Rationeller Energieeinsatz in der aluminiumverarbeitenden Industrie
Von Ansgar Ringleb, Sven Hirschberg, Wolfgang Schlüter, Dietrich Schneider und Günther Pröbstle, Ansbach, sowie Arno Dentel und Wolfram Stephan, Nürnberg
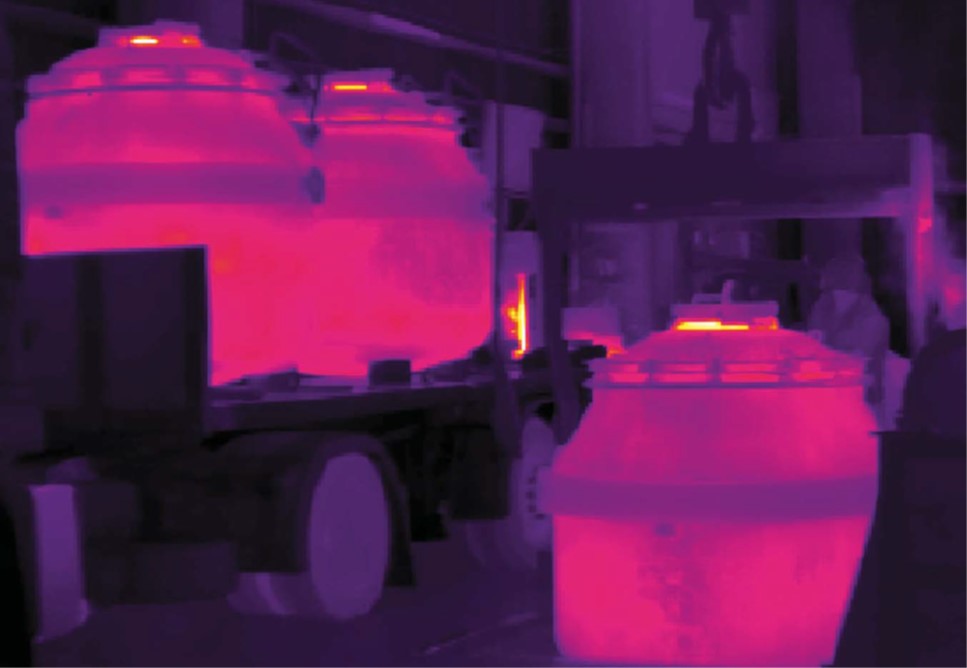
Wärmebildaufnahme eines Lkws während des Beladens mit Aluminiumtiegeln.
Erschienen in GIESSEREI 06/2013
In der metallverarbeitenden Industrie zählt der Schmelzvorgang zu den energieintensivsten Prozessen mit den größten Energieeffizienzpotentialen. Aluminiumschmelz- und -gussbetriebe suchen im Zuge der Energiewende verstärkt nach Möglichkeiten, die hohen spezifischen Energiekosten ihrer Fertigung zu reduzieren. In einem Teilprojekt des bayerischen „Forschungsverbundes Energieeffiziente Technologien und Anwendungen“ (FORETA) wurden die Möglichkeiten eines rationellen Energieeinsatzes in der aluminiumverarbeitenden Industrie untersucht.
Transport von Flüssigaluminium
Aufbauend auf grundlegenden Arbeiten zur Energieeffizienz und effizienten Anwendungen in Aluminiumschmelzbetrieben [1] wurden in Zusammenarbeit mit einschlägigen Firmen Möglichkeiten zur Abwärmenutzung sowie zur Optimierung des Transportes von Flüssigaluminium untersucht. Der Flüssigaluminiumtransport nimmt zunehmend eine tragende Rolle in der Aluminium-Gießerei-Industrie ein.
Dabei werden hohe Anforderungen an die Schmelzbetriebe gestellt: so muss das flüssige Aluminium in einem engen Temperaturfenster angeliefert und über weite Fahrtstrecken im öffentlichen Straßenverkehr transportiert werden. Dabei wird die Abkühlung des flüssigen Aluminiums beim Transport von einer Vielzahl von Prozessparametern beeinflusst. Die Beherrschung des Abkühlprozesses und damit die Steigerung der Prozesssicherheit stand im Fokus der Untersuchungen. Demzufolge kann der Transport von Flüssigaluminium weiter verbessert und Energiepotentiale in der Produktion gehoben werden.
