Energieeffizienzsteigerung im Speisersystem - ECO-Speiser mit erweiterten Einsatzmöglichkeiten
Von Jörg Schäfer, Thomas Schäfer, Grevenbroich, Thomas Baginski, Leipzig
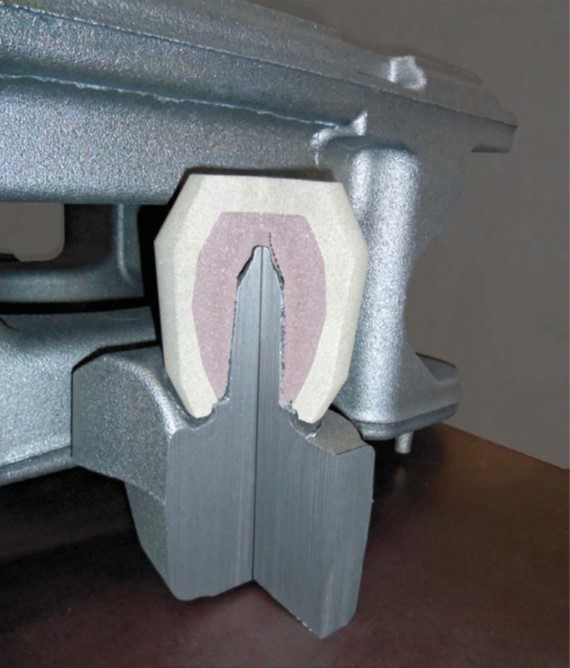
Positionierung eines platzoptimierten ECO-Speisers im Kern mit dünner Außenwand
Erschienen in GIESSEREI 08/2013
Dem globalen Trend und der Erforderlichkeit, Ressourcen effizienter zu nutzen sowie Rohmaterialien und Hilfsstoffe hinsichtlich ihrer Leistungsfähigkeit zu optimieren, kann sich auch die Gießerei- und deren Zuliefererindustrie nicht verschließen. Vor dem Hintergrund der Energieintensität der Produktionsprozesse in Gießereien können große Potentiale im Bereich der Energieeffizienz gefunden werden. Neben dem Schmelzen wird an verschiedenen Stellen im Herstellungsprozess zusätzliche Energie benötigt und entsprechend zugeführt. Einer der Hauptpunkte im Prozess, an dem zusätzliche Energie zugeführt wird, ist das Speisersystem. Neben den wirtschaftlichen Aspekten eines modernen Speisers mit optimiertem Energiehaushalt gibt es auch anwendungstechnische Vorteile eines solchen Speisersystems, die neue Möglichkeiten bieten, komplexe Gussgeometrien prozesssicher speisen zu können.
Die Erstarrungslenkung erfolgt heute vorwiegend mit exothermen Speisereinsätzen, die das Speisungsmetall punktuell aufheizen und somit die Speisung von relevanten Knotenpunkten des Gussteils ermöglichen. Hierbei werden dem Prozess einerseits zusätzliche Energie durch die exotherme Reaktion des Speisermaterials zugeführt als auch zusätzliches Flüssigmetall zur Speisung im Speisersystem bereitgestellt. Im Rahmen der GIFA 2011 stellte die GTP Schäfer Gießereitechnische Produkte GmbH, Grevenbroich, eine neue Produktstudie vor: Ein Speisersystem mit optimiertem Energiehaushalt, den ECO-Speiser. Die Zuführung von zusätzlicher Energie durch das Speisersystem wird minimiert und gleichzeitig die Produkteffizienz gesteigert.
Anwendungsbereiche von Speisereinsätzen in der modernen Serienfertigung
In den letzten Jahren sind die Anforderungen an die Gießereien seitens der Endkunden, immer komplexere Teilgeometrien in der Serienproduktion prozesssicher darzustellen, deutlich gestiegen. Grund für die Zunahme der Komplexität ist – neben der Übernahme von zusätzlichen Funktionen und Aufgaben der Bauteile im Gesamtsystem – die kontinuierliche Gewichtsreduktion zur Optimierung des Energieverbrauchs. Dabei spielt heute auch die Anwendung der Bionik eine große Rolle. Dank der Strukturoptimierung durch Simulation können Konstruktionsprinzipien der Natur in bionisches Design der Gussteile übertragen werden.
