Energieaspekte bei brennstoffbeheizten Schmelz- und Warmhalteöfen (NE)
Die Gründe für den Einsatz elektrischer Energie bei Schmelzprozessen können verfahrenstechnischer und metallurgischer Natur sein.
- Bereitstellung von Prozesswärme ohne direkte Flammeneinwirkung vor Ort
- Keine Verunreinigungen der Legierungen durch unerwünschte Abgasbestandteile
- Möglichkeit Legierungswechsel unproblematisch vornehmen zu können
- Hohe Wärmeleistungsdichten
- Hoher Wirkungsgrad der Energiewandlung elektrischer Energie in Wärme am Einsatzort
Mögliche Nachteile können sein:
Durch die intensive Badbewegung können Verunreinigungen in die Schmelze eingebracht werden, die sich vom Gussbauteil nicht entfernen lassen.
Induktiv beheizte Öfen zeichnen sich durch folgende Eigenschaften aus:
- Gute Regelung der Energiezufuhr
- Gezielte Einstellung der Schmelztemperatur
1. Induktionsbeheizte Schmelzöfen
Die Anwendung des Induktionsprinzips zum Schmelzen von Metallen ist mit elektrischen und thermischen Verlusten der Ofenanlage verbunden, die in ihrer Höhe zum Einen von dem zu erschmelzenden Metall, zum Anderen vom Ofentyp abhängen.
Bei Metallen mit einem niedrigen spezifischen elektrischen Widerstand wie im Falle von Kupfer und Aluminium treten höhere elektrische und thermische Verluste auf, als dies bei Eisenwerkstoffen der Fall ist.
Der Gesamtwirkungsgrad eines Induktionsofens setzt sich zusammen aus dem elektrischen Wirkungsgrad (Effizienz des Einbringens der elektrischen Energie in das Schmelzgut) und dem thermischen Wirkungsgrad (Wärmeverluste beispielsweise über Wände und Abstrahlung).
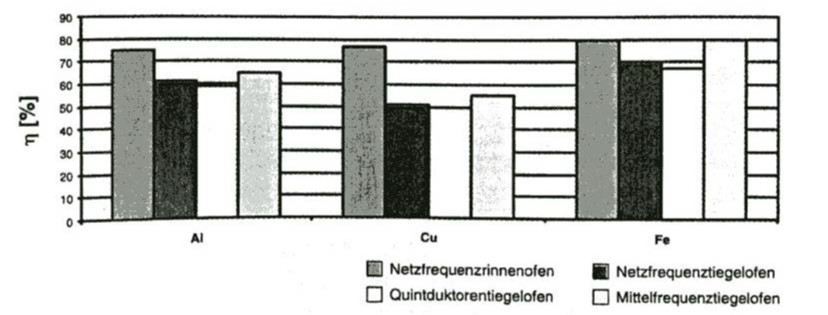
2. Induktions-Tiegelöfen
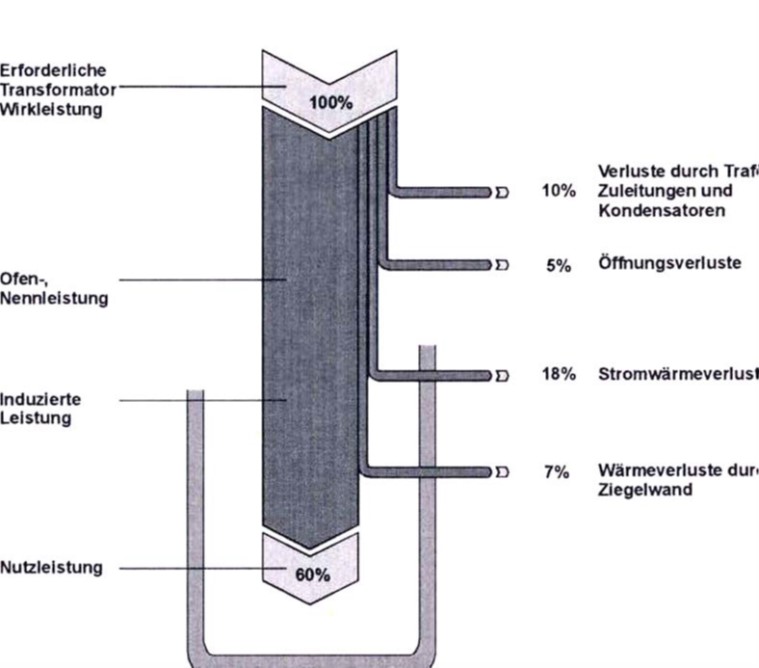
Der Gesamtwirkungsgrad eines Induktions-Tiegelofens, resultierend aus den elektrischen und thermischen Wirkungsgraden liegt nach [18] bei Aluminium im Bereich von 55 % bis 70 %.
Der Mittelfrequenz-Induktionstiegelofen (MF-ITO) weist deutlich höhere Leistungsdichten als ein Netzfrequenz-Induktionstiegelofen (NF-ITO) auf. Die höhere Leistungsdichte beim Mittelfrequenz-Induktionstiegelofen (MF-ITO) bewirkt kürzere Schmelzzeiten. Damit verbunden sind geringere Wärmeverluste.
Tabelle 1: Mittlerer spezifischer Energiebedarf von Elektroschmelzöfen verschiedener Bauart für Aluminium-Legierungen
Ofenart | Schmelztemperatur in °C | Schmelzenthalpie und Überhitzungswärme in kWhel/t | Wirkungsgrad in % | Tatsächl. spezifischer Energieverbrauch in kWhel/t |
Induktionsofen | 750 | 329 | 60-70 | 470-550 |
Widerstandsofen | 750 | 329 | 60-70 | 440-510 |
3. Induktions-Rinnenöfen
Induktions-Rinnenöfen werden in Formgießereien selten als Schmelzöfen und Gießöfen eingesetzt. Ein Vorteil des Induktions-Rinnenofens gegenüber dem Induktions-Tiegelofen ist sein besserer elektrischer Wirkungsgrad (Effizienz des Einbringens der elektrischen Energie in das Schmelzgut).
