Gusseisen mit Kugelgraphit
Metallurgie
Inhalt dieser Seite
Metallurgie
Grundsätzliches
Man hatte Mitte des 20. Jhs. mit der Magnesiumbehandlung ein serientaugliches Verfahren zur kugelförmigen Ausbildung des Graphits im Gusseisen entwickelt. Magnesium und Cer waren die entscheidenden Hilfsmittel, denn beide entschwefeln und desoxidieren zugleich und führen zur Kugelbildung. Wie die Kugeln aber wirklich entstehen, wusste damals mit Ausnahme der Aachener Gießer keiner so richtig (Bild 54). Die Frage dürfte heute zu etwa 70 % geklärt sein, die „letzten Geheimnisse“ spielen also noch immer eine Rolle. Auch der Streit darüber, welche Form des Graphits – die Lamelle oder die Kugel – die „natürliche“ wäre, ist noch nicht vom Tisch, obwohl die Tatsache, dass die Lamellenbildung reversibel ist und die Kugelbildung nicht, die Fronten hätte bereinigen sollen. Wie dem aber auch sei, Gusseisen mit Kugelgraphit floriert, ist aber durchaus noch entwicklungsfähig, was alle Beteiligten, Hersteller wie Abnehmer, freuen sollte (Bild 55).
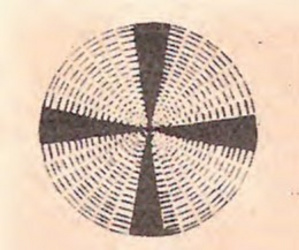
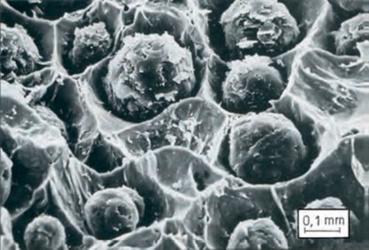
Chemische Zusammensetzung
Eine Vielzahl von metallurgischen und kristallographischen Einflüssen ist an der Graphitkugelbildung beteiligt, die zu unterschiedlichen Ausbildungsformen führen. Für das Schmelzen ergibt sich daraus die Forderung nach einwandfreien Rohstoffen vorzugsweise für den Einsatz in einem Induktionstiegelofen. Als Einsatzstoffe für das Erschmelzen des Basiseisens werden Roheisen, Stahlschrott und arteigenes Kreislaufmaterial verwendet. Das Verhältnis Roheisen/Stahl variiert etwa zwischen 0,5 und 2. Häufig werden auch Legierungselemente zugesetzt, sei es zur Einstellung des gewünschten Perlitanteils im Gefüge des Gusszustands oder bei der Herstellung von legierten Sorten.
Angaben zur chemischen Analyse von Gusseisen mit Kugelgraphit nach DIN EN 1563 und DIN EN 1564 berühren ein sehr komplexes Gebiet. In den Gießereien werden für eine Analyse bis zu 30 chemische Elemente analysiert und bewertet. Für allgemeine unverbindliche Orientierung sei als ein Beispiel für eine chemische Analyse für Gusseisen mit Kugelgraphit folgende Zusammensetzung genannt: 3,67 % C; 2,4 % Si; 0,42 % Mn; 0,03 % P; 0,02 % S und 0,041 % Mg. Über die Bedeutung dieser Elemente und über den Einfluss von Legierungs- und Spurenelementen auf die Eigenschaften von Gusseisen mit Kugelgraphit wird umfassend in [46] berichtet.
Eine Gießerei liefert Gussteile aus Gusseisen mit Kugelgraphit nach den oben genannten Normen nach Festlegung der mechanischen Eigenschaften. Dazu gehören die Zugfestigkeit, die 0,2 %-Dehngrenze, die Bruchdehnung, in speziellen Fällen die Kerbschlagarbeit sowie Angaben zur Brinellhärte. Die genannten Normen legen fest: „Das Verfahren zur Herstellung von Gusseisen mit Kugelgraphit sowie dessen chemische Zusammensetzung und jede Wärmebehandlung sind, sofern der Käufer nichts festgelegt hat, dem Ermessen des Herstellers überlassen.“ Für die chemischen Elemente, die im Gusseisen mit Kugelgraphit vorhanden sind, kann folgende Einteilung gewählt werden:
- Graphitisierend wirkende Elemente: Sie fördern die Erstarrung nach dem stabilen Fe-C-Diagramm mit Bildung von Graphitkristallen.
- Carbidstabilisierende Elemente: Diese Elemente führen wie zum Beispiel. Chrom (Cr) zu einer Erstarrung nach dem metastabilen Fe-C- Diagramm ohne Graphitkristalle.
