Gusseisen mit Kugelgraphit
Technische Richtlinien
Inhalt dieser Seite
Allgemeine Informationen
Gusseisen mit Kugelgraphit wird erst seit fast 60 Jahren industriell gefertigt, zuerst in den USA, Kanada und Großbritannien. Das Gusseisen mit Kugelgraphit ist zufällig entdeckt worden. 1937/1938 berichtete C. Adey (RWTH Aachen) über die sphärolithische (kugelige) Form der Graphitkristalle im Gusseisen. Adey befasste sich bewusst mit der Suche nach einer zweckmäßigen Ausbildungsform des Graphits in Kolbenringen und meldete das Verfahren zum Patent an [1]: „Verfahren zur Herstellung von Grauguss höherer Festigkeit dadurch gekennzeichnet, dass ein eutektisches oder übereutektisches schlackeneinschlussfrei gemachtes Eisen mit einem Mindestgehalt von 1 % Silicium so rasch zum Erstarren gebracht wird, dass der Graphit ganz oder zum Teil in sphärolithischer Form in der metallischen Grundmasse ausgeschieden ist.“
H. Morrogh und W. J. Wiliams vom Britischen Gießereiinstitut, BCIRA in Birmingham erzeugten Kugelgraphit im Gusseisen durch Cer-Zusatz zur Schmelze im Jahre 1947. Im gleichen Jahr wurden aus den USA auch Arbeiten und Patentanmeldungen von K. D. Millis, A. P. Gagnebin und N. Pilling bekannt, die die Herstellung von Gusseisen mit Kugelgraphit durch Magnesiumzusatz in Form von magnesiumhaltigem Nickel zur Schmelze zum Gegenstand hatten [2]. Ein Durchbruch gelang C. K. Donoho [3] bei ACIPCO (American Cast Iron Pipe Company), der 1949 durch Versuche mit Magnesium überraschend gute Erfolge erzielte.
Erst nach Ende des Zweiten Weltkrieges wurde das der INCO erteilte Patent veröffentlicht und dann auch weltweit von ihr lizenziert. Zuständig dafür war die MONDNickel-Ltd., London, eine englische Tochtergesellschaft der INCO. Das Vermitteln der Lizenzen an Gießereien in Deutschland und in einigen anderen Ländern erfolgte über die Metallgesellschaft AG (MG) in Frankfurt am Main.
Im Bild 1 ist eine Graphitkugel mit dem typischen Sphärolithenkreuz abgebildet. Ausgehend von der Entdeckung der Graphitkugeln begann eine stürmische Entwicklung des Gusseisens mit Kugelgraphit, das mit seinen stahlähnlichen Eigenschaften zu vielen wirtschaftlich günstigen Substitutionen von Stahl führte.
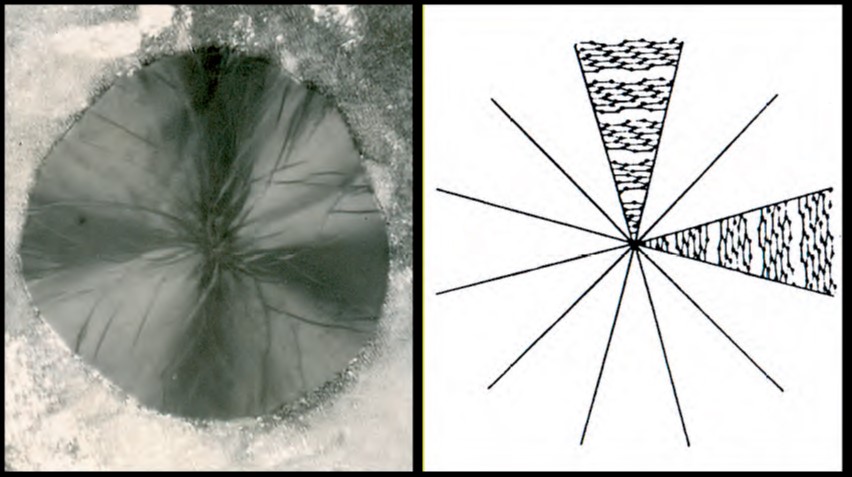
Die Sorten
Gusseisen mit Kugelgraphit (GJS) ist nach DIN EN 1563 (Normalsorten) und DIN EN 1564 (hochfeste Sorten) ein Eisen-Kohlenstoff-Gusswerkstoff, dessen als Graphit vorliegender Kohlenstoffanteil nahezu vollständig in weitgehend kugeliger Form im Gefüge vorliegt (Bild 2). Das Kurzzeichen EN-GJS (alte Bezeichnung GGG) bedeutet: Gusswerkstoff (G) aus Eisen (Iron, J) mit Kugelgraphit (speroidal graphite, S). Das oft vorgestellte EN weist auf die EU-Normbezeichnung hin.
