Energie- und Rohstoffeinsparung durch konsequente Nutzung der Gießprozesssimulation
Von Jörg C. Sturm, Aachen
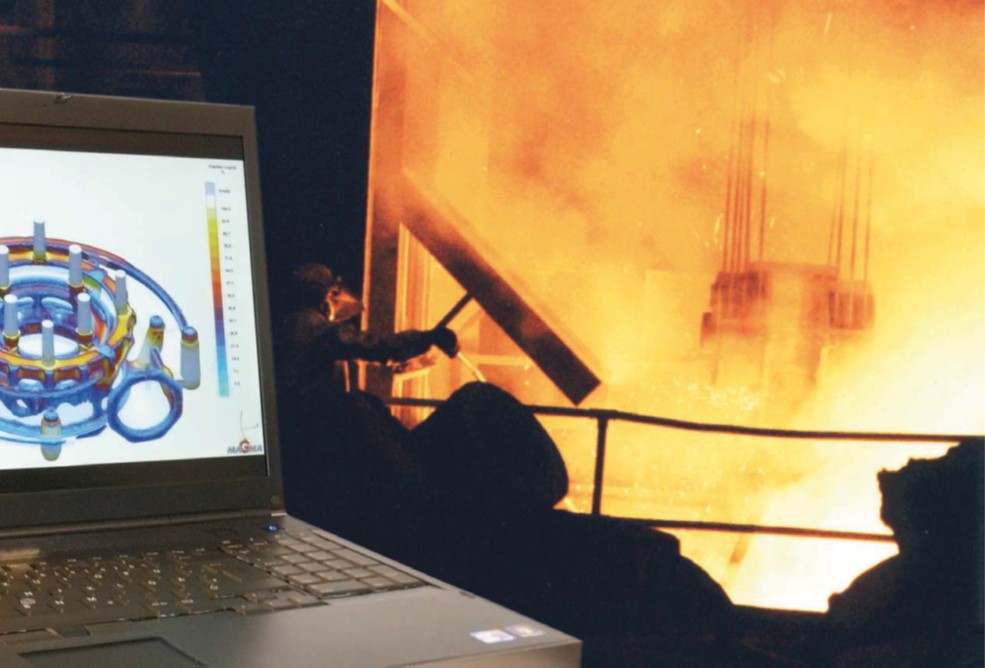
Erschienen in GIESSEREI 06/2011
Einleitung
Für die Herstellung einer t Gusseisen sind im Durchschnitt etwa 1000 kWh Strom und 100 kg Koks notwendig, deren Nutzung mit entsprechenden Emissionen zwischen 1500 und 2000 kg CO2/t gutem Guss verbunden sind [1]. Der mittlere Energieeinsatz für Druckguss beträgt ca. 5600 kWh pro t gutem Guss, was CO2-Emissionen von ca. 2500 kg pro t entspricht [2]. In Deutschland werden 5,9 Mio. t Metall erschmolzen und vergossen (4,8 Mio. Stahl und Eisen, 1,1 Mio. t Nicht-Eisen-Werkstoffe [3]). Wenn man beispielhaft diese gemittelten Zahlen (2000 kWh pro t guter Guss, 563 g CO2/ kWh Strom in Deutschland [4]) nutzt, ergeben sich überschlägig ein jährlicher Energieverbrauch der Industrie von ca. 11 Mrd. kWh und entsprechende Emissionen von 6,5 Mio. t CO2. Betrachtet man diese Zahlen, wird klar, dass energiesparende „grüne“ Gießereien viel zum Klimaschutz beitragen können.
Natürlich beschäftigt sich die Gießereibranche allein aus betriebswirtschaftlicher Motivation schon lange damit, energieschonende Gießprozesse einzusetzen und weiterzuentwickeln. Denn der Energieverbrauch bildet einen massiven Kostenblock in den Betrieben. Seine Größe ist für Gewinn und Wettbewerbsvorteile entscheidend.
Der Hauptfokus der Energiesparmaßnahmen liegt vielfach in der Optimierung der energetischen Vorgänge um den Schmelzvorgang und Maschinenpark herum: effizientere Öfen mit höheren Wirkungsgraden, Auskleidungsmaterialien mit höheren Isolierleistungen, die Nutzung von Abwärme oder optimierte Versorgung mit Druckluft gehören zu den aktuellen Forschungsfeldern.
Weniger Energie- und Rohstoffeinsatz durch Gießprozesssimulation
Einen wichtigen Beitrag zur energieeffizienten Gießerei kann der konsequente Einsatz der Gießprozesssimulation leisten. Sie hilft auf verschiedene Art und Weise, den Materialeinsatz und damit auch die notwendige Energie beim Gießen zu reduzieren. Ein großer Teil des erschmolzenen Materials geht in der Energiebilanz des einzelnen Gussteils durch Kreislauf oder Abbrand verloren. Lässt sich dieser Anteil vermindern und das Ausbringen damit erhöhen, spart dies erhebliche Mengen an Energie. Das Institut für Gießereitechnik IfG, Düsseldorf, hat in seinem Fachbericht „Der energieeffiziente Gießereibetrieb“ errechnet, dass die Steigerung des Ausbringens von 60 auf 70 % bei einer Monatsproduktion von 2000 t gutem Guss beim Schmelzen im Induktionsofen rund 300 000 kWh Strom pro Jahr einspart [1]. Energie kann aber darüber hinaus in der gesamten Fertigungskette eingespart werden (Tabelle 1, siehe auch Bild 12). Nur die konsequente Optimierung aller „energetischen Baustellen“ führt volkswirtschaftlich zu reduzierten CO2-Emissionen und sichert den Gießereien Kosten- und Wettbewerbsvorteile.
Tabelle 1: Spezifische mittlere Energieverbräuche für Eisen- und Stahlguss für unterschiedliche Fertigungsschritte. Die Prozesse im Schmelzbetrieb, beim Form en und in der Wärmebehandlung eignen sich am besten zur Optimierung mit der Gießprozesssimulation ([1] modifiziert).
Prozess | Eisen (kWh/t) | Stahl (kWh/t) |
Schmelzbetrieb | 944 | 1000 |
Wärmebehandlung | 42 | 514 |
Pfannenwirtschaft | 214 | 214 |
Formen | 171 | 120 |
Putzerei | 128 | 171 |
Der analytische Blick in die Gussform
Die Idee zur Gießereiprozesssimulation als Werkzeug zur Energie- und Kosteneinsparung wurde in Aachen „geboren“. Bereits in den frühen 1980ern wurde der Wert dieses Ansatzes auch von der Deutschen Forschungsgemeinschaft erkannt und die Grundlagen im Rahmen eines Sonderforschungsbereiches an der RWTH Aachen zur „Energie- und Rohstoffeinsparung von Fertigungsverfahren“ gefördert [5].
Mit der Einführung der Gießprozesssimulation in die Gießereibetriebe Ende der 1980er-Jahre wurde es erstmals möglich, in die „Blackbox“-Gussform virtuell hineinzuschauen und die Gießtechnik, die Verfahrensbedingungen und Formen auf der Basis handfester Daten vor dem Abguss zu optimieren. Die primären Ziele der Gießprozesssimulation liegen in der Entwicklung wirtschaftlicher, kostensparender Gießprozesse, um Gussteile mit einer höheren Qualität sicher zu produzieren. Damit einher geht das Ziel der energieund kostensparenden Verbesserung des Materialeinsatzes. Eine systematische Nutzung der Gießprozesssimulation bereits während der Gussteil- und Prozessentwicklung und in der Prototypenphase, die zur Reduzierung von Ausschuss und Nacharbeit führen, liefert weitere Einsparungen. Darüber hinaus können heute Energieeinsparungen durch eine höhere Produktivität, durch verbesserte Formtemperierung sowie in nachgelagerten Fertigungsschritten, wie z. B. der Wärmebehandlung realisiert werden.
Zusätzliche geldwerte Vorteile ergeben sich mit der Simulation durch die Verkürzung von Produkt- und Prozessentwicklungszeiten, die Verbesserung der Kommunikation (intern und mit dem Kunden), sowie durch Mitarbeiterqualifizierung und transparente Dokumentation des Unternehmens-Know-hows.
Programme zur Gießprozesssimulation haben sich in den vergangenen 30 Jahren in vielen Gießereien von einem Werkzeug zur Fehlererkennung und Überprüfung der Gießtechnik hin zu einer akzeptierten Methodik der konsequenten Effizienzsteigerung und Absicherung von robusten Prozessen weiterentwickelt. Dies liegt natürlich auch an dem Vertrauen, das die Fachleute heute in die Ergebnisse der Simulation setzen. Daher wird die Vorhersage des Prozesses inzwischen vielfach wie eine „virtuelle Versuchsgießerei“ genutzt, bei der die Gießtechnik nicht nur einmal nachgerechnet wird, sondern im Vorfeld der Fertigung durch Parameter- und Sensitivitätsstudien wichtige Einflussgrößen auf stabile Prozesse ermittelt werden. Dies schafft auch die Voraussetzungen für das Verständnis der wichtigen Einflussgrößen auf die Energie- und Materialeffizienz in der Gießerei. Beispiele hierzu werden im Folgenden vorgestellt.
