Gusseisen mit Kugelgraphit
Wärme- und Oberflächenbehandlung
Inhalt dieser Seite
Wärme- und Oberflächenbehandlung
Wärmebehandeln ist in der Fertigungstechnik nach DIN 8580 die Hauptgruppe 6 „Stoffeigenschaftsändern“. Hierzu gehört eine Gruppe von Fertigungsverfahren, die die Eigenschaften eines Werkstoffes verändern. Das geschieht zumeist durch Veränderungen im submikroskopischen oder interatomaren Bereich, zum Beispiel durch Diffusion von Atomen, Erzeugen und Bewegen von Versetzungen im Atomgitter und durch chemische Reaktionen.
Stoffeigenschaftsändern ist Fertigen eines festen Körpers durch Umlagern, Aussondern oder Einbringen von Stoffteilchen, wobei eine etwaige unwillkürliche Formänderung nicht zum Wesen der Verfahren gehört. Zum Stoffeigenschaftsändern durch Umlagern von Stoffteilchen zählen die Verfahren, bei denen das Gefüge oder das Kristallgitter oder beide verändert werden wie das Härten und Anlassen sowie ferner die Verfahren, die ohne wesentliche Formänderung durch örtliches Umformen allein der Kaltverfestigung dienen (zum Beispiel Festwalzen und Glattwalzen), und schließlich diejenigen Verfahren, bei denen die Stoffeigenschaften durch Wirkmedien verändert
werden (zum Beispiel Magnetisieren). Zum Stoffeigenschaftsändern durch Aussondern von Stoffteilchen gehört beispielsweise das Entkohlen und zum Stoffeigenschaftsändern durch Einbringen von Stoffteilchen zum Beispiel das Aufkohlen und das Nitrieren.
Eine andere technische Einteilung für Wärmebehandlungsverfahren erfolgt nach der Art des Verfahrens in
- thermische Verfahren (Verändern des Mikrogefüges): Dabei wird das Gussteil bestimmten Temperatur-Zeit-Folgen ausgesetzt. Die Veränderung des Mikrogefüges und damit die Veränderung der Eigenschaften erfasst das gesamte Gussteil. Die Kinetik der Gefügeumwandlung wird mit Zeit-Temperatur-Austenitisierungs- (ZTASchaubildern) (Bilder 64 und 65) [56, 57] und Zeit-Temperatur-Umwandlungsschaubildern (ZTU-Schaubildern) (Bilder 66 und 67) [58 - 60] beschrieben.
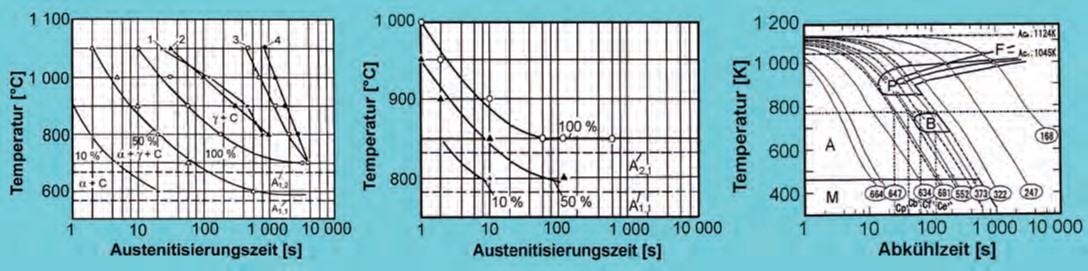
1 Erreichen des gebundenen C-Gehaltes von 0,8 %
2 Erreichen der Maximalhärte von HV0,05
3 Ende der isothermen Längenzunahme
4 Ende der Graphitauflösung
Bild 65(Mitte): Isothermisches ZTA-Diagramm für perlitisches Gusseisen mit Kugelgraphit
Bild 66(rechts): Kontinuierliches ZTU-Diagramm für Gusseisen mit Kugelgraphit
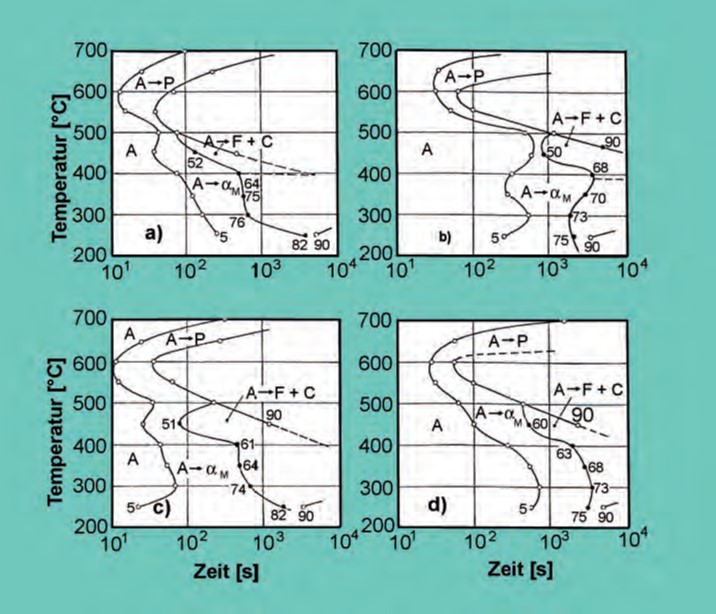
a) unlegiert
b) mit 0,8 % Cu legiert
c) mit 0,98 % Ni legiert
d) mit 2,13 % Ni legiert
- thermochemische Verfahren (Einbringen von Stoffteilchen): Bei den thermochemischen Verfahren wird die chemische Zusammensetzung eines Gussteils durch Einlagern eines oder mehrerer Elemente in der Randschicht absichtlich verändert, um bestimmte Eigenschaften der Randschicht zu verändern.
- thermomechanische Verfahren (Kombination von Umformen und Wärmebehandlung): Bei der Teilefertigung durch Gießen entfallen die Verfahren des Umformens. Somit haben thermomechanische Verfahren der Wärmebehandlung für Gussteile keine Bedeutung.
Wärmebehandlungen an Gussteilen aus Gusseisen mit Kugelgraphit werden mit unterschiedlichen Zielsetzungen durchgeführt. Hierzu gehören das Einstellen der Werkstoffsorten, das Gewährleisten von Werten für die Kerbschlagzähigkeit, das Steigern von Zugfestigkeit, Härte und Verschleißwiderstand, das Vermeiden von Verzug und Rissbildung im Betrieb sowie das Einstellen bestimmter physikalischer Eigenschaften. Um das zu erreichen, gibt es folgende Möglichkeiten:
- Ändern der Menge an gebundenem Kohlenstoff;
- Herstellen von Härtungs- und Vergütungsgefügen;
- Beseitigen von Gussspannungen;
- Randschichtbehandlungen.
Die drei erstgenannten Verfahrensvarianten beeinflussen die Gussteile im gesamten Volumen, die vierte Variante verändert nur die Eigenschaften der Randschicht der Gussteile.
Einerseits haben einige Wärmebehandlungsverfahren bei Gusseisen mit Kugelgraphit an Bedeutung verloren. Die Mikrogefüge und damit die mechanischen Eigenschaften der Grundsorten des Gusseisens mit Kugelgraphit nach DIN EN 1563 können in den meisten Fällen im Gusszustand erreicht werden. Nur bei den kaltzähen Sorten EN-GJS-350-22-LT und EN-GJS-400-18-LT ist in einigen Fällen eine Glühbehandlung zum Einstellen eines einwandfreien ferritischen Grundgefüges erforderlich, und die rein ferritische Stranggusssorte GJS-400-15C wird grundsätzlich geglüht. Duktile Rohre aus Gusseisen mit Kugelgraphit werden in jedem Fall wärmebehandelt. Auch ein Glühprozess zum Verringern von Gussspannungen gehört zum Produktionsprozess in der Gießerei. Andererseits haben Wärmebehandlungsvarianten zur Verbesserung der Eigenschaften an Bedeutung gewonnen. Dazu gehören die Wärmebehandlung für die hochfesten Sorten des Gusseisens mit Kugelgraphit nach DIN EN 1564 und alle Randschichtbehandlungen.
Ob eine Wärmebehandlung von Gusseisen mit Kugelgraphit durchgeführt wird oder nicht, entscheidet der Hersteller. In der europäischen Norm DIN EN 1553 heißt es: „... jede Wärmebehandlung ist, sofern der Käufer nichts festgelegt hat, dem Ermessen des Herstellers zu überlassen.“
Thermische Verfahren
Über die Varianten der thermischen Wärmebehandlungsverfahren ist ausführlich in [61] hinsichtlich der Begriffe, des angestrebten Zieles und der Temperatur-Zeit-Folgen erichtet worden. Im Bild 68 sind die Temperatur-Zeit-Folgen für die Varianten der Wärmebehandlung zusammengestellt.
