Grundlagen einer intelligenten Energie- und Ressourceneffizienz in der Gießerei
Von Dierk Hartmann und Stefan Grimm, Kempten
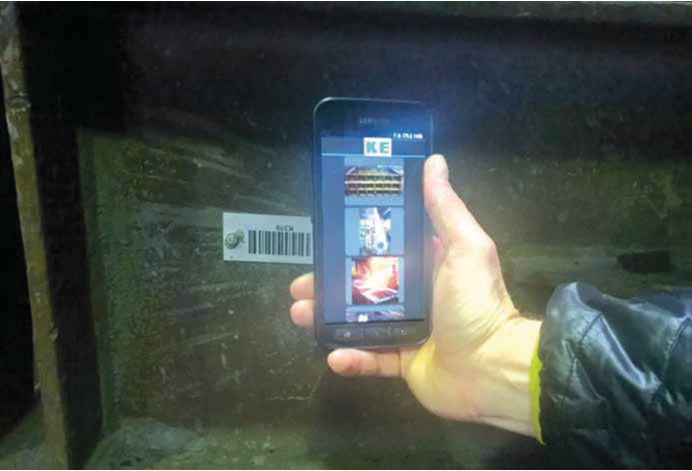
Mit der eigens entwickelten Handy-App werden die kompletten Prozessdaten des
Schmelzbetriebes, der Formerei und des Gießvorgangs über Barcodes miteinander verknüpft und gussteilbezogen in einer kontinuierlich aktualisierten Prozessdatenbank abgelegt. So werden Informationen wie z. B. zu technischen Fertigungsparametern, zum Auftragsstand oder zum Energieeinsatz online verfügbar.
Erschienen in GIESSEREI 09/2018
Die lückenlose Rückverfolgung der Gussteilherstellung über die gesamte Wertschöpfungskette der Fertigung ist Voraussetzung für eine valide Prozessoptimierung. Die große Schwierigkeit ist jedoch, diese lückenlos umzusetzen.
Die Markierung und Verfolgung der einzelnen Bauteile innerhalb des Produktionsprozesses in einem Gießereibetrieb gestaltet sich als nicht trivial. Die einzelnen Fertigungsbereiche, wie z. B. die Kernherstellung, das Formen, das Gießen oder das Auspacken, beinhalten relevante und komplexe Arbeitsschritte, jedoch ist die Vernetzung der Einzelbereiche oftmals lückenhaft oder nicht vorhanden.
Zur Umsetzung eines Lösungsansatzes zur Vernetzung und Digitalisierung der einzelnen Insellösungen müssen für jeden Bereich eigene Konzepte zur Datenerfassung entwickelt werden, da jeweils unterschiedliche Störfaktoren wie Hitze, Staub und Magnetfelder auftreten. Aus diesem Grund ist eine vollständige Rückverfolgbarkeit nur durch den Einsatz verschiedener Markierungstechniken und -verfahren möglich. Diese verschiedenen Ansätze zur Identifikation werden unter dem Sammelbegriff AutoID verstanden. Dazu zählen optisch auslesbare Codes wie z. B. Barcode, Data-Matrix-Code oder andere Marker sowie Technologien wie RFID, die elektromagnetische Wellen zur Übertragung nutzen1.
Mit einer logistischen Überwachung der Produktionsprozesse und -abläufe können Daten aufgenommen werden, woraus sich Standzeiten, Durchlaufzeiten und Prozesszeiten ermitteln und als zeitliche Abfolge darstellen lassen. Eine visualisierte Darstellung deckt schnell und übersichtlich zeitintensive Prozesse und Bottlenecks sowie Potenziale, wie die Auslastung einzelner Maschinen oder Produktionsbereiche, auf. Des Weiteren steigt die Prozesssicherheit, da Fehler und Probleme, die in der Wertschöpfungskette auftreten können, schneller erkannt und zugeordnet werden können. Ein frühzeitiges Warnsystem ermöglicht eine systematische Alarmierung, Analyse und Dokumentation der Auslöser, welche durch problemorientierte Lösungsansätze behoben werden können.