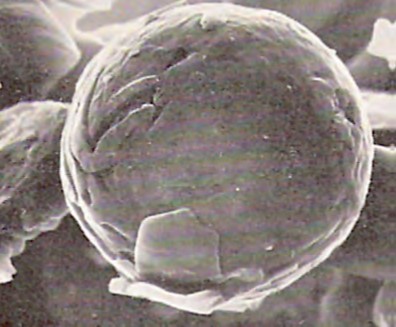
Bei den Werkstoffsorten nach DIN EN 1563 und DIN EN 1564 handelt es sich um unlegiertes oder niedriglegiertes Gusseisen mit Kugelgraphit, wobei entsprechend der Festlegungen in den genannten Normen die chemische Zusammensetzung und die Wärmebehandlung im Ermessen des Herstellers liegt. Beim austenitischen Gusseisen mit Kugelgraphit nach DIN EN 13825 handelt es sich um eine Gruppe von hochlegierten Gusseisensorten, bei denen neben den mechanischen Eigenschaften auch die chemische Zusammensetzung festgelegt ist.
In den gültigen Europäischen Normen (EN) lauten die Bezeichnungen für diese Gusseisenwerkstoffgruppe „Gusseisen mit Kugelgraphit“, „Spheroidal graphite cast iron“ und „Fonte a graphite spheroidal“. Eine Reihe weiterer Namen wie beispielsweise „Kugelgraphitguss“, „duktiles Gusseisen“, „sphärolithisches Gusseisen“, „Kugelgraphitgusseisen“ und „SPHÄROGUSS®“ bezeichnen keine Sondersorten, sondern die gleiche Werkstoffgruppe. In den USA wird Gusseisen mit Kugelgraphit „Ductile Cast Iron“, "Nodular Cast Iron“ oder „SG (Spheroidal Graphite) Cast Iron“ genannt. Die Bezeichnung „Sphäroguss“ war ein gesetzlich geschützter Handelsname in der Zeit, als Deutschland noch für die Produktion von Gusseisen mit Kugelgraphit Lizenzgebühren bezahlen musste.
In der Norm DIN EN 545 für die Produktgruppe Gussrohre, Formstücke und Zubehörteile zur Errichtung von Rohrleitungen sind die Bezeichnungen „Duktiles Gusseisen“ und „Duktile Rohre“ festgelegt. Es handelt sich dabei um mit dem Schleudergießverfahren hergestellte Rohre aus einem ferritischen Gusseisen mit Kugelgraphit (Bild 3). Die Bezeichnung „Duktiles Gusseisen“ (Bild 4) wird in der Industriestatistik des Deutschen Gießereiverbandes (DGV) auch als Oberbegriff für Summe der Produktion von Gusseisen mit Kugelgraphit und Temperguss verwendet.
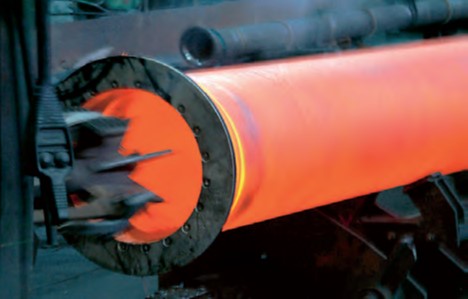
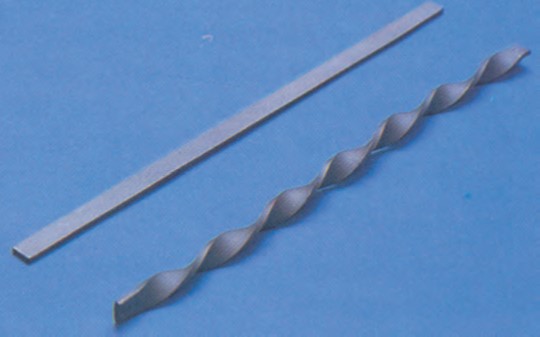
Seit einiger Zeit rückt eine Gusseisen-Werkstoffgruppe mit der weit verbreiteten Bezeichnung ADI immer stärker in den Vordergrund. Die Abkürzung ADI wurde aus dem Englischen übernommen und bedeutet „Austempered Ductile Iron“. Durch eine spezielle Wärmebehandlung entsteht bei diesen Sorten des Gusseisens mit Kugelgraphit ein Grundgefüge aus lattenförmigem Ferrit und Restaustenit. Die mechanischen Eigenschaften dieser Werkstoffe zeichnen sich durch sehr hohe Festigkeiten bei gleichzeitig hoher Plastizität und Zähigkeit aus (siehe Kapitel 8).
