Hightech-Gießerei führt Energiemanagement ein
Von Frank Leischner Und Johanna Hirsch, Kassel
Erschienen in GIESSEREI 11/2012
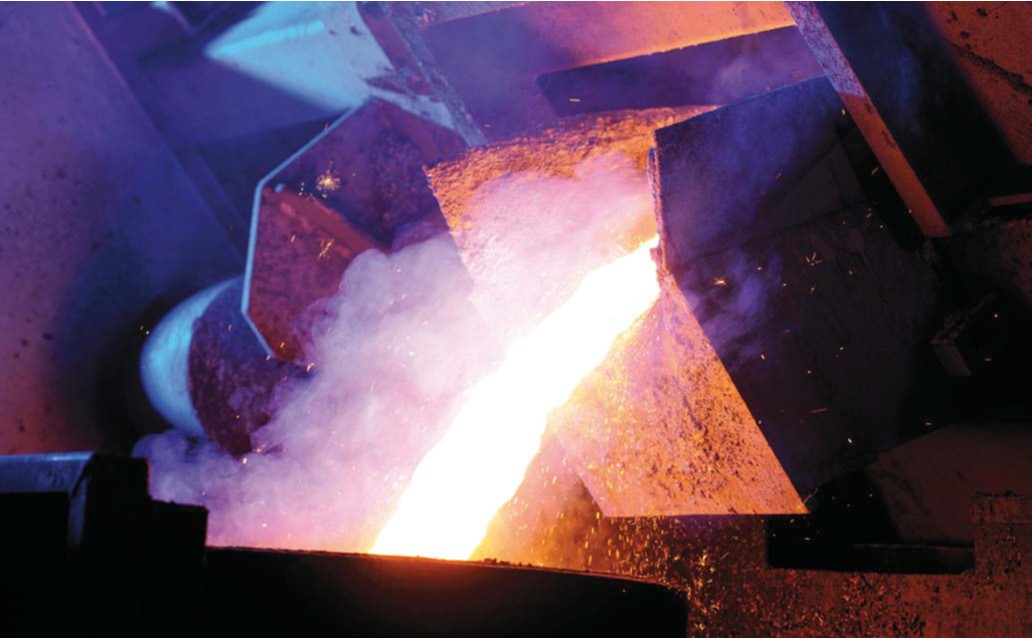
Ofenabstich bei CLAAS GUSS. Die Eisengießerei hat an all ihren Standorten ein EnMS nach DIN ISO EN 500001 eingeführt.
Energiemanagementsysteme (EnMS) sind für eine kontinuierliche Ver besse rung von Energieeinsätzen und zum Erreichen geplanter Energieeinsparungen eine wesentliche Basis. Durch die Dar stellung und Systematisierung von ener gie - relevanten Prozessen und Struk turen in transparenter Form lassen sich allen Beteiligten um fang reiche Informationen und aussagekräftige Kennzahlen zugänglich machen. Des Weiteren zwingen politische wie auch wirtschaftliche Rah men bedingungen Unternehmen im mer mehr, Energieeffizienzmaßnahmen systematisch voranzutreiben. Neben der Energie- und Stromsteuer erfordert bereits die Ausgleichsregelung nach §§ 40 ff. EEG ein vorhandenes EnMS zur Minderung der zu zahlenden Umlage. Die Unternehmen, die den Spitzenausgleich ab 2013 in Anspruch nehmen wollen, müssen ein EnMS nach DIN ISO EN 50001 verbindlich einführen und betreiben. Bild 1 verdeutlicht mögliche Einsparpotentiale für Unternehmen.
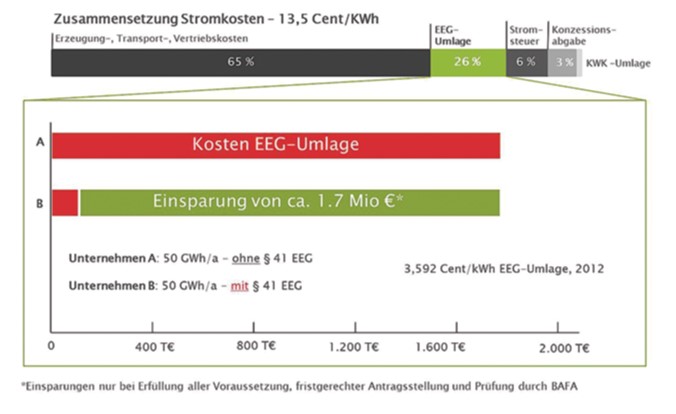
Bild 1: Einsparpotentiale durch ein Energiemanagement.
