-System vorgenommen. Über eine entsprechende Schnittstelle können die gespeicherten Daten abgerufen werden.
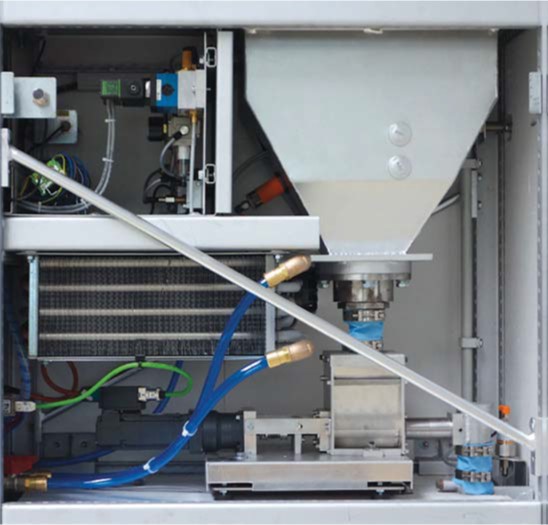
In umfangreichen Versuchen wurde die volle Funktionsfähigkeit nachgewiesen und eine hohe Dosiergenauigkeit erzielt. Zum Zeitpunkt dieses Berichtes befindet sich der Prototyp der neuen Impfeinrichtung in einem Langzeittest unter Produktionsbedingungen bei dem UnternehmenErgocast Guss GmbH aus Jünkerath.
Sonderausführungen Abgießen
Das direkte Gießen mit dem geregelten Einstopfensystem in den Eingießtrichter der Form ist in einigen Fällen nicht möglich, dies trifft zu wenn:
- ein gewichtsdosiertes Impfen oder Legieren unmittelbar vor dem Gießen erfolgen soll,
- ein offener Oberlauf in der Form eingesetzt wird,
- die unmittelbare Positionierung des Stopfens über den Einguss aus Platzgründen nicht möglich ist,
- die Gießzeit länger als die Taktzeit der Formanlage ist, gleichzeitig zwei Formen oder eine Form mit zwei Eingießtrichtern abzugießen ist oder
- die Formanlage mit kontinuierlichem Vorschub arbeitet.
In diesen Fällen bieten sich Konzepte mit Doppelstopfen, Zwischenpfannen oder Verteilerrinnen an, um die technischen Anforderungen erfüllen zu können [4].
Werden in einem Formkasten zwei unterschiedliche Gussstücke mit getrenntem Einguss hergestellt, ist ein Doppelstopfensystem einzusetzen (es wurden auch schon Dreifachsysteme eingesetzt). Dies trifft auch zu, wenn mit zwei Eingüssen für ein Gussstück gearbeitet wird. Dabei können die Eingüsse parallel oder nacheinander mit Eisen gefüllt werden. Sollen zwei Formkästen gleichzeitig abgegossen werden, so kommt ebenfalls eine Lösung mit Doppelstopfen zur Anwendung. Bei sehr hohen Leistungen der automatischen Formanlage und damit kurzen Zeiten für den Formprozess ist unter Umständen die Taktzeit kürzer als die Gießzeit. Mit dem Einsatz von mitfahrenden Zwischenpfannen kann die erforderlich Gießzeit eingehalten werden.
Eine alternative Lösung besteht darin, die Zeit für das Gießen dadurch zu verdoppeln, dass immer zwei Formballen oder Formkästen zusammen vorgeschoben werden, also der Takt zwei Formprozesse umfasst. Daraus ergibt sich die Anforderung an den Gießofen, gleichzeitig zwei Formen abzugießen, deren Position des Eingießtrichters sich ändern kann. Mit einer Neuentwicklung von Otto Junker [5], einem System mit zwei unabhängig voneinander schwenkbaren Stopfen, kann diese Anforderung erfüllt werden. In Bild 6 ist die Prinzipzeichnung dieser Lösung zu sehen. Inwieweit dieses System zum Einsatz kommen wird, bleibt der industriellen Erprobung vorbehalten.
