Umweltschutz und Energietechnik (2. Folge)
Von Manuel Bosse, Düsseldorf
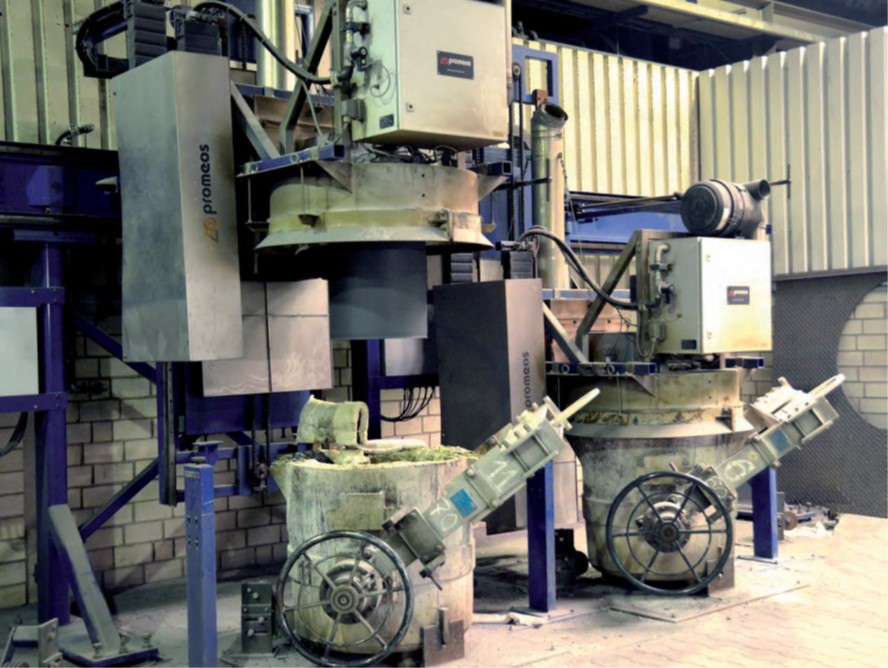
Erschienen in GIESSEREI 10/2014
Umwelt- und Arbeitsschutz
Seit der letzten Jahresübersicht Umweltschutz und Energietechnik in der Giesserei H. 6/2013 hat es nur einzelne qualitativ hochwertige Beiträge im Bereich des Umwelt- und Arbeitsschutzes in Gießereien gegeben. Diese Themen werden in der nächsten Jahresübersicht wieder aufgegriffen. Aktuell liegt der (politische) Fokus auf den zwei „Megathemen“ Ressourcen- und Energieeffizienz, wobei in der Gießerei-Industrie überwiegend zum zweiten Thema Beiträge veröffentlicht wurden.
Nach Auswertung der „Betriebswirtschaftlichen Kennzahlen der Gießerei-Industrie“ vom Bundesverband der Deutschen Gießerei-Industrie (BDG) [1] haben in den meisten Gießereien die Personalkosten den größten Anteil. Es folgen die Rohstoff- und Energiekosten. Die genaue Reihenfolge hängt bei der gegebenen Heterogenität der Branche und vom Schwerpunkt der Fertigung ab. Es gibt sehr materialintensive Produkte, die mit einer hohen Kapitalintensität hergestellt werden. Es gibt aber auch Produkte mit einer sehr hohen Personalintensität.
Preistreiber waren in den letzten Jahren jedoch die Rohstoff- und Energiepreise. Basierend auf der Kostenstrukturstatistik stieg zum Beispiel im Branchendurchschnitt der Anteil der Roh-, Hilfs- und Betriebsstoffe am Bruttoproduktionswert in den Eisengießereien in den letzten 12 Jahren von 28 % auf mehr als 40 % und der Anteil der Energiekosten im gleichen Zeitraum von 5,4 % auf in der Spitze 9,0 %. Bezieht man die Energiekosten auf die Bruttowertschöpfung, ist ihr Anteil von 12 % auf mehr als 28 % gestiegen. Viele Preise für wichtige Rohstoffe – aber auch für die Energieträger Koks, Öl und Gas – werden am Weltmarkt gebildet. Insofern werden alle Gießereien weltweit von steigenden Preisen (für Gießerei-Stahlschrott zum Beispiel) gleich getroffen.
