Gienanth setzt Energie-Effizienz-Manager erfolgreich bei Heißwindkupolofen ein
Von Heinz Kadelka, Düsseldorf und Mike Weber, Eisenberg
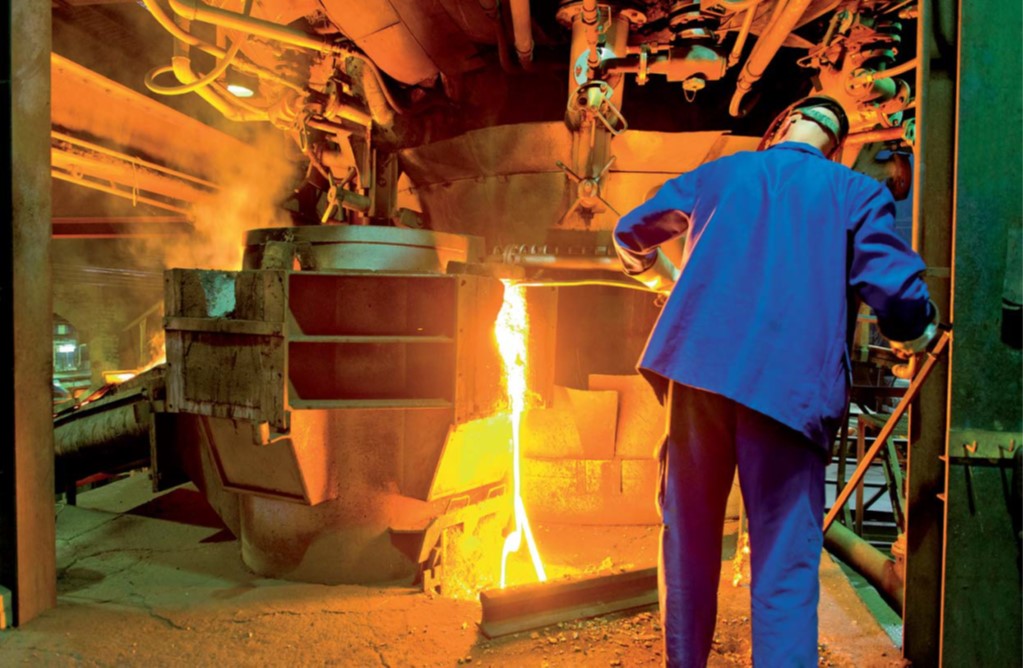
Abschlacken am Kupolofen bei der Gienanth GmbH in Eisenberg. Um gute Schmelzergebnisse zu gewährleisten, ermöglicht eine Software jetzt sowohl präventive als auch direkte Eingriffe in den Schmelzprozess.
Erschienen in GIESSEREI 08/2015
Emissionsreduzierung, Flexibilitätssteigerung, die Erweiterung der Produktvielfalt und die Notwendigkeit mit günstigsten Einsatzstoffen zu arbeiten – diesen Zwängen sehen sich die Betreiber von Kupolöfen heute gegenüber, wenn sie ihre Wettbewerbsfähigkeit erhalten wollen. Um unter diesen Rahmenbedingungen leichmäßig gute Schmelzergebnisse zu gewährleisten, ist eine effiziente Fahrweise des Ofens notwendig. Herkömmliche Optimierungsmaßnahmen haben dabei jedoch einen entscheidenden Nachteil: Der Ofenfahrer kann erst dann reagieren, wenn sich bereits Abweichungen im Schmelzprozess zeigen. Eine Alternative bietet eine neue Ofensteuerungssoftware: der sogenannte Energie-Effizienz-Manager (EEM). Wie der Praxisbetrieb bei der Gienanth GmbH zeigt, ermöglicht die Software sowohl einen präventiven als auch einen direkten Eingriff in den Schmelzprozess. So lassen sich Abweichungen von vornherein vermeiden.
Als traditionsreiche Eisengießerei hat sich die Gienanth GmbH im pfälzischen Eisenberg auf die Verarbeitung verschiedener Gusseisensorten spezialisiert. Mit einer 280-jährigen Geschichte und einer Produktionskapazität von über 100 000 t pro Jahr hat das Unternehmen dabei sowohl das notwendige Know-how für eine herkömmliche Fahrweise von Kupolöfen als auch die Innovationskraft für zukunftsweisende Optimierungen. Deshalb weiß man in Eisenberg auch: Der Schmelzprozess in Kupolofenfahrweise ist zweifellos komplex. Denn eine Vielzahl von Parametern wie der Siliziumanteil oder der Kokssatz nimmt Einfluss auf die Qualität des Schmelzergebnisses. Hinzu kommt, dass jeder Kupolofen auf Änderungen dieser Einflussgrößen ganz unterschiedlich reagiert. Es gilt deshalb, den Prozess durch die richtigen Entscheidungen im richtigen Moment zu steuern und optimierend einzugreifen.
