Gusseisen mit Kugelgraphit
Werkstoff mit besonderen Eigenschaften
Inhalt dieser Seite
-
Austenitische Gusseisen mit Kugelgraphi
-
Carbidisches Gusseisen mit Kugelgraphit
-
Gusseisen mit Vermiculargraphit (GJV)
-
SiMo-Gusseisen
-
Weiterführende Informationen
-
Download
-
Autoren und Quellen
Neben den Normalsorten gibt es beim Gusseisen mit Kugelgraphit noch legierte Sorten mit speziellen Eigenschaften für erweiterte Anwendungsbereiche, die nachfolgend kurz vorgestellt werden. Für diese Sorten gibt es gesondertes Schriftmaterial bei der Zentrale für Gussverwendung in Düsseldorf, das unter den angegebenen Schrifttumsangaben bei Bedarf bezogen werden kann.
Austenitische Gusseisen mit Kugelgraphit
Die austenitischen Gusseisen mit Kugelgraphit nach EN 13835 sind hoch legierte Gusseisenwerkstoffe, die in Bezug auf Korrosionsbeständigkeit, Hitze- und Zunderbeständigkeit, Kaltzähigkeit, Nichtmagnetisierbarkeit, Verschleißbeständigkeit sowie besonders hohe oder niedrige thermische Ausdehnungskoeffizienten optimiert sind. Diese Werkstoffgruppe wird ausführlich in [10, 227, 228] beschrieben. Die Norm EN 13835 enthält insgesamt zehn Sorten mit Kugelgraphit.
Austenitische Gusseisen haben, wie der Name sagt, eine austenitische Grundmasse. Sie werden vielfach kurz mit dem Handelsnamen „Ni-Resist“ bezeichnet. Im Gegensatz zu den üblichen Normen für Gusseisen, wo nur die Eigenschaften vorgeschrieben werden, legt die Norm für die austenitischen Gusseisen wie bei legierten Stahlgusssorten auch die chemische Zusammensetzung fest, da die Eigenschaften hiervon in besonderem Maße abhängig sind. In der Tabelle 19 sind die mechanischen Eigenschaften nach EN 13835 und in der Tabelle 20 ein Vergleich der Sorten und Bezeichnungen nach DIN 1694 und EN 13833 sowie Handelsnamen enthalten.
Tabelle 19: Mechanische Eigenschaften der in EN 13835 genormten austenitischen Gusseisen
Werkstoffbezeichnung | Zugfes- tigkeit Rm [N/mm2)] | 0,2 %-Dehn- grenze Rp0,2 [N/mm2] | Bruch- dehnung A [%] | Mittelwert für die Kerb- schlagarbeit A min.3) [ J ] | Charpy-V Kerbschlag- arbeit Av2) [ J ] | Elastizitäts- modul E2) [kN/mm2] | Brinell- härte HB2) | Druck- festigkeit RD2) [N/mm2] | |
Kurzzeichen | Werkstoff- Nummer | ||||||||
Normalsorte | |||||||||
EN-GJLA-XNiCuCr15-6-2 | EN-JL3011 | 170 – 210 | – | 2 | – | – | 85 – 105 | 120 – 215 | 700 – 840 |
EN-GJSA-XNiCr20-2 | EN-JS3011 | 370 – 480 | 210 – 250 | 7 – 20 | 131) | 11 – 24 | 112 – 130 | 140 – 255 | – |
EN-GJSA-XNiMn23-4 | EN-JS3021 | 440 – 480 | 210 – 240 | 25 – 45 | 24 | 20 – 30 | 120 – 140 | 150 – 180 | – |
EN-GJSA-XNiCrNb20-2 | EN-JS3031 | 370 – 480 | 210 – 250 | 8 – 20 | 131) | 11 – 24 | 112 – 130 | 140 – 200 | – |
EN-GJSA-XNi22 | EN-JS3041 | 370 – 450 | 170 – 250 | 20 – 40 | 20 | 17 – 29 | 85 – 112 | 130 – 170 | – |
EN-GJSA-XNi35 | EN-JS3051 | 370 – 420 | 210 – 240 | 20 – 40 | – | 18 | 112 – 140 | 130 – 180 | – |
EN-GJSA-XNiSiCr35-5-2 | EN-JS3061 | 380 – 500 | 210 – 270 | 10 – 20 | – | 7 – 12 | 130 – 150 | 130 – 170 | – |
Sondersorte | |||||||||