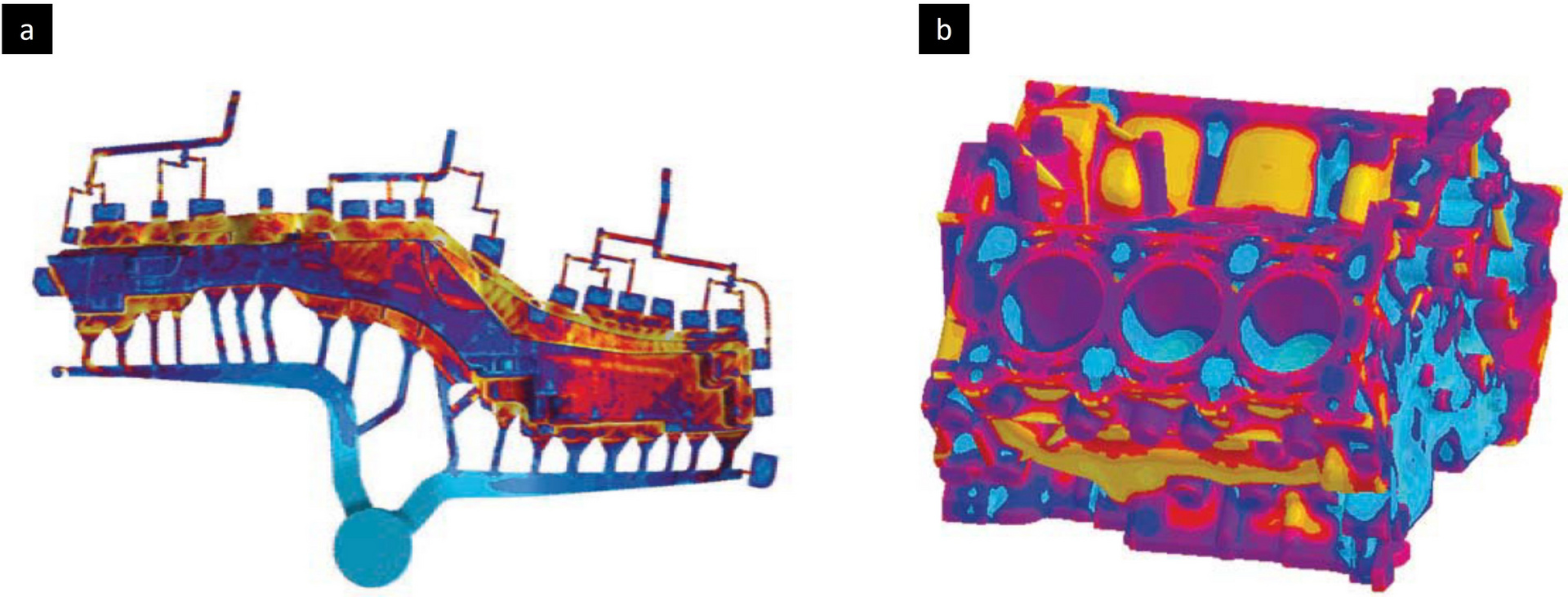
Konstruktion energiesparender Gussteile
Leichtbau ist sowohl in der Automobilindustrie als auch im Maschinenbau eine Schlüsseltechnologie. 100 kg Gewichtseinsparung im Fahrzeug bedeuten eine Treibstoffreduzierung von 0,2 bis 0,4 l/100 km. Bei einer Gesamtfahrleistung von 250 000 km können damit pro Fahrzeug bis zu 1000 l Benzin oder 2.3 t CO2 eingespart werden. Auch der Maschinenbau muss in Leichtbaukategorien denken. So wird das zunehmende Gewicht der Gondeln zukünftiger großer Offshore-Windkraftturbinen zum kritischen Machbarkeits- und Erfolgsfaktor.
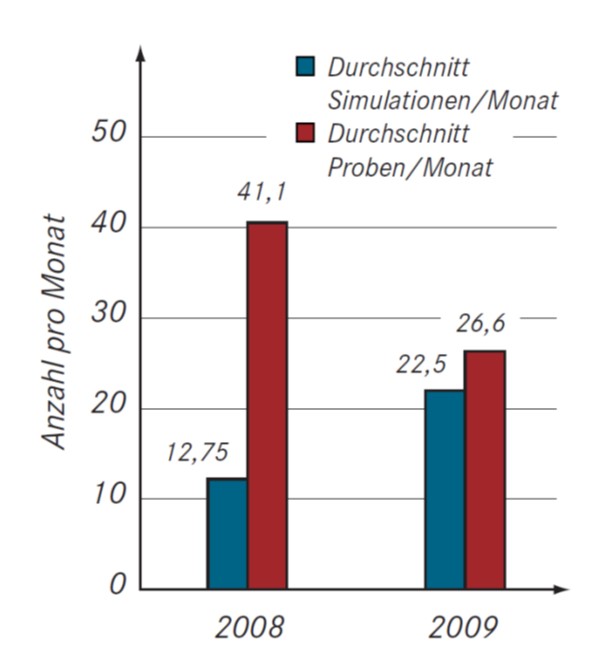
Durch Einsatz moderner Simulationsprogramme ist es möglich, das gesamte Potential gegossener Werkstoffe und der dafür genutzten Fertigungsverfahren für das Gussteil auszunutzen. Simulationsprogramme sind heutzutage in der Lage, Einflüsse von Fertigungsparametern auf die Gussteilqualität sehr genau vorherzusagen und können somit auch frühzeitig zur Gewichtsreduzierung eingesetzt werden. Die gelieferten Informationen von Simulationsprogrammen unterstützen sowohl den Konstrukteur bei einer gießgerechten und gewichtsoptimierten Auslegung des Bauteils als auch den Gießer hinsichtlich einer prozesssicheren und kostengünstigen Fertigung.
Der Konstrukteur legt sein Bauteil zunächst belastungsgerecht aus. Gießtechnisches Know-how kommt häufig erst bei der Entscheidung für einen Zulieferer ins Spiel. Zu diesem Zeitpunkt ist die Geometrie des Gussteils häufig schon festgelegt und jede gießtechnisch notwendige Änderung wird sehr aufwendig und erfordert eine zusätzliche kostenintensive Abstimmung. Es gilt der Erfahrungswert, dass bei der Bauteilkonstruktion bereits 80 % der später anfallenden Herstellkosten festgelegt werden. Gerade für Bauteile mit besonderen Anforderungen an Leichtbau kommt dem frühzeitigen Einsatz der Gießprozesssimulation als Informationsquelle eine noch stärkere Bedeutung zu (Bild 1). Durch die Konstruktion bedingte gießtechnische Problemzonen und Qualitätsverluste lassen sich durch zeitnahe Verwendung der Simulation frühzeitig erkennen und gemeinsam mit dem Zulieferer beurteilen. Dies gilt insbesondere bei mehrstufigen Fertigungsabläufen, bei denen der Gießprozess, die Wärmebehandlung und nachgelagerte Bearbeitungsschritte die Eigenschaften des Bauteils im Einsatz bestimmen.
