Analyse von Aluminiumdruckgießprozessen mittels dualer Energiesignatur
Von Rainer Schillig, Aalen, Timo Stock, Aalen/Chemnitz, Miriam Schmeiler, Aalen und Egon Müller, Chemnitz
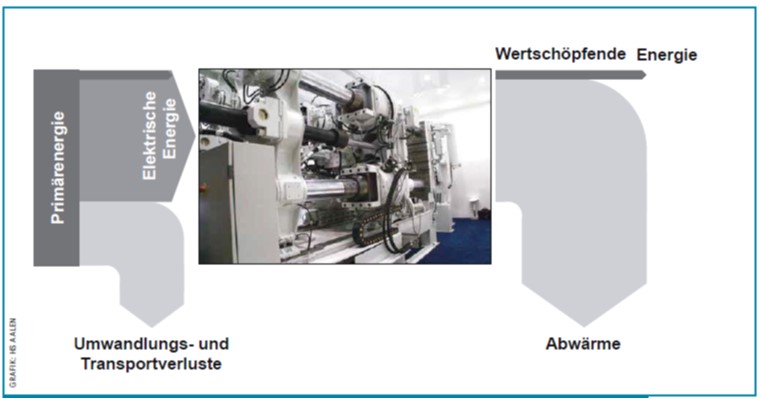
Erschienen in GIESSEREI 07/2015
Energie gewinnt aufgrund der Begrenztheit fossiler Energieträger in Verbindung mit dem wachsenden Energiebedarf der Industrienationen als Kostenfaktor zunehmend an Bedeutung. Speziell die energieintensiven Branchen, darunter die Gießereibranche, sind von den steigenden Energiepreisen betroffen.
Das Aluminiumdruckgießen zählt in der Automobil- und Zulieferindustrie zu den bedeutendsten Gießverfahren. Der Druckgießprozess ist sehr energieintensiv. In den letzten Jahren wurden in vielen Aluminiumdruckgießereien erste Energieeinsparmaßnahmen, wie die Optimierung des Schmelzofens, erfolgreich umgesetzt [1]. Die Druckgießmaschinen und deren unmittelbare Peripherie jedoch blieben bislang weitestgehend unangetastet, obwohl dort die wesentlichen Einsparpotentiale liegen.
Das Verfahren der dualen Energiesignaturen zur Identifikation von Energieverschwendung in Fertigungsprozessen hat sich gut bewährt [2]. Dabei erfolgt die Einteilung des Zeit- und Energieeinsatzes ausschließlich dual in wertschöpfend und nicht wertschöpfend. Wertschöpfender Energiebedarf führt zu einem Mehrwert am Produkt [2]. Dieser Ansatz ist an etablierte Klassifizierungsmethoden (Einteilung der Prozessabläufe mittels der vier Leistungsarten [3] oder der Refa-Lehre [4]) angelehnt. Bei den Leistungsarten wird die Nutzleistung als wertschöpfend definiert (Bild 1 oben). Stützleistung ist aus technischen Gründen teilweise erforderlich, jedoch wie Blind- und Fehlleistung per Definition nicht wertschöpfend [5]. Bild 1 zeigt Beispiele für die Leistungsarten.
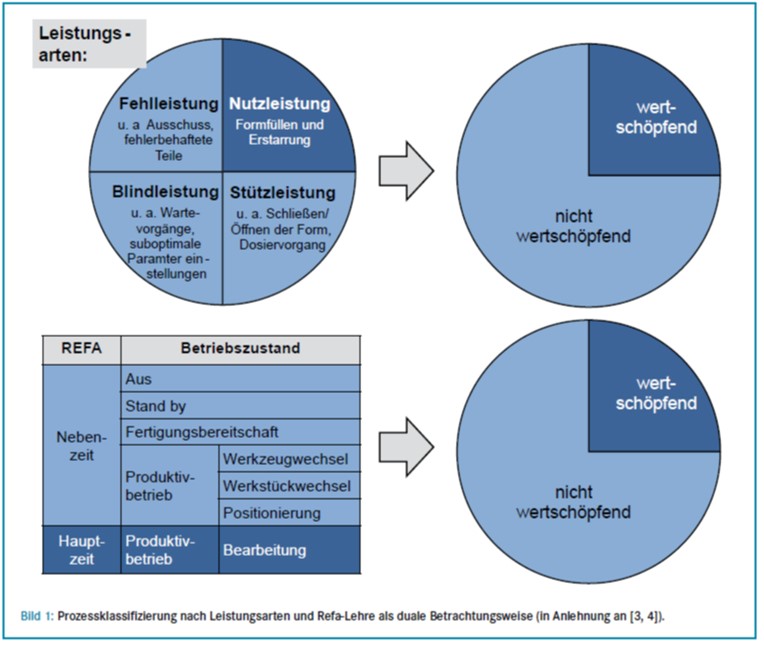
Diese Logik auf die Refa-Lehre übertragen bedeutet:
- Die Hauptzeit, der Betriebszustand Produktivbetrieb/Bearbeitung, wird als wertschöpfend definiert (Bild 1 unten).
