Handformguss
Gute Handarbeit bei heißen Metallen
Du fragst dich sicherlich, wie Handarbeit und heiße Metalle zusammenpassen. Hand auf, Metall rein? Natürlich nicht!!! Das flüssige Metall ist viel zu heiß und würde die Hand erheblich verletzen. Die Form, also der Hohlraum, in den das flüssige Metall gegossen wird, ist Handarbeit. Daher HANDFORMguss. War doch klar, sagst du? Na gut, da hast du wohl recht, aber trotzdem gucken wir uns das Verfahren mal im Detail an. Hierzu haben wir die Edelstahlwerke Schmees in Langenfeld und zwei ihrer Azubis besucht.
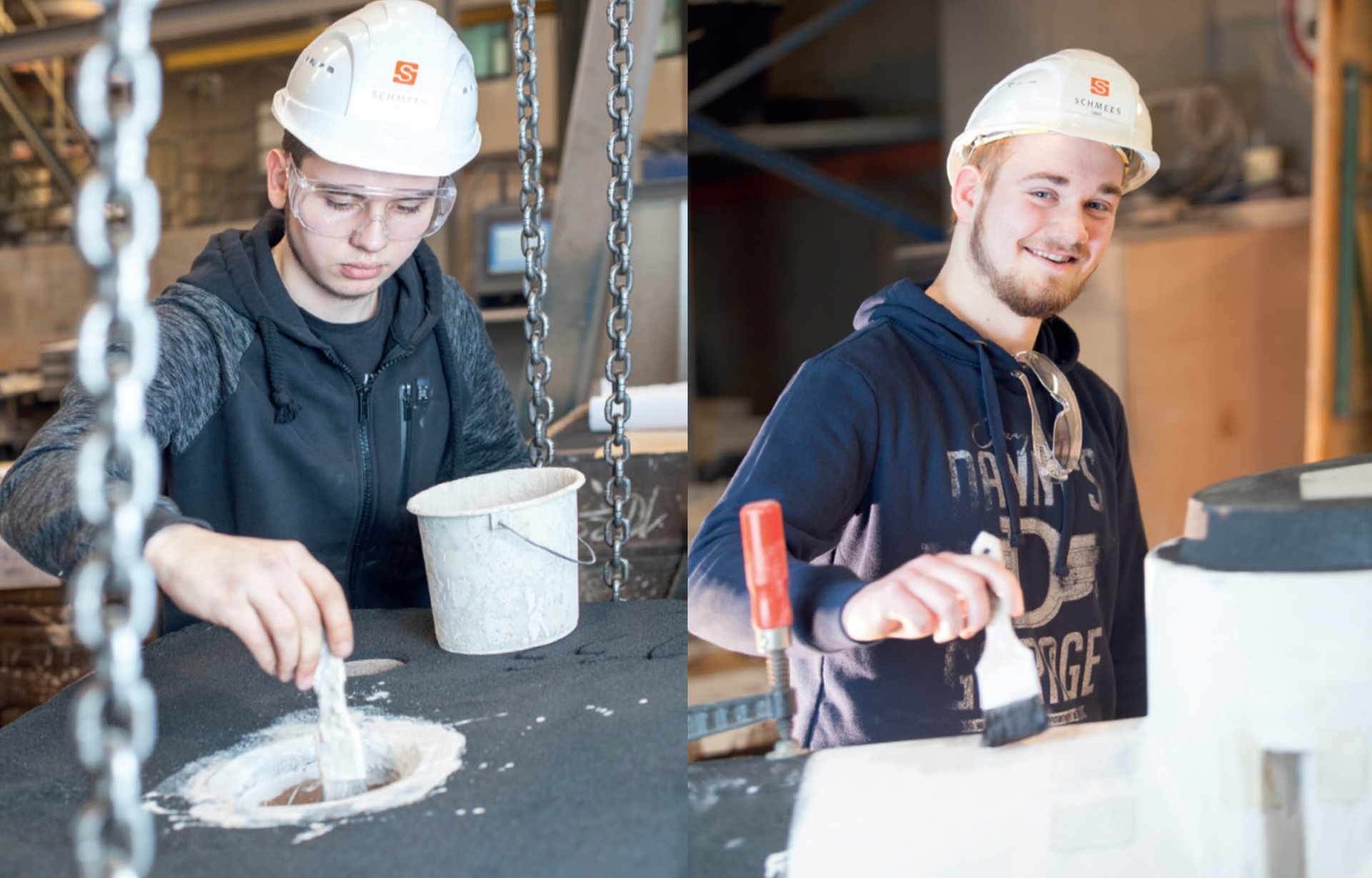
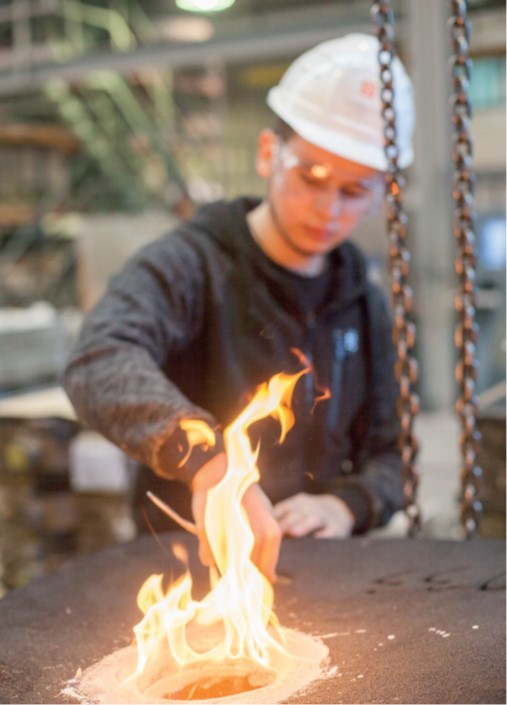
Das Verfahren wird hauptsächlich für die Herstellung von Großgussteilen, wie z. B. Windradnaben mit einem Durchmesser von teils über 3 Meter oder Maschinenbetten, die über 50 Tonnen wiegen können, sowie Kleinserien und die Einzelteilfertigung, für z. B. Statuen oder Sonderbauteile, eingesetzt.
Für die Herstellung der Form werden unterschiedliche Dinge benötigt. Ein Modell, ein Formkasten und der Formstoff. Und wenn das Gussteil innere Konturen hat, wie Kanäle für Flüssigkeiten, dann benötigen wir auch noch einen Kernkasten und Formstoff für den Kern.