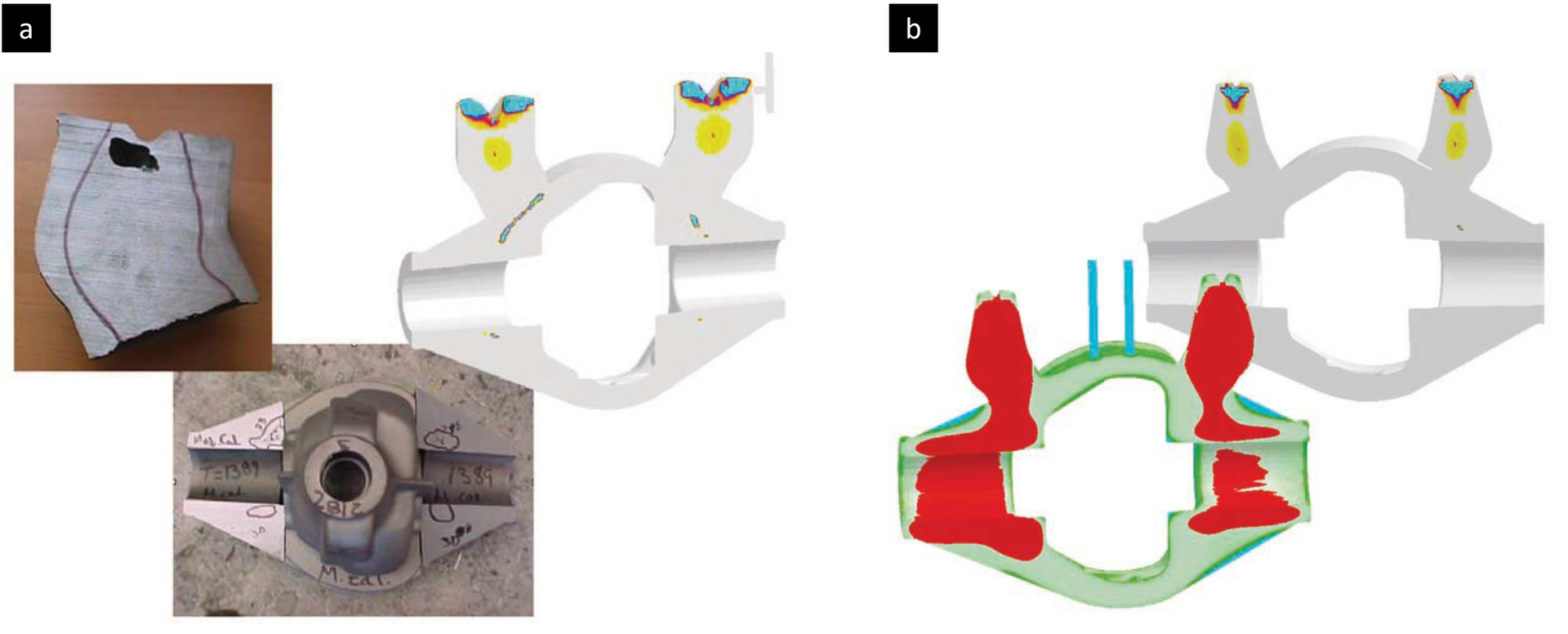
Energieeinsparungen durch Reduzierung von Proben und Versuchsabgüssen
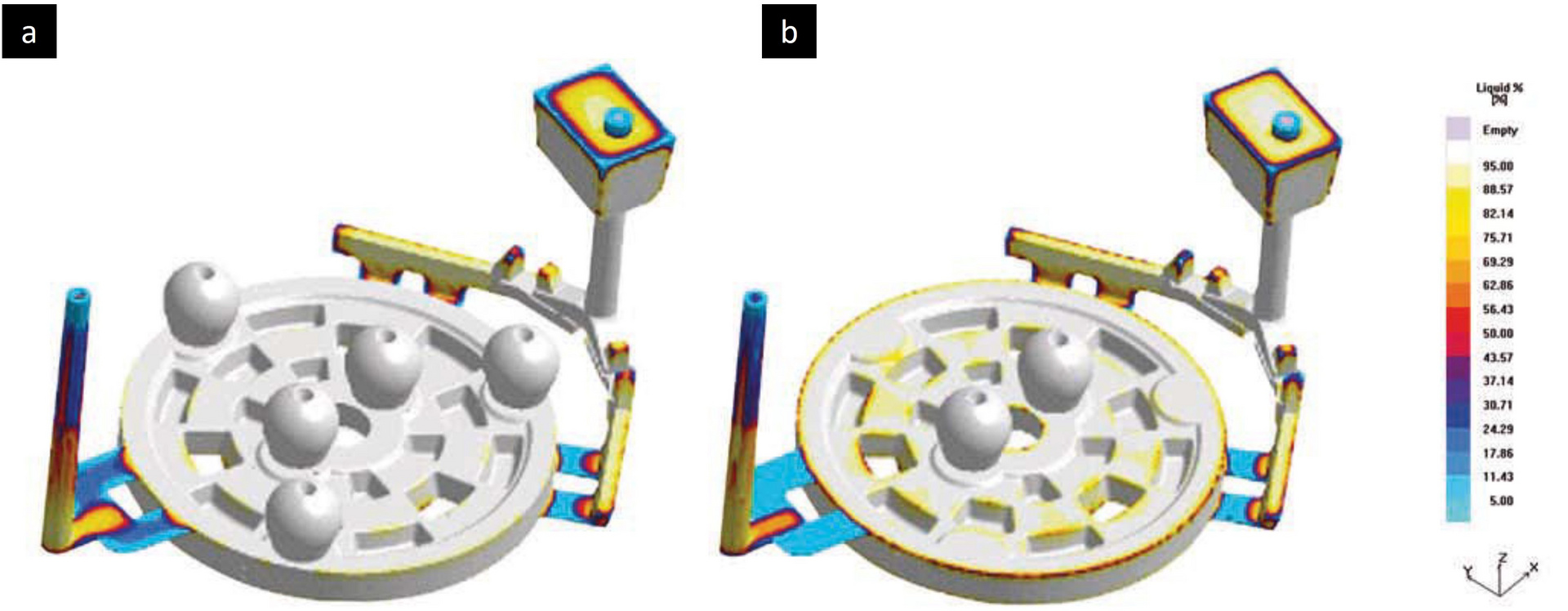
Ohne Gießprozesssimulation muss nach der Konstruktion eines Gussteils der Gießprozess mit vielen aufwendigen Probegüssen entwickelt werden. Die Simulation macht dieses „Herangießen“ an den optimalen Prozessablauf weitgehend überflüssig. Der Fachmann in der Gießerei nutzt die Software, um vor dem ersten Abguss die Fertigungsbedingungen für einen robusten Prozess festzulegen und zu optimieren.
Durch signifikante Reduzierung von Versuchsabgüssen sind bereits die ersten Werkstoff- und Energieeinsparungen realisiert. Eine amerikanische Gießerei hat nach der Einführung der Gießprozesssimulation die Anzahl der Versuchsabgüsse so drastisch reduziert, dass die Kosten für Prototypen um 580 000 US Dollar und Anlaufversuche, die zu keine guten Gussteilen führten, um weitere 208 000 US Dollar vermindert werden konnten [8].
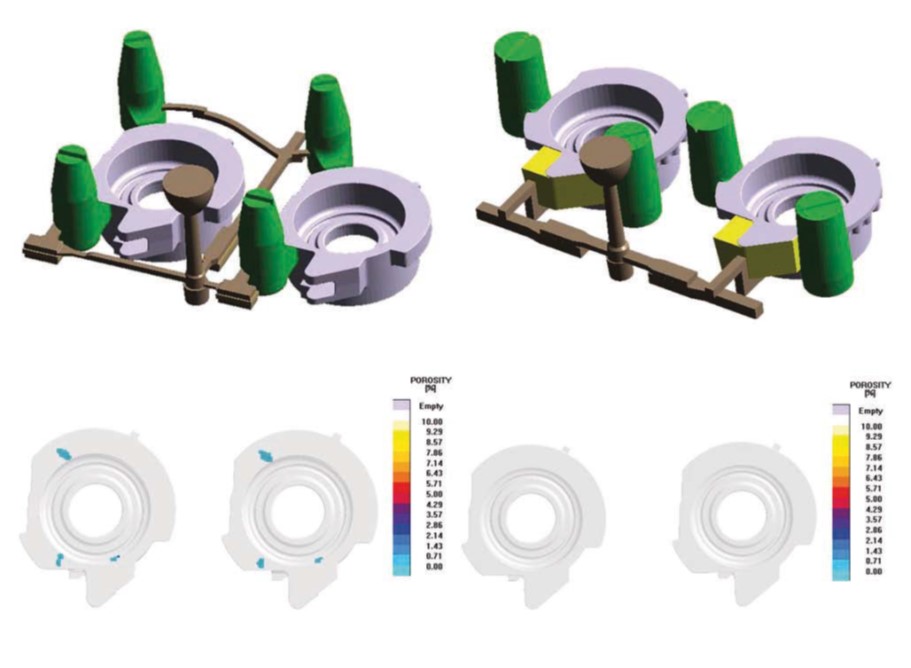
Auch eine namhafte Stahlgießerei nutzt die Gießprozesssimulation unter anderem zur Einschränkung notwendiger Versuchsund Probeabgüsse. Der Vergleich von Simulationsaufwand und Anzahl von Proben zeigt eine klare Korrelation: durch die Intensivierung der Simulationsaktivitäten um 56 % konnte die Anzahl von Probeabgüssen gleichzeitig um 64 % in einem Jahr reduziert werden (Bild 2). Mit simulationsunterstützter gießtechnischer Auslegung von ca. 30 Teilen pro Monat konnte die Gießerei innerhalb eines Jahres den Gesamtausschuss um absolut 2,65 % absenken, was einer Gesamteinsparung von 514 000 US Dollar entspricht [9].
Einführung einer neuen Gießtechnik
Die Einführung einer neuen Gießtechnik ist für jede Gießerei eine Herausforderung und mit Risiken verbunden. Die Chancen für erhöhte Energie- und Materialeffizienz werden gesehen, aber das Fertigungsrisiko und gemachte Terminzusagen führen immer wieder dazu, dass bevorzugt bereits bekannte Vorgehensweisen verfolgt werden.