- Nebenzeiten, wie die Betriebszustände „Aus“, „Stand by“ und „Fertigungsbereit“, tragen nicht unmittelbar zum Mehrwert am Produkt bei und sind damit nicht wertschöpfend.
In diesem Beitrag wird ein Verfahren zur Berechnung des wertschöpfenden Energieeinsatzes beim Aluminiumdruckgießen vorgestellt.
Durch Gegenüberstellung mit dem tatsächlich gemessenen Gesamtenergiebedarf der Druckgießmaschine können ein energetischer Wertschöpfungswirkungsgrad ηEva berechnet und Verbesserungspotentiale abgeleitet werden. Gleichzeitig wird der zeitliche Wertschöpfungswirkungsgrad ηtva bestimmt.
Analyse und Bilanzierung des elektrischen Energieeinsatzes
Druckgießmaschinen werden vorwiegend hydraulisch betrieben. Dies ermöglicht eine hohe Dynamik zum Beschleunigen der Massen während des Formfüllens.
In einer mittelständischen Gießerei wurde mit einer hydraulischen Kaltkammer-Druckgießmaschine (Frech DAK 720) ein Kühlkörper mit den Abmessungen ca. 450 mm × 300 mm × 5 mm aus Aluminiumdruckguss hergestellt.
Bild 2 zeigt die elektrische Leistungsaufnahme der Druckgießmaschine in den einzelnen Prozessabschnitten. Der Gesamtenergiebedarf innerhalb eines Zyklus beträgt 338,1 Wh. Dieser setzt sich aus dem Bedarf der Antriebe, der Steuerung und der Schaltschrankkühlung zusammen. Neben der konstanten Grundlast (ca. 15 000 W) fallen die hohen Leistungsspitzen (ca. 70 000 W) auf. Diese werden durch die Maschinenbewegung und das Aufladen des Druckspeichers hervorgerufen.
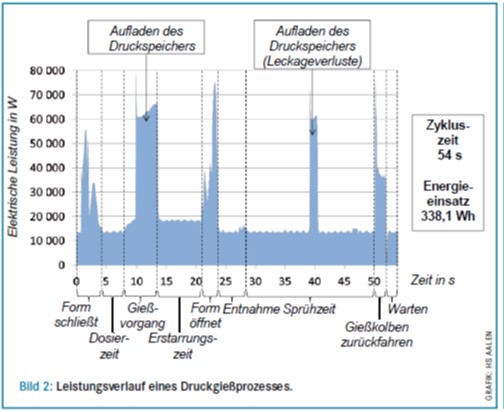
Bilanzierung des Zeit- und Energieeinsatzes mittels dualer Energiesignaturen
Zur Erstellung dualer Energiesignaturen beim Aluminiumdruckgießen wird folgendes Verfahren vorgeschlagen:
a) Aufnahme des Gesamtenergiebedarfs der Druckgießmaschine und Beschreibung der Prozessabschnitte (Bild 2),
b) Berechnung eines „idealen Druckgießprozesses“,
c) Gegenüberstellung des gemessenen Gesamtenergiebedarfs und des „idealen Druckgießprozesses“ auf der Basis der Wertschöpfungsdefinition.
Definition von Wertschöpfung beim Druckgießen
Der Füllprozess ist in drei Phasen eingeteilt [6]. Als wertschöpfend kann jedoch nur der Energieeinsatz, der zum Formfüllen benötigt wird, angesehen werden [7]:
- In der 1. Phase wird die Schmelze langsam bis zum Anschnitt geführt. Der Energieeinsatz ist nicht wertschöpfend.
