Abwärmeverstromung muss sich wieder lohnen!
Von Manuel Bosse, Düsseldorf
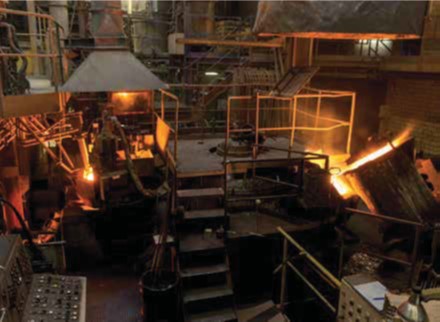
Schmelzaggregate wie Kupolöfen, von denen in Deutschland noch 60 in Betrieb sind, haben noch ungenutzte Abwärmepotenziale.
Erschienen in GIESSEREI 06/2016
Welche Rohstoffpreise sind normal? Dieser Frage ging ein Artikel in der GIESSEREI vom April 2016 nach. Fest steht, dass zusammen mit den Einstandspreisen für Rohstoffe Energie einen Anteil von etwa 35 % an den Selbstkosten einer Gießerei hat. Systematisches Energiemanagement hat daher in den letzten Jahren einen zunehmend höheren Stellenwert erhalten. Die Konsequenz daraus ist, dass in deutschen Gießereien proaktiv seit dem Jahr 2011 immer mehr Systeme zur Verbesserung der Energieeffizienz betrieben werden, z. B. Energiemanagementsysteme nach DIN EN ISO 50001. Maßnahmen zur Verbesserung der Energieeffizienz konnten bei relativ stabilen Weltmarktpreisen, z. B. für Rohöl zwischen 70 und 100 Euro je Barrel mit akzeptablen Amortisationszeiten in den Aktionsplänen der Gie ßereien aufgeführt werden. Doch spätestens im Jahr 2014 sind alle Amortisa tionsrechnungen „über den Haufen geworfen worden“: Der Rohölpreis sank von 90 unter 60 Euro im Jahr 2014 sowie auf unter 30 Euro im Jahr 2016. Überwiegend werden Investitionen zur Abwärmenutzung auf Basis des Erdgasbedarfs gerechnet und dieser ist von 50 Euro pro MWh auf unter 15 Euro pro MWh im Jahr 2016 gesunken. Eine verbesserte, „erdgaseffiziente“ Pfannenvorwärmung mit innovativer Technik lässt sich gegenwärtig dem kaufmännischen Geschäftsführer in einer Gießerei nur schwerlich verkaufen, denn durch die gesunkenen Energiepreise rücken Amortisationszeiten von unter fünf Jahren in weite Ferne.
Ein erhebliches Potenzial in Gießereien stellen große Mengen Abwärme dar, die jedoch in den meisten Betrieben als ungenutzte Abwärme an die Umwelt abgegeben werden. Dennoch steigt der Energiebedarf von Gießereibetrieben im Winter erheblich an, weil zusätzliche Erdgasstrahler, Diesel- oder Heizölbrenner aufgestellt werden, um Einzelarbeitsplätze- oder ganze Hallen zu erwärmen. Dabei existieren bereits heute verschiedene Best-Practice-Beispiele, wie sich diese Abwärme intern nutzen lässt. Die Erwärmung von Hallenluft und Wasser für Sanitäranlagen, z. B. mit der Abluft von Druckluftkompressoren, ist bei Neuinvestitionen Stand der Technik. Ebenfalls positiv sind Erfahrungsberichte, wonach Abwärme zur Trocknung von Roh- und Einsatzstoffen genutzt wird. Aufwendige
Umbauten sind hierfür nicht notwendig, vielmehr genügt es bereits, wenn benachbarte Bunker der Gattierhalle für Schrottoder Späne angewärmt werden, um Schmelzzeiten zu reduzieren. Auch bei
Einsatzstoffen der Gießereichemie (Schlichten, Wasserlacke etc.) macht sich die Abwärmenutzung bezahlt, denn im Bereich der Formerei und der Kernmacherei kann eine gleichbleibende Qualität
durch geringere Temperaturschwankungen sichergestellt werden. Bei Neu- oder Umbauten von Werkshallen hat die Energieeinsparverordnung, welche vor allem aus dem privaten Gebäudebereich bekannt ist, ebenfalls Einfluss auf Gießereien. So werden Werkhallen besser gedämmt und Fußbodenheizungen verbaut. In einer Gießerei werden beispielsweise bearbeitete Gussstücke vor der Grundierung und Lackierung durch gezielte Lagerung im Bereich der Fußbodenheizung „auf Temperatur gebracht“.