Während der Fertigung von komplexen Achsgehäusen aus Gusseisen mit Kugelgraphit zeigte sich in einer Gießerei ein speisungsbedingter Fehler im Gussteil erst bei der nachfolgenden Bearbeitung. Die ersten Simulationsrechnungen zeigten zunächst den Fehler und seine Ursachen auf: die Speisungswege in die kritischen Zonen schnürten zu schnell ab. Durch ein geändertes Speiser-Layout konnte der Fehler behoben werden (Bild 3). Die dadurch notwendige neue Gießtechnik reduzierte zusätzlich das Gießgewicht um 13 kg und die Formfüllzeiten um 2,5 s. Die realisierte Einsparung von 13 t Flüssigmetall pro Jahr entspricht einer Energieeinsparung beim Schmelzen von 12 272 kWh. Darüber hinaus wurde der Speiserhals um 25 % verkleinert, was zu verminderten Putzkosten führte. Das modifizierte Layout führte zu einer um 11 min verminderten Erstarrungszeit und damit zu einer um 15 % höheren Produktivität. Die ursprüngliche Aufgabenstellung war, den Fehler zu beseitigen. Die vorgeschlagene Lösung auf Basis der Simulation führte zu deutlich verminderten Herstellkosten [10].
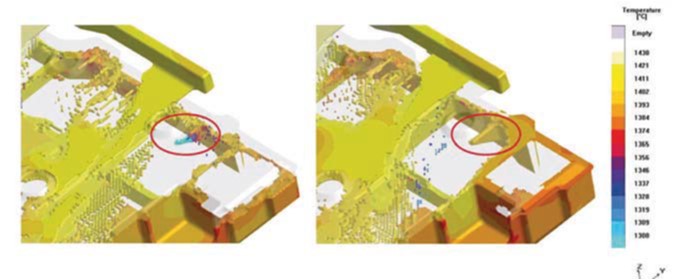
Erweiterung des Anwendungsbereichs dieser Speisereinsätze
Die Umstellung der Gießtechnik eines Stahlgusspumpengehäuses der Otto Junker Edelstahlgießerei, Simmerath, von Seitenspeisern auf Direktgießen mit Filterspeisern wurde nur praktiziert, weil die Machbarkeit durch Ergebnisse der Gießprozesssimulation vorab gezeigt wurde. Dies reduzierte die Menge an notwendigem Flüssigmetall auf 81 % gegenüber der Ausgangssituation. Wesentliche Einsparungspotentiale konnten aber zusätzlich durch verringerte Formzeiten (79 %), Brennzeiten für die Speiser (87 %) und Putzzeiten realisiert werden. Insgesamt wurden die Fertigungskosten um 12 % reduziert [11].
Eine südamerikanische Eisengießerei konnte durch eine mit der Gießprozesssimulation erarbeitete neue, ungewöhnliche Anschnitttechnik das Ausbringen für ein Getriebegehäuse aus Gusseisen mit Kugelgraphit von 62 % auf 67 % erhöhen. Gleichzeitig sank der Gesamtausschuss von 17 % auf 7 %. Bei 24 000 pro Jahr gefertigten Teilen konnten damit nahezu 700 000 kWh eingespart werden, was insgesamt zu Gesamtkosteneinsparungen von 500 000 US Dollar führte [12].

Energie- und Kosteneinsparung durch Speiseroptimierung
Die Gießerei der Heidelberger Druck AG in Amstetten hat allein in einem Jahr die Gießtechnik von 38 laufenden Teilen mit einem Produktionsvolumen von 32 000 Stück pro Jahr mit der gießtechnischen Simulation überprüft und entsprechend modifiziert. Dadurch konnte sie Kreislaufmaterial um 295 t bei einem Gesamtmaterialeinsatz von 1300 t reduzieren. Heidelberger Druck konnte allein in den ersten 18 Monaten der Nutzung der Gießprozesssimulation 100.000 Euro pro Jahr nur an Material- und Energiekosten einsparen [13].
Zum Beispiel wurde auf Grund von Simulationsergebnissen in der Gießerei die Gießtechnik für ein Zahnrad so optimiert, dass statt fünf nur zwei Speiser eingesetzt werden mussten. Dadurch reduzierte sich der Einsatz von Flüssigeisen um 69 kg pro Teil bzw. um 82 t für die gesamte Fertigung pro Jahr, so dass sich pro Teil 32 Euro und pro Jahr 38 000 Euro einsparen ließen (Bild 4).
Der Einsatz der Simulation ermöglichte es auch, anstelle einer Dreifachform für Walzenlager eine Vierfachform zu realisieren und dabei gleichzeitig die Anzahl der Speiser zu reduzieren. Das Ausbringen stieg auf 53 %, die Kosten für die Walzenlager sanken um 2,18 Euro pro Teil.
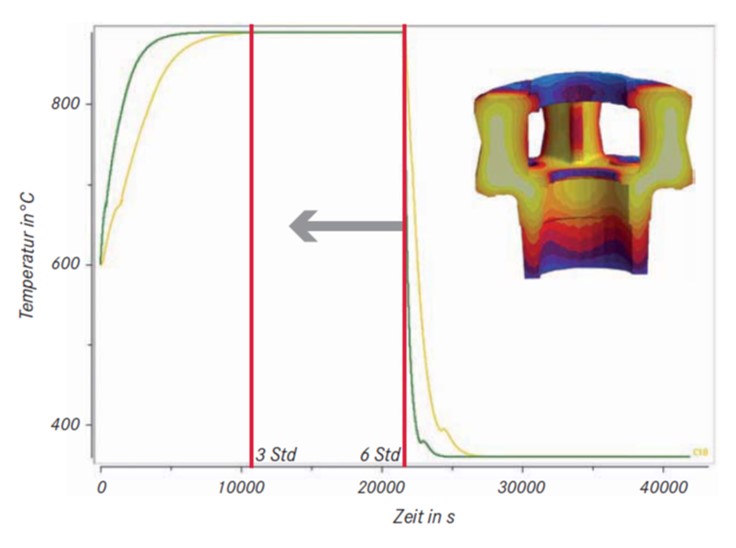
Simulationsgestützte Qualität vermeidet energieintensiven Ausschuss
John Deere, Moline, Illinois/USA, konnte den Ausschuss eines Graugussteils durch eine neue Gießtechnik von 10,3 % auf 1,4 % mit jährlichen Einsparungen von 66 936 US Dollar reduzieren (Bild 5). Gleichzeitig wurde das Ausbringen durch die konsequente Nutzung der Gießprozesssimulation von 58 % auf 64 % erhöht. Dies entspricht verminderten Kosten von 66 600 US Dollar pro Jahr. Insgesamt konnte der Eisenbedarf um 195,6 t reduziert werden, was bei einer ausgelasteten Anlage 274 Formen zusätzlicher Kapazität entspricht. Insgesamt resultierten diese Optimierungen in einer Energieeinsparung von 160 000 kWh pro Jahr. Im Fall einer frühzeitigeren simulationsgestützten Optimierung hätten nach eigener Aussage bereits im ersten Jahr der Produktion 140 000 US Dollar plus Änderungskosten in Höhe von 120 000 US Dollar vermieden werden können.
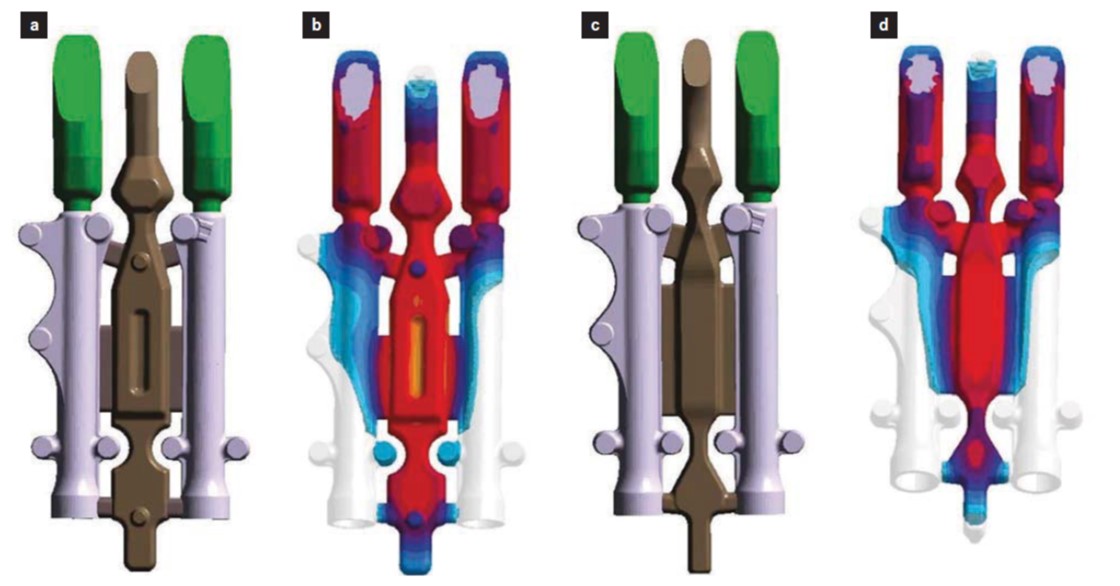
Die simulationsunterstützte Verlegung des Anschnitts reduzierte die Nachbearbeitungskosten für ein Seitenteil in der Gießerei bei Heidelberger Druck AG erheblich: beim ursprünglichen Gussteil führten Temperaturverluste zu einer unvollständigen Füllung der Rippe, wodurch Schweißarbeiten bei 90 % der Rohteile erforderlich waren. Durch Verlegung des Anschnitts wurde eine optimale Füllung erreicht und die Nacharbeit überflüssig (Bild 6).
