Steigerung der Energie- und Ressourceneffizienz in der Produktion
Von Christoph Herrmann, Tim Heinemann und Sebastian Thiede, Braunschweig
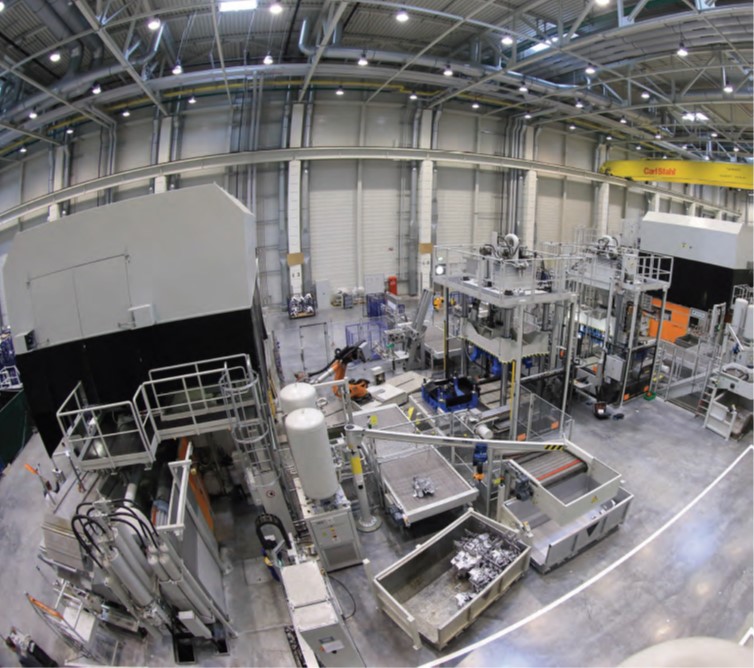
Fertigung von Aluminiumdruckgussteilen in der neuen Audi-Druckgießerei in Münchsmünster. Die neue Gießerei für Strukturbauteile gilt als eine der weltweit modernsten. Bei ihrer Planung spielten Energie- und Ressourceneffizienz eine große Rolle.
Erschienen in GIESSEREI 02/2015
Neben klassischen Zielgrößen wie Auslastung, Durchlaufzeiten/Termintreue und Qualitätsraten sollten künftig auch Energie- und Ressourcenverbräuche in die betrieblichen Entscheidungsprozesse einfließen.
Aus ökonomischen und ökologischen Motiven kommt der bewussten Betrachtung von Energie- und Ressourcenverbräuchen in der Produktion eine immer wichtigere Bedeutung zu. Eine realistische und zielgerichtete Analyse und Ableitung von Effizienzpotenzialen verlangt allerdings ein ganzheitliches, systemorientiertes Verständnis, um z. B. Zielkonflikte zu lösen und Problemverschiebungen vermeiden zu können. Dies umfasst z. B. ein erweitertes Prozessverständnis mit allen Eingangs- und Ausgangsgrößen und realistischem Verbrauchs-/Emissionsverhalten sowie die notwendige Berücksichtigung von Wechselwirkungen mit der technischen Gebäudeausstattung. Im Themenfeld Energie- und Ressourceneffizienz ergeben sich verschiedene Handlungsfelder. Basierend auf einmaliger oder permanenter Datenerfassung, dem Verstehen von Zusammenhängen sowie geeigneten Methoden zur Bewertung und Vorhersage von Betriebsverhalten (z. B. über energieorientierte Simulation) gilt es letztendlich, Energie- und Ressourcenverbräuche neben klassischen Zielgrößen (z. B. Auslastung, Durchlaufzeiten/Termintreue, Qualitätsraten) als weitere Dimension in die betriebliche Entscheidungswelt zu integrieren. Beispiele für ganzheitliche Betrachtungsansätze finden sich in den BMBFgeförderten Projekten ProGRess und EnHiPro. ProGRess (Gestaltung ressourceneffizienter Prozessketten am Beispiel des Aluminiumdruckgusses, www.progress-aluminium.de) fokussierte die Bewertung und Gestaltung der energieintensiven Prozesskette Aluminiumdruckguss hinsichtlich des Energie- sowie des Materialeinsatzes. In EnHiPro (Energie- und hilfsstoffoptimierte Produktion, www.enhipro.de) lag das Ziel in der notwendigen Integration von Energie- und Hilfsstoffverbräuchen in das betriebliche Produktionsmanagement mit besonderem Fokus auf produzierende kleine- und mittlere Unternehmen (KMU). Diese wurden kontinuierlich in die Lage versetzt, organisatorische und technische Maßnahmen zur Effizienzsteigerung zu ermitteln und die Auswirkungen zu bewerten.