Die größten Abwärmepotenziale ergeben sich jedoch in der deutschen Gießerei-Industrie an den 60 verbliebenen Kupolöfen, wobei das Hauptaugenmerk auf den 28 Heißwindkupolöfen liegt. Thermoölleitungen ermöglichen die Nutzung von Abwärme in anderen Gießereiprozessen, z. B. durch Substitution von Heizöl und Erdgas in Lackieranlagen, Glüh- und Trockenöfen.
Wenn Gießereien ihre Abwärme nicht wirtschaftlich in anderen Bereichen nutzen können, dann müssen andere Wärmesenken für die Wärme aus der Gießerei genutzt werden. Das in der Industrie meistzitierteste Leuchtturmprojekt ist Endeder sogenannten Nullerjahre durch eine industrie standortübergreifende Abwärmenutzung in einer Gießerei realisiert worden, die einem Unternehmen der Lebensmittel-Industrie zugute kam. Weitere Best-Practice-Beispiele zur externen Abwärmenutzung stellen die Einleitung in ein Fernwärmenetz sowie die externe Sekundärnutzung in Schwimmbädern oder benachbarten Auto- oder Gewächshäusern dar.
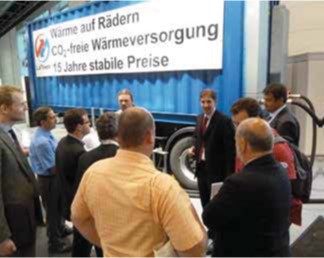
Eine stationäre Alternative zur Abwärmenutzung wird gegenwärtig in einem Forschungsprojekt mit einer Eisengießerei getestet, bei dem Feststoffspeicher den Wärmebedarf in Stillstandzeiten des
Kupolofens decken sollen. Eine weitere Möglichkeit stellen Wärmespeicher dar, welche, z. B. als Latentwärmespeicher, eine „mobile, trassenlose Wärmeversorgung“ von Verwaltungsgebäuden über
mehrere Kilometer ermöglichen können. Trotz intensiver Bemühungen ist jedoch weiterhin kein Latentwärmespeicher in der Gießerei-Industrie im Einsatz.
Alternativ kann die Wärme auch zur Kälteerzeugung in einer wärmebetriebenen Kältemaschine genutzt werden. Zwei Gießereien nutzen bereits diese Möglichkeit, um z. B. im Sommer den Formsand
zu kühlen. Auch eine gezielte Beschleunigung von Abkühlvorgängen der Formen nach dem Abguss wäre denkbar.
Ein Ergebnis des im Auftrag des Umweltbundesamts erarbeiteten Umweltforschungsplanprojekts „ErneuerbareEnergienGießerei“ war, dass mehr regenerative Energien im deutschen Stromnetz auch mehr Flexibilität der Gießereiprozesse und der Gießereibeschäftigten erfordern. Eigenstromerzeugung und Speicherung könnten zwei Möglichkeiten sein, die Flexibilität im Gießereiprozess zu erhöhen. Bei einem Leuchtturmprojekt der deutschen Gießerei-Industrie in den 1990er-Jahren wurde an einem Heißwindkupolofen eine Dampfturbine angeschlossen. Ein weiteres Pilotprojekt zur Verstromung von Abwärme mit Hilfe einer Organic-Rankine-Cycle-Anlage (ORC) mit Gaskolbenmaschine ist kurz vor Abschluss Anfang der 2010er-Jahre gescheitert. Bis heute stehen Fördermittel im Rahmen des Umweltinnovationsprogramms für eine solche Anlage mit Demonstrationscharakter zur Verfügung. Andere Industrien haben diese Möglichkeit genutzt und beispielsweise Pilotprojekte mit einem Zündstrahlmotor und einem thermoelektrischem Generator, einer Steam-Rankine-Cycle-Anlage oder ORCModulen umgesetzt.
