Umweltschutz und Energietechnik (4. Folge)
Von Manuel Bosse, Düsseldorf
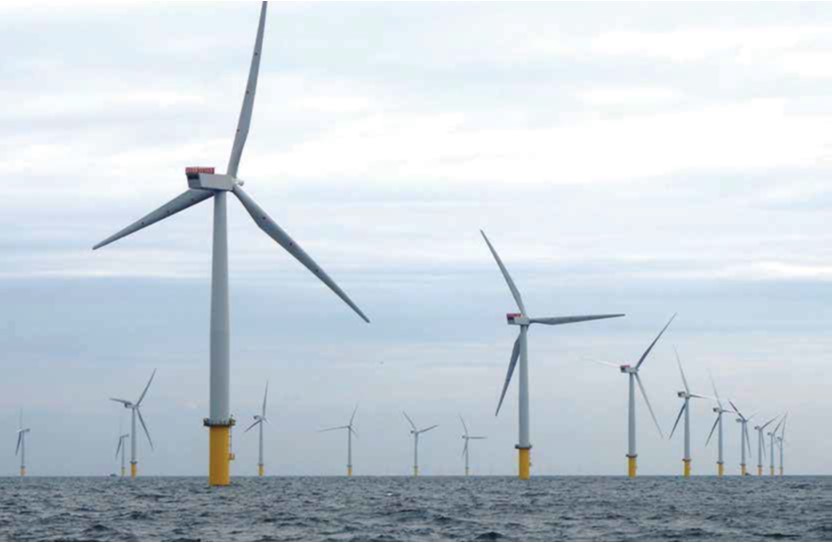
Erschienen in GIESSEREI 10/2016
Umwelt- und Arbeitsschutz
Schimansky [1] beschreibt, warum das Erneuerbare-Energien-Gesetz (EEG) immer wieder für Unsicherheit in Gießereien sorgt. So ist zwei Jahre nach Inkrafttreten des EEG 2014 dieses wieder überarbeitet worden und wird voraussichtlich als EEG 2017 Anfang nächsten Jahres in Kraft treten. Im Rahmen des EEG 2017 können zukünftig wieder alle Gießereien mit über 14 % Stromkostenintensität eine Begrenzung der EEG-Umlage erhalten. Das EEG 2014 hatte jedoch mit seiner „Hopp-oder-Top“-Regel zur Folge, dass im Jahr 2016 nur noch 138 der 588 deutschen Gießereien (zum Vergleich: Im Jahr 2015 waren es 145 Gießereien) von einer reduzierten EEG-Umlage profitieren (Tabelle 1).
Tabelle 1: Deutsche Gießereien, welche die EEG-Ausgleichsregelung in Anspruch nehmen können.
NACE-Code | Bezeichnung | Anzahl der begrenzten Gießereien 2016 | Anzahl der begrenzten Gießereien 2015 |
2451 | Eisengießereien | 88 | 93 |
2452 | Stahlgießereien | 16 | 14 |
2453 | Leichtmetallgießereien | 29 | 35 |
2454 | Buntmetallgießereien | 5 | 3 |
24 | Gesamtanzahl | 138 | 145 |
Doch leider wird die EEG-Umlage an sich auch in den nächsten Jahren weiterhin steigen. So stieg die Umlage von 6,17 Cent im Jahr 2015 auf 6,354 Cent pro Kilowattstunde in diesem Jahr. Agora Energiewende erwartet im Jahr 2017 eine weitere Erhöhung auf 7,1 bis 7,3 Cent pro Kilowattstunde Strom. Nun liegt die Hoffnung der Gießereien (mit elektrischem Schmelzbetrieb) vor allem darauf, dass die Preise an der Strombörse weiterhin niedrig bleiben. So konnte erstmals seit dem Jahr 2001 ein Rückgang der Strompreise für deutsche Gießereien verzeichnet werden: Diese zahlten im Jahr 2015 durchschnittlich 16,30 Cent anstatt 16,96 Cent pro Kilowattstunde im Jahr 2014 (Bild 1).
