Magnesium-Schmelztechnologie: Nachhaltige, qualitative Schutzgasregelung
Von Niklas Schwenke und Martin Fehlbier, Kassel
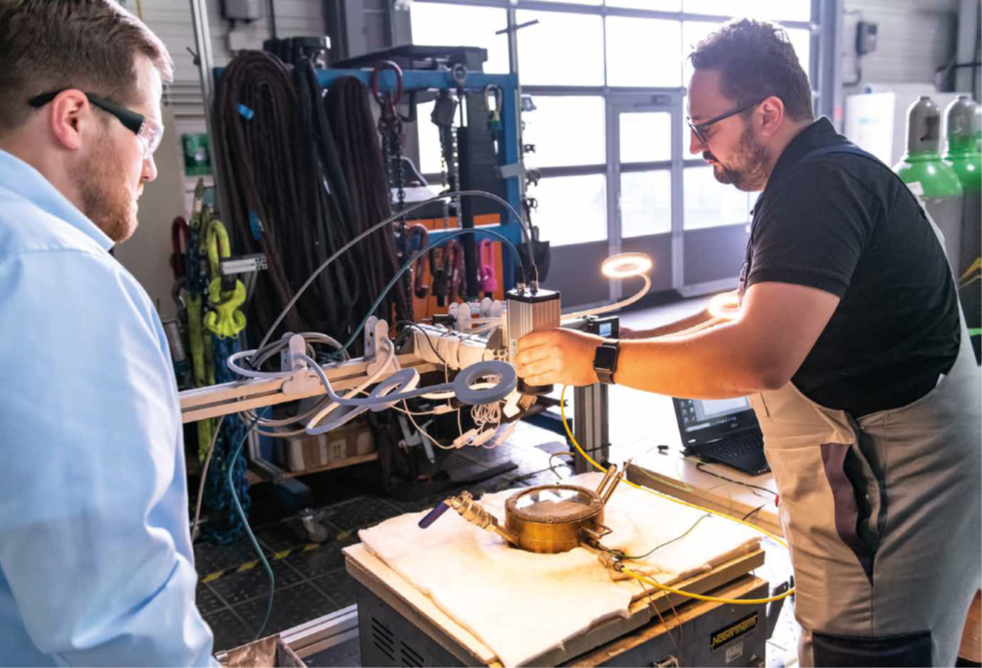
Das Fachgebiet Gießereitechnik (GTK) der Universität Kassel entwickelt Prototypen zur automatisierten Schutzgas-Regelung in Magnesium-Schmelzöfen.
Erschienen in GIESSEREI 03/2021
Über 90 % der Magnesiumlegierungen werden im äußerst wirtschaftlichen und produktiven Druckgießverfahren verarbeitet [5]. Das breite Anwendungsspektrum von Magnesiumlegierungen reicht vom klassischen Fahrzeugbau über die Herstellung ultraleichter elektrischer Handmaschinen bis zur Umsetzung urbaner E-Mobilitäts-Konzepte (Bild 1).
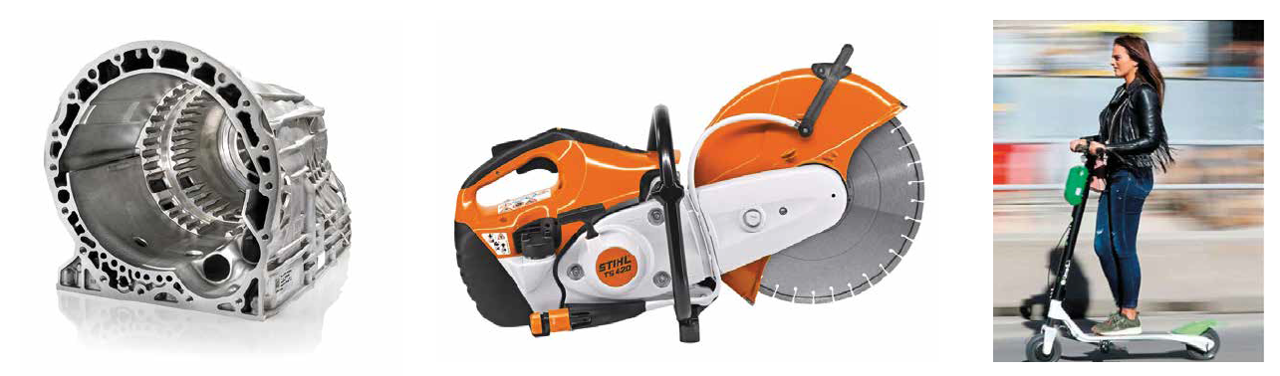
Die Gewichtsersparnis ermöglicht einen geringeren Kraftstoffverbrauch und somit einen reduzierten Schadstoffausstoß klassischer Verbrennungsmotoren, ein verbessertes Handling bei gleichzeitig hochwertiger Haptik und hoher Langlebigkeit von elektrischen Handmaschinen sowie eine erhöhte Reichweite bzw. Reduktion der Batteriekapazität urbaner E-Mobilitätskonzepte.
