Autonomous Engineering of Steel Casting − State-of-the Art, Applications and Ongoing R+D
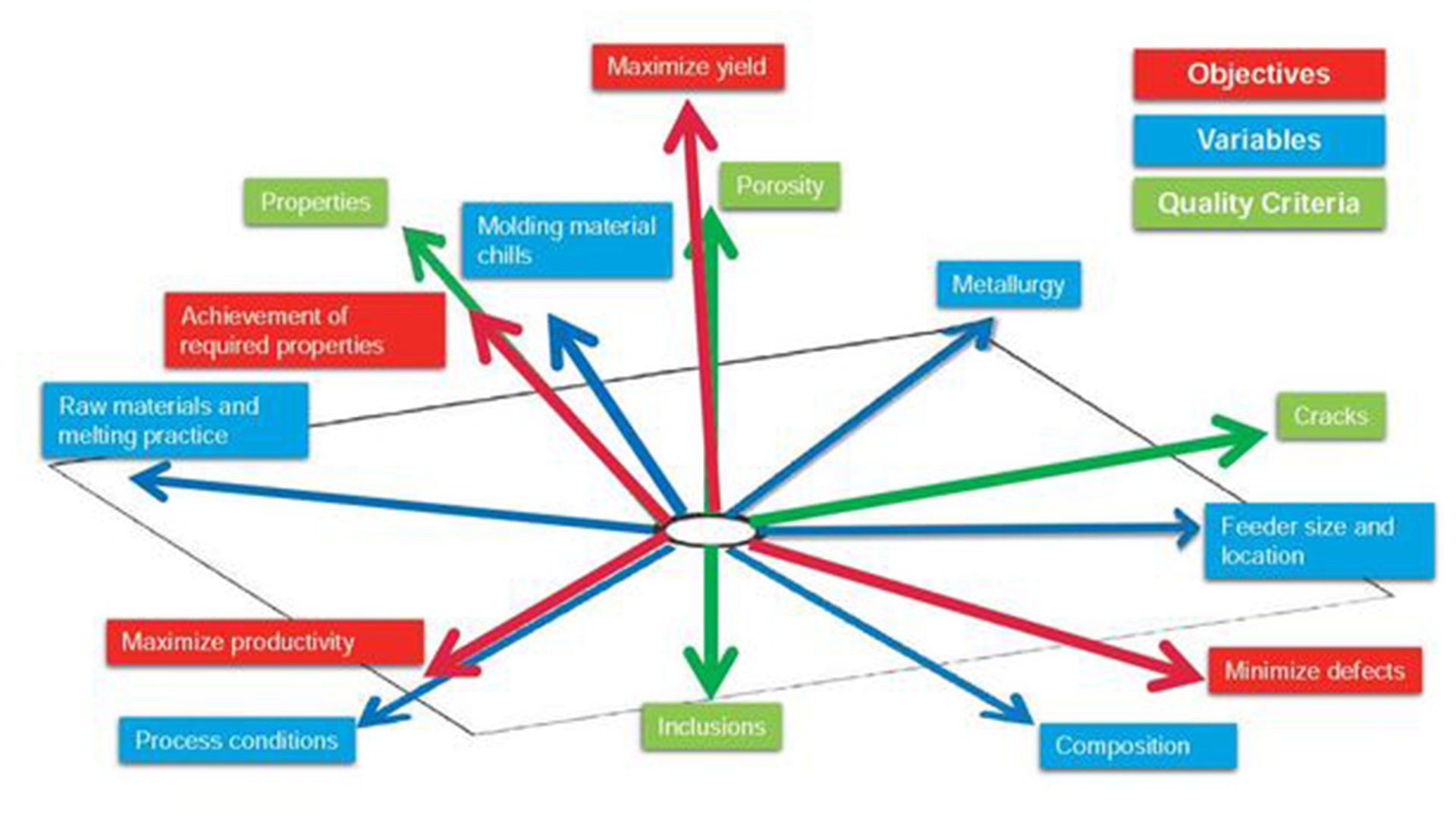
Max Peymandar and Jörg C. Sturm, MAGMA Gießereitechnologie GmbH, Aachen
40 years after its introduction, casting process simulation has become an accepted tool for the layout and process design of steel castings worldwide. Today, the results from simulation address many different quality issues in steel castings. The diversity of steel grades, the variety of factors that affect casting quality and complex interactions between physics, metallurgy, casting geometry and the process sequence all play a role in the quality of a steel casting.