- In der 2. Phase wird die Schmelze mit hoher Geschwindigkeit in die Form gefüllt. Die hohe Kolbengeschwindigkeit wird durch Zuschalten eines Druckspeichers realisiert. Wertschöpfend ist der unmittelbare Energieeinsatz für das Formfüllen aus dem Druckspeicher (Speicherenergie) und das Urformen, um die Schmelze in die gewünschte geometrische Form zu bringen (Urformenergie).
- In der 3. Phase wird die erstarrende Schmelze unter hohem Druck verdichtet. Dies dient der Volumenkontraktion von Gasen und dem Ausgleich der Schwindung. Der hohe Druck wird oft durch einen zusätzlichen Druckspeicher/ Multiplikator realisiert. Wertschöpfend ist lediglich der Energieeinsatz, der zur Dichtspeisung beiträgt (Verdichtungsenergie).
Berechnung eines „idealen Druckgießprozesses“
Der Kunde ist bereit, für das Bauteil zu bezahlen, für das Angusssystem und die Überläufe nicht. Folglich wird ausschließlich das Bauteil und das dafür benötigte Material als wertschöpfend angesehen. Die Berechnung eines idealisierten Verarbeitungsprozesses erfolgt unter folgenden weiteren Randbedingungen: Die Maschinenbewegungen und das Formfüllen werden als reibungsfrei angenommen. Das Zuhalten der Druckgießmaschine erfolgt kraftfrei und benötigt ebenso keine Energie.
Zur Herstellung eines Formteils wird folglich in einem idealisierten Prozess lediglich die wertschöpfende Energie benötigt, bestehend aus Speicher-, Urformund Verdichtungsenergie (siehe vorhergehender Abschnitt). Diese werden mithilfe der Gleichungen (1) bis (7) berechnet. Bild 3 zeigt das Funktionsprinzip eines Gießaggregats. Die farbigen Markierungen dienen der Verständlichkeit und finden in den nachfolgenden Formeln Snwendung.
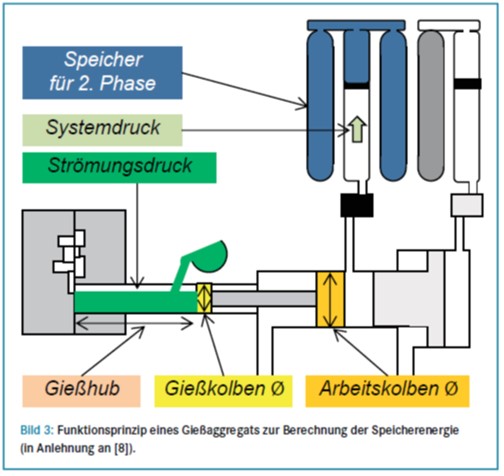
Der tatsächliche Gießhub (ohne Angusssystem und Überläufe) wird nach den Gleichungen (1) und (2) unter folgenden Annahmen berechnet:
- Masse des Bauteils: 0,419 kg (ohne Anguss),
- Dichte Aluminium: 2700 kg/m3 (hier wird vereinfacht mit der Dichte im erstarrten Zustand gerechnet, im flüssigen ist diese etwas geringer) [6].
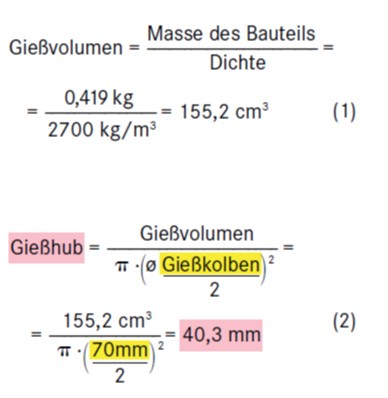
Der tatsächliche Gießhub beträgt 40,3 mm.
Berechnung der Speicherenergie
Die Gusslegierung wird in der zweiten Phase in kürzester Zeit in die Form transportiert. Dies erfordert eine hohe Beschleunigung, da die Schmelze sonst bereits während des Formfüllens erstarrt. Die dafür erforderliche Energie wird in einem Druckbehälter gespeichert (Speicherenergie). Die Hydraulikpumpe fördert entgegen dem eingeschlossenen Gas eine bestimmte Ölmenge in den Druckspeicher, bis der eingestellte Maximaldruck im Speicher erreicht ist. Die Speicherenergie berechnet sich wie folgt.