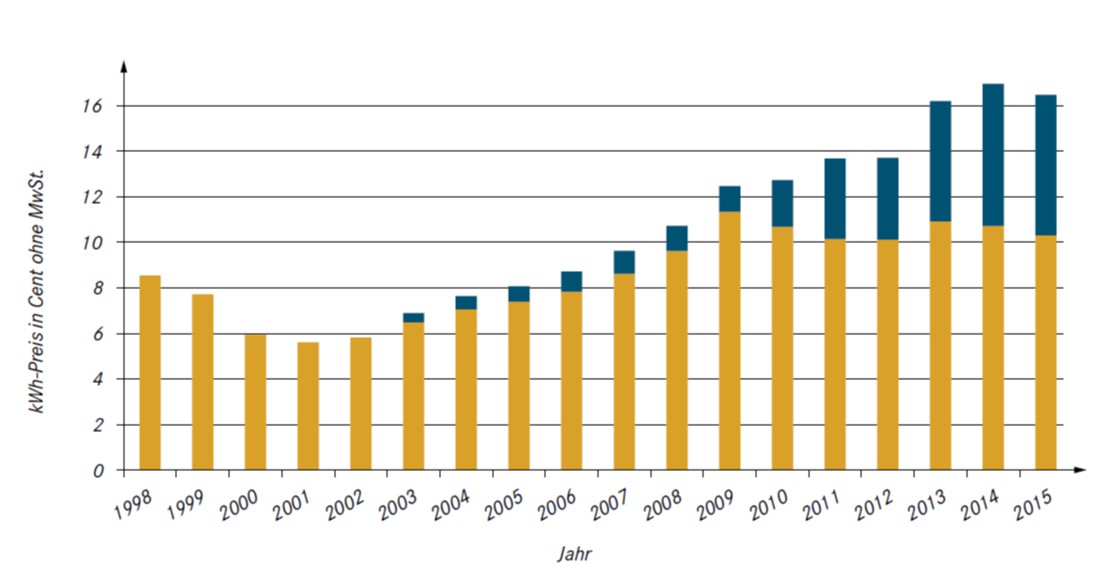
Die deutsche Industrie ist eine der bedeutendsten der Welt und trug im letzten Jahr fast 23 % der gesamten deutschen Wertschöpfung bei. Während in der gesamten Europäischen Union mit (noch) 28 Ländern der Anteil von 18,9 auf 15,5 % in den Jahren 2000 bis 2015 zurückging, konnte Deutschland den Anteil der Wertschöpfung im Verarbeitenden Gewerbe nahezu stabil halten. Um die Industrie als wichtigen Wachstumstreiber in einer Volkswirtschaft auszubauen, soll die Wertschöpfung in der EU bis ins Jahr 2020 auf 20 % steigen [2]. Gießereien sind daher auch in den nächsten Jahrzehnten äußerst wichtig für den Industriestandort Deutschland, denn Eisen- und Nichteisenmetall sind für die moderne Bauwirtschaft und praktisch alle anderen Industriebranchen essentiell und nur selten substituierbare Bestandteile. Die Gießereitechnologie setzt traditionell auf hohe Effizienz in all ihren Prozessen. Gießen ist das ressourcenschonende – weil endkonturnahe – Fertigungsverfahren par excellence. Aus diesem Grund sind gerade bei Zukunftsthemen wie Leichtbau in der Automobilindustrie, Erneuerbare Energien und digitaler Wandel Gießereien unverzichtbar [3].
An dem Thema „Industrie 4.0“ kommen daher auch die Gießereien nicht vorbei. Dies führt dazu, dass in vielen Fachbeiträgen gegenwärtig „4.0“ thematisiert wird, z. B. „Beschaffung 4.0“ für Gießereien oder die „Industrie 4.0-Gießerei“, eine „Smart Foundry“. Die VDG-Akademie zeigte auf einem Symposium im November 2015, was dies konkret für unsere deutschen Gießereien bedeutet. Was man sich unter den Fachbegriffen, wie z. B. Cyber-physische Systeme und Big Data, die im Zusammenhang mit Industrie 4.0 genutzt werden, vorstellen kann, erläuterten Bosse und Kabelitz [4]. Günther [5] beschreibt die Zielausrichtung zukünftiger Gießereien: Diese sollten zur vernetzten, energie- und ressourceneffizienten Gießerei ausgebaut werden, die wandlungsfähige Abläufe aufweist und gleichzeitig ihre Umweltauswirkungen systematisch
reduziert. Zwei Gießereien stellen beispielhaft ihre Konzepte für eine solche Produktion vor: Lange [6] beschreibt die Smart Foundry, der es mit einer SAP-Lösung gelungen ist, durchgängige Prozessketten zu etablieren, in der manuelle Fertigungsschritte und ein automatisiertes Logistiksystem optimal zusammenspielen. Herzstück sind die vier fahrerlosen Transportsysteme, welche die Formkästen zu den verschiedenen Stationen im Ablauf einer Gießerei bringen. Lüking und Throm [7] beschreiben eine andere Gießerei, welche durch drei Softwaremodule vernetzt wird: Das erste Modul vernetzt alle betrieblichen Einrichtungen einschließlich der Haustechnik und kann per
Tablet oder Smartphone überwacht und gesteuert werden. Eine zweite Software wird als zentrales Steuerungs- und Planungsinstrument eingesetzt, welches eine 100 %ige Rückverfolgbarkeit erlaubt. Durch dieses Rückmeldesystem kann jederzeit exakt und stücknummerngenau bestimmt werden, wo sich ein Gussteil gegenwärtig befindet. Das dritte Modul erlaubt es den Kunden, Zugriff auf bestimmte Fertigungsinformationen zu bekommen und laufende Aufträge sowie den Fertigungsstand zu überprüfen. Weitere Verbesserungspotenziale werden vor allem durch den Einsatz von RFID-Chips bei der Modell- und Formkastenverwaltung gesehen.
Lebenszyklusbetrachtungen und Carbon Footprinting sind immer wieder ein Diskussionsthema in der Gießerei-Industrie. Die systematische Analyse von Gussbauteilen ermöglicht die ökologischen Auswirkungen einzelner Gussstücke oder ganzer Serien zu bestimmen. Diese Lebenszyklusanalysen nach DIN EN ISO 14040 ff. für Guss werden gegenwärtig vor allem von Automobilherstellern angefragt, die beispielsweise für ganze Modellreihen Ökobilanzen erstellen. Biedermann, Raupenstrauch et al. [8] weisen darauf hin, dass Gießereiprodukte aufgrund des energieintensiven Produktionsprozesses im Vergleich zu anderen Werkstoffen eine schlechtere Energiebilanz aufweisen können. Daher ist es wichtig, den gesamten Lebenszyklus von Gussstücken miteinzubeziehen, weil diese am Ende ein hohes Potenzial zur Wiederverwertung im Sinne der Kreislaufwirtschaft haben. Insgesamt wurde in einem Forschungsprojekt deutlich, dass sich die höchsten Kosten und Umweltauswirkungen nicht bei der Produktion, sondern vor allem in der Nutzungsphase der Gussprodukte ergeben. Sogenannte „lösungsorientierte Gussteile“, die gezielt den kumulierten Energieaufwand über den gesamten Lebenszyklus eines Gussteils senken, können daher eine bessere Umweltbilanz aufweisen, obwohl womöglich der spezifische Energiebedarf pro Tonne guter Guss in der Gießerei selbst steigt. Abschließend werden in dem Artikel verschiedene Maßnahmen zur Verbesserung der Energieeffizienz im Gießereibetrieb systematisiert (Tabelle 2).
