Abwärmenutzung mit thermoelektrischen Generatoren - Weites Einsatzspektrum auch in Gießereien
Von Stefan Schumann, Dirk Lehmann, Marl, Patrick Stenner, Hanau, Sascha Hoch, Essen
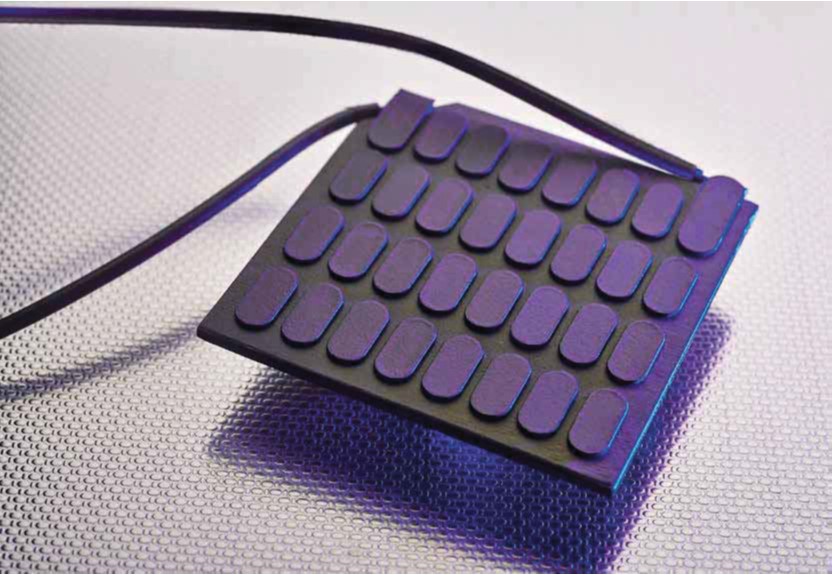
Erschienen in GIESSEREI 10/2017
Evonik Creavis hat ein neuartiges, industriell umsetzbares Fertigungsverfahren für thermoelektrische (TE) Module entwickelt, das sich durch verringerte Systemkosten bei gleichzeitig verbesserter Handhabung auszeichnet. Durch die High-TEG-Module Esprix kann nun Ab- sowie Strahlungswärme der Industrie – auch in Gießereien – in elektrischen Strom umgewandelt und erstmalig wirtschaftlich erschlossen werden. Diese vielversprechende Entwicklung wurde mit dem „Deutschen Nachhaltigkeitspreis Forschung 2016“ gewürdigt [1].
Bezahlbare Thermoelektrik für die Wärmewende
Abwärme entsteht in allen Bereichen des täglichen Lebens und besitzt mit geschätzt 300 TWh pro Jahr in Deutschland ein bisher kaum genutztes Potenzial als nachhaltige Energieressource. Dabei fallen in energie- und wärmeintensiven Industrien besonders große Abwärmeverluste an.
Eine Methode zur direkten Wandlung von Abwärme in höherwertige elektrische Energie ist der Einsatz thermoelektrischer Generatoren (TEGs) – Maschinen, die bereits aus kleinen Temperaturdifferenzen emissions- und geräuschlos Strom erzeugen. Die Thermoelektrizität nutzt einen lang bekannten Festkörpereffekt (Seebeck-Effekt), bei dem Wärmeströme direkt, ohne bewegliche Teile, in elektrischen Strom umgewandelt werden. Obwohl mit heutigen Materialien nur 5 % der Abwärmeenergie direkt umwandelbar sind, gelingt so die Nutzung von Abwärmeströmen, die mit anderen Verfahren nicht zu erschließen wären.
Das Prinzip veranschaulicht Bild 1a: Ein TEG-Modul hat im Betrieb eine der Wärmequelle zugewandte Seite, die Heißseite, und eine abgewandte Seite, die Kaltseite. Die Temperaturdifferenz zwischen
beiden erzeugt am thermoelektrisch aktiven Material (TE-Schenkel im Modulinneren) eine proportionale Spannung (typischerweise ± 300 μV/K). Je nach Dotierung des Halbleitermaterials
(n- oder p-Dotierung) findet der Elektronenfluss in die entgegengesetzte Richtung statt. Je ein n- und ein p-Schenkel stellen ein Schenkelpaar dar. Für eine nutzbare Spannung wird eine Vielzahl solcher
Schenkel elektrisch in Reihe geschaltet und bildet so ein TEG-Modul (Bild 1b).