EN-GJLA-XNiMn13-7 | EN-JL3021 | 140 – 220 | – | – | – | – | 70 – 90 | 120 – 150 | 630 – 840 |
EN-GJSA-XNiMn13-7 | EN-JS3071 | 390 – 470 | 210 – 260 | 15 – 18 | 16 | 15 – 25 | 140 – 150 | 120 – 150 | – |
EN-GJSA-XNiCr30-3 | EN-JS3081 | 370 – 480 | 210 – 260 | 7 – 18 | – | 5 | 92 – 105 | 140 – 200 | – |
EN-GJSA-XNiSiCr30-5-5 | EN-JS3091 | 390 – 500 | 240 – 310 | 1 – 4 | – | 1 – 3 | 90 | 170 – 250 | – |
EN-GJSA-XNiCr35-3 | EN-JS3101 | 370 – 450 | 210 – 290 | 7 – 10 | – | 4 | 112 – 123 | 140 – 190 | – |
1) Freigestellte Anforderung nach Vereinbarung zwischen Hersteller und Käufer
2) Nicht genormt
3) Mittelwert für die Kerbschlagarbeit aus 3 Versuchen an Charpy-V-Proben nach EN 10045-1
Tabelle 20: Übersicht der nationalen und internationalen (teilweise nicht mehr gültigen ) Normen und Bezeichnungen der austenitischen Gusseisen und übliche Handelsnamen
Werkstoffbezeichnung nach EN 13835 | DIN1694:1981 | ASTM A 436: 1984 | ASTM A 439:1983 ASTM A 571:1984 | BS 3468: 1962 | BS 3468: 1986 | ISO2892: 1973 BS3468: 1974 | NFA32-301: 1992 | Inter- nationaler Handels- name | |
Kurzzeichen | Werkstoff- Nummer | ||||||||
Lamellengraphit | |||||||||
EN-GJLA-XNiCuCr15 -6-2 | EN-JL3021 | GGL-NiMn 13 7 | - | - | - | - | L-NiMn 13 7 | FGL Ni13 Mn7 | Nomag |
EN-GJLA-XNi Mn13-7 | EN-JL3011 | GGL-NiCuCr 15 6 2 | Type 1 | - | AUS 101A | F1 | L-NiCuCr 15 6 2 | FGL Ni15 Cu6 Cr 2 | Ni-Resist 1 |
- | - | GGL-NiCuCr 15 6 3 | Type 1b | - | AUS 101B | F1 | L-NiCuCr 15 6 3 | FGL Ni15 Cu6 Cr3 | Ni-Resist 1b |
- | - | GGL-NiCr 20 2 | Type 2 | - | AUS 102A | F2 | L-NiCr 20 2 | FGL Ni20 Cr2 | Ni-Resist 2 |
- | - | GGL-NiCr 20 3 | Type 2b | - | AUS 102B | F2 | L-NiCr 20 3 | FGL Ni20 Cr3 | Ni-Resist 2b |
- | - | GGL-NiSiCr 20 5 3 | - | - | AUS 104 | - | L-NiSiCr 20 5 3 | FGL Ni20 Si5 Cr3 | - |
- | - | Type 3 | - | AUS 105 | F3 | L-NiCr 30 3 | FGL Ni30 Cr3 | Ni-Resist 3 | |
- | - | GGL-NiCr 30 3 | Type 4 | - | - | - | L-NiSiCr 30 5 5 | FGL Ni30 Si5 Cr5 | - |
- | - | GGL-NiSiCr 30 5 5 | Type 5 | - | - | - | L-Ni35 | FGL Ni35 | - |
Kugelgraphit | |||||||||
EN-GJSA-XNiMn13-7 | EN-JS3071 | GGG-NiMn13 7 | - | - | - | S6 | S-NiMn 13 7 | FGS Ni13 Mn7 | Nodumag |
EN-GJSA-XNiCr20-2 | EN-JS3011 | GGG-NiCr 20 2 | - | D2 | AUS 202A | S2 | S-NiCr 20 2 | FGS Ni20 Cr2 | Ni-Resist D-2 |
EN-GJSA-XNiCrNb20 -2 | EN-JS3031 | GGG-NiCrNb 20 2 | - | - | - | S2W | - | FGS Ni20 Cr2 Nb 0,15 | - |
- | - | GGG-NiCr 20 3 | - | D2B | AUS 202B | S2B | S-NiCr 20 3 | FGS Ni20 Cr3 | Nicrosilalspheronic |
- | - | GGG-NiSiCr 20 5 2 | - | - | - | - | - | FGS Ni20 Si5 Cr2 | Ni-Resist D-2C |
EN-GJSA-XNi22 | EN-JS3041 | GGG-Ni 22 | - | D2C | AUS 203 | S2C | S-Ni 22 | FGS Ni22 | Ni-Resist D-2M |
EN-GJSA-XNiMn23-4 | EN-JS3021 | GGG-NiMn 23 4 | - | D2M1) | - | S2M | S-NiMn 23 4 | FGS Ni23 Mn4 | Ni-ResistD-3A |
- | - | GGG-NiCr 30 1 | - | D3A | - | - | S-NiCr 30 1 | FGS Ni30 Cr1 | Ni-Resist D-3 |
EN-GJSA-XNiCr30-3 | EN-JS3081 | GGG-NiCr 30 3 | - | D3 | AUS 205 | S3 | S-NiCr 30 3 | FGS Ni30 Cr3 | - |
- | - | GGG-NiSiCr 30 5 2 | - | - | - | - | - | FGS Ni30 Si5 Cr2 | - |