Durch die durchgängige Datenerfassung und Datendokumentation werden Methoden der „Predictive Analytics“ eingesetzt, um Muster und Zusammenhänge zwischen Prozessführung und Energieverbrauch offensichtlich zu machen und belastbare Lösungen für eine optimale Prozessführung zu entwickeln. Eine solche Umsetzung ist auch für die Zertifizierung nach ISO 50001 gefordert. Hierzu ist die Erstellung von Vorhersagen über den Energieverbrauch notwendig. Dabei sollen erhöhte Werte zum frühestmöglichen Zeitpunkt erkannt werden, um die Möglichkeit zu bieten, frühzeitig regelnd in den Prozess eingreifen zu können. Das Ziel ist es, dadurch Schlüsselstellen im Prozess zu erkennen, die für unnötige Verbrauchsspitzen verantwortlich sind. Bei alldem soll das, was in vielen industriellen Fertigungen als „Stand der Dinge“ gilt, in der Umgebung einer Gießerei unter großen Anstrengungen realisiert werden.
Zielsetzung des Forschungsprojekts IEREguss
Die zentrale Zielsetzung des Verbundforschungsvorhabens IEREguss ist die Realisierung einer energie- und ressourcenschonenden Prozessregelung. Dabei werden zunächst Verfahren der Digitalisierung und Erfassung von energierelevanten Prozessdaten und Energieverbrauchsdaten eingeführt. Neben den Energiedaten sollen die anderen betrieblichen IT-Systeme über eine zentrale Datenbank verbunden werden. Eine solche Datenstruktur soll innerhalb des Projektes aufgebaut werden. Die gesammelten Daten sollen mittels der Methoden und statistischen Analysen des Data Minings ausgewertet werden2. Das dadurch generierte Prozesswissen gibt Handlungsempfehlungen und Entscheidungsgrundlagen vor und baut eine Wissensbasis auf. Auf diesem Weg können Erfahrungswerte und langjährig gesammeltes Wissen einen stetig effizienteren Prozess erzeugen und dienen zur nachhaltigen Verbesserung der Energiebilanz des Unternehmens. Bild 1 stellt diesen Prozess dar. Entscheidend ist die mit diesem Verfahren mögliche adaptive Prozessführung, in der durch die immer wieder neu lernenden Vorhersagewerkzeuge auch bereits optimierte Prozesse neu beurteilt werden.
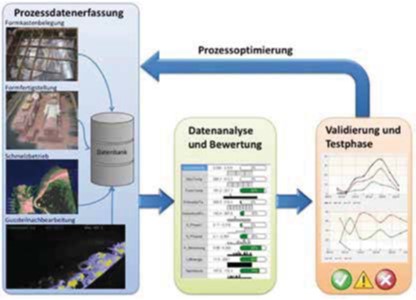
Ausgangslage
Da das Ziel als Energieeffizienz und -transparenz definiert ist, müssen im ersten Schritt die bereits vorliegenden und erfassten energiespezifischen Daten betrachtet werden. Zu Beginn wurden die bestehenden Datenstrukturen und der Ablauf der einzelnen Produktionsprozesse nachvollzogen. Bis heute wurden Energieverbräuche nicht automatisch erfasst, sondern es wurden die Stromzähler abgelesen und die Werte händisch in eine Tabelle eingetragen. Es wurden dabei nur monatliche Verbräuche aufgezeichnet, somit war keine tiefgehende Analyse von Spannungsspitzen möglich. Aus dem geringen Datenstand wurde lediglich eine grobe Kategorisierung der Stromverbräuche vorgenommen. Speziell wurden die Materialflüsse von Eisen und Furansand betrachtet und den produzierenden Abteilungen zugeordnet. Durch diese Kategorisierung soll eine Transparenz der Verbrauchswerte geschaffen werden.
