Energieeinsparung gegenüber anderen Fertigungsverfahren
Moderne Gießverfahren und Gusswerkstoffe ersetzen vielfach Schweiß-, Niet- und Schraubkonstruktionen und führen zu deutlichen Materialeinsparungen und zu energieeffizienter Fertigung.
Die Fertigung endkonturnaher Gussteile realisiert hohe Energieeffizienz, beispielweise durch Verringerung des Anteils spanender Bearbeitung.
Für die spanende Bearbeitung ist ein hoher Energieaufwand (spezifischer Energieaufwand je t Späne) notwendig, der den Energieaufwand für das Schmelzen (spezifischer Energieaufwand je t Schmelze) erreicht und Angaben zufolge sogar übersteigen kann.
In einem Beitrag von Ketscher, N. et al. [44] werden die Vorteile des Fertigungsverfahrens Gießen gegenüber den Fertigungsverfahren „Spanen“ und „Fügen“ dargestellt.
Anhand zweier Fallstudien (Flachteil aus Stahlhalbzeug und bei der Rahmenstruktur einer Airbus-Passagiertür aus Aluminiumhalbzeug) wird nachgewiesen, dass die Formgebung durch Gießen im Vergleich zum Spanen und zum Fügen zu Materialeinsparungen und geringerem Energieeinsatz führt.
1. Energieeinsparung gegenüber dem Fertigungsverfahren „Spanen“
Untersuchungen zeigen, dass für das Spanen ein hoher Energiebedarf erforderlich ist [44].
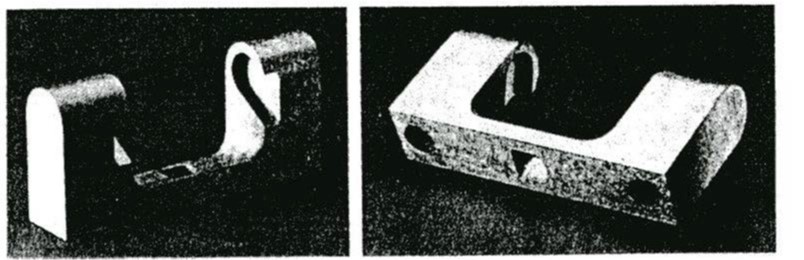
Das in der Abbildung dargestellte Bauteil wurde bislang durch Spanen aus einem Flachmaterialzuschnitt (Werkstoff St60, warmgewalzt, DIN 1017) mit den Ausgangsabmessungen 70*30*150 mm hergestellt.
Der Vergleich der Herstellung des Bauteils durch Spanen und der Herstellung des Bauteils durch Gießen erfolgt an Stoff- und Energiebilanzen.
Für den vorliegenden Fall wurden der Energiebedarf am Spanwerkzeug, der spezifische Nutzenergiebedarf an der Werkzeugschneide, der Direktenergiebedarf der eingesetzten Werkzeugmaschine, der bauteilbezogene Primärenergieaufwand des Vorgangs der Zerspanung und der Produktionsenergiebedarf, einschließlich Nebenverbrauch, mit 3,838 GJ/t Fertigteil ermittelt.
Für das vergleichbare Gussbauteil aus der Tempergusssorte GTW-S 38-12 nach DIN 1692, GJMW-360-12 nach DIN EN 1562, Ausgabe August 1997, wurden zunächst die Betriebsdaten einer Tempergießerei für die Gattierung, den jährlichen Verbrauch der Energieträger, das Gussteilausbringen und die Jahresproduktion erfasst:
Tabelle1: Betriebsdaten aus der Tempergießerei
Gattierung | 7,5 % Roheisen 60,3 % Kreislaufmaterial 32,2 % Stahlschrott |
Energieträger | 604.677m3/a Gas 3.156.340 kWh/a Elektroenergie 1.451 t/a Koks 62.369 kg/a Öl |
Produktion | 3.919 t/a |
Gussteilausbringung | 40 % |
Mit Hilfe der Heizwerte und der Energieumwandlungsgrade sind der Verbrauch an Nutzenergie und an Primärenergie sowie der spezifische Energieaufwand für die Herstellung einer Tonne Gussteile ermittelt worden:
Tabelle 2: Spezifischer Energieaufwand in der Tempergießerei
Nutzenergie | 19.190 GJ/a Gas 11.362 GJ/a Elektroenergie 41 GJ/a Koks 2.663 GJ/a Öl |
Primärenergie | 20.200 GJ/a Gas 35.506 GJ/a Elektroenergie 46 GJ/a Koks 2.956 GJ/a Öl |
Spezifischer Energieaufwand (GJ/t Gussteil) | 8,486 GJ/t Nutzenergie 14,980 GJ/t Primärenergie |
Energieaufwand Roheisen | 2,482 GJ/t |
Energieaufwand Kreislaufmaterial | 0 |
Energieaufwand Stahlschrott | 0 |
Gesamtbilanz Gussteilfertigung | 14,980 GJ/t 2,482 GJ/t |
17,462 GJ/t |
Unter Einbeziehung des Roheisenanteils in der Gattierung und des spezifischen Energieaufwandes (Primärenergie) für die Produktion von einer Tonne Roheisen wurde der spezifische Energieaufwand für 1 Tonne Gussteile erfasst.