Das Wichtigste ist wahrscheinlich der Formstoff selbst. Der Formstoff ist das Material, aus dem die Form entsteht, ähnlich wie das Kunststoffförmchen das im Sandkasten unseren Burgen ihre Form gegeben hat.
So werden die Formen, die dem Metall ihre spätere Form geben sollen, aus einem Sand-Binder-Gemisch mit weiteren Zusätzen hergestellt. Ja, es ist in der Regel der Sand, den jeder kennt, der gelbliche Quarzsand, der oft in Sandgruben abgebaut wird. Nur eben für das Handformen aufbereitet.
In den Gießereien wird dieser Sand dann mit dem Binder in großen Mischern vermengt und für die Formherstellung bereitgestellt.
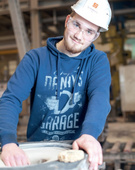
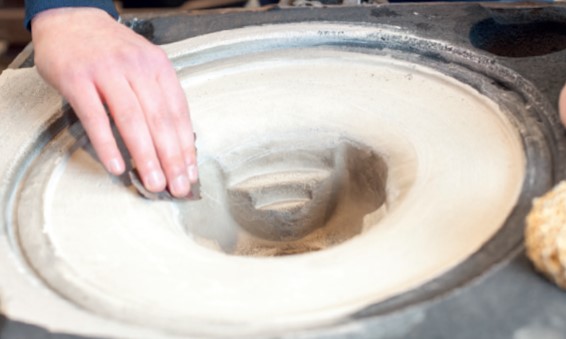
Der Binder ist eine Art „Klebstoff“ der eingesetzt wird, damit der Sand während des gesamten Gießvorgangs seine Kontur stabil hält. Es gibt zwei verschiedene Arten von Bindern:
Zum einen kann ein Ton benutzt werden, der in Zusammenspiel mit Wasser seine Klebwirkung erzeugt, die die Form zusammenhält. Solche Formstoffe werden üblicherweise für die maschinelle Produktion und kleine Gussteile im Handformguss genutzt.
