Dünnwandiger Stahlguss - Realisierung einer großserientauglichen Prozesskette für den Automobilbau
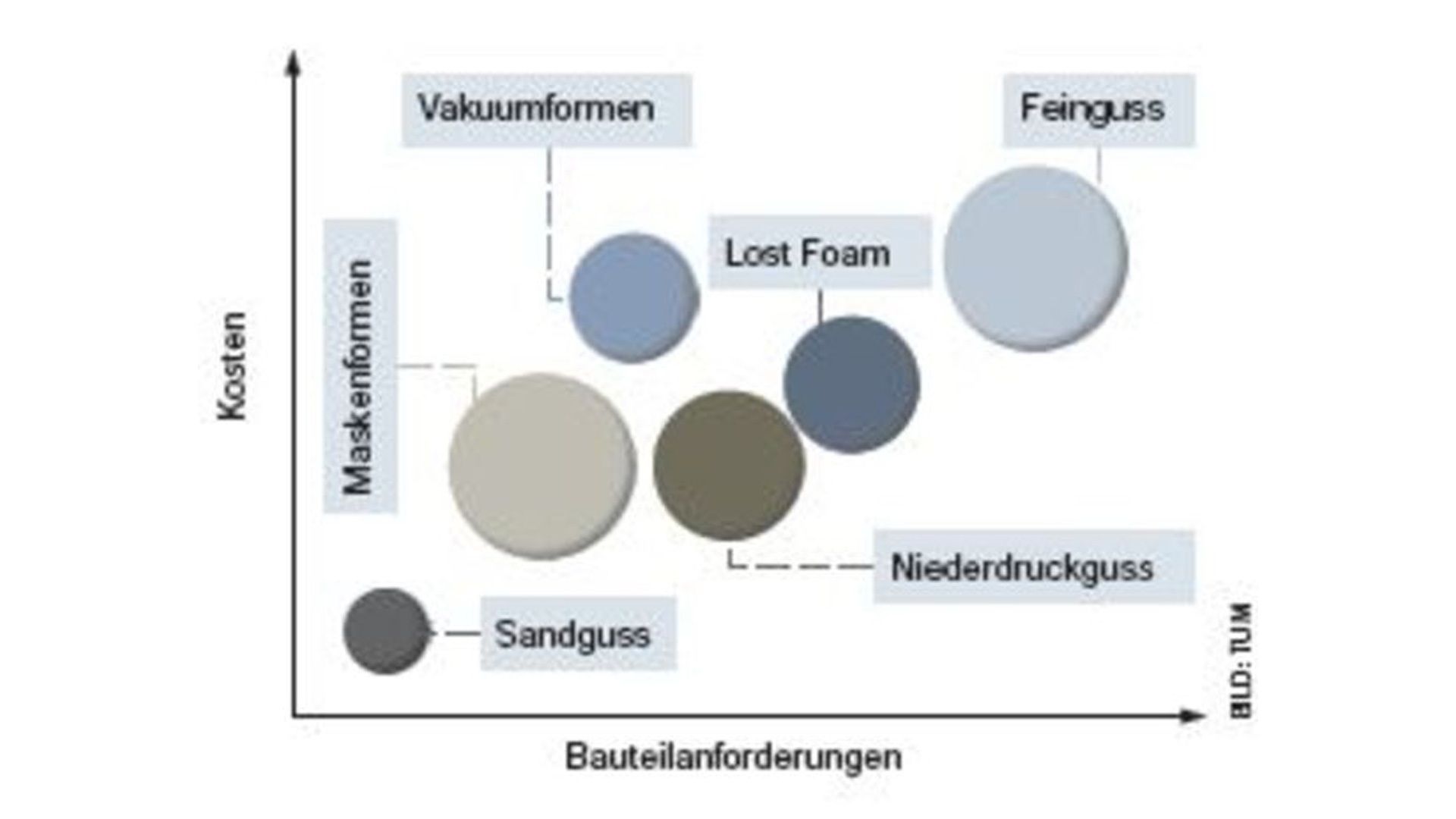
BMW Group, Werk Landshut und Lehrstuhl für Umformtechnik und Gießereiwesen der Technischen Universität München
Der dünnwandige Stahlguss stellt den Brückenschlag zwischen Schwermetallguss und der konsequenten Verfolgung des Leichtbaugedankens dar. Die Kombination dünner Wandstärken mit, im Vergleich zu Leichtbauwerkstoffen wie Aluminium oder Magnesium, hoher materialspezifischer Festigkeit und Steifigkeit erlaubt die gewichts- und bauraumsparende Realisierung kompakter und integraler Gussbauteile für hochbeanspruchte Bereiche z. B. in der Karosserie eines Fahrzeugs.
