Pfannenaufheizen unter den Aspekten Energieeffizienz und Kostenoptimierung
Von Heinz Kadelka, Düsseldorf, und Mike Weber, Eisenberg
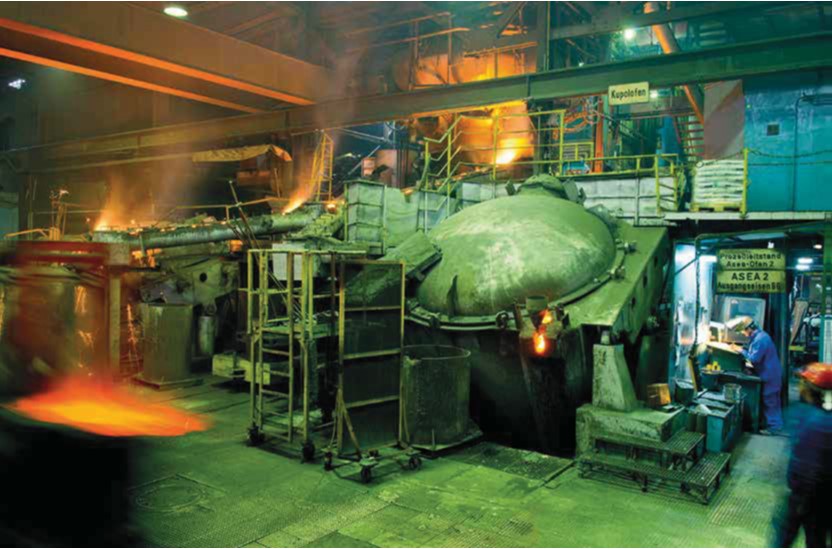
Bei Gienanth in Eisenberg verglich die Firma Linde die Wirkungsgrade verschiedener Brennertypen zum Aufheizen und Warmhalten von Gießpfannen.
Erschienen in GIESSEREI 02/2017
Wie bewähren sich Brennersysteme zum Pfannenaufheizen im Praxisvergleich? Das war das Thema einer Untersuchung der Firma Linde Gas in Kooperation mit der Gießerei Gienanth in Eisenberg. Dafür wurde die Leistung von Poren- und Erdgas-Sauerstoffbrenner beim Aufheizen von Gieß- und Behandlungspfannen für Gusseisen mit Lamellengrafit und Kugelgrafit sowie Vermiculargrafit verglichen.
Praxisvergleich
Ziele waren die Untersuchung der Wirtschaftlichkeit, Flexibilität, Energieeffizienz, Standzeit, Sinterung und der Temperaturwechsel beim Aufheizen. Gegenstand der Untersuchung war eine 4-t-Transportpfanne für Gusseisen, die mit den beiden unterschiedlichen Brennersystemen aufgeheizt wurde.
Hintergrund
Pfannen stellen einen bedeutenden Anteil am Gesamtenergieeinsatz im Schmelzprozess von flüssigem Eisen dar. Sie müssen auf Betriebstemperatur aufgeheizt und letztlich kontinuierlich betriebswarm gehalten werden. Dies soll in jeder Hinsicht wirtschaftlich und flexibel erfolgen, sodass die Pfannen geringeren Temperaturwechseln ausgesetzt werden, eine lange Feuerfeststandzeit möglich ist und die Pfannenpflege auf ein notwendiges Minimum reduziert wird.
Versuchsaufbau
Bild 1 zeigt die Lage der Thermoelemente im Feuerfestbereich der 4-t-Gießpfanne.
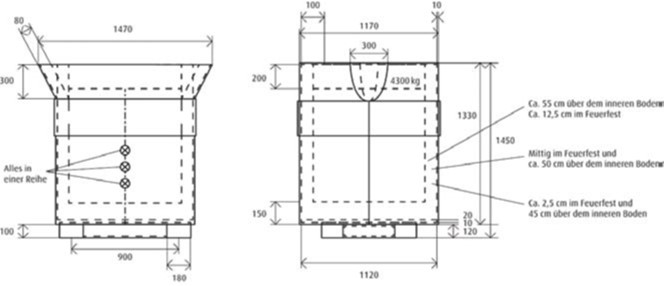
Eigenenergiehaushalt einer betriebswarmen Gießpfanne
Das Durchwärmen einer Pfanne ist im Wesentlichen durch den Wärmeinhalt des Feuerfestmaterials, insbesondere der Überhitzung der inneren Randschicht, gekennzeichnet. Nach dem Füllen mit flüssigem Eisen wird Wärmeenergie in die Pfanne eingetragen, die dann über das Feuerfestmaterial nach außen abgeführt wird.
Insbesondere am Meßpunkt M 1 im Abstand von 2,5 cm von der inneren Feuerfestwand wird nach dem Füllen mit flüssigem Eisen ein Temperaturanstieg deutlich (ca. 970 °C; Bild 2). Die Pfanne war für diese Untersuchung ca. 8 min mit 3 t Eisen gefüllt. Somit konnte ein optimales Durchwärmen nachgestellt werden.
