Kokillenguss
Was ist das?
Die Firma Krause Präzisions-Kokillenguss GmbH sitzt im mittelfränkischen Pappenheim und ist eine Gießerei für Messingbauteile. Was hier so tagtäglich - hinter normalerweise verschlossenen Türen - produziert wird, sind Bauteile die mit einer nicht alltäglichen Technologie hergestellt werden: dem Kokillengießverfahren.
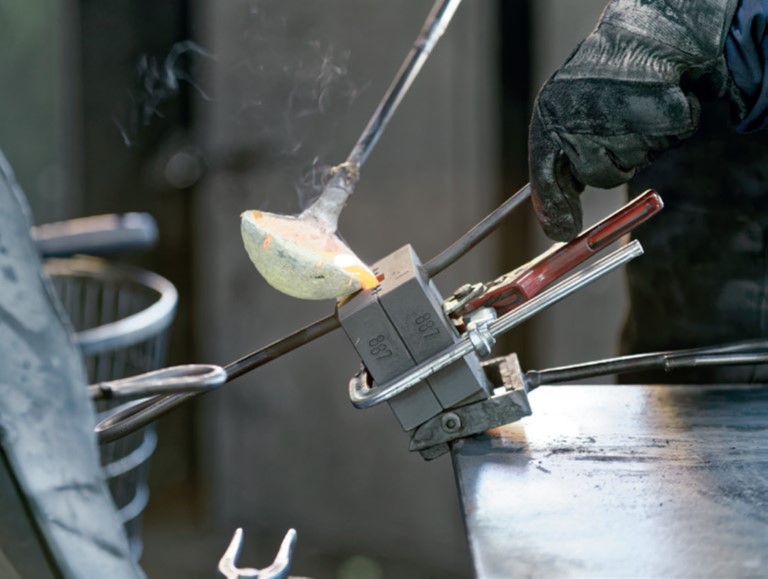
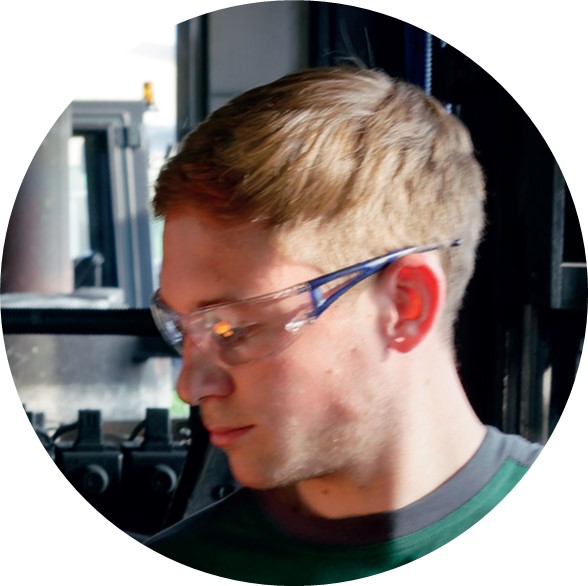
Eine Kokille ist eine Dauerform aus hoch temperaturbeständigem Stahl, welche mit flüssigem Metall und bei Krause Guss nur mithilfe der Schwerkraft befüllt wird. „Mit diesem Verfahren können wir Bauteile mit einem Gewicht von 2 g–15 kg und einer Wandstärke ab 2,5 mm herstellen“, sagt Sebastian Ludwig, der Ausbildungsleiter.
Tim macht eine Ausbildung zum Gießereimechaniker und ist im 3. Lehrjahr. Wir begleiten ihn einen Tag lang und schauen uns an, welche Aufgaben er tagtäglich hat. Während der Ausbildung lernt er nämlich alle Arbeitsschritte, die notwendig sind, um ein Gussteil im Kokillengießverfahren herzustellen.
Der Tag fängt heute für Tim bereits um 4 Uhr in der Früh an. Für ihn steht die Produktion eines seewasserbeständigen Messingbauteils auf dem Plan, welches in der Schiffsindustrie zur Anwendung kommt.