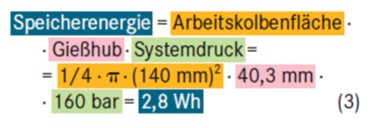
Die berechnete Energie zum Befüllen des Speichers beträgt 2,8 Wh. Diese Energie steht sofort zur Verfügung, wenn das Schussventil öffnet und die Hydraulikflüssigkeit abströmen kann.
Berechnung der Urformenergie
Die Urformenergie wird zum Einfüllen der Schmelze in den Formhohlraum benötigt. Die Berechnung erfolgt mit Hilfe der Bernoulli- Gleichung für quasistationäre Strömungen. Die durchschnittliche Strömungsgeschwindigkeit beträgt i. d. R. 30 bis 50 m/s [9]. Hier wurden 45 m/s angenommen.
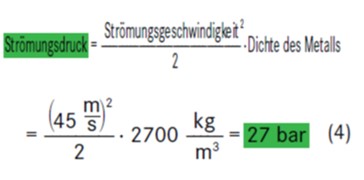
Aus dem errechneten Strömungsdruck und dem Gießvolumen ergibt sich die Urformenergie.
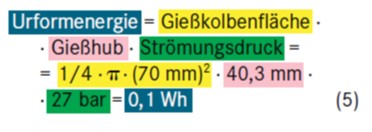
Verdichtungsenergie
Die Erstarrungsschrumpfung stellt beim Übergang vom flüssigen in den festen Zustand eine Volumenabnahme des Bauteils dar. Die direkte Folge ist ein Volumendefizit in Form von Porosität als Lunker [6]. Das Volumendefizit der Schrumpfung kann beim Gießprozess durch Nachspeisen kompensiert werden.
Die Erstarrungsschrumpfung beträgt für Aluminiumlegierungen ca. 4 % [10]. Somit können 4 % des Gießhubes der 2. Phase als Hub der Nachdruckphase angesehen werden. In der Realität ist dieser jedoch meist höher, da das Volumen im Überlauf und dem Angusssystem ebenfalls schwindet.
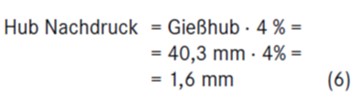
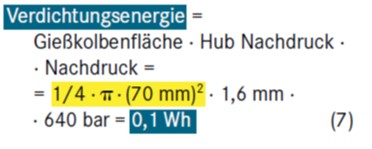
Die Höhe des eingestellten Nachdrucks beträgt 640 bar. Der Zyklus wurde ohne zusätzlichen Speicher in der Nachdruckphase und ohne Multiplikator gefahren. Es ergibt sich folgende Berechnung für die Verdichtungsenergie:
Die Verdichtungsenergie von 0,1 Wh wird lediglich innerhalb der Erstarrungszeit benötigt, da das Material nur bis zur vollständigen Erstarrung des Teils verdichtet werden kann. Zu beachten ist, dass sich die eindringende Wärmestromdichte proportional zum Wärmeeindringkoeffizienten verhält und mit der Zeit abklingt (Chvorinov) [11]. Die Erstarrungszeit für unser Bauteil mit einer maximalen Wanddicke von 3 mm lässt sich somit näherungsweise wie folgt berechnen:
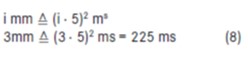
Die Verdichtungsenergie wird folglich in der Erstarrungszeit von 225 ms benötigt.
Duale Energiesignatur mittels des „idealen Druckgießprozesses“
Der wertschöpfende Energieanteil ergibt sich aus der o. g. Berechnung und beträgt in Summe 3 Wh: Speicherenergie 2,8 Wh, Urformenergie 0,1 Wh und Verdichtungsenergie 0,1 Wh (Bild 4, dunkelblaue Anteile der Signatur). Der wertschöpfende Zeitanteil von 3,8 s ist oberhalb der Signatur dunkelorange gekennzeichnet. Damit ist zweifelsfrei ersichtlich, dass nur, wenn Energie wertschöpfend eingesetzt wird, auch die Zeit wertschöpfend sein kann.
Die hellblaue Signatur zeigt den nicht wertschöpfenden Energieeinsatz der Druckgießmaschine. Dieser beträgt 335,1 Wh. Der zugehörige nicht wertschöpfende Zeiteinsatz beträgt 50,2 s, hellorange dargestellt.
Mittels dualer Signatur kann nun der zeitliche Wertschöpfungswirkungsgrad ηtva von 7 % (Gleichung (9)) und der energetische Wertschöpfungswirkungsgrad ηEva von 1 % berechnet werden (Gleichung (10)).