Motivation
Produktion ist „die Erzeugung von Ausbringungsgütern (Produkten) aus materiellen und nicht-materiellen Einsatzgütern (Produktionsfaktoren) nach bestimmten technischen Verfahrensweisen“ [1] und damit ein gleichzeitig wertschöpfender wie wertverzehrender Transformationsprozess. Neben menschlicher Arbeit und Betriebsmitteln stellen hierbei Rohmaterialien und Energie wesentliche Eingangsfaktoren dar. Der effizienten Nutzung von Energie und Ressourcen kommt eine immer stärkere Bedeutung zu. Zum einen sind mit der Gewinnung bzw. Erzeugung teilweise erhebliche Umweltwirkungen verbunden. So verbrauchen produzierende Unternehmen z. B. ca. 47 % der Elektrizität in Deutschland und sind allein dadurch für 18 % der nationalen CO2 Emissionen verantwortlich. (Dazu kommen weitere ca. 20 % durch direkte Emission, z. B. Feuerungen) [2]. Zum anderen ist die Gewinnung und Aufbereitung von Rohstoffen ebenfalls oftmals mit erheblichen Umweltbelastungen verbunden, der Bauxitabbau zur Aluminiumherstellung sei hierfür nur beispielhaft erwähnt. Die Vermeidung bzw. Reduzierung von Umweltwirkungen rückt in den letzten Jahren durch gesetzliche Rahmenbedingungen, gesamtgesellschaftliche (Klima-) Diskussion und auch eigenmotivierte Umweltorientierung der Unternehmen verstärkt in den Vordergrund. Darüber hinaus beinhaltet die Berücksichtigung dieser zunächst umweltorientierten Aspekte mittlerweile auch eine klare wirtschaftliche Motivation. Dies liegt vor allem an den in den letzten Jahren gestiegenen bzw. volatilen Preisen für Rohstoffe (z. B. Aluminium) und Energie (Gas, Öl, Elektrizität), was zu erhöhtem Kostendruck in den Unternehmen führte (Bild 1). Trotz momentan aufgrund der gesamtwirtschaftlichen Lage wieder etwas entspannter Preislage, ist zukünftig von weiteren Steigerungen auszugehen. Aus mittel- bis langfristiger Sicht ist in diesem Zusammenhang auch ein möglicher zukünftiger Mangel an strategisch wichtigen Ressourcen ein entscheidender Treiber.
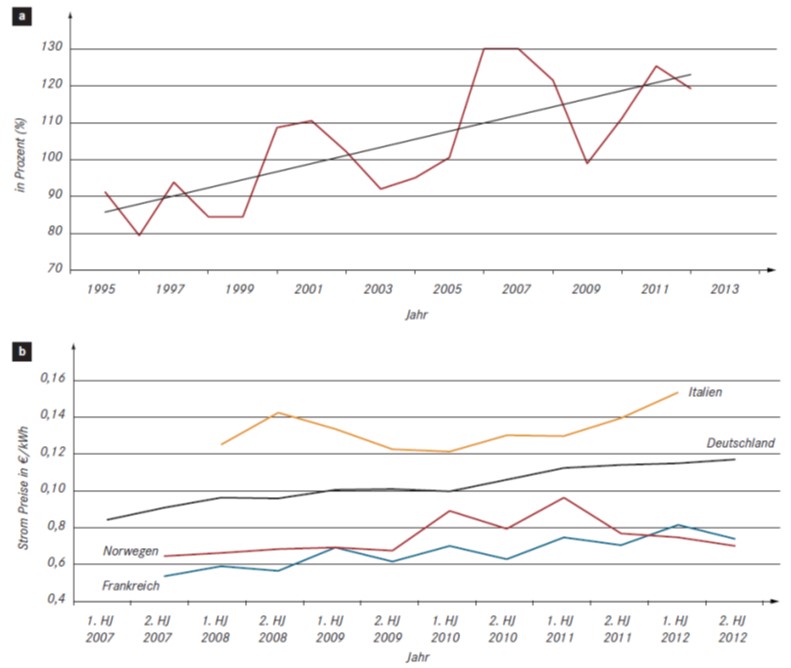
Ganzheitliches Systemverständnis
Eine realistische und zielgerichtete Analyse und Effizienzverbesserung von Energie- und Ressourcenverbräuchen in der Produktion verlangt ein ganzheitliches, systemorientiertes Verständnis, um z. B. Zielkonflikte zu lösen und Problemverschiebungen vermeiden zu können [5]. Hierfür lassen sich einige Voraussetzungen definieren.
Erweitertes Prozessverständnis
Für die Schaffung ganzheitlicher Lösungen und zur Vermeidung von Problemverschiebungen müssen explizit alle In- und Output-Ströme von Produktionsprozessen berücksichtigt werden. Dies umfasst alle energetischen (z. B. Druckluft, Strom, Abwärme) und stofflichen Flüsse (z. B. Hilfsstoffe wie Kühlschmierstoffe), die direkt oder indirekt (z. B. durch notwendige Bereitstellung) zu zusätzlichem Energieund/ oder Ressourcenverbrauch führen.