EN-GJSA-XNiSiCr30 -5-5 | EN-JS3091 | GGG-NiSiCr 30 5 5 | - | D4 | - | - | S-NiSiCr 30 5 5 | FGS Ni30 Si5 Cr5 | Ni-Resist D-4 |
EN-GJSA-XNi35 | EN-JS3051 | GGG-Ni 35 | - | D5 | - | - | S-Ni 35 | FGS Ni35 | Ni-Resist D-5 |
EN-GJSA-XNiCr35-3 | EN-JS3101 | GGG-NiCr 35 3 | - | D5B | - | - | S-NiCr 35 3 | FGS Ni35 Cr3 | Ni-Resist D-5B |
EN-GJSA-XNiSiCr35 -5-2 | EN-JS3061 | GGG-NiSiCr 35 5 2 | - | D5S | - | S5S | - | FGS Ni35 Si5 Cr2 | Ni-Resist D-5S |
1) Austenitisches Gusseisen mit Kugelgraphit für Druckbehälter für Tieftemperaturbetrieb
Um den Austenit bis zu tiefen Temperaturen stabil zu machen, ist ein Mindestgehalt an Nickel, Mangan und Chrom erforderlich. Die drei Elemente werden in einem Nickel-Äquivalent = % Ni + % Cr + 2 x % Mn zusammengefasst, das über etwa 20 % liegen sollte. In Fällen, wo ein absolut stabil austenitisches Gefüge verlangt wird, sollte es mindestens 23,5 % sein. Bei niedrigeren Werten kann sich unter Umständen beim Spannungsarmglühen oder bei tiefen Temperaturen Martensit bilden, der den Werkstoff versprödet. Ein Ersatz von Nickel durch Mangan ist nur bei der kaltzähen Sorte möglich, da Mangan keinen Beitrag zur Korrosionsbeständigkeit oder Hitzebeständigkeit liefert. Chrom muss aus Gründen der Zähigkeit und Bearbeitbarkeit auf 2 bis 3 % begrenzt werden.
Fast alle Sorten haben gute bis sehr gute Korrosionsbeständigkeit, Zunderbeständigkeit und Kaltzähigkeit. Die wichtigsten Sorten sind EN-GJSA-XNiCr20-2 und ENGJSA-XNiCrNb20-2 als korrosionsbeständige Sorten und EN-GJSA-XNiSiCr35-5-2 als hitzebeständiger Werkstoff. Der Nickelgehalt ist wesentlich für die Korrosionsund Zunderbeständigkeit. Chrom ist vor allem für die Verschleißbeständigkeit wichtig, Silicium für hohe Zunderbeständigkeit.
Der Nickelgehalt beeinflusst die physikalischen Eigenschaften des Werkstoffs. Der thermische Ausdehnungskoeffizient ist bei etwa 20 % Ni am höchsten, sinkt mit steigendem Nickelgehalt und erreicht bei etwa 35 % ein Minimum. Die Sorten mit rund 20 % Nickel und die manganhaltigen Sorten sind nicht magnetisierbar. Von etwa 26 % Ni an wird das austenitische Gusseisen wieder magnetisch.
EN-GJSA-XNiCr20-2 und EN-GJSAXNiCrNb20-2 werden vor allem als korrosionsbeständige Werkstoffe verwendet. Im Gegensatz zu Edelstählen sind sie allerdings nicht passivierbar, sondern ihre Korrosionsbeständigkeit beruht auf einer Schutzschicht aus nickelhaltigen Reaktionsprodukten. Das Haupteinsatzgebiet sind Seewasser beständige Gussteile, da sie im Gegensatz zu den meisten Edelstählen in stagnierendem Meerwasser nicht durch Lochfraßkorrosion gefährdet sind. Gelegentlich finden Sie auch als warmfeste und zunderbeständige Werkstoffe Verwendung.
EN-GJSA-XNi22 und EN-GJSA-XNiMn23-4 werden in der Tieftemperaturtechnik eingesetzt. Vor allem EN-GJSA-XNiMn23-4 ist speziell als Tieftemperaturwerkstoff entwickelt worden und hat nur eine geringe Korrosionsbeständigkeit. EN-GJSA-XNi30-3 hat eine erhöhte Korrosionsbeständigkeit und findet auch als Werkstoff Verwendung, bei dem durch Variation des Nickelgehaltes der thermische Ausdehnungskoeffizient in relativ engen Grenzen eingestellt werden kann.