Im Lkw-Bereich wird das Ziel der Gesamtgewichtsreduktion konsequent vorangetrieben, um eine höhere Energieeffizienz, eine Minderung des Schadstoffausstoßes und eine Lärmminimierung zu erreichen. Auf der Werkstoffseite ist vor allem das hochsiliciumhaltige Gusseisen mit Kugelgraphit ein wachsender Anwendungswerkstoff. Dieser zeichnet sich durch eine höhere Belastbarkeit, bessere Bearbeitbarkeit und eine gleichmäßige Härteund Festigkeitsverteilung im Bauteil aus. Durch die Optimierung von Konstruktion und Werkstoff sollen neben den Produktionskosten vor allem die Betriebskosten (Kraftstoffverbrauch) reduziert werden, wobei gleichzeitig die mechanische Beanspruchung der Bauteile weiter zunimmt.
Um diese eigentlich gegensätzlichen Zielvorgaben parallel zu erreichen, bedienen sich die Konstrukteure einer Konstruktionsweise mit minimalen Wanddicken, wobei das Bauteil an den festigkeits- und montagerelevanten Stellen punktuell verstärkt wird. Durch diese Konstruktionsweise werden zusätzliche Knotenpunkte im Gussstück geschaffen, die bei der Auslegung des Speiser- und Anschnittsystems entsprechende Berücksichtigung finden müssen. Während einfache Bauteile mit nur wenigen und teilweise zusammenhängenden Knotenpunkten durch ein bis zwei Seitenspeiser gespeist werden können, weisen die o. g. komplexen Gussteile eine deutlich höhere Anzahl an Knotenpunkten auf, die entsprechend punktuell gespeist werden müssen.
Bei der Serienfertigung dieser Gussteile werden daher zunehmend Kopfspeiser mit entsprechendem Zubehör eingesetzt. Die Speiser werden unmittelbar auf den relevanten Knotenpunkten positioniert, da hier der letzte Punkt der Erstarrung erreicht und die Lunkerbildung aufgrund der Schrumpfung des Werkstoffes (5 bis 7 %) eintreten wird. Beim Formfüllen werden die meist am höchsten Punkt in der Gießform sitzenden Speiser ebenfalls mit Eisen gefüllt. Aufgabe des Speisers ist es, durch eine punktuelle Beeinflussung des Erstarrungsverlaufs den letzten Punkt der Erstarrung vom Gussteil weg in den Speiser zu verlagern.
Effizienzentwicklung der Speisersysteme im Zeitverlauf
Hinsichtlich der Effizienz der in der Gießerei-Industrie eingesetzten Speiser wurde diese in den letzten drei Jahrzehnten bereits deutlich gesteigert. Bild 1 zeigt einen Vergleich der Aussaugbarkeit der klassischen Speisersysteme. Bei der Einführung von Gusseisen mit Kugelgraphit (EN-GJS) in den Gießereien wurden ausschließlich Natur- oder Sandspeiser eingesetzt, deren Aussaugbarkeit 10 bis 15 % beträgt. Um ein Gussteil von 20 kg zu speisen, müssen bei Zugrundelegung einer Schrumpfung von 5 % pro kg 7 bis 10 kg Flüssigmetall im Speiser zur Verfügung gestellt werden. Allein durch den Speiser wird die Ausbringung in diesem Beispiel um 30 % reduziert. Das Speiserrestmaterial wird dem Schmelzprozess wieder zugeführt und muss erneut unter Einsatz von Energie und Legierungsmitteln für das Gießen vorbereitet werden.