Neben den energetischen Daten wurde der Produktionsablauf intensiv analysiert. Das war notwendig, da keine Dokumentation über die einzelnen Arbeitsschritte vorhanden ist. Dieses Prozesswissen ist nur direkt bei den jeweiligen Meistern und Facharbeitern vorhanden oder in Form von Auftragsdaten in dem ERP-System eingepflegt. Ein solches System dient der Produktionsplanung und sollte eigentlich die Grundlage einer gemeinsamen Datenbasis schaffen. Die Kundenanfragen werden dort aufgenommen und für die Produktion eingeplant. Gerade in dem Handwerk der Gießereibranche werden noch relativ wenige Arbeitsvorgänge automatisiert und computergesteuert bearbeitet. Es müssen viele mechanische Schritte durch Facharbeiter ausgeführt werden, um ein Gussteil herzustellen. Dementsprechend schwierig gestalten sich durch IT unterstützte Prozessoptimierungen. Zudem werden aktuell nur sehr wenige Daten innerhalb des Produktionsprozesses aufgenommen. Speziell im Bereich Handformguss mit Mischkästen ist es daher äußerst aufwendig eine genaue Anordnung und Zuordnung der einzelnen Modelle vorzunehmen.
Nach intensiver Betrachtung des bestehenden Produktionsprozesses und der existierenden IT-Strukturen hat sich herausgestellt, dass ein weiteres vollautomatisiertes Erfassen von Prozessparametern durch IT-Unterstützung erst sinnvoll ist, wenn die bestehenden IT-Systeme bewusst und optimiert eingesetzt werden. Aus diesem Grund wurde auch großer Wert auf die optimale Nutzung der bestehenden Systeme gelegt, um das volle Funktionsspektrum der Software auszunutzen.
Problemfelder und Lösungsansätze
Grundlage waren zwei vorhandene Prozessschaubilder, einmal für den Materialfluss und einmal für den Datenfluss. Doch keines dieser beiden Prozessschaubilder bildet den Ablauf des Produktionsprozesses ab. Bei der Darstellung des Materialflusses liegt der Fokus auf der Lagerung und den Verarbeitungsorten der einzelnen Materialien. Bei dem Datenfluss liegt das Hauptaugenmerk auf den metallurgischen Daten, wodurch kritische Informationen zu der Qualität der Schmelze sowie der Schmelzbehandlung erzielt werden können. Aber eine Relation zu den Durchlaufzeiten der einzelnen Arbeitsschritte wird nicht abgebildet. Ebenso werden die Schnittstellen zwischen den einzelnen angebundenen IT-Systemen und den Kommunikationswegen zwischen den verschiedenen Abteilungen nicht betrachtet. Doch eben genau diese Informationen sind zur Darstellung und zum Aufbau eines optimalen Prozessablaufs in einer gesamtheitlichen End-To-End-Betrachtungsweise (E2E) essenziell notwendig. In Bild 2 wird in einer Prozessübersicht der Produktionsprozess vom Auftragseingang bis zur Produktübergabe gezeigt.
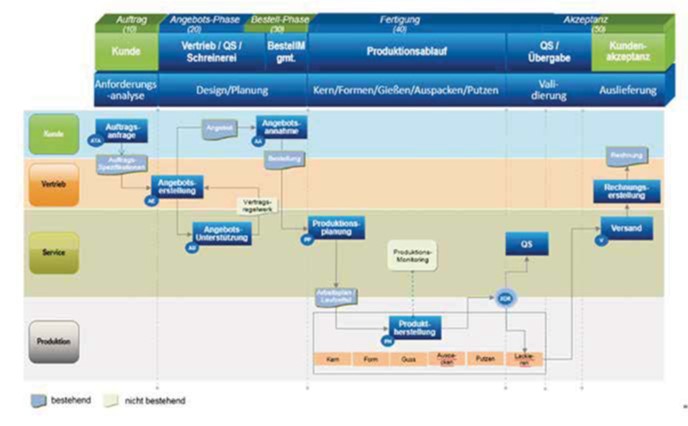
Ausgehend von dem in Bild 2 dargestellten Prozessablauf wurden mehrere Workshops mit den Meistern und Verantwortlichen abgehalten. Dabei wurden die Durchlauf- und Prozesszeiten aus allen Abteilungen aufgenommen. Aus diesen Informationen wurde der Leistungsprozess der produzierenden Abteilungen aufgebaut (Bild 3). Die markierten Synchronisationspunkte haben jeweils bestimmte Abhängigkeiten zu unterschiedlichen Abteilungen. Wenn es hierbei zu Verzögerungen in der Bereitstellung von Materialien und Hilfsmitteln kommt, schlägt sich der zeitliche Rückstand unmittelbar in der jeweiligen Prozesszeit nieder. Aus diesem Grund müssen gerade Schnittstellengüter, welche auf dem kritischen Pfad der Wertschöpfungskette liegen, gezielt und bewusst überwacht werden, um einen reibungslosen Ablauf zu gewährleisten. Der Prozessablauf muss in dem ERP-System abgebildet sein. Für diese zielorientierte Anpassung gab es eine Abstimmung mit dem Softwarehersteller, um alle nötigen Anforderungen einzuarbeiten.
