Energieeffiziente Produktion in NE-Schmelz- und Druckgießbetrieben
Forschung am Kompetenzzentrum für Industrielle Energieeffizienz (KIEff) der Hochschule Ansbach
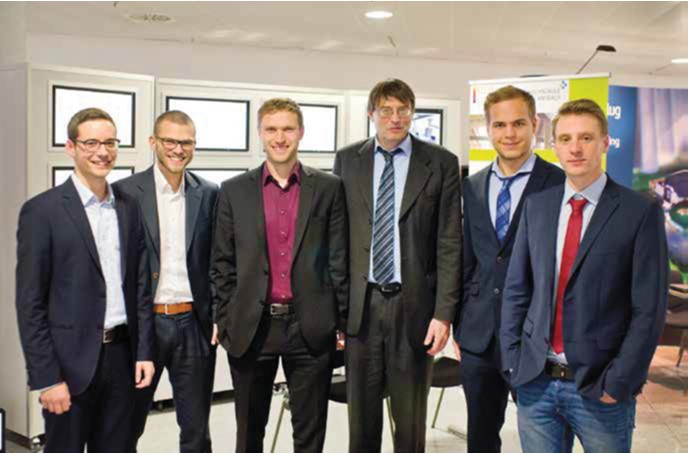
Das Team des KIEff auf dem 3. Green Factory Bavaria-Kolloquium 2016.
Erschienen in GIESSEREI 06/2017
Schwerpunkt der Forschung am Kompetenzzentrum KIEff der Hochschule Ansbach ist die Steigerung der Energieeffizienz in Nichteisenmetall-Schmelz- und Druckgießbetrieben. In verschiedenen Projekten des Forschungsverbundes Green Factory Bavaria und des Energie Campus Nürnberg (EnCN) werden gemeinsam mit industriellen Kooperationspartnern intelligente Lösungen für den Schmelz- und Druckgießbetrieb von morgen gesucht.
Bei den Forschungsarbeiten liegt der Fokus auf folgenden Themen:
- Simulation: Materialflusssimulation, energetische Modelle, Strömungs- und Wärmetransportsimulation,
- Datenanalyse: Untersuchung von Überlastsituationen im Schmelzbetrieb, Staplerauslastung, Ausfallverhalten von Druckgießmaschinen,
- Automatisierung: Onlineerfassung und Onlineanzeige von Prozessdaten aus dem Schmelz- und Druckgießbetrieb, Leitwartenkonzepte,
- Smart Services: Assistenzsysteme zur Stapler- und Schmelzofensteuerung, Prognosesysteme für Flüssigaluminiumbedarf, automatisierte Auswertung von historischen Prozessdaten.
Das KIEff arbeitet im Rahmen der Forschung eng mit dem durch Mittel des Europäischen Fonds für Regionale Entwicklung (EFRE) geförderten Kompetenzzentrum Strömungssimulation (KSTS) zusammen, in dem der Schwerpunkt auf der Simulation von Strömungs- und Wärmetransportvorgängen liegt. Schnittpunkte ergeben sich beispielsweise bei der Untersuchung der thermodynamischen Vorgänge im Schmelzofen durch Strömungssimulation sowie der Bestimmung der Einflussfaktoren bei den Wärmeverlusten beim Flüssigaluminiumtransport. Die Forschungsergebnisse werden im Rahmen von Veranstaltungen wie dem Deutschen Druckgusstag oder dem Green
Factory Bavaria-Kolloquium einem Fachpublikum präsentiert (Bild oben).