In einem gemeinsamen Projekt untersuchten Linde, München, und Gienanth nun, ob sich dieser Prozess mit der neu en Ofensteuerungssoftware Energie- Effizienz- Manager (EEM) automatisieren und damit verbessern lässt. Als Unter suchungs gegenstand diente ein konkreter, beispielhafter Heißwindkupolofen der Gienanth GmbH.
Herkömmliche Fahrweise des Heißwindkupolofens
Als Ausgangspunkt für die Versuchsreihe diente die bisherige Fahrweise des Ofens. Wie ein Überblick zeigt, waren die herkömmlichen Eingriffsmöglichkeiten in den Schmelzprozess durchaus vielfältig:
Metallischer Einsatz
Bild 1 zeigt, dass der Gattierer den Durchschnittswert der metallischen Einwägung (Schichtmittel) im Tagesmittel sehr genau getroffen hat. Zieht man jedoch zwei bis drei nachfolgende Sätze zur Betrachtung heran, lassen sich deutliche Abweichungen beobachten. Eine Gattierung mit einem Satzgewicht von 2000 kg wird in der Realität um bis zu 15 % unter- oder übertroffen (1700- 2300 kg). Und auch der reine Stahlanteil, der in der Regel um 50 % (1000 kg) liegt, schwankt. Bei der Betrachtung des Verhältnisses der metallischen Einsatzstoffe zum Gießereikoks zeigen sich, trotz aller Automatisierung in der Gattierung, beachtliche Unterschiede, welche der Ofenschacht nicht ausgleichen kann.
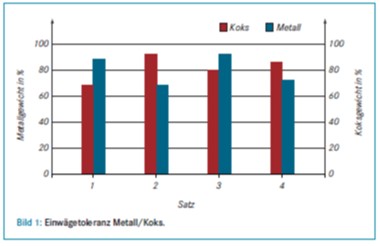
Zuschlagsstoffe
In der Realität kommt es zu bis zu 12 % Abweichung im Mittel bei einem Satz. In der Addition von zwei bis drei Sätzen sind Abweichungen von über 8 % zu verzeichnen. Selbstverständlich werden bei genauer (gleichmäßiger) Zugabe von SiC-Formlingen nicht die hohen Schwan kungen im Stahleinsatz ausgeglichen. (siehe Bild 1).
Bei einer Schmelzleistung von 18 t/h und der Beobachtung (Analyse der Stoffe in der Schmelzzone) von drei Sätzen (6 t) betrachtet man somit eine Schmelzzeit von jeweils 20 min (Bild 2). Hierbei zeigen sich hohe Schwankungen.
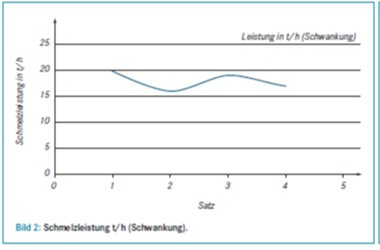
Wind und Sauerstoff
In der Regel wird zum Schmelzprozess leistungsabhängig Heißwind und Sauerstoff dazugefahren. Kommt das Beispiel mit den Materialschwankungen in der Charge aber zum Tragen, erfolgt die Zugabe von Wind und Sauerstoff konstant und greift nicht in die tatsächlichen energetischen und metallurgischen Verhältnisse ein (Bild 3).
Dies hat Auswirkungen auf die Rinnenanalyse wie schwankende Schmelzzeit der einzelnen Chargen, Silizium-Ausbringung aufgrund von Abbrand und dem Verhältnis zur Metallmenge, Rinneneisentemperaturschwankungen und in der Folge Aufkohlungsschwankungen.
