Gusseisen mit Kugelgraphit
Spanende Bearbeitung
Inhalt dieser Seite
-
Allgemeines
-
Drehen
-
Bohren
-
Gewindeschneiden
-
Reiben
-
Fräsen
-
Räumen
-
Bearbeitung von ADI-Gusseisen
-
Download
-
Autoren und Quellen
Allgemeines
Die spanende Bearbeitung von Bauteilen ist ein maßgeblicher Kostenfaktor. Die Optimierung von Werkzeug- und Schnittdaten ist im Hinblick auf eine wirtschaftliche Fertigung von Bedeutung. Dieses beinhaltet nicht nur kurze Stückzeiten, sondern auch eine möglichst hohe Automatisierung des Produktionsablaufes mit geringer Überwachung.
Die Beurteilung der Zerspanbarkeit eines Werkstoffes erfolgt üblicherweise nach den Gesichtspunkten
- abzuspanendes Werkstoffvolumen (Materialzugabe für die Bearbeitung),
- Standzeit und Werkzeugverschleiß,
- Spanbildung,
- Schnittkraft,
- Oberflächengüte und Maßhaltigkeit.
Die beiden ersten Kriterien beeinflussen die Bearbeitungskosten direkt durch ihre Auswirkungen auf die Fertigungszeit (Anzahl Schnitte und Operationen, Spanvolumen pro Zeit aus Schnitttiefe, Vorschub und wirtschaftlicher Schnittgeschwindigkeit). Die Spanbildung ist ein wesentlicher Faktor für die Automatisierungsfreundlichkeit des Fertigungsprozesses. Diesem Kriterium versuchen heute unzählige Spanleitstufengeometrien für die Stahlbearbeitung gerecht zu werden. Für Gusseisen mit Kugelgraphit ist dies nicht erforderlich, da die in die Eisenmatrix eingebetteten Graphiteinschlüsse zu einem
kurzbrüchigen Span führen. Die Graphiteinschlüsse sind auch der Grund für die niedrigeren Schnittkräfte bei der Bearbeitung von Gusseisen mit Kugelgraphit (Tabelle 18). Sie können als günstige Randbedingung im Zerspanungsprozess betrachtet werden, die zu geringerer Werkstück-, Werkzeug- und Maschinenbelastung führen, ein günstigeres Schwingungsverhalten aufweisen und niedrigere Antriebsleistungen erfordern. Als Oberflächenrauheit werden beim Feindrehen, Feinfräsen oder Reiben Werte bis knapp unter Ra = 1 μm erzielt, die für Festsitze vollkommen ausreichend sind. Noch bessere Werte können durch Schleifen, Honen, Läppen oder Glattwalzen erreicht werden.
Insgesamt betrachtet ist Gusseisen mit Kugelgraphit gut und unproblematisch zerspanbar. Wenig Schwierigkeiten mit der Späneabfuhr und geringe Empfindlichkeit bei unterbrochenen Schnitten (niedrigere Schnittkräfte und bessere Dämpfung) selbst beim Anschnitt in die Gusshaut sind kennzeichnende Merkmale dieser Werkstoffgruppe. Verglichen mit Stählen gleicher Härte oder ähnlicher Festigkeit liegen bei Gusseisen mit Kugelgraphit die anwendbaren Schnittgeschwindigkeiten, vor allem beim Schlichten mit Hartmetall, etwas tiefer. Mit höheren Vorschüben und optimierter Werkzeugauslegung oder beim Schruppdrehen
mit Mehrfach-Werkzeug-Bestückung beziehungsweise weniger Schnitten dank geringerer Materialzugabe kann dieser Nachteil sehr oft ausgeglichen werden.
Drehen
Der bevorzugte Schneidstoff für die Drehund Fräsbearbeitung im üblichen (Zahn) Vorschubbereich von 0,15 bis 0,6 mm/U ist Hartmetall in Form von Wendeschneidplatten. Den steigenden Ansprüchen an Verschleißfestigkeit und Stabilität sowie an die Schneidengeometrie begegnen die Hersteller mit der Entwicklung immer besserer Schneidstoffe und optimaler Geometrien für das bestmögliche Zerspanungsergebnis. Dank der rasanten Entwicklung von Werkzeugen und Maschinen ist die Bearbeitung heute dreimal schneller als noch vor 25 Jahren (Bilder 187 und 188).
