Geringere Energiekosten und CO2-Emissionen bei der Schmelzeversorgung
Forschungskonsortium entwickelt innovatives Technologie- und Anlagenkonzept
Von Stefan Scharf, Magdeburg, Jörg Tom Felde, Nürnberg, Hagen Stein, Bad Langensalza
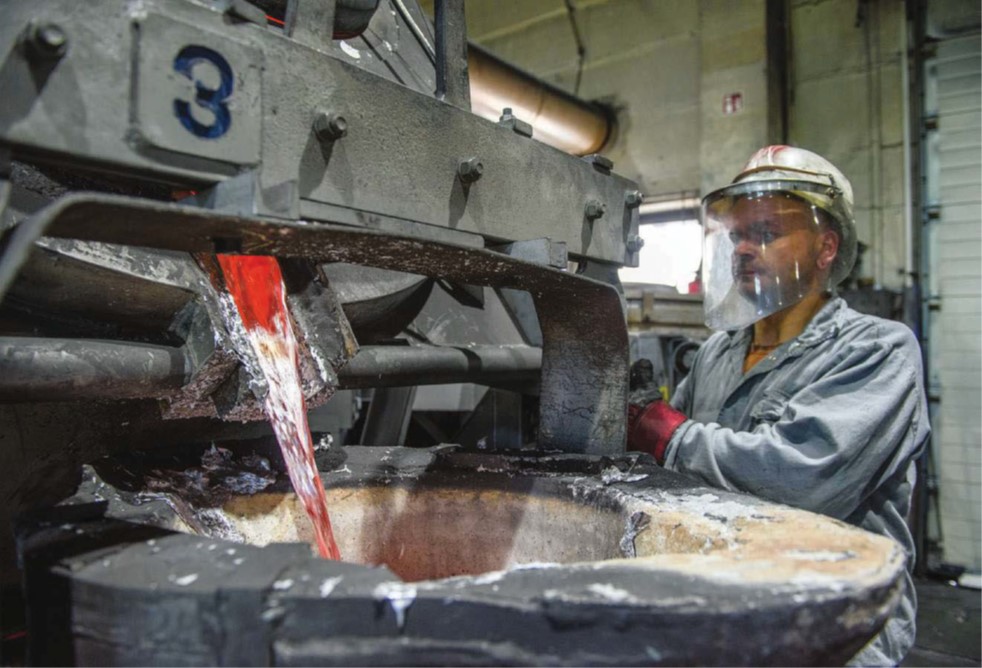
In Gießereien ist zum Schmelzen und Beheizen sehr viel Energie erforderlich.
Erschienen in GIESSEREI 08/2019
Mit Blick auf das gesteigerte Bewusstsein für planetare Grenzen und die Verantwortung für die Lebensgrundlagen kommender Generationen besteht eine der aktuell akuten industriellen Herausforderungen darin, anforderungsgerechte Prozesse und Lösungen zu entwickeln, die sich durch einen ressourcenschonenden Materialeinsatz sowie eine effiziente Nutzung der benötigten Energieträger auszeichnen. In der metallverarbeitenden Industrie, insbesondere in Gießereien, wird besonders viel Energie verbraucht und entsprechend auch viel CO2 erzeugt. Ein neu entwickeltes Technologie- und Anlagenkonzept, das auf der diesjährigen Hannover Messe der Öffentlichkeit präsentiert wurde, ermöglicht erstmals eine hocheffiziente dezentrale Schmelzeversorgung, mit der Leichtmetall-Gießereien künftig bis zu 60 Prozent der produktionsbedingten Energiekosten und 80 Prozent der anfallenden CO2-Emissionen einsparen können.
Eine energieeffiziente und nachhaltige Fertigung ist für die künftige Wettbewerbsfähigkeit von klein- und mittelständischen Unternehmen der metallverarbeitenden Industrie von elementarer Bedeutung. Vor dem Hintergrund der global stetig steigenden Energiepreise sowie drohender Strafzahlungen für die Emission von Schadstoffen, gleichwohl aber auch vor dem Hintergrund einer scheinbar unaufhaltsam zunehmenden Erderwärmung und einem wachsenden ökologischen Verantwortungsbewusstsein, gilt es heutzutage daher mehr denn je, anforderungsgerechte Lösungen zu entwickeln, die einen ressourcenschonenden Materialeinsatz sowie eine nachhaltige Nutzung der zur Verfügung stehenden Energieträger ermöglichen und dabei die Summe der klimaschädigenden Schadstoffemissionen (insbesondere CO2) auf ein Minimum reduzieren. Politische Restriktionen, sowohl auf globaler Ebene als auch auf Bundesebene, verknüpfen dabei bewusst ökologische und ökonomische Aspekte miteinander, um die avisierten Zielstellungen zu erreichen. In diesem Kontext bekommt der Produktionsfaktor Energie auch aus wirtschaftlicher Sicht eine immer bedeutsamere Rolle. So betragen aktuell nach Angaben des Statistischen Bundesamtes die in deutschen Gießereien anfallenden Energiekosten inzwischen ca. 25 % der gesamten Bruttowertschöpfung [1].