Während der Entwicklung dieser Werkstoffgruppe des hochfesten Gusseisens mit Kugelgraphit traten für sie mehrere verschiedene Bezeichnungen auf wie „Bainitisch-austenitisches Gusseisen mit Kugelgraphit“, „bainitisches Gusseisen mit Kugelgraphit“, „zwischenstufenvergütetes Gusseisen mit Kugelgraphit“ und „Austempered Ductile Iron (ADI)“. Da erst seit wenigen Jahren Klarheit über die Gefügebildung bei dieser Gruppe des Gusseisens mit Kugelgraphit besteht, scheint sich gegenwärtig folgende Bezeichnung durchzusetzen „Austenitisch-ferritisches Gusseisen mit Kugelgraphit“ („Ausferritic spheroidal graphit cast iron“, Fonte ausferritique a graphite spheroidal“) [2]. Trotz dieser unterschiedlichen Bezeichnungen handelt es sich immer um hochfestes Gusseisen mit Kugelgraphit mit den gleichen mechanischen und physikalischen Eigenschaften (Bild 5).
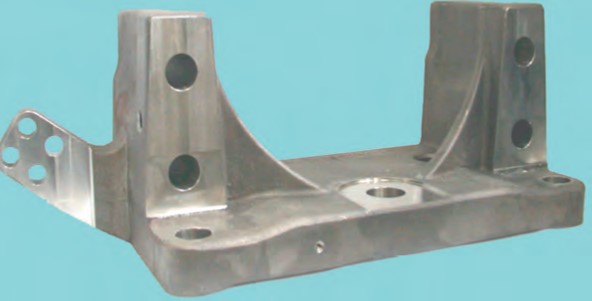
Charakteristisch für austenitisches Gusseisen mit Kugelgraphit ist sein auch bei Raumtemperatur und tiefen Temperaturen stabiles austenitisches Grundgefüge (Bild 6). Viele Sorten des austenitischen Gusseisens werden auch als „Ni-Resist“ bezeichnet. Diese Werkstoffe haben Nickelgehalte von 12 bis zu 36 % und zeichnen sich durch eine ganze Reihe außergewöhnlicher Eigenschaften aus.
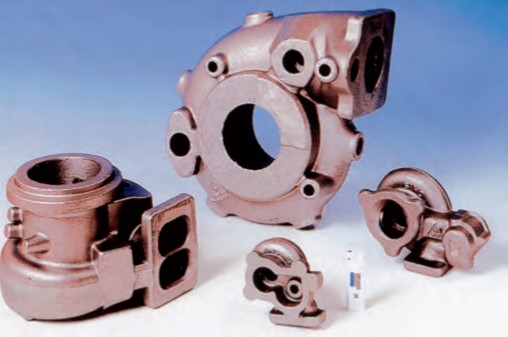
Zu den Entwicklungen der jüngeren Vergangenheit gehören auch die SiMo-Werkstoffe des Gusseisens mit Kugelgraphit für den Einsatz bei hohen Temperaturen (Bild 6). Ein erhöhter Zusatz von Silicium verstärkt die Zunderbeständigkeit und verringert die Schädigung des Werkstoffs durch innere Oxidation. Molybdän erhöht als Legierungselement die Warmfestigkeit.
Bei experimentellen Untersuchungen zur Herstellung von Gusseisen mit Kugelgraphit wurden Abweichungen von der Graphitkugelform beobachtet, die als wurmförmiger Graphit, Vermiculargraphit (Wurm
– vermis, lat.) bezeichnet wurden. Später entstand daraus eine selbstständige Werkstoffgruppe – das Gusseisen mit Vermiculargraphit mit bis zu 10 % Kugelgraphit, jedoch ohne Lamellengraphit.
Durch die Entdeckung der Graphitkugeln im Gusseisen und den nachfolgenden Forschungs- und Entwicklungsarbeiten umfasst die Familie des Gusseisens heute folgende Werkstoffgruppen:
- Gusseisen mit Lamellengraphit [5];
- Gusseisen mit Vermiculargraphit [6];
- Gusseisen mit Kugelgraphit (Normalsorten);
- austenitisch-ferritisches Gusseisen (hochfestes Gusseisen), international als ADI bekannt [7];
- SiMo-Werkstoffe [8];
- Austenitisches Gusseisen, darunter auch austentisches Gusseisen mit Kugelgraphit [9, 10];
- Verschleißbeständiges Gusseisen [11].