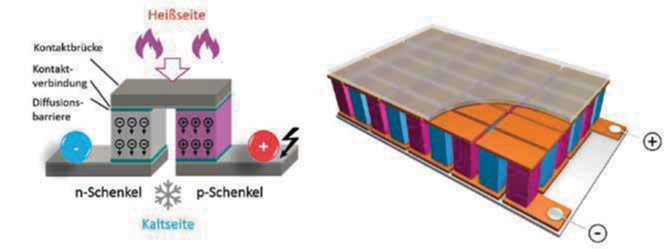
Der herkömmliche TEG-Herstellprozess ist sehr komplex und enthält eine Vielzahl manueller Schritte, deren erhebliche Kosten zusätzlich zu denen für das thermoelektrische Material anfallen. Aufgrund der hohen spezifischen Kosten von > 5 €/Wel und des begrenzten Temperaturbereichs verfügbarer Materialien (< 200 °C) bleiben die TEGs bisher auf Nischenanwendungen beschränkt. Nur preiswerte und damit rentable industrielle Herstellverfahren könnten dabei helfen, eine wesentliche Lücke in der regenerativen Energieerzeugung zu schließen.
Diese technische Aufgabe hat die Evonik Creavis GmbH mit den High- (Hochtemperatur-)TEG-Modulen der Marke Esprix bewältigt. Entwickelt wurde ein Hochleistungsprozess für thermoelektrische
Energiewandler, der kostengünstiger sowie industriell skalierbar ist und robuste, leistungsfähige TEG-Module liefert, die für Anwendungstemperaturen von bis zu 310 °C geeignet sind. Der Prozess erlaubt zudem den Einsatz neuer, in der Entwicklung befindlicher, preiswerterer Materialien. Durch diese Kostenreduktion verlassen die TEG-Module endgültig ihr Nischendasein und können auch die Energiebilanz beim Anwender verbessern sowie zur CO2-Einsparung beitragen.
Herkömmliche TEGs
Bisher erfolgt die Herstellung von TEGs aus vielen einzelnen thermoelektrischen (TE-)Schenkeln weitgehend manuell. Dabei werden n- und p-Typ-Schenkel abwechselnd zwischen zwei dünnen keramischen Leiterbahnplatten so eingelötet, dass sie elektrisch in Reihe und thermisch parallel verschaltet sind. Die Herstellung der Einzelschenkel ist aufwendig und teuer:Aus Pulver des Aktivmaterials werden Blöcke gesintert, zu Scheiben zersägt, poliert, um sie auf exakt gleiche Dicke zu bringen und dann weiter zu kleinen Würfeln, den TE-Schenkeln zerteilt. Die Schenkel sind in der Regel quaderförmig und wenige Kubikmillimeter groß. Die Sägeprozesse verursachen erhebliche Materialverluste. Die elektrischen Kontaktstellen werden dann mit einer lötbaren, schützenden Metallisierung versehen. Für Anwendungen bei höherer Temperatur sorgt ein elektrisch isolierendes Coating der übrigen Schenkelseiten zudem für einen Oxidationsschutz.
Diese manufakturähnliche Herstellung der Module erlaubt keine industriell skalierbaren, kostengünstigen Prozesse und kann damit den Markt der Industrieanwendungen nicht bedienen. Weitere Einschränkungen liegen in der Zerbrechlichkeit der Module und des begrenzten Temperaturbereichs auf meist < 200 °C.
Neuer Hochleistungsprozess für TEGs
Die Innovation von der Evonik Creavis GmbH besteht in der gleichzeitigen Herstellung aller Schenkel eines TEGs innerhalb eines mechanisch stabilen, thermisch und elektrisch isolierenden Trägers. Aktivmaterial wird in zylindrische Ausstanzungen des Trägers überführt und thermisch getempert (Bild 2a). Die Trägermatrix erlaubt damit das simultane und präzise Einsetzen aller Schenkel gleichzeitig, was erstmalig die Automatisierung des sonst sehr aufwendigen Setzprozesses ermöglicht. Die Metallisierung dient einerseits der Sicherstellung niederohmiger Kontakte und andererseits zum Schutz des Aktivmaterials der Schenkel. Im nächsten Schritt werden die Schenkel mit Metallbrücken auf den Kontaktstellen verbunden und so in Reihe geschaltet, um eine möglichst hohe Modulspannung abzugreifen. Zuletzt sorgt die Beschichtung der TEGs mit einem hitzebeständigen, schwarzen Lack für die elektrische Isolation (Bild 2b).
Als Aktivmaterial dient der bewährte Halbleiter Bismuttellurid (Bi2Te3), der einen hohen Seebeck-Koeffizienten und eine gute Temperaturstabilität aufweist. Die Flexibilität des entwickelten Konzepts erlaubt aber auch den Einsatz neuer, in der Entwicklung befindlicher, preiswerterer Materialien.