- Störelemente: Diese Elemente stören die Bildung von Kugelgraphit.
Das wichtigste graphitisierend wirkende Element ist das Silicium (Si). Die Werkstoffsorten des Gusseisens mit Kugelgraphit sind deshalb Fe-C-Si-Legierungen.
Carbidstabilisierende Elemente dürfen bestimmte Gehalte nicht übersteigen, weil sonst bei der Erstarrung oder bei der Gefügeumwandlung im festen Zustand unerwünschte Effekte auftreten können. Bei der Erstarrung besteht bei zu hohen Gehalten an Carbid stabilisierenden Elementen die Gefahr, dass im ganzen Gussteil oder in bestimmten Bereichen von ihm sich keine Graphitkristalle bilden, sondern ein graphitfreies Mikrogefüge, dass als weißes Gusseisen bezeichnet wird. Dadurch kann ein Gussteil völlig unbrauchbar werden oder muss, wenn der Anteil an weißem Gefüge relativ klein ist, wärmebehandelt werden. Das erhöht die Produktionskosten.
Bei der Umwandlung des Austenits bei der Abkühlung im festen Zustand wird die Einstellung eines hochwertigen ferritischen Gefüges durch Carbid stabilisierende Elemente beeinträchtigt. Eine Wärmebehandlung kann hier hilfreich sein, beeinträchtigt aber die Wirtschaftlichkeit. Unerlässlich ist die Berücksichtigung der Perlit stabilisierenden Wirkung von Elementen auf das Grundgefüge im Gusszustand. Dieser Einfluss wurde durch die Perlitwertzahl Px ausgedrückt [47].
Px = 3,0 Mn – 2,65 (Si – 2,0) + 7,75 Cu + 9,0 Sn + 375 Pb + 333 Bi + 20,1 As + 9,6 Cr + 71,7 Sb (1)
Aus der Beziehung F = 961 e-Px (in %) lässt sich der Ferritanteil in Prozent ermitteln.
Andererseits wirken Carbid stabilisierende Elemente sich günstig auf die Einstellung eines perlitischen Gundgefüges aus, oder sie führen zu günstigen speziellen Eigenschaften wie z.B. ein Zusatz von Molybdän (Mo) bei den SiMo-Werkstoffen.
Es gibt chemische Elemente, die speziell die Kugelgraphitbildung bei der Erstarrung stören, die sogenannten Störelemente [47, 48]. Dazu gehören z.B. Blei (Pb), Wismut (Bi), Antimon (Sb), Arsen (As), Titan (Ti), Zinn (Sn) und Aluminium (Al). Übersteigen die Gehalte solcher Störelemente kritische Gehalte, wie zum Beispiel 0,004 % Wismut, so bilden sich bei der Erstarrung keine Graphitkugeln mehr, sondern sehr ungünstige Graphitformen. Es entsteht kein Gusseisen mit Kugelgraphit mehr. Die kritischen Gehalte der Störelemente sind meist sehr klein. Sie liegen im Bereich von einigen Tausendstel bis Hundertstel Prozent. Diese Störwirkung ist auch abhängig von der Gussteilwanddicke. Diese Störelemente wirken um so schärfer, je größer die Gussteilwanddicke ist. Für die komplexe Wirkung technisch bedeutungsvoller Störelemente wurde eine Spurenbewertungszahl Sb ermittelt [47]. In die nachstehend angeführte Gleichung werden für die einzelnen Elemente die tatsächlich vorliegenden Gehalte eingesetzt: Je höher die Zahl vor einem Störelement ist, um so kleiner ist der kritische Gehalt. Für die Brauchbarkeit eines metallischen Einsatzstoffs muss die Spurenbewertungszahl < 1 sein.
Sb = 4,4 Ti + 2,0 As + 2,3 Sn + 5,0 Sb + 290 Pb + 370 Bi + 1,6 Al (2)
Die genannte Störwirkung kann durch Zusatz von Seltenen Erdmetallen wie zum Beispiel Cer (Ce) in gewissen Grenzen neutralisiert werden, was jedoch die Produktionskosten erhöht. Die kritischen Gehalte der Störelemente sind von ihrem Atomvolumen abhängig. Je größer das Atomvolumen ist, um so kleiner ist der kritische Gehalt eines Störelements[48].
Bei der Wahl der richtigen chemischen Analyse für Gusseisen mit Kugelgraphit spielt auch die Größe des Gussteils (seine Wanddicke) und die Art des Gießverfahrens eine bedeutende Rolle.