Die Datenbox (Bild 4, rechts) fasst die Ergebnisse zusammen.
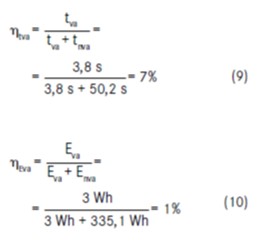
ηtva liegt im einstelligen Prozentbereich. Bei solch geringen wertschöpfenden Zeitanteilen sollte der Prozessablauf überprüft werden. Möglicherweise liegt hier Verbesserungspotenzial durch Reduktion nicht wertschöpfender Zeitabschnitte.
ηEva liegt bei ca. 1 %. Das heißt, ca. 99 % des Energieeinsatzes sind nicht wertschöpfend und damit Energieverschwendung. Die Dimensionierung der Maschine sollte überprüft, nicht wertschöpfende Energieanteile sollten kritisch hinterfragt werden.
Prinzipielle Ansätze zur Steigerung der Energieeffi zienz im Druckgießprozess
Die elektrische Energie E ist das Integral der Leistung P über der Zeit t (Bild 5). Um die Prozesseffizienz zu steigern, sind grundsätzlich zwei Ansatzpunkte möglich [12]:
- Absenkung des Leistungsniveaus P und
- Verkürzung der Prozesszeit t.
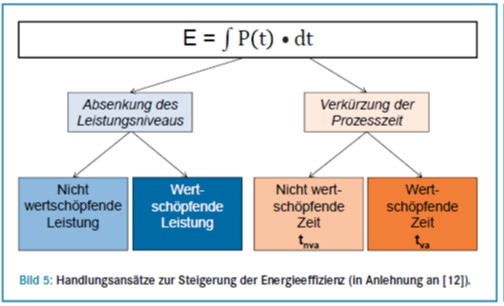
Im Druckgießprozess lässt sich die Energieeffi zienz durch folgende prinzipielle Ansätze steigern:
a) Verkürzen der Prozesszeit: Eine Prozesszeitverkürzung führt neben einer Produktivitätssteigerung regelmäßig auch zu einer Energieeinsparung. Grund: Um Energie zu verschwenden, wird Zeit benötigt. Wird die Zeit reduziert, wird folglich auch der Energiebedarf reduziert. In der Praxis erfolgt die Einstellung der Prozessparameter Sprüh- und Erstarrungszeit im Allgemeinen nach Erfahrungswerten. Diese nicht wertschöpfenden Zeitabschnitte kritisch zu hinterfragen, zeigt regelmäßig Verbesserungspotenzial (Bild 6).
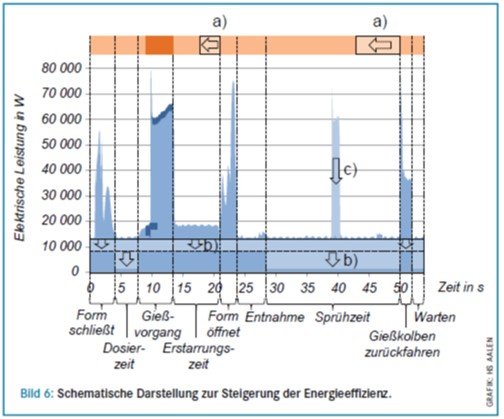
b) Absenken des Leistungsniveaus: Das gesamte Leistungsniveau kann reduziert werden, beispielsweise durch den Einsatz energieeffi zienter Hydraulikkomponenten und strömungsgerechter Rohrleitungsgestaltung (s. Bild 6). Geregelte Pumpen bieten den Vorteil der bedarfsgerechten Bereitstellung von Energie. Somit kann der Energiebedarf in Zeiten ohne Maschinenbewegung reduziert werden (s. Bild 6). Eine weitere Möglichkeit zur Energieeinsparung bieten hybride Maschinenkonzepte. Während die hohen Beschleunigungsvorgänge beim Füllprozess bislang den Einsatz von Hydraulikkomponenten erfordern, ist der Einsatz von elektrischen Antriebskonzepten für sonstige Maschinenbewegungen zu prüfen. Diese sind deutlich energieeffi zienter und bieten weitere Vorteile wie Positioniergenauigkeit und geringeren Wartungsaufwand.
c) Weitere Verbesserungsmaßnahmen: Leckagen führen beim eingesetzten Hydraulikspeicher zu Druckverlust. Dieser muss ausgeglichen werden, um die Druckenergie in der 2. Phase zu gewährleisten (Bild 6, Leistungspeak bei 40 s). Leckage kann durch Abdichten oder steuerungstechnische Änderungen vermieden werden (Bild 6). Steuerungstechnisch kann das Aufl aden des Druckspeichers an das Zyklusende verschoben werden, damit das Speicherladen näher am nächsten Schuss erfolgt. Dies führt zu einer Energieeinsparung von ca. 5 %.
