Gießtechnik
Für das Herstellen von Gusseisenteilen durch Gießen kommen grundsätzlich zwei Verfahrensgruppen für die Formherstellung zur Anwendung, die Sandformen, die nach dem Abguss zerstört werden (verlorene Formen), um das Gussteil zu entnehmen, und die metallischen Kokillen (Dauerformen), die zwei- bis mehrteilig sind und zur Gussentnahme geöffnet werden. Der in diesen Formen vorzusehende Hohlraum, der dem späteren Gussteil entspricht, ist bei den metallischen Kokillen spanend ausgearbeitet. Bei den Sandformen werden Modelle, die ein Abbild des Gussteils darstellen, in den Formstoff eingearbeitet, die nach ihrer Entnahme den Formhohlraum als Negativ des Gussteils freigeben, in den das Gießmetall eingegossen wird.
Zur Abbildung von Innenhohlräumen im Gussteil kommen Kerne zur Anwendung (Bild 34).
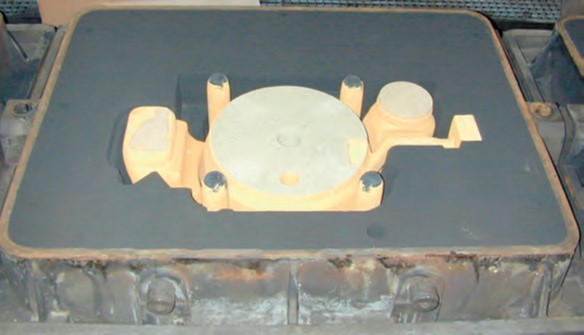
Sie werden aus geeigneten Sand gebundenen Formstoffen gefertigt, die in die Form lage- und passsicher eingelegt werden. Die Herstellung dieser Kernteile, die neben den Innenhohlräumen auch im Außenbereich der Form bei Hinterschnitten zum Einsatz kommen können, benötigt eine meist mehrteilige Kernkasteneinrichtung zur maßgenauen Fertigung. Komplexe und biegegefährdete Kerne können mit Kernstützen zusätzlich
an mit dem Kunden vereinbarten Stellen abgesichert werden (Bild 35).
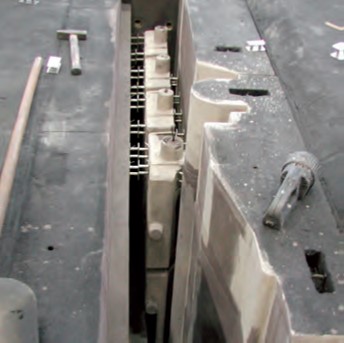
Zum Füllen der Form ist ein Gießlauf erforderlich, durch den das Metall in die Form gelangen kann. Da der Formfüllungsprozess Einfluss auf die Gussteilqualität hat, ist diese als Anschnitt- oder Gießsystem bezeichnete ein- oder mehrkanalige Öffnung für die Formfüllung genau zu dimensionieren und am Gussteil dort anzubringen, wo es gieß- und fertigungstechnisch erforderlich ist. Das Anschnitt- oder Gießsystem wird nach dem Guss entfernt. Es besteht im Allgemeinen aus dem Trichter, einem oder mehreren Läufen und Anschnitten, die Bestandteil der Modelleinrichtung sind oder aus feuerfesten Kanalsteinen, die im Baukastensystem zusammengesetzt werden.
Die Querschnitte der einzelnen Bestandteile sind nach den Gesetzen der Hydromechanik genau berechnet, um ein möglichst laminares und gesteuertes Einfließen der Schmelze in den Formhohlraum zu ermöglichen. Die Anpassung an die physikalischen Gesetzmäßigkeiten des Fließens von Flüssigkeiten und die Gussteilgestalt erfolgt nach gießereitechnischen Erfahrungen und wissenschaftlich technischen Untersuchungen und gehört zum Aufgabengebiet der ausführenden Gießerei. Mit der numerischen Simulation der Formfüllung am Computer ist es heute der Gießerei möglich, die komplexen Vorgänge der Gussspeisung im Zusammenhang zu den abkühlungsbedingten Speisungsvorgängen exakt vorherzubestimmen [13].