Das komplexe System für eine gussteilbezogene optimale chemische Analyse für Gusseisen mit Kugelgraphit wird von den Fachleuten in den Gießereien voll beherrscht. Die Kunden einer Gießerei erhalten hochwertige Gussteile mit den von ihnen bestellten und von der Gießerei nach den gültigen DIN EN 1563 und DIN EN 1564 festgelegten mechanischen Eigenschaften. Um die chemische Zusammensetzung des Gusseisens mit Kugelgraphit brauchen sie sich gar nicht zu kümmern. Das schließt nicht aus, dass in wenigen Sonderfällen von den Kunden spezielle Wünsche für die chemische Zusammensetzung an die Gießereien herangetragen werden können. Das ist dann in Absprache mit einer Gießerei in den Lieferverträgen unter Beachtung der allgemeinen und speziellen Lieferbedingungen DIN EN 1559-1 und DIN EN 1559-3
festzulegen.
Ein besonderer Wert muss auf die Auswahl des Roheisens und geeigneter Stahlschrottsorten gelegt werden. Bedingung sind niedrige Gehalte an Phosphor und Schwefel sowie solchen Begleitelementen, die einen ungünstigen Einfluss auf die Kugelgraphitbildung und die Ausbildung der metallischen Grundmasse haben, wie zum Beispiel Blei, Antimon, Wismut, Bor, Arsen und Titan.
Als Stahlschrott darf auf keinen Fall der „Sammelschrott“ eingesetzt werden, der stets von unhomogener Zusammensetzung ist. Empfehlenswert dagegen ist so genannter Entfallstellenschrott, das heißt, Abfälle aus der Stahl herstellenden oder verarbeitenden Industrie. Die genaue Kenntnis der Entfallstelle sichert ein Einsatzmaterial von gleicher chemischer Zusammensetzung - Knüppelenden, Grobblechabschnitte, Flanschschrott, Tiefziehblech. Das Beschaffen von geeignetem Schrott ist jedoch im Zuge der Globalisierung der Wirtschaft zunehmend schwieriger geworden.
Unerwünschte Spurenelemente können sowohl durch Roheisen als auch durch Stahlschrott eingeschleppt werden. Beim Roheisen handelt es sich um charakterisierende Gruppierungen (Fingerabdrücke), die Unterschiede sind aber weit geringer als beim Stahlschrott, der in der Regel die Hauptmenge an Spurenelementen einbringt [44]. Die Qualität des Stahlschrotts nimmt aus der Sicht des Gießers mit steigender Tendenz ab. Unmittelbare Ursachen dafür sind der steigende Anteil an legiertem und vor allem mikrolegiertem Stahl an der Gesamtproduktion und steigende Mengen an Nichteisen-Bestandteilen. Eine in den achtziger Jahren vom U. S. Bureau of Mines auf Grundlage von Untersuchungen des Batelle-Instituts und der Ohio State University veröffentlichte Studie [45] weist für die Zukunft auf die Konsequenzen hin, die sich aus der Verwendung von Stahlschrott ergeben. Innerhalb der letzten zwanzig Jahre hat sich diese Vorhersage mehr als erfüllt. Weitere wichtige Einsatzstoffe zum Einstellen der gewünschten chemischen Zusammensetzung sind Aufkohlungsmittel (schwefelarme Elektrodenkohle, Petrolkoks, Koksgrus), Aufsilicierungsmittel (Ferrosilicium, Siliciumcarbid), Ferromangan sowie - zum Einstellen besonderer Eigenschaften - beispielsweise Kupfer, Zinn, Nickel und Ferromolybdän. Auch für diese Stoffe gilt die Forderung nach Reinheit und Gleichmäßigkeit der chemischen und physikalischen Eigenschaften. Die sorgfältige Auswahl der Einsatzstoffe und das exakte Einhalten der Zusammensetzung sind letztlich maßgebend für die äußere und innere Beschaffenheit der Gussstücke. Sie beeinflussen nicht nur die Art des Erstarrens, sondern führen
über die gezielte Ausbildung des Grundgefüges zu reproduzierbaren Werkstoffund Werkstückeigenschaften. Beim Herstellen im Gusszustand muss die chemische Zusammensetzung - unter Berücksichtigung der Abkühlgeschwindigkeit in der Gießform beziehungsweise der Wanddicken des Gussstücks - so eingestellt werden, dass je nach Erfordernis ein ferritisches, ein rein perlitisches oder ein perlitisch/ferritisches Gefüge entsteht. Bei den verschiedenen Werkstoffsorten, die über eine ärmebehandlung eingestellt werden können, wird üblicherweise von einer Einheitszusammensetzung ausgegangen. Es können größere Analysenstreubreiten als beim Herstellen im Gusszustand toleriert werden, denn das Gefüge und damit die Werkstoffsorte werden ausschließlich von der Art der Wärmebehandlung bestimmt.