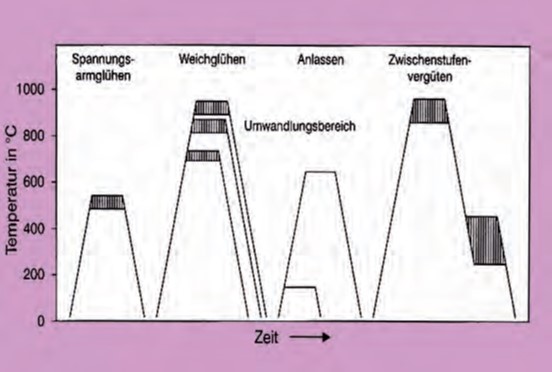
Die Tabelle 1 enthält eine Zusammenfassung der wichtigen Wärmebehandlungsparameter. Bei der vorliegenden Gliederung werden das Oberflächenhärten/Randschichthärten und die thermochemischen Wärmebehandlungsverfahren im Kapitel Randschichtbehandlung vorgestellt.
Wärmebehandlungs- verfahren | Gusseisensorte | Angestrebtes Ziel | Temperatur [°C] | Zeit1) | Abkühlen |
Spannungsarmglühen | Unlegiert, niedrig legiert, hoch legiert | Beseitigen von Spannungen | 500 - 550 560 - 600 600 - 650 | 1 h + 1 h je 25 mm Wanddicke | Ofenabkühlung 40 K/h bis 300 °C( bis 100 °C für komplizierte Teile) |
Weichglühen bei niedriger Temperatur (Ferritisieren, Graphitisieren) | Unlegiert, niedrig legiert | Ferritisches Gefüge, Erreichen bester Zerspanbarkeit | 700 - 760 | 45 min bis 1 h je 25 mm Wanddicke | Ofenabkühlung 55 K/h zwischen 540 und 300 °C |
Weichglühen bei mittlerer Temperatur (Ferritisieren, Graphitisieren) | Legiertes Gusseisen und solche Sorten, die für das Glühen bei niedriger Temperatur nicht geeignet sind | Ferritisches Gefüge, Erreichen bester Zerspanbarkeit | 790 - 900 | > 45 min je 25 mm Wanddicke | Ofenabkühlung von Glühtemperatur bis 300 °C |
Weichglühen bei hoher Temperatur (Ferritisieren, Graphitisieren) | Meliertes oder weißes Gusseisen | Ferritisches Gefüge, Erreichen bester Zerspanbarkeit | 900 - 955 | 1 bis 3 h + 1 h je 25 mm Wanddicke | Ofenabkühlung von Glühtemperatur bis 300 °C |
Weichglühen bei hoher Temperatur | Meliertes oder weißes Gusseisen | Beseitigen von Carbideinschlüssen unter Beibehaltung maximaler Festigkeit und Härte | 900 - 955 | 1 bis 3 h + 1 h je 25 mm Wanddicke2) | Luftabkühlung bis 540 °C, dann Ofenabkühlung bis 300 °C |
Perlitglühen (Perlitisieren) | Alle Sorten | Perlitisches Gefüge | 850 - 955 | 1 bis 3 h + 1 h je 25 mm Wanddicke | Luftabkühlung bis 540 °C,dann Ofenabkühlung bis 300 °C |
Härten | Alle Sorten | Martensitisches Gefüge höchster Härte | 800 - 950 | 1 h + 1 h je 25 mm Wanddicke | Luft- oder Flüssigkeits- abschreckung auf < 200 °C |
Vergüten (Härten mit nachfolgendem Anlassen) | Alle Sorten | Vermindern der Spödigkeit des Martensits | 150 - 650 | 1 h je 25 mm Wanddicke | Luft- oder Ofenabkühlung |
Zwischenstufenvergüten | Unlegiert, niedrig legiert | Bainitisches Gefüge (Zwischenstufengefüge) | 850 - 950 | 1 h + 1 h je 25 mm Wanddicke | Luft- oder Flüssigkeits- abschreckung auf 230 bis 400 °C, 1,5 bis 4 h halten |
Tabelle 1: Übersicht der wichtigsten Wärmebehandlungsverfahren für Gusseisen mit Lamellen- oder Kugelgraphit
1) Kürzere Zeiten lassen sich bei Glühöfen mit Strahlungsbeheizung erreichen.
2) Die Carbide können häufig bereits in kürzerer Zeit abgebaut werden.
Die Wärmebehandlungsverfahren zum Einstellen hoher Festigkeiten sind in Bild 69 [62, 63] nochmals hervorgehoben. Für die Temperatur-Zeit-Abläufe der Grundvarianten sind zur Orientierung das eutektoide Intervall A1.1 und A1.2 und ein isothermisches ZTU-Diagramm stark vereinfacht eingezeichnet. Die Grundvarianten I, III und V Inthalten eine vollständige Austenitisierung und die Grundvarianten II, IV und VI eine unvollständige Austenitisierung innerhalb des eutektoiden Intervalls. Die Grundvariante I ist das klassische Vergüten (Härten und Anlassen) und die Grundvariante III das klassische Bainitisieren (Zwischenstufenvergüten). Mit der Grundvariante V werden die Sorten des austenitisch-ferritischen Gusseisens mit Kugelgraphit durch unvollständiges Bainitisieren (unvollständiges Zwischenstufenvergüten) hergestellt.
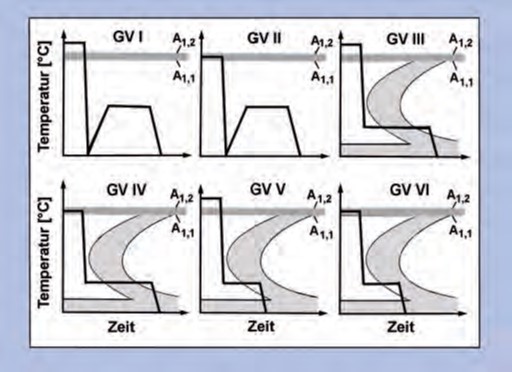
Metallkundliche Grundlagen zur Wärmebehandlung werden in [12, 13] vorgestellt.
Austenitisieren
Für das Verändern des Mikrogefüges und damit der mechanischen Eigenschaften ist das Austenitisieren des Gusseisens mit Kugelgraphit ein wichtiger Verfahrensschritt. Ziel des Austenitisierens ist es, bei Temperaturen zwischen etwa 820 und 950 °C einen mit Kohlenstoff gesättigten Austenit als Ausgangszustand für weitere Verfahrensvarianten einzustellen [57]. Beim Austenitisieren finden folgende Gefügeumwandlungen statt:
- Der Perlit und der Ferrit des Mikrogefüges im Gusszustand wandelt in Austenit um.
- Eventuell vorhandener Ledeburit im Gussgefüge löst sich im Austenit auf.
- Der Austenit sättigt sich mit Kohlenstoff.
Bei ursprünglich perlitischen Gefügen stellt sich aufgrund des hohen gebundenen Kohlenstoffgehalts relativ schnell ein mit Kohlenstoff gesättigter Austenit ein. Bei ferritischen Ausgangsgefügen muss der Kohlenstoff von den im Gefüge vorliegenden Graphitkugeln in den Austenit diffundieren. Die dafür erforderliche Zeit ist von den Diffusionswegen und der Austenitisierungstemperatur abhängig. Das Zusammenspiel zwischen Austenitisierungstemperatur und der für eine Austenitisierung erforderlichen Zeit beschreiben ZTA-Schaubilder [56, 57]. Für ein Gusseisen mit Kugelgraphit mit 3,26 % C; 2,64 % Si; 0,92 % Mn; 0,093 % Cr; 0,14 % P und 0,06 % S sind isothermische ZTA-Diagramme für ein ferritisches und für ein perlitisches Gusseisen mit Kugelgraphit experimentell ermittelt worden (Bilder 64 und 65). Die Graphitkugeln hatten einen Durchmesser von 40 bis 60 Mikrometer. Es zeigt sich ein deutlicher Unterschied für das Verhalten des Werkstoffs bei der Austenitisierung in Abhängigkeit vom Zustand der metallischen Grundmasse vor der Austenitisierung. Beim ferritischen Gusseisen mit Kugelgraphit ergeben sich für gleiche Austenitisierungstemperaturen längere Umwandlungszeiten als bei einem perlitischen Ausgangszustand. Beim perlitischen Gusseisen mit Kugelgraphit kann die Austenitisierung und Aufkohlung schneller als beim ferritischen ablaufen, weil der Perlitanteil schnell austenitisiert. Die Ferritzwischenräume werden sehr schnell aufgekohlt. Beim Austenitisieren von ferritischem Gusseisen mit Kugelgraphit verläuft die Aufkohlung des Austenits bevorzugt entlang ehemaliger Ferritkorngrenzen, und die Kohlenstoffsättigung entsteht nur durch Nachdiffusion von Kohlenstoff von den Graphitkugeln. Je kleiner der Graphitkugeldurchmesser d bzw. die Graphitlamellendicke d ist, um so schneller ist der Austenit bei einem ferritischen Ausgangsgefüge mit Kohlenstoff gesättigt (Bild 70 [64].