EN-GJSA-XNiSiCr30-5-5, EN-GJSAXNiCr30-3 und EN-GJSA-XNiCr35-5-2 zeichnen sich dank des hohen Siliciumgehalts durch eine hohe Zunderbeständigkeit aus und sind aufgrund des niedrigen thermischen Ausdehnungskoeffizienten auch gegen Temperaturwechsel und thermomechanische Beanspruchungen gut beständig [10, 229].
EN-GJSA-XNi35 wird als Werkstoff mit sehr niedrigem thermischem Ausdehnungskoeffizienten eingesetzt.
Aus EN-GJSA-XMnNi13-7 werden nichtmagnetisierbare Gussstücke hergestellt.
Ausführlich werden die austenitischen Gusseisensorten in [9 und 10] beschrieben. Die Quellen können bei der Zentrale für Gussverwendung in Düsseldorf bezogen werden.
Carbidisches Gusseisen mit Kugelgraphit
Die Verschleißbeständigkeit von Gusseisen mit Kugelgraphit kann durch freie Carbide, das heißt Anteile von Ledeburit, erheblich gesteigert werden. Carbidische Gusseisen mit Kugelgraphit lassen sich erzeugen, in dem eine an sich weiß erstarrende Gusseisenschmelze mit Magnesium behandelt, normales Gusseisen mit Kugelgraphit mit Chrom legiert oder die Schmelze gegen eine Schreckplatte oder in Kokille gegossen wird. Je nach Abstand von der abgeschreckten Oberfläche entsteht bei letztgenanntem Verfahren ein Gradientengefüge, bei dem der Carbidanteil von der Außenseite zum Kern hin abnimmt. Über die Einstellung der chemischen Zusammensetzung und der Impfung lässt sich der Carbidanteil in weiten Grenzen variieren (Tabelle 21).
Tabelle 21: Verschleißbeständige carbidische Gusseisen-Werkstoffe nach DIN EN, DIN, ASTM sowie deren Handelsnamen
Werkstoffsorte nach DIN EN 12 513 | Werkstoffsorte nach DIN 1695 | Werkstoffsorte nach ASTM A 532 | Handelsname | ||
Kurzzeichen EN- | Nummer EN- | Kurzzeichen | Nummer | ||
- | - | G-X 300 NiMo 3 Mg | 0.9610 | - | - |
GJN-HV350 | JN2019 | - | - | - | - |
GJN-HV520 | JN2029 | G-X 260 NiCr 4 2 | |||
GJN-HV550 | JN2039 | G-X 330 NiCr 4 2 | |||
GJN-HV600 | JN2049 | G-X 300 CrNiSi 9 5 2 | |||
GJN-HV600(XCr11) | JN3019 | - | - | Class II Type A 12 % Cr | - |
GJN-HV600(XCr14) | JN3029 | G-X 300 CrMo 15 3 G-X 300 CrMoNi 15 2 1 | 0.9635 0.9640 | Class II Type B 15 % CrMo | |
GJN-HV600(XCr18) | JN3039 | G-X 260 CrMoNi 20 2 1 | 0.9645 | Class II Type D 20 % CrMo | |
GJN-HV600(XCr23) | JN3049 | G-X 260 Cr 27 G-X 300 CrMo 27 1 | 0.9650 0.9655 | Class III Type A 25 % Cr | - |
Durch entsprechendes Legieren mit Nickel, Molybdän und Kupfer kann man eine martensitische oder bainitische Grundmasse erreichen, die ebenfalls zur Steigerung der Verschleißbeständigkeit beiträgt (Tabelle 22). Die Härte dieser Werkstoffe liegt je nach Carbidanteil und Grundmasse zwischen 300 und 550 HB. Der Vorteil eines derartigen Gefüges gegenüber rein carbidischen Gusseisensorten sind geringere Rissanfälligkeit und höhere Thermoschockbeständigkeit. Die Verschleißbeständigkeit ist allerdings etwas geringer.