Die Geschichte
Bereits in den dreißiger Jahren des 20. Jahrhunderts wurden von verschiedenen Forschern die günstigen Eigenschaften eines Gusseisens mit möglichst kugeliger Graphitausbildung vorausgesagt. Weltweit gelang es 1937 erstmalig am Gießerei-Institut der RWTH Aachen, gezielt Gusseisen mit Graphitkugeln herzustellen. Beim Schmelzen in hochbasischen Schmelztiegeln unter hochbasischer Schlacke wurde auf der Suche nach einem hochwertigen Gusseisen mit Lamellengraphit solches mit Kugelgraphit entdeckt. Nahezu gleichzeitig wurde im British Cast Iron Research Institute die Wirksamkeit von Cer, das der Gusseisenschmelze zugesetzt wurde, für die Kugelgraphitbildung im Gusseisen gefunden.
Jedoch erst die Zufallsentdeckung in den Laboratorien der International Nickel Inc. in den USA, dass durch die Zugabe einer Ni-Mg-Legierung zur Gusseisenschmelze bei der Erstarrung Kugelgraphit entsteht, legte den Grundstein für die industrielle Produktion von Gussteilen aus Gusseisen mit Kugelgraphit. Es folgte die Pionierzeit der Werkstoffentwicklung mit Untersuchungen der Werkstoffeigenschaften, einer stetigen Verbesserung der Herstellungstechnologie und der Suche nach immer neuen Anwendungsgebieten unter Beteiligung vieler Forschungsinstitute, Gießereien und Gussanwender.
Mitte der fünfziger Jahre des 20. Jahrhunderts wurden in Deutschland die Fe-Si-Mg-Vorlegierungen für die Schmelzebehandlung entwickelt, die anstelle der vergleichsweise teuren Ni-Mg-Vorlegierungen eine wirtschaftlichere Behandlung der Gusseisenschmelze ermöglichten. In dieser Zeit begann auch die Entwicklung der duktilen Schleudergussrohre aus ferritischem Gusseisen mit Kugelgraphit, die nach umfangreichen Untersuchungen von den Technischen Überwachungsvereinen (TÜV) für den Gas- und Wasserleitungsbau freigegeben wurden. Unbemerkt von der Öffentlichkeit versorgen inzwischen viele Tausende von Kilometern duktiler Schleudergussrohre Haushalte und Betriebe in Städten und Gemeinden mit Gas und Wasser oder sorgen für die Abwasserableitung. Im Vergleich zu Rohren aus Gusseisen mit Lamellengraphit konnten mit den duktilen Rohren Gewichtseinsparungen bis zu 40 % realisiert werden.
Anfang der siebziger Jahre des 20. Jahrhunderts wurden der Maschinenbau (Bild 7) und der Fahrzeugbau Abnehmer von Gussteilen aus Gusseisen mit Kugelgraphit, wobei häufig Gusseisen mit Lamellengraphit (veraltete Bezeichnung „Grauguss“), Temperguss und Stahlguss durch Gusseisen mit Kugelgraphit substituiert wurde. Im Fahrzeugbau wurden beispielsweisedieKurbelwellen für PKW und Kleintransporter, die traditionell aus Schmiedestahl bestanden, sehr weitgehend auf Gusseisen mit Kugelgraphit umgestellt (Bild 8).
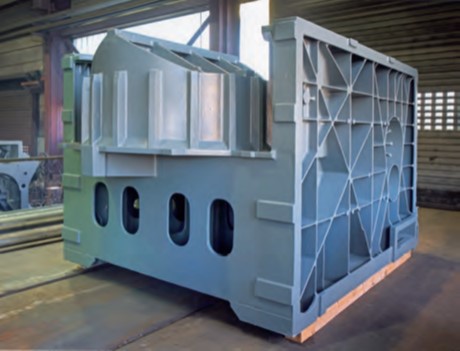
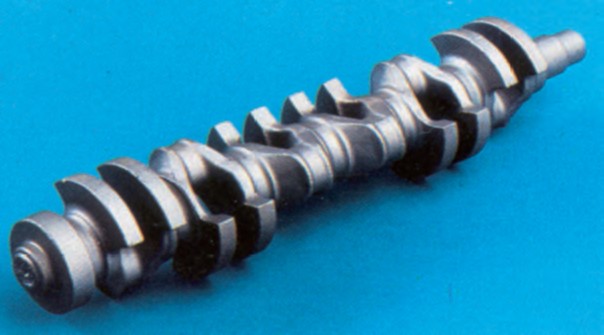
1967 lief das Hauptpatent für die Herstellung von Gusseisen mit Kugelgraphit ab, und der Lizenzgeber stellte die Benutzung auch der Folgepatente frei. Damit gehört die Bezeichnung „SPHÄROGUSS®“ der Vergangenheit an. Diese Bezeichnung war zur Zeit der Lizenznahme durch Deutschland der eingetragene patentgeschützte Handelsname, wird aber vielfach heute noch verwendet.