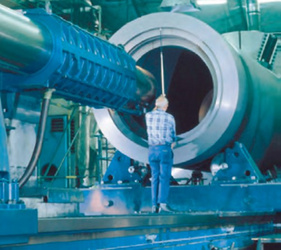
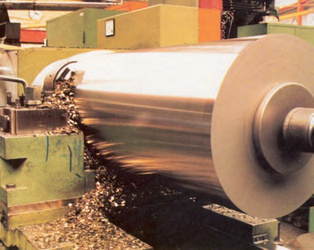
Zum Drehen haben sich beschichtete Hartmetalle HC-K25 und HC-K30 von der Schrupp- bis hin zur Feinschlichtbearbeitung durchgesetzt. Die Beschichtung erfolgt mit TiC, TiCN oder Al2O3. Auf modernen Hartmetall-Wendeschneidplatten werden diese Schichtwerkstoffe zu Mehrlagenbeschichtungen kombiniert. Je nach Schneidengeometrie und Maschinenleistung sind Schnitttiefen bis etwa 10 mm möglich. Die Schnittgeschwindigkeiten bewegen sich im Bereich von 200 bis 600 m/min, wobei die Obergrenze eher für ferritische Werkstoffe mit geringer Härte erreicht wird, während die festen perlitischen GJS-Sorten sowie Werkstücke mit hoher Oberflächenhärte mit geringeren Schnittwerten zu bearbeiten sind (Bild 189).
Schneidplatten aus Oxidkeramik konnten sich beim Drehen von Gusseisen mit Kugelgraphit nicht wie bei manchen Bauteilen aus Gusseisen mit Lamellengraphit, auf breiter Basis durchsetzen. Ebenso zeigen unbeschichtete Schneidkeramiken aus Siliciumnitrid ihre Hauptvorteile bei Gusseisen mit Lamellengraphit, nämlich die relative Unempfindlichkeit gegenüber thermischer Wechselbelastung und mechanischer Schlagbeanspruchung. Bei der Bearbeitung von Gusseisen mit Kugelgraphit im nicht unterbrochenen Schnitt treten jedoch wesentlich höhere Temperaturen an der Schneide auf. Erst die mit TiN, TiCN oder Al2O3 beschichtete Siliciumnitrid-Keramik weist einen ausreichenden Temperatur- und Verschleißwiderstand und damit die geforderte Standzeit auf. Aufgrund von Gratbildung wird sie meist nur zur Schruppbearbeitung von ferritischem Gusseisen mit Kugelgraphit bei Schnittgeschwindigkeiten von 200 bis 1500 m/min eingesetzt.
Zum Schlichten von perlitischem oder gehärtetem Gusseisen mit Kugelgraphit kommen CBN-Schneidplatten BH-K20 und BH-K25 bei Schnittgeschwindigkeiten von 200 bis 800 m/min (in Einzelfällen auch bis 1 500 m/min) und Schnitttiefen bis etwa 4 mm zum Einsatz. Aufgrund der hohen Härte und Bruchzähigkeit ist CBN für das Hartfeindrehen im unterbrochenen Schnitt prädestiniert. Beim Hartfeindrehen mit nicht unterbrochenen Schnitten und gleichmäßigem Aufmaß wird die empfindlichere Mischkeramik aus Titancarbonitrid und Al2O3 verwendet. Sie kann bei deutlich geringeren Kosten pro Schneide im gleichen Schnittgeschwindigkeits- und Vorschubbereich eingesetzt werden wie CBN.
Um das große Potential hinsichtlich der Schnittbedingungen bei Keramik- und CBN-Werkstoffen zu nutzen, müssen hohe Spindelleistungen, -drehzahlen und -vorschübe, eine hohe Maschinensteifigkeit sowie ein geringes Lagerspiel ebenso vorausgesetzt werden wie ein geschlossener Arbeitsraum mit einer schnellen Späneabfuhr.