Tabelle 2: Typische Maßnahmen zur Verbesserung der Energieeffizienz in Gießereien.
Wirkungsgrad | Prozesslandschaft | Bauteil |
Erhöhung der Nettogewichte | Bauteilbezogene optimierte Fertigungstechnik | Near-Net Shape |
Wärmerückgewinnung | Automatisches Gießen | 0-Fehler-Strategie |
Abwärmenutzung | Pure Casting |
Andere Gießereinationen haben gegenüber Deutschland kräftig aufgeholt, z. B. die Türkei, welche mittlerweile im Eisen- und Stahlguss vor Frankreich und Italien die zweitgrößte Gießerei-Nation in Europa ist und im NE-Metallguss hinter Italien auf Platz 3 liegt. Auch im weltweiten Vergleich sind andere Länder deutlich innovativer als gedacht: So zeigte Daniel M. Jansen auf dem 3. VDG-Meisterforum, dass z. B. Indien abseits von der „Galileo-Reportage“ [9], welche das Abgießen unter prekären Arbeitsbedingungen in einer indischen Kanaldeckel-Gießerei zeigt, auch für innovative Gusstechnologie steht. Umweltschutz – vielfach getrieben durch die Luftverunreinigung insbesondere in den Großstädten – ist in chinesischen Gießereien ein großes Thema, was bei einem Symposium im Jahr 2015 in China deutlich wurde. Während deutsche Gießereien weiterhin mit den gesetzlichen Rahmenbedingungen zu kämpfen haben und daher keine Abwärmeverstromungsanlagen installieren,
ist dies in China bei neuen Gießereien teilweise bereits Pflicht. Passend dazu war daher „Abwärmeverstromung muss sich wieder lohnen!“ die Überschrift eines Standpunktes [10], welcher die Grundlage für die Fachserie „Abwärmenutzung in Gießereien“ legte. Gießereien können Vorhaben zur Abwärmevermeidung und Abwärmenutzung über das KfWEnergieeffizienzprogramm 294 seit Mai 2016 fördern lassen.
Doch schon in den letzten Jahren haben Gießereien Erfahrungen mit Wärmerückgewinnungsanlagen gemacht. Koch und Temming [11] beschreiben ein Heißwassersystem, welches die Wärmemenge von 7 MW aus einem Heißwindkupolofen an insgesamt 15 Gebäudeteile überträgt und dadurch große Mengen Erdgas einspart. Weitere wichtige Erkenntnisse zu Abwärmepotenzialen in der deutschen Gießerei-Industrie konnten im Rahmen eines geförderten Projekts im Haus der Gießerei-Industrie gesammelt werden. Mehrere Praxisbeispiele in der Gießerei-Industrie zeigen, dass bereits heute schon Abwärme intern oder extern genutzt werden kann, um
- Hallenluft zu erwärmen
- Fußbodenheizungen zu installieren (bei Neu- oder Umbau)
- Warmwasser für Sanitäranlagen zu produzieren
- in Gießereiprozessen, wie z. B. für Glühund Trockenöfen genutzt zu werden
- Roh- und Betriebsstoffe, z. B. Schrott, Späne, Schlichte, Formen und Wasserlacke zu trocknen
- zur externen Sekundärnutzung eingesetzt zu werden, z. B. in Schwimmbädern oder benachbarten Unternehmen
- Wärme, z. B. in mobilen thermischen Energiespeichern oder Feststoffspeichern zu speichern
- (Kraft-)Wärme-Kälte-Kopplung (Kälteerzeugung für Kühlprozesse) zu nutzen
- Dampf zur Einleitung ins Fernwärmenetz zu erzeugen
- elektrische Energie zu erzeugen
Schmidt [12] beschreibt ein ORC-Abwärmekraftwerk, welches Abwärmeströme über 230 °C verstromen kann. Durch Förderprogramme und das Kraft-Wärme-Kopplungsgesetz bei gleichzeitigem Entfall oder Reduzierung gesetzlicher Umlagen können Amortisationszeiten von unter fünf Jahren erreicht werden.
Gammel [13] stellt die Wärmerückgewinnung aus Rauchgas in einer großen deutschen Leichtmetallgießerei vor. Vor Umsetzung des Konzepts wurde im Werk Wärme mit Hilfe von drei Erdgaskesseln mit je 16 MWth erzeugt. Der Kältebedarf wurde über zwei Kompressoren gedeckt. Zusätzlich werden elektrische Energie und Wärme in zwei Blockheizkraftwerken mit 2,8 MWel und 2,8 MWth produziert. Drei erdgasbefeuerte Öfen schmelzen angelieferte Aluminiummasseln ein und drei Öfen werden im Warmhaltebetrieb gefahren, u. a. auch für die angelieferte Menge Flüssigaluminium. Das Rauchgas aus den Schmelzöfen hat eine Temperatur von etwa 640 °C. Eine Verstromung der Abwärme, z. B. in einer ORC-Anlage, konnte zum damaligen Zeitpunkt nicht wirtschaftlich dargestellt werden. Daher wurden verschiedene Maßnahmen kombiniert. Ein Teil der Abwärme wird in das bestehende Heißwassernetz eingespeist. Zudem wird die Kälte nun überwiegend in Absorptionskältemaschinen gewonnen, die aus Wärme Kälte erzeugen (Kraft-Wärme-Kälte-Kopplung). Um die Heizkessel nur noch für Mittel- und Spitzenlasten zu nutzen, wurde ein weiteres Blockheizkraftwerk mit 2,6 MWel und 2,4 MWth installiert.