Der Unterschied – die Graphitformen
Der Begriff „Gusseisen“ war lange einerseits ein Synonym für Beständigkeit (ehern, eisern), andererseits aber mit der „Sprödigkeit“ des Werkstoffs verbunden. Spröde ist natürlich nur das Gusseisen mit Lamellengraphit. Diese Aussage trifft auf das Gusseisen mit Kugelgraphit nicht zu, was mit dem Begriff „Duktiles Gusseisen“ verdeutlicht werden soll. Grauerstarrende Gusseisen-Werkstoffe sind genauer betrachtet Eisen-Kohlenstoff-Silicium-Werkstoffe, die aus einem metallischen Grundgefüge mit eingelagerten Graphitkristallen bestehen. Das Grundgefüge entspricht einem eutektoiden Stahl mit höherem Siliciumgehalt.
Grauerstarrende Gusseisen-Werkstoffe haben also schon immer ein Grundgefüge wie Stahl. Mit den Graphitlamellen wird dieses Grundgefüge stark unterbrochen, und an den Rändern dieser Graphitlamellen bilden sich bei Beanspruchung durch äußere Kräfte Spannungsspitzen aus (Bild 9). Die Graphitlamellen haben eine innere Kerbwirkung. Das sind die Ursachen für die relativ geringe Festigkeit und das spröde Verhalten von Gusseisen mit Lamellengraphit.
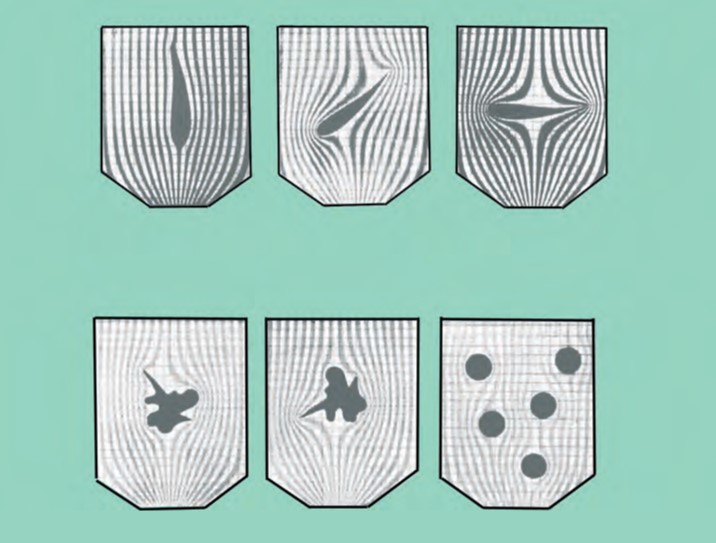
Seit einiger Zeit gibt es nun in den industriell genutzten Gusseisen-Werkstoffen drei verschiedene Graphitformen – Lamellengraphit, Vermiculargraphit und Kugelgraphit, die im Bild 10 mit Schliffbildern – also bei zweidimensionaler Betrachtung – gezeigt sind. Bild 11 vermittelt einen Eindruck über die räumliche Ausbildung der genannten Graphitkristalle.
Durch die Entwicklung des Gusseisens mit Kugelgraphit kommen die schon immer vorhandenen stahlähnlichen mechanischen Eigenschaften wieder voll zum Tragen. Mit den Graphitkugeln wird die metallische Grundmasse viel weniger unterbrochen, und die innere Kerbwirkung gibt es nicht mehr. Die Festigkeitswerte springen nach oben, und das Gusseisen erreicht hohe Duktilität (Bild 12).
