Energieeffizienz bei Lichtbogenöfen
Bezug zum BREF Gießerei, Ausgabe Mai 2005
Siehe Abschnitt im Foundry-BREF: 2.4.2
Beschreibung
Für die Stahlherstellung ist der Lichtbogenofen besonders gut geeignet.
Ein Lichtbogenofen ist ein Elektroschmelzofen, bei dem mittels
Graphitlanzen ein Lichtbogen oberhalb des metallischen
Einsatzmaterials und der Stahlschmelze erzeugt wird. Der Lichtbogen weist hohe Energiekonzentrationen auf und am Lichtbogen selbst sind Temperaturen bis zu 4000 °C möglich.
Neben den Rohstoffen ist der spezifische elektrische Energiebedarf eine der wichtigsten Kostengrößen in der Elektrostahlherstellung. Der Einfluss der verschiedenen Stoffeinsätze und Energieträger auf den spezifischen elektrischen Energiebedarf, auf die Produktivität und auf die Produktionskosten ist dabei von besonderem Interesse.
Die aktuellen Entwicklungen der Kosten für Stahlschrott, Rohstoffe und Energie verstärken das Bestreben, die kostenoptimale Zusammenstellung der Energien unter Berücksichtigung der metallurgischen Randbedingungen für den Lichtbogenofenprozess einzustellen. Die Anzahl an Lichtbogenöfen in Deutschland geht langfristig zurück. Lichtbogenöfen sind in Deutschland aufgrund der hohen Temperaturen ausschließlich in Stahlgießereien im Einsatz.
Technische Beschreibung
Der spezifische Energiebedarf von Lichtbogenöfen ist in den letzten 50 Jahren signifikant vermindert worden.
Zwischen 1991 und 2005 sank der mittlere spezifische elektrische Energiebedarf der Elektrostahlwerke in Deutschland von 562 kWh/t auf 525 kWh/t und der spezifische Erdgasverbrauch von 21 m³/t auf 11 m³/t. Demgegenüber stieg der spezifische Sauerstoffverbrauch in den Elektrostahlwerken von 24 m³/t auf 36 m³/t.
Gleichzeitig sind auch die Schmelzfolgezeit und der spezifische Elektrodenverbrauch gesunken.
Entscheidende Maßnahmen sind in der folgenden Grafik visualisiert:
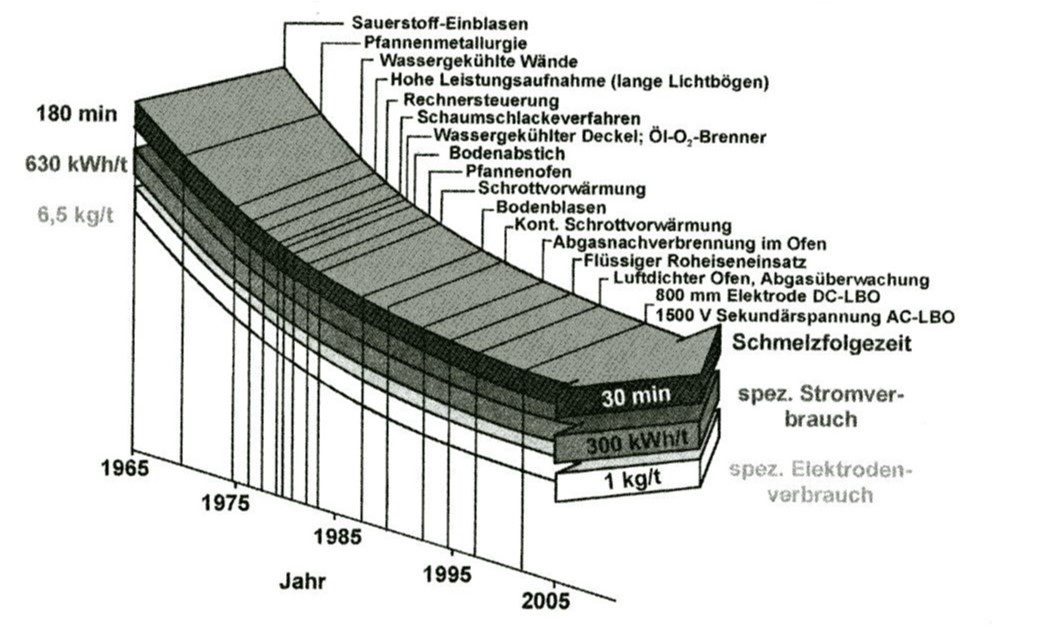
Entscheidendes Potenzial zur Verbesserung der Energieeffizienz wird in der Modernisierung bestehender Lichtbogenöfen gesehen. Zunehmende Verschleißerscheinungen, Leistungsabfall und Störungen sind erste Anzeichen bei Lichtbogenöfen, dass eine Instandsetzung sowohl ökonomische als auch ökologische Verbesserungen bringt.