Das KIEff ist in der Fakultät Ingenieurwissenschaftenan der Hochschule Ansbach angesiedelt. Studierenden der Fachrichtungen Energie- und Umweltsystemtechnik,
Wirtschaftsingenieurwesen sowie Produktions- und Automatisierungstechnik bietet sich nach dem Erlernen von Simulations- und Automatisierungstechniken in grundlegenden Vorlesungen und Praktika die Möglichkeit, anhand von industrienahen Fragestellungen Themen aus dem Bereich Industrie 4.0 für die Schmelz- und Druckgießindustrie zu bearbeiten. Dies kann in Form von teamorientierten Projektarbeiten, Bachelor- und Masterarbeiten geschehen. Themen wie „Simulationsgestützte Analyse der Behältervorwärmung bei der Bereitstellung von Flüssigaluminium“ oder „Usability mit der Visualisierung von Maschinendaten in Echtzeit im Rahmen von Industrie 4.0.“ können hier beispielhaft genannt werden. Im Folgenden werden exemplarisch einige Forschungsarbeiten beschrieben.
Verringerung des spezifischen Energieverbrauchs in Schmelzereien der NE-Schmelz- und Druckgießindustrie durch Prozesssimulation
Bearbeiter: Matthias Henninger, B.Eng.
Der Energiekostenanteil in der NESchmelz- und Druckgießindustrie kann laut statistischem Bundesamt 25 % der Bruttowertschöpfung übersteigen. Diese hohe Belastung zeigt sich auch durch eine hohe Stromkostenintensität, welche für 25 % der deutschen Gießereien hoch genug ist, um eine EEG-Befreiung/Reduktion zu erhalten. Bis zu 60 % dieser Energie entfallen auf den Aufschmelzvorgang des Aluminiums, welcher in der Regel in gasbefeuerten Sekundäraluminiumschmelzöfen der werksinternen Schmelzerei abläuft. Die Energieeffizienz der verwendeten Schmelzöfen ist stark abhängig von dessen Bauart, Alter, Auslastung und Betriebsweise. Aufgrund der schlechten Datengrundlage des Schmelzleiters, der Produktionsschwankungen in der Gießerei, der Überdimensionierung der Öfen und der komplexen Bedarfsabschätzung
an flüssigem Aluminium werden die Öfen häufig außerhalb des idealen Betriebsbereiches gefahren, wodurch Energie verschwendet wird.
Um die Auswirkungen der genannten Betriebseinflüsse sowie spezifische Ofeneinflussgrößen auf den Energieverbrauch zu untersuchen und Verbesserungspotenziale zu identifizieren, wurde am Kompetenzzentrums für industrielle Energieeffizienz (KIEff) ein dynamisches Prozesssimulationsmodell zum Energie- und Materialfluss innerhalb des Schachtschmelzofens entwickelt und an verschiedene Ofentypen adaptiert. Um die Qualität der entwickelten Modelle zu garantieren, werden die Modelle mit Messdaten validiert. Der Vergleich zwischen Messung und Simulation ergibt in der Regel Abweichungen kleiner 10 % und bestätigt die Eignung des Simulationsmodells für weiterführende Untersuchungen. Mit dem validierten Energiemodell können die Auswirkungen der folgenden Rahmenbedingungen/ Einflussfaktoren auf die wichtigsten
Leistungsdaten des Schmelzofens (wie Schmelzleistung und Energieverbrauch) untersucht werden:
- Füllstand des Schmelzschachtes,
- Auslastung des Schmelzofens,
- Steuerung der Brenner,
- Beschickungshäufigkeit,
- Temperatur des Beschickungsmaterials (externe Vorwärmung der Masseln),
- Reihenfolge des Beschickungsmaterials,
- Verweildauer des flüssigen Aluminiums und
- Dämmung des Warmhaltebereichs.
Ausgeführte Simulationsstudien bestätigen die herausragende Bedeutung der Ofenauslastung und des Schmelzschachtfüllstandes für den spezifischen Energieverbrauch des Schmelzofens (Bild 1).