Studien prognostizieren einen weltweiten Umsatzanstieg alleine für thermoelektrische Generatoren von 50 Mio. Euro im Jahr 2015 auf über 900 Mio. Euro im Jahr 2023. Die Europäische Union und
auch die deutsche Bundesregierung möchten Maßnahmen zur Verbesserung der Energieeffizienz im Bereich der Abwärmenutzung aktiv fördern, doch gegenwärtig werden in Deutschland weitere Investitionen in die Eigenstromerzeugung durch gleich zwei energiepolitische Hürden massiv behindert:
In der Gießerei-Industrie erhalten 142 der 595 Gießereien eine Begrenzung der EEG-Umlage im Rahmen der Besonderen Ausgleichsregelung. Für diese Gießereien ist es häufig unattraktiv, Eigenstrom zu erzeugen, weil ansonsten zu befürchten steht, dass die Schwellenwerte von 17 bzw. 20 % Stromkosten zu Bruttowertschöpfung nicht mehr erreicht werden und die Zahlung der vollständigen EEG-Umlage fällig wird. Mit dem EEG 2014 müssen grundsätzlich alle nach August 2014 errichteten Eigenstromerzeugungsanlagen eine (anteilige) EEG-Umlage zahlen, also auch hocheffiziente KWK-Anlagen und Anlagen auf Basis erneuerbarer Energien. Es steht auch zu befürchten, dass diese Regelung auf Bestandsanlagen durch die EU ausgeweitet wird.
Bezeichnend dafür ist, dass nur in einer französischen Gießerei aufgrund „ besserer“ politischer Rahmenbedingungen bereits ein 1-MW-ORC-Modul installiert wurde. Auch aus anderen CAEF (Com mittee of Associations of European Foundries)-Mitgliedsländern sind solche Bestrebungen bekannt. Daher liegt die Hoffnung jetzt auf dem neuen Kraft-Wärme-Kopplungs-Gesetz, welches am 21. Dezember 2015 in Kraft trat. Dieses Gesetz weist in § 35 Absatz 4 eine Übergangsregelung für Brennstoffzellen und ORC-Anlagen aus. Betreiber können alternativ eine Vergütung nach dem KWKG 2012 in Anspruch nehmen, wenn eine verbindliche Bestellung der ORC-Anlage bis zum 31. Dezember 2016 und die Inbetriebnahme dieser Anlagen bis zum 31. Dezember 2017 erfolgt.
Eine Studie des Umweltbundesamts zum Klimaschutz im Jahr 2050 hat klare Erwartungen, was in den nächsten Jahren technisch möglich sein soll, an unsere Branche skizziert. Wirtschaftliche Aspekte blieben dabei allerdings außen vor. Das Umwelt- und Energieteam im Haus der Gießerei- Industrie hingegen treibt auch zukünftig das Thema Abwärmeverstromung unter allen drei Nachhaltigkeitsgesichtspunkten, was ökonomische Betrachtungen explizit mit einschließt, aktiv voran, ohne einzelne Technologien zu bevorzugen. Gegenwärtig stehen es mit vier Anbietern in Kontakt, denen in einer der nächsten Ausgaben der GIESSEREI die Möglichkeit geben wird, die Vorteile ihrer Technologie zu skizzieren. Spätestens im Rahmen der Kupolofenkonferenz im Jahr 2017 sollen weitere Fortschritte bekanntgegeben werden.
Vision des Umweltbundesamts: Deutsche Gießerei-Industrie 2050
„Trotz der steigenden Produktionszahlen kann für 2050 ein Rückgang des Endenergieverbrauchs in der Branche um rund 50 % im Vergleich zu 2008 sowie eine treibhausgasneutralen Gussproduktion in
Deutsch land realisiert werden. Dies kann [...] durch die Erhöhung der Energieeffizienz in der gesamten Gussteilproduktion erreicht werden. […] Überdies werden Techniken zur konsequenten Rückgewinnung und Nutzung von Restwärme bzw. Abwärme entlang der gesamten Produktionskette einge setzt, um bspw. Abwärme aus dem Schmelz- und Gussteilabkühlprozess als Prozesswärme in vor- und nachgelagerten Ver- und Bearbeitungsschritten wie Kern- und Formherstellung sowie Trocknung zu verwenden.“