Kokillengießen
NE-Metalle
Das Kokillengießen ist den Gießverfahren zugeordnet, die mit Dauerformen arbeiten (Bild 1). Mit dem Kokillengießverfahren lassen sich maßgenaue Gussteile mit guter Oberflächenbeschaffenheit herstellen. Durch die relativ schnelle Erstarrung werden im Kokillenguss gute mechanische Werkstoffkennwerte erreicht, die den Standardsandguss übertreffen.
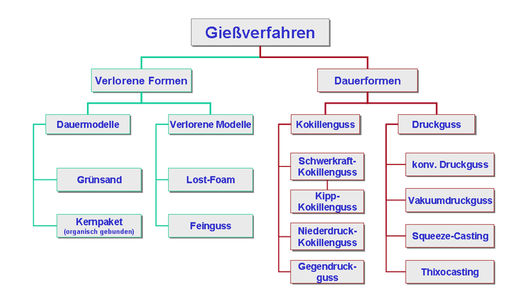
Bild 1: Einordnung der Kokillengießverfahren in die anderen Dauerformverfahren
Im Kokillenguss lassen sich breit gespannte Seriengrößen wirtschaftlich fertigen. Mit hohem Automatisierungsgrad wird das Verfahren auch für Großserien eingesetzt. Die größten Produktionsanteile haben die Gussteile für die Automobilindustrie. Typische Anwendungsbeispiele sind Zylinderköpfe, PKW-Kolben oder Räder. In Bild 2 sind Kokille, Roh- und Fertiggussteil einer Fahrwerkskomponente aus einer Aluminiumgusslegierung abgebildet. Über die Automobilbranche hinaus werden Kokillengussstücke aus NE-Metallen aber auch in vielen anderen Bereichen eingesetzt. Beispiele sind Armaturen und Beschläge im Haus- und Sanitärbereich, Gehäuse und Zahnkränze im Maschinenbau, Elektrotechnik und vielen weiteren Branchen.
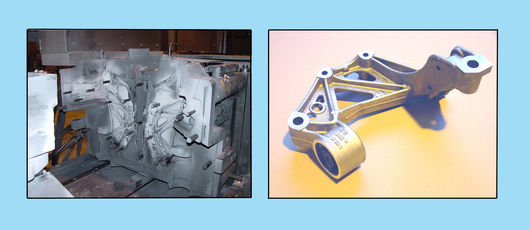
Bild 2: Im Kokillenguss gefertigte Fahrwerkskomponente aus Aluminium (Foto: KSM Casting, Hildesheim)
Die zwei- oder mehrteiligen Kokillen (= Formen) werden aus Stählen oder aus Gusseisen mit Lamellengraphit gefertigt. Für Gussteile, die in größerer Serie produziert werden sollen, werden Kokillen aus Warmarbeitsstählen verwendet. Besteht die gesamte Kokille aus Metall, so spricht man von einer Vollkokille; besteht bei einer Form das Unterteil aus einer Kokille und das Oberteil aus einer Sandform, so spricht man von einer Halbkokille. Die Kokillen werden im Betrieb zur Erhöhung der Standzeiten geschlichtet.
Durch Verwendung von Sandkernen und metallischen Dauerkernen lassen sich auch Komponenten mit komplexen Geometrien erzeugen und eine Vielfalt an Funktionen in ein Gussteil integrieren. Präzise gearbeitete Werkzeuge garantieren eine hohe Maßhaltigkeit der gefertigten Komponenten. Mit einem sicher beherrschten Gießprozess lässt sich darüber hinaus eine hohe Wiederholgenauigkeit für die Gussteile erreichen.
Nachstehend wird eine Reihe von Verfahrensvarianten erörtert. Die Auswahl des Verfahrens ist auszurichten auf die wirtschaftlichen und technischen Anforderungen (Stückzahl, Maßhaltigkeit, Oberflächengüte, mechanische Eigenschaften usw.) die an die Gusskomponente gestellt werden.
Schwerkraftkokillenguss
Bei diesem Standard-Kokillengießverfahren erfolgt die Formfüllung mittels Schwerkraft und in der Regel im steigenden Guss, d. h., die Schmelze wird durch einen Einguss gefüllt, fließt dann über einen Lauf, der unterhalb und ggf. seitlich des eigentlichen Gussteils angeordnet ist, und über den (die) Anschnitt(e) in den Formhohlraum. Damit wird die Form von unten nach oben steigend gefüllt (Bild 3).
