Bewertung von Energieeffizienz-Maßnahmen in Aluminium-Druckgussbetrieben durch Simulation
Von Johannes Dettelbacher und Wolfgang Schlüter, Ansbach
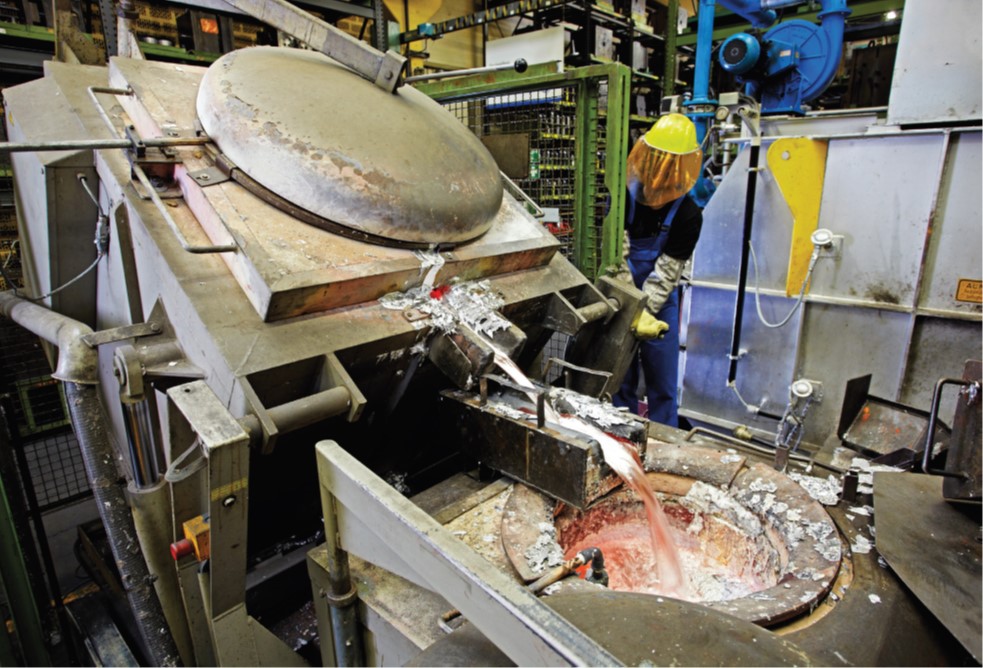
Simulationsgestützte Voruntersuchungen helfen bei der Beurteilung der Wirksamkeit von Energieeffizienzmaßnahmen in der Druckgussproduktion.
Erschienen in GIESSEREI 05/2019
In Zusammenarbeit mit den Kooperationspartnern pressmetall Gunzenhausen GmbH, ZPF GmbH, Siegelsbach, und dem Bundesverband der deutschen Gießerei-Industrie (BDG) wurde an der Hochschule Ansbach ein Demonstrator zur simulationsgestützten Analyse von Energieeffizienzmaßnahmen entwickelt, in dem ein beliebig konfigurierbarer Schmelz- und Druckgussbetrieb virtuell abgebildet werden kann. Das Kompetenzzentrum Industrielle Energieeffizienz (KIEff) an der Hochschule Ansbach forscht im Bereich der Steigerung der Energieeffizienz bei energieintensiven Betrieben wie der Nichteisen-Schmelz- und Druckgussindustrie. In verschiedenen Projekten des Forschungsverbundes Green Factory Bavaria und des Energie Campus Nürnberg (EnCN) wird gemeinsam mit industriellen Kooperationspartnern an Themen wie Simulation, Datenanalyse und Automatisierung von Schmelz- und Druckgussbetrieben gearbeitet.
Energieeffizienz in der Gießereibranche
Die Bedeutung der industriellen Energieeffizienz hat speziell in Deutschland infolge der fortschreitenden Energiewende und der steigenden Konkurrenz durch die Globalisierung stark zugenommen. Ein großes Energie- und Kosteneinsparungspotenzial zeigt sich dabei insbesondere in energieintensiven Branchen wie z. B. der Nichteisen-Gussindustrie. Die Energiekostenbelastung kann dort laut statistischem Bundesamt 25 % der Bruttowertschöpfung übersteigen [1]. In der Branche liegt der Energieverbrauch pro Tonne gutem Guss in der Regel zwischen 2000 und 6000 kWh [2, 3]. Dabei sind die Aufschmelz- und Warmehalteprozesse in den Schmelz- bzw. Warmhalteöfen mit bis zu 60 % der aufgebrachten Energie maßgebend für die betriebliche Energieeffizienz. Die Energieverluste eines Ofens können zwar durch Maßnahmen wie Erneuerung der Ausmauerung oder einer verbesserten Isolierung reduziert werden, jedoch sind entsprechende Verfahren meist mit hohen Investitionen und längerfristigen Stillständen der Anlagen verbunden. Weiteres Einsparpotenzial ergibt sich hingegen durch eine Optimierung der Auslastung und Fahrweise der Schmelzöfen sowie durch die energetische Nutzung des Abgases. Die Erprobung der Effizienzmaßnahmen ist jedoch mit weitreichenden Eingriffen in den Produktionsablauf verbunden und gefährdet damit die Planungssicherheit im Werk.