a) d = 55 μ,
b) d = 43 μ,
c) = 25 μ,
d) d = 18 μ
Die Gefügeumwandlungsprozesse, die beim Austenitisieren von ferritischem und perlitischem Gusseisen mit Kugelgraphit ablaufen, sind ausführlich in [6] beschrieben worden. Die Austenitkorngröße entspricht beim Gusseisen mit Kugelgraphit etwa der von Feinkornstählen. Mit zunehmender Austenitisierungstemperatur und Austenitisierungsdauer nimmt die Austenitkorngröße bei Gusseisen mit Kugelgraphit nur in geringem Maß zu (Bild 71) [65, 66].
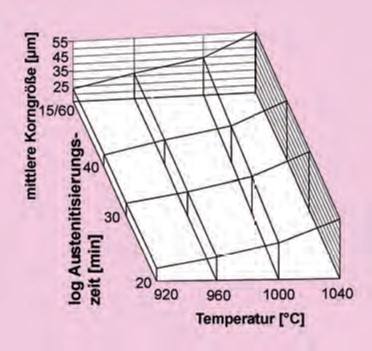
Nach einer Austenitisierung des Gusseisens mit Kugelgraphit wird das Umwandlungsverhalten des Werkstoffs durch ZTU-Diagramme beschrieben. Im Bild 66 ist ein kontinuierliches ZTU-Diagramm für ein Gusseisen mit Kugelgraphit mit 3,6 % C; 2,46 % Si; 0,21 % Mn; 0,014 % P: 0,008 % S und 0,043 % Mg dargestellt [58]. Die Austenitisierungstemperatur lag bei 1223 K und die Austenitisierungsdauer bei 900 s. Isothermische ZTU-Diagramme für unlegiertes und legiertes Gusseisen mit Kugelgraphit enthält Bild 67 [59]. In dem Temperaturgebiet, das für die Herstellung von ausferritischem Gusseisen mit Kugelgraphit wichtig ist, wird keine Linie für eine hundertprozentige Umwandlung angegeben, sondern wie zum Beispiel bei Teilbild c) die Zahlenwerte 61, 64, 74 und 82 %, was bedeutet, dass nur 61, 64, 74 und 82 % des Austenits umgewandelt sind und entsprechend 39, 36, 26 und 18 % Restaustenit vorliegen. Die Austenitumwandlung ist also unvollständig. Weitere ZTUDiagramme sind in [67] zusammengestellt.
In der technischen Anwendung wird über eine Dauer zwischen 15 Minuten und 4 Stunden bei Temperaturen zwischen 880 und 940 °C austenitisiert, vornehmlich in Elevator-, Hauben- oder Herdwagenöfen. Duktile Rohre aus Gusseisen mit Kugelgraphit werden in Durchlauföfen wärmebehandelt. Beim Austenitisieren von Gusseisen mit Kugelgraphit muss ein Verzundern und eine Randentkohlung möglichst ganz vermieden werden.
Weichglühen bei hoher Temperatur
Gussteile aus Gusseisen mit Kugelgraphit dürfen zur Gewährleistung ihrer typischen mechanischen Eigenschaften und einer guten Zerspanbarkeit keine weißerstarrten Gefügebestandteile enthalten. Liegen nach der Erstarrung Anteile von eutektischen (ledeburitischen) Carbiden oder gar Primärcarbide vor, so muss zu deren Beseitigung eine Glühtemperatur deutlich oberhalb des eutektoiden Intervalls zwischen 900 und 950 °C gewählt werden. Die Wahl der Abkühlungsgeschwindigkeit aus dem Austenitgebiet ist davon abhängig, welches Mikrogefüge eingestellt werden soll. Diese Wärmebehandlungsvariante wird nur dann notwendig, wenn beim Herstellungsprozess von Gusseisen mit Kugelgraphit nicht optimal gearbeitet wurde.
Weichglühen bei niedriger Temperatur
Diese Wärmebehandlungsvariante dient dem Umwandeln von Perlit in Ferrit. Während beim Weichglühen von Stahl nur ein Einformen des streifigen Perlits in körnigen Perlit erreicht werden kann, führt das Weichglühen von Gusseisen mit Kugelgraphit zu einem rein ferritischen Grundgefüge ohne Anteile von eutektoidem Eisencarbid. Die Glühtemperatur liegt dabei knapp unterhalb des eutektoiden Intervalls bei etwa 700 °C. Abgekühlt wird mit einer Geschwindigkeit um 50 K/h.
Beim Herstellen von Gusseisen mit Kugelgraphit der Sorten EN-GJS350-22-LT und EN-GJS-400-18-LT, also von Sorten mit garantierter Kerbschlagzähigkeit bei tiefen Temperaturen, werden die geforderten Werte für die Kerbschlagzähigkeit nicht immer im Gusszustand erreicht. Die beschriebene Wärmebehandlung ist dann Bestandteil der Fertigungsfolge in der Gießerei. Das gilt auch für nach dem Stranggießverfahren verarbeitetes Gusseisen mit Kugelgraphit der Sorte GJS-400-15C, bei der die genannte Wärmebehandlungsvariante zum Produktionsprogramm der Gießerei zählt.
Zweistufiges Weichglühen
Sind beim Gusseisen mit Kugelgraphit höchste Zähigkeitsanforderungen zu erfüllen, können die gewünschten Eigenschaften bei unlegierten Sorten nur durch eine zweistufige Wärmebehandlung erfüllt werden. Sie besteht aus einem Austenitisieren bei 850 bis 950 °C, anschließendem Abkühlen im Ofen oder an Luft und nachfolgendem Halten (5 bis 10 Stunden) am eutektoiden Intervall zwischen 650 und 740 °C. Eine solche Wärmebehandlung wird zum Beispiel bei den duktilen Rohren aus Gusseisen mit Kugelgraphit durchgeführt.
Perlitglühen
Ziel des Perlitglühens ist es, ein vollperlitisches Grundgefüge einzustellen, um bestimmte Festigkeitseigenschaften zu erzielen oder das Grundgefüge in unterschiedlichen Wanddickenbereichen zu vergleichmäßigen. In Anlehnung an die Wärmebehandlung von Stahl wird sie auch als Normalisieren oder Perlitisieren bezeichnet. Beim Perlitglühen wird das Gussteil auf Temperaturen zwischen 900 und 920 °C aufgeheizt, wodurch das Austenitgebiet oberhalb des eutektoiden Intervalls erreicht wird. Anschließend erfolgt eine beschleunigte Abkühlung, um eine Ferritbildung zu unterdrücken. Die optimale Abkühlungsgeschwindigkeit wird je nach Gussteilwanddicke mit Hilfe ruhender Luft, Anblasen mit Druckluft oder durch Wassersprühnebel eingestellt.
Härten
Als Eisen-Kohlenstoff-Silicium-Werkstoff kann Gusseisen mit Kugelgraphit ebenso gehärtet werden wie Stahl. Das Härten von Gusseisen mit Kugelgraphit zielt entweder auf die Bildung einer verschleißbeständigen Randschicht (siehe 5.2) oder es dient als Vorstufe für das Vergüten. Damit erreicht Gusseisen mit Kugelgraphit eine hohe Härte von 45 bis 60 HRC und einen hohen Verschleißwiderstand. Beim Härten wird das Gussteil bei Temperaturen zwischen 850 und 950 °C oberhalb des eutektoiden Intervalls erwärmt. Während der Austenitisierung wird der Austenit bis zur Sättigung aufgekohlt. Kohlenstoffquellen sind dabei das eutektoide Carbid des Perlits und die Graphitkugeln. Das sich anschließende schnelle Abkühlen (Abschrecken) des Gussteils verhindert eine Ferrit- oder Perlitbildung und führt zu einer Grundmasse aus Martensit und Restaustenit. Die erforderlichen hohen Abkühlungsgeschwindigkeiten werden durch Eintauchen des Gussteils in Öl, Emulsionen oder Wasser eingestellt. Das Härten des ganzen Gussteilvolumens ist die erste Stufe des Vergütens.
Vergüten
Das Vergüten ist eine Kombination von Härten als erste Stufe und anschließendem Wiedererwärmen (Anlassen) als zweite Stufe. Durch das Vergüten von Gusseisen mit Kugelgraphit lassen sich die mechanischen Eigenschaften durch Variation der Anlasstemperatur deutlich in Richtung höherer Festigkeiten einstellen (Bild 72) [68]. Zugfestigkeit und Dehngrenze erreichen Werte wie bei Vergütungsstählen. Jedoch sind oft die Werte für ausreichende Plastizität und Zähigkeit relativ schwer einstellbar. Das Vergüten von Gusseisen mit Kugelgraphit wird relativ selten angewendet, insbesondere deshalb, weil mit dem isothermischen Austenitumwandeln weit interessantere mechanische Eigenschaften bereitgestellt werden können.