Ganzheitliche Systemdefinition der Fabrik
Interne Wechselwirkungen der konstituierenden Elemente einer Fabrik verlangen auch ein erweitertes Verständnis des Systems Fabrik als Ganzes. Hiernach sind im Wesentlichen die drei Teilsysteme Produktion (Maschinen und Mitarbeiter koordiniert durch Produktionsplanung und -steuerung), Technische Gebäudeausstattung (TGA) und Gebäudehülle zu unterscheiden. Aufgaben der TGA sind im Fabrikzusammenhang die Sicherstellung notwendiger Umgebungsbedingungen der Produktion (z. B. Klimatisierung) sowie die Herstellung, Bereitstellung und Aufbereitung (bei Kreislaufführung) notwendiger Medien und Energie (z. B. Druckluft, Prozesswärme in Form von Dampf, Warm-/ Kaltwasser). Dazu wird ebenfalls Energie in Form von Elektrizität, Gas oder Öl benötigt bzw. direkt aus regenerativen Energiequellen erzeugt (z. B. Solarenergie, Windenergie, Biomassekraftwerk). Wie in Bild 2 dargestellt, sind die drei Teilsysteme keinesfalls isoliert zu betrachten, es gilt vielmehr, die systemdynamischen Abhängigkeiten zu berücksichtigen. Eine Bewertung der Energieeffizienz einer Fabrik muss z. B. alle von außerhalb des Systems zugeführten nichtregenerativen Energieströme (z. B. Strom, Öl, Gas) berücksichtigen - sowohl den Energiebrauch der Produktion als auch den der technischen Gebäudeausstattung [6].
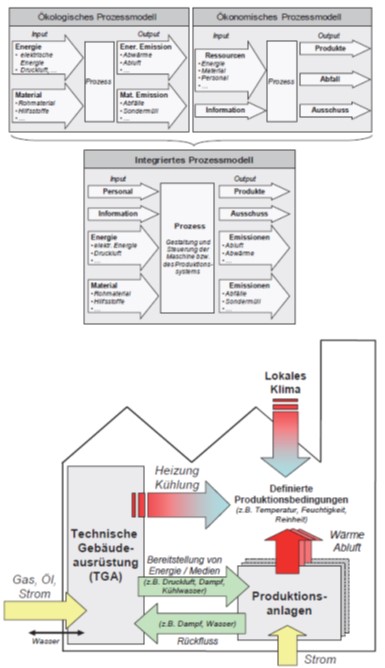
Dynamik des Verbrauchs-/ Emissionverhaltens und Wechselwirkungen
Alle relevanten In- und Output-Ströme sind überwiegend dynamische Größen und hängen vom Betriebszustand der Prozesse bzw. der Maschinen ab. Auf Fabrikebene ist erst das dynamisch auf Basis von Einzellastprofilen und Wechselwirkungen entstehende Gesamtlastprofil (z. B. Prozesswärmebedarf, Druckluftbedarf, Wärmefluss in die Fabrikhalle) entscheidend für Auslegung und Aussteuerung der TGA.
Denken in Prozessketten
Endprodukte sind normalerweise nicht Resultat eines einzelnen Fertigungsprozesses, sondern entstehen vielmehr in mehreren Schritten auf verschiedenen Produktionsanlagen im Sinne einer Produktionsprozesskette. Vor dem Hintergrund der Energie- und Ressourceneffizienz muss die Prozesskette als Ganzes betrachtet und bewertet werden, da hier ggfs. weitere Potenziale liegen (z. B. Zusammenfassung von Prozessen) oder aber verbessernde Maßnahmen in einem Prozess ggfs. zu einer Verschlechterung in anderen Teilprozessen führen können.
Lebenszyklusorientierte Sichtweise
Analog zur Denkweise in Prozessketten müssen bei Verbesserungsmaßnahmen der Energie- und Ressourceneffizienz alle Lebensphasen von Produkten (dies sind auch die Betriebsmittel selbst) berücksichtigt werden, da auch hier Problem verschiebungen entstehen können oder Potenziale ungenutzt bleiben. So liegt der entscheidende Hebel zur Erhöhung der Energieeffizienz von z. B. Werkzeugmaschinen natürlich weniger bei der Verbesserung einzelner Parameter eines speziellen Prozesses, sondern vielmehr bereits bei der Entwicklung der Maschine selbst. Auch hat die Wahl bestimmter Prozesse (z. B. Fügeverfahren) direkte Auswirkungen auf Nutzungs- und Entsorgungsphase (z. B. Festigkeit, Demontierbarkeit), was dort zu erhöhten Aufwänden führen kann.
Berücksichtigung aller Nachhaltigkeitsdimensionen und integrierte Bewertung
Zur Ableitung vorteilhafter Lösungen sind mehrere relevante Zieldimensionen integrativ zu berücksichtigen. Neben einer ökologischen Bewertung (mit korrekter Verrechnung der verschiedenen Eingangs- und Ausgangsgrößen, z. B. Umweltauswirkung von Strom- bzw. Gasverbrauch) umfasst dies eine realistische wirtschaftliche (auf Basis eines geeigneten Kostenmodells, das reale Vertragskonditionen berücksichtigt) und technische Betrachtung (z. B. Auswirkungen auf Produktqualität). Mögliche Zielkonflikte müssen aufgezeigt und Entscheidungsunterstützung zu deren Lösung angeboten werden.