Festlegung der zukünftigen Energiepolitik
Zur Implementierung eines EnMS entsprechend der Norm müssen Unternehmen, die eine effizientere und nachhaltigere Energienutzung erreichen wollen, verschiedene Teilprozesse durchlaufen.
Ziel dabei ist es, die Betriebe in die Lage zu versetzen, ein mit der DIN EN ISO 50001 konformes EnMS aufzubauen und erfolgreich aufrechtzuerhalten. Das in der Norm definierte System orientiert sich dabei an dem bewährten Managementmodell „PDCA“, Plan – Do – Check – Act (zu Deutsch: Planen – Ausführen – Kontrollieren – Optimieren). Aufgrund des damit verbundenen schrittweise fortlaufenden Vorgehens wird dieses Modell auch als PDCA-Zyklus bezeichnet. Bild 2 stellt eine Übersicht über den PDCA-Zyklus und die dazugehörenden Aktivitäten für ein erfolgreiches EnMS dar. In erster Instanz erfolgt dabei die Bewertung des Systems durch die Geschäftsführung und die Erarbeitung von Maßnahmen zur Verbesserung der jeweiligen Prozesse und Verfahren. In diesem Zusammenhang ist die Geschäftsführung dazu verpflichtet, Personen zu benennen, die für die Einführung und Aufrechterhaltung des Systems verantwortlich sind. Zudem muss die Geschäftsführung sicherstellen, dass den Verantwortlichen Informationen sowie alle Ressourcen (Finanzen, Personen, Techniken) zum Erreichen der Ziele zur Verfügung stehen. Darauf aufbauend kann die Festlegung einer zukunftsorientierten Energiepolitik erfolgen. Zudem unterstützen die gesammelten Informationen den Zertifizierungsprozess sowie die Kommunikation der Ergebnisse nach innen und außen. Danach geht es an die eigentliche Implementierung des EnMS. In dieser Phase werden, wenn möglich, alle Aktivitäten umgesetzt, die im vorangegangenen Planungsprozess festgelegt wurden. Um eine effektive Umsetzung zu gewährleisten, bedarf es der Erarbeitung von Kommunikations- und Schulungsmaßnahmen, um alle Mitarbeiter der Organisation wirksam einzubinden. Um letztendlich einen kontinuierlichen Verbesserungsprozess zu gewährleisten, sind alle Systembestandteile regelmäßig zu überprüfen. In wiederkehrenden Abständen sollten des Weiteren Energieaudits zur Identifikation von Energieeinsparpotentialen durchgeführt werden. Nur so können Schwachstellen aufgedeckt und durch Korrekturmaßnahmen behoben werden. Darüber hinaus ist die Geschäftsführung verpflichtet, eine Bewertung des EnMS durchführen, um die kontinuierliche Eignung, Angemessenheit und Wirksamkeit des Systems bewerten zu können. Diese sogenannten Management-Reviews enthalten eine übersichtliche Zusammenfassung aller Daten und Ergebnisse des eingeführten EnMS und überprüfen regelmäßig seine Leistungsfähigkeit.