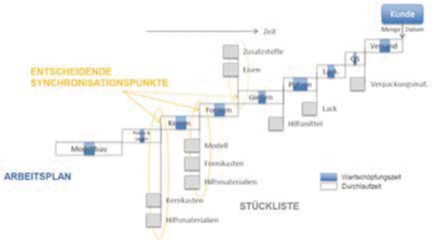
Neben den eingeleiteten Schritten für einen optimierten Prozessablauf wurden noch mehrere Themen bearbeitet, um eine Effizienzsteigerung bezüglich Energie und Ressourcen zu schaffen. Neben dem Aufbau von neuen Methoden zur Datenakquise aus den Fertigungsbereichen wird eine Webanwendung zur Darstellung der aktuellen Kundenaufträge sowie ein Energiemonitoring aufgebaut. Zudem wurden noch die Auslastungen der Flurförderfahrzeuge und die Fahrwege innerhalb der Gießerei betrachtet. Nachfolgend werden jeweils die einzelnen Themen genauer beschrieben.
Mobile-App
Gemäß den Digitalisierungsansätzen werden die Prozessparameter der einzelnen Teilbereiche innerhalb der Wertschöpfungskette benötigt, um eine durchgängige Verfolgung der Kundenaufträge zu ermöglichen. Gerade im Handformbetrieb mit Mischkästen erweist sich eine automatisierte digitale Protokollierung der Zuordnung der Modelle zu den Formkästen als sehr schwierig. Aus diesem Grund werden an Kästen und Pfannen Barcode-Tags angebracht. Diese sollen über die Kamera an einem Smartphone und eine eigens entwickelten Mobile-App gescannt und zusammen mit den Aufträgen in einer Datenbank gespeichert werden. Über die Mobile-Anwendung sollen zusätzlich der Abstich des Ofens sowie das Abgießen der einzelnen Kästen durch die Pfannen protokolliert werden. Durch die erfassten Zeitstempel lässt sich der Produktionsweg der einzelnen Gussteile aufnehmen. Neben dem Nutzen der Transparenz können Qualitätsoptimierungen erschlossen werden. Durch die eindeutige Zuordnung der unterschiedlichen Aufträge in einem Kasten lässt sich das Sand-Schmelze-Verhältnis berechnen. Ebenso dient zusätzlich ein Foto zur Dokumentation der Kastenbelegung.
Auftragsmonitoring
Im Auftragsmonitoring sollen die laufenden Aufträge aller Kunden dargestellt werden. Durch Filterfunktionen soll die Ansicht der angezeigten Daten reduziert werden, um einen schnellen Überblick zu ermöglichen. Anwendungsszenarien könnten z. B. die Selektion aller Aufträge eines Kunden sein oder die Anzeige aller Aufträge mit einem Liefertermin innerhalb von zwei Wochen. Zu den einzelnen Kundenaufträgen sollen alle aufgenommenen Prozessdaten aus den verschiedenen Datenbanksystemen mit angezeigt werden. Dadurch können die benötigten Ressourcen und die aufgewendete Energie den einzelnen Aufträgen und Teilen zugeordnet werden. Zur Darstellung ist eine Web-Anwendung im Aufbau, die gezielt die verschiedenen Datenbanken abfragt und als Verzeichnisstruktur darstellt. Der Einsatz kann in einzelnen Abteilungen erfolgen, jedoch auch abteilungsübergreifend. Die übersichtliche Darstellung schafft einen Überblick, wodurch auch eine Priorisierung von Aufträgen erfolgen kann, ohne andere Aufträge aus dem Auge zu verlieren.