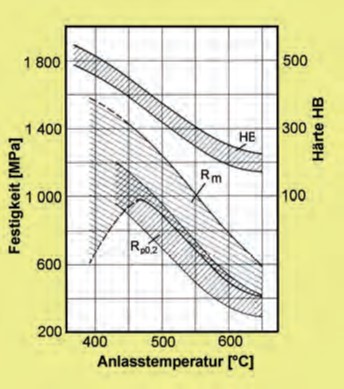
Beim Anlassen wird das Abschreckgefüge des Härtens (Martensit und Restaustenit) durch Wiedererwärmen schrittweise abgebaut. Die Anlasstemperatur liegt in Abhängigkeit von den zu erzielenden mechanischen Eigenschaften zwischen 150 und 650 °C. Mit zunehmender Anlasstemperatur nehmen die Zugfestigkeit, Dehngrenze und Härte ab, während Bruchdehnung und Kerbschlagzähigkeit zunehmen. Mit steigenden Anlasstemperaturen werden mehrere Anlassstufen durchlaufen, die beim Gusseisen mit Kugelgraphit wegen des vorhandenen Siliciumgehalts im Gegensatz zu den Stählen bis zu einen carbidfreien Zustand – also einer rein ferritischen Grundmasse – führen [69].
Bainitisieren (Zwischenstufenvergüten)
Das isothermische Austenitumwandeln bei Temperaturen unterhalb der Perlitstufe und oberhalb der Martensitstufe wird traditionell als Zwischenstufenvergüten oder heute besser als Bainitisieren bezeichnet. Beim Gusseisen mit Kugelgraphit hat diese Wärmebehandlung mit vollständiger Bainitisierung nicht zu besonders guten mechanischen Eigenschaften geführt. Es ergeben sich damit zwar hohe Festigkeiten, jedoch sind die Bruchdehnungen sehr gering. Diese Sorten des Gusseisens mit Kugelgraphit haben aber einen hohen Verschleißwiderstand. Jedoch ergab sich auf diesem Gebiet eine spezielle Wärmebehandlungsvariante mit einer unvollständigen isothermischen Austenitumwandlung nach vollständiger Austenitisierung, die beim Gusseisen mit Kugelgraphit eine vorzügliche Kombination von hohen Festigkeiten und hoher Plastizität und Zähigkeit bewirkt. Es entstehen dabei die austenitisch-ferritischen Sorten des Gusseisens mit Kugelgraphit, die bei hohen Festigkeiten auch eine hohe Plastizität und Zähigkeit aufweisen (siehe 5.1.9).
Beim Gusseisen mit Kugelgraphit ist das Bainitisieren ein wegen des hohen Siliciumgehaltes zweistufiger Umwandlungsprozess. Bild 73 zeigt schematisch ein Gefügemengen-Zeit-Diagramm mit dieser Besonderheit. Während der 1. Stufe entwickelt sich aus dem Austenit ein Mikrogefüge aus Ferritnadeln und einem mit Kohlenstoff gesättigten Restaustenit ohne Carbide (ausferritisches Gusseisen mit Kugelgraphit). Zwischen der 1. und der 2. Umwandlungsstufe kommt der Umwandlungsprozess praktisch zum Stillstand und kann damit technologisch gut genutzt werden. Während der 2. Umwandlungsstufe entstehen erst die für bainitische Gefüge typischen Carbide, und der Restaustenit verarmt d adurch wieder an Kohlenstoff. Am Ende der 2. Umwandlungsstufe ist der Austenit aufgebraucht und das Mikrogefüge besteht aus Ferritnadeln und Carbiden. Das Ergebnis ist dann ein bainitisches Gusseisen mit Kugelgraphit.
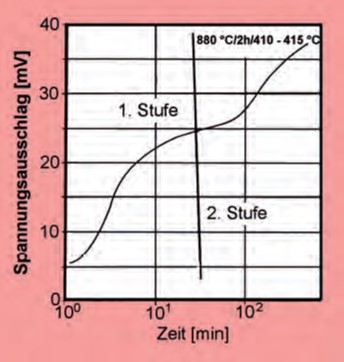
Unvollständiges Bainitisieren
Beim isothermischen Austenitumwandeln wird das Gussteil aus Gusseisen mit Kugelgraphit zunächst bei 875 bis 920 °C vollständig austenitisiert. Werden die Gussteile dann schnell in ein Salzbad mit Temperaturen zwischen 300 und 400 °C umgesetzt, beginnt die Austenitumwandlung mit der Bildung von Ferritnadeln und einer Sättigung der verbleibenden Austenitanteile mit Kohlenstoff, die zu einer Stabilisierung dieses Restaustenits führen. Die Ms-Temperatur des Restaustenits fällt auf sehr niedrige Temperaturen, so dass eine Martensitbildung bis zu -100 °C nicht erfolgt. Die Carbidbildung unterbleibt und die Austenitumwandlung kommt nahezu zum Stillstand. Es handelt sich um eine unvollständige isothermische Austenitumwandlung, ein unvollständiges Bainitisieren. Nach dem Abkühlen aus dem Salzbad auf Raumtemperatur liegt dann ein Grundgefüge aus nadligem Ferrit und hohen Restaustenitanteilen von bis zu 40 % vor.
Die Sorten des Gusseisens mit Kugelgraphit, die durch das isothermische Austenitumwandeln hergestellt werden können, sind unter der Bezeichnung ADI (Austempered Ductile Iron) am meisten bekannt geworden. Sie werden auch als bainitisches Gusseisen bezeichnet und in naher Zukunft wahrscheinlich als austenitisch-ferritisches Gusseisen mit Kugelgraphit. Bei diesen Werkstoffsorten des hochfesten Gusseisens mit Kugelgraphit ist eine sorgfältige Abstimmung von chemischer Zusammensetzung des Gusseisens, der Gussteilwanddicke und der Wärmebehandlungsparameter erforderlich. Erst die
Ermittlung präziser Prozessfenster für diese Abhängigkeiten führen zu einer prozesssicheren Produktion.
Spannungsarmglühen
Ein Gussteil ohne innere Spannungen (Eigenspannungen, Gussspannungen) herzustellen, ist wegen der unterschiedlichen Abkühlungsgeschwindigkeiten innerhalb eines Gussteils nicht möglich. Die Höhe und die Richtung dieser Gussspannungen sind von der Geometrie des Gussteils und den Verfahrensbedingungen beim Gießen abhängig. Bei den meisten Gussteilen aus Gusseisen mit Kugelgraphit sind diese Gussspannungen jedoch so gering, dass sie die Beanspruchbarkeit nicht beeinträchtigen.
Das Spannungsarmglühen ist eine Wärmebehandlung, die speziell zum Abbau der Gussspannungen eingesetzt wird. Die Glühtemperaturen zwischen 500 und 550 °C liegen unter dem Bereich der eutektoiden Umwandlung, wodurch eine unerwünschte Gefügeveränderung und damit eine Änderung der mechanischen Eigenschaften während des Glühprozesses vermieden wird. Um zu verhindern, dass weitere Eigenspannungen beim Spannungsarmglühen durch das Aufheizen und das Abkühlen entstehen, müssen Aufheizgeschwindigkeiten zwischen 10 und 50 K/h und Abkühlungsgeschwindigkeiten zwischen 25 und 50 K/h eingehalten werden.
Wärmebehandlung beim austenitischen Gusseisen mit Kugelgraphit
Wenn Gussteile aus austenitischem Gusseisen mit Kugelgraphit für statische oder zyklische Beanspruchungen bei Temperaturen oberhalb 500 °C eingesetzt werden sollen und enge Maßtoleranzen einzuhalten sind, wird ein Hochtemperatur-Stabilisierungsglühen empfohlen. Dabei wird mit einer Geschwindigkeit von maximal 150 K/h bis zu Glühtemperaturen im Bereich von 875 bis 900 °C aufgeheizt und anschließend im Ofen mit maximal 50 K/h auf 500 °C und weiter an Luft abgekühlt.
Randschichtbehandlungen
Zu den Randschichtbehandlungen werden das Oberflächenhärten (Flamm-, Induktions-, Laserstrahlhärten), die chemischthermischen Wärmebehandlungsverfahren, das Randschicht-Umschmelzen, das Randschicht-Umschmelzlegieren und Oberflächen-Umformen (Festwalzen, Glattwalzen, Kugelstrahlen) gezählt.
Unter Oberflächenhärten wird das Härten der Randschicht eines Gussteils verstanden. Dabei wird eine harte Oberfläche am Gussteil erzeugt, die einen hohen Verschleißwiderstand hat und hohe Flächenpressungen aufnehmen kann. Im Kern bleibt das Gussteil zäh und weicher und kann gut stoßartige und wechselnde Beanspruchungen aufnehmen. Die tiefer liegenden Gussteilbereiche werden in der kurzen Aufwärmzeit nicht bis auf Härtetemperatur erwärmt und bleiben deshalb ungehärtet.