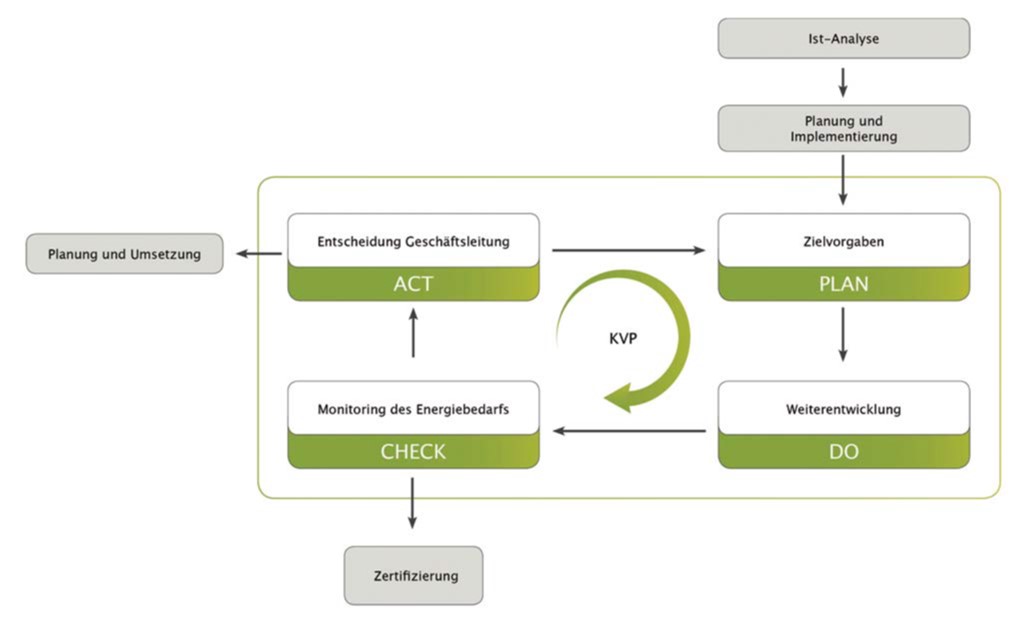
Energieeffizienz ist unerlässlich
Vor allem für Gießereibetriebe sind Energiemanagementsysteme eine lohnende Investition. Betrachtet man den Herstellungsprozess für 1 t Gusseisen (Netto-Rohguss), sind dabei im statistischen Durchschnitt etwa 2200 kWh Energie erforderlich. Dies entspricht bei Zugrundelegung der aktuellen Strompreise Kosten in Höhe von ca. 250 Euro. Bei einer Jahresproduktion von 15 000 t hat eine durchschnittliche Gießerei dann allein für diese beiden Energieträger 2 Mio. Euro aufzubringen. Es ist somit gerade für Gießereien unabdingbar, zukünftig den Energieeinsatz so effizient wie möglich zu gestalten und langfristig Energiekosten einzusparen, um auf dem Markt bestehen zu können.
Schritte bei der Implementierung
Die Einführung eines EnMS umfasst mehrere Schritte, um langfristig Effizienzpotentiale im Unternehmen zu etablieren. Die Erfahrung zeigt, dass die Vorgehensweise nach Norm dabei nicht immer eingehalten werden kann. Vielmehr besteht die Notwendigkeit, sich jedem Unternehmen individuell zu widmen und dieses anhand seiner speziellen Ausganglage zu analysieren.
Die Limón GmbH, Kassel, beginnt dabei im ersten Schritt mit einer ausführlichen Besichtigung der Betriebsstätten. Auch im Fall von CLAAS GUSS wurde damit begonnen, sich eine Übersicht der Energieverbräuche zu verschaffen und die Hauptverbraucher für Strom, Erdgas und Koks zu identifizieren.
Hierzu wurden die Standorte Bielefeld, Gütersloh (Bild 3), Bad Saulgau und Nortorf besichtigt.
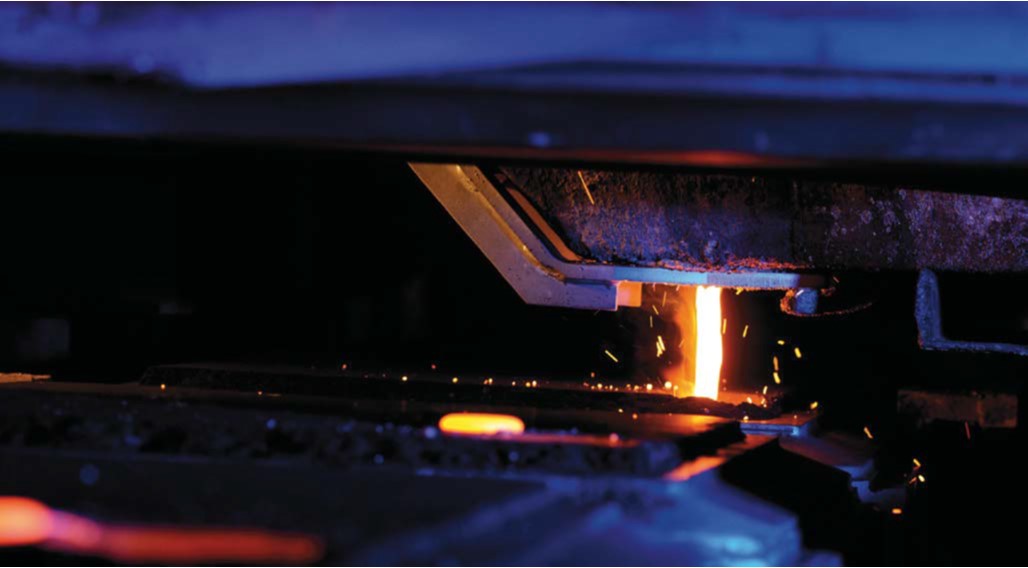
Obwohl an allen Betriebsstätten Gussteile gefertigt werden, unterscheiden sich diese bezüglich ihrer Verfahrensweisen. Um diese Verschiedenheiten optimal zu berücksichtigen, war es entscheidend die Mitarbeiter vor Ort in den Prozess der Potentialidentifikation einzubinden. Auch der Erfahrungsaustausch zwischen verschiedenen Produktionsstätten kann hierbei wichtige Erkenntnisse erbringen. Die Praxis zeigt, dass an verschiedenen Standorten bereits Maßnahmen umgesetzt wurden, die an anderer Stelle ebenso ergiebig sein können. Durch die Kombination aus Fachleuten und Anlagenbedienern an den Standorten sowie dem externen Know-how von Limón konnten die wesentlichen Energieverbräuche (Bild 4) identifiziert und zahlreiche wirtschaftliche Einsparideen generiert werden.