Einen großen Hebel zur Verbesserung der Material- und Energieeffizienz bieten sowohl die Erhöhung der Ausbringung als auch die Reduzierung von Kreislaufmaterial sowie des Ausschusses. Mit verbesserter Ausbringung, also einem besseren Verhältnis von Flüssigeisen zu gutem Guss oder guter Ware, sinkt auch gleichzeitig der verhältnismäßige Energiebedarf. Die Gießprozesssimulation erlaubt die Vorhersage von Gieß- und Erstarrungsprozessen in Bezug auf Geschwindigkeits-, Temperatur-, Seigerungs- und Spannungsfeldern vor dem ersten Abguss, ohne dass Flüssigmetall geschmolzen werden muss. Eine optimale Speisung durch verbesserte exotherm-isolierende Speisermassen verbessern sowohl die Ausbringung als auch die prozesssichere Speisung von Knotenpunkten, wodurch Gussfehler proaktiv vermieden werden [14].
Schmelzbetrieb
Wie soll der Schmelzbetrieb der Zukunft aussehen? Enzenbach [15] erläutert, dass in der Vergangenheit die Antwort klar war: Kupolöfen sind die dominierenden Schmelzaggregate für das Basiseisen in Eisengießereien und werden zunehmend durch flexible Elektroöfen ergänzt (Bild 2).
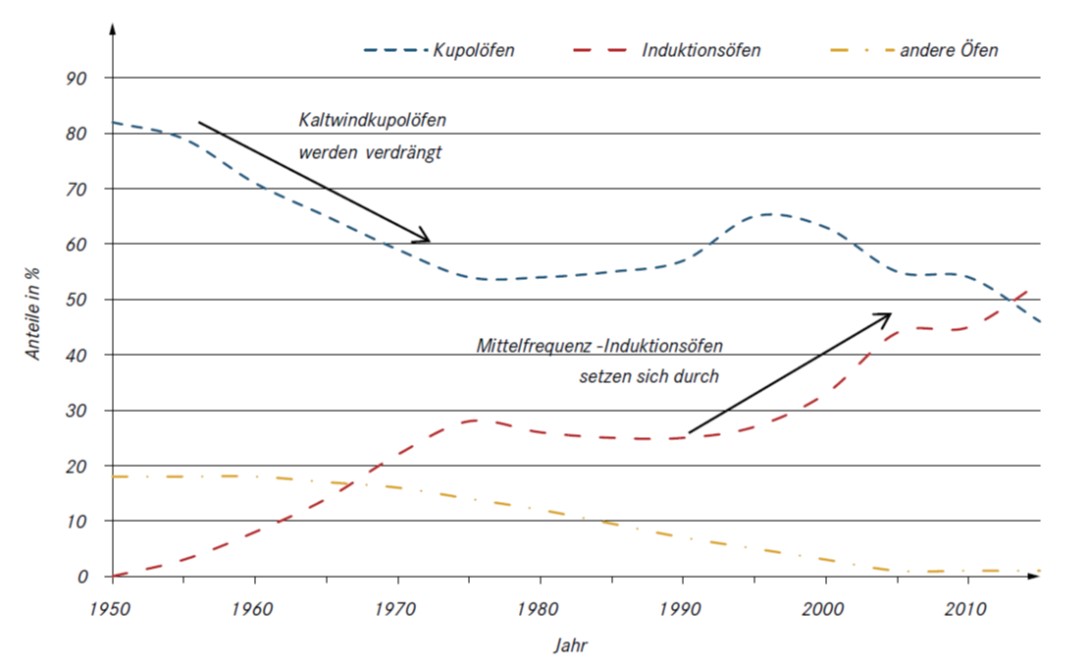
Das Umweltbundesamt hingegen sieht „die Tage des Kupolofens“ gezählt, um das politische Ziel der Treibhausgasneutralität zu erreichen. Vier Maßnahmen werden jedoch auch zukünftig den Kupolofen wettbewerbsfähig machen, wenn
- der thermische Wirkungsgrad weiter erhöht
- die Substitution von Teilen des Kokses durch CO2-neutrale Energieträger vorangetrieben
- das CO2 aus dem Abgas entfernt und
- eine umfangreiche Rückgewinnung der entstehenden Wärme ermöglicht wird.
In der Vergangenheit wurden Gussstücke abgegossen und anschließend mit Hilfe zerstörungsfreier Prüfung untersucht, ob sich Bauteile für den bestimmten Einsatz eignen. Kendrick, Careil, Freyn und Simon [16] wählen den entgegengesetzten Ansatz und beschäftigen sich mit der direkten Messung der Schmelzequalität und möglichen Einflussgrößen, die zu ihrer Verbesserung führen. Die drei wichtigsten Methoden zur Bestimmung der Eigenschaften einer Aluminiumschmelze werden in einer Softwarelösung kombiniert. Entscheidend sind:
- Wasserstoffgehalt im Aluminium vor dem Vergießen
- Reinheit der Schmelze, damit das Gussstück oxidfrei bleibt
- Mikrostruktur des fertigen Produkts
Eine Herausforderung an die prozesssichere Fertigung stellt der Aluminiumschmelzetransport in Gießereien dar, welcher durch mehrfache Umfüllvorgänge zur Abkühlung der Schmelze und Anreicherung mit Wasserstoff und Oxiden führt. Zur Verhinderung der Anreicherung ist daher eine sichere und energieeffiziente Prozessführung wichtig.