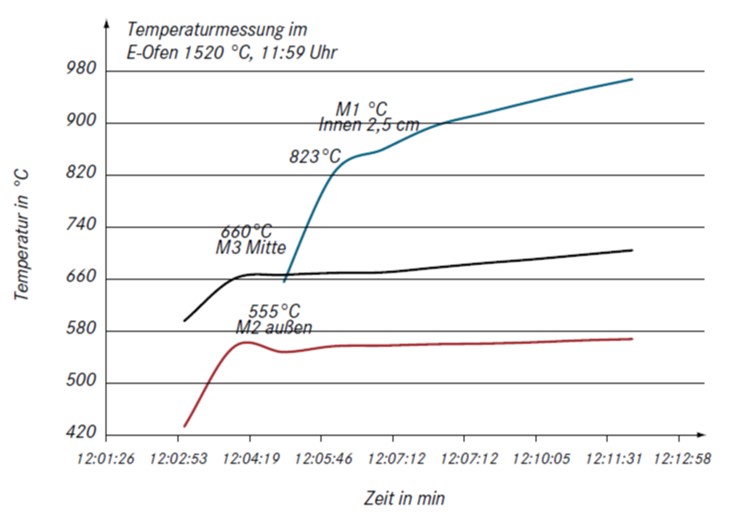
Nach dem Abguss ist zu erkennen, dass die Feuerfestrandschicht auf den ersten 2,5 cm überhitzt wurde (Bild 3). In dieser nur 2,5 cm starken Randschicht kann eine Temperaturdifferenz von über 550 °C zum Messpunkt M 1 nachgewiesen werden. Dieser Wärmeenergieinhalt sollte auch durch ein Pfannenvorwärmen eingetragen werden, um diese Energie dem flüssigen Eisen nicht zu entziehen.
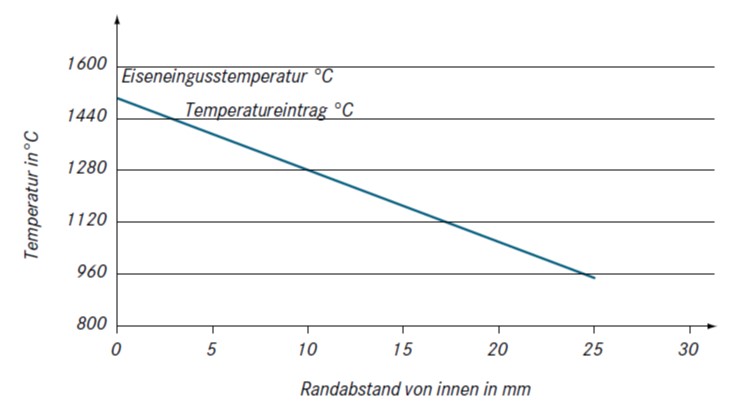
Temperaturwechselbeständigkeit
Beim Befüllen von Pfannen mit flüssigem Eisen wird die innere Randschicht erwärmt. Befindet sich die Temperatur dieser Schicht vor dem Einguss auf hohem Niveau, findet ein geringerer Temperaturaustausch statt (Bild 3). Ist dieser Bereich „kalt“ oder nur unzureichend aufgeheizt, sind die Temperaturwechsel hoch und führen zu frühem Verschleiß, kurzer Lebensdauer und Schlackenanhaftungen in den eingesetzten Pfannen. Durch die aus Bild 3 ersichtliche überhitze Randzone des Feuerfestmateriales wird dieser Energieanteil nach dem Abguss an das Feuerfest-Innere abgegeben.
Auskühlung des Feuerfestmaterials
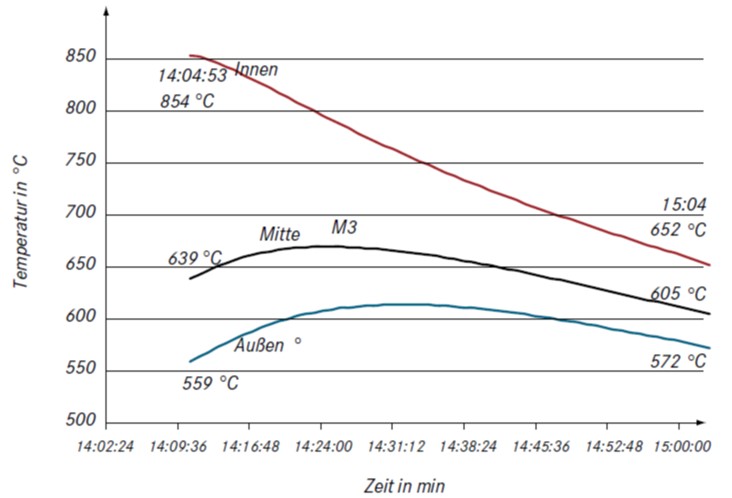
Dieser Effekt kann in Bild 4 zwischen 14:04 und 14:20 Uhr für ca. 20 min an Messstelle 3 beobachtet werden. Gleich einer Welle wird Wärmeenergie in das Feuerfestmaterial eingetragen. Es kommt zum Temperaturanstieg. Die überhitzte Masse in der Randschicht des Feuerfestmaterials (Rand und Boden) kann mit über 200 kg angenommen werden. Wärmeinhalt: ca. 4 bis 5 m³ Erdgas. Selbst wenn die Pfanneninnenfläche schon als „kalt“ bezeichnet wird (Dunkelrot), ist wenige Millimeter im Feuerfestmaterial noch mit Temperaturen von deutlich über 1200 °C zu rechnen.