Beim Flammhärten (Brennhärten) wird bei den zu härtenden Gussteilen die Randschicht ganz oder teilweise durch Brennerflammen in das Austenitgebiet erhitzt und durch eine Wasserbrause abgeschreckt und dadurch gehärtet (Bild 74). Es können Einhärtetiefen zwischen 2 und 10 mm erzeugt werden.

Beim Induktionshärten wird die Wärme durch Induktion eines Wirbelstroms in das Gussteil erzeugt. Eine Kupferspule, die der Gussteilgeometrie angepasst sein muss, wird mit einem hochfrequenten Wechselstrom betrieben und dadurch ein Wirbelstrom in der Randschicht induziert (Bild 75). Eine nachgeführte Wasserbrause schreckt anschließend die Randschicht ab. Die Einhärtetiefe ist abhängig von der Vorschubgeschwindigkeit der Spule, der Stromstärke und der Stromfrequenz.
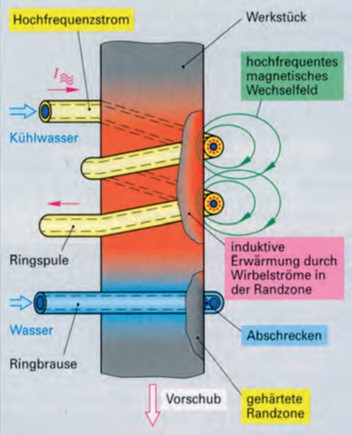
Beim Laserstrahlhärten erfolgt der Energieeintrag über einen Laserstrahl. Verwendet werden als Strahlquellen CO2-Laser und NdYAG-Laser. Das Härten mit einem Laserstrahl erfolgt punktgenau. Das Abkühlen erfolgt meist durch Selbstkühlung durch den Gussteilwerkstoff, dessen Wärmeleitung sehr groß ist. Die sehr rasche Wärmeabfuhr in den kalten Grundwerkstoff des Gussteils führt dazu, dass zum Beispiel auf eine Wasserbrause verzichtet werden kann.
Bei Laufflächen eines Getriebedeckels aus EN-GJS-600-03 ergab sich durch Laserstrahlhärten auf eine Tiefe von 0,5 mm eine Oberflächenhärte von annähernd 800 HV. Verwendung fand ein CO2-Laser. Die auftreffende Leistung lag bei 1300 W, die Vorschubgeschwindigkeit bei 1 m/min. Es trat praktisch kein Verzug auf [70].
Eine spezielle Art des Laserstrahlhärtens ist das Punkthärten einer Oberfläche. Mit dem Laserstrahl werden nur einzelne Punkte gehärtet, die auf der Oberfläche ein bestimmtes Muster bilden. Das Punkthärten von Gusseisen mit Kugelgraphit erfolgte mit einem CO2-Laser. Die Mikrohärte erreicht 900 bis 1000 HV. Das Mikrogefüge besteht aus Martensit mit eingelagerten Graphitkugeln [71].
Bei einem austenitisch-ferritischen Gusseisen mit Kugelgraphit (ADI) (870 °C/2 h/ 370 °C/1 h) wurde vor dem Laserstrahlhärten die Probenoberfläche mit Ruß beschichtet, um die Laserstrahlung besser zu koppeln. Verwendung fand ein 1,5-kWCM-CO2-Laser. Eingetragen wurde eine Leistung zwischen 500 bis 800 W. Der Laserstrahldurchmesser lag bei 2 mm und die Vorschubgeschwindigkeit bei 60 mm/s. Es wurde eine Oberflächenmikrohärte von 850 bis 1200 HV erreicht. Die gehärtete Schicht war etwa 0,3 mm dick [72].
Das Elektronenstrahlhärten erfolgt durch einen gebündelten Elektronenstrahl im Hochvakuum. Beim Oberflächenhärten von Gussteilen wird dieses Verfahren selten angewendet.
Chemisch-thermische Verfahren
Zu den interessierenden chemisch-thermischen Wärmebehandlungverfahren gehören vor allem das Nitrieren, Chromatieren, Aluminieren und Borieren. Nachfolgend wird nur auf das Nitrieren eingegangen.
Nitrieren ist eine chemisch-thermische Behandlung zur Diffusionssättigung der Randschicht bei Stahl- oder Gusseisenteilen mit Stickstoff beim Erwärmen in einem stickstoffhaltigen Medium. Das Nitrieren verfolgt den Zweck, durch Aufnahme von Stickstoff in die Randschicht, die Härte, den Verschleißwiderstand, die Dauerfestigkeit und auch die Korrosionsbeständigkeit zu erhöhen.
Die Vorgänge beim Nitrieren basieren auf dem Zustandsdiagramm Eisen - Stickstoff. Beim Nitrieren unterhalb der eutektoiden Temperatur sättigt sich zunächst der α-Mischkristall mit Stickstoff an. Dann bildet sich das Nitrid Fe4N (γ´-Phase). Nach deren Sättigung entsteht als weitere Phase das Nitrid Fe2N (ε-Phase). Die Härte der Randschicht beruht nicht auf der Martensitbildung. Damit entfällt das Abschrecken. Die Nitrierschichtdicke beträgt 0,05 bis 1,2 mm.
Das Nitrieren wird in Salzbädern oder in einer Gasphase durchgeführt. Das Badnitrieren erfolgt in Zyansalzbädern und ist wegen der gleichzeitig ablaufenden Aufkohlung eigentlich ein Carbonitrieren. Die verwendeten Salzbäder bestehen entweder aus Natrium- oder Calciumzyanid mit geringen Zusätzen an Chloriden. Eine Aufkohlung der Randschicht ist bei Gusseisen mit Kugelgraphit nicht notwendig.
Das Gasnitrieren basiert auf der Verwendung von Ammoniak, der bei den angewendeten Temperaturen zwischen 500 und 560 °C thermisch dissoziiert. Damit steht der benötigte atomare Stickstoff an der Gussteiloberfläche zur Verfügung. Die Nitrierdauer ist relativ lang. Eine Verringerung der Nitrierdauer ist durch Nutzung von Glimmentladungen und Zusatz oxidierender Gase möglich.
Im Bild 78 sind für das Gasnitrieren Nitrierkurven für Gusseisen mit Kugelgraphit der Sorte GJS-400-15C (Strangguss) dargestellt. Bei einer Nitriertemperatur von 510 °C und einer Nitrierdauer von 36 Stunden wurde eine Nitrierhärtetiefe von 0,2 mm (Kurve a) sowie bei einer Nitriertemperatur von 580 °C und einer Nitrierdauer von 5 Stunden eine Nitrierhärtetiefe von 0,1 mm erreicht (Kurve b) [34].
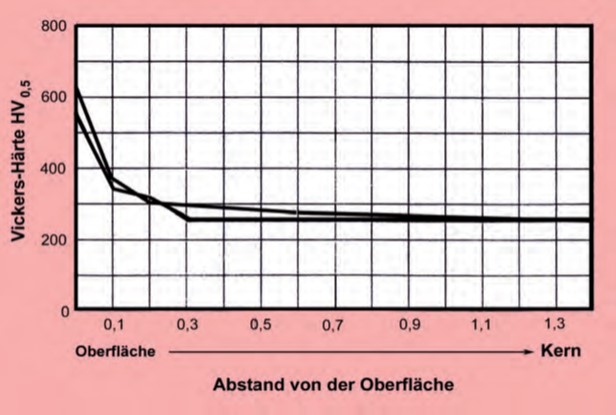
Diese Untersuchungen zeigen, dass Gusseisen mit Kugelgraphit genau so wie Stahl erfolgreich nitriert werden kann. Angewendet wurde das Gasnitrieren bei einem Zahnkranz aus Gusseisen mit Kugelgraphit der Sorte GJS-400-15C (Bild 79). Dieser Zahnkranz hat folgende Merkmale: Modul 3,5, 20 Zähne, Grundkreis 63 mm, 44 Einheiten Mindesthärte auf den nitrierten Zahnflanken, Innen- und Außendurchmesser nach dem Nitrieren geschliffen. Die Anforderungen an das Nitrieren des Zahnkranzes konnten wie bei einem Stahlzahnkranz voll erfüllt werden [34].
Beschichten
Beschichten ist das Aufbringen einer fest haftenden Schicht aus formlosem Stoff auf Werkstücke. Das Beschichten ist die Hauptgruppe 5 der Fertigungsverfahren nach DIN 8580 als Bezeichnung für eine Gruppe verschiedener Fertigungsverfahren, bei denen ein Beschichtungswerkstoff auf ein Werkstück aufgebracht wird und eine fest haftende Schicht bildet. Dabei kann es sich um eine dünne oder eine dicke Schicht handeln. Die Unterscheidung ist nicht genau definiert und orientiert sich am Beschichtungsverfahren und Anwendungszweck.