Einzige und zugleich wichtige Ausnahme ist der elektrische Strom. Hier greifen nationale Gesetze. Sie führen dazu, dass deutsche Gießereien den Strom im Vergleich zu wichtigen Wettbewerbern in der Europäischen Union unverhältnismäßig teuer einkaufen müssen. Dass der hohe deutsche Strompreis für die deutsche Gießerei-Industrie international ein gravierendes Wettbewerbsproblem darstellt, lässt sich auch aus der Bedeutung des Stroms an den Energiekosten ableiten: Von den gesamten Energiekosten entfallen etwa 50 % auf die Schmelzenergie, 30 % sind Kraftstrom, die restlichen 20 % werden durch Öl, Erdgas und „Wasser“ verursacht.
Energietechnik und Energieeffizienz
Energiepolitische Rahmenbedingungen
Auch im Jahr 2013 wies die deutsche Industrie im europäischen Vergleich mit 11,21 Cent/KWh die zweithöchsten Strompreise aus (Abnahmegruppe 20 bis 70 GWh/a) (Bild 1). und für deutsche Gießereien setzte sich auch im Jahr 2013 wieder der ununterbrochene Trend mit steigenden Strompreisen fort, was vor allem durch den Anstieg der Erneuerbare- Energie-Gesetz(EEG)-Umlage bedingt war (Bild 2).
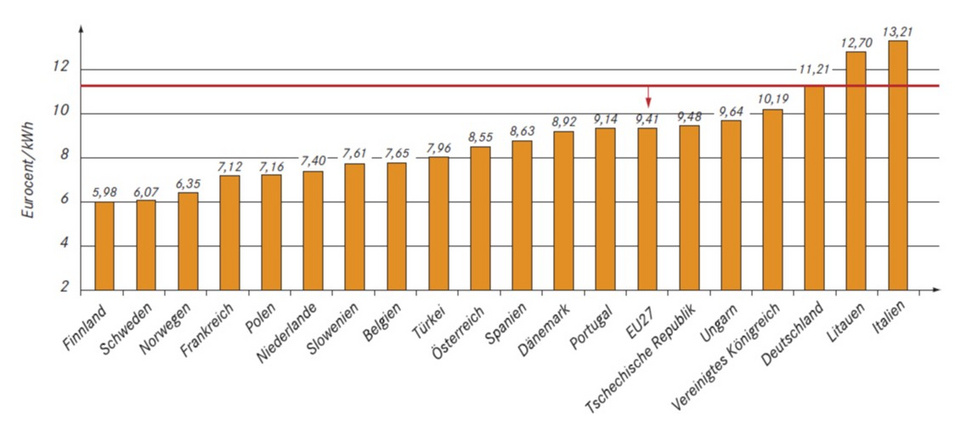
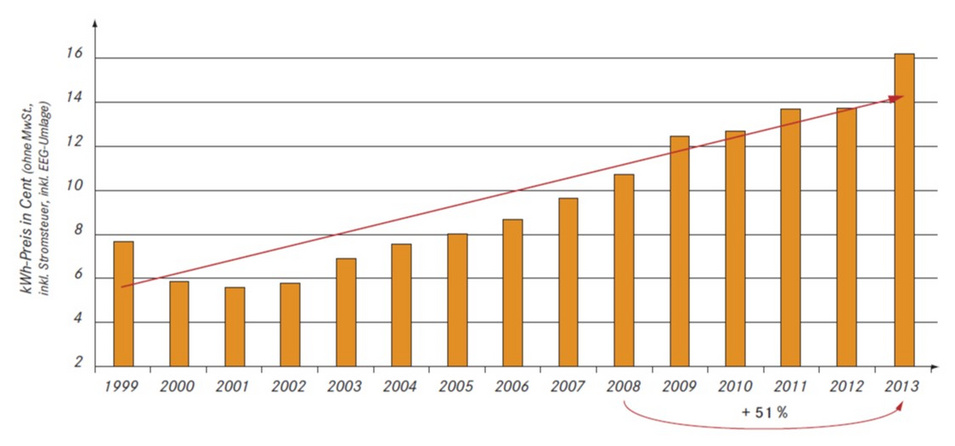
Die EEG-Umlage war auch das wichtigste energiepolitische Thema seit Ende Dezember 2013, da die Europäische Kommission am 18. Dezember 2013 ein Prüfverfahren gegen bestimmte Themenkomplexe des EEG einleitete. Die Novelle des Erneuerbare-Energien-Gesetzes (EEG 2014) und damit verbunden die Überarbeitung der Besonderen Ausgleichsregelung für energieintensive Unternehmen trat am 1. August 2014 in Kraft. Von den 599 deutschen Gießereien konnten im Jahr 2013 140 eine Teilentlastung der EEG-Umlage erreichen (90 Eisengießereien, 10 Stahlgießereien, 38 Nichteisenmetallgießereien und 2 Buntmetallgießereien).