Der Abkühlprozess wird durch Prozessbedingungen (Krätzebildung, Zustand der Isolierung), die Wärmetransportmechanismen (Wärmeleitung, Konvektion und Wärmestrahlung) und Umwelteinflüsse (Sommer/Winter, Regen, Verkehrslage) beeinflusst. Zur Analyse und Bewertung dieser Einflussfaktoren wurden modernste Mess- und Simulationstechniken eingesetzt.
Die Abkühlung der Schmelze während des Transportes wurde durch Temperatursensoren erfasst und dokumentiert. Zur Sichtbarmachung der Wärmeverluste am Transportbehälter wurde Infrarotthermographie und Temperaturmesstechnik eingesetzt (Bild links). Zur Bestimmung der Einflüsse auf den Abkühlvorgang wurden Strömungssimulationen (engl. Computational Fluid Dynamics, CFD) der Lkw-Fahrt und dynamische Simulationen des Abkühlprozesses durchgeführt.
Zunächst wurden die Einflussfaktoren während des Lkw-Transportes mittels Strömungssimulation bestimmt. Dazu wurde ein CAD-Modell des Lkws und des Aufliegers mit den Transportbehältern erstellt. Anschließend wurde die Lkw-Fahrt simuliert und der Wärmetransport an den Behälterbereichen ermittelt (Bild 1). Dieser wurde in Form von Wärmeübergangskoeffizienten in die sogenannte Fahrtensimulation eingelesen. Die Fahrtensimulation selbst ist ein dynamisches Simulationsmodell der Abkühlung der Aluminiumschmelze, wobei ein instationärer Temperaturausgleichsprozess auf Basis von Energiebilanzen numerisch gelöst wird.
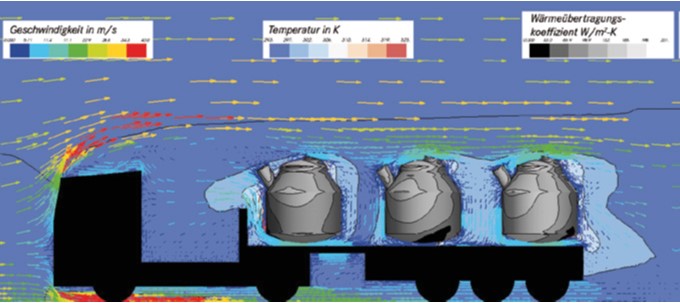
Zur Validierung der Simulationen wurden umfangreiche Messdaten aus über 100 Lkw-Transporten in Kooperation mit den Industriepartnern erhoben und ausgewertet. Mittels dieser Messwerte konnten die Simulationen stetig verbessert werden. Letztendlich konnte mit Hilfe der Simulationen die Abkühlung im Mittel mit ca. 7 % Genauigkeit vorausberechnet werden.
Die so entwickelte Simulation des Abkühlverhaltens konnte nun zur gezielten Untersuchung der Einflussfaktoren herangezogen werden. Zu Beginn des Forschungsvorhabens herrschte größtenteils Unklarheit über die Art und Höhe des Einflusses einzelner Faktoren wie Wetter oder Verkehrsbedingungen. Im Zuge der Untersuchungen konnte die Anzahl möglicher Einflussfaktoren von weit über 10 auf 4 nennenswerte Einflüsse reduziert werden. Des Weiteren konnte gezeigt werden, dass die Masse des flüssigen Aluminiums einen besonderen Einfluss auf das Abkühlverhalten besitzt. So bewirkt eine um 1,5 t gesteigerte Aluminiummasse eine um 2,4 K/(h*t) reduzierte Abkühlung des Flüssigaluminiums, dies entspricht ca. 60 % des Gesamteinflusses auf die Abkühlung (Tabelle 1). Dies bedeutet für einen Transport von 5 t Flüssigaluminium pro Behälter und einer Fahrzeit von 4 h eine um 48 K reduzierte Abkühlung des flüssigen Aluminiums. Darüber hinaus konnte gezeigt werden, dass von den Umgebungsbedingungen lediglich die durchschnittliche Geschwindigkeit einen signifikanten Einfluss von 1,6 K/(h*t) besitzt. Weiterhin besitzen die Tiegelposition und die Außentemperatur einen Einfluss, der jedoch mit einem Wert von kleiner als 0,1 K/(h*t) eher unbedeutend ist. Signifikante Einflüsse durch weitere Faktoren wie Niederschlag oder Schnee, konnten in den Messungen nicht nachgewiesen werden und wurden daraufhin aus weiteren Betrachtungen ausgeschlossen.