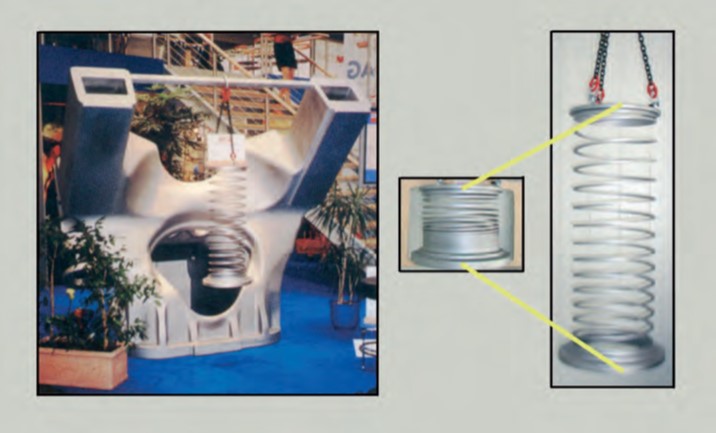
Vorschnell wäre jedoch die „logische Folgerung“, ganz ohne Graphit ginge es noch besser. Weit gefehlt! Die Graphitkristalle im Gusseisen haben einen günstigen Einfluss auf die Gießbarkeit, die Erstarrung, die Gefügedichtheit, die Zerspanbarkeit, das Notlaufverhalten und die Schwingungsdämpfungsfähigkeit, um nur einige Stichworte zu nennen. Für das Schmelzen von Gusseisen wird weniger Energie verbraucht als beim Schmelzen von Stahl.
Vorteile des Gusseisens mit Kugelgraphit
Seit mehr als 60 Jahren wird Gusseisen mit Kugelgraphit nun schon mit wirtschaftlichen Vorteilen anstelle von Stahl (Stahlguss, Schmiedestahl, Walzstahl) eingesetzt, und dieser Trend setzt sich weiter fort. Das Streckgrenzen/Zugfestigkeits-Verhältnis ist bei Gusseisen mit Kugelgraphit günstiger als bei den Stählen. Dieses Verhältnis liegt für die Stähle bei 0,44 bis 0,53, bei Gusseisen mit Kugelgraphit dagegen bei 0,6 bis 0,7.
Bei den Stählen ist bei vergleichbar hoher Festigkeit die Bruchdehnung höher als beim Gusseisen mit Kugelgraphit. Das ist jedoch, wie sich in vielen Fällen gezeigt hat, kein Nachteil. In diesem Zusammenhang sei auf ein Beispiel aus der Vergangenheit, auf die PKW-Kurbelwellen hingewiesen. In den sechziger Jahren begann die Umstellung dieser Kurbelwellen von Schmiedestahl auf Gusseisen mit Kugelgraphit. Bei gleicher Zugfestigkeit und gleicher Streckgrenze (Dehngrenze) von Kugelgraphit war die Bruchdehnung der verwendeten Gusseisensorte um eine Größenordnung kleiner als die der Stahlsorte (3 statt 20 %) Heute fahren über 90 % aller PKW und Kleintransporter mit Kurbelwellen aus Gusseisen mit Kugelgraphit, die völlig ausreichende Dauerfestigkeiten für Biegung und Torsion aufweisen.
Die Bruchdehnung beschreibt in erster Näherung das Umformverhalten (zum Beispiel die Schmiedbarkeit) eines Werkstoffs und ist deshalb eher eine Verarbeitungs- als eine Gebrauchseigenschaft. Da Gussteile direkt nach dem Erstarren und Abkühlen endabmessungsnah entstehen, ist kein Umformprozess notwendig. Ungefähr 90 % der Bruchschäden an Maschinenelementen sind Dauerbrüche infolge einer Werkstoffermüdung. Der Restbruch bei Dauerbrüchen ist immer ein Sprödbruch, auch bei Stählen mit sehr hohen Bruchdehnungen.
Die Wiederverwendung (das Recycling) von Gusseisen mit Kugelgraphit ist wie bei Stahl fast vollständig. Abgesehen von Materialverlusten durch Verschleiß und Korrosion werden alle Schrotte (Kreislaufmaterial, Späne, ausgediente Bauteile) wieder eingeschmolzen. Dabei gibt es kein „Down-Cycling“, das heißt keinen Verlust an den guten Werkstoffeigenschaften. Es ist sogar ein „Up-Cycling“ jederzeit möglich, das heißt, aus Schrott mit einer geringen Festigkeit kann in der Gießerei auch ein Gusseisen mit Kugelgraphit höherer Festigkeit hergestellt werden.