Das neue EEG 2014 fordert nun nicht mehr eine Stromkostenintensität (Verhältnis der Stromkosten zur Bruttowertschöpfung) von 14 % sondern sogar von 16 % für das Geschäftsjahr 2013, um eine Teilentlastung im Jahr 2015 zu erreichen. Dies wird dazu führen, dass ceteris paribus mindestens 30 Gießereien die Teilentlastung verlieren. Weitere 15 Gießereien müssten eine deutlich höhere EEG-Umlage durch den Anstieg der Stromkostenintensität für das Jahr 2014 zahlen (Antragsstellung 2015 für das Begrenzungsjahr 2016). Einziger „Lichtblick“ in dieser Hinsicht ist der zusammengefasste Kontostand (monatliche Einnahmen und Ausgaben der bertragungsnetzbetreiber), welcher einen Überschuss von 1,5 Mrd. Euro im Juni 2014 auswies. Im Gegensatz dazu lagen die Mindereinnahmen zum gleichen Zeitpunkt im Vorjahr bei etwa 1 Mrd. Im besten Fall könnte unabhängig von der Reform die EEG-Umlage im Jahr 2015 auf 5,8 Cent sinken [1].
Während in der letzten Jahresübersicht „Umweltschutz und Energietechnik“ noch die „EU-Triple-20-Ziele“ im Vordergrund standen, wird aktuell an den Zielen für 2030 gearbeitet. Nach aktuellem Stand der Verhandlungen (Januar und Juli 2014) sind folgende Ziele für das Jahr 2030 vorgesehen:
- Verringerung der Treibhausgasemissionen um 40 % gegenüber dem Jahr 1990 durch „EU-interne Maßnahmen“,
- europaweiter Anteil erneuerbarer Energien von 27 % am Brutto-Endenergie-Verbrauch,
- Energieeinsparungen von 30 % im Vergleich zu 2007.
Darauf abgestimmte Projekte im Institut für Gießereitechnik (IfG) zeigen, wie wichtig die Erkenntnisse im Brancheninstitut für die deutsche Gießerei-Industrie sind, z. B.
- Workshops zum CO2-Emissionshandel für die betroffenen Gießereien (große Kupolöfen mit einer Feuerungswärmeleistung von mindestens 23 t/h),
- Forschungsprojekt „ErneuerbareEnergienGießerei“,
- Forschungsprojekte zu Energieeffizienz und Abwärmenutzung.