Tabelle 22: Einteilung der wichtigsten verschleißbeständigen weißen Gusseisenwerkstoffe
Werkstoffgruppe | Typische Legierungselemente | Handelsname | Härte HB1 | Carbide | Grundmasse |
Perlitischer Hartguss (un- oder niedriglegiert) | - | - | bis 480 | Fe3C | Perlit |
Martensitische weiße Gusseisen (mittellegiert) | Ni, Cr | Ni-Hard 1 und 2 | bis 700 | M3C2 | |
Chromgusseisen (hochlegiert) | Cr, Ni, Si Cr, Mo, Ni, Cu | Ni-Hard 4 15-3, 20-2-1 | bis 700 bis 850 | M7C3, M3C2 Cr-Sondercarbide | Martensit, Austenit Martensit, Austenit |
Sondergusseisen | Cr, Mo, Ni Cu, Nb, V, W | - | bis 900 | Sondercarbide | Martensit, Austenit Ferrit |
1 Anhaltswerte
2 M = Fe, Cr, Mo
Die wichtigste Anwendung von carbidischen Gusseisen mit Kugelgraphit sind Walzwerkswalzen [230]. Weitere Anwendungen Verschleißteile (Bilder 206 und 207).
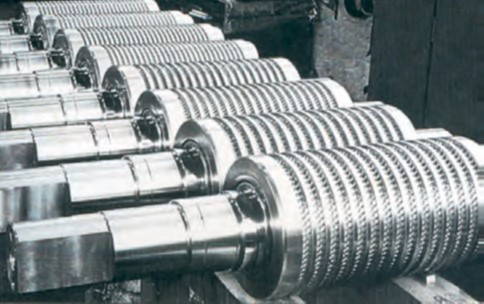
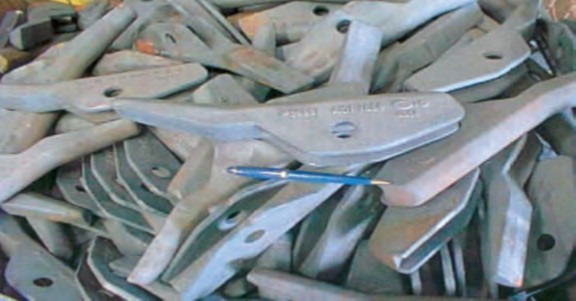
Eine neuere Entwicklung ist carbidhaltiges ADI, das als CADI bezeichnet wird. Es wird durch Legieren von ADI mit Chrom erzeugt und enthält nach der Wärmebehandlung etwa 5 % Carbide bei 0,5 % Cr und 17 % bei 1 % Cr. Seine Verschleißbeständigkeit liegt zwischen der von üblichem ADI und martensitischem weißen Gusseisen EN-GJN-HV550 (Ni-Hard 1) [231 - 232] (Bild 207). Weiterführende Informationen zum CADI sind in [232] und zu den Carbidischen Gusseisen in [233] enthalten, die bei der Zentrale für Gussverwendung in Düsseldorf bezogen werden können.
Gusseisen mit Vermiculargraphit (GJV)
Gusseisen mit Vermiculargraphit ist seit 2006 international in ISO 16112 „Cast iron with compacted (vermicular) graphite“ [234] genormt. Die Norm basiert im Wesentlichen auf dem VDG-Merkblatt W 50 [235] und der ASTM-Norm A842-85 [236]. Es wird in ähnlicher Weise wie Gusseisen mit Kugelgraphit durch Schmelzbehandlung mit Magnesium hergestellt, daher auch die kompakte Ausbildungsform des Graphits. Früher wurde es als ein „Zwischending“ zwischen Gusseisen mit Lamellen- und Gusseisen mit Kugelgraphit betrachtet, dennoch ist es ein eigenständiger Werkstoff, der hier erwähnt wird, damit der Unterschied zum Gusseisen mit Kugelgraphit deutlich wird.
Seine Zwischenposition ist eindrucksvoll im Bild 209 gezeigt.
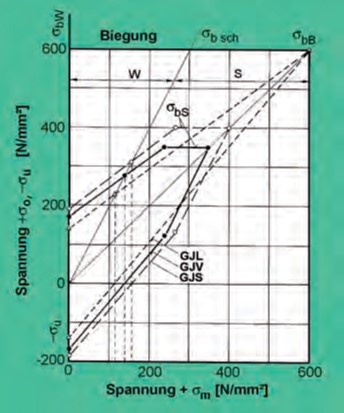
Näher am Werkstoff mit Lamellengraphit (GJL) sind Wärmeleitfähigkeit, Dämpfungsvermögen sowie Gleit- und Reibverhalten, die sämtlich auf die GJL-ähnliche Verzweigung des korallenbaumartig kristallisierenden Graphits (Bild 210) zurückzuführen sind.