Tabelle 1: Einfluss der Prozess- und Umgebungsfaktoren.
Einfluss | |
Aluminiummasse | 59 % |
Geschwindigkeit | 38 % |
Position des Transportbehälters | 2 % |
Außentemperatur | 1% |
Mit Hilfe der Simulationen konnten die wichtigsten Einflussfaktoren auf die Abkühlung der Aluminiumschmelze während des Flüssigtransportes identifiziert und charakterisiert werden. Diese trugen entscheidend zur Stabilisierung und Vorhersagbarkeit des Flüssigtransportes bei, infolgedessen der Transportradius sukzessive vergrößert werden konnte. Aufbauend darauf wurden durch die Projektpartner verschiedene Verbesserungen im Prozess vorgenommen, wodurch sich die Prozesssicherheit zusätzlich verbesserte und innerhalb kürzester Zeit bedeutsame Energieeinsparungen im Tiegelvorheizprozess von über 15 % realisiert werden konnten.
Bild 2: Visualisierung der Temperaturverluste an Transportbehältern mittels Infrarotthermographie
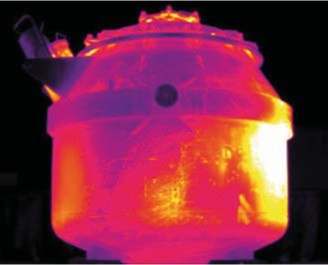
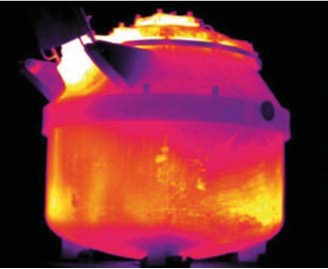
Darüber hinaus weist der Transportbehälter konstruktionsbedingt Schwachstellen in der Isolierung auf. Diese befinden sich im Bereich des Ausgießstutzens, des oberen Impellerdeckels und an den Flanschstellen zur Verschraubung des Deckels und des Impellerdeckels (Bild 2 b) . Durch Simulation des Wärmetransportes von der Schmelze durch die Isolierung und den Behältermantel in die Umgebung konnten die Wärmeverluste einzelner Bereiche des Behälters quantifiziert werden. Dabei wurde berechnet, dass allein über die Bereiche Verschluss, Stutzen und Deckel nahezu 45 % der Wärmeverluste des gesamten Behälters abgeleitet werden (Bild 3), obwohl die Oberfläche dieser Bereiche weniger als 10 % der gesamten Behälteroberfläche entspricht (Bild 3, orangene Balken).
Eine Optimierung der Isolierung der standardisierten Transportbehälter würde die Prozessstabilität zusätzlich verbessern und es ermöglichen, weitere Energieeffizienzpotentiale zu heben. Dazu sind seitens des Kompetenzzentrums Industrielle Energieeffizienz (KIEff) der Hochschule Ansbach weitere Entwicklungsprojekte mit den Herstellern geplant.
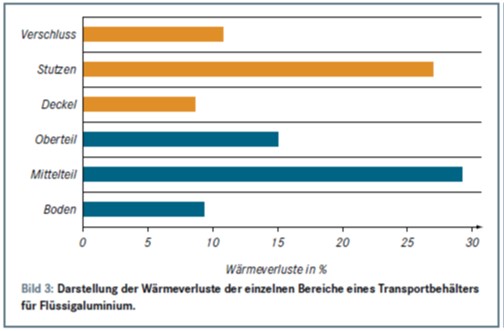
Abwärmenutzung
Der Schmelzbetrieb in Gießereien verursacht große Abwärmemengen, die i. d. R. ungenutzt bleiben. Die Unternehmen suchen vermehrt nach Möglichkeiten, die Abwärmeverluste durch Prozessoptimierung zu minimieren bzw. zu nutzen.