Mit diesen EU-Zielen für 2030 wird die Absicht verfolgt, die Vision 2050 (Reduzierung der Treibhausgasemissionen um 80 bis 95 %) zu erreichen. Was diese Vision im Jahr 2050 für die Gießerei-Industrie bedeutet, zeigt die Studie „Treibhausgasneutrales Deutschland im Jahr 2050“ vom Umweltbundesamt [2]: „Es wird erwartet, dass bis 2050 brennstoffbefeuerte Öfen größtenteils durch elektrische Schmelzöfen substituiert werden, da die Erzeugung von regenerativem elektrischen Strom i.d.R. sowohl energetisch als auch ökonomisch besser zu bewerten sein wird als die Erzeugung von regenerativen Brennstoffen. Es wird davon ausgegangen, dass 2050 in der deutschen Gießerei-Industrie keine Schmelzöfen mehr betrieben werden, die feste oder flüssige Brennstoffe wie z. B. Koks oder Öl einsetzen.“ Da heute etwa die Hälfte des Flüssigeisens in Deutschland in Kupolöfen erzeugt wird, würde diese Vision einerseits einen echten Umbruch für die etwa 70 Gießereistandorte mit Kupolöfen bedeuten.
Andererseits wird auch weiterhin in bestehende Kupolöfen investiert und die Prozesse zusammen mit Experten im IfG verbessert, z. B. durch das „Treibdüsen-Injektions-Verfahren“ mit Petrolkoksstaub-Sauerstoff-Technologie, beschrieben von H. Kadelka u. a. [3], oder die Investition in einen neuen Kupolofen, wie R. Piterek [4] berichtet. Ziel muss es immer sein, die Fahrweise des Kupolofens programmspezifisch zu optimieren und die Koksbeschaffung zu systematisieren. Bild 3 zeigt, dass trotz der angestiegenen und gleichzeitig volatilen Preisentwicklung von Gießereikoks der Koksbedarf pro Tonne guter Guss ungefähr identisch bleibt. Ist die langfristige Investitionsentscheidung in einen neuen Kupolofenbeschlossen worden, so läuft dieses Schmelzaggregat im Dauerbetriebam effizientesten. Daraus folgt für diese Gießereien eine unelastische Nachfrage nach dem Energieträger Gießereikoks, da sie auf Koks angewiesen und relativ unempfindlich gegenüber Preiserhöhungen sind.
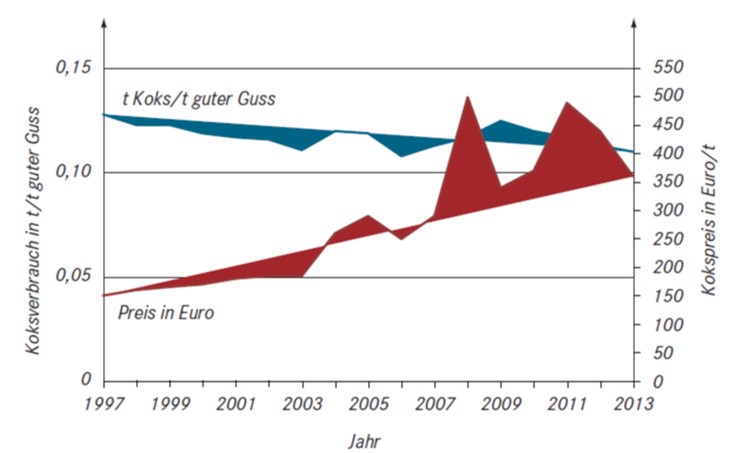
Energieeffizienter Gießereibetrieb
Zum einen sind Energiemanagementsysteme für große Gießereien ein geeignetes, überaus wirksames Instrument, um Energieeffizienzpotenziale zu erschließen und so den spezifischen Energieverbrauch zu senken. Zum anderen sind staatliche Vergünstigungen mittlerweile vermehrt an verpflichtende Systeme geknüpft. Neben den gestiegenen Energiekosten fördern gegenwärtig zwei Gesetze die Einführung von Systemen zur Verbesserung der Energieeffizienz in der Gießerei-Industrie:
- der sogenannte Spitzenausgleich im Energie- und Stromsteuergesetz,
- die besondere Ausgleichsregelung im EEG.