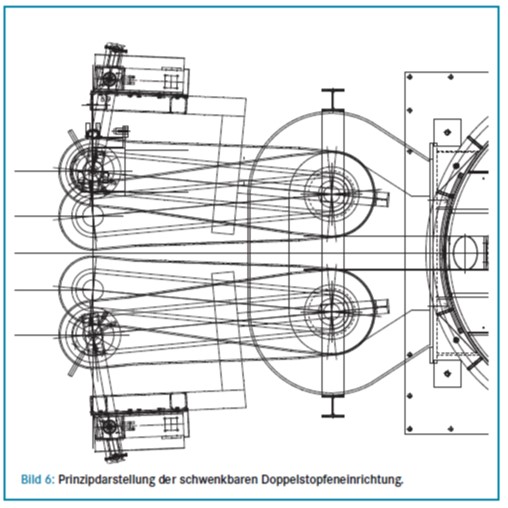
Legierungswechsel und Schnellwechsel
Gießgefäß Da es sich bei einem Gießofen in der Regel um ein mit einem Rinneninduktor beheiztes Aggregat handelt, wurde in der Vergangenheit strikt die Regel beachtet, bei einem Legierungswechsel den Induktor unter keinen Umständen zu entleeren. Somit verblieb immer ein Sumpf im Ofen, was eben diesen Legierungswechsel hinsichtlich der Analyseneinhaltung erschwert. In jüngerer Zeit praktizieren jedoch einige Gießereien eine Totalentleerung des Gießofens, dies zum Teil täglich. Somit gestaltet sich der Wechsel von Gusseisen mit Lamellengrafit auf Gusseisen mit Kugelgrafit unproblematisch und schnell, jedoch muss der Ablauf hinsichtlich Zeit- und Temperaturführung penibel und reproduzierbar erfolgen. Dieses Thema wird in einem künftig erscheinenden Aufsatz vertieft behandelt.
Darüber hinaus erfordern Neuzustellungen des Induktors bzw. des Gießgefäßes und andere Reparatur- und Instandhaltungsmaßnahmen mehr oder weniger häufig einen Wechsel des Gießgefäßes. Dieser Wechsel ist zeitaufwendig und kann zu Ausfallzeiten der Formanlage führen. Bei häufigen Wechseln, z. B. aufgrund von kurzen Standzeiten des Induktors, ist das nur schwer zu verkraften.
Im Fall eines weiteren Projektes bestand die Zielstellung darin, den Gefäßwechsel in einer Schicht bzw. in weniger als 6 h durchführen zu können. Damit kommt es bei einem 2-Schichtbetrieb – auch bei einem Wechsel innerhalb der Woche – zu keinem Produktionsausfall. Dabei wird natürlich vorausgesetzt, dass ein zweites Ofengefäß gesintert und einbaufertig zur Verfügung steht.
Die Möglichkeit, kurzfristig einen Gefäßwechsel an einem druckbetätigten Gießofen durchführen zu können, erforderte Änderungen an der bisherigen Konstruktion. Die Änderungen sehen so aus, dass das Gefäß eine zusätzliche Plattform erhält und ohne den Kipprahmen daran herausgehoben werden kann (Bild 7). Dabei bleiben alle Zusatzeinrichtungen wie Druckluftversorgung, Stopfenantrieb usw. im Gestell beziehungsweise werden nur weggeschwenkt und die Strom- und Wasseranschlüsse werden mittels Schnellkupplungen gelöst. Auch für die unbeheizte Gießeinrichtung von Otto Junker wird dieses System eingesetzt.