Reichen [17] beschreibt in seinem Artikel zur Euroguss 2016, dass die Anlagenverfügbarkeit von Druckgießmaschinen einen erheblichen Einfluss auf die Energiekosten je produziertem Bauteil hat, weshalb eine Verbesserung der Gesamtanlageneffektivität gleichzeitig auch eine Maßnahme zur Verbesserung der Energieeffizienz ist. Der im VDMANormblatt 24499 beschriebene standardi sierte Prozess ermöglicht es, die Leistungs aufnahme verschiedener Druckgieß maschinen zu vergleichen. Ein „Energiezertifikat“ kann anschließend der Leichtmetallgießerei bei ihrer Inves titionsentscheidung helfen. Für Anlagen im Betrieb werden gezielte Analysen angeboten, die Einsparpotenziale in einem Energiemessprotokoll auflisten. Vor allem Stillstandszeiten der verwendeten Zellenkomponenten sind von Interesse, da diese z. B. auf unnötige „Stand-by-Verluste“ oder Bedienfehler hinweisen können. Tabelle 3 zeigt den mittleren, effektiven Energiebedarf für drei unterschiedliche Bauteile aus verschiedenen Gießereien, die als Benchmark herangezogen werden können.

Theis [18] sieht eine genaue Energiedatenerfassung mit Stromsensoren und Datenloggern in Druckgießanlagen als Schlüssel zur Verbesserung der Energieeffizienz. Während heutzutage neue Anlagen ab Werk bereits mit der Energiedatenerfassung ausgestattet sind, können Bestandsanlagen nachgerüstet werden, um kontinuierliche Verbesserungen im Rahmen des betrieblichen Energiemanagements nachzuweisen und einen Schritt zur bereits oben beschriebenen Industrie 4.0-(Druck-)Gießerei zu starten.
Auch Pinto und Navarro [19] beschreiben die Vorteile einer Echtzeitüberwachung von Temperatur- und Strombedarf an widerstandsbeheizten Tiegelöfen für Aluminium, um die Energieeffizienz im Schmelzbetrieb zu erhöhen. Bestimmte Arbeitsschritte lassen sich in Bezug auf Energieeffizienz optimieren, wenn z. B. der Ofendeckel bei der Entgasung zu lange offen gehalten wird oder das Befüllen des Ofens zu langsam geschieht. Gleichzeitig lassen sich Temperaturveränderungen durch Futterverschleiß frühzeitig identifizieren. Ferner misst ein Laser kontinuierlich die Badhöhe und warnt vor Überfüllung oder einem zu niedrigen Füllstand des Flüssigaluminiums.
Seit den 1990er-Jahren haben sich Mittelfrequenzöfen gegen Netzfrequenzöfen etabliert. Die höhere und anpassungsfähige Frequenz des Spulenstroms macht es möglich, die per Umrichter gespeisten Schmelzaggregate mit wesentlich höherer Leistungsdichte und ohne Einbuße der Schmelzleistung im Chargenbetrieb mit jeweils totaler Entleerung zu betreiben. Den optimalen Energiebedarf eines Mittelfrequenzinduktionsofens mit 525 kWh pro Tonne Flüssigeisen bei sehr guter Auslastung skizzieren Dötsch, Ibach, Risch und Yildir in Bild 3 [20].
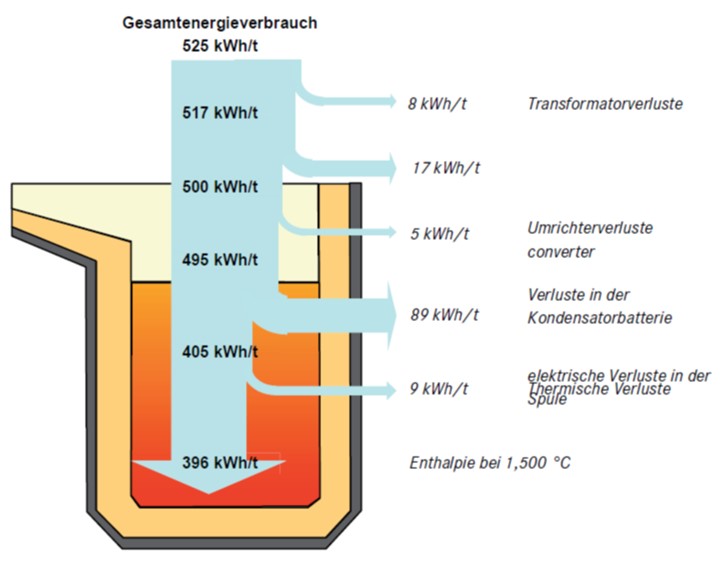
Im Gießereialltag mit schwankender Auslastung liegen gut geführte Tandem-Schmelzbetriebe unter 600 kWh pro Tonne Flüssigeisen. Gründe für einen höheren Energiebedarf können folgende Punkte sein:
- Setzen von sandbehaftetem Kreislaufmaterial,
- Warmhalten mit offenem Ofendeckel,
- ungedrosselte Absaugung beim Warmhalten,
- längeres Warmhalten durch mangelhafte Logistik und
- nicht sachgemäßes Chargieren.
Heavey [21] betont, dass Mitarbeiter im Schmelzbetrieb kontinuierlich geschult werden müssen, um in diesem energieintensiven Bereich der Gießerei kontinuierlich den Energiebedarf im Verhältnis zum Flüssigmetall zu senken und die Ausbringung zu erhöhen.
In den letzten Jahresübersichten sind Erdgas-Porenbrenner vor allem in Zusammenhang mit der Pfannenwirtschaft genannt worden. Ates [22] stellt diese flammenfreien Gasbrenner auch für Schmelzund Warmhalteöfen vor. Entscheidender Vorteil wie bei der Pfannenvorwärmung ist die homogene Erwärmung ohne „Hot Spots“ (Bild 4).