Zusammenfassend lassen sich im Wesentlichen vier Treiber für die stärkere Verbreitung von Energiemanagementsystemenin den nächsten Jahren identifizieren:
- kontinuierliche Optimierung des Einsatzes von Roh-, Hilfs- und Betriebsstoffen,
- höhere Strom- und Energiepreise,
- gesetzliche Vorgaben und Förderprogramme,
- Forderungen der Gussabnehmer.
Eine Untersuchung zu bestehenden (Energie) Managementsystemen führten R. C. Fandl und T. Held [5] im Jahr 2013 durch. Von über 200 untersuchten Gießereien hatten knapp 20 % ein Energiemanagementsystem eingeführt. Nach dem Zusammenführen verschiedener Erhebungen im Haus der Gießerei-Industrie lässt sich abschätzen, dass etwa 155 deutsche Gießereien nach DIN EN ISO 50001 zertifiziert sind (Stand: 1. Quartal 2014). Zahlreiche weitere kleinere und mittlere Gießereien haben mit der Einführung eines sogenannten „Alternativen Systems“ zur Verbesserung der Energieeffizienz begonnen.
Die Einführung eines Energiemanagementsystems nach DIN EN ISO 50001 in einer Druckgießerei beschreiben W. Kallmeyer und D. Rissbeck [6].
N. Brundin und S. Kazemahvazi [7] verglichen verschiedene Unternehmen auf Basis ihrer Ziele zur Senkung des Energiebedarfs oder der CO2-Emissionen. Die Autoren leiten daraus die „Energieeffizienzpyramide“ ab (Bild 4): Auf der ersten Ebene werden nur einzelne Maßnahmen „zusammenhanglos“ im Betrieb durchgeführt, wobei auf der zweiten Ebene ganze Prozesse, z. B. im Schmelzbetrieb, genauer betrachtet und optimiert werden. Die höchste Ebene der „Energieeffizienzpyramide“ wird erreicht, wenn Maßnahmen für einen ganzen Standort oder sogar standortübergreifend durchgeführt werden.
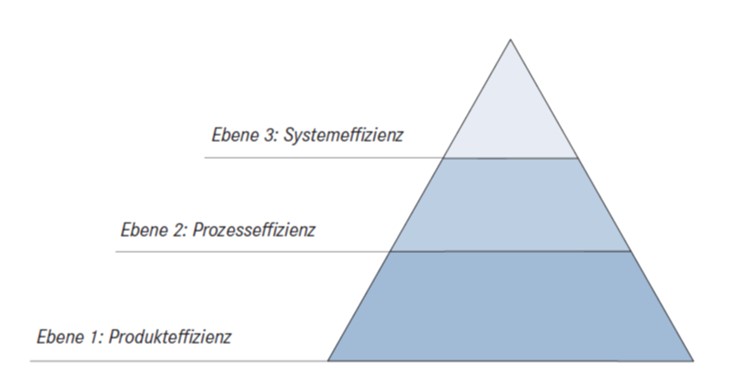
G. Rau [8] weist darauf hin, dass innovative Leichtbaulösungen bei Gussteilen im Automobilbereich dieses ganzheitliche Systemdenken auf einzelne Produkte übertragen, die im System über den gesamten Lebenszyklus Emissionen einsparen.