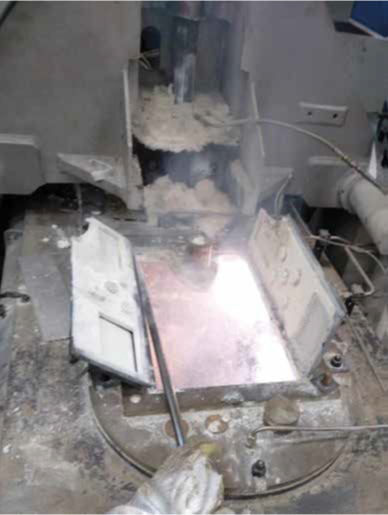
einer nicht bemerkten fehlerhaften Schutzgaszufuhr.
Eine Herausforderung bei der Anwendung von Magnesium als Gusswerkstoff ist die Gefahr des Magnesiumbrandes im flüssigen Zustand (Bild 2), weshalb toxische oder umweltschädliche Schutzgase bislang manuell, d.h. erfahrungsbasiert und daher häufi g fehlerhaft dosiert, eingesetzt werden
Nach dem Verbot von Schwefelhexafl uorid durch die EU-Verordnung Nr. 517/2014 zur Reduktion fl uorierter Treibhausgase stehen der Magnesium-Gießereibranche lediglich R134a, SO2 und Novec-612 zur Verfügung (Tabelle 1), wobei letzteres aufgrund des hohen Verbrauchs an Trägergas, der Anlagen- und Patentkosten sowie dessen starken korrosiven Eigenschaften bislang keinen industriellen Einsatz fi ndet [6].
Tabelle 1: Übersicht der derzeit einsetzbaren Reaktivgase nach dem Verbot von SF6 [11-14]
Tetrafluorethan (R134a – C2H2F4) | Schwefeldioxid (SO2) | Novec™ 612 (CF3CF2C(O)CF(CF3)2) | |
Schützende Wirkung durch | MgF2-Schicht | MgSO4-, MgS- und MgO-Phasen | MgF2-Schicht |
Arbeitsplatzgrenzwert / Treibhauspotenzial | 1000 ppm/1430 GWP (Herstellung: 3,34 GWP) | 1 ppm/1 GWP | 150 ppm/1 GWP |
Eigenschaften | umweltschädlich, Preisanstieg z.T. korrosiv | toxisch z.T. korrosiv | sehr hohe Kosten stark korrosiv |
Projektziel & Konzept
Primäres Ziel des AIF-IGF-Projekts „InPro-Gas“ war es, ein System zu entwickeln, das anhand der Gaskonzentrationen innerhalb eines Magnesiumschmelzofens den optimalen Volumenstrom an Schutzgas (in diesem Projekt R134a und N2) automatisch und vom Bediener unabhängig einstellt und somit fehlerhafte Dosierungen vermeidet. Kritische Situationen, die zum Magnesiumbrand führen könnten, Schmelzeparameter innerhalb und außerhalb des Ofens, in der Umgebung des Bedieners sowie an korrodierten Kühlleitungen gemessen. Auf diese Weise soll der Betrieb von Magnesiumschmelzanlagen sicherer und effizienter gemacht und Anwendungshürden für klein- und mittelständische Unternehmen (KMU) im Bereich der Magnesiumschmelztechnologie reduziert werden. Dazu wurden zahlreiche Messungen der Sauerstoff-, Kohlenstoffmonoxid-, Kohlenstoffdioxid-, Stickstoffmonoxidsowie Stickstoffdioxidgehalte (O2, CO, CO2, NO, NO2) in Magnesiumschmelzanlagen bei unterschiedlichen Betriebs- und Schutzbegasungseinstellungen durchgeführt. Anhand der Messergebnisse wurde ein Prototyp eines Schutzgasregel- sowie Brandfrühwarnsystems für den Einsatz in der Magnesiumschmelztechnologie entwickelt und in den Schmelzprozess einer Frech-DAM-500FWarmkammerdruckgießzelle (580 t Schließkraft, 520kg AZ91 Schmelzeinhalt) integriert. Das System überwacht dauerhaft die Konzentrationen der genannten Gase in der Atmosphäre zwischen dem Ofendeckel und der Schmelzbadoberfläche und gleicht diese mit in Schmelzversuchen ermittelten Sollwerten ab. Anhand der Abweichung zwischen Ist- und Sollwert wird der Volumenstrom des eingebrachten Schutzgases erhöht oder verringert, bis ein Optimum erreicht ist. So lassen sich eine ggf. umwelt- und gesundheitsschädliche Überbegasung des Magnesiumofens sowie das Austreten des korrosiven oder giftigen Schutzgases verhindern. Ausfallende, verstopfte oder anderweitig beschädigte Schutzgaszuführungen können innerhalb von wenigen Sekunden, vor Einsetzen der Magnesiumoxidation, detektiert und signalisiert werden. Das System leitet selbstständig Gegenmaßnahmen ein, warnt das Bedienpersonal aber dennoch durch optische und akustische Signale. Sollte es zu einer Rauchbildung innerhalb des Ofens, z. B. aufgrund verschlissener Tiegeldeckel, Undichtigkeiten, zu hoher Schmelztemperaturen oder eines zu geringen Schutzgasvolumenstroms kommen, wird dies durch die Messung der Verbrennungsgase CO, CO2, NO und NO2 detektiert. Infolge dessen werden automatisierte Gegenmaßnahmen, je nach Rauchbildung in Form einer erhöhten oder einer Notbegasung eingeleitet. Dies soll die Gefahr starker Oxidation bis hin zu Magnesiumbränden in Magnesiumschmelzprozessen reduzieren, die Ressourceneffizienz erhöhen sowie die Schutzgaskosten senken. Somit kann ein Beitrag zur Nachhaltigkeit und zum weiteren Abbau von Anwendungshürden für KMU zum Einsatz von Magnesium aufgrund stetig steigender Anforderungen an die Prozess- und Arbeitssicherheit sowie sich allgemein verschärfender Emissionsrichtlinien geleistet werden. Bild 3 stellt die Einbettung des Magnesiumschmelzofens und der Schutzgasmischstation in ein gesamtheitliches System dar.