Ein durch ein Forschungskonsortium, bestehend aus dem Fraunhofer-Institut für Fabrikbetrieb und -automatisierung IFF (Magdeburg), der Otto-von-Guericke Universität (Magdeburg), der promeos GmbH (Nürnberg) sowie der LGL GmbH (Bad Langensalza), entwickeltes Konzept zur dezentralen Schmelzeversorgung in NE-Gießereien ermöglicht – basierend auf einer innovativen, modular erweiterbaren Brennertechnologie – eine komplette Reorganisation der innerbetrieblichen Materialflüsse. Dadurch werden der Primär-Energieeinsatz sowie die emittierten Schadstoffe signifikant reduziert und gleichzeitig die Gussqualität sowie die Fertigungsflexibilität deutlich erhöht. Möglich wird dies durch den Einsatz neuartiger Heiz-Dockingstationen („heat docks“) und mobiler Tiegelpfannen („mpots“) sowie durch die innovative Brennertechnologie, die anfallende Abwärme thermisch wiederverwerten kann.
Stand der Technik
Bislang wird in Gießereien, speziell in Nichteisengießereien, das zu verarbeitende Schmelzgut in einem abgestuften Prozess mehrfach umgefüllt und dabei permanent erhitzt. Neben offenflammigen Gasbrennern wird für das Schmelzen und Beheizen des Metalls trotz offenkundiger ökonomischer und ökologischer Nachteile überwiegend elektrischer Strom verwendet. Diese konventionelle Art der Prozessführung und die damit verbundenen Umschöpfprozesse beeinträchtigen die Gussqualität und erfordern aufwendige Maßnahmen der Schmelzebehandlung. Zudem sind die bislang bekannten Prozesse durch einen entsprechend hohen Energie- und Ressourcenbedarf gekennzeichnet.
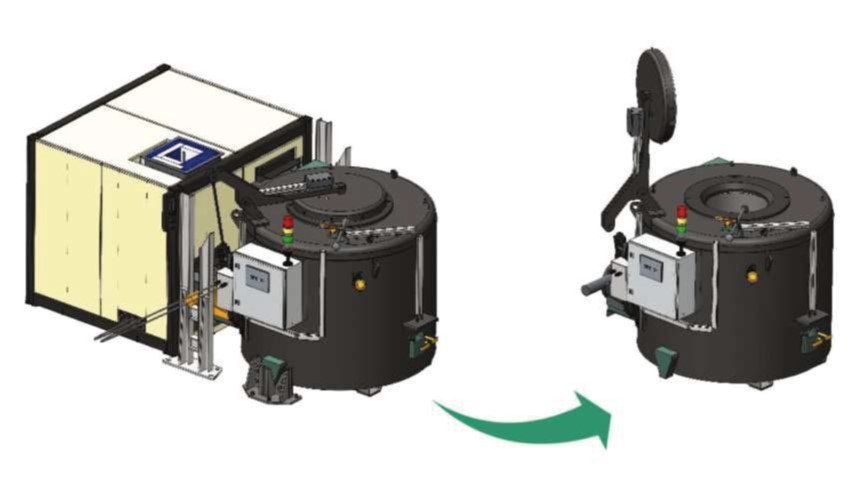
Bild 1: Mobile Tiegelpfanne mit „heat-dock“.
Unkonventionelle neue Technologie
Mit ihrem neuen Ansatz setzten die Projektpartner stattdessen auf ein unkonventionelles, aber hocheffizientes Verfahren, dessen Entwicklung und Erforschung unter dem Projektnamen „ETAL“ noch bis Mitte 2020 vom Bundesministerium für Wirtschaft und Energie gefördert wird.