Kriterien für den Vergleich
Grundsätzlich sollten die natürlichen Vorgaben, die unter „Energiehaushalt einer betriebswarmen“ Pfanne beschrieben wurden, erreicht werden.
Für die untersuchte 4-t-Gießpfanne wurde als Grundlage das Temperaturniveau in der Mitte des Feuerfestmaterials angenommen. Ziel der Vorheizung mit den unterschiedlichen Brennersystemen sollte das konstante Erreichen und Halten dieser Temperaturen sein. Im Untersuchungsfall herrschten ca. 640 °C bis ca. 660 °C am Feuerfestmesspunkt M3 Mitte. Am Messpunkt M1 Innen sollten über 820 °C erreicht werden.
Das entspricht dem tatsächlichen Temperaturniveau der im Produktionsprozess befindlichen Gießpfanne.
Vorüberlegung zur Pfannenwirtschaft und zur Ist-Situation
Grundsätzlich ist der momentane Ist-Zustand der Pfannenaufheizung mittels Porenbrenner die Basis des Wirtschaftlichkeitsvergleiches. Letztlich kann dieser Zustand vom Betreiber mit einfachen Mitteln optimiert werden, im Einzelnen kann das eine angepasste Pfannenabdeckung in Verbindung mit einem genau eingestellten Erdgas-Luft-Verhältnis sein.
Auch helfen Thermoelemente im Pfannendeckel, die nach Erreichen eingestellter Temperaturen den Brenner leistungsabhängig regeln oder „takten“. Auch die Sensibilisierung der verantwortlichen Mit arbeiter trägt entscheidend zur Energiereduzierung bei.
Erst nach Umsetzung dieser konventionellen Maßnahmen sollte der Ist-Zustand neu definiert werden. Dieser ist dann die Grundlage für die Entscheidung zukünftiger Aufheizmethoden.
Basis des Vergleichs war die Grundlage gleicher Gesamtkosten, natürlich unter Einbeziehung der technischen Sauerstoffkosten. Grundsätzlich wird versucht, unter dem Einsatz gleicher Kosten bei den untersuchten Brennersystemen ein optimales oder physisch mögliches Ziel zur erreichen und den Effekt der „überhitzten Randschicht“ zu erzielen.
Aufheizen der 4-t-Gießpfanne mittels Erdgas-Sauerstoffbrenner (Oxyfuel-Brenner)
Nach 90 min wurde das selbst gesteckte Ziel mit 649 °C erreicht. Die Temperatur in 2,5 cm Entfernung von der inneren Oberfläche erreichte 832 °C (Bild 5), was der Temperatur nach dem Einguss der betriebswarmen Pfanne entspricht (Bild 2 mit 823 °C).
Die Oberflächentemperatur des Feuerfestmaterials lag sicher über 1550 °C und entspricht damit anderen bekannten Messungen. Der Brenner erreichte einen Wirkungsgrad (ETA v) von 71 %.
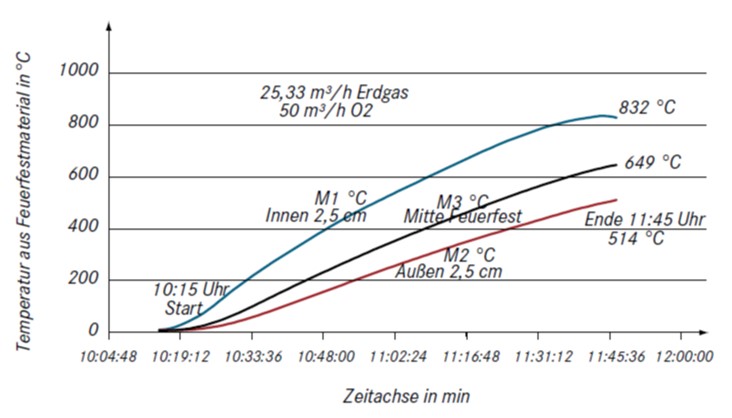
Aufheizen der 4-t-Gießpfanne mittels Porenbrenner
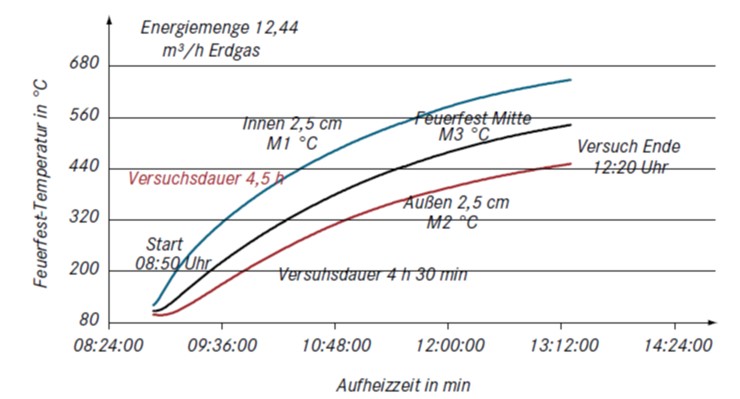
Porenbrenner
Die vorgefundene Konstruktion lässt eine individuelle Höheneinstellung zu und der Brennerdeckel ist so ausgelegt, dass fast alle Pfannendurchmesser eingesetzt werden. Die Pfannen sind so abgedeckt, dass nur ein kleiner Spalt am Umfang zugelassen wird. Das Abgas wird durch ein im Deckel integriertes Rohr abgeführt. Das Brenngas und die Verbrennungsluft werden durch eine poröse Keramik geführt und im Inneren eines hochwarmfesten Edelstahlrohrs gezündet. Das mit dem Pfannendeckel verbundene Rohr wird in die Pfanne versenkt, bis der Brennerdeckel auf dem Pfannenrand aufliegt. Die Brenngase steigen dann zwischen der inneren Pfannenwand und dem äußeren Brennerrohr auf.