Einfluss der metallischen Grundmasse
Die Art des metallischen Grundgefüges ist bei Gusseisen mit Kugelgraphit durch Wahl der chemischen Grundzusammensetzung, Legieren und/oder Wärmebehandeln in weiten Grenzen variierbar. Die Grundsorten mit einem ferritischen Grundgefüge haben die geringste Festigkeit und die höchste Plastizität und Zähigkeit und die mit einem perlitischen Grundgefüge die höchste Festigkeit und geringere Plastizität und Zähigkeit (Bild 13). Sorten mit einem Mischgrundgefüge (mit unterschiedlichen Ferrit-Perlit-Verhältnissen) liegen zwischen den genannten Grenzen. In Richtung sehr hoher Festigkeiten bei gleichzeitig günstiger Plastizität
und Zähigkeit haben sie ein austenitischferritisches Grundgefüge. So umfasst zum Beispiel die Zugfestigkeit der seit langem bekannten Normalsorten einen Bereich von 350 bis 900 N/mm2 und der neu entwickelten hochfesten Sorten von 800 bis 1600 N/mm2. Die mit Nickel hoch legierten Sorten des austenitischen Gusseisens mit Kugelgraphit haben ein bei hohen und niedrigen Temperaturen beständiges austenitisches Grundgefüge.
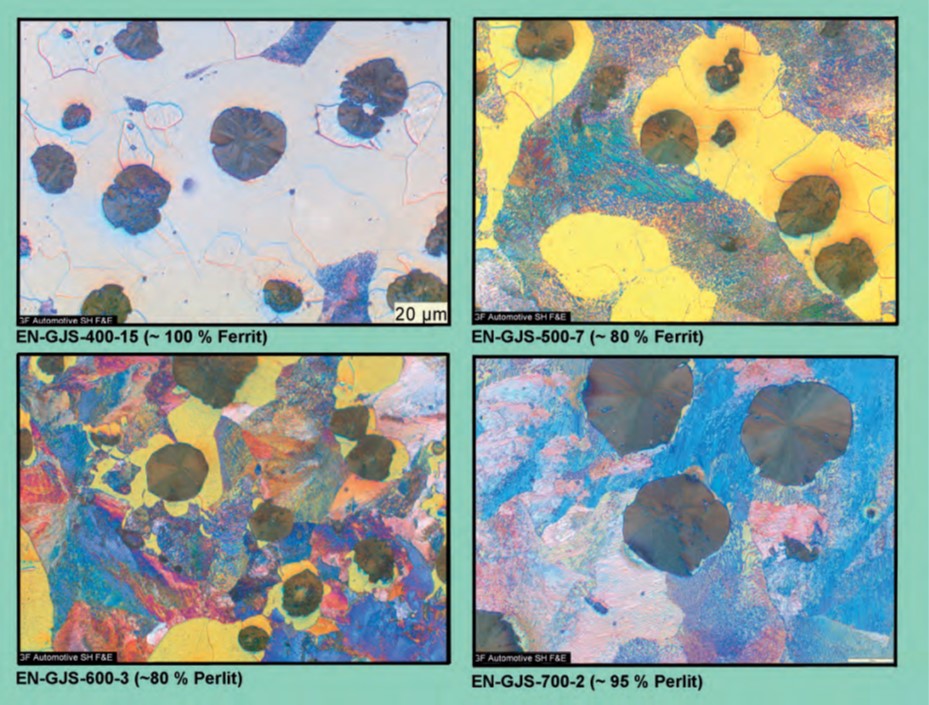
Grundlegende Betrachtungen zur Gefügebildung bei der Erstarrung und Gefügeumwandlung durch Wärmebehandlung beim Gusseisen mit Kugelgraphit werden in [12, 13] angestellt.
Weltweit betrug die Produktion von Gussteilen aus Gusseisen mit Kugelgraphit 2005 19,6 Mio. Tonnen [14]. Die Produktion von Gussteilen auf Eisenbasis erreichte im Jahr 2006 in Deutschland folgende Werte [15]: Gussteile auf Eisenbasis gesamt 4,48 Mio. t (100 %) und davon aus
- Gusseisen mit Lamellengraphit 2,60 Mio. t (58,1 %),
- Gusseisen mit Kugelgraphit 1,60 Mio. t (35,7 %),
- Temperguss 0,06 Mio. t (1,3 %),
- Stahlguss 0,22 Mio. t (4,9 %).