Der größte Energiebedarf wird im Schmelzbetrieb von Gießereien benötigt: Mögliche Maßnahmen zur Verbesserung der Energieeffizienz an Kupolöfen wurden bereits ausführlich im Jahr 2012 auf der 4. Internationalen Kupolofen-Konferenz in Dresden diskutiert. J. von Scheele [9] erläutert Einsatzmöglichkeiten von Sauerstoff zur verbesserten Fahrweise von Kupolöfen und fokussiert sich letztendlich auf das Highjet-TDI-Verfahren. Der Einsatz von Sauerstoff anstelle von Luft mit 78 % Stickstoffanteil hat den Vorteil, dass Stickstoff nicht mit erwärmt werden muss. Daher sehen Verbesserungsmaßnahmen sowohl im Kupolofen als auch bei der Pfannenvorwärmung den Einsatz von Sauerstoff vor, um eine intensivere und heißere Verbrennung (bei Reduzierung des Koksbedarfs) zu fördern. Folgende Vorteile des Systems werden von dem Autor am Ende des Artikels zusammengefasst:
- höhere Schmelzleistung des Kupolofens (Kapazitätssteigerung),
- niedrigerer Koksbedarf,
- höhere Rinneneisentemperatur,
- niedrigere Mengen an NOx, CO2 und SO2 im Rauchgas,
- niedrigeres Rauchgasvolumen,
- höhere Flexibilität des Kupolofens,
- verbesserte metallurgische Eigenschaften beim Schmelzen,
- um 30 bis 50 % niedrigerer Strombedarf,
- niedrigere Kosten je Chargierung.
Ein weiterer Artikel von J. Würz, J. Rachner, H.-J. Rachner und M. Lemperle [10] im Jahr 2013 vertieft die Frage, ob sich die Abwärmenutzung, z. B. in Form von Heißwinderzeugung über die Stromerzeugung bis hin zu den Verwendungen zum Trocknen oder Heizen, am Kupolofen lohnt. Heißwinderzeugung ist seit vielen Jahren Stand der Technik. Bei der Stromerzeugung aus Abwärme haben sich drei Verfahren etabliert, wobei jedoch die reine Stromerzeugung nicht empfohlen wird:
- Dampfkessel mit Kondensationsturbine,
- Dampfkessel mit Gegendruckturbine,
- Thermalölkessel mit ORC (Organic Rankine Cycle).
Für das Erwärmen und Heizen werden im Beitrag vier Möglichkeiten diskutiert:
- Heizung und Brauchwasser,
- Hallenbeheizung,
- Trocknungsanwendungen,
- Dampferzeugung.
Darauf, dass moderne Induktionstechnologie mit Mittelfrequenztechnik die Energieeffizienz im Schmelzbetrieb gegenüber alter Netzfrequenztechnik verbessert, verweisen M. Rische und E. Dötsch in [11]. Einerseits ist der Energiebedarf mit 520 bis 580 kWh gegenüber 570 bis 700 kWh pro Tonne Flüssigeisen bei Mittelfrequenzöfen niedriger, andererseits können diese Öfen in Produktionsstillstandzeiten vollständig entleert werden und müssen nicht auf Temperatur gehalten werden. In den nächsten Jahren liegt das Verbesserungspotenzial darin, dass Verluste minimiert und Wirkungsgrade der Öfen von 75 bis 80 % auf 81 bis 87 % erhöht werden. Ansatzpunkte für diese Optimierungen bieten fünf „Verlustbereiche“ am Induktionsofen:
- Transformator,
- Umrichter,
- Kondensator,
- elektrische Verluste,
- thermische Verluste.
Das Betriebsverhalten von Induktionsrinnenöfen kann nach E. Baake und A. Jakovics [12] durch Anwendung von Computersimulationen verbessert werden.
Die Instandsetzung und Modernisierung eines 8-t-Lichtbogenofens beschreiben P. Kuhlow, W. Weber und G. Sachse [13]. Den Erfolg dieser umfangreichen Maßnahme zeigt die Tabelle 1: Es konnten gleichzeitig die Lastzeit in Minuten und der Energiebedarf gesenkt werden.