Simulationsgestützte Voruntersuchungen bieten Schmelz- und Druckgussbetrieben die Möglichkeit, die Wirksamkeit der Maßnahmen im Voraus zu beurteilen, ohne die Produktion zu beeinflussen. Ausgehend von den Simulationsergebnissen sollte ein Demonstrator zum Aufzeigen von Einspar- und Verbesserungspotenzialen bei Energieeffizienzmaßnahmen in den Betrieben entwickelt werden.
Analyse der Betriebsstruktur
In einer Voruntersuchung wurden die Betriebsstruktur sowie die betrieblichen Abläufe der Gießereibetriebe analysiert. Die Analyse des grundsätzlichen Aufbaus verschiedener Betriebe zeigt die Unterschiede und Gemeinsamkeiten sowie ihre Auswirkungen auf den innerbetrieblichen Materialfluss. Der Fertigungsprozess von Druckgussbetrieben setzt sich stets aus einer Kombination kontinuierlicher (z. B. Schmelzen) und diskreter (z. B. Gießen) Prozessschritte zusammen, welche in der Simulation abzubilden sind. Folgende Prozessschritte sind für die Simulation relevant und werden berücksichtigt:
- Anlieferung von flüssigem Aluminium bzw. Blockmaterial (Masseln)
- Beschicken der gasbetriebenen Schachtschmelzöfen (SO) über Stapler mit Masseln, Rücklauf- oder Ausschussmaterial
- Erwärmen, Schmelzen und Überhitzen bzw. Warmhalten des Metalls
- Verteilung des flüssigen Aluminiums auf die Dosieröfen der Druckgießmaschinen (DGM) mithilfe von DGMStaplern
- Produktion von Gussteilen in den Druckgießmaschinen und Qualitätsprüfung
- Transport von vollen/leeren Materialbehältern aus der Druckgießerei oder von Masselpaketen aus dem Lager zum Schmelzbetrieb
Betriebsspezifische Simulation
Im Rahmen des Green Factory Bavaria-Projektes E|Melt wurde ein hybrides Simulationsmodell, das den Materialfluss des Gesamtbetriebes und den Energieverbrauch der Schmelzöfen abbildet, entwickelt und anhand von realen Produktionsdaten validiert.
Die Software wurde hierbei so konzipiert, dass sich beliebige Betriebe abbilden lassen. Über eine Anlagenkonfiguration, welche die Betriebsstruktur und die Anzahl der produzierenden Druckgießmaschinen, der Schmelzöfen und der Transportstapler umfasst, werden die betriebsspezifischen Simulationsmodelle generiert. Der grundlegende Simulationsablauf ist in Bild 1 dargestellt. Mithilfe des Materialflussmodells wird der komplette Materialfluss innerhalb des Werks aufgezeichnet. Das Energieflussmodell erfasst die thermodynamischen Vorgänge in den Aluminiumschmelzöfen. Die Kommunikation beider Ebenen erfolgt mithilfe eines Schnittstellen-Objekts, das den Austausch der relevanten Daten zwischen den beiden Modellen ermöglicht. In einem von der Simulation entkoppeltem Steuerungsmodul werden auf Basis der ermittelten Anlagen- und Prozessparameter sowie der definierten Steuerungsstrategien Aufträge für die verschiedenen Komponenten generiert.