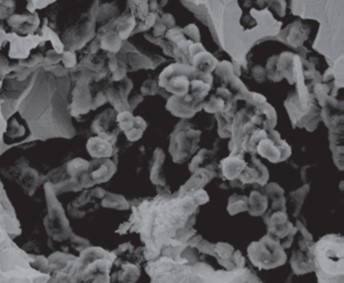
Dieser Graphit bricht zum Beispiel unter Reibbelastung nicht aus der metallischen Grundmasse heraus, sondern bleibt fest darin verankert. Näher am Werkstoff mit Kugelgraphit (GJS) sind jedoch E-Modul, und Dauerwechselfestigkeit. Diese Gemeinsamkeiten, merkwürdigerweise aber auch die Note „ausreichend“ in Duktilität, die ihm eine GJL-ähnliche hohe zulässige Flächenpressung verleiht, definieren die erwähnte Eigenständigkeit und den vorzugsweisen Einsatz von GJV im Motorenbau.
Nach der „Neuentdeckung“ des GJV zu Beginn der neunziger Jahre des 20. Jhs., als es erstmalig möglich wurde, die Grenzen zu GJL einerseits und zu GJS andererseits metallurgisch zu kontrollieren, werden Bauteile für diesen Anwendungsbereich wie Zylinderblöcke- und -köpfe sowie Zylinderlaufbüchsen vom Schiffsdiesel bis zum PKW-Motor in großen Stückzahlen produziert. Weitere Beispiele sind Abgasrohre sowie Pumpen- und Hydraulik-Ventilgehäuse. GJV ist aus der einst prophezeiten „Nischenposition“ längst herausgetreten.
GJV wird in den Festigkeitsklassen von 300 bis 500 N/mm2 geliefert. Die Daten in der Tabelle 23 wurden auszugsweise der ISO 16112 entnommen.
Tabelle 23: Mechanische Eigenschaften von Gusseisen mit Vermiculargraphit, gemessen an Proben aus getrennt gegossenen Probekörpern nach VDG-Merkblatt W 50
Werkstoff EN-... | Rm [N/mm²] | Rp0,2 [N/mm²] | A [%] | E-Modul [kN/mm²] | λ (23 °C) [W/m.K] | HBW |
GJV-300 | 300 - 375 | 210 - 295 | 1,5 | 130 - 145 | 45 | 140 - 210 |
GJV-350 | 350 - 425 | 260 - 335 | 1,5 | 135 - 150 | 45 | 160 - 220 |
GJV-400 | 400 - 475 | 300 - 375 | 1,0 | 140 - 150 | 40 | 180 - 240 |
GJV-450 | 450 - 525 | 340 - 415 | 1,0 | 145 - 155 | 40 | 200 - 250 |
GJV-500 | 500 - 575 | 380 - 455 | 0,5 | 145 - 160 | 35 | 220 - 260 |
Die Zugfestigkeit von GJV ist wanddickenabhängig und lässt sich für verschiedene Querschnitte aus der notwendigerweise bekannten Zugfestigkeit der getrennt gegossenen sogenannten Y-Probe wie folgt berechnen:
Rmy = Rmx + 0,50 (ln Mx – ln My) (12)
Darin sind
Rmy - unbekannte Zugfestigkeit eines Querschnitts mit Modul My
Rmx - bekannte Zugfestigkeit der getrennt gegossenen Probe mit dem Modul My
Modul -Verhältnis des Volumens eines Querschnitts zu dessen wärmeführender Oberfläche (V/O) in cm.
Für eine Platte beträgt er etwa die halbe Wanddicke und bei einem Rundstab ein Viertel des Durchmessers in cm.
Eine auf der Basis von etwa 500 Messungen basierende Korrelation zwischen Dehngrenze und Zugfestigkeit lautet:
Rp0,2 = 0,8 . Rm - 5 (13)
Ausführliche Informationen zum Werkstoff Gusseisen mit Vermiculargraphit sind in [237] enthalten. Die Informationsschrift kann bei der Zentrale für Gussverwendung in Düsseldorf angefordert werden.
SiMo-Gusseisen
Während GJV-400SiMo als Werkstoff für Abgaskrümmer schon eine lange Tradition hat, wurde GJS erst in den 1960er Jahren für diesen Zweck erprobt. Die ersten Tests wurden von GM-Opel im Rahmen einer Diplomarbeit [238] durchgeführt. Als Versuchobjekt dienten auf Restwanddicken von 3, 3,3 und 3,6 mm aufgebohrte Probestäbe (Bild 211).
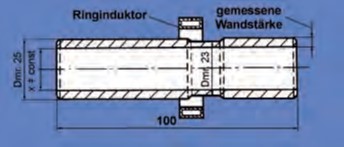
Ziel war eine Simulation der Temperaturwechselbelastung eines Abgasrohres zwischen 20 und 600 beziehungsweise 700 °C. Als Bewertungsmaßstab diente eine in Vorversuchen erstellte Richtreihe mit sechs Rissklassen, Durchriss nicht inbegriffen. Geprüft wurden EN-GJS-700-2, GJV-400SiMo sowie auch zwei Varianten des Gusseisens mit Lamellengraphit (GJL-250CrMo und GJL-250MoSnN), die zuvor im Hinblick auf Verwendung für Pkw-Zylinderköpfe geprüft worden waren, und von denen die zweite so erfolgreich war, dass sie auch heute noch Einsatz findet. Darüber wurde bereits berichtet [239]. Die chemische Zusammensetzung der drei Werkstoffe enthält Tabelle 24.