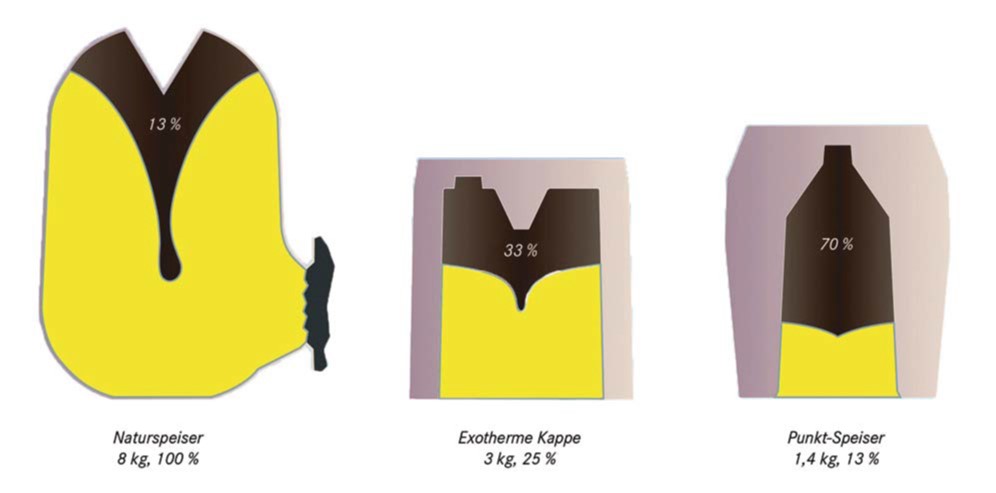
In den 1970er-Jahren wurden isolierende und später auch exotherme Kappen eingesetzt, die mit 20 bis 25 % eine Verbesserung der Aussaugbarkeit zeigten und die Ausbringung der Gießereien erhöhten. Neben der höheren Effizienz der Kappen hatten diese den Vorteil, dass sie zumindest auf bestimmten Teilgeometrien, zum Beispiel geraden Flächen, als Kopfspeiser eingesetzt werden konnten. Jedoch wurde auch die Effizienz der Seitenspeiser durch den zusätzlichen Einsatz von isolierenden oder exothermen Kappen erhöht.
Seit den 1990er Jahren werden zunehmend kompakte, hochexotherme Speisereinsätze mit Brechkernen eingesetzt. Mit einer Aussaugbarkeit von 60 bis 70 % sind diese Speiser den zuvor beschriebenen Speisereinsätzen weit überlegen. Das Zubehör kann hierbei verschiedene Aufgaben übernehmen. Je nach Legierung und Teilgeometrie soll es die Speisung zusätzlich unterstützen (z. B. durch zusätzliche Beheizung des Speiserhalses durch exotherme Reduzierplatten) oder die Putzkosten in der Serienfertigung durch eine Reduzierung des Speiserhalsquerschnitts (Quarzsandbrechkern) minimieren.
Heute verwendete Speisermassen
Je nach Anwendungsfall und Präferenz des Kunden können heute drei verschiedene Arten von Speisermassen unterschieden werden:
- Isolierende Speisermassen: Hierbei wird die Speiseraußengeometrie aus einem isolierenden Material erstellt, dessen Wärmeleitfähigkeit deutlich geringer als die des Quarzsandes der Grünsandform ist. Durch das Isolationsmaterial wird die Energie (Wärme) länger im Speiserinneren gehalten und somit die Erstarrung des Flüssigmetalls im Speiser verzögert. Der Speiser kann somit länger Material an das Gussstück bzw. den Knotenpunkt abgeben.
- Exotherme Speisermassen: Die heute am meisten verbreiteten Speisermassen weisen leicht- bis hochexotherme Eigenschaften auf. Durch den Kontakt der Schmelze mit dem Speisermaterial wird die exotherme Reaktion, welche auf dem Goldschmidt-Verfahren beruht, initialisiert. Durch die exotherme Reaktion der Speisermasse wird dem Metall im Speiser im Verlauf des Erstarrungsprozess des Gussteils zusätzliche Energie zugeführt, wodurch die Erstarrung verzögert wird. Durch die Speisergeometrie und durch modulgerechte exotherme Eigenschaften kann eine deutlich höhere Aussaugung des Speisers gewährleistet werden.