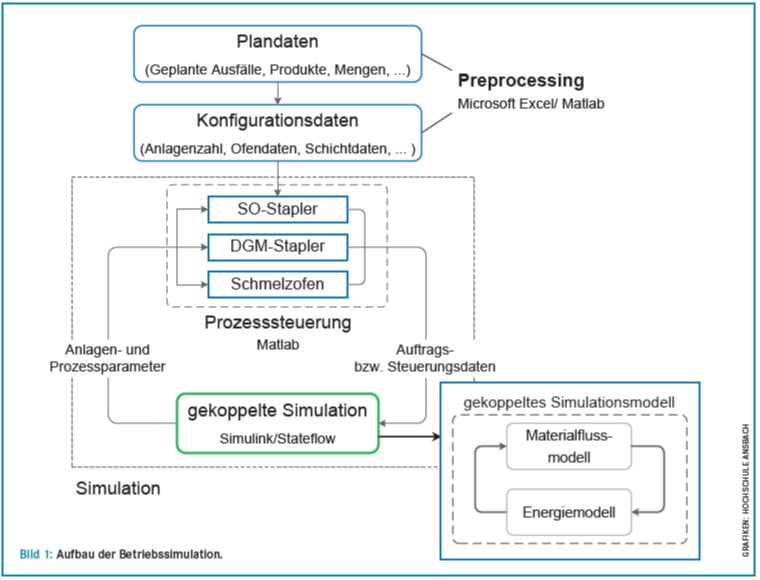
Kernelement der Simulation ist das Energiemodell, das die energetischen Vorgänge innerhalb des Schmelzofens abbildet. Zur Validierung wurden die Vorgänge mit komplexen Modellen beschrieben, sodass die notwendige Datengrundlage der Modelle oftmals den Grad der vorhandenen Datenerfassung innerhalb des Betriebs überstieg. Daher wurde anhand von umfangreichen Messdaten ein vereinfachtes Energiemodell entwickelt, das weiterhin aussagekräftige Ergebnisse über den Energieverbrauch der Anlage liefert und den Datenbedarf auf drei Parameter reduziert. Somit entfallen aufwendige messtechnische Untersuchungen am Schmelzofen. Als Datengrundlage für die Initialisierung der Simulation dienen die Anlagen- und Betriebskonfiguration. Die Anlagenkonfiguration enthält neben der Anzahl der Druckgussmaschinen, Schmelzöfen und Transporter auch Kapazitäten der einzelnen Maschinen sowie Fahrt- und Ladezeiten der Transporter. Die Betriebskonfiguration umfasst die Steuerungsstrategien der Stapler und Maschinen, die Produktionsdaten sowie die Ausfallzeiten der Maschinen.
Validierung in zwei verschiedenen Betrieben
Die Validierung der gekoppelten Simulation wurde anhand von zwei realen Referenzbetrieben durchgeführt. Hierfür wurden die Betriebsdaten schichtübergreifend für eine Kalenderwoche verwendet. Bei dem Materialflussmodell ergaben sich eine Abweichung in der Anzahl der produzierten Aluminium-Gutteile sowie der verbrauchten Aluminiummenge von 1,4 bzw. 0,9 %. Auch die Ergebnisse des Energiemodells konnten anhand der aufgezeichneten Daten bestätigt werden. Die geschmolzene Aluminium-Masse und der Gasverbrauch weichen hierbei um 1,5 bzw. 0,5 % von den tatsächlichen Werten ab. In Bild 2 ist der Verlauf der Aluminium-Masse im Schmelzschacht und die Rauchgastemperatur am Schachtaustritt in einem Zeitraum von fünf Stunden dargestellt. Es zeigt sich, dass die Simulation auch den zeitlichen Verlauf des Schmelzprozesses sehr gut abbilden kann.
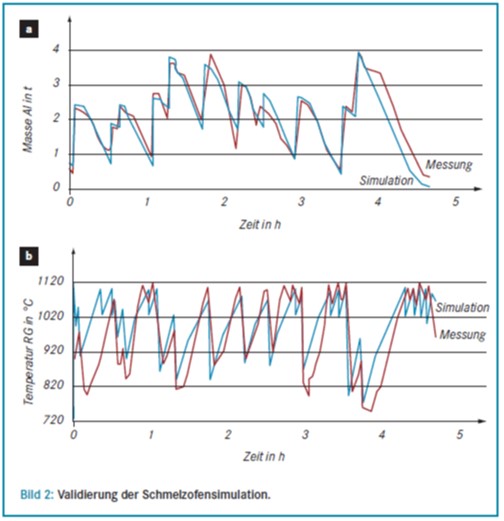
Effizienzmaßnahmen
Mithilfe der entwickelten Simulation lassen sich Effizienzmaßnahmen in spezifischen Betrieben simulativ untersuchen.