Zusammenfassung
Das Thema Energieeffi zienz gewinnt aufgrund der steigenden Energiepreise zunehmend an Bedeutung. Die Steigerung der Energieeffi zienz erfordert Transparenz hinsichtlich des Energie- und Zeitbedarfs der Maschinen und Anlagen. Mittels dualer Energiesignaturen kann der Energie- und Zeiteinsatz in wertschöpfende und nicht wertschöpfende Anteile unterteilt werden. Bei Aluminiumdruckgießprozessen kann dies mittels des „idealen Prozesses“ erfolgen. Dabei wird der Zeit- und Energieeinsatz eines realen Prozesses einem idealisierten gegenüber gestellt. Der wertschöpfende Energieanteil wird theoretisch berechnet. Aus den Analysen lassen sich der energetische und zeitliche Wertschöpfungswirkungsgrad berechnen und Verbesserungspotentiale ableiten.
Prof. Dr.-Ing. Rainer-Ulrich Schillig, Hochschule Aalen, Aalen, M.B.A.+Eng. Timo Stock, Hochschule Aalen, Aalen,/TU Chemnitz, Chemnitz, M.Sc. Miriam Schmeiler, Hochschule Aalen, Aalen, Prof. Dr.-Ing. Egon Müller, TU Chemnitz, Chemnitz
Literatur:
[1] Hartmann G.; Pries, H.; Herrmann, C.: Energie- und ressourceneffi ziente Produktion von Aluminiumdruckguss. Springer Vieweg: Springer Verlag, Berlin, Heidelberg, 2013.
[2] ZWF 107 (2013), [Nr. 1-2], S. 20-26.
[3] Pfeifer, T.: Qualitätsmanagement, Strategien, Methoden, Techniken. 3. völlig überarbeitete und erweiterte Aufl age. Carl Hanser Verlag, München/Wien, 2001. S. 197.
[4] REFA Verband für Arbeitsstudien und Betriebsorganisation e.V.: Methodenlehre des Arbeitsstudiums, Teil 2 Datenermittlung. 6. Aufl . Carl Hanser Verlag, München, 1978. S. 30, 31.
[5] Erlach, K.; Westkämper, E.: Energiewertstrom – Der Weg zur energieeffi zienten Fabrik. Fraunhofer Verlag, Stuttgart, 2009. S. 57
[6] Hasse, S.: Gießereilexikon. Foundry Technologies & Engineering GmbH (FT&E), (GL), Kantonsgericht Schaff hausen. Online verfügbar unter: www.giessereilexikon.com/giesserei-lexikon/ Stichwort: Umschaltpunkt, Strömungsgeschwindigkeit beim Druckgießen, Erstarrungsschrumpfung
[7] Beitz W.; Grote K.-H.: Dubbel, Taschenbuch für den Maschinenbau. 20. Ausg. Springer-Verlag, Berlin, Heidelberg, New York, 2001. ISBN: 3-540-67777-1. S. 34.
[8] Ruhland, N.: Druckgießen für Praktiker. 1. Aufl . Gießerei-Verlag, Düsseldorf, 2003. S. 25.
[9] Brunhuber, E.: Praxis der Druckgußfertigung. 3. Aufl . Fachverlag Schiele und Schön, Berlin, 1980. S. 15, 19.
[10] Ostermann, F.: Anwendungstechnologie Aluminium. 2. Aufl . Springer-Verlag, Berlin, Heidelberg, New York, 2007. S. 197.
[11] Leis, W.: Wärmeübertragung beim Druckgießen. Fachtagung Gießereikolloquium, Hochschule Aalen, 2008.
[12] Müller, E.; Engelmann, J.; Löffl er, T., u. a.: Energieeffi ziente Fabriken planen und betreiben. 1. Aufl . Springer-Verlag, Berlin, 2009. S. 122.