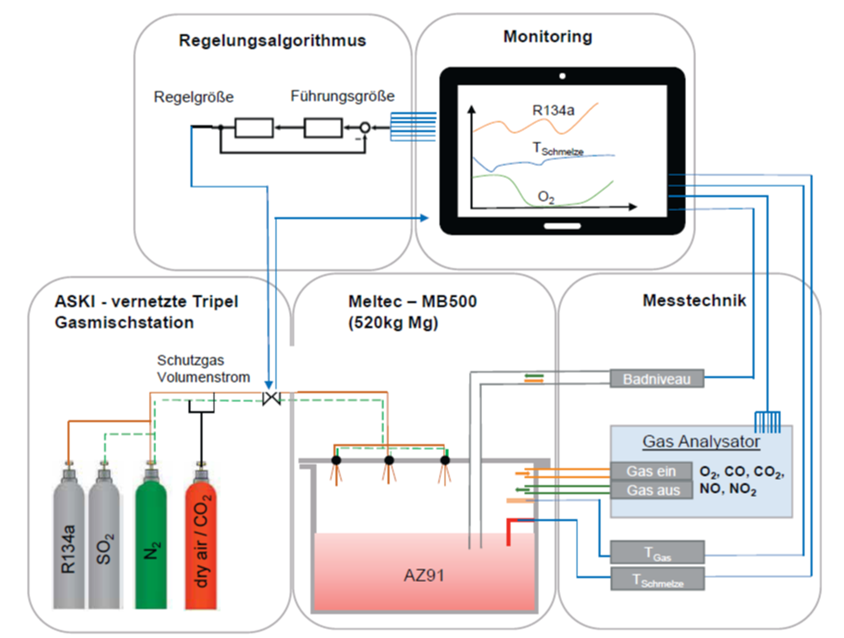
Messungen in Labor- und Industrieschmelzöfen
Zunächst wurden in Schmelzversuchen an einem elektrisch widerstandsbeheizten Laborofen der Firma Nabertherm GmbH in einem nickelfreien Edelstahltiegel 7 kg AZ91-Magnesiumlegierung geschmolzen. Bei variierten Schmelzetemperaturen und Schutzgaseinstellungen wurden jeweils die Gaskonzentrationen sowie die Schmelze- und Gastemperaturen aufgezeichnet. Die Vorversuche wurden mit einem Schutzgasgemisch von 99,8 Vol.-% N2 und 0,2 Vol.-% R134a durchgeführt. In Extremfalluntersuchungen wurde die Schutzgaszufuhr von 15 l / h bis auf ein Minimum von 0 l / h reduziert und eine Rauchbildung provoziert. Aufgrund des geringen Tiegelvolumens wurde eine druckneutrale Gasrückführung entwickelt, die das angesaugte und analysierte Gas zurück in den Tiegel leitet, um eine Verfälschung aufgrund des kleinen Volumens zu verhindern. Diese Vorversuche dienten zum einen der Verifizierung der These, dass sich anhand der Gaskonzentrationen in der Gasphase oberhalb der Schmelze eine Aussage über den Zustand der Schmelzbadoberfläche treffen lässt. Zum anderen sollten die Messbereiche sowie die für die Regelung und das Brandfrühwarnsystem relevanten Gase, deren Konzentrationen und Bildungsgeschwindigkeiten ermittelt werden. Bild 4 zeigt die Schmelzbadoberfläche bei einer Metalltemperatur von 630 °C und die Rauchgasbildung bei Abstellen der Schutzgasversorgung. Es ist zu erkennen, dass die vermehrte Bildung der Stickoxide NO und NO2, bzw. der summierte Wert NOx, bereits bei der Reduktion des Volumenstroms von 15 auf 10 l / h zu messen ist und damit deutlich vor der Entstehung einer Rauchbildung im Tiegel und einem Austreten des Rauchs aus dem Ofen zu detektieren ist. Das Frühwarnsystem könnte somit deutlich früher alarmieren und Gegenmaßnahmen einleiten, als der Anlagenbediener die Rauchbildung bemerken kann.