Graphithaltige Eisengusswerkstoffe benötigen keine Kühlschmierung. Wird eine Kühlschmieremulsion zum Werkstückkühlen sowie Wegschwemmen von Spänen und Gussstaub eingesetzt, so kann dies bei modernen Schneidwerkstoffen aufgrund der permanenten Thermoschockbelastung der Schneide beim Drehen mit unterbrochenem Schnitt sowie beim Fräsen zu einer deutlichen Verringerung der Werkzeugstandzeit führen [220]. Gegenüber der reinen Trockenbearbeitung lassen sich Standzeit, Schnittgeschwindigkeit und Oberflächenqualität durch Minimalmengenschmierung deutlich steigern. Dabei ist eine
innere Zufuhr des Aerosols durch die Werkzeugaufnahme und das Werkzeug zu bevorzugen.
Grundsätzlich kann und sollte beim Schruppen von Gusseisen mit Kugelgraphit mit hohen Vorschüben gearbeitet werden, sofern es die Stabilität von Werkstück, Werkzeug und Maschine zulässt. Die Richtwerte für Vorschübe und Schnittgeschwindigkeiten hängen stark von der Art der Beschichtung und der Scheidengeometrie ab, so dass auf die Angaben in den Herstellerkatalogen verwiesen werden muss. Der Streubereich der Richtwerte ist weitgehend abhängig von der Werkstoffhärte, wobei eine niedrige Härte die Anwendung der höheren Schnittgeschwindigkeit zulässt. Die Vorschubwerte sind von der Härte nur minimal abhängig. Die Schnitttiefe hat im üblichen Bereich von 1 bis 5 mm keinen Einfluss.
Die Ergebnisse beim Drehen von Randund Kernzone sind bei einwandfreien GJS-Gussteilen gleicher Härte und mit sauber gestrahlter Oberfläche innerhalb von ± 10 % gleich. Die Gusshaut wirkt sich bei Werkstoffen mit geringerer Härte etwas stärker auf das Verschleißverhalten der Werkzeuge aus, da hierbei der Einfluss höherer Schnittgeschwindigkeiten verstärkend wirkt. Andererseits ist zunehmende Werkstückhärte oft mit einer leichten Randentkohlung verbunden, welche die Randschichthärte verringert, wodurch die Standzeit etwas erhöht wird.
Da in einer reibungslosen Fertigung mit geringer Überwachung feste Werkzeugwechsel-lntervalle eingeplant sind, müssen unvorhergesehene Schneidenbrüche vermieden werden. Die Tendenz zur Masseeinsparung und Formoptimierung zum Beispiel von Bauteilen im Fahrzeugbau führt zu Konstruktionen mit Werkstoffaussparungen und damit zu unterbrochenen Schnitten. Eine Untersuchung beim Drehen im unterbrochenen Schnitt bei mehreren Instituten und Firmen hat gezeigt, dass die Werkzeugbruchgrenze vor allem mit höheren Vorschüben und niedrigeren Schnittgeschwindigkeiten ansteigt [228, 221]. Dabei führt die schlagartige Beanspruchung der Werkzeugschneidkante beim Drehen von Stählen früher zum Bruch als bei Gusseisen mit Kugelgraphit.
Im Bild 190 sind die Grenzvorschübe fe dargestellt, bei denen verschiedene Hartmetall-Wendeschneidplatten beim Längsdrehen Z = 3 000 Schläge von 2,5 mm Schnitttiefe aushielten. Die Bruchgrenzen liegen für EN-GJS-400-15 und ENGJS-700-2 im Grenzvorschubbereich fG = 1,25 bis 0,4 mm/U, bei dem Stahl C45E (frühere Bezeichnung Ck 45 N und Ck 45 V) dagegen bei fQ = 0,65 bis 0,1 mm/U.