Energiemonitoring
Im Zuge dieses Projektes wurde ein Energiemonitoring-System eingeführt, das den Arbeitsaufwand des monatlichen Ablesens des Zählerstands einspart. Zudem werden nun die Energiedaten täglich von vielen Messstellen automatisch aufgezeichnet und in einer Datenbank abgespeichert. Durch eine solche konsistente Datenbasis können verschiedene Algorithmen zur Analyse der Daten verwendet werden. Es ist somit einfach möglich, Ausreißer und Überschreitungen von Schwellwerten aufzuzeigen und Alarm auszulösen. Die im Softwareprodukt enthaltenen Auswertungstools befinden sich aktuell noch im Aufbau. Ebenso ist eine Datenkorrelation mit den Produktionsdaten aus dem ERP-System vorgesehen.
Flurförderfahrzeuge
Bereits bei der Analyse des Fertigungsablaufs in der Gießerei konnte eine hohe Anzahl an Flurförderfahrzeugen festgestellt werden. Um eine detaillierte Aussage treffen zu können, war es nötig, die aufgezeichneten Fahrt- und Standzeiten auszuwerten. Dabei konnte beobachtet werden, dass es häufig zu Leerfahrten kommt oder die Stapler nicht im Einsatz sind. Zudem ließ sich feststellen, dass Aufladezeiten der Elektrostapler nur selten eingehalten werden. Nach Herstellerangaben sollte ein unterbrechungsfreies Ladeintervall durchgeführt werden, um eine optimale Batterielebensdauer zu gewährleisten. Ebenso ist nachweisbar, dass einige Fahrzeuge nur wenige Stunden im Einsatz sind. Durch die Generierung von Ab- und Beladeplätzen lässt sich der Fuhrpark um ein bis zwei Flurförderfahrzeuge, bei gleichzeitigem Einhalten von unterbrechungsfreien Ladezyklen, reduzieren. Dadurch können direkt hohe Summen an Leasinggebühren eingespart werden.
Ausblick
In den nächsten Schritten müssen die in den verschiedenen Systemen gesammelten Daten strukturiert und korreliert werden. Über die Verknüpfung der Daten aus der Mobile-App, dem ERP-System, dem Energiemanagement-System und der Ofensteuerung lassen sich die verbrauchte Energie und somit auch entstandene Kosten pro Gussteil errechnen. Bild 4 zeigt den schematischen Aufbau. Im unteren Bereich sind die verschiedenen Datenquellen abgebildet. Über den ETL-Prozess (Extract, Transform, Load) werden die benötigten Daten aus den verschiedenen Datenquellen geladen. Die Webanwendung soll die Daten konsolidiert und nutzbringend darstellen [1].
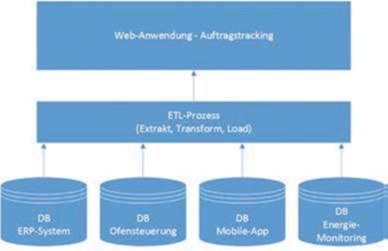
Bei gussbedingten Defekten kann die Datenbasis einen wertvollen Beitrag zur Fehleranalyse leisten. Neben dem offensichtlichen Nutzen der aufgebauten Systemlandschaft kann der konstante Datenstrom durch mathematische Algorithmen analysiert und ausgewertet werden. Dadurch lassen sich Änderungen im Produktionsprozess schnell aufdecken und es kann proaktiv dagegen vorgegangen werden, um beispielsweise die Ausschussrate zu senken.
Das IGF-Vorhaben 18061N der Forschungsvereinigung Gießereitechnik e. V. (FVG), Hansaallee 203, Düsseldorf, wurde im Rahmen des Programms zur Förderung der industriellen Gemeinschaftsforschung und -entwicklung (IGF) vom Bundesministerium für Wirtschaft und Energie (BMWi) aufgrund eines Beschlusses des Deutschen Bundestages gefördert.
Prof. Dr.-Ing. Dierk Hartmann, M.Sc. Inf. Stefan Grimm, Hochschule für angewandte Wissenschaften Kempten, Kempten
Literatur:
[1] Alpar, P.; Alt, R.; Bensberg, F., u. a.: Anwendungsorientierte Wirtschaftsinformatik. Springer, 2014, S. 234 ff.