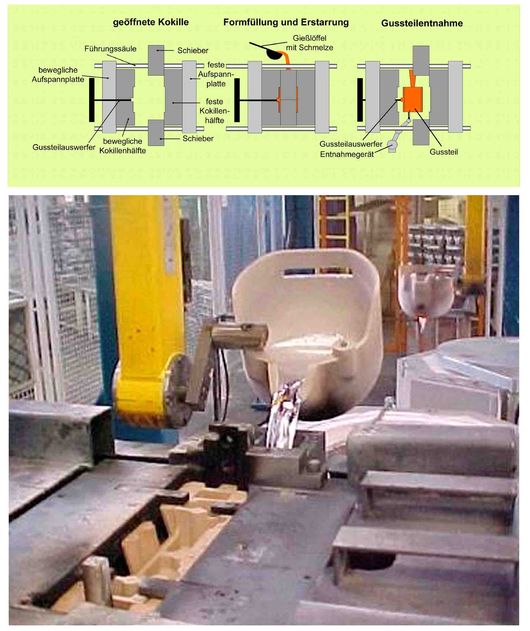
Bild 3: Schematische Darstellung Kokillenguss (oben) und Füllvorgang – steigender Guss (Schwerkraftfüllung) (unten)
Kippkokillenguss
Um den Füllprozess zu optimieren wurden alternativ zum Standard-Kokillengießverfahren Verfahrensvarianten entwickelt, bei denen die Form über eine Drehbewegung um die Kokillenlängsachse gefüllt wird. Abhängig von der Gussteilgeometrie erfolgt die Füllung direkt durch sogenannte Einlaufspeiser oder aber durch seitlich angeordnete Gießläufe. Durch die Neigung der Form zu Beginn der Formfüllung werden schädliche Turbulenzen vermieden. Gleichzeitig wird die gelenkte Erstarrung gefördert, da in der Regel durch jene gießtechnischen Elemente gefüllt wird, aus denen während der Erstarrung die Sättigung (Speisung) erfolgt. Mit dem Kippkokillengießen lässt sich die Gussteilqualität verbessern, da weniger füllbedingte Einschlüsse und Poren im Gussteil vorliegen. Aus dem Kippkokillengießverfahren haben sich Sonderformen entwickelt, die unter verschiedenen Markennamen verbreitet sind (z.B. Rotacast-Verfahren (Bild 4) oder Nemak-Dynamic-Casting System NDCS).
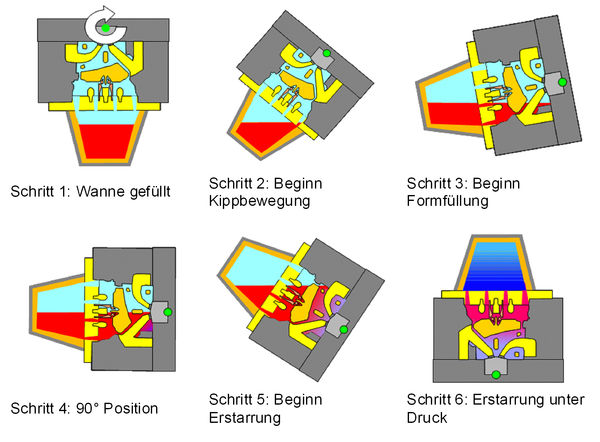
Bild 4: Verfahrensschritte Rotacast®-Verfahren (Graphik: Nemak, Wernigerode)
Um weitere Verbesserungen hinsichtlich der Gussteilqualitäten zu realisieren, wurden nachfolgend beschriebene Gießverfahrensvarianten entwickelt:
Niederdruck-Kokillengießverfahren
Während beim oben beschriebenen Kokillengießverfahren die Formfüllung mittels Schwerkraft erfolgt, geschieht dies beim Niederdruck-Kokillengießverfahren durch einen geringen Überdruck von etwa 0,3 bis 0,7 bar (Bild 5). Dazu wird ein druckdichter Gießofen über ein Steigrohr mit der darüber angeordneten Kokille verbunden. Durch eine Druckerhöhung steigt der Metallspiegel durch das Steigrohr von unten in den Formhohlraum. Damit wird eine ruhige Formfüllung und bei geeigneter Gussteilgestalt eine gute Speisung erzielt. Bei entsprechenden Gussteilen und Seriengrößen lässt sich auch das Niederdruck-Kokillengießverfahren weitgehend mechanisieren. Bevorzugt werden rotationssymmetrische Teile mit diesem Verfahren hergestellt, z.B. Aluminium-Räder.