Die Abwärmenutzung aus produktionsrelevanten Vorgängen mittels effizienzsteigernder Prozessverbesserungen erfordert eine hohe Funktionssicherheit, d. h. es darf zu keiner Beeinträchtigung des Produktionsablaufes kommen. Darüber hinaus erfordert die Abwärmenutzung mittels Wärmetauscher aufgrund der im Abgas enthaltenen Stoffe korrosionsbeständige Werkstoffe, welche sehr kostenintensiv sind und setzt eine neu konzipierte Steuerung der Anlagentechnik voraus. Eine Analyse des Abwärmepotentials unter Berücksichtigung moderner Wärmerückgewinnungs-und Schmelzofentechnik zeigte, dass mindestens 24 % der Abgasverluste mittels Wärmerückgewinnung (WRG) bei Gewährleistung geringer Amortisationszeiten nutzbar sind (Bild 4).
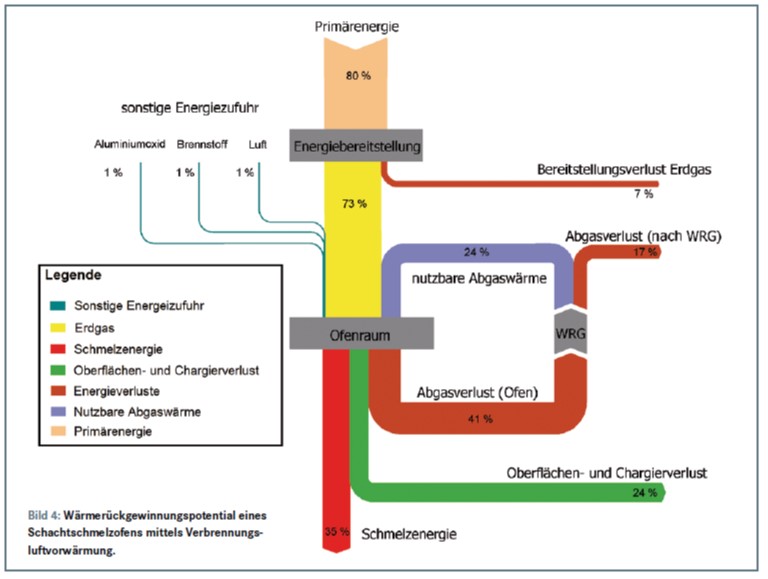
Die weiterführende Analyse des Abwärmestroms eines typischen gasbetriebenen Schachtschmelzofens zeigte, dass während der Produktion große Temperaturschwankungen zwischen 130 °C und 400 °C auftreten. Diese entstehen prozessbedingt durch die verschiedenen Ofenbetriebszustände Schmelz- und Warmhaltetrieb sowie Stillstand. Die Analyse der Abgaswärmeleistungen ergab, dass Spitzenleistungen von nahezu 500 kW je Ofen Mittelwerten von ca. 120 kW je Ofen gegenüberstehen. Für einen mittleren Schmelzbetrieb mit ca. 20 000 MWh Abwärme pro Jahr, können auf einem Temperaturniveau von 90 °C ca. 20 % der Abwärme rückgewonnen werden, welche zur Deckung des Heizbedarfes oder der Prozesswärme verwendet werden können.
Weiterhin wurden die Möglichkeiten der Abwärmenutzung zur Vorwärmung des Schmelzgutes (Masseln, Rücklaufmaterial) unter Berücksichtigung geringer Amortisationszeiten untersucht, dabei wurden erhebliche Potentiale im Rahmen studentischer Abschlussarbeiten prognostiziert. Als Folge dieser Erkenntnisse wurde in Zusammenarbeit mit einem Industriepartner eine Anlage zur Masselvorwärmung konzipiert und angeschafft. Im weiteren Verlauf des Projektes konnte die Effizienzsteigerung infolge dieser Maßnahme verfiziert werden. So ergab sich, dass durch Masselvorwärmung der Schmelznutzungsgrad der Ofenanlage von 29 % um 5 % auf 34 % verbessert werden konnte (Tabelle 2).