Vor dem Hintergrund dieser Ausführungen zeigt Bild 3 Handlungsfelder im Themenfeld Energie- und Ressourceneffizienz in der Produktion. Hierbei kann zwischen der Maschinen- bzw. Prozessperspektive und der Sichtweise auf Prozessketten bzw. Fabriksysteme differenziert werden, wobei beides unmittelbar zusammenhängt. Basierend auf einmaliger oder permanenter Datenerfassung, dem Verstehen von Zusammenhängen sowie geeigneten Methoden zur Bewertung und Vorhersage des Betriebsverhaltens gilt es letztendlich, Energie- und Ressourcenverbräuche neben klassischen Zielgrößen (z. B. Auslastung, Durchlaufzeiten/ Termintreue, Qualitätsraten) in der betrieblichen Entscheidungswelt zu etablieren. Angelehnt an diese Systematik werden in den folgenden Abschnitten einzelne Elemente anhand von Beispielen detaillierter erläutert.
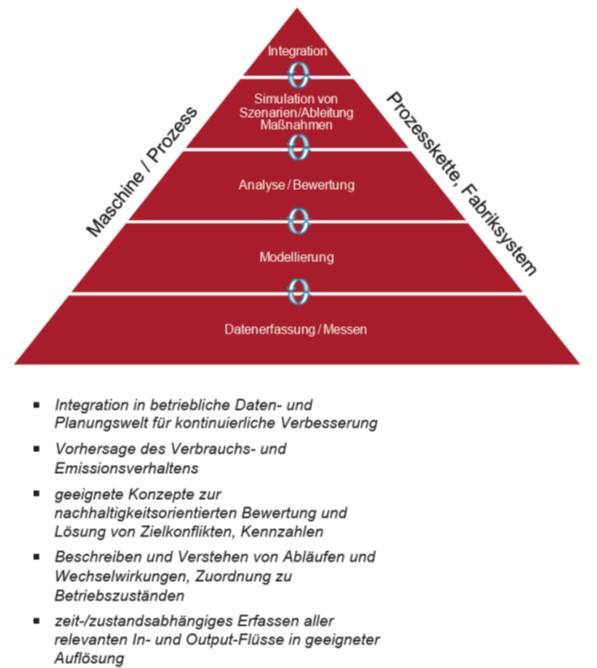
Das Aluminiumdruckgießen als energie- und ressourceneffiziente Prozesskette
Die Wettbewerbsfähigkeit der deutschen Aluminiumdruckgussindustrie ist aufgrund hoher branchenspezifischer Energieverbräuche eng mit den aktuell vorherrschenden, hohen Energiepreisen gekoppelt. Die notwendige Energie wird im Wesentlichen zum Erwärmen und Schmelzen des Aluminiums, für die Druckgießmaschine mit den Peripheriegeräten und für die Formtemperierung benötigt. Die Wärmebilanz des Gesamtprozesses ist dabei durch hohe Energieverluste gekennzeichnet, die in Bild 4 dargestellt sind. Die energetischen Verluste wurden im Rahmen eines von der Deutschen Bundesstiftung Umwelt (DBU) geförderten Projektes zur Energiebilanz des Druckgießprozesses ermittelt [7]. Es wird deutlich, dass ein großer Teil der eingebrachten Energie während des Prozesses in Form von Wärme bzw. durch Kühlvorgänge verloren geht. Insgesamt sind die hohen Wärmeverluste im Druckgießprozess unter Gesichtspunkten des Umweltschutzes als äußerst unbefriedigend anzusehen.
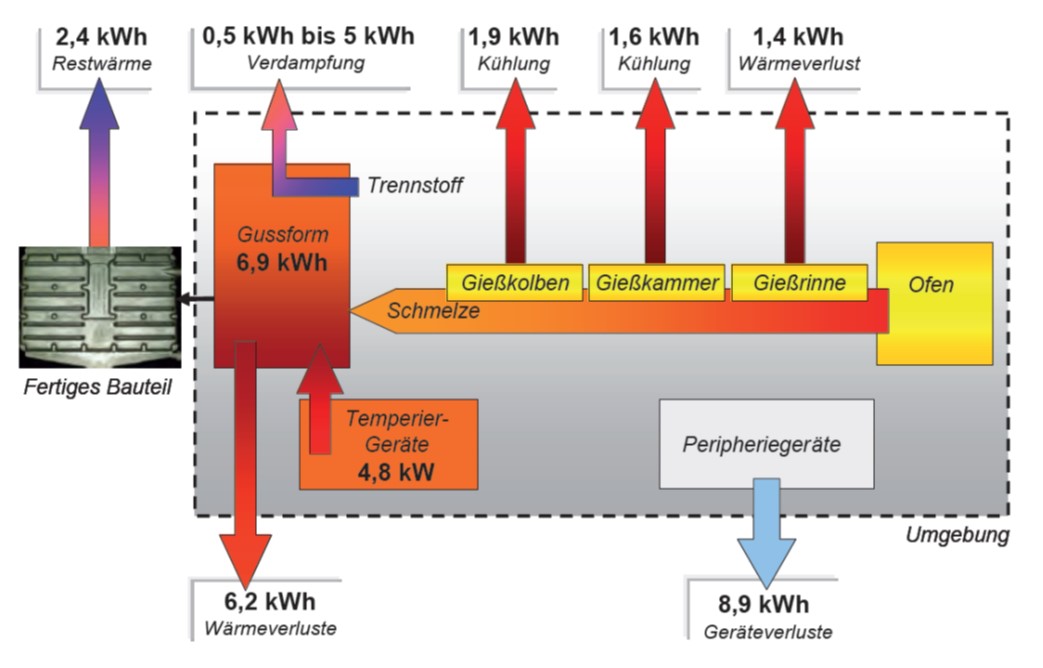
Neben der Betrachtung der effizienten Nutzung von Energie und Hilfsstoffen bei der Herstellung von Aluminiumgussteilen ist auch die möglichst effiziente Bereitstellung und Nutzung des Aluminiums selbst von wichtiger Bedeutung. Je nach Teilespektrum, Anzahl der verwendeten Legierungen und vorrätiger Infrastruktur wird die Schmelzebereitstellung aus Masseln/ Kreislaufmaterial und Aufarbeitung in der Gießerei vorgenommen oder die flüssige Legierung wird direkt in Thermobehältern angeliefert. Es bestehen somit diverse Stoffkreisläufe, in denen Material in unterschiedlichen Qualitäten immer wieder erschmolzen und aufgearbeitet werden muss. Allerdings ist gerade die prozessbedingt nicht vollständige Ausnutzung des Rohstoffs Aluminium im Prozess problematisch. Überlauf und Anguss (die bis zu 50 % der gegossenen Form ausmachen