„Heute sind es Schiffshaken, mit denen Rettungsboote oder Rettungskapseln an Kreuzfahrtschiffen oder Frachtern befestigt werden. Zu wissen, dass mein Bauteil seinen Teil dazu beiträgt im Notfall Menschen zu retten, ist eine tolle Sache“, sagt Tim begeistert.
Als Erstes steht für Tim das Vorbereiten der Schmelzöfen auf dem Programm. Nachdem er die Elektro- und Ölöfen eingeschaltet hat, bereitet Tim eine Messing-Legierung vor, die normalerweise hauptsächlich aus Kupfer und Zink besteht, jedoch mischt Tim der Basislegierung noch Eisen, Aluminium und Silizium bei, um die Eigenschaften des Metalls zu verbessern. Zuerst stellt er mithilfe des Meisters die Eisenkupferplatten in den Tiegel, danach werden die Legierungsbestandteile Aluminium und Silizium zugemischt. Wenn alles flüssig ist, setzt Tim mit einer Legierstange das Zink ein. Die Legierstange ist ein gebogenes Rohr aus Eisen, mit dem die Zinkplatten in das bereits flüssige Kupfer geführt werden. Aufsteigender weißer Rauch bestätigt Tim die erfolgreiche Reaktion. Sobald alle Bestandteile im Ofen geschmolzen sind, vermengt Tim das Ganze wie in einem großen Suppentopf. Zum Schluss verteilt er ein Pulver auf die Schmelze und entfernt Verunreinigungen, die sogenannte Krätze, die sich auf der Oberfläche des flüssigen Metalls absetzt, mit einem Schäumer. So wird die Qualität des flüssigen Metalls verbessert.
Um sicherzustellen, dass das Metall den Anforderungen, denen es im späteren Einsatz ausgesetzt wird, auch gewachsen ist, muss Tim vor der weiteren Produktion des Bauteils das Messing mit bestimmten Untersuchungen überprüfen. Hierbei wird die genaue chemische Zusammensetzung mithilfe der sogenannten Spektralanalyse und der Verschleißwiderstand mithilfe der sogenannten Härteprüfung überprüft. Parallel dazu wird die Kokille des Bauteiles für den Abguss vorgeheizt. Das ist nötig, damit das einfließende Metall nicht zu schnell im kalten Stahl fest wird, sondern die Kontur der Kokille sauber annimmt. Erst wenn die Härteprüfung und Spektralanalyse die optimalen Ergebnisse zeigen, kann Tim die letzten Vorbereitungen für die Gussproduktion tätigen. Neben den Öfen stehen große Fässer, die mit einer Wasser-Graphitmischung gefüllt sind, die den Verschleiß der Kokille verhindert und zusätzlich eine bessere Gussoberfläche entstehen lässt. Nach dem Eintauchen - der Gießer spricht vom Schwärzen - der beiden Kokillenhälften, werden diese zusammengesetzt und mit Schnellverschlusszwingen befestigt. Damit Tim sich nicht mit dem heißen, flüssigen Metall verletzt, trägt er eine Schutzausrüstung, die aus Schutzbrille, Handschuhen, Schürze und Arbeitsschuhen besteht.