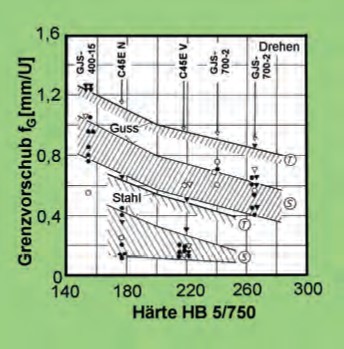
S - Standardtestplatte (positiv) SPUN 120 308,
Halter CSBPR 2525
T - Dreikantplatte (negativ) TNUN 160 408, Halter CTGNR 2525
Schneidstoff:
?? - unbeschichtetes Hartmetall
? - unbeschichtete HM-WSP, Vierkantplatte SPUN, γ = + 6°, λ = 0°, κ = 75°
? - beschichtetes HM-WSP, Dreikantplatte TNUN, γ = - 6°, λ = - 6°, κ = 90°
Schnitttiefe ap = 2,5 mm, Schnittgeschwindigkeit vc = 100 m/min für EN-GJS-700-2, alle anderen Werkstoffe vc = 160 m/min, keine Kühlung
Für den Dauerbetrieb müssen diese Grenzvorschübe um 30 bis 40 % reduziert werden. Optimale Schneidwerkstoffe erlauben beim Drehen im unterbrochenen Schnitt von Gusseisen mit Kugelgraphit im Härtebereich von 150 bis 220 HBW Vorschübe von f = 0,8 bis 0,4 mm/U, also kaum oder nur unwesentlich niedriger (maximal 25 %) als beim Drehen im glatten, kontinuierlichen Schnitt. Die Schnittgeschwindigkeit sollte jedoch keinesfalls reduziert werden.
Bei der Stahlbearbeitung im unterbrochenen Schnitt müssen dagegen zunächst die Werkzeuge (Schneidplatte, Schneidstoff) und Schnittdaten optimiert werden, um einigermaßen günstige Vorschübe erreichen zu können. Daher wird beim Drehen von Gusseisen mit Kugelgraphit höherer Härte der Nachteil niedrigerer Schnittgeschwindigkeit gegenüber Stahl durch wesentlich höhere anwendbare Vorschübe beim unterbrochenen Drehen mehr als ausgeglichen.
Zudem liegt die Bruchgrenze in einem viel engeren Vorschub-Streubereich, ist also genauer definiert. Somit sind in der Praxis beim Drehen von Gusseisen mit Kugelgraphit im unterbrochenen Schnitt keine Schwierigkeiten zu erwarten, sofern ein Minimum an Stabilität von Werkstück, Werkzeug und Maschine gewährleistet ist.
Bohren
Noch wichtiger als beim Drehen ist beim Bohren der kurze Spanbruch von Gusseisen mit Kugelgraphit, wodurch auch bei tiefen Bohrungen geringen Durchmessers die einwandfreie Späneabfuhr gewährleistet ist. Ferner wirken sich hier stärker als beim Drehen die Arbeitsbedingungen wie Vorschub, Bohrverhältnis l/d, Sackoder Durchgangsloch, Kühlschmierung, Bohrkadenz (Taktzeit), Bohrertyp und Schneidwerkstoff auf das Bohrergebnis Noch wichtiger als beim Drehen ist beim Bohren der kurze Spanbruch von Gusseisen mit Kugelgraphit, wodurch auch bei tiefen Bohrungen geringen Durchmessers die einwandfreie Späneabfuhr gewährleistet ist. Ferner wirken sich hier stärker als beim Drehen die Arbeitsbedingungen wie Vorschub, Bohrverhältnis l/d, Sackoder Durchgangsloch, Kühlschmierung, Bohrkadenz (Taktzeit), Bohrertyp und Schneidwerkstoff auf das Bohrergebnis aus. Beim Bohren von Gusseisen mit Kugelgraphit gibt es praktisch keine Spanablaufprobleme und dank der Graphitschmierung kann mit relativ hohen Vorschüben und Schnittgeschwindigkeiten selbst bei größeren Bohrtiefen gearbeitet werden [223, 224]. Niedrigere Vorschubkräfte und Drehmomente als beim Bohren von Stahl schonen Werkzeug und Maschine (Bild 191).