Dabei nutzt ein neu konzipiertes modular erweiterbares Brennersystem den günstigen und ökologisch sinnvollen Primärenergieträger Gas so für die Wärmeerzeugung, dass eine bisher nur aus elektrisch beheizten Aggregaten bekannte Regelgüte und Homogenität erzielt wird. Herauszuheben ist zudem, dass durch diese Neuentwicklung erstmalig vorgewärmte Verbrennungszuluft und somit die anfallende Abwärme prozesssicher wiederverwertet werden kann, was die Technologie besonders effizient macht.
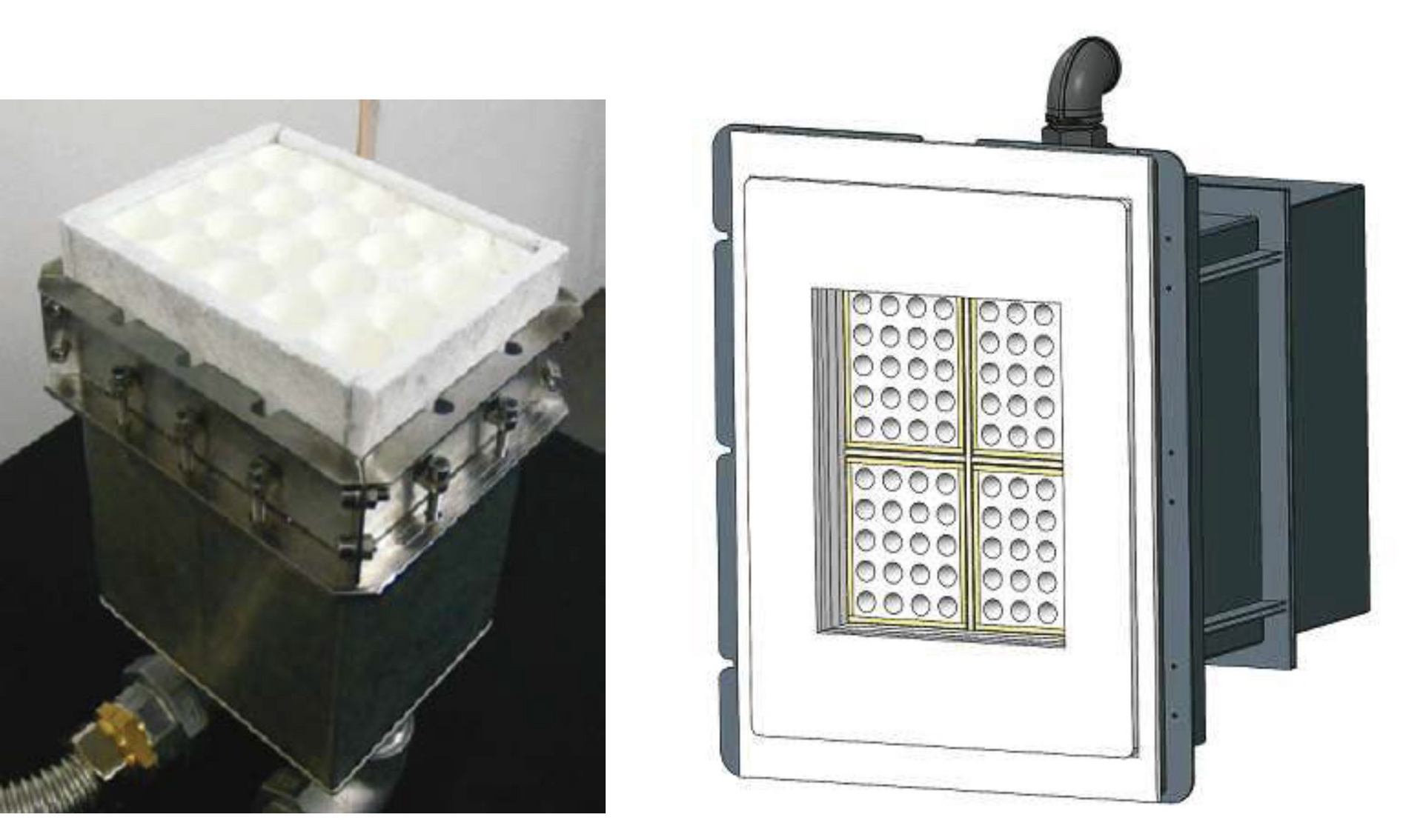
Innovative modulare Brenner
Vollvormischende Brenner der Firma promeos arbeiten bisher als Kaltluftbrenner und zeichnen sich durch die Abstinenz raumgreifender Diffusionsflammen aus. Die flächige und flammenfreie Verbrennung des Gas-Luft-Gemisches erlaubt es, Wärme als homogene Infrarot-Strahlung und mit gleichmäßiger Konvektion zur Verfügung zu stellen. Die Vorteile sind:
- keine Hot-Spots, da freie Flammen fehlen
- stufenlose Regelbarkeit der Wärmeleistung
- beliebige Anpassung der Brennergeometrie
- beliebige Skalierung der Brennerleistung
- hohe Leistungsdichte von bis zu 4 MW/m2
Aufgrund der Zündbedingungen der industriell verwendeten Brenngase (Erdund Flüssiggase) ist eine Vollvormischung von Luft hoher Temperatur mit Brenngas ausgeschlossen. Um jedoch die oben genannten Vorteile auch mit vorgewärmter Luft hoher Temperatur und somit das Ziel der angestrebten Abwärmewiederverwertung realisieren zu können, entwickelte promeos das Konzept eines multi-zellularen Flächenbrenners, welcher durch Parallelschaltung einzelner Verbrennungszellen mit dezentraler Gemischaufbereitung die Realisierung beliebig 2-D-skalierbarer Brennermodule für Hochtemperaturprozesse erlaubt.