Die Hauptgruppe 5 umfasst das
- Beschichten aus dem gas- oder dampfförmigem Zustand (zum Beispiel Aufdampfen),
- Beschichten aus dem flüssigen, breiigen oder pastenförmigen Zustand (zum Beispiel Anstreichen, Spritzlackieren, Tauchemaillieren, Auftragsschweißen),
- Beschichten aus dem ionisierten Zustand durch elektrolytisches oder chemisches Abscheiden (zum Beispiel Galvanisieren),
- Beschichten aus dem festen (körnigen oder pulverigem) Zustand (zum Beispiel Pulverbeschichten).
Das Beschichten von Oberflächen ist ein sehr variantenreiches Gebiet. Für das Gusseisen mit Kugelgraphit werden einige ausgewählte Bespiele vorgestellt.
Emaillieren
Zum Emaillieren wird der Beschickungswerkstoff (Emailleschlicker) durch Tauchen oder Spritzen auf die zu beschichtende Oberfläche aufgetragen. Nach einem Trocknungsprozess des Emailleschlickers wird dieser bei Temperaturen von 700 bis 900 °C gebrannt. Das Emaillieren wird für korrosionsbeständige, hitzebeständige und dekorative Beschichtungen angewendet. Im Bild 80 sind emaillierte und komplett in der Gießerei montierte Hydranten dargestellt. Die Gießereien bieten auf diesem Gebiet nicht nur Gussleistungen an, sondern entwickeln auch eigene Emaillierungen und realisieren auch andere Beschichtungslösungen für die Verbesserung der Ästhetik der Gussoberfläche und den Korrosionsschutz. Zudem werden komplette Bearbeitungsleistungen einschließlich der Montage angeboten.
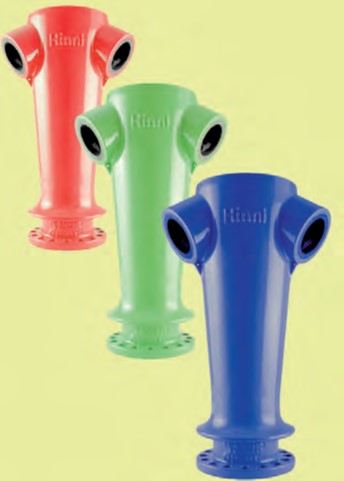
Pulverbeschichten
Das umweltfreundliche lösungsmittelfreie Pulverbeschichten ist ein Beschichtungsverfahren, bei dem in der Regel elektrisch leitfähiger Werkstoff mit Pulverlacken beschichtet wird. Dabei wird das Pulver elektrostatisch oder tribostatisch auf die zu beschichtende Oberfläche aufgesprüht und anschließend eingebrannt. Vorher ist die Oberfläche gut zu entfetten und gegebenenfalls mit Korrosionsschutzmitteln zu behandeln. Die Einbrenntemperaturen variieren stark. Typische Einbrenntemperaturen liegen zwischen 140 und 200 °C. Typisch sind Pulverlacke auf Basis von Polyurethan-, Epoxid- oder Polyesterharzen. Durch das Einbrennen soll ein dauerhaftes Anhaften und eine gleichmäßige dichte Beschichtung erreicht werden, was teils durch Koagulation, teils durch Anschmelzen der Partikel erfolgt. Durch unterschiedliche Oberflächenstruktur (glatt, strukturiert, Feinstruktur, Hammerschlag) und entsprechende Pigmente können praktisch fast alle Oberflächeneffekte erzielt werden. Im Bild 81 sind pulverbeschichtete Führungsstangen zu sehen.
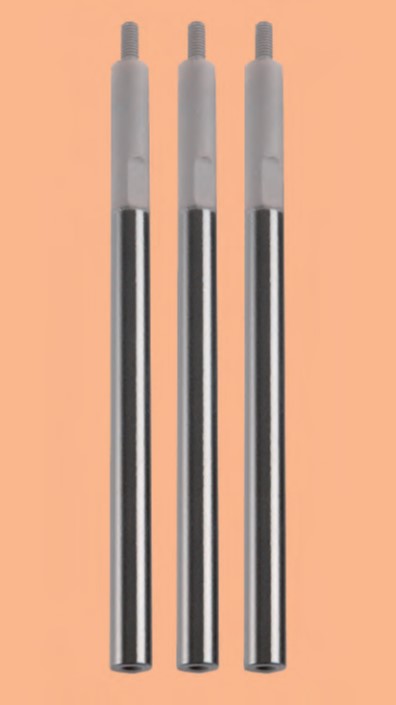
Verzinken
Bei duktilen Rohren aus Gusseisen mit Kugelgraphit wird für den Außenschutz ein Zinküberzug aufgebracht. Dieser Zinküberzug besteht aus aufgebrachten Spritzverzinkungen mit metallischem Zink. Für das Verzinken wird ein Zinkdraht in einer Flamme oder einem elektrischen Lichtbogen aufgeschmolzen. Das flüssige Zink wird im Luftstrom auf das rotierende Rohr geschleudert.
Das Zink besitzt einen aktiven Schutzcharakter auf elektro-chemischer Basis und wird seinerseits durch eine bitumöse Deckbeschichtung passiv geschützt. Deshalb kommt es vor allem für den Korrosionsschutz bei Bauwerksteilen aus Stahl und auch aus Gusseisen zum Einsatz, wie bei den im Bild 82 gezeigten napfförmigen Verbindungsstücken für das Stahltragwerk der wärmedämmenden wabenförmigen Tragwerkshallen der beiden Tropenhäuser des „Eden Projects“ von Cornwell (GB), die sich zu einem Besuchermagnet entwickelt haben. Diese Teile wurden aus Gründen des Korrosionsschutzes und der Angleichung des Aussehens an die ebenfalls verzinkte Stahlkonstruktion feuerverzinkt. Die etwa 80 kg Gussteile wurden im Sandguss aus den Legierungen EN-GJS-400-18 und EN-GJS-500-7 entsprechend den statischen Berechungen gegossen und entsprechend vorbehandelt.
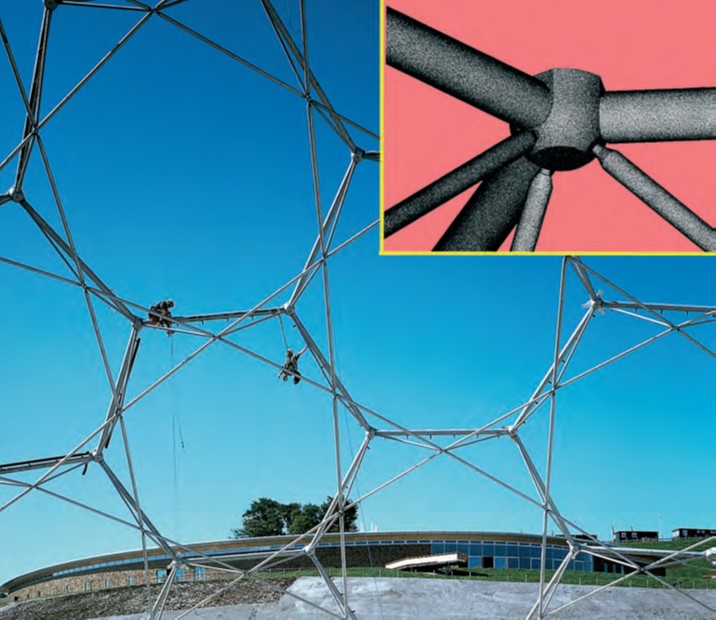
Vernickeln
Das galvanische Beschichten erfolgt als elektrochemische Abscheidung von metallischen Schichten auf metallischen Gegenständen. Dabei wird durch ein elektrolytisches Bad Strom geschickt. Am Pluspol (Anode) befindet sich das Metall, das aufgebracht werden soll (beispielsweise Nickel), am Minuspol (Kathode) der zu beschichtende Gegenstand (in diesem Fall das Gussteil). Der elektrische Strom löst dabei Metallionen von der Verbrauchselektrode ab und lagert sie auf der Oberfläche des zu beschichtenden Gegenstands ab. Je länger sich der zu beschichtende Gegenstand im elektrolytischen Bad befindet, umso dicker wird die Metallschicht. Das Aussehen einer Nickelschicht ist stark vom Einhalten der optimalen Verfahrensparameter abhängig (Glanz- und Zusatzstoffe, Metallionengehalt, Temperatur, pH-Wert).
Bei Castoren (Cask for Storage and Transport of Radioavtive Material) wird beispielsweise an der Innenseite elektrolytisch eine Nickelschicht von 3 mm Dicke aufgetragen [73] (Bild 83). An einem Castor mit einer Höhe bis zu 5,9 m, einem Durchmesser von 2,5 m und einem Gewicht von 96 t befindet sich eine zu beschichtende Innenfläche von 30 m2. Für die Innenbeschichtung wird 1 t Nickel gebraucht.