- Exotherm-isolierende Speisermassen: Bei dieser Art der Speisermasse handelt es sich um eine Kombination der beiden vorher genannten Speisermassen. Hierbei werden einer exothermen Speisermasse isolierende Füllstoffe beigemischt. Die Speisermasse verfügt somit über die Fähigkeit, dem Speisermetall aufgrund der exothermen Reaktion zusätzliche Energie zuzuführen. Parallel bietet die Speisermasse nach Beendigung der exothermen Reaktion einen höheren Isolierwert.
Analyse der Energieeffizienz heute verwendeter Speisersysteme
Im Vorfeld der folgenden Analyse ist voranzustellen, dass die heute verwendeten Speisersysteme für die großtechnische Serienproduktion ein bereits weit auf den Produktionsprozess optimiertes Leistungspaket darstellen. Durch die kontinuierliche Weiterentwicklung der Anwendungstechnik mit dem Ziel, die Speisereinsätze möglichst nah an den relevanten Knotenpunkten zu positionieren und zugleich einen Beitrag zur Optimierung der Putzkosten zu leisten, konnte dem Gießer in den letzten Jahren ein breites Feld an flexiblen und auf den individuellen Anwendungsfall abstimmbaren Speisersystemen zur Verfügung gestellt werden.
Als relevantes Maß für die Effizienz eines Speisersystems kann neben dem Modul eines Speisers dessen Aussaugbarkeit identifiziert werden. Dies ist für den Gießer die wohl relevanteste Größe im Prozess, da durch die Ausbringungsquote des Gießsystems die Kapazität und Wirtschaftlichkeit des gesamten Produktionsprozesses entscheidend beeinflusst wird. Ist der Gießer in der Lage seine Ausbringung zu steigern, kann er die vorhandenen Produktionskapazitäten – insbesondere Schmelzbetrieb, Formanlage, Putzerei – besser ausnutzen und somit bei gleichem Einsatz an Produktionsfaktoren, also Maschinen- Energie- und Personaleinsatz, mehr „guten Guss“ produzieren. Demzufolge setzen die Gießereien heute zunehmend mehr hochexotherme Speisereinsätze ein.
Wie bereits im vorangegangenen Teil dieses Beitrages beschrieben, gibt die exotherme Speisermasse Energie ab und führt diese dem Gießprozess gezielt punktuell zu. Betrachtet man den Temperaturverlauf im Umfeld des Speisers genauer, so stellt man fest, dass die Energie der exothermen Reaktion nur zu einem bestimmten Anteil an das Speisermetall abgegeben wird. Der exotherme Speisereinsatz ist umgeben vom Formsand, der eine relativ hohe Wärmeleitfähigkeit besitzt, soll er doch die Erstarrung des Gussteils möglichst schnell gewährleisten.
Vergleicht man die in Bild 2 schematisch gezeigten relevanten Oberflächen, also die Kontaktfläche des Flüssigmetalls im Speiserinneren, durch die das Flüssigmetall Energie aufnehmen kann, mit der Kontaktfläche des Speisers außen mit dem Formsand, also der Kontaktfläche, mit welcher der Speiser Energie an den Formsand abgibt, so stellt man fest, dass diese deutlich größer ist und somit ein hoher Anteil der exothermen Energie in den Formsand abgeleitet wird. Es stellt sich somit die Frage, ob und wie die exotherme Energie effizienter genutzt bzw. in Richtung des Speiserinneren gelenkt werden kann.