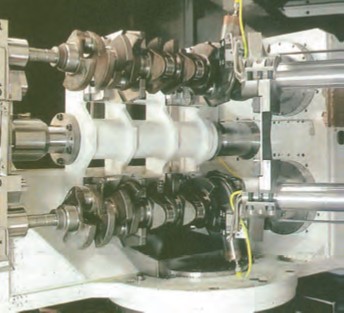
Im Bild 192 sind Vorschub-Richtwerte für drei verschiedene Bohrer-Schneidwerkstoffe angegeben. Spiralbohrer und Wendelbohrer aus Schnellarbeitsstahl HSS sind die am häufigsten verwendeten Werkzeuge. Vollhartmetallbohrer (VHM), meist beschichtet, sind zwar wesentlich teurer, aber sehr leistungsfähig dank zweibis dreifacher Schnittgeschwindigkeit und höheren Vorschüben. Sie können bis 5 x d, in einigen Ausführungen auch bis 10 x d eingesetzt werden und sind häufig mit integrierten Kanälen für eine effektive Kühlmittelzuführung versehen. Kurzbohrer mit Hartmetall-Wendeschneidplatten (HM-WSP) können bei Gusswerkstoffen nur für Bohrtiefen bis 3 x d, vereinzelt bis 5 x d, eingesetzt werden. Beschichtete Wendeschneidplatten erlauben hohe Schnittgeschwindigkeiten bis zum Fünffachen der von HSS bei etwa auf die Hälfte reduzierten Vorschüben. Trotz des teureren Werkzeugs kann dank preiswerter Wendeschneidplatten unter der Voraussetzung wirtschaftlich gebohrt werden, dass kein Bohrerbruch auftritt. Dies ist jedoch bei Gusswerkstoffen äußerst selten der Fall. Voraussetzung dafür sind stabile, leistungsstarke und schnelllaufende Bohrmaschinen, Bohreinheiten oder Bearbeitungszentren.
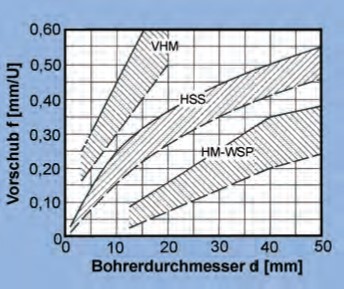
VHM - Vollmetall-Spiralbohrer, meist TiN-beschichtet, mit speziellen Spitzenanschliffen (zum Beispiel HFS- oder SE-Drill), Bohrtiefen bis 3 . d; d = 3 bis 20 mm)
HSS - Schnellarbeitsstahl-Spiralbohrer, Bohrtiefen bis zu 5 . d
HM-WSP - Kurzbohrer (Vollbohrer) mit Hartmetall-Wendeschneidplatten, Bohrtiefen 3 bis 5 . d = >/= 12 mm
Da bei Massenartikeln wie HSS-Spiralbohrern die Preise stark gedrückt werden, kann es große Qualitätsunterschiede geben. Bei Schneidstoff, Wärmebehandlung und Fertigschliff können Einsparungen oft Leistungseinbußen bewirken, wie im Bild 193 dargestellt ist. Das Fabrikat B (durchgezogene Linien) erlaubt 3,4- bis 5-fach längere Standwege oder wie bei Beispiel L = 2000 mm 16 bis 29 % höhere Schnittgeschwindigkeiten als das Fabrikat A (unterbrochene Linien).
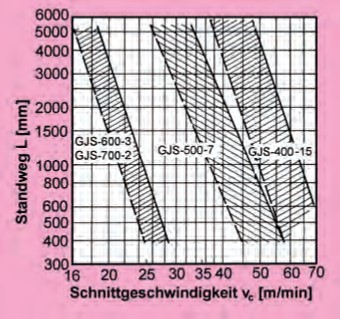
Bohrerdurchmesser d = 8 mm, Bohrtiefe L = 40 mm (= 5 . d), Vorschub f = 0,20 mm/U
Sacklochbohrungen, Kernzone, ohne Kühlung, kein Entspannen
Im Bild 194 ist für L = 2000 mm Standweg die Schnittgeschwindigkeit in Abhängigkeit von der Werkstoffhärte angegeben. Das Streuband der Schnittgeschwindigkeit von Gusseisen mit Kugelgraphit im Härtebereich von 130 bis 300 HBW5/750 liegt etwas unterhalb desjenigen von schwarzem Temperguss (GJMB), aber über dem vom Kohlenstoffstahl C45E.