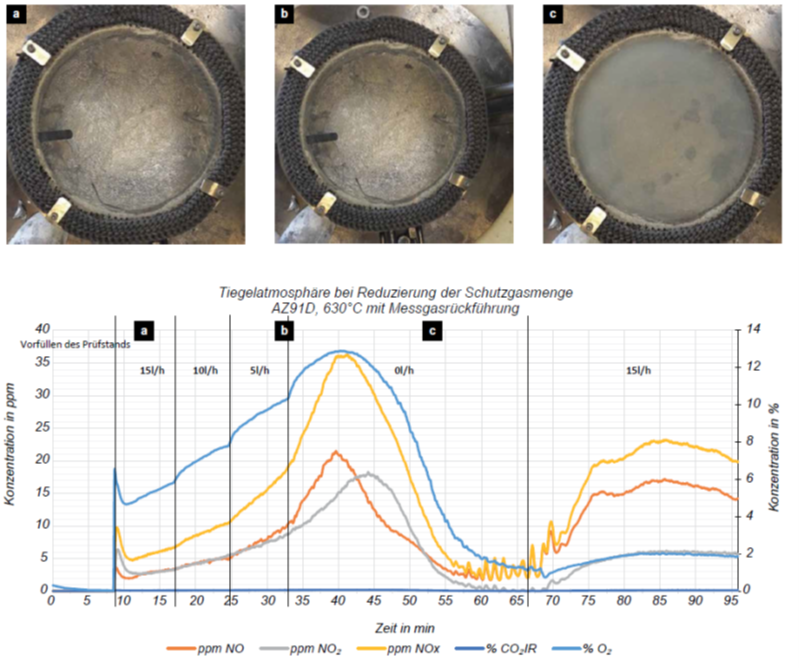
bei einer Reduktion der Schutzbegasung steigen und eine Rauchbildung innerhalb eines Ofens somit frühzeitig erkennbar wäre.
In zahlreichen Schmelzversuchen am MB-500-Schmelz- und Warmhalteofen der Frech-DAM-500F (Bild 5) des Fachgebiets Gießereitechnik GTK der Universität Kassel wurden für diverse Parametervariationen die Gaskonzentrationen innerhalb des Ofens gemessen.
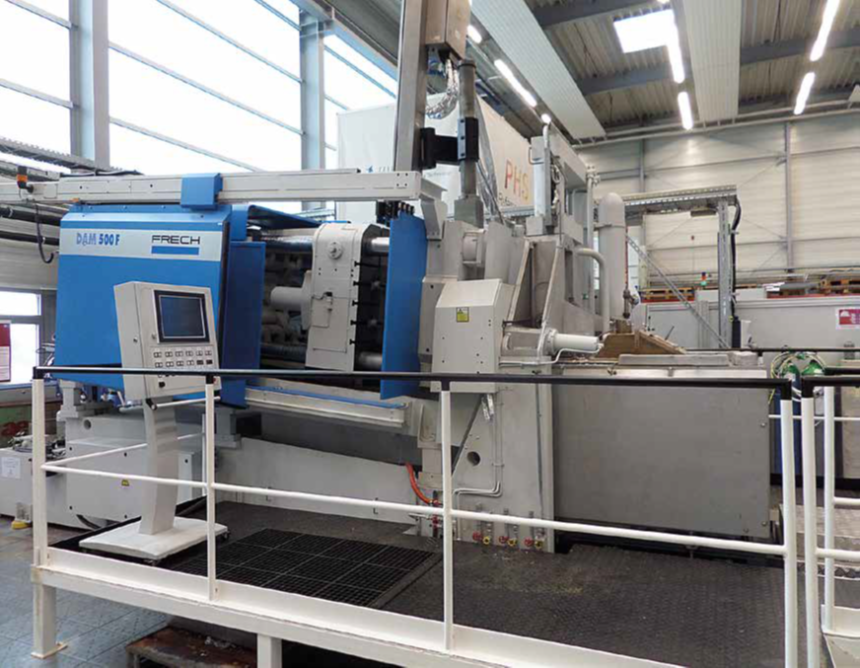
Der Tiegelinhalt lag bei 520 kg Magnesiumlegierung AZ91 und die standardmäßige Schutzbegasung, bestehend aus 99,8 Vol.-% N2 und 0,2 Vol.-% R134a, bei 450 l / h. Daraus wurden Sollwerte für bestimmte Ofeneinstellungen abgeleitet. Bild 6 zeigt die Auswertung einer Versuchsreihe für schrittweise reduzierte Schutzgasmengen, ebenfalls mit der Schutzgaszusammensetzung 99,8 Vol.-% N2 und 0,2 Vol.-% R134a.