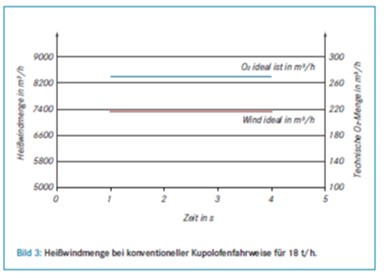
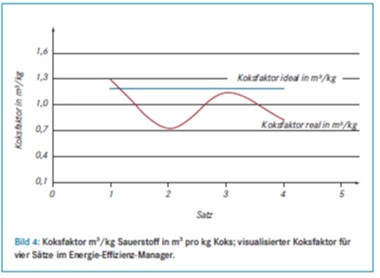
Koksfaktor
Setzt man den gesamten eingesetzten Prozesssauerstoff in Relation zum eingesetzten Koks, ergibt sich der Koksfaktor als eine wichtige ofenspezifische Kenngröße. Bild 4 zeigt den idealen Koksfaktor, der sich bei der Annahme von gleicher Schmelzleistung zur eingestellten konstanten Windmenge und zur technischen Sauerstoffmenge ergibt. Es zeigt sich eine stark schwankende Kenngröße (Bild 4).
In der Software-Anwendung des Energie-Effizienz-Managers kann der Koksfaktor spezifisch für eine Bilanz von mehreren Sätzen ermittelt werden. In der Anwendung bei Gienanth werden für die Regelung immer die letzten vier in der Schmelzzone befindlichen Sätze für die Berechnung herangezogen. Kleinere Einheiten hätten zu viele Steuerungsaktionen zur Folge und würden der „natürlichen“ Durchmischung der Sätze im Schacht nicht gerecht werden, heißt es bei Gienanth.
Gichtgas
Der Energiegehalt des Gicht- oder Rohgases ist die Folge der primär in der Schmelzzone ablaufenden Verbrennungsprozesse. Das Verbrennungsverhältnis wird durch den Kohlenstoffmonoxid-Gehalt (CO) und den Kohlenstoffdioxidgehalt (CO2) bestimmt. Diese bilden letztlich den verbrennungstechnischen Wirkungsgrad (ETA-V). Hier wird die Theorie des Boudouard-Gleichgewichts, das von den spezifischen Verhältnissen im Schmelzprozess bestimmt wird, mit Leben gefüllt. Bild 5 zeigt zusätzlich das Beispiel der CO-Konzentration im Gichtgas.
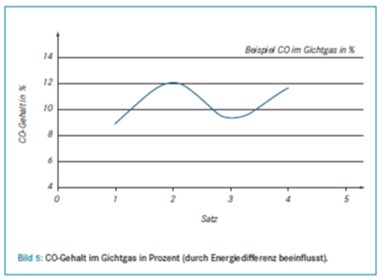
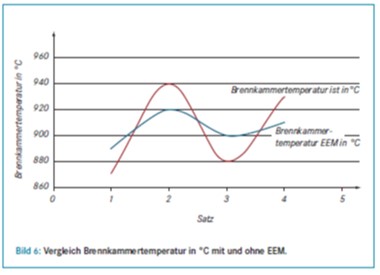
Brennkammer
Die Brennkammer ist von entscheidender Bedeutung für die Einhaltung der in der „Technischen Anleitung zur Reinhaltung der Luft“ (TA Luft) festgelegten gesetzlichen Grenzwerte. Die notwendige Feuerraumtemperatur beträgt in der Regel ca. 900 °C, um die Verbrennung von gasförmigen Schadstoffen zu garantieren (Beispiel CO-Grenzwert 150 mg/m³). Fällt die Temperatur unter diese Marke, ist die Einhaltung des Grenzwertes kaum möglich. Die Energieführung der Brennkammer wird primär durch den Energiegehalt des zugeführten Gichtgases bestimmt. Reduziert sich dieser Energiegehalt, muss zwangsläufig mehr Fremdenergie eingesetzt werden (z. B. Erdgas).
Um den Eintrag von kostenintensiver Fremdenergie zu minimieren, wird versucht, ein ausgewogenes CO-Niveau als chemisch gebundene Wärme mit dem Gichtgas in die Brennkammer zur Verbrennung einzutragen.
Die unterschiedliche energetische Auslastung der Brennkammer (Kühlluft, Verbrennungsluft usw.) führt zu ständigen Druckdifferenzen − u. a. mit der Folge von sichtbarem Rauchen an der Obergicht und erheblichen Temperaturschwankungen (Bild 6). Die Saugzugregelung versucht dann automatisch, einen geforderten Unterdruck zu initiieren und steuert die Absaugleistung. Tritt hierbei jedoch sichtbar Rauch aus, wird die Fahrweise vom Automatikbetrieb häufig auf Handbetrieb gestellt, um die Trägheit der automatischen Regelung zu überstimmen. In der Folge strömen undefinierte und erhöhte Mengen Falschluft aus der Gicht mit in den Prozess und kühlen die Brennkammer. Das so verdünnte Gichtgas führt dann zu einem erhöhten Fremdenergieverbrauch.