können) sowie fertige Bauteile, die nicht der geforderten Qualität entsprechen, oder Teile aus dem Anfahrprozess werden zum Teil als Recyclingmaterial in Masseln umgeschmolzen und müssen den gesamten energieintensiven Prozess erneut durchlaufen. Dies betrifft je nach Fertigungsparametern bzw. Bauteil 30 – 70 % des ursprünglich eingebrachten Materials. Darüber hinaus fallen 2 – 5 % Materialverluste an, die nicht wieder in den Prozess eingebracht werden können (z. B. durch starke Verunreinigungen) und somit verloren sind [8]. Während diese Verluste aus Sicht des Unternehmens vor allem wegen der Materialkosten entscheidend sind, ist aus Umweltsicht die energieintensive und umweltschädigende Gewinnung von Aluminium als große Herausforderung zu sehen (Abfälle mit Umweltgefährdungspotenzial, große Flächen zum Abbau von Bauxit notwendig, Elektrolyse zur Aluminiumgewinnung). Damit führt eine Verbesserung der Materialeffizienz und damit Reduktion des Aluminiumverbrauchs aus globaler Sicht indirekt ebenfalls zu einer erheblichen Senkung des Energiebedarfs und weiterer schädlicher Umweltwirkungen.
In einem vom Bundesministerium für Bildung und Forschung (BMBF) geförderten Projekt ProGRess wurde in Einklang mit dem erweiterten Prozess- und Systemverständnis ein integrierter Ansatz verfolgt. Neben der isolierten Analyse von Material- und Energieverbräuchen und -verlusten einzelner Prozesse wurde in ProGRess die Bewertung und Gestaltung der gesamten Wertschöpfungskette des Aluminiumdruckgießens hinsichtlich des Energie- sowie des Materialeinsatzes angestrebt. Hierfür wurde eine Betrachtung der Energieverbräuche und Stoffströme von der Ebene der Einzelprozesse über einzelne Produktionssysteme bis hin zu unternehmensübergreifenden Lieferketten entlang der Prozesskette Aluminiumdruckgießen durchgeführt.
Ausgehend von Unternehmenskennzahlen wurden zunächst Verbrauchskennwerte der Anwenderunternehmen generiert und als Effizienzmaß für das individuelle Produktionssystem genutzt. So konnten erste Zusammenhänge zwischen Produktionsvolumen und Produktionssystemen in Beziehung zum Ressourcenverbrauch und Energieaufwand pro Fertigteil identifiziert werden. Für die unternehmensinterne Prozesskette vom Einschmelzen des Materials über das Warmhalten und Dosieren an der Druckgießanlage und den Druckgießprozess selbst bis hin zur mechanischen Nachbearbeitung lassen sich so als Folge unterschiedlicher Automatisierungsgrade, Nutzungsgrade und Losgrößen auch stark differierende Verbrauchsgrößen hinsichtlich der verwendeten Energieträger dokumentieren. Bild 5 zeigt die Anteile der Energieträger Gas und Elektrizität an dem Energiebedarf pro Kilogramm endbearbeitete Gussteile über die hausinterne Prozesskette zweier ausgewählter Gießereien.