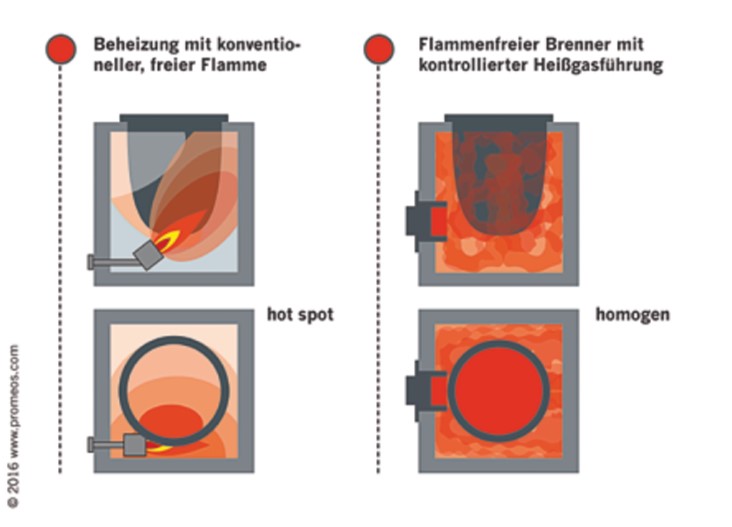
In deutschen Gießereien gibt es seit mehreren Jahren einen Trend, dass sowohl Lichtbogenöfen als auch Kaltwindkupolöfen durch moderne Mittelfrequenz-Induktionsöfen substituiert werden. Bei der Herstellung gewisser Stahlqualitäten überwiegen jedoch die Vorteile eines Lichtbogenofens, da ein höherer Einsatz von Recyclingmaterial verbunden mit kürzeren Schmelzzeiten möglich ist. Huscher und Schmitz beschreiben die Modernisierung eines Lichtbogenofens, durch die Standzeiten, Wartungsfreundlichkeit und Energieeffizienz erhöht wurden [23].
Henriksen and Needham [24] beschreiben die Ausweitung der Produktionskapazität einer Stahlgießerei von 130 auf 160 t pro Tag durch den Bau eines dritten Lichtbogenofens. Während mit zwei Lichtbogenöfen immer wieder 25 min lang keine flüssige Schmelze verfügbar war, hat sich dies nun durch den dritten Ofen geändert. Bild 5 zeigt, dass durch die Verbesserung der Arbeitsabläufe und die Beseitigung von Engpassstellen in der Gießerei nun alle 60 min anstatt zuvor 90 min Flüssigstahl zum Abguss
bereitsteht. Durch die bessere Auslastung erhöht sich gleichzeitig die Energieeffizienz des Stromeinsatzes im Verhältnis zu gutem Stahlguss oder Flüssigstahl.
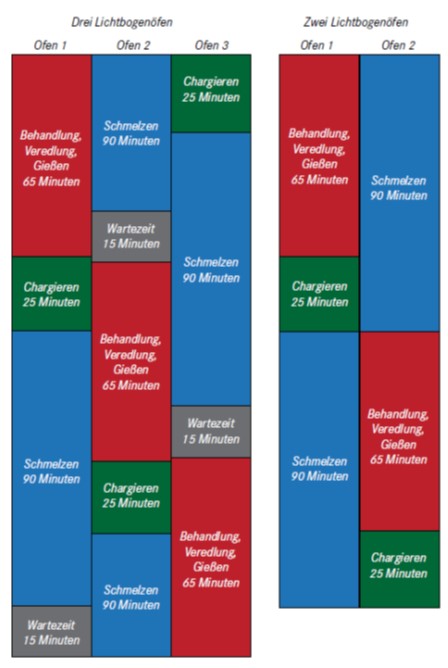
Querschnittstechnologien
Die Reduzierung der Antriebsleistung oder der Einbau von drehzahlgeregelten Motoren bei Strahlanlagen führt ebenfalls zu einer Reduzierung des Energiebedarfs. Laut Mülle [25] konnte bei neuen Strahlanlagen durch sogenannte Hochleistungsturbinen mit einer speziellen konkaven Form der Wurfschaufeln, welche eine höhere Abwurfgeschwindigkeit bei gleichzeitigem höherem Strahlmitteldurchsatz bei reduzierter Turbinendrehzahl ermöglichen, die Leistung von 45 auf 37 kW gesenkt werden.
Druckluft wird in vielen Gießereien als Energieträger gesehen, der wie elektrische Energie immer zur Verfügung steht. Bei Gießereien mit brennstoffbefeuerten Schmelzbetrieben kann die Drucklufterzeugung bis zu 25 % des Gesamtstrombedarfs verursachen, was etwa 3-6 % des Gesamtenergiebedarfs einer solchen Gießerei bedeutet. Da Druckluft in Gießereien jedoch überwiegend mit eigenen Kompressoren erzeugt wird, fehlt häufig eine Kostentransparenz, welcher Aufwand für die Erzeugung, Aufbereitung und Verteilung von Druckluft erforderlich ist. In einigen Gießereien wird daher ein Druckluft-Contracting thematisiert, um aus „Druckluft“ einen externen Energieträger“, wie z. B. elektrische Energie oder Erdgas, zu machen, der von einem externen Lieferanten mit transparenter Rechnung bezogen wird. Ein Druckluft-Audit, welches teilweise kostenfrei von den Kompressorherstellern angeboten wird, kann erhebliche Verbesserungspotenziale aufdecken. Bei gewachsenen Kompressoren-Parks kann allein die Aktualisierung der Kompressorsteuerung für Energieeinsparungen sorgen. Häufig sind auch die bestehenden Kompressoren schlichtweg überdimensioniert. Im nächsten Schritt können sich deswegen auch die Investition in einen kleineren, effizienteren Grundlastkompressor oder einen drehzahlgeregelten Kompressor für die Spitzenlast in unter drei Jahren amortisieren. Hersteller versprechen einen reduzierten Energiebedarf von bis zu 35 % [26]. Bei Druckluftkompressoren werden über 90 % der elektrischen Leistungsaufnahme in Wärme umgewandelt. Deswegen sollte bei Investitionen in neue Druckluftkompressoren geprüft werden, ob sich eine Wärmerückgewinnung realisieren lässt, um benachbarte Arbeitsbereiche, wie z. B. die Kernmacherei oder den Formenbau zu beheizen. Kompressorhersteller sind daher dazu übergegangen neue Anlagen direkt mit einer eingebauten Wärmerückgewinnungseinheit auszustatten.
