Druckgießen
Serienverfahren für hochkomplexe dünnwandige Leichtmetallgussteile
Nach dem Druckgießverfahren werden Gussteile aus Aluminium-, Magnesium- und Zink-Legierungen hergestellt, die in großen Stückzahlen benötigt werden. Bei diesem Gießverfahren wird die Schmelze nicht direkt in den Formhohlraum gegossen. Vielmehr wird die Schmelze zunächst in die Gießkammer einer Druckgießmaschine gefüllt und von dort mit einem Kolben über einen oder mehrere Kanäle (Anschnitte) in den Formhohlraum gepresst.
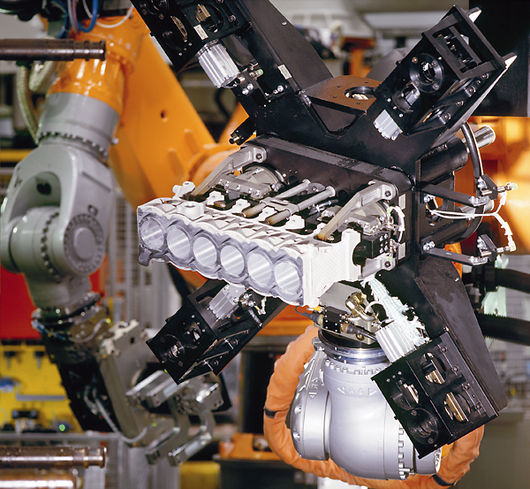
Gussteilentnahme mit Industrieroboter (Foto: BMW)
Dabei werden Drücke von 150 bis 1200 bar erzeugt, die zu Strömungsgeschwindigkeiten der Schmelze von 10 bis 150 m/s sowie zu sehr kurzen Formfüllzeiten von 50 bis 200 ms führen, was die Herstellung auch großflächiger Gussteile mit komplizierter Gestalt und geringen Wanddicken bis zu etwa 1 mm ermöglicht.
Die Druckgießformen sind wegen der hohen mechanischen Beanspruchung Dauerformen aus hochwertigen warmfesten Stahlsorten. Die Hälften der Druckgießform sind auf einer „festen" und einer „beweglichen" Maschinenplatte der Druckgießmaschine montiert. Für das Zusammenhalten der meist vertikal geteilten Druckgießform sind wegen des hohen Drucks beim Gießen Verriegelungen mit großen Zuhaltekräften erforderlich. Um eine optimale Erstarrung und Abkühlung der Gussteile zu gewährleisten, sind Druckgießformen an bestimmten Stellen gekühlt oder/und beheizt. Hohlräume in den Gussteilen werden beim Druckgießverfahren in der Regel durch metallische Kerne abgeformt, die zu einem optimalen Zeitpunkt der Gussteilbildung gezogen werden.
Beim Druckgießverfahren können zwei Verfahrensvarianten unterschieden werden: das Kaltkammer- und das Warmkammer-Druckgießverfahren. Der Verfahrensablauf beim Kaltkammer-Druckgießverfahren, das für die Herstellung von Aluminiumgussteilen eingesetzt wird, ist in Bild 1 dargestellt. Die Schmelze wird in die Gießkammer eingefüllt. Der hydraulisch bewegte Gießkolben in der Gießkammer drückt die Schmelze durch das Kanalsystem (Anschnitt) in den Hohlraum der geschlossenen Druckgießform. Nach dem Erstarren des Gussteils, was unter Druck stattfindet, wird die Druckgießform hydraulisch geöffnet. Das Gussteil mit Anschnitt wird durch automatisch betätigte Auswerferstifte ausgestoßen oder von einem Roboter entnommen und einer Abgratepresse zugeführt.
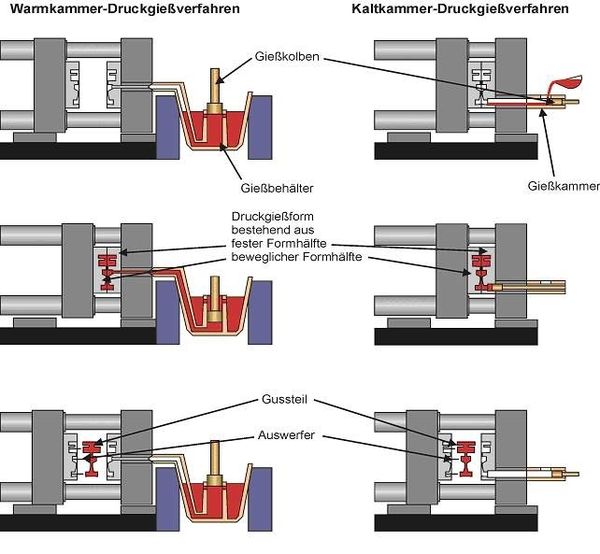
Bild 1: Prinzip des Kaltkammer- und Warmkammer-Druckgießens
Eine spezielle Verfahrensvariante ist das Vakuum-Druckgießverfahren, bei dem der Hohlraum der Druckgießform vor den Gießen evakuiert wird. Eine besondere Ausführung davon ist das Vacural-Verfahren, wo die Schmelze zudem durch Unterdruck über ein beheiztes Rohr aus dem Warmhalteofen in die Gießkammer gesaugt wird. Damit gelingt es, porenfreie und damit schweißbare Druckgussteile aus Aluminiumlegierungen herzustellen. Ein Beispiel dafür stellen die gegossenen Knoten für das Spaceframe-Konzept für Automobilkarosserien dar, die mit Aluminiumblechen verschweißt werden.