Schmelzen
Je nach Produktionsprogramm und den betrieblichen Gegebenheiten wird das Basiseisen für die Herstellung von Gusseisen mit Kugelgraphit überwiegend nach diesen Verfahren erschmolzen:
- Schmelzen im Induktionstiegelofen (Simplex-Verfahren): Das Aufschmelzen soll schnell erfolgen und die Temperatureinstellung richtet sich nach der gewählten Gießtemperatur unter Berücksichtigung der auftretenden Temperaturverluste für das Behandeln und Umfüllen. Eine Überhitzung bis auf die Temperatur der Entkohlungsreaktion ist weder üblich noch angeraten.
- Vorschmelzen im Heißwind-Kupolofen oder Lichtbogenofen, anschließend Umsetzen in einen Induktionstiegelofen zur Korrektur der chemischen Zusammensetzung und Temperatur (Duplex-Verfahren).
- Gegebenenfalls Umfüllen in einen Warmhalteofen.
Im Anschluss an das Erschmelzen des Basiseisens folgen drei entscheidende Schritte, die zum einen erst die kugelige Ausbildung des Graphits beim Erstarren der Schmelze ermöglichen, zum anderen auf das angestrebte Grundgefüge hinwirken:
- Entschwefeln der Schmelze;
- Behandlung mit Magnesium;
- Impfen.
Entschwefeln
Im Hinblick auf eine technisch und wirtschaftlich optimale Magnesiumbehandlung soll der Schwefelgehalt des Basiseisens (deutlich) unter 0,02 % liegen, wenn die Magnesiumzugabe mit Vorlegierungen erfolgt. Wird dagegen mit Reinmagnesium behandelt, dürfte der zwingend bekannte Schwefelgehalt eigentlich auch etwas höher liegen. Aber je größer sein Anteil im Ausgangseisen ist, desto eher verbleiben Reaktionsprodukte wie zum Beispiel MgS als Einschlüsse im Gussstück. Darum wird diese Vorgehensweise nicht empfohlen.
Zunehmend beliebt ist das Vorgehen in zwei getrennten Phasen. Zuerst wird mit Magnesium entschwefelt und danach erst behandelt, wobei zwischen diesen Vorgängen eine Speicherphase zwischengeschaltet werden kann. Die Behandlung erfolgt dann wirtschaftlich von einem niedrigen Schwefelniveau aus nach jedem beliebigen Verfahren.
Überwiegend werden zum Entschwefeln jedoch Mittel auf Grundlage von Calciumcarbid CaC2 verwendet, die derart modifiziert sind, dass CaC2 möglichst vollständig ausreagiert. Der Vorgang findet in Gefäßen außerhalb des Schmelzaggregats statt, wobei durch mechanisches Rühren das Mittel und die Schmelze stets in Kontakt bleiben, beispielsweise in sogenannten Schüttelpfannen, mit Hilfe von Balkenrührgeräten oder durch Einblasen in die Schmelze.
Bewährt hat sich auch das kontinuierliche Entschwefeln unter Zugabe des Calciumcarbids in den Siphon des Kupolofens. Gelegentlich wird auch im Induktionstiegelofen direkt entschwefelt.
Behandlung mit Magnesium
Beim Herstellen von Gusseisen mit Kugelgraphit auf automatischen Gießanlagen mit Gießstrahlimpfung ergaben Untersuchungen [49], dass eine ausreichende Kugelgraphitbildung bei Rest-Mg-Gehalten unterhalb 0,04 % erzielt wird, wenn der Schwefelgehalt sehr niedrig ist. Wenn das Magnesiumsulfid nach dem Behandeln ausreichend Zeit zum Abscheiden hat, weist die im Gießofen vorliegende Schlacke bis zu 30 % Schwefel auf, während in der Schmelze davon nur 0,001 % oder noch weniger vorliegen. Daraus ist die enorme Entschwefelungskraft des Magnesiums ersichtlich.
