Energieeinsparung bei der Gussbauteilproduktion
Die Hauptabnehmer von Gussteilen, Automobilindustrie und Maschinenbauindustrie, setzen Impulse für die Gießereien und verlangen immer leichtere Gussteile bei gleichbleibender Funktionalität.
Bereits in den siebziger Jahren setzte unter dem stetig steigendem Zwang zu Energie- und Kosteneinsparungen eine kontinuierliche Entwicklung zum Leichtbau bei gleichzeitig zu verringernden Produktionskosten ein.
In der heutigen Zeit steht Leichtbau mit möglichst hoch festen Werkstoffen im Mittelpunkt der Entwicklungen in der Gießereiindustrie.
Durch die enormen gestalterischen Freiheiten und durch die Vielfalt in der Werkstoffanwendung zählt die Gießereiindustrie zu den innovativen Branchen mit großen Nachhaltigkeitseffekten (Leichtbau).
Der Einsatz der Topologieoptimierung, unter Berücksichtigung bionischer Aspekte, die Verwendung optimierter Konstruktionselemente oder die Anwendung der Geometrieoptimierung lässt die Gießereien die Bedürfnisse der Kunden in Hinblick auf Leichtbauweise und gewünschter Funktionalität erfüllen.
Neben der Gießsimulation, die seit langem Stand der Technik ist, kommt in den Gießerei-en verstärkt die Finite-Element-Berechnung und Topologieoptimierung zur Erzeugung materialminimierter Strukturen und optimaler Trag-fähigkeit bzw. Steifigkeit zum Einsatz.
Die Resultate der Topologieoptimierung weisen, aufgrund des optimal verteilten Kraftflusses, eine Ähnlichkeit mit organisch gewachsenen Strukturen auf, die sich mittels des Fertigungsverfahrens Gießen sehr gut umsetzen lassen.
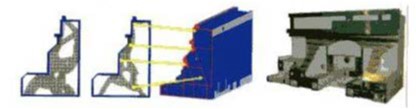
In Abbildung 1 sind v. l. n. r. dargestellt: Gestaltungsvorschläge, umgesetzte 3D-CAD-Konstruktion und einbaufertig bearbeitetes Bauteil.
Durch den mit Hilfe der Topologieoptimierung gefundenen kraftflussgerechten Gestaltungsvorschlag, der in eine fertigungsgerechte Verrippung umgesetzt wurde, verringerte sich das Bauteilgewicht des Maschinenbettes um 30 % gegenüber der Vorgängerkonstruktion, ohne das Kompromisse bei der Steifigkeit eingegangen werden mussten.
Da sich zudem die Anzahl der benötigten Kerne von etwa 80 auf 16 verringerte, konnten auch die Fertigungskosten für das Gussbauteil erheblich gesenkt werden.