Werden Magnesiumlegierungen nach dem Kaltkammer-Druckgießverfahren verarbeitet, sind weitere Besonderheiten zu beachten. Die Schmelze im Warmhalteofen muss mit einer Schutzgasatmosphäre geschützt werden, und der geringe Wärmeinhalt der Magnesiumlegierungen verlangt einen schnellen Prozessablauf.
Charakteristisch für das Warmkammer-Druckgießverfahren ist, dass sich die Gießkammer in ständigem Kontakt mit der Schmelze befindet (Bild 1). Über ein Ventil gelangt die Schmelze in die Gießkammer, von wo sie mit Hilfe eines Kolbens mit hoher Geschwindigkeit in die geschlossene Druckgießform gepresst wird. Der weitere Verfahrensablauf erfolgt analog dem Kaltkammer-Druckgießverfahren.
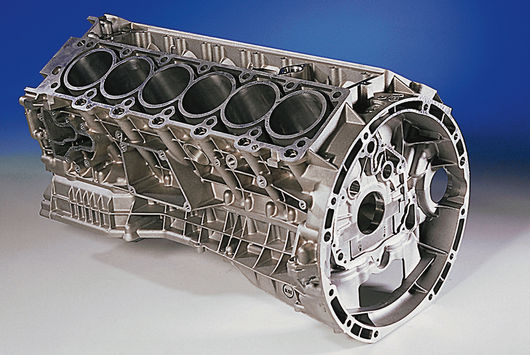
Bild 2: 12-Zylinder-Aluminium-Motorblock für den Maybach und die S-Klasse der Daimler AG (Foto: Honsel)
Das Warmkammer-Druckgießverfahren eignet sich besonders für die Herstellung von Gussteilen aus Zink-, Blei- und Zinnlegierungen. Für die Herstellung von Gussteilen aus Magnesiumlegierungen wurde das Dynacast-Verfahren entwickelt, das einen Hochgeschwindigkeits-Warmkammer-Druckgießprozess darstellt, bei dem die Druckgießmaschine die fünffache Geschwindigkeit einer traditionellen Maschine erreicht.
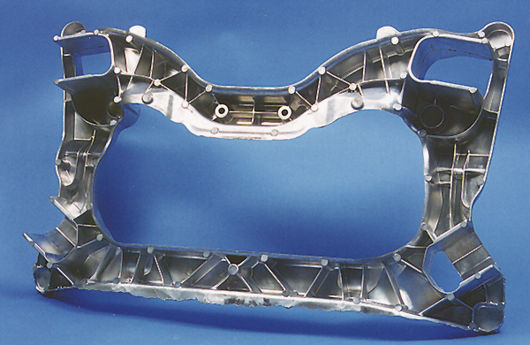
Bild 3: Integralträger für Mercedes-S-Klasse Coupe aus Aluminiumdruckguss (Foto: Daimler)
Das Druckgießverfahren wird heute einschließlich der notwendigen Peripherie in automatisierten Fertigungszellen unter Nutzung von Industrierobotern realisiert. Moderne Druckgießmaschinen werden automatisch mit Echtzeitregelung betrieben. Die mit dem Druckgießverfahren hergestellten Gussteile sind sehr maßgenau und erfordern kaum eine spangebende Nacharbeit. Damit liegt eine ausgezeichnete endkonturnahe Fertigung direkt aus der Schmelze vor. Zudem ermöglicht das Druckgießverfahren die Herstellung sehr dünnwandiger, aber komplex gestalteter Bauteile, was den Anforderungen vieler Konstruktionen nach weiteren Leichtbau ideal entspricht (Bilder 2 und 3).
Weiterführende Informationen: K. Herfurth, N. Ketscher und M. Köhler: Giessereitechnik kompakt – Werkstoffe, Verfahren, Anwendungen. Giesserei-Verlag GmbH, Düsseldorf 2003, veränderter Nachdruck 2005 (ISBN 3-87260-148-2)