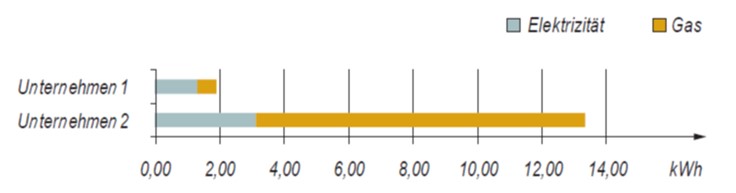
Wie aus Bild 6 ersichtlich ist, können für ausgewählte Verbraucher charakteristische Lastgänge (hinsichtlich Standby-Verbräuchen, Lastspitzen, lastabhängigen Niveaus, etc.) dokumentiert werden, die im Rahmen des Projektes ProGRess auch in anderen Produktionsumgebungen der Aluminiumdruckgussbranche beobachtet werden konnten und sich teilweise nur durch einen Skalierungsfaktor unterscheiden. Sie bieten sich also an, um bereits bei der Planung einer neuen Druckgießlinie oder auch im Rahmen einer dynamischen Simulation der Aluminiumdruckgussfertigung herangezogen zu werden. So kann bereits vor Inbetriebnahme neuer Produktionssysteme oder aber auch bei der Änderung von Prozessparametern frühzeitig das Verhalten der Prozesskette vorherbestimmt und energetisch effizient ausgelegt werden. Darüber hinaus lassen sich die aufgenommenen Lastgänge auch zur Effizienzsteigerung in bereits bestehenden Druckgießzellen nutzen, um sowohl technologische als auch organisatorische Potenziale zu identifizieren und Maßnahmen abzuleiten. Auf diesem Wege können sowohl auf Einzelprozessebene als auch unternehmensübergreifend Hebel zur Steigerung der Energie- und Ressourceneffizienz identifiziert werden, um Emissionen von Klimagasen dauerhaft reduzieren und gleichzeitig die Wettbewerbsfähigkeit der deutschen Aluminiumdruckgussbranche sichern zu können.
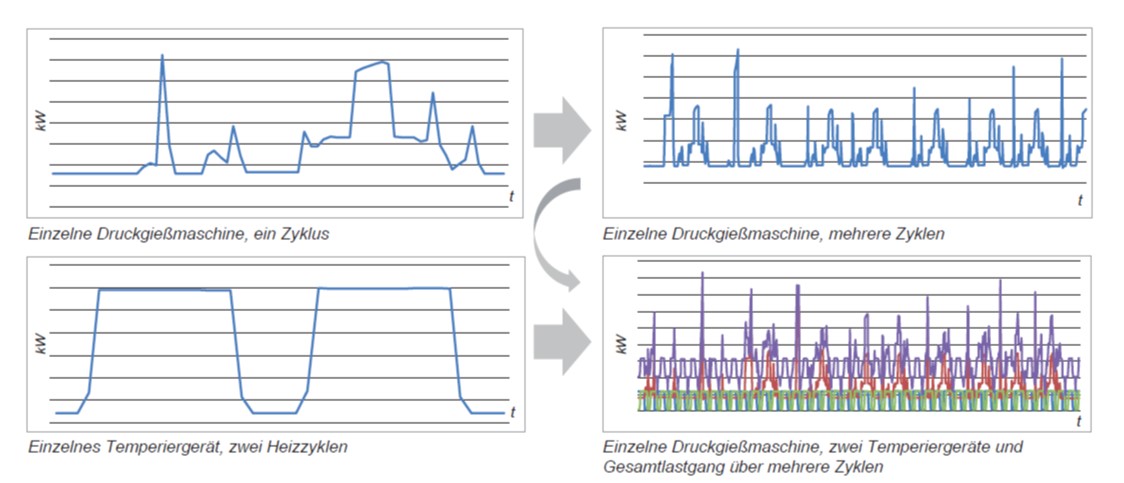
Energieorientierte Simulation
Für eine realistische, energie- und ressourceneffiziente Auslegung von Systemen mit mehreren Maschinen ist die Berücksichtigung der Verbrauchs- und auch Emissionsdynamik von großer Bedeutung. So können nichtwertschöpfende Verluste aufgezeigt und Gegenmaßnahmen eingeleitet werden. Auch sind Belastungsspitzen sowohl aus wirtschaftlicher (z. B. Leistungs-/Leistungsüberschreitungpreiskomponente in Energieversorgungsverträgen) als auch aus technischer Sicht (z. B. Auslegung des elektrischen Netzes und TGA) von großer Bedeutung. Da statische Ansätze hierzu nicht mehr ausreichend sind, wurde zur energieorientierten Analyse und Bewertung von Prozessketten bzw. Fabriksystemen ein geeigneter Simulationsansatz entwickelt [9] [10] [11]. Hiermit können Produktionssysteme mit allen Anlagen und den relevanten energetischen und stofflichen Flüssen modelliert werden. Zudem werden Wechselwirkungen mit der TGA wie z. B. die notwendige Energie zur Bereitstellung von Druckluft berücksichtigt. Bild 7 zeigt beispielhaft Ergebnisse einer Fallstudie: Auf Basis eines modellierten Produktionssystems wurden Szenarien (in diesem Fall Variationen im Bereich Produktionsplanung und -steuerung) simuliert und eine integrierte Bewertung nach ökologischen (Stromverbrauch), wirtschaftlichen (Stromkostenberechnung auf Basis eines realen Vertragsmodells mit Leistungspreis) und technischen (Produktionszeit) Gesichtspunkten durchgeführt. Die Diagramme zeigen das resultierende Lastprofil verschiedener Szenarien. Es fällt auf, dass das energetische Verhalten des Produktionssystems wesentlich durch Produktionsplanung und -steuerung beeinflusst werden kann. Auch zeigen sich in diesem Fall Zielkonflikte zwischen den verschiedenen Bewertungsdimensionen. Wie dargestellt, ist auf dieser Basis nun eine integrierte Bewertung und die Ableitung von vielversprechenden Maßnahmen möglich (im Beispiel ist z. B. Szenario 3 zu bevorzugen), die sich aus der Gesamtsicht ergeben.