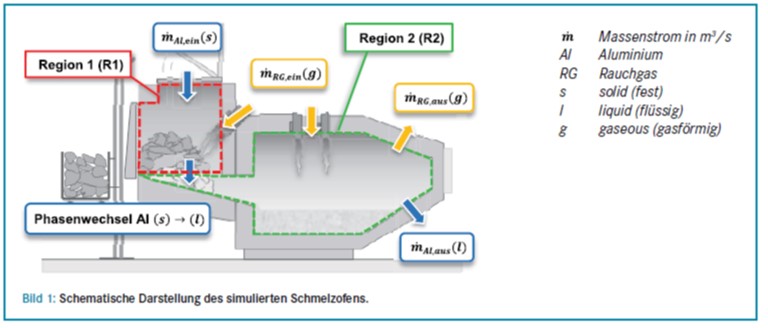
Im Rahmen von Modellerweiterungen sollen Energieflussmodelle für die Transportvorgänge des Flüssigaluminiums mit den Gabelstaplern und im Dosierofenspeicher der Druckgießmaschinen entwickelt und implementiert werden. Dies ermöglicht die Untersuchung der kompletten Flüssigaluminiumtransportkette und die energetische Bewertung verschiedener Betriebsstrategien. Damit lässt sich z. B. die energetisch ideale Überhitzungstemperatur des Aluminiums in der Schmelzofenwanne ermitteln. Des Weiteren kann der Energieverbrauch des Dosierofenspeichers in Abhängigkeit der Speicherdauer bewertet werden.
Durch die Wahl des dynamischen Prozesssimulationsansatzes und die damit verbundene Verringerung der mathematischen Komplexität ist das Modell auch für Langzeituntersuchungen oder für die Integration in ein Gesamtmodell, welches die komplette Aluminiumkette vom Schmelzen bis zum Gießen erfasst, geeignet.
Einsatz numerischer Strömungssimulationen zur Steigerung der Energieeffizienz im Schmelzbetrieb
Bearbeiter: Konstantin Zacharias, M.Sc.; Stefan Müller, B.Eng.
Der Prozess des Metallschmelzens in den Gießereien weist den höchsten Energieverbrauch innerhalb des Betriebes, aber auch gleichzeitig das größte Einsparpotenzial auf. Mit einer Bündelung der Expertisen der Kompetenzzentren Industrielle Energieeffizienz (KIEff) und Strömungssimulation (KSTS) werden numerisch die Strömungsvorgänge und der Wärmetransport im Schmelzofen untersucht. Mit der Kenntnis dieser Transportvorgänge kann die Betriebsweise der Öfen optimiert werden.
Aufgrund der hohen Komplexität der physikalischen Phänomene im Schmelzofen werden zunächst vereinfachte numerische Modelle erstellt, validiert und die Ergebnisse anschließend auf Simulationsmodelle mit realistischer Ofengeometrie übertragen. So wurde in einem Projekt die konvektive Wärmeübertragung vom Rauchgas zur Schüttung in einem Schmelzofen untersucht. Dabei wurde die Abhängigkeit des Wärmeübergangskoeffizienten von unterschiedlichen Verhältnissen von Oberfläche zu Volumen (A/V-Verhältnis) der Schüttung und der Strömungsgeschwindigkeit analysiert. Es konnte aufgezeigt werden, dass der Wärmeübergangskoeffizient linear mit der Einströmgeschwindigkeit und dem A/VVerhältnis ansteigt. Die örtliche Strömungsgeschwindigkeit in den Zwischenräumen der Schüttung ist jedoch entscheidender für die Wärmeübertragung als die Vergrößerung der Oberfläche der Schüttung.
In weiteren Projekten werden die Wärmestrahlung und der Schmelzvorgang detailliert untersucht, um den kompletten Aufwärm- und Schmelzprozess stationär simulieren zu können. Die Ergebnisse dienen zusammen mit erhobenen Messwerten der Kalibrierung von dynamischen Simulationsmodellen verschiedener Schmelzöfen, mit denen kann deren Betriebsführung optimiert werden kann.