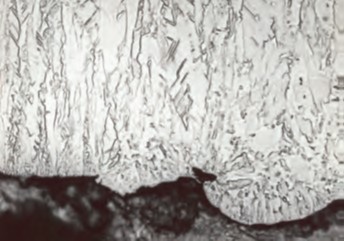
Randschicht-Umschmelzen
Randschicht-Umschmelzen ist ein Sammelbegriff für eine Gruppe von speziellen Randschicht-Behandlungsverfahren, gekennzeichnet durch energieintensiven Wärmeeintrag mit einer Leistungsdichte von mehr als 105 W/cm2 und hohen Aufheizgeschwindigkeiten von 107 bis 109 K/s der Randschicht über die Schmelztemperatur mit örtlichem Aufschmelzen und nachfolgender Erstarrung mit hohen Abkühlungsgeschwindigkeiten von 104 bis 107 K/s durch Wärmeabfuhr in die nicht umgeschmolzenen Werkstoffbereiche mit dem Ziel des Härtens (Randschicht-Umschmelz-Härten), oder des Legierens (Randschicht-Umschmelz-Legieren). Als Erwärmungsquellen kommen Lichtbogen, Hochfrequenzinduktion, Laserstrahlen und Elektronenstrahlen zur Anwendung.
Die Laserstrahlbehandlungen von Randschichten zeichnen sich durch eine spezielle Eigenschaft aus: Die Bahnen der Laserstrahlen sind sehr genau und leicht steuerbar. Dadurch lassen sich spezielle geometrische Muster für die Laserstrahlbehandlung auf den Oberflächen von Bauteilen aus metallischen Werkstoffen erzeugen (Honigwabenmuster, Mäandermuster u.a.m.), die das tribologische Verhalten (Reibung, Schmierung und Verschleiß) von Reibpaarungen sehr positiv beeinflussen.
Randschicht-Umschmelz-Härten
Randschicht-Umschmelz-Härten ist eine spezielle Variante zum Erzeugen von feinkristallinen Randschichtgefügen durch energieintensives kurzzeitiges Erwärmen der Randschicht auf Temperaturen oberhalb des Schmelzpunktes mit nachfolgendem Erstarren bei hohen Abkühlungsgeschwindigkeiten. Beim Gusseisen mit Kugelgraphit erfolgt dabei die Erstarrung nach dem metastabilen System. Es entsteht eine weißerstarrte Randschicht aus Ledeburit und Martensit und eine darunter liegende gehärtete Schicht.
Mit einem CO2-Laser wurde die Randschicht von einem Gusseisen mit Kugelgraphit der Sorte EN-GJS-400-12 umschmelzgehärtet. Die umgeschmolzene Schicht bestand aus einem feinkörnigen Mikrogefüge aus Austenit und Ledeburit. Die Graphitkugeln waren von einer dünnen martensitischen Schicht umgeben. Die gehärtete darunter liegende Schicht enthielt Martensit, Restaustenit und Ferrit an den Graphitkugeln. Die Mikrohärte erreichte 1000 HV100 bis zu einer Tiefe von etwa 100 μm. Bis zu 500 μm Tiefe lag die Mikrohärte bei etwa 850 HV100. [74]. Bild 84 zeigt schematisch die durch die Laserbestrahlung beeinflussten Zonen in der Randschicht.
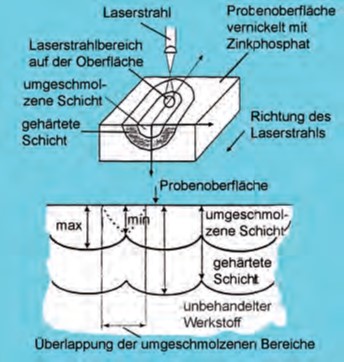
Ein Randschichtumschmelzen kann auch so durchgeführt werden, dass ein kontrolliertes Liniennetzwerk aus weiß erstarrtem Gusseisen in der Randschicht erzeugt wird, eine Mosaikstruktur. Mit einem CO2-Laser wurden bei einem Gusseisen mit Kugelgraphit der Sorte EN-GJS-400-12 umgeschmolzene Linien von 1,6 mm Breite erzeugt. Das Mikrogefüge der umgeschmolzenen Schicht enthielt Ledeburit und Martensit.
Randschicht-Umschmelzlegieren
Randschicht-Oberflächen-Legieren ist ein Sammelbegriff für alle Verfahren zum Legieren einer Randschicht durch energieintensive kurzzeitige lokale Erwärmung auf Temperaturen oberhalb des Schmelzpunkts und Abkühlen (Erstarren) durch intensive Wärmeabfuhr in die benachbarten Werkstoffbereiche. Die Zufuhr von Legierungselementen erfolgt während des Schmelzens oder durch vorheriges Aufbringen von Schichten.
Bei einem Gusseisen mit Kugelgraphit mit 3,4 % C; 2,8 % Si; 0,3 % Mn und 0,06 % Mg wurde mit einem CW-YAG-Laser in der Randschicht beim Umschmelzen mit Chrom oder Wolfram oberflächenlegiert [75]. Die Laserleistung lag bei 500 bis 700 W, der Laserstrahldurchmesser bei 2 mm an der Oberfläche, die Vorschubgeschwindigkeit bei 1 bis 5 mm/s. Die Gusseisenoberfläche wurde vorher mit dem Metallpulver beschichtet oder das Legierungselement wurde elektrolytisch aufgetragen. Durch das Randschicht-Umschmelz-Legieren mit Chrom entstanden in der Randschicht Chromcarbide (Cr7C3). Die Oberflächenmikrohärte betrug mindestens 950 HV01. Beim Oberflächenlegieren mit Wolfram enthielt die Randschicht Wolframcarbid ((Fe,W)6C6) und Fe3C). Als Oberflächenmikrohärte wurden 1300 HV01 erreicht. Diese Carbide lagen in einer metallischen Grundmasse aus Martensit und Restaustenit.
Beim Randschicht-Umschmelz-Legieren mit einem 2000-W-CW-CO2-Laser wurden in ein perlitisches Gusseisen mit Kugelgraphit mit 3,62 % C; 2,32 % Si; 0,36 % Mn; 0,57 % Cu; 0,036 % Mg und 0,030 % Ce Wolframcarbidteilchen eingebracht [76]. Die Gusseisenoberfläche wurde mit Wolframcarbidpulver mit einem organischen Bindemittel beschichtet. Die Pulverteilchen hatten eine Korngröße von < 0,071 mm. Die Laserleistung wurde mit 1500 und 1800 W eingestellt. Der Laserstrahldurchmesser lag bei 4 mm, die Vorschubgeschwindigkeit bei 2,5 bis 15 mm/s. Nach der Laserstrahlbehandlung ergab sich folgender Schichtaufbau: Eine Schicht mit Wolframcarbid und einem Wolframgehalt bis zu 17 %, eine wärmebehandelte Übergangsschicht mit Austenit und Ledeburit. Die Tiefe der aufgeschmolzenen Schicht lag bei 0,4 bis 0,8 mm. Die Oberflächenmikrohärte erreichte 1500 HV.
Oberflächenverformen
Zum Verformen der Oberflächen von Gussteilen kommen mehrere Verfahren zur Anwendung, die zum Einstellen bestimmter Eigenschaften zum Einsatz kommen.
Das Festwalzen ist eine örtliche plastische Verformung durch Querwalzen mit dem Ziel, in der Randschicht des Gussteils Druckeigenspannungen zu erzeugen.
Das Glattwalzen ist ein fortschreitendes Druckumformen der oberflächennahen Bereiche eines Gussteils mit dem Ziel, die Oberflächenrauheit zu verringern. Gleichzeitig findet auch eine Kaltverfestigung der Randschicht statt.
Unter Kugelstrahlen versteht man das Strahlen metallischer Werkstoffe mit kugeligem Strahlmittel (Stahlkugeln) zum Erzeugen von Druckeigenspannungen in der Randschicht von Gussteilen, um die Schwingfestigkeit von gegossenen Bauteilen zu verbessern.
Festwalzen/Glattwalzen
Bei Untersuchungen zum Festwalzen von zwischenstufenvergütetem Gusseisen mit Kugelgraphit mit einer Zugfestigkeit von 1000 N/mm2 wurden zylindrische Proben mit einem Einrollenwalzdorn bei einer Drehzahl von 355 Umdrehungen/min und einem Vorschub von 0,19 mm je Umdrehung auf einer Zugspindeldrehmaschine bearbeitet. Die Walzkraft wurde mit 1500, 2000, 2500 und 3000 N festgelegt. Im Bild 85 ist die mittlere Rauhtiefe Rtm in Abhängigkeit von der Walzkraft dargestellt. Die mittlere Rautiefe sinkt zunächst mit zunehmender Walzkraft stark ab, durchläuft ein Minimum und steigt dann wieder stark an. Die Verringerung der Rautiefe bis zu einem Minimalwert von 4 μm ist auf eine zunehmende Glättung des Oberflächenfeinprofils zurückzuführen. Der anschließende Anstieg der Rautiefe hat eine Zerstörung der Randschicht als Ursache. Durch Mikrohärtemessungen als Funktion des Randabstands wurden eine Verfestigungstiefe von 550 μm und ein Verfestigungsgrad von 1,45 errechnet. Der maximale Wert der Mikrohärte in unmittelbarer Randnähe lag bei 1400.