Verbesserte Beschickung der Schmelzöfen
Die zeitliche Optimierung der Beschickung, die ohne zusätzlichen Investitionsaufwand möglich ist, zielt auf eine Steigerung der Energieeffizienz des Schmelzvorgangs ab. Ziel ist es, einen dauerhaft hohen Füllstand im Ofen-Schmelzschacht zu gewährleisten, um eine optimale Wärmeübertragung zwischen Rauchgas und Aluminium zu realisieren. Erreicht wird dieses Ziel mit einer verbesserten Strategie beim Beschicken. Durch diese Maßnahme sinkt der Energieverbrauch des Schmelzofens um etwa 10 %. Notwendige Voraussetzung dafür ist eine präzise Datenerfassung des Schmelzschacht- und des Ofenwannenfüllstandes.
Vorwärmung der beschickten Masselpakete
Durch die Nutzung der in den Schmelzofen-Abgasen enthaltenen Restwärme wird das feste Aluminium auf 300 °C erwärmt. Die nötige Energie zur Erwärmung im Schmelzofen sinkt dadurch bereits im Vorfeld deutlich, was in einer gesteigerten Schmelzrate resultiert. Hierdurch verringert sich der Energieverbrauch um bis zu 9 %. Im Rahmen der Untersuchung der Materialvorwärmung wurden anhand von Strömungssimulationen unterschiedliche Masselgeometrien und Schichtungsstrategien untersucht (siehe Bild 3). Für die Realisierung der Materialvorwärmung ist eine Vorwärmkammer erforderlich, die in die betrieblichen Abläufe integriert werden muss.
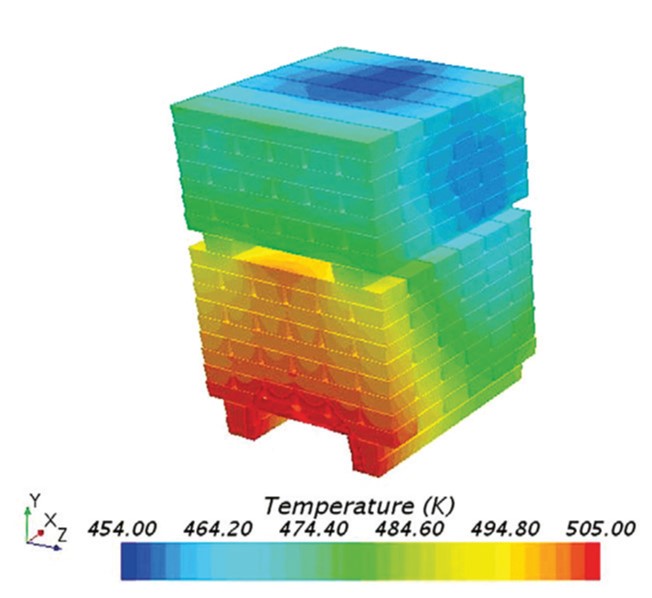
Verbesserte Belieferung der Druckgießmaschinen
Die Belieferung der Druckgießmaschinen erfolgt derzeit in zahlreichen Schmelzund Druckgussbetrieben noch anhand starrer Regeln, welche die aktuelle Versorgungssituation der Druckgießmaschinen nur rudimentär berücksichtigen. Angewandte Strategien sind eine feste Reihenfolge der Belieferung oder das Signalisieren von Aluminiummangel durch eine Ampelanzeige. Die Erfassung des relativen Füllstands sämtlicher Maschinen ermöglicht eine bedarfsgerechte Belieferung, wodurch sich die Dauer der durch Aluminiummangel entstehenden Ausfälle deutlich gesenkt bzw. ganz vermieden wird. Für die Umsetzung dieser Maßnahme wird eine präzise Füllstandserfassung der Dosieröfen an den Druckgießmaschinen sowie eine übersichtliche Darstellung der Daten für die Staplerfahrer benötigt. Es wurde simulativ gezeigt, dass mit den drei beschilderten Effizienzmaßnahmen der spezifische Energieverbrauch [kWh/t] der Schmelzöfen in den einzelnen Betrieben um bis zu 25 % gesenkt werden konnte. Dabei ließ sich eine Steigerung der OEE (Anlageneffizienz) um bis zu 3 % erzielen.