Lösungsansätze
Die oben dargestellte herkömmliche Ofenfahrweise erhöht nicht nur den CO2-Ausstoß, sie verursacht auch kontinuierlich Energiemehrverbräuche: Zum einen zusätzliche Energie für den Saugzug und die Brennkammer. Zum anderen müssen Siliziumcarbid (SiC), Koks und technischer Sauerstoff vorgehalten werden. Kommt es bei der konventionellen Fahrweise zu einem Sauerstoffüberschuss in der Verbrennungsluft im Verhältnis zur fossilen Energiemenge – also dem Gießereikoks – oxidieren zudem die Elemente Silizium (Si), Eisen (Fe) und Mangan (Mn).
Um gleichmäßig gute Schmelzergebnisse bei einer effizienten Fahrweise des Heißwindkupolofens zu erzielen, können folgende Maßnahmen ergriffen werden:
- Chargieren der erforderlichen Zuschlagsstoffe (Koks, Kalk, SiC usw.) in direkter Abhängigkeit von Satzgewicht und Stahlanteil
- Verfolgen der Sätze oder Satzfolgen bis in die Schmelzzone und Betrachten des Energiegehaltes
- Eintrag von Wind, Sauerstoff und Brennstoffen wie Koks in Abhängigkeit zum Energiegehalt in der Schmelzzone
- Bestimmen des Energiegehaltes im Gichtgasstrom durch die Messung von CO und CO2 und Ermitteln des ETA-V
- Einflussnahme von Wind, Sauerstoff und Feststoffen auf das Ergebnis der Gichtgasmessung mit dem Ziel der gleichmäßigen Energieführung
- Einflussnahme auf die Brennkammertemperatur durch die Veränderung der Gichtgaszusammensetzung
- Leistungsabhängige Fahrweise mit festen Kenngrößen
Die aufgeführten Lösungsansätze haben jedoch einen entscheidenden Nachteil: Der Ofenfahrer kann erst dann reagieren, wenn sich bereits Abweichungen im Schmelzprozess zeigen.
Die Alternative: Ofensteuerungssoftware Energie-Effizienz-Manager (EEM)
Eine Alternative verspricht eine neue Ofensteuerungssoftware: der Energie-Effizienz-Manager (EEM). Wie umfangreiche Tests bei Gienanth belegt haben, ermöglicht diese Software einen präventiven bzw. direkten Eingriff in den Schmelzprozess. So lassen sich Abweichungen von vornherein vermeiden. Möglich wird dies durch eine intensive Datenerfassung in der Projektphase, spezifisch für den betroffenen Kupolofen. Aufgrund der Datenauswertung ergibt sich dann − in Abhängigkeit von der Schmelzleistung − das optimale Prozessfenster für den automatisierten Ofenbetrieb. Die spätere Ofensteuerung greift dann auf die hinterlegten Daten in den Parametertabellen zu und nutzt diese für das Steuern und Überwachen der Ofenfahrweise. Als Primärschlüssel dient immer die Schmelzleistung als entscheidendes Kriterium im laufenden Prozess.
In der Praxis wird die Software folgendermaßen angewendet: Der Ofenbediener muss die gewünschte Schmelzleistung in einer Eingabemaske der EEM-Visualisierung eingeben. Der EEM ermittelt daraufhin auf der Grundlage einer Datenbank (hinterlegte Parametertabellen) die optimalen Einstellungen für Wind, Sauerstoffund Koksmenge. Der Anlagenbediener muss anschließend lediglich die vorgeschlagenen Werte akzeptieren − oder diese innerhalb eines vorgegebenen Toleranzbereiches überstimmen. Nach Bestätigung der Werte werden diese direkt in die diversen Regler der Kupolofensteuerung übernommen. Danach läuft die Steuerung automatisiert ab und gibt Warnmeldungen an den Ofenbetreiber aus, wenn sich im Schmelzprozess Abweichungen zu den geplanten Eingriffs- und Toleranzgrenzen aus den Parametertabellen ergeben. Damit wird sichergestellt, dass nicht die Automatisierung, sondern der Mensch die Entscheidungsgewalt über den Prozess besitzt.
In seiner derzeitigen Form vereint der EEM die Berechnung des Energiegehaltes des eingesetzten Kokses mit dem tatsächlich notwendigen Energiebedarf. Die Energiedifferenz wird mit einem einstellbaren Anteil in Form von Petrolkoks ausgeglichen (Bild 7). Berechnungsbasis ist die Addition von mehreren Sätzen in der Schmelzzone (Bild 8).