Wichtige Entwicklungsinhalte umfassen dabei die sichere, modulare Medienversorgung der einzelnen Brenner-Zellen sowie die Materialauswahl und -verarbeitung der 3-D-strukturierten Brennerzellen selbst. Ermöglicht wird diese Verfahrensentwicklung u.a. durch moderne Simulationstechniken sowie den Einsatz generativer Fertigungsverfahren, was im Zusammenspiel der Forschungskooperation erfolgreich umgesetzt wurde.
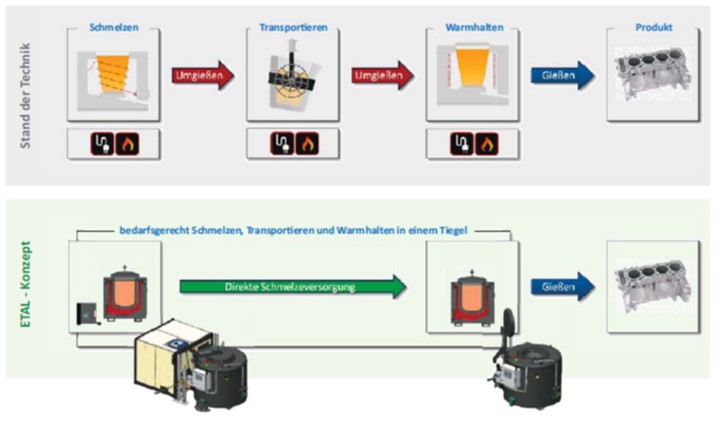
Erfolgreiches Prozess- und Anlagenkonzept
Diese Brennerentwicklung wieder umstellt die grundlegende Voraussetzung für ein erfolgreiches Gelingen des Prozessund Anlagenkonzeptes dar, das den konventionell üblichen Prozessablauf künftig massiv verkürzt und erheblich vereinfacht. Das Metall wird dann in vollkommen mobilen Tiegelpfannen, den „mpots“, eingeschmolzen, transportiert und warmgehalten, wodurch die qualitätsbeeinträchtigenden Umschöpfvorgänge komplett entfallen und sich der gesamte Prozess deutlich effizienter gestaltet.
Das Besondere dabei ist, dass die „mpots“ keine feste Beheizungslösung brauchen, vielmehr beziehen sie die zum Schmelzen erforderliche Energie an den neuartigen Docking-Stationen („heat-docks“), die mithilfe der neuen Brenner arbeiten. Je nach erforderlicher Schmelzkapazität lassen sich mehrere „heat docks“ koppeln. Dann besteht auch die Möglichkeit, die anfallende Abwärme zusätzlich auch kaskadenartig an die Partnerstation weiterzugeben, um so zusätzliche Effizienzpotenziale zu erschließen.
Nach dem Einschmelzen verfahren die „mpots“ an die Gießplätze und versorgen diese entsprechend bedarfsgerecht mit flüssigem Metall. Dabei funktionieren sie ähnlich einer Thermoskanne und nutzen die zuvor bezogene Heißluft gezielt als Wärmeisolationspolster. Sofern erforderlich können an den Gießplätzen optional (z.B. wenn beim Abgießen kleinvolumiger Bauteile der „mpot“ übermäßig lange am Gießplatz verbleiben muss) weitere, entsprechend kleiner dimensionierte „heat docks“ mögliche Wärmeverluste des Metalls ausgleichen, was den systemischen spezifischen Energieverbrauch senkt. Bei Bedarf können auch in einer beliebigen Anzahl solcher „mpots“ komplett unterschiedliche Legierungen verarbeitet werden, wodurch der zunehmenden Herausforderung einer stetig steigenden Produktdiversität Rechnung getragen
wird.