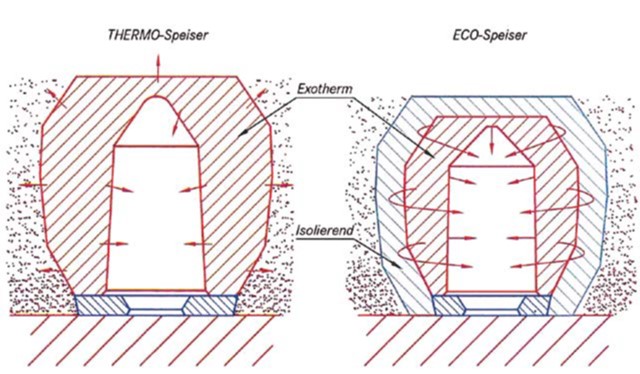
Optimierungsansatz: partielle/ gelenkte Isolation
Vor dem Hintergrund der oben beschriebenen Energieabgabe des exothermen Speisers an den Formsand ist es das Ziel, ein Speisersystem zu konzipieren, das einen höheren Anteil seiner Energie für die Speisung des Gussstücks – also der Erstarrungslenkung des Flüssigmetalls im Speiser – zur Verfügung stellt und weniger Energie an den Formsand abgibt. Dies kann nur erreicht werden, indem die beiden möglichen Eigenschaften von Speisermassen – Exothermie und Isolation – miteinander kombiniert werden. Die Schwierigkeit besteht darin, dass bei den heute gebräuchlichen exotherm-isolierenden Speisermassen die Isolationswirkung aufgrund der exothermen Bestandteile der Mischung minimiert wird, da exotherme und isolierende Bestandteile gemischt werden. Des Weiteren fordert ein möglicher Optimierungsansatz, dass die Energieabgabe in das Speiserinnere gelenkt wird. Als Ergebnis ist festzuhalten, dass ein solches Prinzip nicht innerhalb einer homogenen Speisermasse umsetzbar ist.
Umsetzung der partiellen/ gelenkten Isolation im Speisersystem
Eine mögliche Umsetzung des oben beschriebenen Prinzips der partiellen bzw. gelenkten Isolation erfordert, dass die Speisermasse zwei Eigenschaften gleichzeitig aufweist. Zum einen sollte die Masse über hochexotherme Eigenschaften verfügen, um somit möglichst viel Energie an das flüssige Metall im Speiserinneren abzugeben, zum anderen dabei jedoch eine zu hohe punktuelle Erhitzung des Metalls (Verkochen) verhindern. Des Weiteren sollte die Masse eine geringe Wärmeleitfähigkeit aufweisen, um möglichst wenig Energie an den Formstoff abzugeben.
Oben wurde bereits herausgestellt, dass eine solche Speisermasse nicht homogen sein kann und folglich modular aufgebaut werden muss. Auf dieser Basis wurde in Zusammenarbeit zwischen GTP Schäfer und Thomas Baginski von der Georg Fischer GmbH in Leipzig der sogenannte ECOSpeiser entwickelt. Das ist ein modular aufgebauter Speiser, der aus zwei Speisermassen besteht. Die innere Schicht besteht aus einem hochexothermen Speisermaterial, das die Erstarrung des Flüssigmetalls im Speiser – wie bei den heute bereits verwendeten Speisereinsätzen – mit Hilfe der exothermen Energie verzögert bzw. lenkt. Die innere Kontaktfläche des Speisereinsatzes ist hierbei der Übergabepunkt der Energie an das Flüssigmetall. Um die Energieabgabe des exothermen Materials an den Formsand zu verringern, wurde das exotherme Speisermaterial zusätzlich mit einer isolierenden Speisermasse ummantelt. Diese Isolation bewirkt, dass die Energieabgabe der exothermen Reaktion an den Formstoff reduziert bzw. minimiert wird.
Erste Analyse der Energieeffizienz
Durch die Verringerung der Energieabgabe des Speisers durch die äußere Speiseroberfläche an den Formstoff kann bei gleicher Außengeometrie ein höherer Speisermodul dargestellt werden. Im vorliegenden Beispiel konnte mit einem ECO-Speiser mit geringerem Volumen und kleinerer Exothermität eine Modulplatte dichtgespeist werden, die mit einem rein exothermen Speiser mit leicht größerer Außengeometrie ein klares Lunkerbild im Übergang Speiserhals/ Modulplatte zeigt. Die in Bild 3 gezeigten Simulationsergebnisse des modular aufgebauten ECO-Speisers in Vergleich zu einem herkömmlichen Speiser konnten in den Versuchsreihen bestätigt werden (Bild 4).