Tabelle 2: Einfluss der Aluminiumvorwärmung auf Energieeffizienz.
mit Abwärmenutzung | ohne Abwärmenutzung | |
Spezielle Schmelzenergie (kWhth/t Alu) | 927 | 1072 |
Schmelznutzungsgrad | 0,34 | 0,29 |
Aufbauend auf der Analyse der Schmelzöfen und des Abgaswärmestroms wurde mit den Industriepartnern ein mehrstufiges Konzept zur Erhöhung der Energieeffizienz entwickelt. Das Konzept beinhaltet prozessinterne (z. B. regenerative Abwärmenutzung) und prozessexterne (z. B. Abwärmenutzung zur Heizungsunterstützung) Maßnahmen.
Zusammenfassung
Zur Erzeugung von flüssigem Aluminium in der Gießerei-Industrie sind sowohl das Aufschmelzen von Festmaterial in der Gießerei selbst als auch die Belieferung der Gießereien mit Flüssigaluminium durch die Hütte etablierte Verfahren. In der Hütte entstehen zur Herstellung und Verarbeitung von Aluminium – ob fest oder flüssig – beträchtliche Energiemengen. Bei Verwendung von Flüssigaluminium muss in der Hütte zum Vorheizen der Transportbehälter und in der Gießerei zum Warmhalten der Schmelze zusätzlich Energie aufgewendet werden (Bild 5).
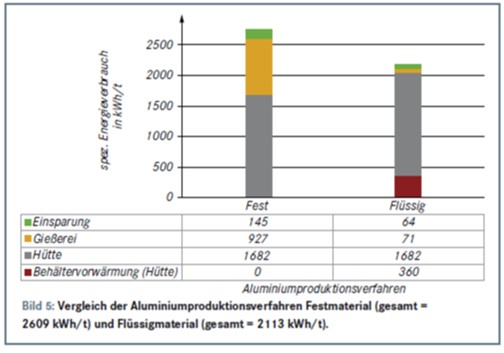
Der Transport von Flüssigaluminium konnte durch intensive Anwendung simulationsgestützter Methoden systematisch analysiert und darauf aufbauend gezielt verbessert werden. In der Folge stellte sich eine deutlich gesteigerte Prozesssicherheit ein. Zudem wurde eine Steigerung der Energieeffizienz im Bereich der Tiegelvorwärmung von über 15 % erreicht.
Beim Bezug von Festmaterial ist in der Gießerei zusätzliche Energie zum Schmelzen der Barren oder Masseln notwendig. Die dabei entstehende Abwärme birgt in den mittelständischen Gießereibetrieben noch immer große Nutzungspotentiale. So können rund 24 % der Prozessabwärme mittels moderner Wärmerückgewinnungstechnologien z. B. zur Brennerluftvorwärmung genutzt werden. Beträchtliche Energiesparpotentiale bestehen aber auch bei der Masselvorwärmung oder bei der Deckung des Heizbedarfes.
Dipl.-Ing. (FH) Ansgar Ringleb, B.Eng. Sven Hirschberg, und Prof. Dr. Wolfgang Schlüter, Kompetenzzentrum Industrielle Energieeffizienz (KIEff), Hochschule für angewandte Wissenschaften Ansbach, Dipl.-Ing. Päd. (TU), Dipl.-Inf. Wirt.(FH) Dietrich Schneider und Prof. Dr. Günther Pröbstle, Hochschule für angewandte Wissenschaften Ansbach, M.Eng. Dipl.-Ing.(FH) Arno Dentel und Prof. Dr.-Ing. Wolfram Stephan, Institut für Energie und Gebäude (ieg), Georg-Simon-Ohm-Hochschule Nürnberg.
Literatur:
[1] Bayerisches Landesamt für Umweltschutz (Hrsg.): Effiziente Energienutzung in Nicht-Eisen-Metall-Schmelzbetrieben, Augsburg, 2005