Besonderheit
Die Gastemperatur ist aus materialtechnischen Gründen begrenzt. Im Vergleich war die Temperatur auf 1000 °C limitiert (Thermoelement am äußeren Brennerrohr).
Situation
Die Vorgabe der Eisengießerei Gienanth, Eisenberg, bei der Zieltemperatur betrug 1000 °C (konstruktive und materialspezifische Voraussetzungen zur Vermeidung von thermischer Überlastung).
Versuchseinstellungen
Der Erdgaseinsatz wurde mit 12,44 m³/h ermittelt, an der Oberfläche des Brennerrohres wurden maximal 1020 °C gemessen. Die maximale Abgastemperatur lag bei knapp 1000 °C. Somit kann davon ausgegangen werden, dass der Wärmeübertrag an das Feuerfestmaterial bei dieser Temperatur erfolgt.
Zielerreichung an den Messstellen des Feuerfestmateriales
Bei einem Gesamtenergieeinsatz von 56 m³ Erdgas nach durchschnittlich 4,5 h Aufheizzeit wurden 538 °C am mittleren Messpunkt M3 erzielt. 2,5 cm von der inneren Oberfläche wurden 650 °C gemessen (M1, Bild 6). Der Wirkungsgrad bezogen auf die Temperatur in der Mitte des Feuerfestmaterials wurde mit ca. 47 % berechnet.
Das Ziel einer betriebswarmen Pfannenaufheizung (> 640 °C) wurde damit mit dem Porenbrenner mit identischen Kosten nicht erreicht (538 °C). Der Effekt einer überhitzen Randschicht kann mittels Porenbrenner nicht erzielt werden.
Gesamtvergleich beim Aufheizen
Nach ca. 4,5 h (270 min) wurde bei der Beheizung mit dem Porenbrenner eine Temperatur von 538 °C erzielt (ETA v 47 %). Der Erdgas-Sauerstoffbrenner erreichte diese Temperatur bereits nach 1,22 h (73 min), (ETA v 71 %) Das Temperaturniveau des Porenbrenners (538 °C) wurde mit dem Erdgas-Sauerstoffbrenner mit ca. 10 % geringeren Energiekosten (inkl. technischem Sauerstoff) erreicht (Bild 7).
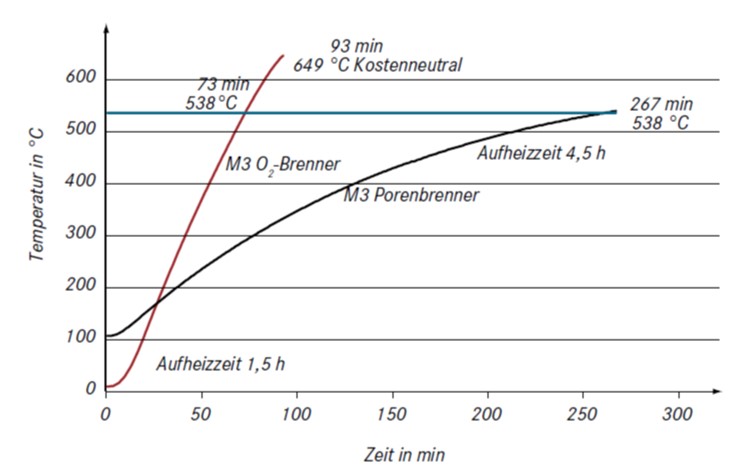
Wird die Aufheizzeit bei der Porenbrennerbeheizung verlängert, steigt die Temperatur nur unwesentlich an, und der Wirkungsgrad (ETA v) sinkt dramatisch ab.
Das tatsächliche Temperaturniveau der Pfanne aus dem Gießprozess konnte in den Versuchen mit dem Erdgas-Sauerstoffbrenner bereits nach 90 min erreicht werden (649 °C). Vergleiche hierzu bieten Bild 2 und Bild 5.
Der Energieeinsatz zum Ausgleichen der Temperaturdifferenz des Feuerfestmaterials am Messpunkt M3 von 538 °C beim Porenbrenner und 649 °C beim Erdgas-Sauerstoffbrenner muss durch die Energieabgabe (höhere Abstichtemperatur) des flüssigen Eisens an das Feuerfestmaterial ausgeglichen werden. Es ist sinnvoller, diesen Energieaustausch mittels Brenner vorzunehmen, als die negativen metallurgischen Folgen einer überhöhten Abstichtemperatur in Kauf zu nehmen.