Bei einem Gussteilausbringen von 40 % werden für eine Tonne Gussteile 2,5 Tonnen Schmelze benötigt. Der Roheisenanteil in der Gattierung liegt bei 7,5 %. Es ergibt sich ein Verbrauch von 0,188 Tonnen Roheisen für eine Tonne Gussteile.
Der spezifische Energieaufwand wird für eine Tonne Roheisen mit 13,2 GJ angesetzt. Für die Tonne Gussteile fließen demnach 2,482 GJ für Roheisen in die Gussteilfertigung ein. Damit ergibt sich ein spezifischer Energieaufwand von 17,462 GJ/t Gussteile, Tabelle 3.
Die Materialausnutzung ist im vorliegenden Fall nach [44] als eine Schwachstelle der spanenden Fertigung aus dem Stahlhalbzeug zu sehen.
Der Stabstahlabschnitt hatte eine Ausgangsmasse von 2470 g, das Fertigteil eine Masse von 700 g. Die Materialausnutzung beträgt 28,4 %.
Werden bei derartigen Betrachtungen die im Material kumulierte Energie für Stabstahl mit 12,9 GJ/t und die Schmelz- und Warmhalteverluste mit 10 % berücksichtigt, so ergibt sich für das Flachteil beim Spanen aus Stahlhalbzeug ein kumulierter Energieaufwand von 49,362 GJ/t und eine Materialausnutzung von nur 25,5 %.
Tabelle 3: Vergleich der Fertigungsverfahren Spanen und Gießen – Stoffbilanz
Spanen von Halbzeug (Stahl) | Fertigung durch Gießen (Temperguss) | |
Teile | 1,000 t | 1,000 t |
Halbzeug | 3,529 t | - |
Späne | 2,529 t | - |
Schmelze | 3,921 t | 2,500 t |
Bei der Formgebung durch Gießen verbessert sich die Materialausnutzung auf 40 %. Deutlich treten die Vorteile des Gießens bei der Betrachtung der Primärenergiebilanz in Erscheinung.
Von der Schmelze bis zum vergleichbaren Teilezustand liegt der Energieaufwand beim Spanen aus dem Vollen bei 49,362 GJ/t Teile, beim Fertigen durch Gießen aus Temperguss ergibt sich dagegen ein Energiebedarf von 17,462 GJ/t Teile, siehe Tabelle 4.
Tabelle 4: Vergleich der Fertigungsverfahren durch Spanen und Gießen – Energiebilanz (Primärenergie)
Fertigung aus Halbzeug | |
Spanende Fertigung | 3,838 GJ/t |
Halbzeugfertigung | 45,524 GJ/t |
Gesamt | 49,362 GJ/t |
Fertigung durch Gießen | |
Energiebedarf der Gießerei | 14,980 GJ/t |
Energiebedarf für Roheisen | 2,484 GJ/t |
Gesamt | 17,462 GJ/t |
Für die Teilefertigung durch Gießen wird nur ca. ein Drittel der Primärenergie als beim Spanen von Stahlhalbzeug benötigt.
2. Energieeinsparung gegenüber dem Fertigungs-verfahren „Fügen“
Durch die Herstellung von Integralgussteilen, die herkömmliche Konstruktionen aus zahlreichen Einzelkomponenten durch ein einziges gegossenes Teil ersetzen, ergeben sich hohe Energie-einsparungspotentiale durch Vermeidung der Herstellung dieser Einzelteile und ihrer Montage.
Um die Möglichkeiten der Gusstechnik zu verdeutlichen, wird als Beispiel die Herstellung einer Airbus-Passagiertür beschrieben.
Die Airbus-Passagiertür besteht im Wesentlichen aus der Türrahmenkonstruktion, Strukturbauteilen aus einer Aluminiumlegierung, den Beschlagbauteilen und den Ausrüstungsteilen. Bei der bisherigen Differentialbauweise der Airbus-Passagiertür werden gegenwärtig ohne Normteile (Niete, Ringe und Stifte) 64 Frästeile aus Aluminiumhalbzeugen (Stranggussstangen und Bleche) spangebend gefertigt, die anschließend durch ca. 500 Niete zusammengefügt werden.
Für die Differentialbauweise ergeben sich die folgenden Prozessketten:
- Schmelzen – Stranggießen von Stangen – Herstellung von Rohteilblöcken durch Fräsen Spanen von Außenkonturen durch Fräsen – Bohren – passnahes Reiben
- Schmelzen – Stranggießen von Stangen – Blechherstellung durch Walzen – zuschneiden der Rohteilbleche - Spanen von Außenkonturen durch Fräsen – Bohren - Biegen
Für das Gießen der Segmente für die Rahmenstruktur wurde ebenfalls eine Aluminiumlegirrung vorgesehen, die aus Primäraluminium hergestellt wird.