Gusseisen mit Kugelgraphit wird industriell heute ausschließlich unter Zuhilfenahme von Magnesium (mit oder ohne Zusatz von Cer) hergestellt. Jeder ist dabei bestrebt, mit so wenig Magnesium wie möglich auszukommen, nicht nur um Kosten zu sparen, sondern vor allem wegen der äußerst nachteiligen Einflüsse von überschüssigem Magnesium auf die Qualität der Gussteile (Bildung von Schlacken („Dross“) während des Gießens und von Eisencarbid in den zuletzt erstarrenden Stückbereichen). Wie viel Magnesium nun wirklich benötigt wird, hängt in erster Linie vom Ausgangsgehalt des Eisens an Schwefel ab, weil der Vorgang des Abbindens von Schwefel nicht schon kurz nach dem Zusatz von Magnesium abgeschlossen ist, sondern sich unter Einschlussbildung bis zu den letzten Phasen der Erstarrung des Eisens hin fortsetzt [49]. Zum Erhalten von 100 % Kugelgraphit wird in jedem Fall ein Magnesiumgehalt gefordert, der den Wert 3 . % S überschreitet, zum Beispiel um 0,025 %. Daraus ergibt sich bei 0,001 % S ein Gehalt von 0,028 % Rest-Magnesium. Darin ist der Magnesiumbedarf für die Desoxidation (üblicherweise Abbau von rund 30 ppm Sauerstoff) mit 0,0045 % Mg bereits berücksichtigt. Will man mit weniger als 0,02 % Rest-Mg auskommen, muss der Ausgangsgehalt an Schwefel unter 0,001 % liegen und die Desoxidation muss separat mit Aluminium und/ oder Cer erfolgen. Dies ist jedoch im praktischen Betrieb kaum zu realisieren.
Wegen seiner geringen Dichte und seines niedrigen Siedepunktes ist das Einbringen von Reinmagnesium in flüssiges Gusseisen nicht ohne besondere Vorkehrungen durchzuführen. Das Problem des betriebssicheren Einbringens wurde daher zunächst durch Legieren des Magnesiums mit anderen Metallen gelöst (zum Beispiel Nickel oder Kupfer oder Ferrosilicium). Das Überführen des Magnesiums in metallische Verbindungen hat gleichzeitig seine Verdünnung zur Folge, wodurch der Dampfdruck beträchtlich erniedrigt wird. Demzufolge haben diese Legierungen (auch Vorlegierungen genannt) einen um so kleineren Dampfdruck, je geringer ihr Magnesiumgehalt ist. Diese Erfahrung hat 1949 bereits C. K. Donoho [3] gemacht, dessen erste Versuche mit einer 90%igen Magnesiumlegierung (Flugzeugschrott) angesichts der gleißenden Lichtentwicklung und des Metallauswurfs aus der vermutlich offenen Pfanne ziemlich dramatisch verlaufen sein mussten. Danach wurden Ni-Mg- und Cu-Mg-Vorlegierungen mit Magnesium gehalten bis hinunter auf 18 % Mg mit einem von 0 bis auf 20 % gestiegenen Ausbringen entwickelt [50].
Vorlegierungen mit 3 bis 15 % Magnesium werden vorwiegend nach dem Übergießverfahren oder nach dem „Sandwich“-Verfahren in die Schmelze eingebracht. Sie werden am Boden beziehungsweise in einer seitlichen Vertiefung der Pfanne angeordnet und mit Blechabfällen, Gusseisenspänen oder Ferrosilicium abgedeckt, um die starke Reaktion mit dem ersten in die Pfanne einlaufenden Eisen abzumildern. Vorlegierungen mit höheren Magnesiumgehalten (bis 35 %) sowie mit Magnesium getränkter Koks beziehungsweise Eisenschwamm werden mit Tauchglocken in die bereits gefüllte Behandlungspfanne eingebracht. Behandlungsmittel mit hoher Dichte, zum Beispiel Ni-Mg, werden entweder auf die Badoberfläche aufgeworfen, auf dem Pfannenboden überschüttet oder auch getaucht. Weil Nickel als karzinogen gilt, kommen diese Legierungen großtechnisch allerdings nicht mehr zur Anwendung.
Steigender Beliebtheit erfreut sich nach überwundenen Hardwareproblemen das Draht-Einspulverfahren. Der Draht wird mit einer FeSiMg-Vorlegierung (etwa 12 % Mg und 4 % Cer-Mischmetall) gefüllt und meterweise in eine Behandlungspfanne oder auch in einen Gießofen zur eventuell erforderlichen Auffrischung eingespult. In dieser Flexibilität liegt letztlich auch der Vorteil der Methode.
Beim so genannten Inmold-Verfahren für die Serienfertigung wird eine Vorlegierung mit niedrigem Magnesiumgehalt in eine in der Gießform angeordnete Reaktionskammer eingebracht. Das gesamte in die Form einlaufende Eisen, das besonders gut entschwefelt sein muss, kommt mit der Vorlegierung zur Reaktion. Kammergröße, Gießgeschwindigkeit und Auflösungsverhalten der Vorlegierung sollten sorgfältig aufeinander abgestimmt sein.