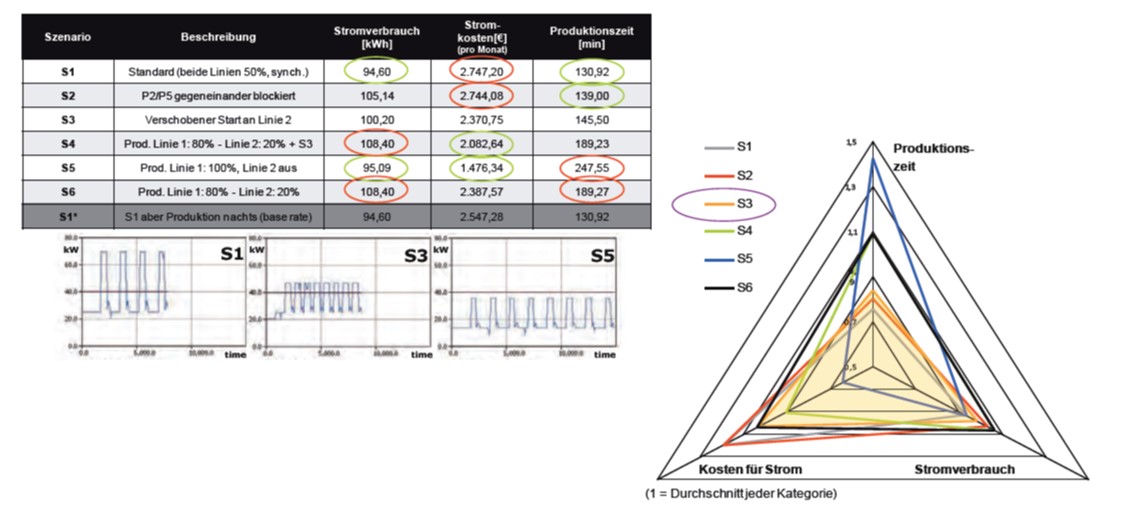
Energie- und hilfsstoffoptimierte Produktion
In Forschung und industrieller Praxis sind mittlerweile eine Vielzahl möglicher Maßnahmen zur Erhöhung der Energie- und Ressourceneffizienz grundsätzlich bekannt [12]. Allerdings fehlt es insbesondere für KMU an Entscheidungsunterstützung bzgl. konkreter Einsetzbarkeit und Wirksamkeit solcher Ansätze im speziellen Fall. Mit dem BMBF-geförderten Projekt EnHiPro wurden produzierende KMU auf kontinuierlicher Basis in die Lage versetzt, solche organisatorischen und technischen Maßnahmen zur Effizienzsteigerung zu ermitteln und die Auswirkungen zu bewerten. Neben Strom-, Gas- oder Ölverbräuchen wurden hierbei explizit auch andere Energieformen bzw. Hilfsstoffe wie z. B. Druckluft, Prozesswärme oder Kühlschmierstoffe berücksichtigt. Wie in Bild 8 dargestellt, lag das Ziel in der notwendigen Integration von Energieund Hilfsstoffverbräuchen in das betriebliche Produktionsmanagement.
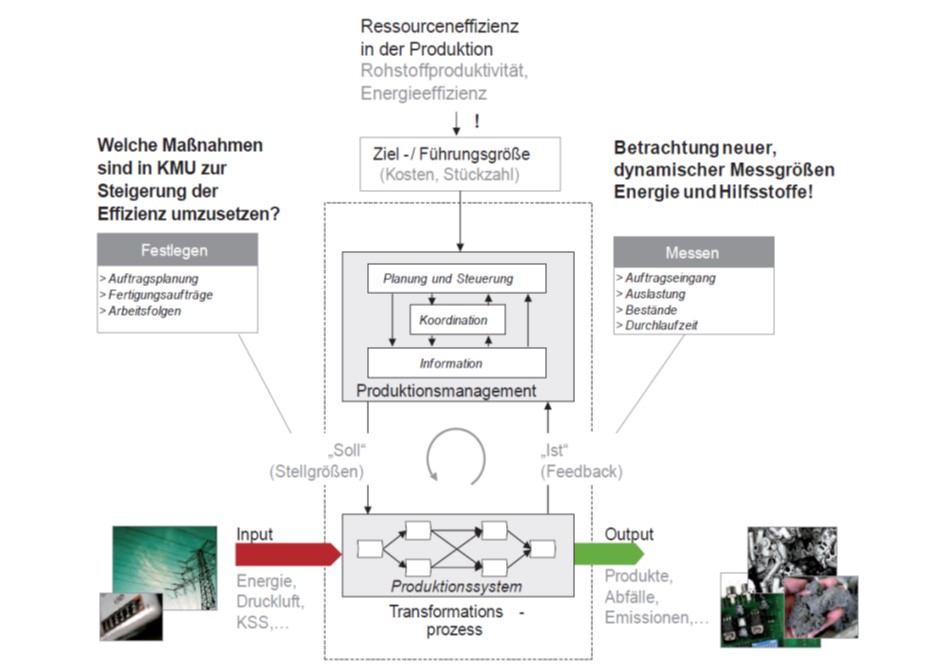
Durch eine geeignete Verknüpfung von Messtechnik und IT-Anwendungen zur Verbrauchserfassung und -kontrolle wurden hierfür die realen Verbrauchswerte zunächst erfasst und visualisiert. Diese Daten bilden die Grundlage zur Analyse und Bewertung von Maßnahmen zur Optimierung der Energie- und Hilfsstoffeffizienz, indem Effekte und Potenziale von Maßnahmen vorhergesagt und visualisiert werden. Auf Basis einer energie- und hilfsstoffverbrauchsorientierten Auswertung von Prozessketten wird hiermit ein Beitrag zur Schließung der vielfach zu beobachtenden Lücke zwischen Wissen und Handeln geleistet.