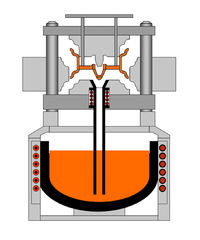
Bild 5: Schematische Darstellung einer Niederdruck-Kokillengießanlage
Gegendruck-Kokillengießverfahren
Das Prinzip des Gegendruck-Kokillenverfahrens (auch CPC-Verfahren – Counter Pressure Casting) wurde aus dem Niederdruckgießen entwickelt. Der wesentliche Unterschied besteht darin, dass die Kokille druckdicht ausgeführt wird (Bild 6). Vor der Formfüllung wird die Kokille unter Druck gesetzt (ca. 4 bis 5 bar) und dann über einen entsprechend höher liegenden Differenzdruck gefüllt. Der Vorteil des Verfahrens liegt darin, dass der Speisungsdruck gegenüber dem klassischen Niederdruckguss erhöht ist, wodurch sich ein porenärmeres Gefüge und damit bessere mechanische Eigenschaften erzeugen lassen. Der verfahrenstechnische Aufwand ist höher und dementsprechend auch die Gussteilkosten.
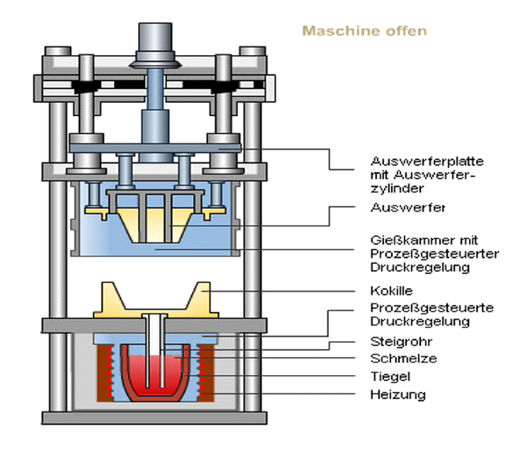
Bild 6: Gegendruck-Kokillengießverfahren (CPC-Verfahren) (Graphik: KSM Casting, Hildesheim)
Schleuder-Kokillengießverfahren
Das Schleuder-Kokillengießverfahren lässt sich vorteilhaft zur Herstellung von dickwandigen Büchsen und Rohren aus Kupfer- und Aluminiumgusslegierungen anwenden. Bei diesem Verfahren wird das flüssige Metall in eine sich drehende zylindrische Kokille mit horizontal liegender oder vertikal stehender Längsachse eingefüllt. Auf hydraulisch geführten Schleudergießmaschinen mit gekühlten Dauerkokillen werden unter Ausnutzung einer hohen Zentrifugalbeschleunigung Gussprodukte gefertigt, die höchsten Ansprüchen genügen. Durch hohe Zentrifugalkräfte entsteht ein dichtes Gefüge mit sehr guten mechanischen Eigenschaften.
Stranggießen
Das Stranggießen ist ein Verfahren, das in erster Linie zur Herstellung Formaten (Halbzeug) eingesetzt wird. Die Formate sind erforderlich für die Weiterverarbeitung durch Walzen, Pressen oder Schmieden zur Herstellung von Folien, Blechen und Bändern sowie von Profilen und Drähten oder von Schmiedeteilen. Im Stranggießverfahren werden sowohl Leichtmetalle (AI, Mg) wie auch Bunt- und Schwermetalle (Cu, Zn) verarbeitet. Den weitaus größten Produktionsanteil hat aber der Stahlstrangguss.
Im Kokillenguss sind als Gusswerkstoffe schwerpunktseitig Aluminium- und Kupferlegierungen etabliert. In Abgrenzung vor allem zu den Eisengusswerkstoffen liegen bei den Aluminiumgusslegierungen die Gießtemperaturen so niedrig, dass die thermische Wechselbeanspruchung keinen frühzeitigen Werkzeugverschleiß verursacht. Neben Aluminium- und Kupferlegierungen werden auch Magnesium- und Zinklegierungen in den Kokillengießverfahren verarbeitet. Die erreichbaren mechanischen Eigenschaften sind den jeweiligen Werkstoffnormen zu entnehmen (DIN EN 1706 Aluminium und Aluminiumlegierungen – Gussstücke sowie DIN EN 1982 Kupfer und Kupferlegierungen – Blockmetalle und Gussstücke).
Quellen:
Sand- und Kokillenguss aus Aluminium – Technische Richtlinien, Herausgeber BDG, Düsseldorf 2010
Guss aus Kupfer und Kupferlegierungen – Technische Richtlinien, Herausgeber BDG und Deutsches Kupferinstitut, Düsseldorf 2011
K. Herfurth, N. Ketscher und M. Köhler: Giessereitechnik kompakt – Werkstoffe, Verfahren, Anwendungen. Giesserei-Verlag GmbH, Düsseldorf 2003, veränderter Nachdruck 2005 (ISBN 3-87260-148-2)
konstruieren + giessen 33 (2008) Nr. 2, S. 22-25
DIN-Taschenbuch Nr. 455, Gießereiwesen 2 - Nichteisenmetallguss, Beuth-Verlag