Hierbei spielen drei Aspekte eine tragende Rolle:
- Die Geometrie muss bauraumsparend und funktional gestaltet sein, um die Einbringung zusätzlicher Komponenten der Vernetzung, Digitalisierung und Elektrifizierung zu ermöglichen und gleichzeitig den daraus resultierenden Gewichtseintrag auszugleichen.
- Die Wirtschaftlichkeit des Gesamtprozesses muss unter Berücksichtigung von Investitions- und Produktionskosten bei Großserienproduktion gegeben sein.
- Es werden fähige Prozesse benötigt, die mittelfristig weltweit bei Lieferanten verfügbar sind.
Die möglichen Gießverfahren müssen unter Berücksichtigung der genannten Aspekte gegeneinander abgewägt werden. Die Geometrie fließt dabei (neben weiteren Eigenschaften) in die Bauteilanforderungen ein, während die Wirtschaftlichkeit in den Bauteilkosten berücksichtigt wird. Der Durchmesser der Indikatoren im Blasendiagramm ist ein Maß für die Verfügbarkeit des Prozesses nach heutigem Stand der Technik unter Berücksichtigung der Fähigkeit, höchste Anforderungen an Wandstärke, Wandstärkentoleranz und Oberflächenqualität zu erfüllen. Es wird deutlich, dass die hochwertigsten Bauteile derzeit mittels Feingießen hergestellt werden können. Bei Fokussierung auf die Wirtschaftlichkeit ist das herkömmliche Sandgießen zu wählen. Trotz der zu erwartenden Abstriche in der realisierbaren Bauteilqualität wurde im Projekt aufgrund der Prämisse der Wirtschaftlichkeit in Großserienproduktion das Sandgießen gewählt.
Zur Sicherstellung des Korrosionsschutzes wird eine Verzinkung auf die Bauteile aufgebracht, deren erforderliche Mindestschichtdicke mit der Oberflächenrauheit der Gussoberfläche zunimmt. Gleichzeitig besteht eine Obergrenze für die Dicke der Zinkschicht, bis zu der die Qualität der durch Punktschweißen erzeugten Fügepunkte sichergestellt werden kann. Bei feuerverzinktem Sandguss wird diese Obergrenze bedingt durch die Oberflächenrauheit überschritten. Zur Lösung dieses Anforderungskonfliktes wurden zwei grundsätzliche Ansätze untersucht. Bei einer geringeren Oberflächenrauheit wäre eine dünnere Zinkschicht für einen adäquaten Korrosionsschutz erforderlich. Unter Beibehaltung des Gießverfahrens lässt sich eine nachträgliche umformtechnische Reduzierung der Oberflächenrauheit jedoch nicht wirtschaftlich umsetzen. Im Rahmen des Projekts wurde hier ein alternativer Lösungsweg beschritten.
Während die Korrosionsschutzanforderung flächig auf dem gesamten Bauteil gilt, muss die Punktschweißbarkeit nur lokal an den Fügestellen sichergestellt werden. Es wurde die Möglichkeit untersucht, an den Fügestellen die Zinkschicht lokal zu entfernen, um das Fügen des freigelegten Stahlgusses mit dem Fügepartner (im Karosseriebau meist Stahlblech) zu ermöglichen. Dabei wurde die Zinkschicht thermisch lokal an den Fügestellen mittels einer gepulsten Laserstrahlung zersetzt, um das Grundmaterial freizulegen. Die untersuchten Gussproben zeigten dabei einen sehr definierten Schichtabtrag, sowohl in die Tiefe als auch im Grenzbereich zur nicht entfernten Zinkschicht. Die damit erreichte Punktschweißbarkeit des Gusses unterstreicht das Potenzial zur Lösung des aufgezeigten Zielkonfliktes. Am Ende entsteht ein Prozess, der die Herstellung dünnwandiger Stahlgussbauteile für den Automobilbau unter Berücksichtigung des vielfältigen Anforderungsportfolios ermöglicht.
Weitere Informationen
Thomas Greß M.Sc.
TU München
Lehrstuhl für Umformtechnik und Gießereiwesen (utg)
Walther-Meißner-Straße 4, 85748 Garching
Tel.: +49 (0)89 / 289 – 13980
thomas.gress(at)utg.de
www.utg.mw.tum.de
Florian Hofbauer
BMW Group
Leichtmetallgießerei
Ohmstraße 2, 84030 Landshut
Tel.: +49-151-6040-4067
E-Mail: florian.ma.hofbauer(at)bmw.de
www.bmwgroup.com