Reinmagnesium muss unter Zwang in geschlossenen Behandlungsgefäßen in die Schmelze eingebracht werden. Hier hat sich vor allem das Konverterverfahren durchgesetzt. Der „Urkonverter“ stand, wie könnte es anders sein, im Aachener Gießereiinstitut. Stellvertretend für die Vielzahl der Behandlungsmethoden sind in den Bildern 56 und 57 das Konverterverfahren und das Drahteinspulverfahren gezeigt.
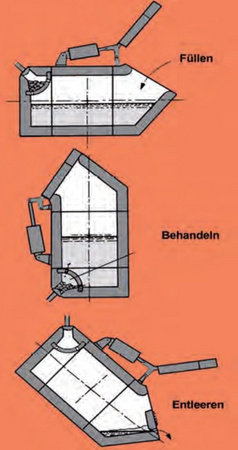
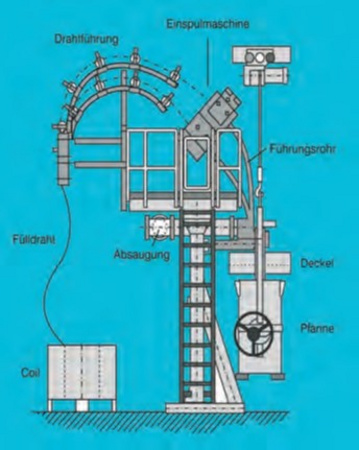
Impfen
Nach der Behandlung mit Magnesium und möglichst unmittelbar vor dem Gießen der Schmelze in die Gießform muss (ausgenommen beim Inmold-Verfahren) die Kristallisation des Graphits durch Einbringen von Keimen angeregt werden. Dieser Vorgang wird „Impfen“ genannt. Hochwissenschaftlich spricht man auch von der „heterogenen Keimbildungskatalyse“. Es handelt sich um die Zugabe von meist feinkörnigen Impfmitteln auf Ferrosilicium-Basis. Diese werden entweder in die Gießpfanne eingemischt oder in den Gießstrahl eingebracht. Häufig wird als zusätzliches oder auch als alleiniges Verfahren ein Impfen in der Form durchgeführt, bei der Ferrosilicium-Formlinge ähnlich wie beim Inmold-Verfahren in die Form eingelegt werden.
Durch das Impfen wird in der Schmelze ein günstiger Keimzustand eingestellt. Dieser bewirkt eine gezielte Graphitausscheidung (Anzahl und Größe der Sphärolithen) und schließlich das Einstellen des gewünschten Grundgefüges. Gute Impfmittel bleiben in der Schmelze lange wirksam und sind auf die Erstarrungszeit des jeweiligen Gussstücks abgestimmt. Zur Förderung der Keimbildung enthalten sie dosierte Zusätze von Calcium, Aluminium, Barium, Zirkonium, Strontium, Seltenerdmetalle Erden und anderen Elementen, die entweder einzeln oder kombiniert der Schmelze zugesetzt werden. Die Zugabemenge des Impfmittels richtet sich nach dessen Wirksamkeit und liegt im Bereich von 0,1 bis 0,5-Masse-%.
Seit Beginn des neuen Jahrtausends gilt es als erwiesen, dass die Kristallkeime für Kugelgraphit aus zwei Komponenten bestehen [51]. Grundkeim ist ein Reaktionsprodukt von Magnesium mit Sauerstoff und Silicium, ein Silicat namens Enstantit. Dieser verfügt über ein Kristallgitter, das mit demjenigen des Graphits recht wenig Ähnlichkeit besitzt und von ihm als äußerst unattraktiv empfunden wird. Der Trick besteht nun darin, dass auf diese Enstantit-Teilchen Verbindungen der Elemente Aluminium, Strontiuim, Barium usw. kondensieren, die über die gewünschte Attraktivität allerdings verfügen. Ende 2005 wurde an der RWTH oder FH Aachen wohl erstmalig ein Enstantit-Teilchen im Zentrum einer Graphitkugel nachgewiesen und Mitte 2006 wurde am IfG, Düsseldorf, im Auftrag eines Kunden nach dem gleichen Prinzip eine Methode entwickelt, wonach auch keimwirksame Graphitschichten auf solchen Teilchen „transportiert“ werden [52].
Überwachungsmethoden
Die Herstellung von Gusseisen mit Kugelgraphit wird im Verlauf des gesamten Prozesses überwacht (Bild 58).