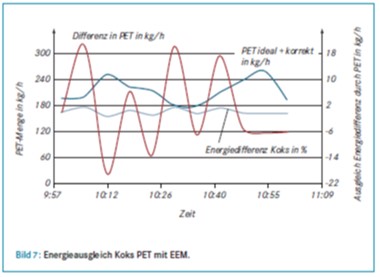
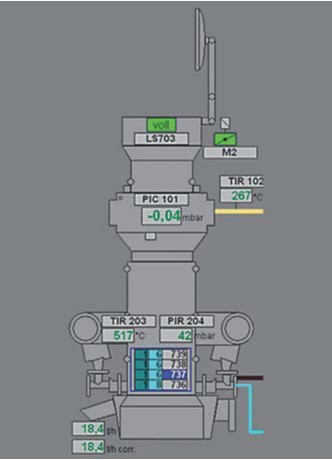
Die Grafik zeigt die letzten vier Satzfolgen auf, die energetisch und analytisch zusammengefasst werden. Der erforderliche Energieeintrag wird nach jedem geschmolzenen Satz neu berechnet und so durch die Einstellung der PET-, Wind- und O2-Menge satzweise gesteuert. In der Folge ergibt sich eine deutliche Vergleichmäßigung des Schmelzprozesses und der Abgaswirtschaft. In Bild 9 wird die reale Ofenfahrweise (EEM) mit technischem Sauerstoff aufgezeigt.
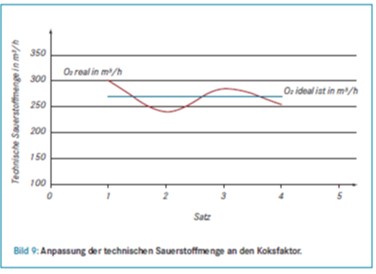
Ein weiteres wichtiges Kriterium ist der Energiegehalt des Gichtgases. Fallen der Energiebedarf (CO/CO2-Messung) sowie die Brennkammertemperatur, wird die Fahrweise angepasst. Es erfolgt eine flexible Zugabe von anteiligem Petrolkoks in Abhängigkeit zur automatischen Windund Sauerstoffkorrektur in engen Toleranzen. In Bild 10 wird der optimierte Energieeintrag durch die Vergleichmäßigung der CO-Konzentration aufgezeigt.
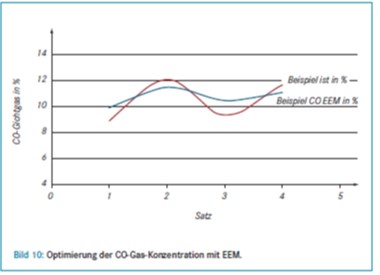
Steigerung von Effizienz und Qualität
Der Einsatz der Ofensteuerungssoftware EEM hat sich bei Gienanth durch eine Vielzahl positiver Effekte bemerkbar gemacht:
- deutlich verbesserte Gichtgasführung
- Vergleichmäßigung des Energiegehaltes des Gichtgases
- reduzierte und gleichmäßige Saugzugleistung geringerer Falschluftanteil über die Obergicht
- geringerer Fremdenergieeintrag in der Brennkammer
- engere Analysentoleranzen
- gleichmäßigere Analysen
- geringe Temperaturschwankungen
- schnelles Erreichen von Rinneneisenund Heißwindtemperatur.
Fazit
Die Ofensteuerungssoftware Energie-Effizienz-Manager leistet eine wichtige Hilfestellung beim Betrieb einer Heißwindkupolofenanlage. Denn der gezielte Einsatz von Wind, technischem Sauerstoff und Petrolkoks führt zu einem optimierten und berechenbaren Schmelzprozess. Der Kupolofen verliert dadurch vieles von seiner ursprünglichen „Magie“. Die beschriebene Optimierung der Prozessführung ist der Schlüssel zu einer deutlichen verbesserten Ofenführung im Verhältnis Metall und Koks. Damit steht auch ein präventiv einsetzbares, wichtiges Werkzeug zur Verfügung, das den Austritt von sichtbarer Rauchentwicklung aus der Ofenanlage minimiert und so die Entscheidungsfindung für die Regelparameter in der Prozessführung vereinfacht.
Heinz Kadelka, VMM Market Development Metallurgy, Linde AG, Gases Division, Düsseldorf, und Mike Weber, Gienanth GmbH, Eisenberg