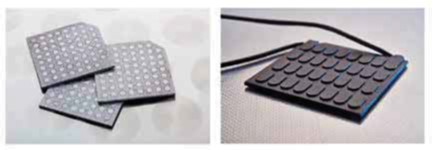
Die Vorteile des neuen Verfahrens sind: höhere Effizienz durch starke Prozessvereinfachung und Reduktion der Materialverluste bei der Schenkelherstellung. Der Prozess ist zudem skalierbar, automatisierbar und damit industriell für eine kostengünstige Massenproduktion geeignet (Bild 3). Eine Qualitätskontrolle der Schenkel ist in jedem Prozessschritt möglich. Eine weitere Leistungssteigerung ist durch den Verzicht auf die sonst eingesetzten spröden keramischen Verschaltungsträgerplatten (Wärmebarriere) realisierbar. Ein großer Gewinn ist auch die deutlich erhöhte mechanische Stabilität des TEGs durch Einbetten der Schenkel in einen stabilen, unzerbrechlichen Träger.
Die Wahl der Materialien erlaubt die Erschließung des für die Industrie sehr wichtigen höheren Temperaturbereiches über 200 °C bis hin zu 310 °C für den dauerhaften Einsatz zur Abwärmenutzung. Die speziell von Evonik entwickelte schwarze Hochtemperaturbeschichtung schützt das Modul vor äußeren Einflüssen im Einsatzbereich nd ist ideal angepasst an die effiziente Nutzung von Strahlungswärme.
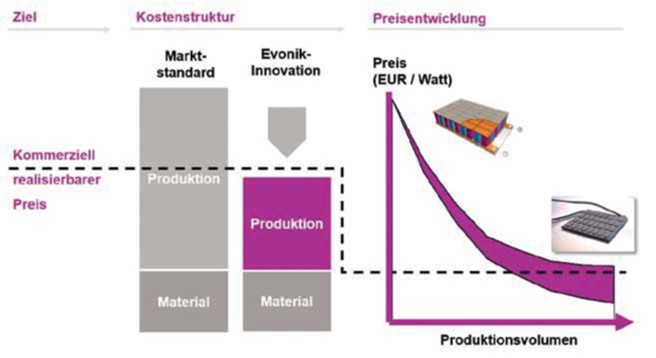
Anwendungen
Ungenutzte Abwärme fällt in vielen Bereichen des täglichen Lebens an. Großes Potenzial für eine Energierückgewinnung bieten speziell die Bereiche Mobilität, Industrie und Energieerzeugung. Durch
die Rückverstromung sind hier eine Effizienzerhöhung und eine damit direkt verbundene CO2-Emissionsverringerung realisierbar.
In der Mobilität eignen sich TEGs speziell für die Abwärmenutzung am Abgasstrang von Lastwagen oder Schiffsdieseln, welche hohe, konstante Wärmeströme liefern.
Ein hohes Potenzial für die Energierückgewinnung mithilfe von TEGs bieten zudem energieintensive Industrien aus den Bereichen Zement-, Glas-, Keramikund Metallherstellung und -verarbeitung – darunter auch Gießereien. Im Hochtemperaturbereich für TEGs von bis zu 310 °C können Esprix High-TEG-Module im direkten Kontakt mit der Wärmequelle und daher direkter Wärmeübertragung verwendet werden. Der robuste Modulaufbau und die Schutzbeschichtung erlauben einen großen Spielraum an Umgebungsbedingungen.
Industrieprozesse mit viel höheren Prozesstemperaturen zur Verarbeitung von Metallen, wie man sie zum Beispiel in Gießereien findet, stellen trotz der nwendungstemperaturgrenze der High-TEGs
eine sehr interessante Quelle für Strahlungswärme und indirekte Wärmeeinkopplung in TEGs dar. Hierbei muss die Distanz zur Strahlungsquelle geeignet gewählt werden, um ein Überhitzen > 310 °C zu verhindern. Geeignete Quellen sind Öfen, Verarbeitungsbereiche der heißen Metalle während des Gießens sowie Abkühlstraßen. Da die TEG-Module klein, dünn und kompakt sind, lassen sie sich sehr flexibel in Wandverkleidungen und Hitzeschirme verbauen. Dabei bewirkt die schwarze Beschichtung eine höchst effiziente Wärmestrahlungsabsorption.
Ausblick
Die Entwicklung der High-TEGs Esprix bei Evonik Creavis befindet sich momentan noch im Kleinserienstatus, um die Prozesse der Serienfertigung zu optimieren und zu verifizieren. Der nächste Schritt
ist die Systemintegration bei ausgewählten Entwicklungspartnern. Eine Serienfertigung mit größeren Stückzahlen (ASerie) ist dann ab 2019 geplant.
Dr. Stefan Schumann und Dirk Lehmann, Evonik Creavis GmbH, Essen, Patrick Stenner, Evonik Technology & Infrastructure GmbH, Hanau, Dr. Sascha Hoch, Evonik Technology & Infrastructure GmbH, Essen.
Literatur
[1] www.nachhaltigkeitspreis.de/2016_forschung_energiewandler_detail/