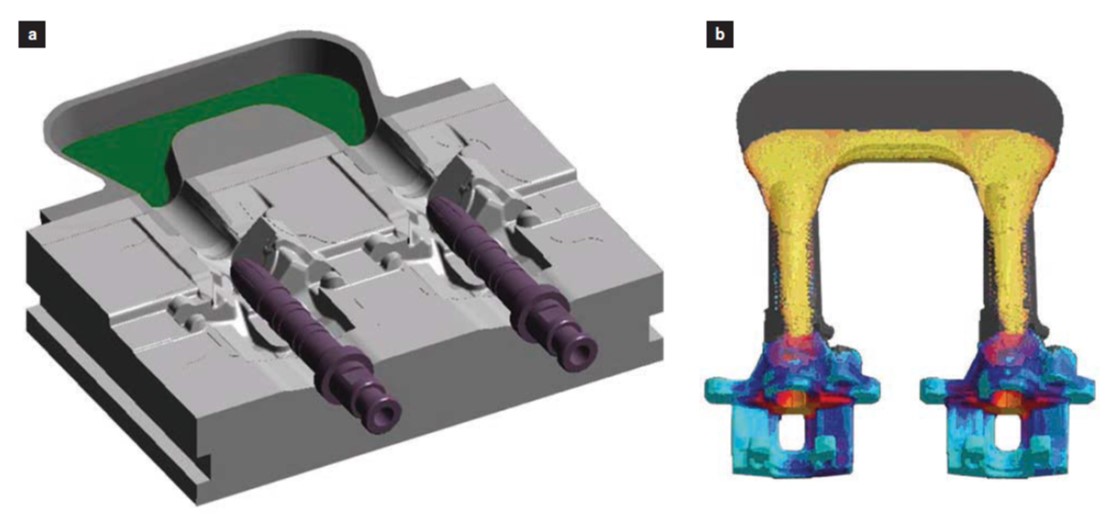
Effizienzsteigerung für Betriebsmittel und Logistik in der Gießerei
Die Vorhersage von Erstarrungs- und Abkühlzeiten für kritische Teile ermöglichte bei Heidelberger Druck die Reduzierung von Durchlaufzeiten und eine Optimierung des Abkühlflächen- und Formrahmenbedarfs. Hierdurch konnten Betriebsmittelkosten und Logistikkosten optimiert werden (Bild 7).
Durch die Simulation konnte auch die Anschnitt- und Speiser-Geometrie für den Guss von Lagerblöcken modifiziert werden, um das Auspacken durch „Knacken“ statt Sägen zu ermöglichen. Jährliche Ersparnis: 5400 Euro bei einer Produktion von 12 700 Stück.
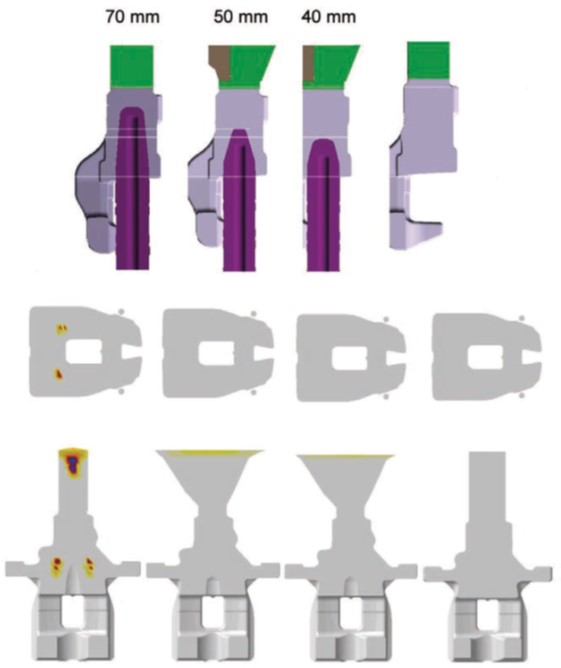
Energieeinsparungspotentiale durch Simulation der Wärmebehandlung
Viele Gussteile erhalten ihre Bauteileigenschaften durch eine nachgelagerte Wärmebehandlung. Die optimale Prozessauslegung und damit der Energieeinsatz während der Wärmebehandlung hängen von der genauen Kenntnis der eingestellten Gefüge ab, die durch die Simulation vorhergesagt werden können. Dies gilt auch für Wärmebehandlungen zur Reduzierung von Eigenspannungen. Vielfach werden den notwendigen Behandlungszeiten massive Sicherheitszuschläge hinzugefügt, die früher aufgrund der Unsicherheit üblich waren. Durch frühzeitige Prozesssimulationen der Wärmebehandlung können diese Zuschläge drastisch reduziert werden. Neue Modelle ermöglichen die Vorhersage von Austenitisierungszeiten durch Berechnung der lokalen Kohlenstoffsättigung bei Gusseisen und Stahlguss [15]. Bei einer Gesamtaustenitisierungszeit eines Windkraftteils von 6 h und einem Reduzierungspotential von 1,5 h ergibt sich eine Energieeinsparung von 128 kWh pro t Einsatzgut. Dies resultiert bei 500 wärmebehandelten Teilen in einer Einsparung von 100 000 KWh pro Jahr (Bild 8).
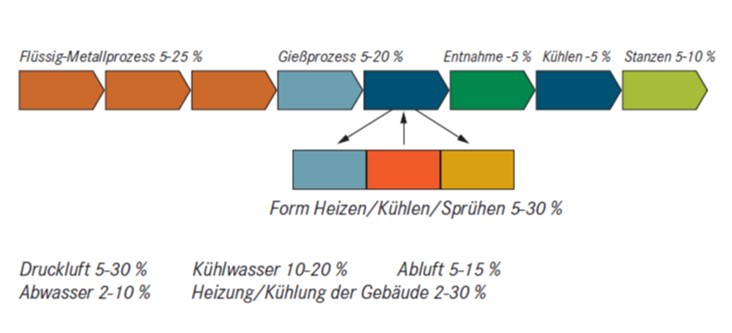
Energie- und Kosteneinsparung im Aluminiumkokillenguss
Die Potentiale zur Energieeinsparung in Seriengussverfahren sind durch die Hebelwirkung der großen Anzahl von gefertigten Teilen besonders hoch. Auf der anderen Seite sind die prozesstechnischen und konstruktiven Freiheitsgrade im Dauerformguss sehr viel geringer als im Sandguss. Die möglichen Energieeinsparungspotentiale sind über den gesamten Prozessablauf verteilt.
Das ursprüngliche Gießsystem einer Vorderradgabel, die im Kippkokillenguss gefertigt wurde, führte zu verschiedenen Qualitätsproblemen, die von der Gießprozesssimulation aufgezeigt wurden. Außerdem lag das Ausbringen bei lediglich 49 %.
Die konsequent auf Basis von Simulationsergebnissen ausgearbeitete neue Lösung eliminierte zuvor vorhandene Turbulenzen während der Füllung. Ebenso wurden ein Wärmezentrum und damit eine Fehlstelle beseitigt. Durch den schmaleren Anguss wurde das Ausbringen um etwa 18,5 % verbessert. Eine schnellere Füllung der dünneren Wandstärken reduzierte die Erstarrungszeit und verkürzte die Zykluszeit um 10 % (Bild 9).
Die Kosteneinsparungen durch den Einsatz der Gießprozesssimulation berechnen sich aus der höheren Ausbringung, der geringeren Ausschussrate, der kürzeren Zykluszeit, und auch aus Einsparungen bei Werkzeug- und Maschinenkosten. Trotz des erheblichen zusätzlichen Mehraufwandes für die neue Gießtechnik und das neue Werkzeug konnte eine Reduzierung der Gesamtkosten bereits im ersten Jahr um 28 000 Euro realisiert werden.
Durch Formänderungen und gießtechnische Maßnahmen, die durch Gießprozesssimulation erst möglich wurden, konnte die Aluminiumgießerei EBCC, Wroclaw, Polen, innerhalb eines Jahres mehr als 100 000 Euro Kosteneinsparungen bei der Herstellung eines Bremssattels realisieren [17]. Der Erfolg resultierte im Wesentlichen aus geringerem Abbrand beim Schmelzen (rund 25 000 Euro/Jahr), aus eingesparten Energiekosten beim Schmelzen (rund 45 000 Euro/Jahr), aus einer geringeren
Taktzeit und einem verringerten Formverschleiß, was in einer geringeren Anzahl von neuen Formen pro Jahr (35 000 Euro/ Jahr) resultierte. Darüber hinaus konnten mit Hilfe der Simulation die Zykluszeiten und damit die Produktivität optimiert werden (Bild 10 und 11).