Die Temperatur, mit der die Schmelze durch das Gießsystem in den Formhohlraum eingefüllt wird, liegt um einen bestimmten Betrag über der Temperatur, bei der die Erstarrung einsetzt, um die Form sicher füllen zu können, denn der Abkühlungsprozess setzt sofort nach der Schmelzeentnahme aus dem Ofen ein. Der Abkühlungs- und Erstarrungsprozess einer Schmelze ist mit einem Volumendefizit verbunden, das werkstoffabhängig ist. Dieser Prozess setzt sich aus drei Stufen zusammen (Bild 36), die gießtechnisch berücksichtig werden müssen, soll ein dichtes lunkerfreies Gussteil entstehen. Die zuerst auftretende Flüssigkontraktion kompensiert das Volumendefizit mit nachspeisender Schmelze aus dem Gieß- und Speisesystem. Bei der zweiten Stufe, der Erstarrungskontraktion, beginnt die Schmelze von außen nach innen fest zu werden. Dabei tritt weiterhin eine Volumenkontraktion auf, die, solange Schmelze vom Gießsystem oder Speiser nachfließen kann, kompensiert werden kann. Wenn in späteren Stadien außen herum das gesamte Metall bereits erstarrt ist, können im Inneren fein verteilte (Mikrolunker) und/oder zu großen (Makrolunker) Blasen und an der Außenseite Einfallstellen als Folge der nun behinderten Schrumpfung entstehen.
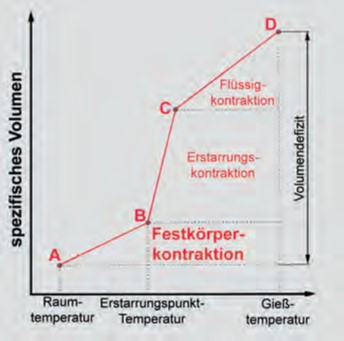
Diese bauteilseitig nicht erwünschte, aber physikalisch nicht vermeidbare Lunkerung lässt sich weitestgehend durch Vorsehen zusätzlicher Speisungsmöglichkeiten (sogenannte Speiser) mit einem so großen Querschnitt, dass durch die dort zuletzt erfolgende Speisung die Lunker aus dem Gussteil in den Speiser verlagert werden, beseitigen (Bild 37). Hierfür kann auch das Gießsystem genutzt werden. Der Werkstoff Gusseisen mit Kugelgraphit weist gegenüber anderen Gusswerkstoffen ein geringeres Schwindungsverhalten auf und damit eine geringere Lunkerneigung. Vielfach kann sogar ohne Speisung lunkerfrei gegossen werden. Da aber die Lunkerneigung stark von der Gusskonstruktion abhängt, lässt sich in vielen Fällen eine günstigere Lösung in der gießgerechten Anpassung des Bauteils finden. So kann sie beispielsweise durch entsprechende konstruktive Maßnahmen, wie Vermeidung großer Wanddickenübergänge und anderer masseintensiver Bereiche sowie durch Vorsehen einer schwindungskompensierenden Gussteilkonstruktion verringert oder sogar vermieden werden.
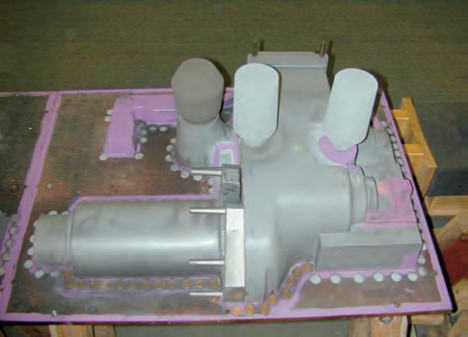
Der dritte Bereich, die Festkörperkontraktion, findet im allseits erstarrten Gussteil statt, bis die Raumtemperatur erreicht ist. Sie ist über den Wärmeausdehnungskoeffizienten des Werkstoffs genau definiert und findet in einem Aufmaß an der Modelleinrichtung oder Kokille, dem sogenannten Schwindmaß Berücksichtigung.
Wie die Prozesse der Formfüllung sind auch die Erstarrungsvorgänge heute simulativ hochgradig für die betreffende Gusskonstruktion vorherbestimmbar. Den zu erwartenden Lunkerstellen kann so bereits im Stadium der Bauteilentwicklung gemeinsam mit dem Kunden durch konstruktive Anpassungen entgegen gewirkt werden. Da das allerdings bei komplexen Gusskonstruktionen oft nicht möglich ist, haben die Gießereien basierend auf umfassenden Untersuchungen Möglichkeiten zur gerichteten oder gelenkten Erstarrung entwickelt.