Durch den Einsatz eines solchen volltransportablen Schmelz- und Warmhaltesystems, in dem die für die Gusserzeugung vorzuhaltende Metallmenge jeweils direkt in einem einzigen Tiegel eingeschmolzen, veredelt, warmgehalten und geschöpft wird, entfallen mindestens zwei Umfüllprozesse. Dadurch wird die Bildung der für die Gussqualität äußerst schädlichen Oxide signifikant reduziert und die mit der Schlackebildung einhergehenden Materialverluste werden minimiert.
Weitere Potenziale
Neben den energietechnischen Vorteilen eröffnen sich durch den innovativen Konzeptansatz und die damit einhergehende Loslösung von den bislang vorrangig krangebundenen Transportwegen der Schmelze, insbesondere auch aus Sicht der Produktionsplanung und Fertigungslogistik, komplett neue Möglichkeiten für die Gestaltung der innerbetrieblichen Materialflüsse. Hier ist eine erhebliche Senkung der Kreislaufmaterialquote und damit des indirekten Energieverbrauches zu erwarten. In diesem Zusammenhang sollen die Bereiche der eigentlichen Wertschöpfung, also die Gießplätze, im Sinne einer vollvernetzten Anlagentechnik die benötigte Schmelzlegierung künftig bedarfsgerecht („PULL“-Prinzipien) und jederzeit transparent an den „heat docks“ anfordern und anschließend direkt aus den bereitgestellten „mpots“ für den Gießprozess schöpfen.
Neue Sensortechnologie zur kontinuierlichen Prozessüberwachung
Eine ebenfalls im Projekt entwickelte sensorbasierte Monitoring-Technologie ermöglicht sowohl eine kontinuierliche Überwachung der Temperaturen und Füllstände als auch eine zielführende Kommunikation zwischen „mpot“ und „heat docks“. Dies bildet die Basis für eine künftig vollkommen automatisierte Prozessführung und demonstriert ein konkretes Anwendungsszenario für die digitalisierte Produktion der Zukunft.
Diese vollvernetzte Monitoring-Technologie (einschließlich sensorgestützter Hardware) soll künftig eine universelle, standardisierte, objektorientierte Echtzeit-Erfassung sowie eine Bewertung und Überwachung der Hochtemperaturprozesse ermöglichen. Die Nutzung dieser Informationen erlaubt die Ableitung vielfältiger betriebstechnischer Zusammenhänge wie den Ereignis- und Zustandsbezug der Anlagen, die Identität, Ortung und Qualitätsermittlung von Prozessen, Produkten und Betriebsmitteln sowie die Bewertung des damit verbundenen energetischen Zustands. Sie bietet damit eine intelligente und nachhaltige Entscheidungsgrundlage und damit die Grundvoraussetzung für eine künftig vollautomatisierte Prozesssteuerung.
Höhere Qualität und weniger Energieverbrauch
In Leichtmetall-Gießereien, für die das neue Verfahren entwickelt wurde, lassen sich so bis zu 60 Prozent der Energiekosten sowie bis zu 80 Prozent der damit zusammenhängenden CO2-Emissionen einsparen. Gleichzeitig werden die Produktionsflexibilität und die Produktqualität signifikant gesteigert. Die Förderung des Forschungsprojekts „ETAL“ durch das Bundesministerium für Wirtschaft und Energie (BMWi) erfolgt auf Grundlage des Rahmenprogramms „6. Energieforschungsprogramm“ zum Thema „Energieeffizienz in der Industrie“.
Dr.-Ing. Stefan Scharf, Geschäftsentwicklung, Fraunhofer-Institut für Fabrikbetrieb und -automatisierung IFF und Otto-von- Guericke-Universität Magdeburg, IFQ Dipl.-Ing. Jörg tom Felde, Leiter Engineering, promeos GmbH Dipl.-Ing. Hagen Stein, Geschäftsführer Leichtmetallgiesserei Bad Langensalza GmbH
Literatur
[1] Bundesverband der Deutschen Giesserei-Industrie (BDG) (Hrsg.): Die Gießerei-Industrie: Eine starke Branche in Zahlen.