Eine bereits in der Praxis befindliche Maßnahme zur Steigerung der Energieeffizienz ist die Vorwärmung der Masseln in Vorwärmkammern. Die Kammer wird dabei mit der Wärme aus den Abgasen des Ofens beheizt. Durch die Vorwärmung der Masseln verringern sich die zum Schmelzen benötigte Energie sowie die Schmelzdauer. Anhand von Strömungssimulationen wurden der Erwärmungsvorgang eines Masselpaketes in einer Vorwärmkammer berechnet und eine Parameterstudie zur Auswirkung der Einflussgrößen durchgeführt (Bild 2). Dabei zeigt sich der große Einfluss der Einströmgeschwindigkeit, der Rauchgastemperatur und der Paketgeometrie auf die benötigte Vorwärmdauer (Bild 3). Mit der Erkenntnis aus der Parameterstudie kann mit einer optimierten Anordnung des Masselpaketes eine Verkürzung der Aufwärmdauer um bis zu 22 % erreicht werden.
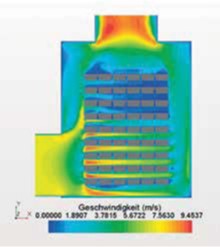
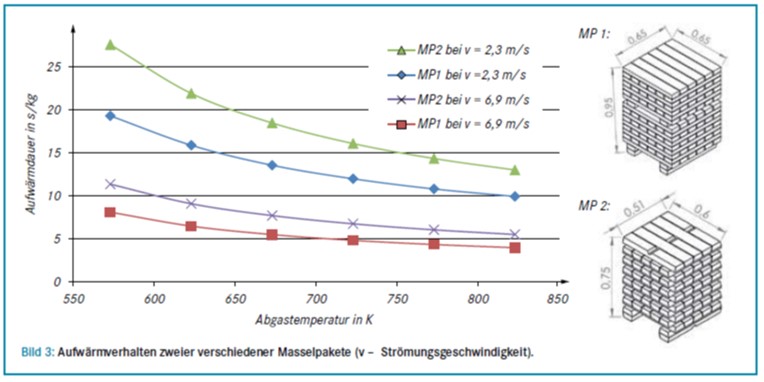
Spezifische Kennzahlen als Basis zur Definition von Smart Services zur Steigerung von Energieeffizienz und Produktivität
Bearbeiter: Jörg Schmidt, M.Sc.
Die Erfassung der anlagenübergreifenden Versorgungssituation der Druckgießmaschinen mit flüssigem Aluminium ist eine wesentliche Voraussetzung für die Lösung des Problems einer ineffizienten Ofenbetriebsweise. Die Betrachtung basiert dabei auf speziell definierten Kennzahlen.
In einem ersten Schritt werden die Füllstände der verschiedenen Flüssigaluminiumquellen (Schmelzöfen) als eine Einheit sowie die Füllstände der verschiedenen Flüssigaluminiumsenken (Druckgießmaschinen) betrachtet (Bild 4). Diese Annahme ermöglicht die Entwicklung der sogenannten Speicherverteilungskennzahl, die die aktuelle Versorgungssituation der Druckgießanlagen mit flüssigem Aluminium beschreibt. Die spezielle Kennzahl ist in der Lage, den komplexen, anlagenübergreifenden Versorgungszustand zu beurteilen. Mithilfe dieser Kennzahl und weiteren etablierten Produktionskennzahlen wie dem OEE-Index oder Auslastungsgraden von Maschinen kann eine spezifische Sammlung von Kennzahlen für NE-Schmelz- und Druckgussunternehmen generiert werden. Diese Kennzahlensammlung ermöglicht die Echtzeit-Aus-wertung des Betriebszustandes (Produktionssicherheit, Maschinenauslastung, Energieverbrauch) und kann zudem zur Steuerung der Betriebsprozesse verwendet werden.