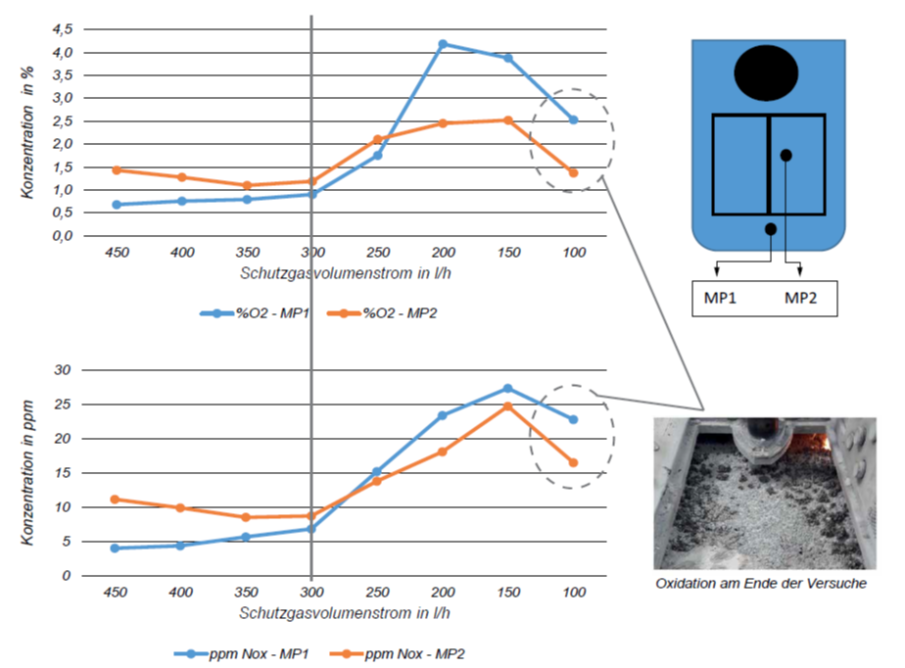
Gemessen wurde an zwei unterschiedlichen Stellen des Warmkammerofens. Die Messposition 1 (MP1) befindet sich im vorderen Bereich des Ofens in der Nähe des Bedieners und die Messposition 2 (MP 2) mittig über dem Ofen. Innerhalb des Projekts wurden mehrere Positionen ausgewertet, um lokale Unterschiede innerhalb des Ofens festzustellen. Es ist zu erkennen, dass es sich solange um ein eingeschwungenes System handelt, bis der Volumenstrom eine Grenze unterschreitet. Diese liegt bei einer Metalltemperatur von 620 °C bei etwa 300 l / h, unterhalb konnte ein verstärktes Oxidwachstum festgestellt werden.
Weitere Messreihen zur Untersuchung der Auswirkungen unterschiedlicher Reaktivgaskonzentrationen ergaben, dass erhöhte Reaktivgasanteile zu verstärkter Bildung von Kohlenstoffmonoxid und -dioxid führen. Für Konzentrationen oberhalb von 0,5 Vol.-% R134a konnte bis zu einem Volumenstrom von 250 l / h keine Rauchgasbildung festgestellt werden (Bild 7), allerdings stiegen die Konzentrationen von CO und CO2 deutlich an. Diese Art der Überdosierung kann die Schmelze zwar vor Oxidation schützen, führt aber zu erhöhten Korrosionserscheinungen, stark erhöhten Begasungskosten und zu gefährlich erhöhten Kohlenstoffmonoxidgehalten. Die Messung der Flusssäurekonzentration innerhalb des Tiegels ergab, dass für alle Begasungsvarianten, mit Ausnahme der Begasung mit 0,1-Vol.-% R134a, Flusssäuregahlte von > 90 ppm erreicht wurden. Dies war die Grenze des messbaren Bereichs der verwendeten Dräger-Kurzzeitröhrchen. Parallele Messungen in direkter Ofenumgebung und im Arbeitsbereich des Bedieners ergaben bei keiner Parametereinstellung messbare Gehalte an Flusssäure.
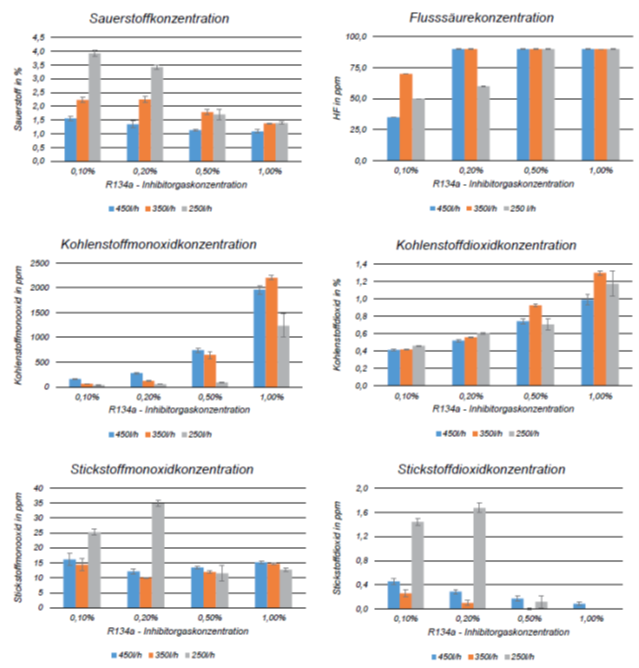
Der Prototyp
Auf Basis der Messergebnisse wurde ein Prototyp des Überwachungssystems entwickelt, bestehend aus:
- einer zentralen Messeinheit, welche die Gasgehalte (O2, CO, CO2, NO, NO2), die Gastemperatur und den Druck im Schmelzofen mit einer Messfrequenz von 1 Hz überwacht,
- einem Analogausgangsmodul zur Weitergabe der Analogsingale,
- einem Schaltschrank mit integriertem Bedienpanel, Signalleuchten und –hupen,
- einer SPS zur Bedienung, Verarbeitung und Anzeige der Messignale sowie zur Ermittlung des optimalen Schutzgasvolumenstroms.
Der Prototyp (Bild 8) ist über eine Ethernet-Schnittstelle direkt mit einer industriellen Schutzgasmischstation der Firma ASKI Gastechnik GmbH verbunden und gibt dieser automatisiert den für den überwachten Kreis notwendigen Volumenstrom vor.