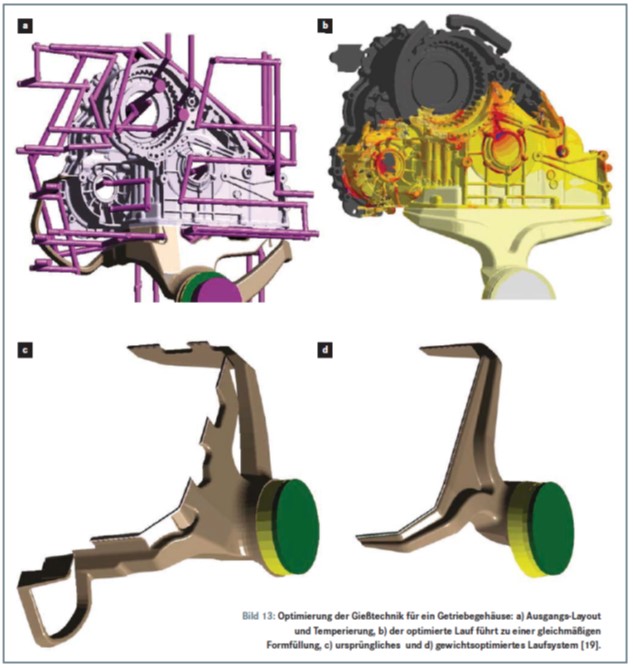
Einsparungspotentiale im Druckguss
Im Druckgießverfahren werden zwischen 40 % und 60 % des Gesamtenergiebedarfs für die Bereitstellung der Schmelze und die entsprechende Restsumme für den eigentlichen Gießprozess benötigt [18]. Der Energiebedarf für das Erschmelzen hängt vom Ausschussanteil (typisch 5 bis 7 %) und von Umschmelzverlusten (2 bis 5 %) sowie maßgeblich vom Verhältnis Gussteilgewicht zu Gesamtgewicht ab, das je nach Teil und Verfahren zwischen 30 und 70 % variiert. Hierdurch, aber auch durch die unterschiedlichen Fertigungseinrichtungen der Gießereien und ihre jeweiligen Anstrengungen zur Energieeinsparung schwankt der spezifische Einsatz von Gas zum Schmelzen um den Faktor 7 und Elektrizität um den Faktor 2 bei einem Mittelwert von 5603 kWh pro t gutem Guss [2]. Diese Angaben zeigen das Potential auf, das durch die Optimierung des Gießsystems und in Folge davon die Reduzierung des Schmelzaufwandes in den Gießereien gehoben werden kann.
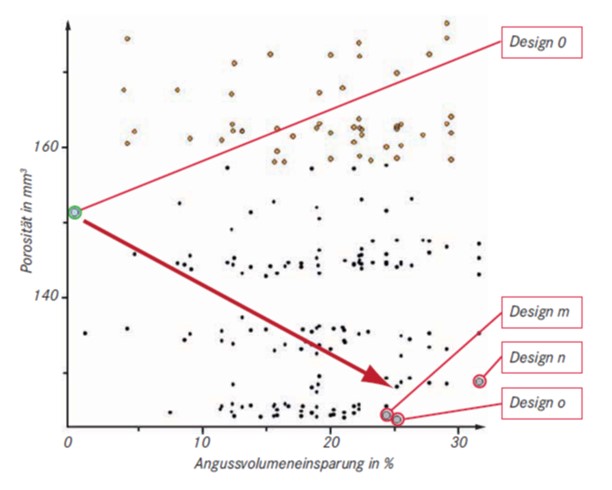
Typisch für den eigentlichen Druckgießprozess sind hohe Energieverluste im Werkzeug durch Kühlung und Abgabe an die Umgebung, sodass nur ein geringer Teil der zugeführten Wärme (Metall und Temperierung) im Teil verbleibt. Weitere substantielle Potentiale für energetische Effizienzsteigerungen liegen in der Werkzeugauslegung (Produktivitätssteigerung durch Mehrfachwerkzeuge) und der Werkzeuglebensdauer (Nutzung der eingesetzten Primärenergie und Einsatz von Betriebmitteln pro gutem Gussteil sowie Wartungsaufwand). Bei konsequenter Optimierung der gesamten Fertigung sind in Summe Energieeinsparungen von 15 bis zu 35 % für jede Gießerei erreichbar (Bild 12) [2]. Auch hierzu kann die Gießprozesssimulation maßgebliche Beiträge leisten, die unter anderem in einem aktuellen Forschungsprojekt im Detail untersucht werden [18].
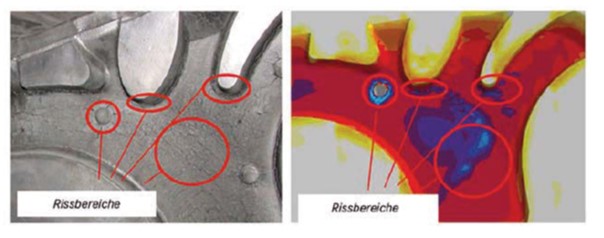
Optimierung des Gießsystems und Kreislaufanteils
Am Beispiel eines Getriebegehäuses wurden im Rahmen dieses Forschungsprojektes Einsparungspotentiale durch die Optimierung des Gießlaufs und durch die Umstellung der Formtemperierung von Öl auf Wasser ermittelt. Dabei war Voraussetzung, dass die Gussteilqualität sich nicht verschlechtern durfte. Hierzu wurde eine umfangreiche virtuelle Parameterstudie (DoE) durch Gießprozesssimulationen unterschiedlicher Fertigungsbedingungen und Gießlaufdesigns durchgeführt (Bild 13). Die Software erlaubt den direkten Vergleich aller gerechneten Versuche und zeigt die besten Lösungen auf (Bild 14).
Als Ergebnis konnte bei gleicher Qualität das Laufvolumen um 25% reduziert werden, was 12 % weniger Materialeinsatz pro Abguss bedeutet. Gleichzeitig wurde durch die optimierte Kühlung und das verminderte Angussgewicht die Taktzeit um 8 % reduziert [19].
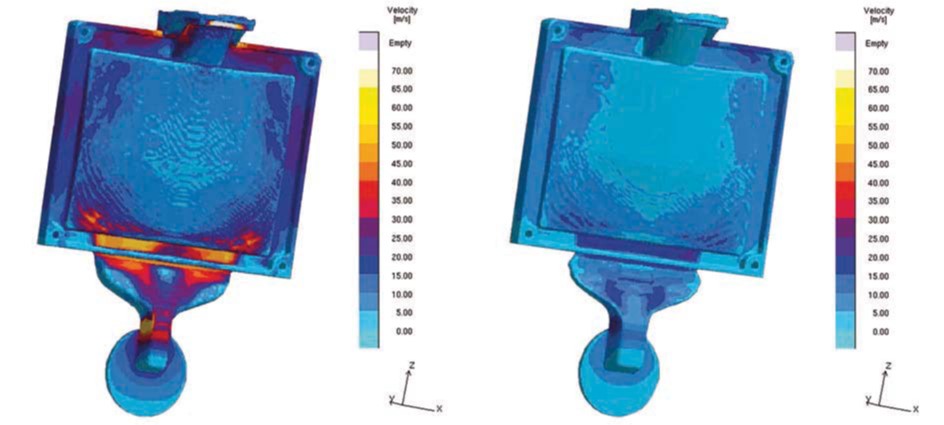
Verlängerung von Werkzeugstandzeiten
Thermomechanische Ermüdung von Druckgießwerkzeugen und abrasiver Verschleiß im Gießsystem sind Hauptursachen für den Ausfall von Formeinsätzen. Die damit verbundenen Kosten sind enorm: typische Kosten für einen neuen Formeinsatz betragen ca. 50 000 Euro, zusätzlich müssen die Stillstandszeiten der Druckgießmaschine mit ca. 3000 Euro/Tag veranschlagt werden. Mit Hilfe der Simulation können heute kritische Stellen für Brandrissbildung und Verschleiß sehr gut identifiziert werden (Bild 15). Durch Modifikation von Prozessparametern, konstruktive Änderungen im Werkzeug oder verbesserte Formwerkstoffe kann diesen Problemen entgegengewirkt werden.
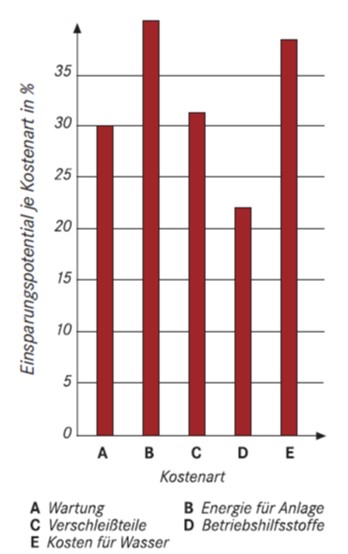
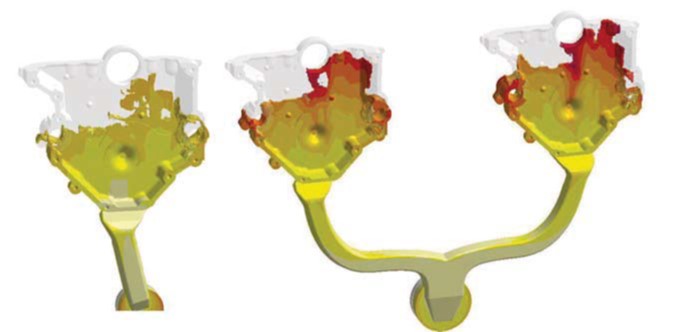
Bei der Metallgießerei Karl Scherb GmbH, Dietenheim, führte die Änderung eines Anschnittsystems mit dem Ziel, vorhandenen Formverschleiß zu optimieren und damit die Standzeit des Werkzeugs zu verlängern, zu einer Kostenreduzierung von 25 000 Euro (Bild 16). 20 000 Euro weniger waren für Prüfkosten und Abdrückvorrichtungen zu zahlen, weil durch die Umkonstruktion eines Formeinsatzes die Porenbildung reduziert werden konnte [22].