Einfluss der Aufheiztechnologien auf das Temperaturprofil
Bei fast gleichen Abstichtemperaturen aus dem Elektroofen (Bild 8) von 1530/1531 °C ergeben sich 3 min nach der Befüllung Temperaturdifferenzen von 29 °C zum O2-System (1498/1469 °C), nach weiteren 5 min wurde mit1469/ 1406 °C eine Differenz von 63 °C nachgewiesen. Bei dem Versuch kam es in der beheizten Pfanne beim Porenbrenner zu Temperaturverlusten von 125 °C, beim O2-Brenner lediglich zu Temperaturverlusten von 61 °C – eine Differenz von 64 °C.
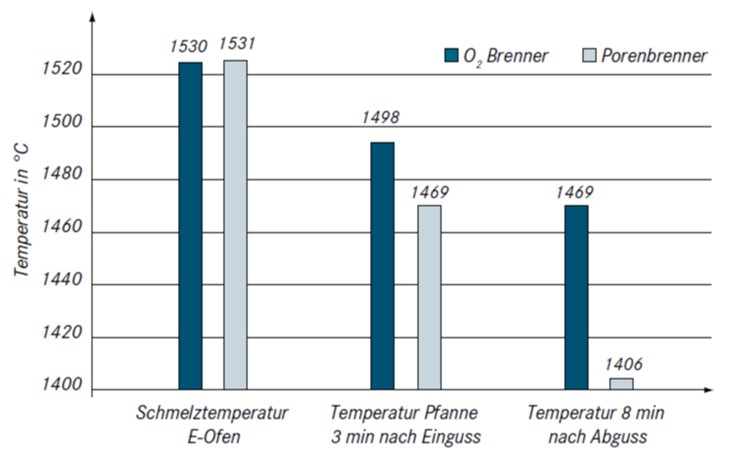
Hieraus ergibt sich ein Potenzial zur Absenkung der Abstichtemperatur im EOfen. Konsequenz: Kosteneinsparungen bei elektrischer Energie plus bewertete metallurgische Vorteile.
Aus Bild 7 wird der Verfahrensvorteil eines Erdgas-Sauerstoffbrenners deutlich. Die physikalischen Voraussetzungen werden unter der Thematik Konvektion und Strahlung nachfolgend aufgezeigt. Die in Bild 2 im Versuch ermittelten Referenztemperaturen wurden mit der Erdgas- Sauerstoffbeheizung erreicht, somit ist die Zielstellung für den Vergleich erfüllt: Messpunkt M1 innen ca. 820 °C und Messpunkt M3, in der Mitte des Feuerfestmaterials, ca. 640 - 660 °C.
Das Ergebnis der Pfannenaufheizung mit dem Erdgas-Sauerstoffbrenner unterscheidet sich nur unwesentlich von einer mit flüssigem Eisen aufgeheizten Pfanne im Produktionsprozess. Insbesondere ist aus den Bildern 9 und 3 ersichtlich, dass sich die innere Randschicht auf ähnlichem Niveau hält.
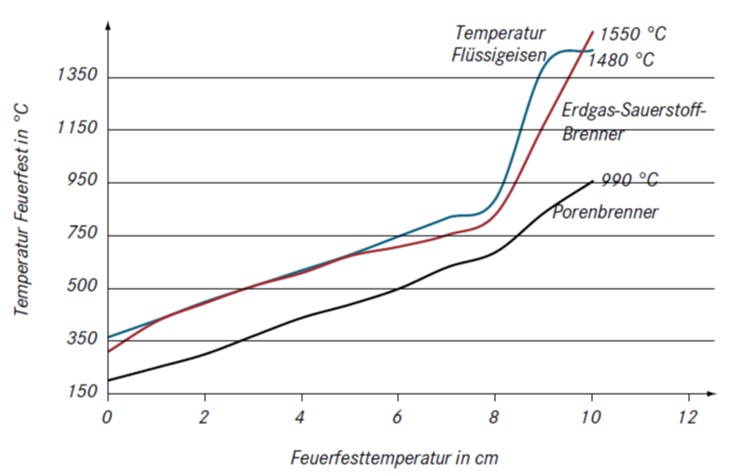
Temperaturdifferenz zwischen der Oberfläche des Feuerfestmaterials innen und dem inneren Messpunkt M1 (25 mm).
Ein wesentlicher Unterschied ist im Energiegehalt der Temperaturdifferenz begründet. Hier erreichte der Porenbrenner nach 4,5 h eine Temperatur von 990 °C an der Feuerfestoberfläche, wie Bild 9 zeigt. Das entspricht einer Temperaturdifferenz zur Sauerstoffbeheizung von über 560 °C. Der Energiegehalt in der Feuerfestrandschicht entspricht der einer betriebswarmen Pfanne.
Bei jedem Aufheizvorgang muss also (Bilder 5 und 6) das Feuerfestmaterial der mit einem Porenbrenner aufgeheizten Pfanne um die Differenz von 185 °C aufgeheizt werden (Messpunkt M1, 647/832 °C), diese zusätzliche Energie muss aus dem Schmelzprozess kommen. Also muss mit höheren Ausgangstemperaturen gegengesteuert werden.