Tabelle 1: Vergleich der Kennzahlen und Messwerte vor und nach der Instandsetzung/Modernisierung.
Vor Modernisierung | Nach Modernisierung | Ergebnis | ||
Charge I-2941 Datum: 2.2.12 | Charge I-3008 Datum: 28.3.12 | Basis korrigiert Einsatz 1545 °C | ||
Einsatzmasse (kalter Satz) in t | 8,200 | 7,900 | 8,200 | 8,200 |
Einschmelzzeit (1545/1537 °C) in min | 94 | 77,00 | 79,8 | |
Lastzeit in min | 91,2 | 73,9 | 76,7 | -14 |
Mittlere Einschmelzleistung (Lastzeit) in tk. S./h | 5,397 | 6,414 | 6,356 | 0,959 |
Mittlere Einschmelzleistung brutto in tk. S./h | 5,234 | 6,156 | 6,104 | 0,870 |
Elektroenergieverbrauch in kWh | 3655 | 3220 | 3342 | |
Mittlerer Energieeintrag (Lastzeit) in kWH/min | 40,1 | 43,6 | 43,6 | |
Spezifischer Elektroenergieverbrauch in kWh/t | 445,7 | 407,6 | 407,6 | -35 |
Spezifische Leistung in kW/t | 293 | 331 | ||
Badtemperatur Einschmelzende in °C | 1550 | 1545 | ||
Mittlere Stromstärke (rms) in kA | 9,428 | 9,381 | 9,381 | |
Wirkwiderstand in mV | 9,020 | 9,902 | ||
Verlustwiderstand (Dr. + Tr. + Leitung) in mV | 0,987 | 0,887 | -0,1 | |
Lichtbogenwiderstand in mV | 8,033 | 9,015 | ||
Lichtbogenspannung in V | 75,7 | 84,6 | ||
Lichtbogenlänge in mm | 55 | 65 | ||
Wirkleistung in kWh/h | 2405 | 2614 | 209 | |
Elektrische Verlustleistung in kWH/h | 263 | 234 | ||
Wärmeverluste in kWh/h | 268 | 260 | -8 | |
Lichtbogenleistung in kWh/h | 2142 | 2380 | 2120 | |
Nutzleistung in kWh/h | 1874 | 2120 | 246 | |
Elektrothermischer Wirkungsgrad | 0,779 | 0,811 | 0,033 | |
Elektrischer Wirkungsgrad | 0,891 | 0,910 | ||
Strahlungsfaktor (ohne Abdeckung) in MWV/m² | 89 | 110 | 22 | |
GE-Verbrauch (berechnet) in kgGE/t | 3,047 | 2,557 | 2,565 | -0,48 |
Erläuterungen: Einschmelzen Basis 1545 °C; alle Messwerte wurden durch ATS Sachse GmbH bereitgestellt; Wirkleistung primär/sekundär Faktor 1,034; die Primärenergie wurde zu Beginn und am Ende der Schmelze gemessen; zum bereinigten Vergleich wurden die Energieverbrauchswerte „vor Instandhaltung“ mit dem Faktor 0,9933 neue Energiemessung korrigiert; die Reduzierung des Verlustwiderstands durch gut instand gesetzte Kontaktbacken beträgt erfahrungsgemäß mindestens 0,1 mV (-26,5 kWh/h bei 9,4 kA); der Anstrich des Ofengefäßes reduziert die Wärmeverluste am Ofengefäß um ca. 3 % (-7,8 kWh/h beim Einschmelzen, ca. 15,6 kWh/h beim Frischen und Feinen). |
A. Ringleb u. a. [14] berichten über ein Teilprojekt des Forschungsverbundes energieeffiziente Technologien und Anwendungen, das sich mit den Wärmeverlusten beim Transport von Flüssigaluminium beschäftigte. Ziel des Projekts war die Beherrschung des Abkühlprozesses und damit die Steigerung der Prozesssicherheit. Es konnten vier Haupteinflussfaktoren identifiziert werden, die in der Tabelle 2 dargestellt sind.