Weitere Einflussfaktoren auf die Gussteilausführung haben die Formverfahren. Während bei der Gussfertigung in Sandformen kaum gestaltungsseitige Restriktionen für die Gussteile bestehen, da die Sandformen nach dem Erstarren des Gussteils zur Gussentnahme zerstört werden (verlorene Formen), Hinterschneidungen am Modell durch Kernteile und Innenbereiche mit Kernen abgeformtwerden können, muss bei den nichtzerstörbaren Dauerformen die Kokillenöffnung und Gussentnahme ohne Hinterschnitte abgesichert werden, was diesemVerfahren zusammen mit den teureren Werkzeugen (metallische Kokillen) Einsatzfälle in speziellen Nischenbereichen, wie dem Strang-, Schleuder- aber auch dem Schwerkraftformguss bringt, wo die spezifischen Eigenschaften des Kokillengusses ausgenutzt werden. Die Sandformverfahren dominieren hier deutlich in der Anwendung, da sie wirtschaftlicher, flexibler und universeller für fast alle Gusssortimente einsetzbar sind.
Sandformverfahren
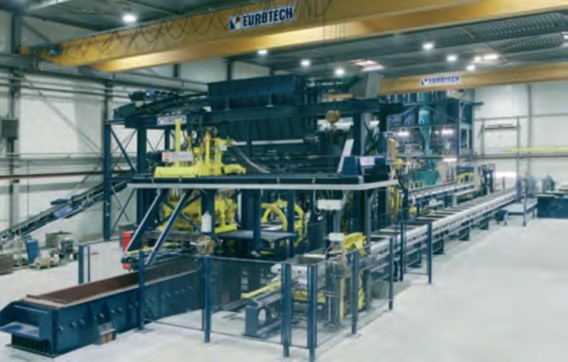
Die Sandgussfertigung hat in den letzten Jahrzehnten bedeutende Fortschritte gemacht. Neben den technischen Verbesserungen bei der Herstellung von Serien-Gussteilen auf Formanlagen und deren Formstoffen können heute durch die verbesserten Verdichtungsparameter und Formstoffe auch Gussteile mit eingeengten Toleranzen, hoher Reproduzierbarkeit und mit einer hohen Oberflächengüte gefertigt werden, die mit der Gießerei vereinbart werden können.
Dauerformverfahren
Im Gegensatz zu den Sandgießverfahren, bei denen die Gießformen nach dem Abguss zur Gussteilentnahme zerstört werden, sind metallische Dauerformen (Kokillen = französisch Schale) aus Gusseisen oder Stahl nicht zerstörbar. Sie sind zwei- oder mehrteilig ausgeführt und müssen nach der Schmelzerstarrung aufgefahren werden, um die Gussteile entnehmen zu können.
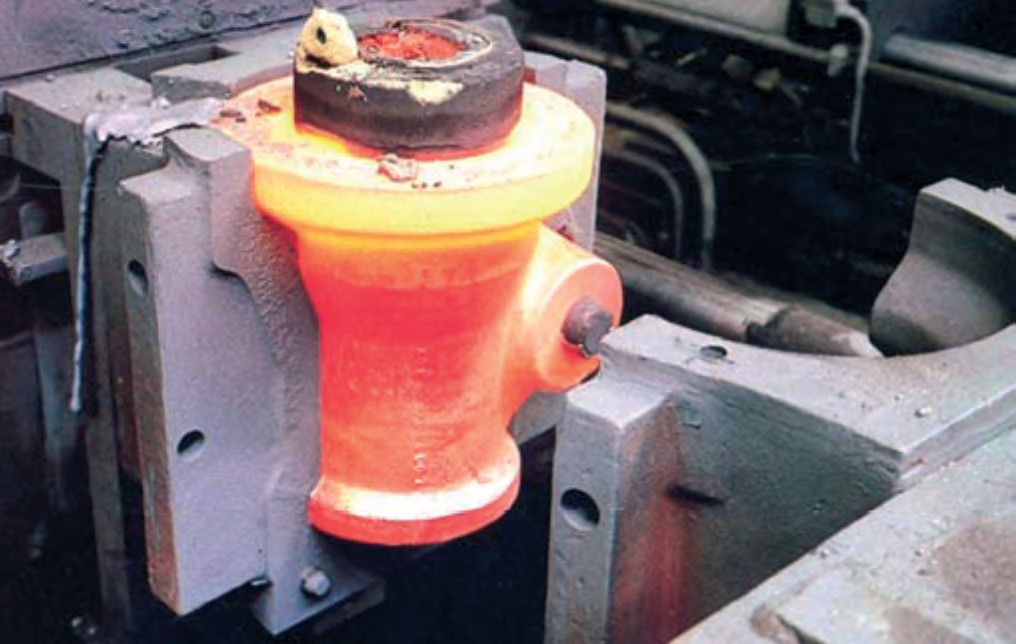