Die Prozesskette beim Gießen stellt sich folgendermaßen dar:
- Schmelzen – Gussbauteilherstellung – Spanen der Außenkontur durch Fräsen – Herstellung von Frästaschen - Bohren – passnahes Reiben
Eine spanende Bearbeitung an den Gussbauteilen wird im Allgemeinen nicht notwendig.
Als Werkstoff für die Halbzeugherstellung wurde eine Aluminiumlegierung DAN 2000 T6 festgelegt, die Aufgrund der Anforderungen seitens der Flugzeugindustrie aus Primäraluminium hergestellt werden muss.
Die 60 % für die Materialausnutzung beinhalten Werkstoffverluste beim Schmelzen und Stranggießen sowie Verschnitt bei der Herstellung der Rohteile. Für das Schmelzen und Stranggießen wurde ein spezifischer Energiebedarf von 6,9 GJ/t angesetzt:
Tabelle 5: Daten für die Halbzeugherstellung (Rahmenstruktur)
Werkstoff | Aluminiumlegierung DAN 2000 T6 100% Primäraluminium |
Energieträger | 65 % Elektroenergie 35 % Gas |
Materialausnutzung | 60 % |
Spezifischer Energieaufwand | 6,9 MJ/kg |
Für das Gießen der Segmente (3 Segmente) für die entsprechende Rahmenstruktur wurde ebenfalls eine Aluminiumlegierung vorgesehen, die aus Primäraluminium hergestellt wird.
Das Gussteilausbringen wird mit 60 % angesetzt. Der spezifische Energieaufwand für die Herstellung der drei Segmente in einer Gießerei wird mit 40 MJ/kg angesetzt.
Tabelle 6: Daten für die Gießerei (Rahmenstruktur)
Werkstoff | Aluminiumlegierung 100% Primäraluminium |
Energieträger | 65 % Elektroenergie 35 % Gas |
Materialausnutzung | 60 % |
Spezifischer Energieaufwand | 40 MJ/kg |
Die Stoffbilanzen für die Rahmenstruktur der Airbustür für die Fertigung aus Halbzeug und für die Fertigung durch Gießen sind in Tabelle 7 angegeben:
Tabelle 7: Vergleich der Fertigungsverfahren Fügen und Gießen – Stoffbilanz
Fertigung aus Halbzeug | Fertigung durch Gießen | |
Fertiggewicht | 42,311 kg | 45,817 kg |
Späne | 62,978 kg | 0,694 kg |
Halbzeuge | 105,289 kg | - |
Gussteile | - | 46,511 kg |
Schmelze | 175,482 kg | 77,518 kg |
Die Fertigteilmasse bei der Differentialbauweise ist ca. 3,5 kg geringer als bei der Gussbauteilvariante, weil im Rahmen der vorliegenden Betrachtungen die Randprofile nicht in die Berechnungen einbezogen worden sind.
Der hohe Anteil an Spänen von ca. 63 kg bei der Fertigung aus Halbzeug wird durch endkonturnahes Gießen mit nur noch ca. 0,7 kg sehr klein und liegt, entsprechend der Angaben, in der Größenordnung von 1 %.
Bei der Fertigung aus Halbzeug müssen ca. 175 kg Werkstoff geschmolzen werden. Demgegenüber stehen ca. 78 kg durch die Fertigung mittels Gießen. Daraus ergibt sich eine Einsparung von etwa 43 %.
Der Vergleich der Energiebilanzen verdeutlicht nochmals den Vorteil des Fertigungsverfahrens Gießen:
Tabelle 8: Vergleich der Fertigungsverfahren Fügen und Gießen – Energiebilanz
Fertigung aus Halbzeug | |
Schmelzen und Stranggießen (Walzen) | 723 MJ |
Spanen | 173 MJ |
Primäraluminium | 28.657 MJ |
Gesamt | 29.553 MJ |
Fertigung durch Gießen | |
Gussteilfertigung | 1.860 MJ |
Spanen | 2 MJ (1,7 MJ) |
Primäraluminium | 12.713 MJ |
Gesamt | 14.575 MJ |
Der Vergleich der Energiebilanzen verdeutlicht den Vorteil der Fertigung durch Gießen.
Während bei der Fertigung aus Halbzeug für die Rahmenstruktur ca. 29.553 MJ Primärenergie benötigt werden, sind dies bei der Fertigung durch Gießen 14.575 MJ.
Die drastische Verringerung des Spanaufkommens durch das endkonturnahe Gießen macht sich in der Energiebilanz zu Gunsten des Gießens bemerkbar. Wurden bei der Fertigung aus Halbzeug noch 173 MJ für das Spanen verbraucht, sind es bei der Fertigung durch Gießen weniger als 2 MJ.