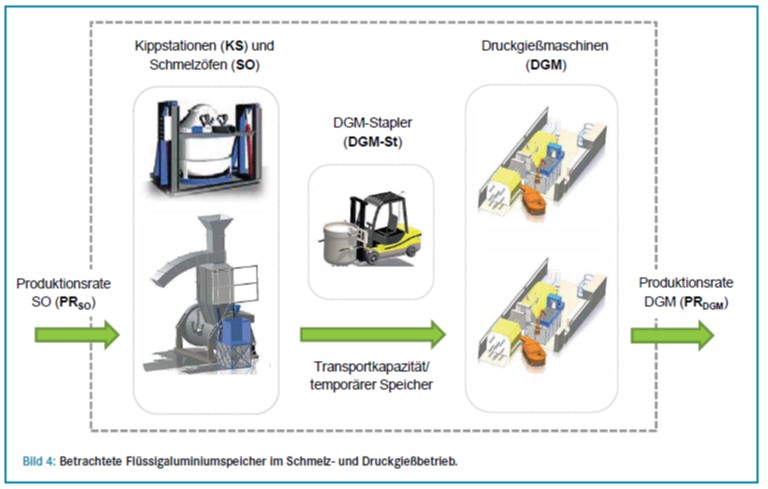
Um diese Betriebsprozesse zu optimieren, ist eine Simulation erforderlich, da sonst der reale Produktionsprozess beeinträchtigt werden würde. Die Simulation des kompletten Aluminium-Materialflusses beginnt mit der Anlieferung in fester und flüssiger Form, setzt sich mit dem Einschmelzen in Schmelzöfen fort und führt schließlich zur Produktion in den Druckgießmaschinen. Der Gasverbrauch des Schmelzvorgangs und weitere energetische Kennzahlen können durch bidirektionale Kopplung mit einem physikalisch basierten Energiemodell der Schmelzöfen bestimmt werden. Das Simulationsmodell wurde durch Messdaten in einer Industrieanlage validiert. Die Ergebnisse der Simulation zeigen die Auswirkungen unterschiedlicher Steuerungsmaßnahmen auf die Schmelz- und Druckgießanlagen. Mit der entwickelten Sammlung von Kennzahlen können die Effekte quantifiziert werden. Damit erhält man einen Einblick in die aktuelle Betriebsweise und kann Optimierungsmaßnahmen ableiten. Beispielsweise erhöht die Vorwärmung des festen Aluminiums die Energieeffizienz im Schmelzvorgang deutlich. Die erhöhte Schmelzleistung kann die Produktivität der Druckgießmaschinen vergrößern.
Perspektivisch kann die Speicherverteilungskennzahl mit anderen Kennzahlen kombiniert werden, um Smart Services zur Steigerung der Energieeffizienz und Produktivität in bestimmten Betriebszuständen zur Verfügung zu stellen. Die Anpassung der Reinigungszeiten der Schmelzöfen oder die Kontrolle der Leistung der Schmelzbrenner sind mögliche Beispiele. Smart Services im realen Betrieb können als Assistenzsystem oder als modellprädiktive Steuerung implementiert werden.
Onlineanzeige und historische Analyse von Prozessdaten in Schmelz- und Druckgießbetrieben
Bearbeiter: Jakob Krieg, B.Eng.
Das Forschungsprojekt „User interface design von Energiedaten in energieintensiven Betrieben“ hat das Ziel, Prozessdaten und Kennzahlen von Schmelz- und Druckgießbetrieben nutzerorientiert auf mobilen Endgeräten online anzuzeigen. Dadurch soll der Betriebsablauf optimiert werden, der bis jetzt wesentlich durch den Erfahrungsschatz der Staplerfahrer gesteuert wird. In verschiedenen Pilotprojekten werden dafür zunächst alle Maschinendaten auf einem Server gesammelt, um diese anschließend online zu visualisieren. So ist es möglich, verschiedenen Nutzergruppen einen Überblick über die aktuelle Betriebssituation zu geben. Dadurch kann beispielsweise den Staplerfahrern direkt vermittelt werden, welche Maschinen angefahren werden müssen, ohne davor jede Maschine kontrolliert zu haben. Fertigungsleiter können die Betriebslage jederzeit vom Büro aus überwachen und daraus entsprechende Handlungsmaßnahmen ableiten. Dabei gilt es, die verschiedenen Nutzergruppen zu identifizieren und Kennzahlen dementsprechend nutzerspezifisch darzustellen. Mithilfe der zentralen Speicherung von Maschinendaten sind weitere Smart Services, wie beispielsweise ein Assistenzsystem oder eine modellprädiktive Steuerung geplant, deren Umfang von den bereitgestellten Daten der Maschinensensorik abhängen. Gemeinsames Ziel der Smart Services ist es, den Staplerfahrer durch Informationstransparenz zu entlasten und gleichzeitig den Betriebsablauf zu optimieren. Diese Ziele entsprechen dem Grundgedanken von „Industrie 4.0“, der in Schmelz- und Druckgießbetrieben bis jetzt nur wenig Anwendung findet, jedoch nicht vernachlässigt werden sollte, um auch zukünftig konkurrenzfähig zu bleiben.