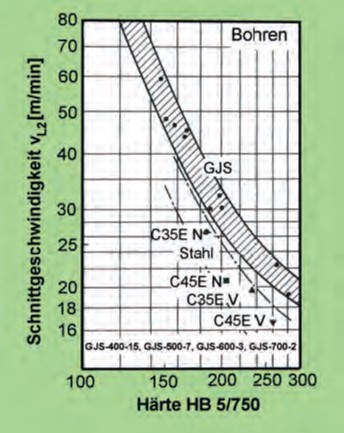
Gewindeschneiden
Innengewinde werden häufig mit HSSWerkzeugen geschnitten. Mit normalen Maschinen-Gewindebohrern wird bei Gusseisen mit Kugelgraphit bei einer Härte bis 250 HBW mit einer Schnittgeschwindigkeit vc = 8 bis 15 m/min und Kühlschmieremulsion und bei Härten bis 300 HBW mit vc = 4 bis 8 m/min vorzugsweise mit Schneidöl gearbeitet [225]. Für höhere Härten sind entsprechend ausgelegte Gewindebohrer einzusetzen. TiNbeschichtete HSS-Gewindebohrer werden mit Schnittgeschwindigkeiten vc um 20 m/min betrieben. Maximale Schnittgeschwindigkeiten vc von 30 bis 100 m/min bieten vorzugsweise mit TiAlN-Beschichtung versehene Hartmetall-Werkzeuge. Selbst bei Trockenbearbeitung liegen die Standzeiten zwei- bis dreimal höher als bei HSS-Werkzeugen. Mit Kühlschmieremulsion lässt sich die Standzeit verdoppeln, mit Minimalmengenschmierung (Hier ist die interne Zuführung durch das Werkzeug zu bevorzugen) sogar noch weiter steigern [226]. Vorteile der internen Minimalmengenschmierung sind zudem eine Unterstützung der Späneabfuhr durch den Luftstrom sowie höhere Oberflächenqualitäten durch die Reibungsminimierung im Schneidenumfeld.
Für duktile Werkstoffe mit einer Bruchdehnung von mindestens 8 % besteht zudem die Möglichkeit, die Fließfähigkeit des Werkstoffes zu nutzen, um so das Gewinde zu furchen. Vorteile sind höhere Gewindefestigkeit und Prozesssicherheit. Dieses Verfahren erfordert allerdings eine gegenüber dem Gewindeschneiden etwa verdoppelte Antriebsleistung sowie das Vorbohren mit größeren und enger tolerierten Werkzeugen.
Reiben
Auf modernen, flexiblen Werkzeugmaschinen werden selbst genaue Bohrungen vorzugsweise mit nachstellbaren Feinbohrwerkzeugen fertig bearbeitet. Dadurch erübrigt sich das Anschaffen teurer Einzweckreibahlen. Die Schnittgeschwindigkeit beim Reiben beeinflusst die Fertigungszeit nur wenig, so dass mit den Richtwerten der Werkzeuglieferanten gearbeitet werden kann (Hartmetall: 25 bis 40 m/min, Hartmetall beschichtet: 50 bis 80 m/min, Cermet: 120 bis 200 m/min, Cermet beschichtet: 150 bis 250 m/min).
Die Abstimmung auf die jeweiligen bauteilspezifischen Anforderungen wie Vorschub, Teilung oder Schmiermittel muss fallweise erfolgen.
Fräsen
Beim Fräsen, naturgemäß ein spangebendes Fertigungsverfahren mit diskontinuierlicher Spanbildung an der Schneide, gelten sinngemäß die Ausführungen für das Drehen mit unterbrochenem Schnitt. Oxid- und Mischkeramiken haben sich nicht bewährt, wohl aber beschichtete Siliciumnitridkeramiken für die Schruppbearbeitung mit Schnittgeschwindigkeiten von 550 bis 1 000 m/min auf Maschinen mit entsprechender Spindelleistung, -drehzahl und -steifigkeit (Bilder 196 und 197).