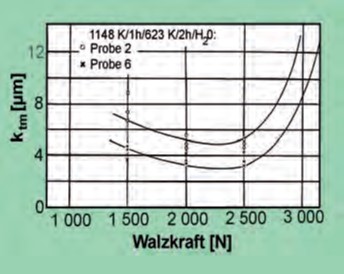
Ausgangsrautiefe:
Probe 2: 30,2; 29,6; 22,5; Dmr. 27,43 μm
Probe 6: 12,5; 16,5; 15,5; Dmr. 14,83 μm
Probe 6 (3000 N): 14,0; 15,6; 19,2 μm
Im Bild 87 wird die Schwingfestigkeit von Kurbelwellen aus Gusseisen mit Kugelgraphit der Sorte EN-GJS-700-2 gezeigt, bei denen die Übergangsradien entweder nitriert oder festgewalzt wurden [78]. Deutlich erkennbar ist, dass die Schwingfestigkeit durch Nitrieren spürbar verbessert werden kann. Durch Festwalzen kann demgegenüber eine noch wesentlich höhere Schwingfestigkeit erreicht werden.
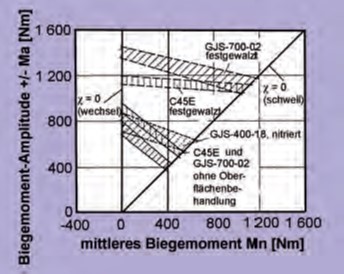
Bei Untersuchungen zum Glattwalzen von zwischenstufenvergütetem Gusseisen mit Kugelgraphit [79] wurden zylindrische Stäbe nach der Wärmebehandlung überschliffen und auf einer Zugspindeldrehmaschine mit Diamantwerkzeugen geglättet. Bei diesen Untersuchungen wurden die Glättspannung, die Anzahl der Glättdurchgänge und der Radius des Glättdiamanten variiert. Die Drehzahl und der Vorschub blieben konstant. Im Bild 88, das die Mikrohärte in Abhängigkeit vom Randabstand zeigt, ist die durch das Diamantglätten erzielte Verfestigung der Randschicht deutlich sichtbar. Die Tiefe der verfestigten Randschicht erreicht dabei 400 bis 500 μm. Die Mikrohärte am Rand steigt von etwa 400 auf rund 700 Härteeinheiten. Bei den durchgeführten Glättversuchen konnte auch eine Verformung der Graphitkugeln in der Randschicht beobachtet werden. Durch Auswertung dieser Graphitkugelverformung konnte auf einen Umformgrad von 40 in der Randschicht geschlossen werden.
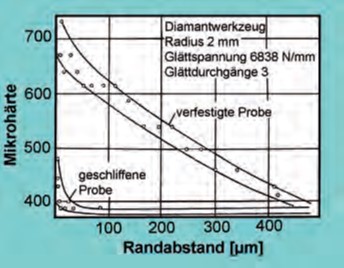
Bei Untersuchungen zum Erhöhen der Schwingfestigkeit von Bauteilen aus Gusseisen mit Kugelgraphit wurden an abgestuften Wellen aus EN-GJS-400-18, ENGJS-600-3, EN-GJS-800-2 (vergütet) und EN-GJS-900-2 (zwischenstufenvergütet) die Biegewechsel- und die Biegeschwellfestigkeit die Übergangsradien fest gewalzt. Die Ergebnisse (Bild 89) [80] wurden mit den Schwingfestigkeit von Proben mit gedrehten Übergangsradien verglichen. Durch das Festwalzen der Übergangsradien konnten die Dauerfestigkeit und die Betriebsfestigkeit wesentlich erhöht werden.
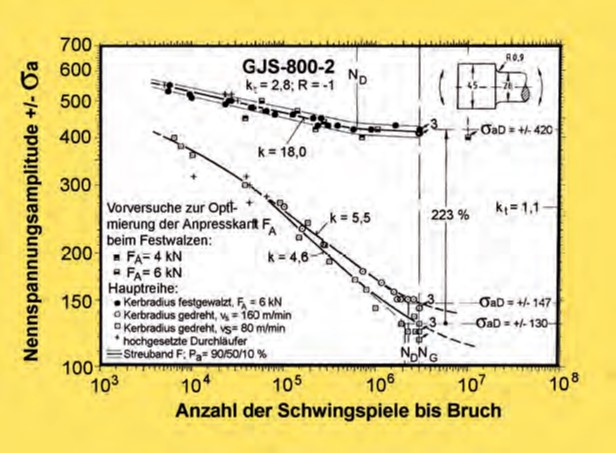
Schwingfestigkeitsuntersuchungen (Zeit-, Dauer- und Betriebsfestigkeitskennwerte bei Wechsel- und Schwellbeanspruchung) an Proben aus EN-GJS-400-15, EN-GJS-700-2 und EN-GJS-1000-5 mit geschliffenen, festgewalzten, induktionsgehärteten und induktiv gehärteten, angelassenen und fest gewalzten Übergangsradien zeigten, dass durch die genannten Randschichtbehandlungen die Schwingfestigkeiten deutlich erhöht werden konnten [81].
Auch das Festwalzen, das Kalibrieren und das Kugeldrücken an Querbohrungen bei abgesetzten Wellen aus Gusseisen mit Kugelgraphit EN-GJS-700-2 führen zu einer Erhöhung der Torsionsschwingfestigkeit bei wechselnder Beanspruchung. Beim Kalibrieren wurde eine Stahlkugel durch die gesamte Bohrung gedrückt. Beim Kugeldrücken wurde eine Stahlkugel beidseitig in die Bohrungsansenkung gedrückt. Die relative Steigerung der Torsionswechselfestigkeit ist im Bild 90 [82] dargestellt. Die wirksamste Maßnahme war dabei das Kalibrieren.
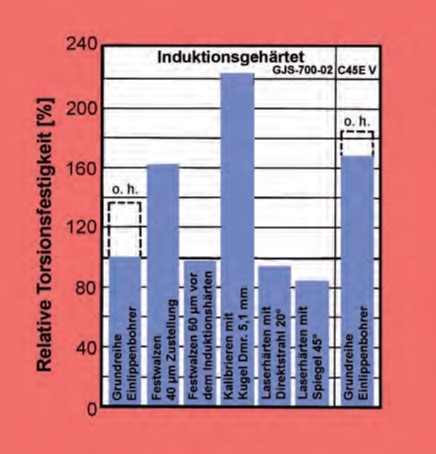
Kugelstrahlen
An Proben aus zwischenstufenvergütetem Gusseisen mit Kugelgraphit (ADI) mit einer Zugfestigkeit von 1135 N/mm2 wurde das Biegewechselverhalten an glatten Proben nach einem Kugelstrahlen und/oder einem Festwalzen ermittelt. Beim Kugelstrahlen bilden sich in der Randschicht hohe Druckeigenspannungen auf.
Gewinderollen
Die gute Umformbarkeit des Gusseisens mit Kugelgraphit erlaubt auch das Gewinderollen. Am Beispiel eines Brückenfittings wurde an der Spindel aus EN-GJS-400-18 ein Trapezgewinde M 48 x 4 mit einer Gewindelänge von 180 mm durch Gewinderollen hergestellt [83].
Weiterführende Informationen zum Werkstoff Gusseisen mit Kugelgraphit
- Hier geht es zu den allgemeinen Informationen: Gusseisen mit Kugelgraphit | GUSS
- Hier finden Sie Informationen zur Matallurgie: Metallurgie | GUSS
- Hier finden Sie Informationen zur Werkstoffprüfung: Werkstoffprüfung | GUSS
- Hier finden Sie Informatioen zu den mechanischen und physikalischen Eigenschafte: Mechanische und physikalische Eigenschaften | GUSS
- Hier finden Sie Informationen zur Spanenden Bearbeitung: Spanende Bearbeitung | GUSS
- Hier finden Sie Informationen zu besonderen Eigenschaften: Besondere Eigenschaften | GUSS
Download
Autoren und Quellen
Autoren:
Dr. Ch. Bartels, DI R. Gerhards, Prof. H. Hanselka, Prof. K. Herfurth, Dr. H. Kaufmann, DI W. Kleinkröger, Dr. M. Lampic, Dr. H. Löblich, Dr. W. Menk, Prof. G. Pusch, Dr. T. Schmidt, DI K.-H. Schütt, DI P. Tölke, Prof. E. P. Warnke