Beim Induktions-Rinnenofen entstehen in der Induktionsspule, dem Gehäuse und dem Kühlmantel elektrische Verluste. Thermische Verluste sind im Oberofen zu registrieren. Die Wirkungsgrade für das Schmelzen von Aluminium liegen etwa bei 70 % wie nachfolgendem Energieflussdiagramm zu entnehmen ist.
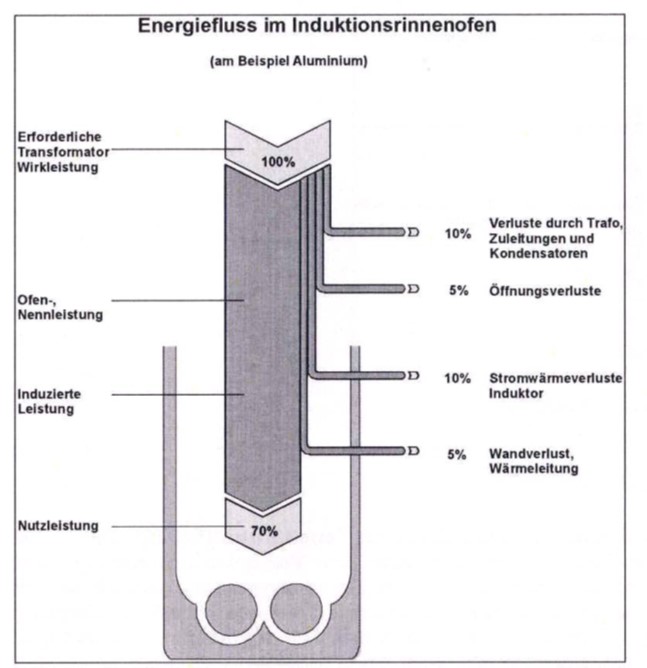
Tabelle 2: Wirkungsgrade und Energieverbrauchswerte für Induktions-Rinnenöfen
Ofenart | Mittlerer Wirkungsgrad in % | Spezifischer Energieverbrauch in kWhel/t |
Induktions-Rinnenofen | 83 | 430 |
Induktions-Tiegelofen | 65 | 530 |
4. Induktionsbeheizte Schmelzöfen in Kupfer,- Messing- und Zink- Gießereien
In den nachfolgenden Tabellen ist der typische mittlere Energieverbrauch von Elektroschmelzöfen verschiedener Bauart für Kupfer und Messing zusammengefasst.
Tabelle 3: Vergleich von Wirkungsgraden und Energieverbrauchswerten von Induktions-Tiegelöfen
NE-Metall | Mittlerer Wirkungsgrad in % | Spezifischer Energieverbrauch in kWhel/t |
Kupfer | 54 | 385 |
Messing | 63 | 260 |
Tabelle 4: Vergleich von Wirkungsgraden und Energieverbrauchswerten von Induktions-Rinnenöfen
NE-Metall | Mittlerer Wirkungsgrad in % | Spezifischer Energieverbrauch in kWhel/t |
Kupfer | 88 | 260 |
Messing | 80 | 225* |
Zink | 85 | 100 |
* Reiner Schmelzaufwand, ohne Nebenzeiten und Materialverluste ca. 195 – 200 [kWhel/t]
Am Beispiel eines 60 Tonnen fassenden Induktions-Rinnenofens zeigt Abbildung 4, dass die Fahrweise mit der vollen verfügbaren Nennleistung energetische Vorteile bietet.
Wird der Induktions-Rinnenofen statt mit 2000 KW mit der vollen Nennleistung von 4000 KW betrieben, so geht der spezifische Stromverbrauch von 285 auf 269 kWh/t Kupfer zurück.
Dabei ist mit zu berücksichtigen, dass auch die Ofenperipherie sowie die Fertigungsabläufe den Betrieb des Ofens mit voller Leistung gestatten müssen, um hier eine Energieeinsparung zu erzielen.
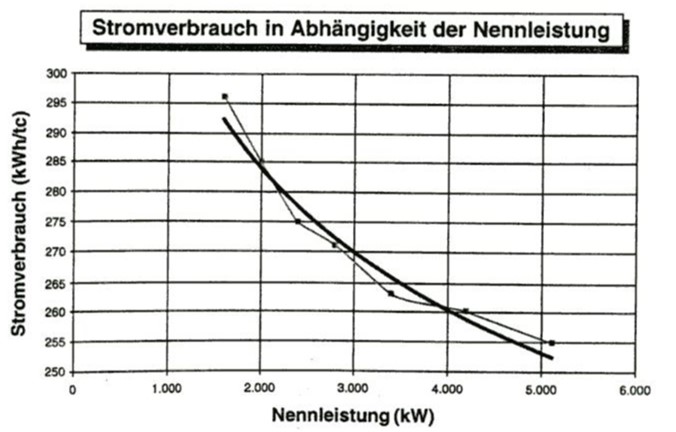
Quellen:
[18] Effiziente Energieverwendung in der Industrie – Teilprojekt „Metallschmelzbetriebe“; Effiziente Energienutzung in Nicht-Eisen-Metall-Schmelzbetrieben; Herausgeber: Bayerisches Landesamt für Umweltschutz; Augsburg 2005
[41] W. Schmitz; D. Trauzeddel; Energiesparendes Schmelzen von Kupferwerkstoffen in modernen Induktionsöfen; GP-Special; 1-2/2007