Mögliche Ansatzpunkte sind die Ofenkühlung, die Leistungsschalter mit Wandler, der Ofentransformator, die komplette Ofensensorik und Notabschaltungen.
Bei einem 8-Tonnen-Ofen konnten folgende Verbesserungen erzielt werden:
Tabelle 1: Kennwerte vor und nach der Instandsetzung
Instandsetzung, Modernisierung | Vorher | Nachher | Ergebnis | ||
Chargen-Nr. | xxx | xxx | |||
Datum | 02.02.12 | 28.03.12 | |||
Bezeichnung | Einheit | Basis | |||
Einschmelzen | 1545 °C | ||||
Einsatzmasse (kalter Satz) | T | 8,200 | 7,900 | 8,200 | 8,200 |
Einschmelzzeit (1545/1537 °C) | Min | 94 | 77,00 | 79,8 | |
Lastzeit | Min | 91,2 | 73,9 | 76,7 | -14 |
Mittlere Einschmelzleistung (Lastzeit) | tk.S./h | 5,397 | 6,414 | 6,356 | 0,959 |
Mittlere Einschmelzleistung brutto | tk.S./h | 5,234 | 6,156 | 6,104 | 0,870 |
Elektroenergieverbrauch | kWh | 3655 | 3220 | 3342 | |
Mittlerer Energieeintrag (Lastzeit) | kWh/min | 40,1 | 43,6 | 43,6 | |
Spezifischer Energieverbrauch | kWh/t | 445,7 | 407,6 | 407,6 | -35 |
Spezifische Leistung | kW/t | 293 | 331 | ||
Badtemperatur Einschmelzende | °C | 1550 | 1545 | ||
Mittlere Stromstärke (ms) | kA | 9,428 | 9,381 | 9,381 | |
Werkwiderstand | mΩ | 9,020 | 9,902 | ||
Verlustwiderstand (Dr.+Tr.+Leitung) | mΩ | 0,987 | 0,887 | -0,1 | |
Lichtbogenwiderstand | mΩ | 8,033 | 9,015 | ||
Lichtbogenspannung | V | 75,7 | 84,6 | ||
Lichtbogenlänge | mm | 55 | 56 | ||
Wirkleistung | kWh/h | 2405 | 2614 | 209 | |
Elektrische Verlustleistung | kWh/h | 263 | 234 | ||
Wärmeverluste | kWh/h | 268 | 260 | -8 | |
Lichtbogenleistung | kWh/h | 2142 | 2380 | ||
Nutzleistung | kWh/h | 1874 | 2120 | 2120 | 246 |
Elektro-thermischer Widerstand | 0,779 | 0,811 | 0,033 | ||
Elektrischer Wirkungsgrad | 0,891 | 0,910 | |||
Strahlungsfaktor (ohne Abdeckung) | MWV/m2 | 89 | 110 | 22 | |
GE-Verbrauch (berechnet) | kgGE/t | 3,047 | 2,557 | 2,565 | -0,48 |
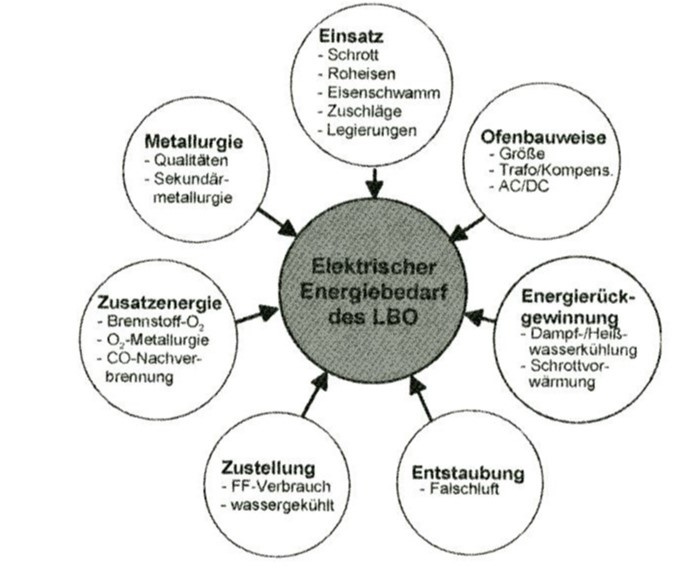
Weitere Maßnahmen zur Verbesserung der Energieeffizienz:
- Effiziente Prozesssteuerung zur Verkürzung der Schmelz- und Behandlungszeiten
- Wirksames Auffangen und Abkühlen der Ofenabgase zur Entstaubung
- Rückführung des Filterstaubs in den Lichtbogenofen Energierückgewinnung aus dem heißen Abgas und Stahlschrottvorwärmung auf mehr als 600 Grad Celsius