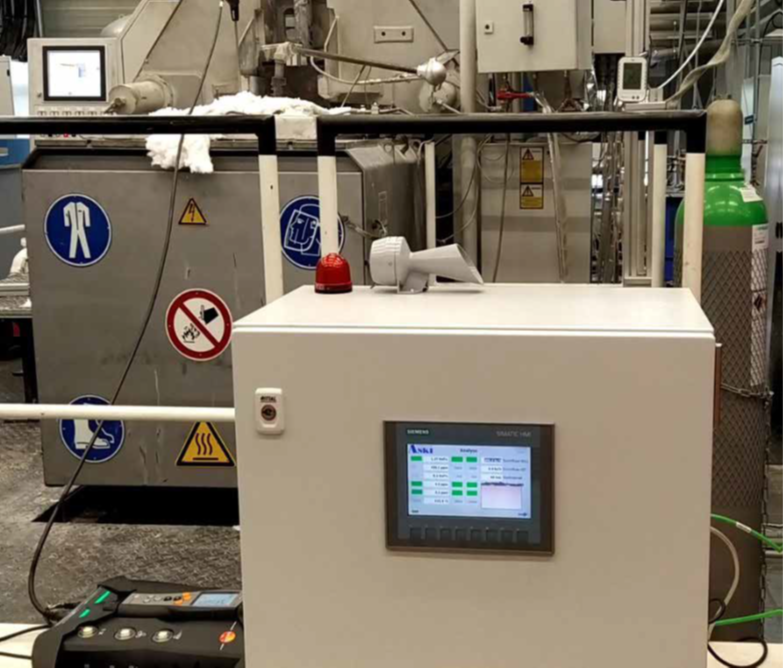
Schutzgasregelsystems mit angeschlossenem Gasanalysegerät Testo-350 während des Schmelzbetriebs an einem Magnesium-Schmelzofen einer Frech-Warmkammer DAM-500F.
Die Gaskonzentrationen und die Gastemperatur werden dabei in Echtzeit auf der Bildschirmseite A1 dargestellt. Mittels eines Touchpanels können die verschiedenen Gase einzeln oder parallel auf der Seite A2 als Regelparameter angewählt werden. Wird ein Gas als Regelparameter gewählt, müssen untere und obere Grenzwerte definiert werden. Auf weiteren Bildschirmseiten können die Grenzwerte für eine Signalgebung, bzw. Alarmierung, für die Schrittweite (Volumenstromanpassung) sowie für das Anpassungsintervall eingegeben werden. Die Einbindung dieses offenen Systems in eine fremde industrielle Magnesiumschmelzanlage ist in Kooperation mit dem Hersteller der Schutzgasmischstation mit nur geringem Aufwand möglich.
Anwendung und Ergebnisse
Die Funktion des Prototyps wurde in unterschiedlichen Schmelzversuchen untersucht. Bild 9 zeigt einen beispielhaften Betrieb bei einer geforderten Schutzgaseinsparung von 10 %. Als Regelparameter wurden ein Sauerstoffgehalt von 1,5 Vol.-% und jeweils maximal 15 ppm NO bzw. NO2 eingestellt. Es ist zu erkennen, dass das System bei der Starteinstellung von 450 l / h zunächst den Volumenstrom erhöht und es zu einem Überschwingen kommt. Innerhalb weniger Minuten pendelt sich der Schutzgasvolumenstrom bei durchschnittlich 400 l / h ein und der Sauerstoffgehalt von 1,5 Vol.-% wird über die gesamte Messdauer gehalten. Die im Projekt geforderte Einsparung von 10 % (45 l / h) kann mit den dargestellten Einstellungen erreicht werden, ohne dass mit zusätzlicher Oxidation zu rechnen ist. Versuche mit weiteren Parametereinstellungen haben gezeigt, dass höhere Schutzgaseinsparungen möglich sind, teilweise aber mit zusätzlicher Oxidation einher gehen. Dies hängt maßgeblich von der Dichte des Tiegeldeckels, der gewählten Schmelzetemperatur und der Betriebsart des Ofens ab.
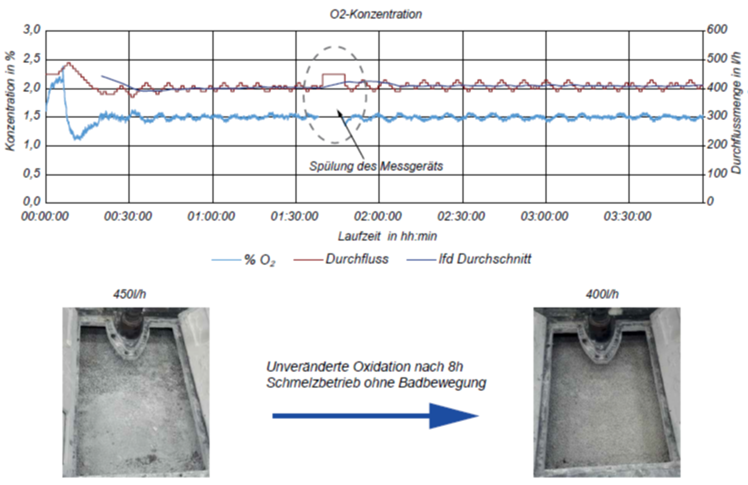
Schmelzofen. Der Zielwert von 1,5 Vol.-% Sauerstoff wird nach einer kurzen Einpendelzeit erreicht und konstant gehalten. Der Schutzgasverbrauch konnte um ca. 10 % gesenkt werden, ohne eine erhöhte Oxidation festzustellen.