Physikalische Hintergründe und Vergleiche zwischen der Erdgas-Luft- und Erdgas-Sauerstoffverbrennung
Flammentemperatur
Die Flammtemperatur ist im Wesentlichen von der Einstellung des Erdgas-Luft/Sauerstoffverhältnisses und der Brennerkonstruktion abhängig. Der Vergleich beruht auf dem Einsatz von Erdgas (Methan, Bild 9). In der Praxis werden hier aber nur Flammentemperaturen von < 1700 bis 1800 °C bei der Erdgas- Luftverbrennung erreicht. O2-Brenner: < 2850 °C.
Verbrennung mit Luft oder mit technischem Sauerstoff (Überschlagsrechnung)
- Ausgangsmenge 10 m³/h Erdgas (CH4).
- Verbrennung mit 100 m³/h Luft. Für die Verbrennung benötigt man ca. 20 m³/h Sauerstoff und ca. 80 m³ Stickstoff (Luft: 20,9 % O2, 78 % N2).
- Verbrennungsprodukt: H2O und CO2.
- Energieverluste (N2): Wird im Abgasstrom der Pfanne eine Temperatur von ca. 1100 °C gemessen, wird 33 % der notwendigen Erdgasenergie für das Aufheizen des Stickstoffes benötigt.
Verbrennung mit O2
Bei der Verbrennung mit technischem Sauerstoff entfällt der aufzuheizende Stickstoffballast, somit benötigt man nur 6,6 m³/h Erdgas. Durch die höhere Flammentemperatur bei der Verbrennung mit reinem Sauerstoff (2860 °C aus Tabelle 1) kommt noch ein weiter Energievorteil zum Tragen und zwar die Strahlung (Bild 10). Dieser Strahlungsvorteil reduziert die eingesetzte Energiemenge um weitere ca. 15 % im Vergleich zur Luftverbrennung. Für die notwendige Verbrennung mit Sauerstoff benötigt man für ein etwa gleiches Verbrennungsergebnis ca. 5,1 m³/h Erdgas oder ca. 50 %.
Tabelle 1: Flammentemperaturen (Quelle: Wikipedia)
Brennstoff | Flammentemperatur | |
mit Luft | mit reinem Sauerstoff | |
Propan/Butan | 1925 °C | 2850 °C |
Wasserstoff | 2130 °C | 3080 °C |
Methan (Erdgas) | 1970 °C | 2860 °C |
Ethin (Acetylen) | 2250 °C | 3030 °C |
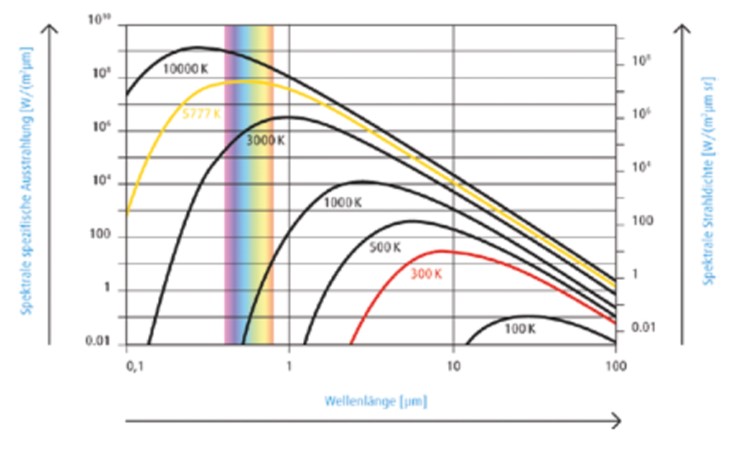
Bei der Erdgas-Sauerstoffverbrennung werden Temperaturen von über 2860 °C erzielt. Alle modernen Brenneranlagen verfügen über die Möglichkeit einer genauen Einstellung des Mischungsverhältnisses (Stöchiometrie). Somit sind Wirkungsgradunterschiede nur in der Konstruktion begründet.
Temperaturübertragung durch Strahlung
Bild 11 zeigt die Temperaturübertragung durch Strahlung.
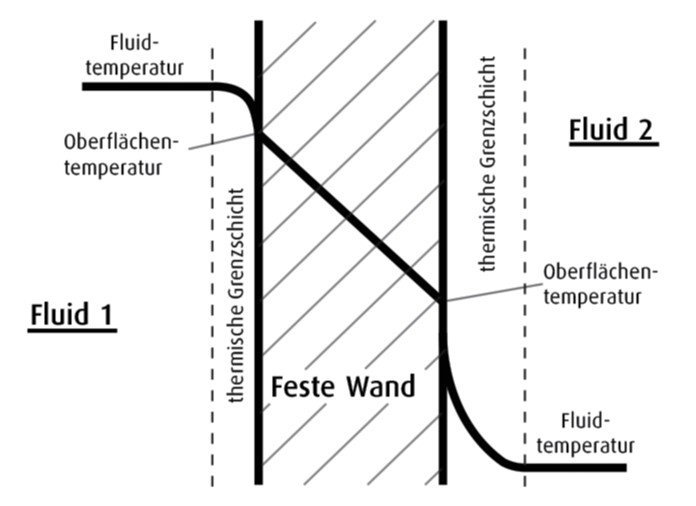
Strahlung bei Porenbrenner
Gastemperatur 1300 K, Wellenlänge 2 μm, spektrale spezifischen Ausstrahlung 105 W/ (m² μm).