- Auslastung sowie Energieeffizienz durch das Aufheizen mit Strom ebenso wie das Nachladen von Schrott auch während des Abstichs verbessern
Das Schaumschlackeverfahren basiert auf dem gleichzeitigen Einblasen von Sauerstoff und Kohlenstoff (in Form von Kohlenstaub) in die Schlacke am Ende des Schmelzprozesses. Der Schlackenschaum entsteht aufgrund von CO-Blasen. Das CO-Gas entsteht durch die Oxidation von Kohlenstoff im Metall durch den eingeblasenen Sauerstoff und durch die Reduktion von Eisenoxid (FeO) durch den eingeblasenen Kohlenstoff.
Die Erzeugung einer schaumigen Schlacke verbessert den Wärmeübergang auf das Einsatzmaterial und schützt das Feuerfestmaterial im Inneren des Ofens. Aufgrund der besseren Stabilität des Lichtbogens und der geringeren Strahlungseffekte führt Schlackeschäumen zu Minderungen des Energiebedarfs und durch einen geringeren Elektrodenverbrauch zu einer Steigerung der Produktivität. Dieses Verfahren, das eine Steigerung der Effizienz des Ofenbetriebes verspricht, ist bei allen neuen und bestehenden Lichtbogenofen-Gießereien, die das Sauerstoffeinblasen praktizieren, anwendbar und entspricht dem Stand der Technik.
Erreichter Umweltnutzen
- Verbesserung der Energieeffizienz
- Reduzierung der Emissionen
Verlagerungseffekte
Keine Verlagerungseffekte
Anwendbarkeit
In allen (Stahl)Gießereien mit Lichtbogenöfen.
Wirtschaftliche Aspekte
Für alle individuellen Maßnahmen sind eigene Amortisationszeiten zu berechnen. Häufig ist die Instandsetzung des bestehenden Lichtbogenofens eine kostengünstige Alternative zur Neuinvestition.
Gründe für die Anwendung dieser Technik
Die Motivation für die Implementierung liegt in der Steigerung der Effizienz des Ofenbetriebes.
Referenzanlagen
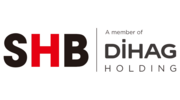
- SHB Stahl- und Hartgusswerk Bösdorf GmbH, Leipzig
- Tyasa, Ixtaczoquitlan (Mexiko)
Informationsquellen
- Energieeffizienter Gießereibetrieb Version 1.0
- Kirschen, M. (2007): Energieeffizienz und Emissionen der Lichtbogenöfen in der Stahlindustrie, Düsseldorf 2007
- Kuhlow, P.; Weber, W.; Sachse, G. (2012): Modernisierung von Drehstrom-Lichtbogenöfen in Stahlgießereien. In: Elektrowärme International, Nr. 4, S. 57-64
- Siemens AG (2010): Recycling von Stahl wird umweltfreundlicher, Abruf April 2013
- Siemens AG (2012): Neuer Lichtbogenofen spart CO2 bei Stahlerzeugung, Abruf April 2013