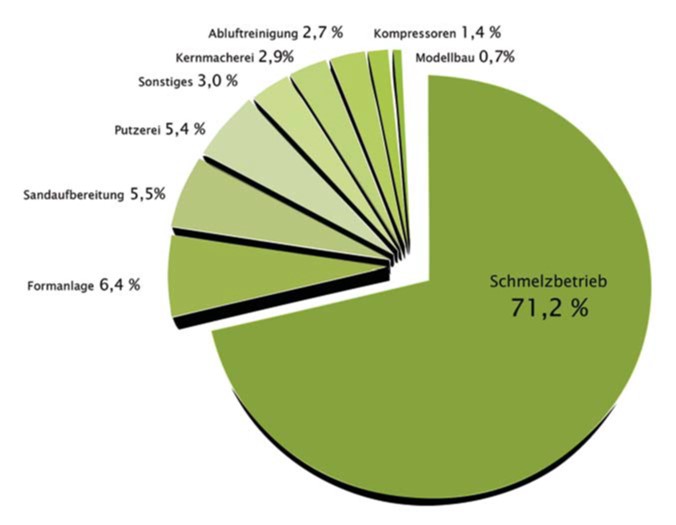
Einsparpotentiale
Ein weiterer entscheidender Faktor auf dem Weg zu einem erfolgreichen EnMS besteht in der darauffolgenden Ermittlung und Gliederung der Parameter, die einen wesentlichen Einfluss auf den Energiebedarf besitzen. Hier bietet es sich an, Prozesse sowie Personen zu identifizieren, die einen wesentlichen Einfluss auf den Energieverbrauch des Unternehmens haben (Bild 5). Die Festlegung der Energieziele erfolgte analog zur Norm und beinhaltete sowohl die strategischen Ziele (z. B. Transparenz der Energieströme erhöhen, Schulung aller Mitarbeiter und Verbesserung der energiebezogenen Leistung um 3 %) als auch die operativen Ziele (Senkung des Energieverbrauchs in der Formanlage, Abluftreinigung, Sandaufbereitung, Pfannenwirtschaft). Kernstück der Einführung eines EnMS war dann die Erstellung einer genauen Verfahrensanweisung zur „Energetischen Planung und Überwachung“, die die Handlungsanweisung für alle Verantwortlichen bildet. Darauf aufbauend konnten bestehende Abläufe hinterfragt und die Planung sowie Beschaffung neuer Anlagen abgestimmt werden, wie zum Beispiel der Bau einer neuen Kernmacherei.