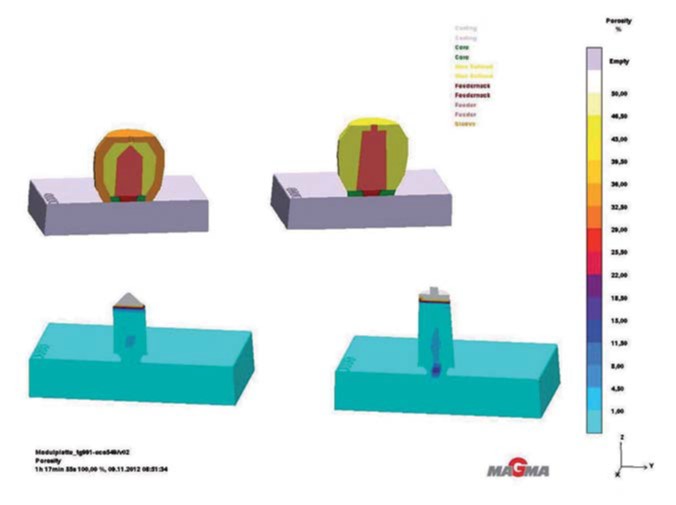
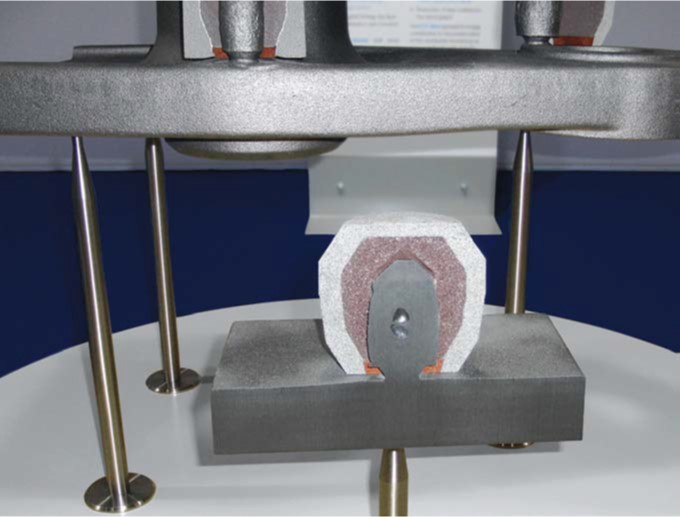
Erweiterung des Anwendungsbereichs dieser Speisereinsätze
Aufgrund des höheren Moduls des Speisers bei gleicher Speisergeometrie werden neue Anwendungsmöglichkeiten für Speisersysteme erschlossen. Zur optimalen Plattennutzung – und somit zur Steigerung der Prozesseffizienz – können Teile des Speisersystems in das Innere der Kernpakete verlagert werden, anstatt diese durch platzraubende Seitenspeiser darzustellen. Erstmals ist es gelungen, einen Speiser mit exothermer Wirkung ganz dicht an der Gussstückkontur zu platzieren (Bild 5).
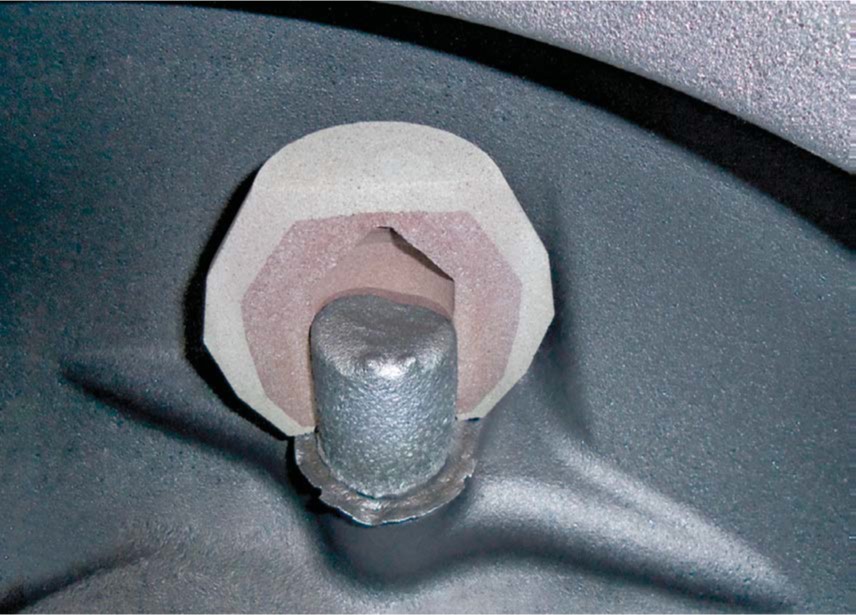
Vor der Einführung dieses Speisers wurde der Einsatz im Kern teilweise durch zwei Faktoren eingeschränkt. Einerseits bietet das Kerninnere nur sehr beschränkten Platz zur Positionierung eines Speisers, der auch das modulgerechte Volumen aufweist. Zum anderen werden die Kerne oder innen liegende Formpartien durch den exothermen Speisereinsatz in Verbindung mit dem Flüssigmetall im Speiser punktuell stark aufgeheizt. Die hierdurch entstehenden punktuellen Aufheizungen bilden sogenannte Nicht-Kühlflächen, die den Modul um den Kern herum vergrößern. Zudem können diese eine Sekundärlunkerung begünstigen, da die Bildung einer geschlossenen Gusshaut an den genannten Kernpartien unterbunden wird.