Um die Produktionssicherheit und Energieeffizienz abschätzen und optimieren zu können, müssen in der Schmelzund Druckgießindustrie eine große Menge an Kennzahlen zur Analyse herangezogen werden. Mit dem Auswertetool Melting Analytics, das vom Kompetenzzentrum KIEff speziell für die Schmelzund
Druckgussindustrie entwickelt wurde, lässt sich diese Aufgabe effizient durchführen.
Zunächst wurde diese Auswertesoftware für die Fertigungssimulation des Schmelz- und Druckgießbetriebes entwickelt, um die große Anzahl an anfallenden Prozessdaten und die über 100 relevanten Kennzahlen mithilfe einer grafischen Benutzeroberfläche schnell und flexibel auswerten zu können (Bild 5). Dabei wurde bewusst eine plattformunabhängige Datenbasis gewählt, um die Auswertesoftware an reale Schmelz- und Druckgießbetriebe ankoppeln zu können. So wird Melting Analytics aktuell bei einem industriellen Projektpartner eingeführt, um Betriebsabläufe historisch zu analysieren und dabei Schwachstellen zu identifizieren. Um dies verschiedenen Benutzern zu ermöglichen, werden alle Maschinendaten auf einem Server gespeichert, auf den verschiedene Endgeräte zugreifen können. Es wird damit möglich sein, jegliche Betriebsprozesse mithilfe von Melting Analytics effizient historisch auszuwerten und entscheidende Kennzahlen automatisiert zu generieren. Dafür können sowohl einzelne Maschinen und Gruppen von Maschinen, beispielsweise für unterschiedliche Legierungen, als auch der Gesamtbetrieb herangezogen werden. Durch die zunehmende Digitalisierung der Industrie wird zukünftig auch in der Schmelz- und Druckgussindustrie die Verwendung und Auswertung von Betriebsdaten eine immer größere Rolle spielen.
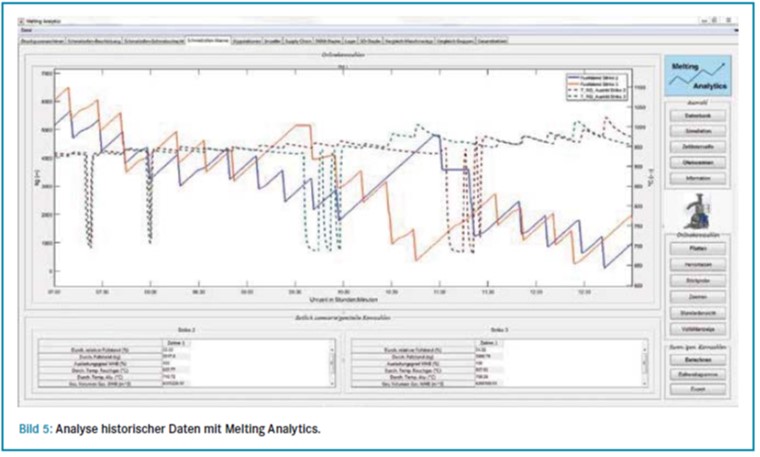
Weitere Informationen:
Hochschule Ansbach
Fakultät Ingenieurwissenschaften
Kompetenzzentrum Industrielle Energieeffizienz
Prof. Dr. Wolfgang Schlüter
Residenzstraße 8
91522 Ansbach
Tel.: 0981/4877-339
E-Mail: wolfgang.schlueter@hs-ansbach.de
www.hs-ansbach.de