Zum anderen können Harze als „Klebstoff“ genutzt werden. In der Regel sind es zwei Komponenten, die zusammen mit dem Sand vermischt werden, sogenannter Kaltharzsand. Durch das Vermischen reagieren diese miteinander und werden nach einer gewissen Zeit fest. Zwischen Mischen und der Verfestigung muss der Formstoff genutzt werden. Hier ist Schnelligkeit gefragt. Ist die Mischung fertig, muss der Sand schnell in die Form und verarbeitet werden, bevor er aushärtet. Das dauert je nach Mischung nicht sehr lange.
Für die Formherstellung benötigen wir außerdem noch ein Modell. Hierbei gibt es unterschiedliche Möglichkeiten. Sie kann bspw. für den einmaligen Gebrauch sein und wird dann einfach aus Styropor erstellt. Das Modell wird anschließend mit Formstoff umhüllt und durch das heiße, flüssige Metall zerstört, wobei aber der Sand immer noch die benötigte Form hat und so dem Gussteil sein Aussehen verpasst. Dieses Verfahren nennt sich dann Lost-Foam. Die andere Möglichkeit ist ein Dauermodell aus Holz, Kunststoff oder Metall. Dieses wird ebenfalls mit Formstoff umhüllt, jedoch vor dem Abguss vorsichtig aus der Form entfernt. Hierbei muss der Formstoff deutlich stabiler sein. Weil die Modelle entfernt werden müssen, werden die Formen manchmal mehrteilig erstellt und anschließend zu einer Gesamtform zusammengesetzt.
Egal um welche Art von Modell es sich handelt, es hat die Kontur des späteren Gussteils, jedoch mit ein paar Änderungen. Als Erstes: es ist größer. Wenn du dich fragst warum, das ist ganz einfach erklärt. Warme Dinge werden beim Abkühlen immer kleiner und da das flüssige Metall, wenn es zum Beispiel Gusseisen ist, eine Temperatur von über 1300 °C hat, kannst du dir sicherlich vorstellen, dass es bei Raumtemperatur etwas kleiner ist. Was für weitere Änderungen gibt es im Vergleich zwischen späterem Gussteil und Modell? Das Modell beinhaltet noch das sogenannte Gießsystem, was du dir als den Kanal vorstellen kannst, durch den das Metall seinen Weg in die Form findet.
Kommen wir zum Formkasten. Das ist eine Art Rahmen, der alles während des gesamten Gießvorgangs zusammenhält und gleichzeitig die Menge an Formstoff für das Gussteil begrenzt. Diese Rahmen müssen in ihrer Größe passend zum Gussteil ausgewählt werden und sind in aller Regel aus Eisen oder Stahl.
Dann haben wir ja alle Materialien zusammen und die Form kann gebaut werden. Das Modell wird mit einer Schicht Formstoff bedeckt und der wird dann wiederum verdichtet. Das Verdichten geschieht entweder mit Stampfern als Werkzeug oder per Hand. Der ganze Formkasten muss nach und nach gefüllt und verdichtet werden. Dabei darf nicht getrödelt werden, denn ansonsten haftet der Formstoff nicht richtig und die Form ist nicht verwendbar. Bei großen Formen, für richtig schwere Teile kann der Formenbau mehrere Stunden oder – bei extrem großen Gussstücken – auch schon einmal Tage in Anspruch nehmen.
Wenn dann die Form fertig ist, kommen wir zum Gießen. Das Metall wird während des Formenbaus geschmolzen und legiert. Sobald die Schmelze fertig ist, kann abgegossen werden. Die per Hand hergestellte Form wird mit dem flüssigen Metall gefüllt. Dann heißt es warten, bis das Metall vollständig erstarrt und abgekühlt ist. Je nach Größe des Gussteils kann das von ein paar Stunden bis hin zu mehreren Tagen dauern.
Abschließend muss das erkaltete Gussteil aus der Form genommen und gesäubert werden. Dabei wird die Form zerstört, für das nächste Gussteil muss also eine neue Form hergestellt werden. Dann wird das Gießsystem vom beinahe fertigen Gussstück entfernt, es gehört ja schließlich nicht zum eigentlichen Teil. Anschließend kann das Gussteil in der mechanischen Bearbeitung nachbearbeitet werden. Das war’s. So funktioniert Handformguss.