Tabelle 24: Chemische Zusammensetzung der im Bild 213 dargestellten Werkstoffe (in [%])
Werkstoff | C | Si | Mn | Cu | Cr | Mo | Mg |
GJL-250 CrMo | 3,38 | 2,22 | 0,56 | 0,33 | 0,38 | 0,59 | - |
GJL-250 MoSnN | 3,47 | 1,74 | 0,56 | 0,30 | 0,19 | 0,27 | - |
GJV-400 SiMo | 3,72 | 3,08 | 0,35 | 0,09 | 0,05 | 0,80 | 0,025 |
GJS-700 | 3,58 | 2,25 | 0,29 | 1,05 | 0,06 | 0,01 | 0,062 |
Die Ergebnisse dieser Tests für 700 °C sind aus Bild 213 ersichtlich. GJL-250CrMo versagte nahezu linear, das ferritische GJV-400SiMo und das ursprünglich perlitische GJS-700 erwiesen sich als praktisch gleichwertig, wobei im Fall von GJS zu erwähnen ist, dass nach 600 Zyklen der Perlit nur bis zur körnigen Ausbildung umgewandelt wurde. Es lag also nahe, den Werkstoff von vornherein in die „SiMo“- Klasse zu erheben. und aus der nodularen Graphitausbildung gegenüber GJV Vorteile zu gewinnen.
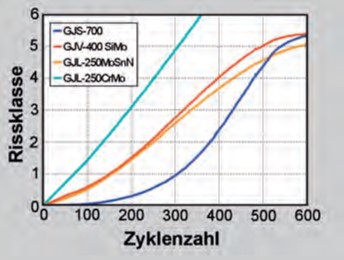
Von den beiden GJL-Sorten wurde leider nur die „bessere“ metallographisch untersucht: Nach 600 Zyklen fand noch keine Ferritisierung statt. Der Perlit und die Legierungscarbide kugelten sich teilweise ein und die Grundmasse enthielt neben Restsorbit auch kubischen Martensit. Dies ist zweifellos in ersten Linie Ergebnis der hohen Wärmeleitfähigkeit. Ein solches „Vergütungsgefüge“ ist regelmäßig bei den sich autonom regenerierenden Bremsscheiben aus dem GJL-Werkstoff „VARIFER zu beobachten. Die Tests werden heute hauptsächlich unter den realen Bedingungen eines Motorprüfstands durchgeführt und decken eine breit angelegte Verhaltensmatrix ab. Sie sind von Werk zu Werk verschieden und z.T. vertraulich.
Nachdem GJV-400SiMo bei Abgastemperaturen in der Größenordnung um 800 bis 850 °C praktisch die Grenzen der Leistungsfähigkeit erreichte, setzte man auf GJS-500SiMo mit über 5 % Si und etwa 1 % Mo, das Abgastemperaturen bis
950 °C widerstehen sollte. Zweckdienlich waren dabei die Verschiebung des Umwandlungsintervalls α-γ zu höheren Temperaturen. Sie ist Ergebnis der gemeinsamen Wirkung von Silicium, Chrom und Molybdän, die alle das γ-Gebiet stark einengen. Andererseits ist GJS gegenüber GJV wesentlich beständiger gegen innere Oxidation.
Im Verlauf der Beanspruchung überzieht sich die Oberfläche des Gussteils mit einer schützenden Fayalitschicht. Risse in dieser Schicht führen beim GJS nur zu einer weiteren Fayalitbildung. Dank der isolierten Graphiteinschlüsse findet aber kein Eindringen des Sauerstoffs in das Innere des Gussteils statt. Im GJV sind die Graphiteinschlüsse miteinander mehr oder weniger stark vernetzt, und eine Verzunderung entlang der Phasengrenzen Graphit/Matrix kann nicht mehr aufgehalten werden, es sei denn, die Verästelung wird durch metallurgische Maßnahmen begrenzt. Die Forderung nach einer solchen Begrenzung ist zum Beispiel Bestandteil der VW-Norm 50021 [240].
Aber auch GJS hat Nachteile:
- Höhere Siliciumgehalte verspröden den Ferrit. Zusammen mit Spannungen, die durch einen hohen E-Modul aufgebaut werden, kann dies bei einem Bodenkontakt im Fahrbetrieb zu Abrissen führen.