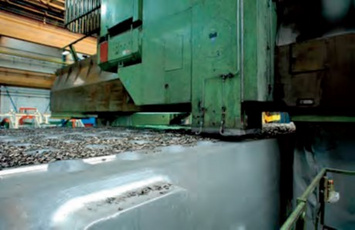
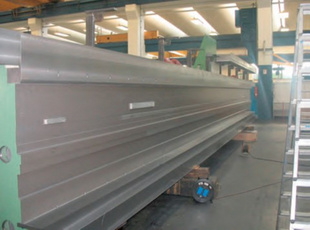
Im Geschwindigkeitsbereich zwischen 200 und 600 m/min kommen Wendeschneidplatten aus Cermet sowohl für die Schlicht- als auch die Schruppbearbeitung zum Einsatz. Dabei handelt es sich um Verbundwerkstoffe aus keramischen Werkstoffen in einer metallischen Matrix, die sich durch eine besonders hohe Härte und Verschleißfestigkeit auszeichnen. Gegenüber den klassischen Hartmetallen, denen die Cermets entsprechend DIN ISO 513 zuzuordnen sind, haben sie aufgrund der anderen Zusammensetzung eine höhere Oxidationsbeständigkeit.
Mit Wendeschneidplatten aus beschichtetem Hartmetall lassen sich je nach Anwendungsfall und Geometrie Schnittgeschwindigkeiten zwischen 60 und knapp 400 m/min erreichen. Aufgrund der Ausführungsvielfalt sei hier auch wieder auf die Angaben in den Herstellerkatalogen verwiesen (Bild 198).
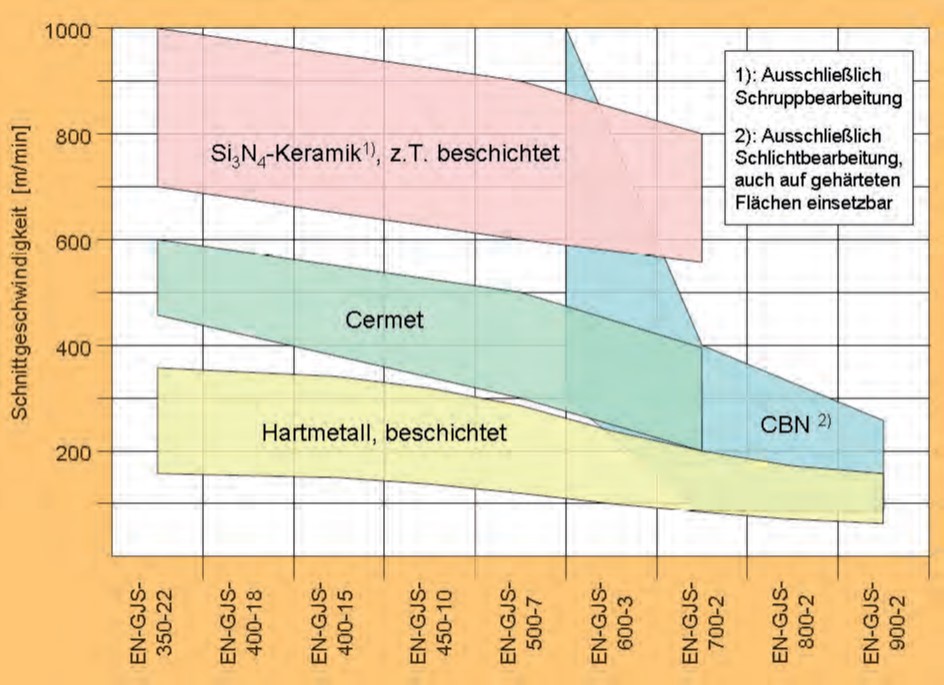
Räumen
Mit HSS-Räumnadeln wird je nach Oberflächenanforderung und Werkzeugauslegung mit einer Schnittgeschwindigkeit von v = 3 bis 10 m/min gearbeitet. Auch hier sind unter stabilen Arbeitsbedingungen sehr hohe Abtragsraten möglich, zur Werkstückvorbearbeitung bis über 0,3 mm Schnitttiefe pro Zahn. Wie fast immer bei graphithaltigem Eisenguss kann trocken oder mit Kühlschmieremulsion gearbeitet werden.