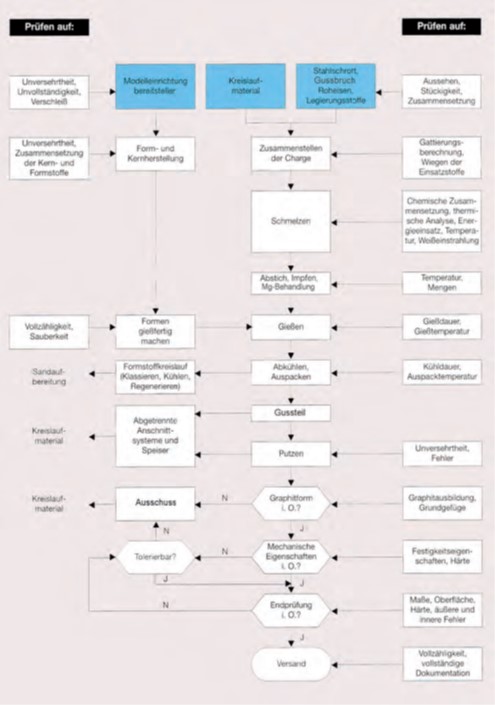
Dies betrifft sowohl die chemische Zusammensetzung als auch Gefügeausbildung und die mechanischen Eigenschaften. Folgende In-Process-Prüfungen kommen dabei zur Anwendung:
- Für die Überwachung der chemischen Zusammensetzung kommt die spektrometrische Bestimmung der Begleit-, Legierungs- und Spurenelemente im Basiseisen vor der Behandlung zum Einsatz. In kleineren Gießereien ist der Spektrometer in der Regel in unmittelbarer Umgebung des Schmelzbetriebs angeordnet. Ist dies nicht der Fall, werden vor Ort zumindest die Gehalte an Kohlenstoff und Silicium thermoanalytisch bestimmt. Hierbei werden Erstarrungskurven auf Merkmale untersucht, die mit den Gehalten beider Elemente korrelieren. Dieser etwa 5 Minuten dauernde Vorgang soll demnächst auf Grundlage von Untersuchungen des IfG auf 60 s verkürzt werden. Größere Gießereien, die sich bisher meist eines Zentrallabors bedienten, gehen zunehmend zur Installierung von Analysenautomaten vor Ort über.
- Für die Bestimmung des Gefüges werden unmittelbar nach der Behandlung mit Magnesium aus jeder behandelten Pfanne besondere Proben entnommen,
die es je nach Größe und Form gestatten, innerhalb von 120 Sekunden (das heißt in der Regel noch vor dem Gießen!) einen metallographischen Schliff zur Überprüfung der Graphitform nach ISO 945 anzufertigen. Für spätere Untersuchungen (Gefüge, mechanische Eigenschaften) werden entweder angegossene Probestücke oder getrennt gegossene, der Wanddicke des Gussteils angepasste Normproben verwendet. - Während der Schwefelgehalt analytisch leicht und schnell ermittelt werden kann, ist die Sauerstoffbestimmung recht aufwändig. Mit Hilfe von sogenannten EMK-Messsonden ist es möglich, die temperaturabhängige thermodynamische Aktivität des Sauerstoffs zu messen. Sinnvollerweise wird diese Messung thermoanalytisch unterstützt [53]. Eine quantitative Bestimmung ist mit Hilfe der Oxidspektrumanalyse zwar möglich, aber zu zeitaufwändig, um bei der Prozessregelung hilfreich zu sein. Inzwischen ist es allerdings gelungen, den aktiven, das heißt an der Keimbildung beteiligten Sauerstoff innerhalb einer
sehr kurzen Zeit auch thermoanalytisch zu bestimmen [54]. Die Analyse einer Erstarrungs- und einer dazugehörigen Längenänderungskurve gestattet auch eine sichere Bewertung der Erstarrungsmorphologie und der Lunkerneigung beziehungsweise der zeitlichen Entwicklung des Volumendefizits [55].
Dies wird eindrucksvoll im Bild 59 gezeigt.
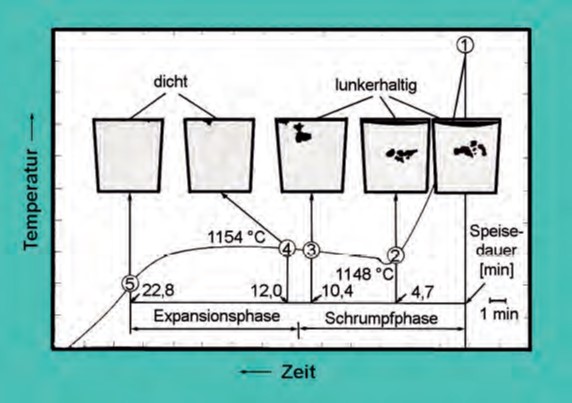
Es leuchtet ein, dass eine kombinierte Prüfung die Sicherheit einer Vorhersage enorm steigert. Ist dies aus betrieblichen Gründen nicht möglich, bedient man sich einer aufwändig analysierten Erstarrungskurve. Entsprechende kommerzielle Produkte für diese Aufgaben sind auf dem Markt erhältlich. Im Bild 60 sind hierzu Beispiele für „gutes“ und „schlechtes“ GJS zu sehen.