Die Kosten, welche durch Druckluftleckagen entstehen, werden in Mitarbeiterschulungen thematisiert, doch bei Energieaudits ergibt sich immer wieder Verbesserungsbedarf in Gießereien. Hartung [27] verweist darauf, dass neben Leckagen häufig auch die Druckluftfiltration Verbesserungspotenziale aufweist. Durch den regelmäßigen Wechsel der Filterelemente innerhalb der empfohlenen Intervalle werden deutliche Einsparungen erzielt und somit die Betriebskosten minimiert. Hightech-Fasern haben eine bis zu 400 % größere Filterfläche im Vergleich zu standardmäßig gewickelten Filtermedien, wodurch sich die Abscheideleistung von Flüssigpartikeln und Aufnahmekapazität für Feststoffpartikel erhöht.
Eine zukünftige Lösung für Gießereien könnte die digitale Leckageüberwachung sein, welche Verschleiß in Rohrleitungen selbstständig meldet. Dücker [28] beschreibt ein WLAN-Frühwarnsystem, welches Leckagen direkt an einen Monitor im Leitstand meldet. Als Beispiel wird die pneumatischen Formsandversorgung der Kernmacherei genannt. Allgemein ist die Instandhaltung gefordert, z. B. einen eigenen Druckluftbeauftragten in jeder Schicht zu benennen, der während seiner Betriebsrundgänge ein Lecksuchgerät dabei hat und sich vor allem in produktionsfreien Zeiten des Themas verstärkt annimmt. Beste Erfahrungen wurden in Gießereien gesammelt, die diese Aufgabe von der Instandhaltung auf die einzelnen Abteilungen übertragen haben, sodass z. B. die Anlagenführer im Bereich der Maschinenformgusses selbst für die Leckagesuche verantwortlich sind und Druckluftverluste „an ihrer Anlage“ umgehend an die Instandhaltung melden. Droste [29] weist neben den hohen Energieverbräuchen auch auf Nachteile wie z. B. die Lärmbelastung von Druckluft am Arbeitsplatz hin. Angepasste Blasdüsen sind effizienter als veraltete, offene Rohre. Bei sogenannten Energiespardüsen lässt sich der benötigte Druck in verschiedenen Stufen regulieren und so der Energiebedarf am einzelnen Arbeitsplatz um mindestens 20 % senken. Gleichzeitig wird durch Sicherheitslärmdämpfer der Lärmpegel um mindestens 10 dB(A) gesenkt. Dies wiederum wird bei vielen Gießereimitarbeitern als nachteilig empfunden: So bekommt der Energiemanagementbeauftragte immer wieder zu hören, dass man Druckluft aufgrund langjährigerErfahrung „hören“ muss und nur dann kann auch „genügend Druck“ für die Tätigkeit am Gießerei-Arbeitsplatz erzeugt werden. Wie bei vielen Energieeffizienzmaßnahmen sollten daher frühzeitig die Mitarbeiter des Energieteams über innovative Neuerungen informiert werden, damit diese trotz Energieeinsparpotenzial im Betrieb nicht pauschal abgelehnt werden. Gerade im Bereich der Putzerei werden die leichten Pneumatikwerkzeuge gegenüber schwereren Hochfrequenzgeräten von Gießereimitarbeitern geschätzt. Wenke [30] plädiert daher für ergonomische und energiesparende Turboschleifer, die dazu eine effiziente Druckluftversorgung erhalten.
Bei anderen Prozessen wie der Zwischenreinigung versucht man gezielt Systeme ohne die Verwendung von Druckluft zu etablieren, um Energieeinsparungen von bis zu 50 % zu realisieren. Anstatt spanend bearbeitete Bauteile mit Druckluft abzureinigen, welche womöglich Rückverschmutzungen am Werkstück verursachen, stellt Straub [31] das Vakuumsaugen vor, welches am Bauteil haftende Späne „abreißt“ und in den Unterdruckbehälter abtransportiert.
Umweltschutz
Das Formsprühen ist beim Druckguss ein wichtiger Prozessschritt, der vier Funktionen erfüllt:
- Auftragen eines Trennstoffes,
- Schmieren von beweglichen Formteilen,
- Beseitigung von Verunreinigungen,
- Abkühlen der Form.
Um die Umweltauswirkungen zu reduzieren, wurde eine neue Generation von wasserfreien Trennstoffen entwickelt, die ein sehr hohes Maß an Haftungsvermögen aufweisen. Sowohl im Aluminium- als auch beim Magnesiumdruckgießen können laut Engelhorn unter anderem folgende Verbesserungen erreicht werden [32]:
- Reduzierung des Trennmittelverbrauchs,
- kein Frischwasserverbrauch,
- kein Abwasseranfall,
- biozidfrei,
- geringe Lärmemission,
- Reduzierung des Wärmeschocks und dadurch
- höhere Formstandzeiten.