Strahlung bei Erdgas-Sauerstoff-Verbrennung
Gastemperatur 3100 K, Wellenlänge 0,77 μm, spektrale spezifische Ausstrahlung 106 W (m² μm).
Durch die höheren Temperaturen ergeben sich kürzere Wellenlängen und somit ein zehnfach höherer Wärmeübergang.
Wärmeübertragung durch Konvektion
Die Berechnung für den Wärmeeintrag eines Gasgemischs von 1000 °C in eine 1300 °C heiße Feuerfestwand lässt keinen physikalischen Ansatz zur Pfannenaufwärmung zu. Die Temperatur der Wandoberfläche führt Wärme in das Brenngas ab. Die Folge ist, dass Wärme aus der Feuerfestwand (Oberfläche) entzogen wird und so die Wandtemperatur fällt (Bild 11), was aber nicht dem Zwecke der Aufheizung von Pfannen dient.
Negative Konvektion
Aber gerade in dieser Phase muss die Oberflächentemperatur auf hohem Niveau gehalten werden, damit die Pfanne für den nächsten Einguss betriebswarm zur Verfügung steht und keinen großen Temperaturschwankungen ausgesetzt ist.
Das Warmhalten im Vergleich – Effekte beim Aufheizen und Warmhalten einer betriebswarmen Pfanne
Porenbrenner
Die konstruktive Anordnung, die eingesetzten Materialien und deren thermische Eigenschaften begrenzen die Temperaturführung zwischen der inneren Pfannenoberfläche und dem Brennermantel des Porenbrennersystems. Die Temperatur ist also direkt abhängig von den eingesetzten Materialien in der Konstruktion des Porenbrenners.
Ein in der Brennerkonstruktion eingebautes Thermoelement begrenzt das Aufheizen auf ca. 1000 °C. Es ist also davon auszugehen, dass sich die Gastemperatur zwischen Brennermanteloberfläche und Feuerfestoberfläche in der Pfanne in einem Bereich bewegt, die nur unwesentlich größer ist.
Die natürliche Abkühlkurve aus Bild 12 wurde mit einer Pfannenabdeckung vorgenommen. Es erfolgte kein zusätzlicher Energieeinsatz. Ein schnelles Abdecken der Pfanne ist deshalb vorteilhafter als der Porenbrennereinsatz.
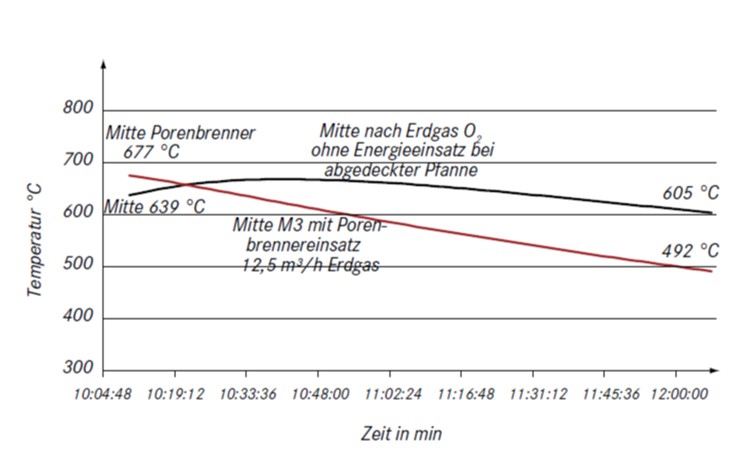
Brennereinsatz
Bei dem Einsatz des Porenbrenners kühlte die Pfanne trotz Energieeinsatz aus.
Vergleich Warmhalten (Messpunkt M1 innen (2,5 cm))
Direkt nach dem Abgießen wurde die Pfanne unter den jeweiligen Brennerstand gefahren. Es galt, den Nachweis zu führen, dass die Pfanne auf einem maximalen Temperaturniveau gehalten werden kann.
Aus Bild 13 wird deutlich, dass die vorgenannten physikalischen Gegebenheiten dazu führen, dass durch den Porenbrennereinsatz die Oberfläche auskühlt (Messpunkt 1 Innen) und somit den Effekt der heißen Randschicht negiert.