Zu erwartende Kosten
Die Kosten des Prototyps belaufen sich derzeit auf ca. 12 500 Euro (9500 Euro Messgerät + 3000 Euro SPS, Schaltschrank und Bedienpanel). Da die SPS und die Schaltschrankanlage für mehrere Öfen nur einmal benötigt wird, wurde innerhalb des Projekts nach günstigeren Alternativen zum verwendeten Messgerät Testo-350 gesucht. Eine Möglichkeit zur günstigen Überwachung des Sauerstoffgehaltes in Magnesiumschmelzanlagen sind z. B. Heißgas-Sauerstoffsonden. Dies würde die Kosten auf ca. 1200 – 1500 Euro pro überwachten Ofen reduzieren. Allerdings ist die Güte des Brandsicherheitssystems dann auf die Messung des Sauerstoffgehaltes reduziert.
CO2-Bilanz
Über den Projektrahmen hinaus wurde die Thematik CO2-Footprint des Magnesium-Druckgießprozesses inklusive Schmelzbetrieb betrachtet. Hier sollen zunächst die Ergebnisse bezogen auf das im Projekt genutzte Reaktivgas R134a vorgestellt werden. R134a besitzt, wie bereits beschrieben, 1430 (kg CO2eq / kg R134a) (GWP). Davon entfallen nach Daten aus der Probas-Datenbank etwa 3,34 (kg CO2eq / kg R134a) auf die Herstellung des flüssigen R134a [15]. Nach Untersuchungen der United States Environmental Protection Agency zerfällt R134a in einem Kaltkammerofen mit einer Schmelzetemperatur von ca. 680 °C zu 98 % [16]. Berechnet man die Zerfallsprodukte eines Mols C2H2F4 (R134a) bei einer Temperatur von 550 °C mit der Software factsage der Firma GTT-Technologies, erhält man die im Bild 10 dargestellten Gase.
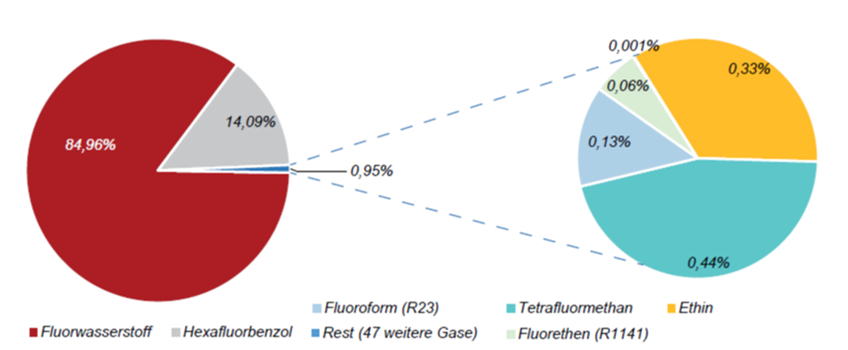
Wie die Messungen am Magnesiumschmelzofen nahelegen, zerfällt das Gas hauptsächlich in Flusssäure. Summiert man nun die einzelnen CO2-Äquivalente der Zerfallsprodukte erhält man 49,72 (kg CO2eq / kg R134azerfallen) anstelle von 1430 (kg CO2eq / kg R134a). Rechnet man dies nun auf eine Betriebswoche des Magnesiumschmelzofens bei einer Begasung von 450 l / h hoch und addiert das CO2-Äquivalent zur Herstellung von R134a (3,34 kgCO2eq / kgR134a) und des Trägergases Stickstoff (0,09 kg CO2eq / kg N2), welcher zuvor mit der Software Gabi berechnet wurde, so erhält man für eine Betriebswoche des Magnesiumschmelzofens ein CO2-Äquivalent von 31,95 (kg CO2eq / Betriebswoche). Bild 11 zeigt die Auswirkungen der CO2-Abschätzung, wenn man mit bzw. ohne das Zerfallen des Gases rechnet, sowie die CO2-Einsparungen für eine reduzierte Begasung (250 l / h).