- Der höhere E-Modul führt, gepaart mit niedriger Wärmeleitfähigkeit, zum Verzug. Die niedrige Wärmeleitfähigkeit wiederum und damit ein hoher Temperaturunterschied zwischen kalter und warmer Seite des Gussteils kann bei hohen Abgastemperaturen vor allem in der kritischen Situation des Motorabschaltens zu Rissen führen.
Auf diese Weise müsste die Verwendung von GJS-500SiMo bei hohen Abgastemperaturen auf Fahrzeuge mit viel Bodenfreiheit und/oder Motoren mit der kühlerseitig eingebauten Abgasanlage beschränkt werden.
Die „magische“ Zahl von 1050 °C ist ein asymptotischer Wert, de facto werden bei dieser Abgastemperatur bereits austenitische Sorten eingesetzt.
Eine Übersicht der wichtigsten Merkmale der GJS-Werkstoffe für Abgasanlagen ist in den Tabellen 25 und 26 enthalten. Für weiterführende Informationen sei die Quelle [8] empfohlen.
Tabelle 25: Chemische Zusammensetzung einiger GJS-Werkstoffe für Abgasanlagen (in [%])
SAE J2582 (Entwurf) | |||||
Werkstoff | C | Si | Mo | Cr | Ni |
1 | 3,5 - 4,5 | max. 0,5 | |||
2 | idem | 0,51 - 0,70 | |||
3 | idem | 0,71 - 1,00 | |||
VW 50021:2006-12 | |||||
GJS-XSiMo5-1 | 3,0 - 3,6 | 4,0 - 5,0 | 0,80 - 1,00 | max. 0,5 | max. 0,6 |
GJS-XSiCrMo4,6-0,8-0,7 | min. 2,9 | 4,4 - 4,8 | 0,55 - 0,70 | 0,70 - 0,85 | max. 0,5 |
GJSAXNiCr30-2 | max. 2,4 | 2,0 - 3,0 | - | 1,75 - 2,25 | 18,0 - 20,0 |
GJSA-XNiCr35-3 | max. 2,0 | 2,0 - 3,0 | - | 2,25 - 2,75 | 34,0 - 36,0 |
GJSA-XNiSiCr35-5-2 | 2,8 - 3,6 | 4,5 - 5,5 | - | 1,75 - 2,25 | 34,0 - 36,0 |
Tabelle 26: Mechanische Eigenschaften einiger GJS-Werkstoffe für Abgasanlagen
SAE J2582 (Entwurf) | |||||
Werkstoff | Härte HBW 5-750 | Rm [MPa] | RP0,2 [MPa] | A 5 mm [%] | E-Modul [MPa] |
1 | 187 - 241 | > 450 | ≥ 275 | ≥ 8 | > 152000 |
2 | 187 - 241 | > 485 | ≥ 389 | ≥ 6 | > 152000 |
3 | 196 - 269 | > 515 | ≥ 415 | ≥ 4 | > 152000 |
VW 50021:2006-12 | |||||
GJS-XSiMo5-1 | 200 - 260 | > 520 | ≥ 420 | ≥ 5,0 | |
GJS-XSiCrMo4,6-0,8-0,7 | 200 - 265 | > 620 | ≥ 500 | ≥ 6,0 | |
GJSAXNiCr30-2 | 140 - 200 | > 370 | ≥ 200 | ≥ 10,0 | |
GJSA-XNiCr35-3 | 140 - 190 | > 370 | ≥ 200 | ≥ 10,0 | |
GJSA-XNiSiCr35-5-2 | 130 - 260 | > 370 | ≥ 200 | ≥ 10,0 |
Weiterführende Informationen zum Werkstoff Gusseisen mit Kugelgraphit
- Hier geht es zu den allgemeinen Informationen: Gusseisen mit Kugelgraphit | GUSS
- Hier finden Sie Informationen zur Metallurgie: Metallurgie | GUSS
- Hier finden Sie Informationen zur Wärme- und Oberflächenbehandlung: Wärme- und Oberflächenbehandlung | GUSS
- Hier finden Sie Informationen zur Werkstoffprüfung: Werkstoffprüfung | GUSS
- Hier finden Sie Informationen zu den mechanischen und physikalischen Eigenschaften: Mechanische und physikalische Eigenschaften | GUSS
- Hier finden Sie Informationen zur Spanenden Bearbeitung: Spanende Bearbeitung | GUSS
Download
Autoren und Quellen
Autoren:
Dr. Ch. Bartels, DI R. Gerhards, Prof. H. Hanselka, Prof. K. Herfurth, Dr. H. Kaufmann, DI W. Kleinkröger, Dr. M. Lampic, Dr. H. Löblich, Dr. W. Menk, Prof. G. Pusch, Dr. T. Schmidt, DI K.-H. Schütt, DI P. Tölke, Prof. E. P. Warnke