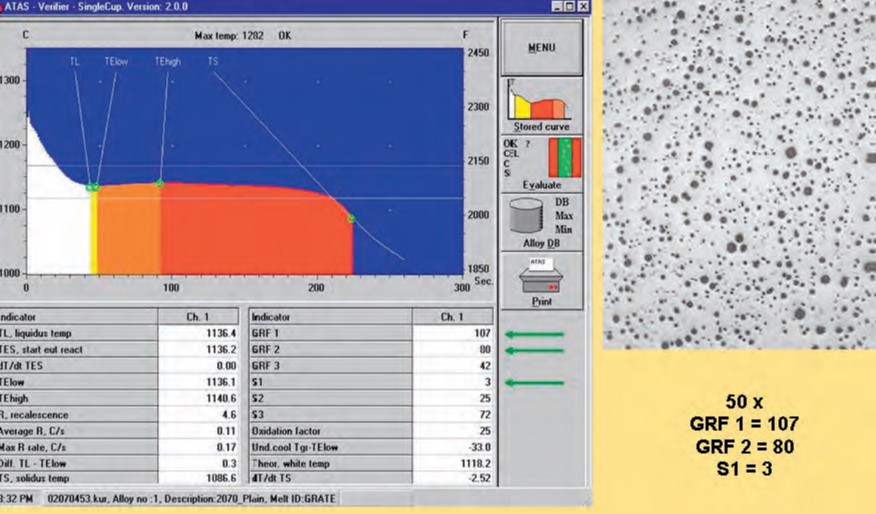
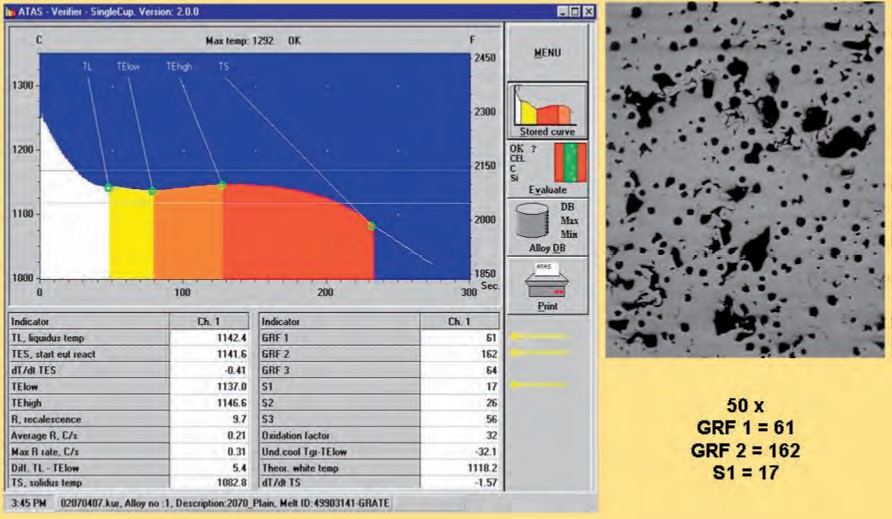
Weiterführende Informationen zum Werkstoff Gusseisen mit Kugelgraphit
- Hier geht es zu den allgemeinen Informationen: Gusseisen mit Kugelgraphit | GUSS
- Hier finden Sie Informationen zur Wärme- und Oberflächenbehandlung: Wärme- und Oberflächenbehandlung | GUSS
- Hier finden Sie Informationen zur Werkstoffprüfung: Werkstoffprüfung | GUSS
- Hier finden Sie Informatioen zu den mechanischen und physikalischen Eigenschafte: Mechanische und physikalische Eigenschaften | GUSS
- Hier finden Sie Informationen zur Spanenden Bearbeitung: Spanende Bearbeitung | GUSS
- Hier finden Sie Informationen zu besonderen Eigenschaften: Besondere Eigenschaften | GUSS
Download
Autoren und Quellen
Autoren:
Dr. Ch. Bartels, DI R. Gerhards, Prof. H. Hanselka, Prof. K. Herfurth, Dr. H. Kaufmann, DI W. Kleinkröger, Dr. M. Lampic, Dr. H. Löblich, Dr. W. Menk, Prof. G. Pusch, Dr. T. Schmidt, DI K.-H. Schütt, DI P. Tölke, Prof. E. P. Warnke