Wie oben bereits erläutert, kann durch den Einsatz eines ECO-Speisers eine Reduzierung des Platzbedarfs gewährleistet werden. Des Weiteren kann durch die äußere Isolation des exothermen Speisereinsatzes im Inneren eine Aufheizung des Kernpakets oder angrenzender Gusspartien vermieden oder stark vermindert werden.
Aber auch auf der Modellplatte bietet der Speiser große Vorteile. Wenn z. B. Speiserkalotten sehr nah an der Gusskontur liegen, müssen sie oftmals vom Gussstück weggerückt werden. Dabei nimmt man eine Verlängerung des Speiserhalses in Kauf. Dies führt oft zum Abfrieren des Halses und erzeugt Lunker im Gussteil. Mit dem ECO-Speiser hat man die Möglichkeit, sehr nah an die Gusskontur zu gehen, da die Aufheizung der Gusskontur gering ist. Dieser Vorteil wird auch mit Kopfspeisern in engen Gusspartien auf dem Modell erreicht.
Ausblick zum ECO-Speiser
Bei den zuerst für Georg Fischer Leipzig konzipierten Speisern wurde nach den ersten praktischen Proben für weitere geplante Speiser eine Versuchreihe am Computer simuliert. Hier lassen sich ohne großen Aufwand geeignete Geometrien für die Speiser entwickeln. Diese werden dann auf speziellen sogenannten Modulplatten praktisch beprobt. Dabei wurden sogar Modulplatten eingesetzt, die jeweils 0,1 cm größer sind. Durch diese feine Abstimmung konnten die Computerergebnisse mit den praktischen Versuchen verglichen werden.
Zusammenfassung und Fazit
Der ECO-Speiser kann zu einem deutlichen Mehrwert zur Steigerung der Energieeffizienz in Speisersystemen bzw. Gießereien beitragen. Neben der Möglichkeit, wesentliche Faktoren wie Produktivität, Kreislaufmaterial und Prozesssicherheit positiv zu beeinflussen, bietet dieses innovative Speisersystem dem Gießer bis dahin nicht erschlossene Einsatzmöglichkeiten. So können Speiser viel näher an kritischen Modellkonturen positioniert werden sowie an platzkritischen Stellen eine modulgerechte Speisung gewährleisten. Die oben beschriebene Zusammenarbeit zwischen GTP Schäfer und Georg Fischer Leipzig unterstreicht die Notwendigkeit der partnerschaftlichen Entwicklung von innovativen Lösungsansätzen zur kontinuierlichen Weiterentwicklung und Verbesserungen der Prozesse durch Gießerei und Zulieferer. Nach der Serieneinführung in verschiedenen Gießereien wird das Speisersystem nun weiter optimiert.
Jörg Schäfer und Thomas Schäfer, GTP Schäfer Giesstechnische Produkte GmbH, Grevenbroich; Thomas Baginski, Georg Fischer GmbH, Leipzig