Empirical knowledge (even if supported by the insights of simulation) just confirms a single predefined operating point but does not provide information about the possible optimum nor about the robustness of the chosen process window. Autonomous Engineering overcomes these limitations by offering the foundry expert a virtual field for systematic experimentation. Autonomous Engineering is a methodology utilizing multiple Magmasoft simulations as a set of virtual experiments in order to achieve the best possible solution. This paper illustrates the benefits of Autonomous Engineering for steel castings using different industrial applications as examples. In addition, new capabilities and current R&D activities are discussed. Applying these developments, the steel foundry will be offered unique opportunities to achieve new and optimized applications as well as to define reliable manufacturing routes before the production of a high integrity casting has begun.
The beginnings of computer-aided predictions of casting processes date back to the 1960s and early 1970s. At first, it were mainly so-called expert systems that linked empirical knowledge with geometric information based on ideas proposed by Heuvers, Pellini and Chrorinov and applied them to steel castings.
This was followed by the first 2-dimensional simulation applications that for the first time took physical laws into account (e. g. Fourier’s heat conduction equation). Finally - also thanks to increasing computing power - 3-dimensional simulation models were developed in the 1980’s.
Steel castings were the first materials to which “solidification simulation” was applied. This was due to the nature of solidification of steel castings, where the formation of shrinkage related defects is strongly linked to the formation of hotspots in the casting. In this way, even a limited heat flow simulation could aid steel casting experts in identifying critical areas in their design and methoding.
In metal casting processes, everything happens at the same time and is closely coupled. While this can be seen as a key advantage of metal casting over other manufacturing processes, it also makes decisions regarding the best or at least an adequate layout for a casting complex. Changing one process parameter can have a multitude of impacts on the rest of the process and can influence the final casting quality in many different ways. This makes it challenging to manually optimize the casting process by evaluating the final component’s quality based on real-world trials and pursuing quality and economic objectives simultaneously.
This is especially true for steel castings, with their unbeaten diversity of grades, resulting microstructures and properties, and the multiple manufacturing steps to achieve the required quality from metallurgy through casting, heat treatment, upgrading to machining. To meet today’s specifications in making high integrity steel castings requires a profound understanding of the material behavior and the process robustness for the entire manufacturing route. The technology of simulating the casting process and predicting the resulting material properties has become an extremely instrumental methodology in two ways:
- Making the mold as a black box transparent for the foundry specialist, helping him to understand the root causes of possible problems prior to producing the first casting.
- Developing virtual simulation tools for the casting process requires a profound and quantitative understanding of the impacts of physics, metallurgy and chemistry as such.
This has changed the empirically driven process substantially into a first principle based and reliable manufacturing process. Through these efforts, today foundrymen can assure the sustainability and growth of their businesses while maintaining a sizable technological edge over competition. Quantitative results provided by casting process simulation also help designers to understand the impact of the process on the performance of castings in use. For most steel foundries, casting process simulation is used daily as a standard tool to assess gating and risering and to predict feeding. It has become an instrument in quality systems and process optimization. State-of-the-art simulation tools consider the special material behavior of the diversity of steel grades with respect to their alloy composition, melting practice, and metallurgy.
Dr.-Ing. Max Peymandar Product Manager and Dr.-Ing. Jörg C. Sturm, Managing Director MAGMA Gießereitechnologie GmbH, Aachen