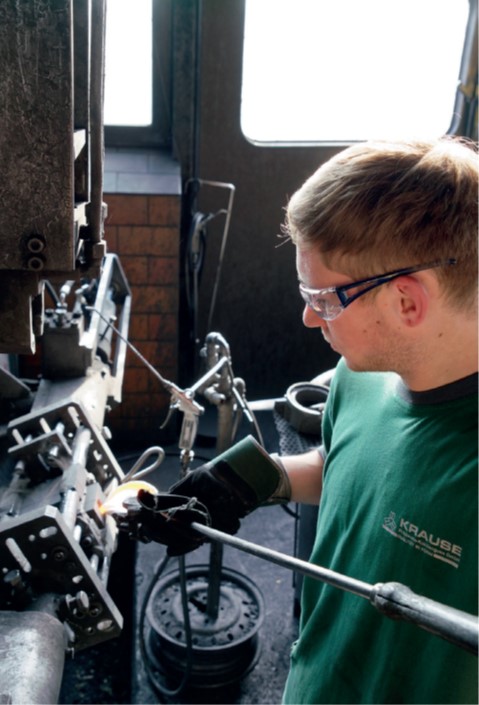
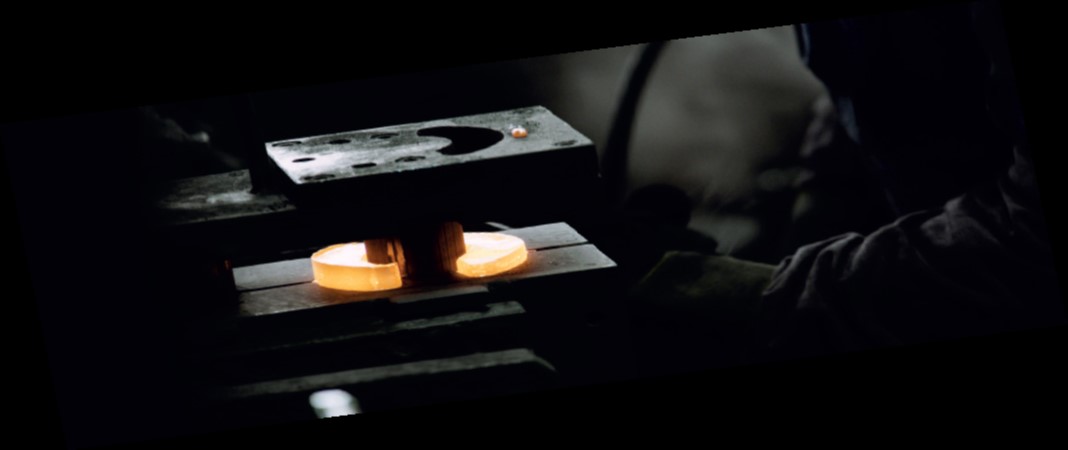
Nach Anbeugen der Kokille, was wie das Kippen eines Weizenbierglases beim Einschütten von Bier funktioniert, wird mit dem Gießlöffel das aus dem Ofen entnommene Metall in den Eingusskanal der Kokille gegossen. Die Schwerkraft lässt den Hohlraum in der Kokille mit dem Material ausfließen.
Das flüssige und heiße Metall kühlt dann sehr schnell ab und entwickelt eine Grundfestigkeit, sodass Tim, direkt nach dem Befüllen, die Zwingen entfernen und das Bauteil entformen kann. Bereits jetzt findet die erste wichtige Qualitätskontrolle des fertigen Gussteils statt: Tim checkt per Sichtprüfung, ob das Gussteil so aussieht, wie es soll und keine Gussfehler aufweist.