Effizienzsteigerung und Kostensenkung durch Mehrfachformen
Für alle Gießverfahren gilt, dass die Produktivität und damit auch der spezifische Material- und Energieeinsatz im Allgemeinen von der Anzahl der in eine Form gegossenen Teile abhängen. Dies ist insbesondere auch beim Druckgießen der Fall, wobei die fertigungstechnischen Herausforderungen an Werkzeugkonstruktion und Gussteilqualität mit der Anzahl der Teile in der Form stark ansteigen. Bei einem Einsatz eines Zweifachwerkzeuges gegenüber einem Einfachwerkzeug können, bezogen auf die einzelnen Kostenarten, Einsparungen zwischen 20 und 40 % erzielt werden (Bild 17). Bezogen auf ein Gussteil liegen neben den anteiligen Wartungskosten die größten Einsparungspotentiale bei der Energie zum Betreiben der Anlage [23]. Klassische Maßnahmen zur Prozessoptimierung des Einfachwerkzeuges führen bei Weitem nicht zu vergleichbaren Produktivitätssprüngen. Gleichzeitig steigt mit der Erhöhung der Zahl der Gussteile pro Abguss jedoch das Fertigungsrisiko erheblich. Daher muss eine hohe Prozesssicherheit für die einzelne Druckgießzelle gewährleistet sein. Die Umstellung von Einfach- auf Mehrfachwerkzeuge zwingt zu einer geänderten Gießlaufgestaltung, die häufig zu Qualitätsunterschieden bei den Gussteilen eines Abgusses führt. Dieses Qualitätsproblem tritt insbesondere bei nichtsymmetrischen Gussteilen auf, bei denen
die Formnester im Werkzeug gleichsinnig eingeformt sind und jeweils über einen separaten Zulauf gefüllt werden. Mit Hilfe der strömungsabhängigen Auslegung des Gießlaufs konnte die Füllcharakteristik des Einfachwerkzeuges beim Zweifachwerkzeug eingestellt werden (Bild 18). Das bereits mit dem Einfachwerkzeug erreichte hohe Qualitätsniveau konnte durch die gezielte Übertragung der beim Einfachwerkzeug gewonnenen Füllcharakteristik mittels autonomer Optimierung des Strömungsverlaufs auf die Doppelform übertragen werden. Das Fertigungsrisiko wurde durch den Einsatz rechnerischer Simulation deutlich gesenkt und in der Gießerei von Anfang an wirtschaftlich umgesetzt.
Der Werkzeughersteller Metabo International GmbH, Nürtingen, produziert zwei Mio. Gussteile pro Jahr, die als Sichtteile, Getriebe, Getriebegehäuse oder Verzahnungen den „massiven“ Kern der Werkzeuge bilden. Mit Hilfe der Gießprozesssimulation gießt man mit kostensparenden Vielfachformen und geht dabei mit der vorhandenen Maschinenausstattung an die Grenzen des Machbaren. Mit der Optimierung ihrer Angusssysteme konnte Metabo in den letzen Jahren 50 % des Kreislaufmaterials einsparen. Die Reduzierung des Kreislaufmaterials schlägt sich darüber hinaus direkt in sinkenden Kosten für Heizenergie, Materiallogistik und Materialtransport nieder [24].
Insgesamt sind die Stückkosten durch die Nutzung von Vielfachformen, durch die längeren Standzeiten der Druckgießwerkzeuge und durch die Einsparungen beim Umlaufmaterial um 40 % gesunken – eine Kostensenkung, die Metabo direkt auf den Einsatz der Gießprozesssimulation zurückführt.
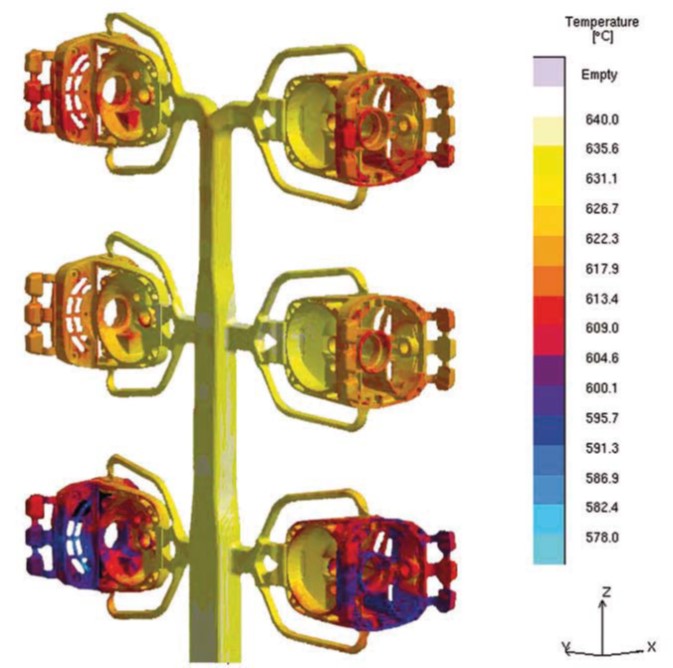
Energieeinsparungen durch Substitution in Guss
An einer ganz anderen Stelle trägt die Gießprozesssimulation ebenfalls zu Energieeinsparungen bei. Im Wettbewerb der Fertigungsverfahren ist Gießen der direkteste Weg zum endkonturnahen Fertigteil und hat durch die geschlossenen Kreisläufe energetische Vorteile gegenüber spanenden Verfahren oder Verbindungstechniken wie Schweißen, da für jede t Gussteile bis zu zwei Drittel weniger Primärenergie benötigt werden als für spanende Verfahren. Verfügbare Simulationstechniken machen es nun möglich, die Substitution in Guss zu unterstützen, um komplexe, endformnahe Gussteile zu realisieren. Das gilt für ganze Teile genauso wie für kleinere Konstruktionselemente. So gießt Metabo aufgrund der Absicherung der Machbarkeit durch die Gießprozesssimulation zahlreiche Werkzeugteile mit vorgegossenen Bohrungen, die zuvor erst anschließend durch zusätzliche mechanische Bearbeitung eingefügt werden mussten (Bild 19). Die wenigen Cent pro Bauteil, die das Gießen von Konstruktionselementen und das Eliminieren von nachträglichen Bearbeitungsschritten einsparen, addieren sich auf mehrere hunderttausend Euro pro Jahr.
Die Potentiale werden auch an einem anderen Beispiel im Maschinenbau deutlich: ein bisher aus einer Schweißkonstruktion hergestelltes Gehäuse für ein Großgetriebe (Bild 20), wurde durch eine Gusskonstruktion aus Gusseisen mit Kugelgraphit substituiert. Dabei wurden zeitgleich Topologieoptimierung und Gießprozesssimulation eingesetzt, um sowohl den Anforderungen für den Lastfall (hier primär Steifigkeit) als auch für die gießgerechte Auslegung Rechnung zu tragen. Ergebnis der gemeinsamen Anstrengungen von Konstrukteur und Gießer war ein dreiteiliges Getriebegehäuse aus Gusseisen mit Kugelgraphit, das eine höhere Steifigkeit als die Schweißkonstruktion aufwies. Gleichzeitig konnten mit 18,4 t ein um 20 % reduziertes Gesamtgewicht und damit auch Kostenvorteile gegenüber der Schweißkonstruktion realisiert werden [25].