Aufgrund der strengeren Auflagen zur Reduktion der Emissionen von flüchtigen organischen Verbindungen, müssen Gießereien die Anstrengungen intensivieren, um ihre Emissionen, insbesondere an leichtflüchtigen Aromaten zu senken. Engelhardt [33] weist darauf hin, dass den Gießereizulieferern dabei eine Schlüsselrolle zukommt, wenn emissionsfreie oder -arme Alternativen zu den heute üblichen Glanzkohlenstoffbildnern wie Steinkohle und Harze entwickelt werden müssen. In Gießereien senken neue, verbesserte Additive die Emission von leichtflüchtigen Aromaten aus dem Formstoff um bis zu 80 %.
Die Revision der Technische Anleitung zur Reinhaltung der Luft (TA Luft) wird voraussichtlich im Jahr 2017 weiter die vorgeschriebenen Grenzwerte in Gießereien herabsetzen. Dadurch wird sich teilweise der Widerspruch zwischen Umweltschutz und Energieeffizienz in Gießereien verstärken, denn durch Automatisierung und durch Erhöhung der Leistung von Abluftreinigungssystemen steigt der Strombedarf in Gießereien. Erfahrungen mit einem neuartigen System bei gleichzeitigem Einsatz hochwertiger Bindemittel werden von Hartung [34] geschildert. Eine innovative Reinigungstechnologie beschleunigt den natürlichen Reinigungsprozess der Erdatmosphäre in einem Kompaktreaktor um das Hundertausendfache, wodurch Amine, Methylformiat, Phenole, Formaldehyd sowie BTEX bis zu 100 % aus der Abluft entfernt werden (Bild 6).

Eine anorganische Sandkernfertigung mit modernisierter Sandaufbereitungsanlage beschreiben Will und Borghoff [35]. Durch die Anorganik konnte die Schadstoffbelastung in der Luft um 98 % gesenkt und eine Wiederaufbereitungsquote des Sandes von 90 % erzielt werden. Vibrationsbrecher zerreiben den Gießereirestsand auf Korngröße und vorhandene Metalle, Schlackereste und andere Fremdstoffe werden spätestens im Linearschwingsieb automatisch entfernt.
Literatur:
[1] GIESSEREI 103 (2016), Nr. 4, S. 90.
[2] BMWi - Schlaglichter der Wirtschaftspolitik, Monatsbericht Juli 2016, S. 13, www.bmwi.de/Dateien/BMWi/PDF/Monatsbericht/schlaglichter-derwirtschaftspolitik-07-2016,property=pdf,bereich=bmwi2012,sprache=de,rwb=true.pdf.
[3] Deutsche Bank – Research, Mittelständische Gießereien meistern Herausforderungen, S. 1, https:// www.dbresearch.de/ MAIL/ DBR_INTERNET_DE-PROD/PROD0000000000408160.pdf.
[4] GIESSEREI 102 (2015), Nr. 12, S. 22-24.
[5] GIESSEREI 103 (2016), Nr. 5, S. 38-41.
[6] GIESSEREI 102 (2015), Nr. 11, S. 60-63.
[7] GIESSEREI 102 (2015), Nr. 11, S. 54-58.
[8] Giesserei-Rundschau (2015), Nr. 7/8, S. 187-195.
[9] youtube/wpOMOfN0Vbs
[10] GIESSEREI 103 (2016), Nr. 6, S. 26-28.
[11] GIESSEREI 102 (2015), Nr. 9, S. 52-54.
[12] GIESSEREI 103 (2016), Nr. 7, S. 28-31.
[13] Giesserei Erfahrungsaustausch (2015), Nr. 11+12, S. 28-30.
[14] Giesserei Erfahrungsaustausch (2015), Nr. 3+4, S. 6-11.
[15] GIESSEREI 103 (2016), Nr. 5, S. 36-37.
[16] GIESSEREI 102 (2015), Nr. 10, S. 72-77.
[17] GIESSEREI 102 (2015), Nr. 12, S. 82-87.
[18] GIESSEREI 102 (2015), Nr.12, S. 100-102.
[19] Foundry Trade Journal (2015), December, S. 348-353.
[20] GIESSEREI 103, (2016), Nr. 2, S. 24-31.
[21] Foundry Trade Journal (2016), May, S. 116.
[22] Giesserei Rundschau (2015), Nr. 07/08, S. 81-83.
[23] GIESSEREI 103 (2016), Nr. 5, S. 52-54.
[24] Modern Casting (2015), August, S. 22-25.
[25] Giesserei Erfahrungsaustausch (2015), Nr. 1+2, S. 32-33.
[26] Giesserei Erfahrungsaustausch (2015), Nr. 11+12, S. 31-33.
[27] Giesserei Erfahrungsaustausch (2016), Nr. 1+2
[28] GIESSEREI 102 (2015), Nr. 9.
[29] Giesserei Erfahrungsaustausch (2016), Nr. 5+6, S. 16-18.
[30] Giesserei-Erfahrungsaustausch (2016) Nr. 5+6, S. 10-13.
[31] GIESSEREI 102 (2015), Nr. 9, S. 154.
[32] Giesserei Erfahrungsaustausch (2015), Nr. 11+12, S.12-14.
[33] GIESSEREI 103 (2016), Nr. 6, S. 44-48.
[34] GIESSEREI 102 (2015), Nr. 11, S. 48-50.
[35] (GIESSEREI 103 (2016), Nr. 2, S. 58-59.