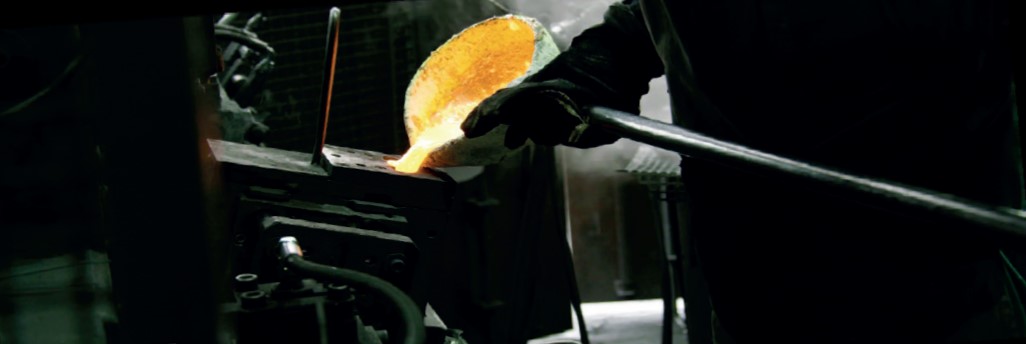
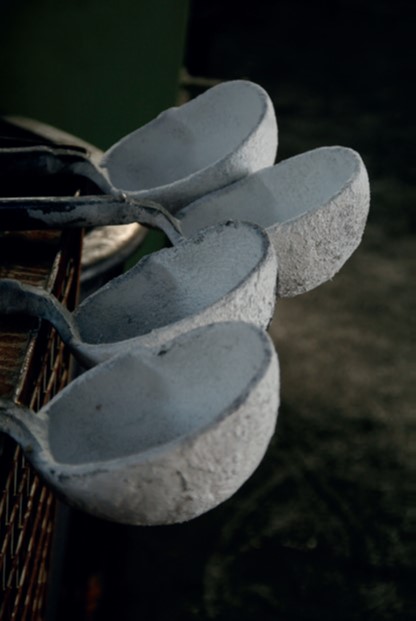
Sein Ausbildungsleiter ist mit Tims Arbeit zufrieden. „Für das Kokillengießen braucht man Fingerspitzengefühl. In welchem Winkel beugt man die Kokille an? Wie setzt man den Gießlöffel an? Wie und in welchem Tempo lässt man das flüssige Metall einfließen? Es sind viele Sachen, auf die man gleichzeitig achtgeben muss. Das macht den Job anspruchsvoll und abwechslungsreich!“
Jedes Bauteil ist anders“, sagt Tim, „das fasziniert mich. Es gibt so viele verschiedene Branchen für die wir produzieren und wo unsere Bauteile eingesetzt werden. Neben der Schiffsindustrie produzieren wir auch für die Medizintechnik, den Pumpenbau, die Lebensmittelindustrie und viele mehr. Langeweile kommt so nie auf.“
Krause Guss setzt für die Zukunft auf top ausgebildeten Fachkräftenachwuchs wie Tim und unterstützt und fördert die Auszubildenden wo es nur geht!
Deine Chance
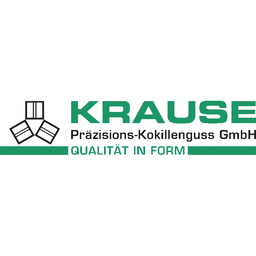
Das klingt spannend? Dann schau doch direkt mal in unserer Ausbildungsbörse oder auf der Website von KRAUSE GUSS vorbei.
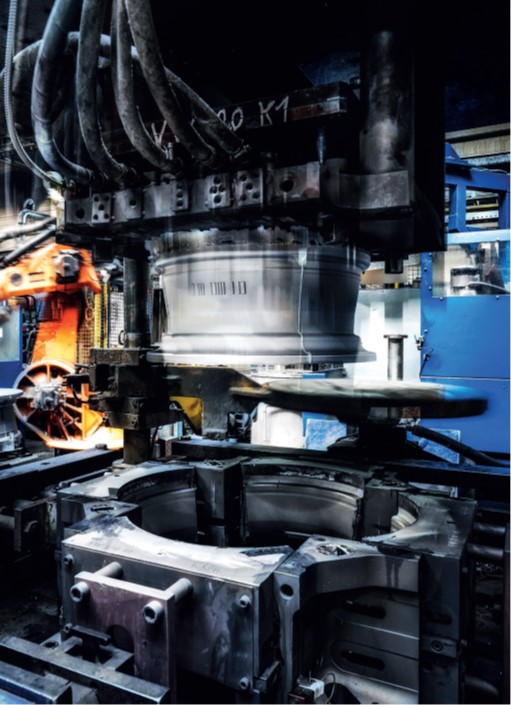
Hightech-Felgen von Borbet sind für jedes Auto ein Hingucker.