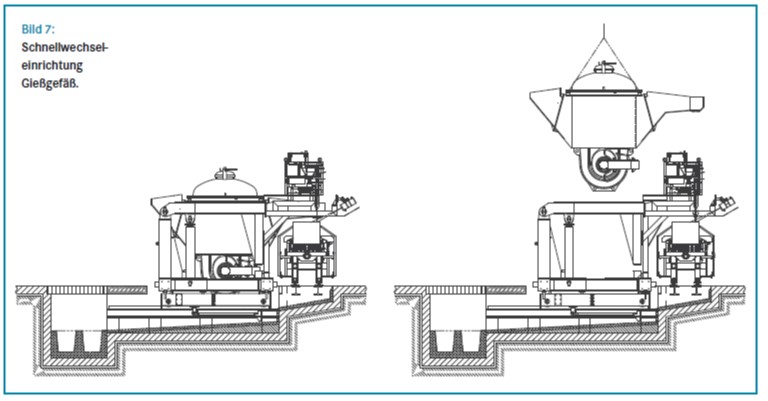
Neue Verfahrenstechnik
Die Anforderungen zur Herstellung von qualitativ hochwertigem Guss mit reduzierter Wanddicke werden den Einsatz der Niederdruckgießtechnik auch im Bereich der Eisengusswerkstoffe vorantreiben. Dabei handelt es um eine Verfahrenstechnik, die im Aluminium- und Kupfergussbereich nicht mehr neu ist und erfolgreich eingesetzt wird [6]
Das Grundprinzip (Bild 8) besteht darin, dass das Ofengefäß mit Druck beaufschlagt wird und das flüssige Metall von unten in die Form gedrückt wird. Da die Gießleistung vom Druckverlauf bestimmt wird und nicht allein von der Schluckleistung der Form abhängig ist, kann die Gießkurve aktiv gesteuert werden. Die Vorteile dieser Gießofentechnik können wie folgt zusammengefasst werden:
- Reduzierung der minimalen Wanddicke
- Steigende laminare Formfüllung ohne Oxideinschlüsse
- Hohe Dosiergenauigkeit und aktiv steuerbare Gießcharakteristik
- Reduzierung Kreislaufmaterial
- Verbesserte Wirtschaftlichkeit und Prozesssicherheit.
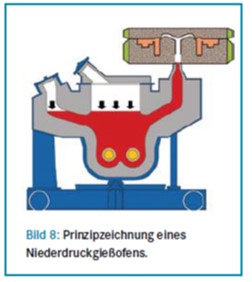
Dabei ist in Kauf zu nehmen, dass entweder nach dem Beendigen des eigentlichen Gießvorganges die Form gedreht bzw. der Eingießbereich mit einem Schieber verschlossen wird oder die Taktzeit bis zum Erstarren des flüssigen Metalls im Eingießbereich verlängert werden muss.
Im Stahlgussbereich gibt es seit geraumer Zeit einige Versuchsanlagen, die mit dieser Verfahrenstechnik arbeiten. Über eine aktuelle industrielle Nutzung für die Herstellung von Abgasturbolader-Turbinengehäusen aus Stahlguss wird von M. Werner und E. Dötsch [7] berichtet. Der Einsatz dieser Verfahrenstechnik zum Gießen dünnwandiger Gussteile aus Gusseisen mit Lamellengrafit bleibt der weiteren Entwicklung vorbehalten.
Fazit
Die Gießofentechnik hat sich in den zahlreichen Einsätzen in den Gießereien bewährt. Die aufgezeigten Entwicklungen und Trends belegen die Möglichkeiten der weiteren Verbesserung und Optimierung dieser Technik und die Erschließung neuer Einsatzgebiete.
Literatur:
[1] Noda,Y.; Nishida, T.: Int. J. of Automation Technology, Vol.2 Nr. 4, 2008, S. 241–246
[2] Trauzeddel, D. Giesserei, 05 2010, S.96–103
[3] Neumann, E.; Trauzeddel, D.: Foundry Trade Journal, July 2002, S. 23–24
[4] Einsatz von Induktionsöfen zum Warmhalten und Gießen von Gusseisenwerkstoffen, Otto Junker GmbH, Eigenverlag, 2010
[5] Deutsche Patentanmeldung: Aktenzeichen 10 2015 101 901.9, Gießvorrichtung zum Abgießen einer metallischen Schmelze
[6] Hauck; A.: Induktionsofensysteme für den Niederdruckguss von Eisen- und Nichteisenwerkstoffen; Deutscher Gießereitag 2013
[7] Werner, M.; Dötsch, E.: elektrowärme international, 4-2014, S. 29–34