Die finalen Ergebnisse der Projekte ProGRess („Energie- und ressourceneffiziente Produktion von Aluminiumdruckguss”, Christoph Herrmann, Helge Pries, Götz Hartmann [Hrsg.], ISBN 978-3-642-39853-7) und EnHiPro („Energie- und hilfsstoffoptimierte Produktion“, Christoph Herrmann, Gerrit Posselt, Sebastian Thiede [Hrsg.], ISBN 978-3-642-38692-3) wurden im Springerverlag veröffentlicht und sollen auch branchenübergreifend als Anregung für weitere Effizienzmaßnahmen dienen.
Der Beitrag basiert auf einer Originalveröffentlichung im Konferenzband der Tagung „Karlsruher Arbeitsgespräche 2010“
Prof. Dr.-Ing. Christoph Herrmann, Dipl.- Wirtsch.-Ing. Tim Heinemann, Dr.-Ing. Dipl.-Wirtsch.-Ing. Sebastian Thiede, Technische Universität Braunschweig, Institut für Werkzeugmaschinen und Fertigungstechnik, Professur für Nachhaltige Produktion und Life Cycle Engineering
Literatur:
[1] Günther, H.-O.; Tempelmeier, H.: Produktion und Logistik [Hauptbd.], Springer, 6. Auflage, 2005.
[2] Bundesministerium für Wirtschaft und Technologie, Energiedaten -nationale und internationale Entwicklung, 2009, verfügbar unter www.bmwi.de/BMWi/Navigation/Energie/energiestatistiken.html
[3] www.destatis.de, 2013a, Daten zur Energiepreisentwicklung – Lange Reihen von Januar 2000 bis Februar 2013, Statistisches Bundesamt, www.destatis.de/DE/Publikationen/Thematisch/Preise/Energiepreise/Energiepreisentwicklung.html.
[4] www.destatis.de, 2013b, Preise – Index der Einfuhrpreise, Statistisches Bundesamt, www.destatis.de/DE/Publikationen/Thematisch/Preise/Aussenhandelspreise/EinfuhrpreiseLangeReihenPDF_5614101.html.
[5] Herrmann, C.: Ganzheitliches Life Cycle Management, Springer, 2009.
[6] Hesselbach, J.; Herrmann, C.; Detzer, R.; Martin, L.; Thiede, S.; Lüdemann, B.: Energy Efficiency through optimized coordination of production and technical building services, In: 15th CIRP International Conference on Life Cycle Engineering, Sydney, Australien, Seiten 624-629, 2008, ISBN 978-1-877040-67-2.
[7] Optimierung der Energiebilanz beim Aluminium-Druckgießprozess, Abschlussbericht September 2007, Deutsche Bundesstiftung Umwelt, Förderkennzeichen AZ 22197, Institut für Füge- und Schweißtechnik, TU Braunschweig.
[8] Institut für Füge- und Schweißtechnik, TU Braunschweig.
[9] Herrmann, C., Thiede, S.: Increasing Energy Efficiency in Manufacturing Companies through Process Chain Simulation, In: Sustainability and Remanufacturing VI
- Global Conference on Sustainable Product Development and Life Cycle Engineering, Pusan, Korea, Seiten 52-57, 2008.
[10] Herrmann, C., Thiede, S.: Process chain simulation to foster energy efficiency in manufacturing, In: CIRP Journal of Manufacturing Science and Technology, Elsevier, 2009, ISSN 1755-5817.
[11] Thiede, S.: Energy Efficiency in Manufacturing Systems, Springer, 2012.
[12] Seefeldt, F; Wünsch, M.; Baumgartner, W.; Matthes, U.: Energieeinsparung und Energieeffizienz. Potenzialermittlung im Auftrag des BMWi 18/06, Prognos AG, 2007.