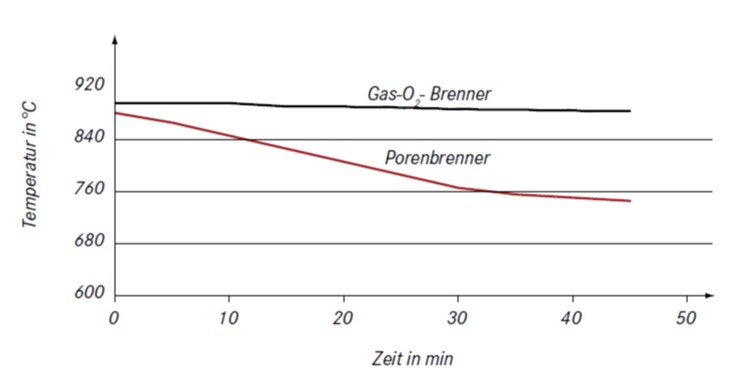
Die Folge ist die Erkenntnis, dass der Porenbrenner erst nach Erreichen von Temperaturen < 500 °C eingesetzt werden sollte (Messpunkt 3). Das bedeutet eine Wartezeit von mehr als 3 h nach Einsatz, ohne dass danach der reale Effekt einer betriebswarmen Aufheizung erreicht wird.
Erdgas-Sauerstoffbrenner
Ein sofortiger Einsatz eines Erdgas- Sauerstoffbrenners kostet Energie und kann zur Überhitzung der Pfannen führen. Eine Überwachung mittels Thermoelement ist unabdingbar. Es können auch Laufzeiten in Abhängigkeit mit der Pfannengröße programmiert werden.
Bild 4 zeigt auf, wie sich eine Pfannenabdeckung auf eine betriebswarme Pfanne und deren Abkühlung auswirkt. Nach ca. 60 min wird eine Temperatur von 605 °C (Messpunkt Mitte) erreicht. Das entspricht fast dem Ausgangszustand.
Vergleich
Bei dem Einsatz eines Erdgas-Sauerstoffbrenners konnten Betriebzustände bei energetischer Kostengleichheit für das Beheizen mit konventioneller Porenbrennertechnologie erzielt werden, die der einer betriebswarmen Pfanne nahe kommen. Der fehlende Energieanteil bei der Beheizung mittels Porenbrenner müsste durch eine höhere Abstichtemperatur ausgeglichen werden oder es muss mit größeren Temperaturverlusten beim ersten Abguss gerechnet werden (Differenz bis zu 60 °C bei der untersuchten Pfanne). Die Kostennutzungsrechnung fällt in der Gesamtbilanz deutlich für den Erdgas-Sauerstoffbrenner aus.
Die Vorteile:
- Hohe Flexibilität, Betriebstemperatur nach 60 bis 90 min
- Schnelle Verfügbarkeit
- Längere Standzeit
- Temperaturwechselbeständigkeit verbessert
- Saubere Pfannen
- Abstichtemperatur des Induktionsofens wird reduziert
- Weniger Reparaturaufwand (ausbessern)
Kostenvorteil des Erdgas- Sauerstoffbrenners
Insbesondere die betriebswarme Verfügbarkeit der Pfanne bei einer Aufheizung mittels Erdgas-Sauerstoffbrenner zeigt nachvollziehbare Kosteneinsparungspotenziale auf, die den „Temperaturfluss“ auf den kostenoptimalen Punkt bringt.
Die Reduzierung der notwendigen Energiekosten am Schmelzaggregat ist offensichtlich nachweisbar. Im Weiteren wird die Problematik der Temperaturwechselbeständigkeit von Pfannen an den Prozess angepasst und garantiert in Verbindung mit sauberen Pfannen eine längere Standzeit.
Die Aussage zu „sauberen Pfanne“ ist insoweit begründet, dass Anhaftungen aus dem Vergießprozess bei hohen Temperaturen abschmelzen und sich am Pfannenboden absetzen.
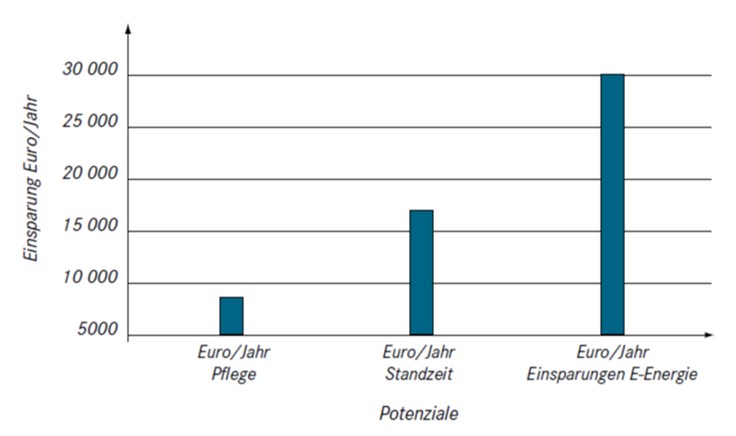
Fazit
Das Einsatzfeld des Porenbrenners in der Eisengießerei ist eingeschränkt. Im Bereich niedriger Abgusstemperaturen, bei großen Wandstärken und zur Trocknung von Pfannen ist sein Einsatz jedoch zu rechtfertigen.
Im Vergleich erreicht der Einsatz eines Erdgas-Sauerstoffbrenners zur Pfannenaufheizung mit geringeren Energiekosten ein physikalisch optimales Betriebsergebnis.
Heinz Kadelka , VMM Marketing Development Metallurgy Linde AG, Geschäftsbereich Linde Gas, Düsseldorf, und Mike Weber, Leiter Schmelzbetrieb, Gienanth GmbH, Eisenberg