Die Produktionsentwicklung von Gussteilen aus Gusseisen mit Kugelgraphit in Deutschland wird im Bild 14 gezeigt. Die Gesamtproduktionsmenge seit den fünfziger Jahren, die Produktionsmengen für den Fahrzeugbau und den Maschinenbau seit den sechziger Jahren des 20. Jahrhunderts lassen bis in die Gegenwart eine ständige Zunahme erkennen. Anfangs bestand die Produktion aus einem sehr hohen Anteil von Schleudergussrohren. Dieser Marktanteil ist seit Mitte der siebziger Jahre etwa konstant geblieben. Für die Zukunft werden weltweit weiter steigende Produktionszahlen für Gusseile aus Gusseisen mit Kugelgraphit erwartet.
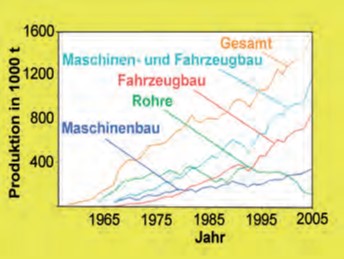
aus Gusseisen mit Kugelgraphit in Deutschland
(bis 1992 nur Westdeutschland) [15]
Die Herstellung von hochwertigen Gussteilen aus Gusseisen mit Kugelgraphit wird heute technisch sicher beherrscht. Die naturwissenschaftliche Ursache für die Entstehung der Graphitkugeln und auch der anderen Graphitformen im Gusseisen ist trotz zahlreicher Untersuchungen und Deutungen noch immer nicht ganz geklärt. Die vielfältigen Faktoren, die auf die Erstarrung und damit auf Keimbildung und Kristallwachstum Einfluss haben, erschweren noch immer eine endgültige Formulierung einer umfassenden Theorie, und es gibt auf diesem Gebiet noch immer unterschiedliche Auffassungen. An dieser Stelle sei deshalb auf spezielle Fachliteratur verwiesen [16 bis 19].
Weitere Informationen zum Werkstoff Gusseisen mit Kugelgraphit
Metallurgie
Eine Vielzahl von metallurgischen und kristallographischen Einflüssen ist an der Graphitkugelbildung beteiligt, die zu unterschiedlichen Ausbildungsformen führen. Für das Schmelzen ergibt sich daraus die Forderung nach einwandfreien Rohstoffen vorzugsweise für den Einsatz in einem Induktionstiegelofen.
Wärme- und Oberflächenbehandlung
Wärmebehandeln ist in der Fertigungstechnik nach DIN 8580 die Hauptgruppe 6 „Stoffeigenschaftsändern“. Hierzu gehört eine Gruppe von Fertigungsverfahren, die die Eigenschaften eines Werkstoffes verändern.
Werkstoffprüfung
Die Werkstoffprüfung bei Gusseisen mit Kugelgraphit unterscheidet sich nicht von der entsprechenden Prüfung bei Stahlguss, Schmiede- oder Walzstählen. Spezifisch ist die Probennahme mit angegossenen, getrennt gegossenen oder dem Gussstück entnommenen Proben.
Mechan. und physikal. Eigenschaften
Anders als bei Gusseisen mit Lamellengraphit, bei dem wegen der ausgeprägten Kerbwirkung des Graphits die mechanischen Eigenschaften durch dessen Menge, Verteilung und Form dominiert werden, hat bei Gusseisen mit Kugelgraphit die Ausbildung der metallischen Matrix entscheidenden Einfluss.
Spanende Bearbeitung
Die spanende Bearbeitung von Bauteilen ist ein maßgeblicher Kostenfaktor. Die Optimierung von Werkzeug- und Schnittdaten ist im Hinblick auf eine wirtschaftliche Fertigung von Bedeutung. Dieses beinhaltet nicht nur kurze Stückzeiten, sondern auch eine möglichst hohe Automatisierung des Produktionsablaufes mit geringer Überwachung.
Besondere Eigenschaften
Neben den Normalsorten gibt es beim Gusseisen mit Kugelgraphit noch legierte Sorten mit speziellen Eigenschaften für erweiterte Anwendungsbereiche, die hier kurz vorgestellt werden.
Download
Autoren und Quellen
Autoren:
Dr. Ch. Bartels, DI R. Gerhards, Prof. H. Hanselka, Prof. K. Herfurth, Dr. H. Kaufmann, DI W. Kleinkröger, Dr. M. Lampic, Dr. H. Löblich, Dr. W. Menk, Prof. G. Pusch, Dr. T. Schmidt, DI K.-H. Schütt, DI P. Tölke, Prof. E. P. Warnke