Online-Demonstrator
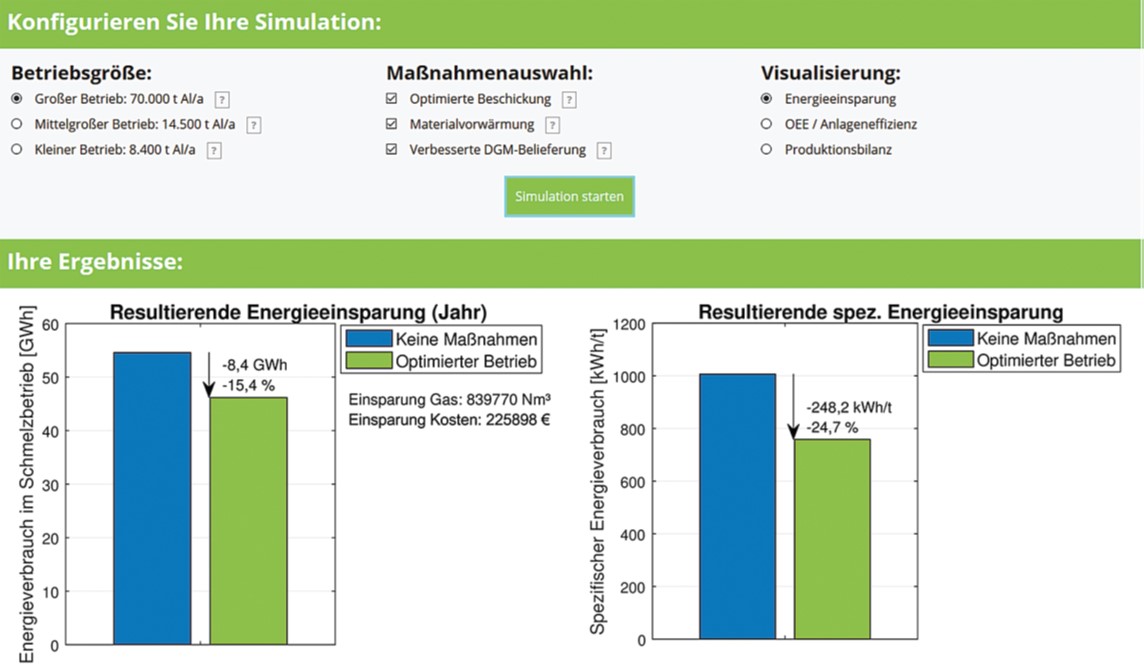
Aufbauend auf den Simulationsergebnissen wurde in Zusammenarbeit mit den Kooperationspartnern ein Online-Demonstrator erstellt. Der Demonstrator ist auf der Homepage der Hochschule Ansbach frei verfügbar. Mit diesem lässt sich die Wirksamkeit der Energieeffizienzmaßnahmen für drei typische Betriebe verschiedener Größe aufzeigen (Bild 4).
Als mögliche Betriebsgröße kann ein großer Betrieb mit einer jährlich verarbeiteten Aluminiummasse von 70 000 t Al/a, ein mittelgroßer Betrieb mit 14 500 t Al/a und ein kleiner Betrieb mit 8400 t Al/a ausgewählt werden. Als Ergebnis kann sich der Nutzer die Energieeinsparung, die Anlageneffizienz sowie die Produktionsbilanz grafisch darstellen und die Ergebnisse als PDF exportieren lassen. Der Demonstrator dient lediglich dem beispielhaften Aufzeigen von Effizienzmaßnahmen sowie deren Potenzialen. Um die Potenziale für einen spezifischen Betrieb zu analysieren, kann dieser mithilfe der betriebsspezifischen Simulation am Kompetenzzentrum Industrielle Energieeffizienz (KIEff) der Hochschule Ansbach genauer untersucht werden.
M. Sc. Johannes Dettelbacher, Prof. Dr. Wolfgang Schlüter, Kompetenzzentrum Industrielle Energieeffizienz (KIEff), Fakultät Technik, Hochschule Ansbach
Literatur
[1] C. Schimansky. Energiepolitik. www.bdguss.de/themen/energie/. Letzter Zugriff am17.04.2019.
[2] M. Bosse, E. Frost, M. Hazrat, J.-M. Rhiemeier und H. Wolff. Ermittlung von branchenspezifischen Potentialen zum Einsatz von erneuerbaren Energien in besonders energieintensiven Industriesektoren am Beispiel der Gießerei-Industrie. IfG Institut für Gießereitechnik, Ecofys Germany GmbH, Düsseldorf, 2013.
[3] C. Herrmann, H. Pries und G. Hartmann. Energie- und ressourceneffiziente Produktion von Aluminium-Druckguss. Springer Vieweg, Berlin, 2013.