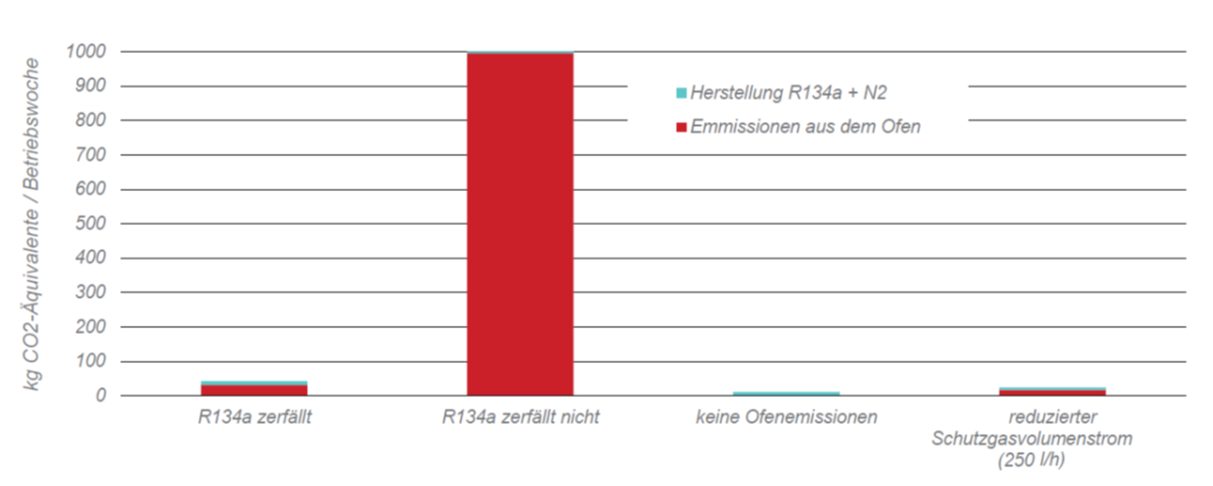
Das IGF-Vorhaben 19713N „Intelligent Protective Gas Control (InProGas)“ der Forschungsvereinigung Gießereitechnik e.V., Hansaallee 203, 40549 Düsseldorf, wurde über die AiF Arbeitsgemeinschaft industrieller Forschungsvereinigungen im Rahmen des Programms zur Förderung der industriellen Gemeinschaftsforschung und -entwicklung IGF vom Bundesministerium für Wirtschaft und Energie aufgrund eines Beschlusses des Deutschen Bundestages gefördert. Die Autoren bedanken sich hierfür sowie für die konstruktive Zusammenarbeit bei den Mitgliedern des Projektbegleitenden Ausschusses.
Dipl.-Ing. Niklas Schwenke, Gruppenleiter Magnesiumtechnologie und Prof. Dr.-Ing. Martin Fehlbier, Ordinarius, Fachgebiet Gießereitechnik (GTK), Universität Kassel
Literatur:
[1] Journal of Cleaner Production (2019), [Vol. 232], S. 1187-1194.
[2] Giesserei 105 (2018), [Nr. 01], S. 47.
[3] Schmitz, M.: Rohstoffrisikobewertung – Magnesium (Metall) – Deutsche Rohstoffagentur DERA Rohstoffinformationen, Berlin, S. 38-68, 2019, ISBN: 978-3-943566-69-7.
[4] Kroll, L.: Technologiefusion für multifunktionale Leichtbaustrukturen – Ressourceneffizienz durch die Schlüsseltechnologie Leichtbau, Springer-Verlag GmbH Deutschland, Berlin, S. 2-3, 2018, ISBN 978-3-662-54733-5.
[5] Bundesverband der Deutschen Gießerei-Industrie (BDG): „Die Gießerei-Industrie. Eine starke Branche in Zahlen.“, www.bdguss.de/branche/die-branche-in-zahlen/, abgerufen am 14.09.2020
[6] Verordnung (EU) Nr. 517/2014 Des Europäischen Parlaments und des Rates vom 16. April 2014 über fluorierte Treibhausgase und zur Aufhebung der Verordnung (EG) Nr. 842/2006, URL:https://eur-lex.europa.eu/legal-content/DE/TXT/PDF/?uri=CELEX:32014R0517&rid=1 (Stand: 14.09.2020).
[7] Albert Handtmann Metallgusswerk GmbH & Co. KG Homepage: URL: www.handtmann.de/leichtmetallguss/produkte/getriebebauteile (Stand:15.02.2021).
[8] Andreas Stihl AG & Co. KG: URL: www.euroguss.de/de/news/presseinformationen/in-magnesium-denkenckex7j9p86_pireport (Stand 14.09.2020).
[9] Innovations- und Wachstumspreis des Landes Hessen, Hessen-Champions 2019, Kategorie Weltmarktführer, castwerk, URL:https://www.hessen-champions.de/castwerk-gmbh-co-kg (Stand 14.09.2020).
[10] Hessische Niedersächsische Allgemeine: castwerk GmbH & Co. KG: Die Welt wird grüner – und castwerk macht mit, URL: www.hna.de/wirtschaft/castwerk-gmbh-welt-wird-gruener-castwerk-macht-pr-12952037.html (Stand:01.10.2020).
[11] Giesserei 95 (2008), [Nr. 08] S. 76–80.
[12] Thiele, K.: Preisexplosion beim Kältemittel R134a. Krafthand 3-4, 2018.
[13] Bundesanstalt für Arbeitsschutz und Arbeitsmedizin: Arbeitsplatzgrenzwerte. TRGS 900, S. 20, 2020.
[14] Bundesanstalt für Arbeitsschutz und Arbeitsmedizin: Tätigkeiten mit Gasen – Gefährdungsbeurteilung. TRGS 407, S.328-364, 2016.
[15] probas: „Prozessdetails: Chem-Org-R134a-DE-2000“, URL:https://www.probas.umweltbundesamt.de/, abgerufen am 11.11.2020.
[16] EPA – United States Enviromental Protection Agency: Characterization of Cover Gas Emissions from U.S. Magnesium Die Casting. 2004.