Tabelle 2: Einfluss der Prozess- und Umgebungsfaktoren.
Einfluss | |
Aluminiummasse | 59 % |
Geschwindigkeit | 38 % |
Position des Transportbehälters | 2 % |
Außentemperatur | 1 % |
Entscheidend für den Abkühlprozess ist die Menge an transportiertem Flüssigaluminium. Im nächsten Schritt wurde die Isolierung der Transportbehälter näher untersucht. Es wurde berechnet, dass allein über die Bereiche Verschluss, Stutzen und Deckel fast 45 % der Wärmeverluste des gesamten Behälters entstehen. Eine Optimierung der Isolierung an diesen Stellen würde die Wärmeverluste deutlich reduzieren. Schließlich wurden auch bestehende Abwärmepotenziale an den Aggregaten zum Schmelzen der Aluminiumbarren oder -masseln in den Gießereien selbst untersucht.
Effizienzverbesserungen an einem 200-kg-Drehtrommelofen von bis zu 35 % erreicht R. K. Jain [15] in seinen mathematischen und statistischen Analysen. Neben dem bereits oben genannten Sauerstoff-Erdgas-Brennersystem zur Transportpfannen-Vorwärmung gibt es noch eine zweite Technologie am Markt: Die sogenannte Porenbrenner-Technologie, welche sich auch für Wärmebehandlungssowie Schmelzöfen eignet. Entscheidende Vorteile sind die gleichmäßigere Erwärmung, die reduzierten Geräuschemissionen und im besten Fall auch der reduzierte Energiebedarf. Bei den neu entwickelten Schmelztiegelöfen sind voraussichtlich Energieeinsparungen sowie Reduzierung der Aufheizzeit von bis zu 20 % möglich.
Von Energieeffizienzsteigerungen in Speisesystemen durch sogenannte ECOSpeiser berichten J. Schäfer, T. Schäfer und T. Baginski [16]. Die Speiser sorgen dafür, dass die Zuführung von zusätzlicher Energie durch das Speisesystem minimiert und gleichzeitig die Produkteffizienz und das Ausbringen gesteigert werden.
Literatur:
[1] Betriebswirtschaftliche Kennzahlen der Gießerei-Industrie. Herausgeber: Bundesverband der Deutschen Gießerei-Industrie (BDG) 2013/2014.
[2] www.umweltbundesamt.de/sites/default/files/medien/378/publikationen/climate-change_07_2014_treibhausgasneutrales_deutschland_2050_0.pdf
[3] Giesserei 101 (2014) Nr. 6, S. 84-91.
[4] Giesserei 101 (2014) Nr. 5, S. 122-126.
[5] Giesserei 100 (2013) Nr. 8, S. 90-95.
[6] Giesserei 100 (2013) Nr. 9, S. 60-69.
[7] Foundry Trade Journal (2013) Nr. 7/8, S. 182-184.
[8] Giesserei-Rundschau (2013) Nr. 9/10, S. 270-272.
[9] Indian Foundry Journal 59 (2013) Nr. 10, S. 29-33.
[10] Giesserei 100 (2013) Nr. 3, S. 76-80.
[11] Giesserei Praxis (2013) Nr. 6, S. 237-240.
[12] Giesserei 100 (2013) Nr. 5, S. 42-47.
[13] Giesserei 100 (2013) Nr. 6, S. 40-46.
[14] Giesserei 100 (2013) Nr. 6, S. 74-77.
[15] Indian Foundry Journal (2012) Nr. 11, S. 35-43, (2013) Nr. 9, S. 23-31 und (2013) Nr. 11, S. 35-42.
[16] Giesserei-Erfahrungsaustausch 57 (2013) Nr. 7/8, S. 12-17.