Bearbeitung von ADI-Gusseisen
Die Eigenschaftskombination aus hoher Festigkeit und erhöhter Duktilität macht ADI (siehe Kapitel 8.2) zu einem im Vergleich zu gewöhnlichem Gusseisen mit Kugelgraphit schwieriger zu bearbeitenden Werkstoff, der höhere Anforderungen an die thermischen Eigenschaften der Schneidstoffe stellt. Um übermäßigen Kolkverschleiß durch die freiwerdende Verformungsenergie zu vermeiden, können beschichtete Hartmetall-Werkzeuge bereits bei der Bearbeitung von EN-GJS-900-7 nur mit relativ geringen Schnittgeschwindigkeiten von 120 bis 200 m/min eingesetzt werden. Bei der Bearbeitung von ADIWerkstoffen wirkt sich die Anwendung von Kühlschmierstoffen Standzeit erhöhend aus. Je nach Fertigungsverfahren lassen sich mit speziellen, auf die ADIBearbeitung abgestimmten Werkzeuggeometrien die Standzeiten erhöhen. So werden mittlerweile Hartmetall-Bohrer angeboten, bei denen ein Radienanschliff die Gefahr von Ausbrüchen an den hochbelasteten Ecken drastisch reduziert.
Mit Schneidkeramik (Aluminiumoxid) kann die Schnittgeschwindigkeit unter günstigen Bedingungen bis 400 m/min gesteigert werden. Siliciumnitridkeramik und CBN sind für hochduktiles ADI nicht einsetzbar [111].
Bezüglich der als schwierig geltenden Bearbeitung haben neuere Untersuchungen gezeigt, dass ADI grundsätzlich nicht schwerer zu zerspanen ist als höherfeste GJS-Sorten. Allerdings sind spezielle an den Werkstoff angepasste Spanungsstrategien erforderlich, die sich von der Vorgehensweise beim Gusseisen mit Kugelgraphit deutlich unterscheiden, denn die hohe Wärmeentwicklung erfordert bei der ADI-Bearbeitung abgesenkte Schnittgeschwindigkeiten im kontinuierlichen Schnitt. Dieser Produktivitätsverlust kann aber durch erhöhte Vorschübe ausgeglichen werden. PKD und CBN sind zwar nicht geeignet, aber Hartmetallschneiden mit speziell abgestimmter Schneide sind einsetzbar. Untersuchungen ergaben, dass bei der Zerspanung von EN-GJS-800-8 (ADI) ein ähnliches Kraftniveau wie beim EN-GJS-600- 3 vorliegt. Bei der Fräsbearbeitung konnten keine signifikanten Unterschiede zwischen dem EN-GJS-800-8 und dem EN-GJS-700-2 nachgewiesen werden.
Weiterführende Informationen zum Werkstoff Gusseisen mit Kugelgraphit
- Hier geht es zu den allgemeinen Informationen: Gusseisen mit Kugelgraphit | GUSS
- Hier finden Sie Informationen zur Metallurgie: Metallurgie | GUSS
- Hier finden Sie Informationen zur Werkstoffprüfung: Werkstoffprüfung | GUSS
- Hier finden Sie Informationen zur Wärme- und Oberflächenbehandlung: Wärme- und Oberflächenbehandlung | GUSS
- Hier finden Sie Informationen zu den mechanischen und physikalischen Eigenschaften: Mechanische und physikalische Eigenschaften | GUSS
- Hier finden Sie Informationen zu besonderen Eigenschaften: Besondere Eigenschaften | GUSS
Download
Autoren und Quellen
Autoren:
Dr. Ch. Bartels, DI R. Gerhards, Prof. H. Hanselka, Prof. K. Herfurth, Dr. H. Kaufmann, DI W. Kleinkröger, Dr. M. Lampic, Dr. H. Löblich, Dr. W. Menk, Prof. G. Pusch, Dr. T. Schmidt, DI K.-H. Schütt, DI P. Tölke, Prof. E. P. Warnke