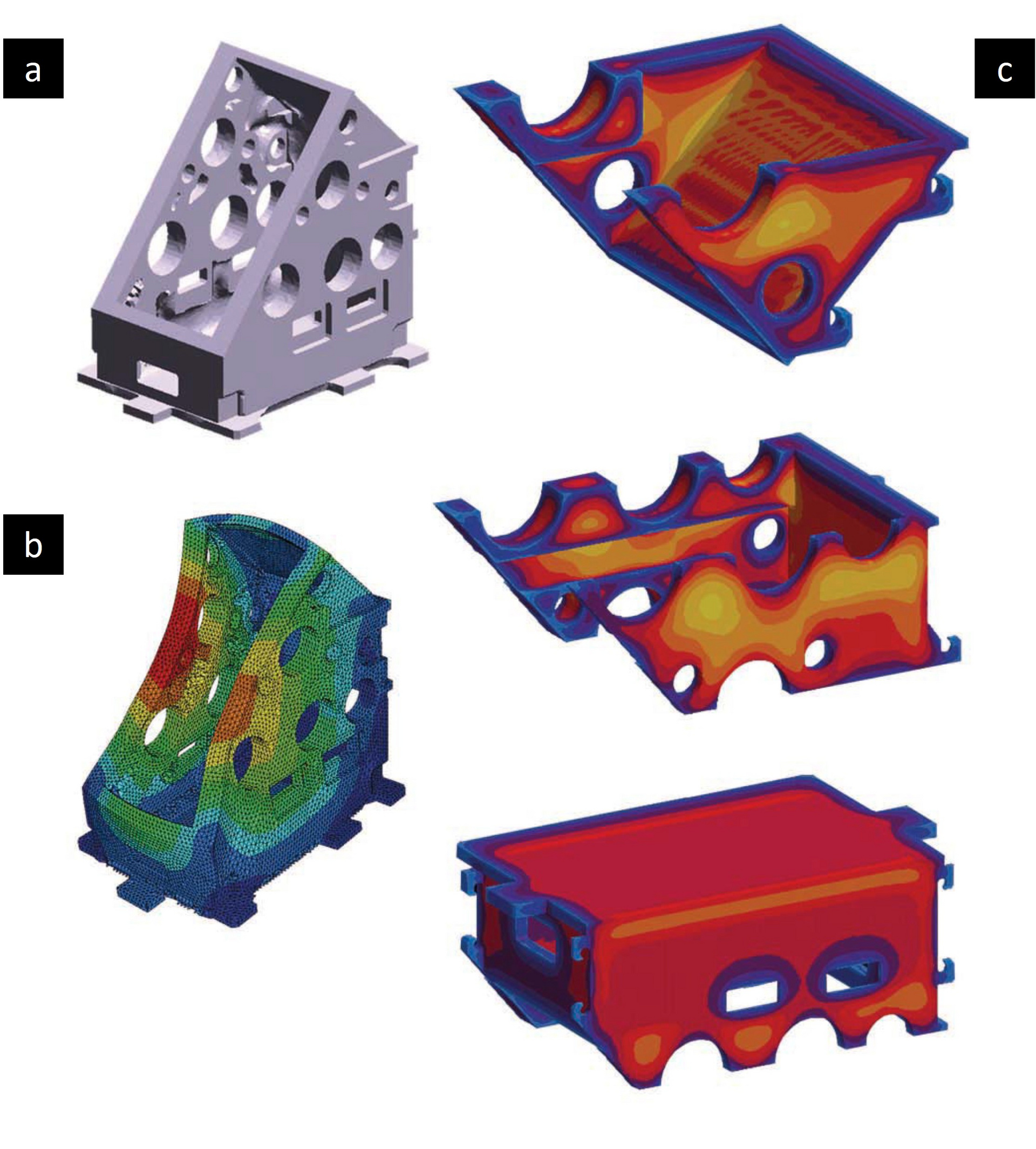
Gießprozesssimulation – vom Wettbewerbsvorteil zur Umwelttechnologie
Die Gießprozesssimulation gehört heute in vielen Gießereien zu den Standardtechniken zur Kostenreduzierung und Absicherung der Fertigung. Zunehmend verlangen Gussteilabnehmer in der Automobilindustrie und im Maschinenbau von ihren Zulieferern simulationsgetestete, robuste und energieschonende Produktionsprozesse und Gussteile. Die von der EU verfolgten Energie- und Klimaschutzziele bis 2020 sehen unter anderem eine Verbesserung der Energieeffizienz um 20 % vor [26]. Die vorgestellten Beispiele dokumentieren, dass bei konsequenter umfassender Nutzung der Gießprozesssimulation über alle Gießverfahren hinweg eine 10%ige Effizienzsteigerung sicher möglich ist. Dies entspricht einem Einsparvolumen allein für die deutsche Gießerei-Industrie von bis zu 1 Mrd. kWh oder 560 000 t CO2 pro Jahr. Vor dem Hintergrund der aktuellen Energiediskussion und der aufgezeigten Möglichkeiten, mit der Gießprozesssimulation Energie und Material zu sparen, wird der konsequente Einsatz der Software in möglichst vielen Gießereien auch zu einer klimapolitischen Forderung.
Dr.-Ing. Jörg C. Sturm, Leiter Vertrieb und Engineering, Magma Gießereitechnologie GmbH, Aachen
Literatur:
[1] „Energieeffizienter Gießereibetrieb“ 2010, Herausgeber: Bundesverband der Deutschen Gießerei-Industrie (BDG).
[2] Jordi, U.: „Energie-Sparpotentiale im Druckguss“, Energieeffizienztagung, Frankfurt (2010).
[3] Jahresbericht 2008 des Bundesverbands der Deutschen Gießerei- Industrie (BDG).
[4] Quelle Umwelbundesamt, http://www.umweltbundesamt.de/e nergie/archiv/co2-strommix.pdf.
[5] Sturm, J.C.: „Optimierung des Feingußverfahrens durch den Einsatz moderner Simulationstechniken“ VDI Verlag, Reihe 5: Grundund Werkstoff e, Nr. 226 ISBN 3-18-14 2605-9.
[6] M. Fehlbier, J. Lerch-Thies, H.-I. Stanescu: „Entwicklung dünnwandiger Strukturbauteile mit Hilfe numerischer Simulationsmethoden“, 6. Magma NE – und Leichtmetallforum (2010), Ludwigsburg.
[7] Egner-Walter, A. Zenker. N. und Fritsche, E.: „Vorhersage von Gefüge und lokalen Eigenschaften für Kurbelgehäuse aus GJV“, VDIFachtagung: Gießtechnik im Motorenbau, Magdeburg (2011).
[8] entnommen aus Vortrag Magma Nord-Amerikanisches Anwendertreffen 2009.
[9] entnommen aus Vortrag Magma Nord-Amerikanisches Anwendertreffen 2009.
[10] entnommen aus „At the Heart of Casting - Mitten im Guss“ Herausgeber: Magma GmbH, 2008.
[11] Schreiner, J. Pfi sterer, W.: „Der Einsatz der numerischen Simulation zur Wirtschaftlichen Auslegung der Gießtechnik am Beispiel eines Edelstahlgussteiles“, Vortrag auf 8. VDI-Tagung in Veithöchheim, 1995.
[12] persönliche Mitteilung.
[13] Giesen, H.: „Qualitätsguss entsteht auf dem Bildschirm“, Industrieanzeiger, Ausgabe 02/2011, 32-34.
[14] Barter. D., John Deere Waterloo Foundry: „Using Magmasoft to Design Cost Eff ective and More Manufacturable Castings“, Vortrag auf dem Magma Nord-Amerikanischem Anwendertreff en 2009.
[15] Sturm, J. C. und Busch, G: „Cast Iron - a predictable material“, Proceedings of World Foundry Congress 2010, Hangzhou, China.
[16] „Kleine Änderungen, große Wirkung“ Magmatimes 01/2008, S. 1-2.
[17] Targowski, W. (EBCC Poland) et. al: „Implementation of Magmasoft to improve a gravity die casting process on an example of aluminum disc brake calipers manufacturing“, Vortrag auf dem Internationalen Magma-Anwendertreff en (2006), Kopenhagen/Oslo.
[18] Pries, H.: „Progresse – Ansätze zur Erhöhung der Energie- und Ressourceneffi zienz in der Prozesskette Aluminium-Druckguss“, Energieeffi zienztagung, Frankfurt (2010).
[19] Hartmann, G.: Vortrag auf Progress-Treff en, Gestaltung ressourceneffi zienter Prozessketten am Beispiel Aluminium-Druckguss, BMBF-Verbundforschungsvorhaben, Karlsruhe 2009.
[20] R. Seefeldt, Vortrag auf Progress-Treff en, Gestaltung ressourceneffizienter Prozessketten am Beispiel Aluminium-Druckguss, BMBF-Verbundforschungsvorhaben, Hindesheim 2011.
[21] Egner-Walter, A. und Olive, S: „Using Stress Simulation to tackle Distortion and Cracking in Castings“, World Foundry Congress 2006, Harrogate, England, Juni 2006
[22] Bärmann, F.: „Breitere Service-Palette, rationelle Produktion”, Produktion, Ausgabe 10/2011, 24.
[23] R. Seefeld, J. Sturm und A. Pawlowski: „Aus Eins mach Zwei“, Giesserei 94 (2007), Ausgabe 4, 34–42.
[24] „Sichere Qualität durch Prozesssimulation”, Produktion, Ausgabe 31-32/2010, 16.
[25] Schulz, R.; Amato, R.;. Egner-Walter; A; Busch G.; Zimmermann, J.: „Von der Schweißkonstruktion zum Gussteil – Topologieoptimierung und Gießsimulation für ein Getriebegehäuse“, Vortrag auf dem 4. Magma-Eisengussseminar 2006, Heilbronn.
[26] Information entnommen aus Schumacher, M: „Energie(-effi zienz) – Ein Schlüsselthema für die Gießerei-Industrie“, Giesserei 98, 04/2011, 68-72.