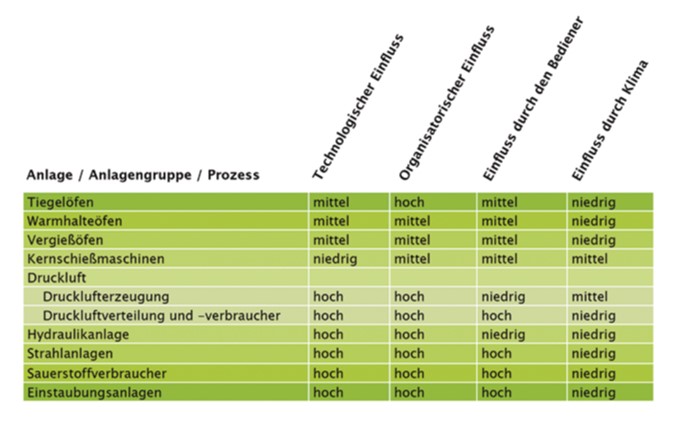
Abschließend wurden alle erforderlichen Vorgänge und Umsetzungen für ein funktionierendes EnMS vom TÜV Nord erfolgreich geprüft und zertifiziert. CLAAS GUSS hat damit, als eine der ersten Gießereien in Deutschland, für seine Standorte Bielefeld, Gütersloh, Bad Saulgau und Nortorf die Zertifizierung für ihr EnMS nach ISO 50001 erhalten.
Die umgesetzten Maßnahmen helfen Gießereibetrieben dabei, ihren spezifischen Energieverbrauch in der Produktion kontinuierlich zu senken, Effizienzmaßnahmen zu koordinieren und Energieströme jederzeit zu überwachen und zu optimieren (Bild 6). Die Zertifizierung nach DIN EN ISO 50001 dient den Unternehmen außerdem als Nachweis eines funktionierenden Energiemanagements zur Beantragung von Steuerrückerstattungen.
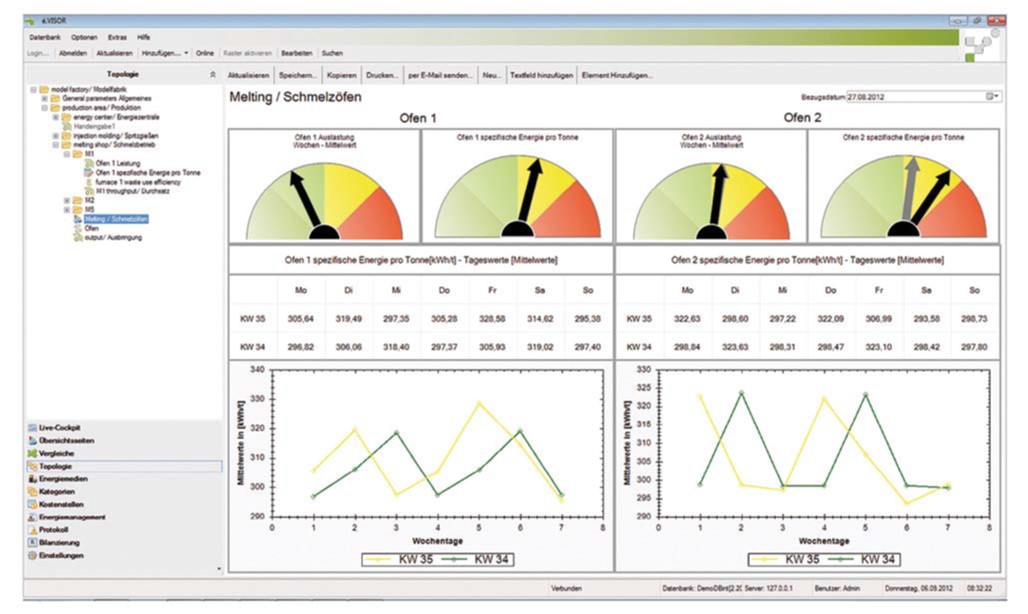
Es bleibt jedoch zu beachten, dass nach Abschluss einer erfolgreichen Zertifizierung weiterhin das Thema Energieeffizienz im Unternehmen implementiert und langfristig gelebt werden muss. Nur so können dauerhaft Energieeinsparungen generiert und umgesetzt werden.
Dipl.-Wirtsch.-Ing. Frank Leischner, Projektingenieur und Mitgesellschafter, und Johanna Hirsch, Limón GmbH, Kassel
Literatur:
Bundesverband der Deutschen Gießerei-Industrie: Energieeffizienter Gießereibetrieb, Fachbericht Institut für Gießereitechnik, Düsseldorf 2008, S. 15.
Junge, M: Energieeffizienz mit System. Auf dem Weg zur CO2-neutralen Fabrik, Ludwigsburg 2012.
Junge, M., Holzäpfel, C.: Energieeffizienz bewerten. Energy 2.0-Kompendium, München, 2011, S. 94-96.