Gießöfen und Gießeinrichtungen – Stand der Technik und Entwicklungsziele
Teil 2: Gießeinrichtungen
Von Thomas Voss, Marc Onder de Linden und Dietmar Trauzeddel, Simmerath-Lammersdorf
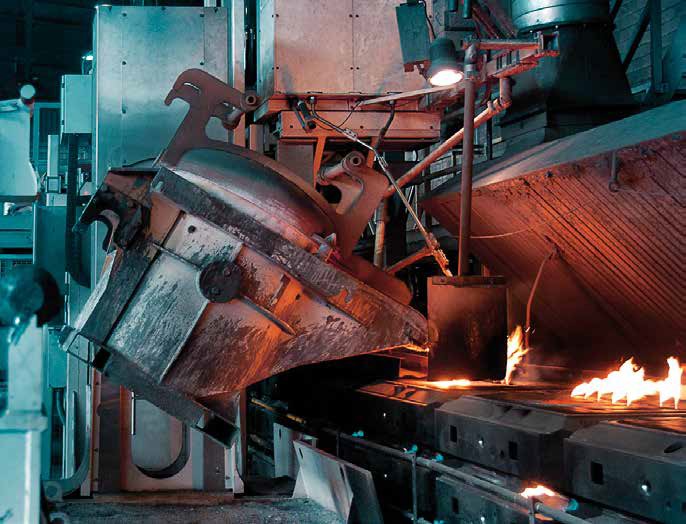
Pfannengießeinrichtung im Einsatz.
Erschienen in GIESSEREI 02/2016
Grundtypen der Gießeinrichtungen
Nach der Art des Gießvorgangs kann in Aggregate mit Stopfenentleerung und in solche mit Entleerung durch Bewegung des Gießgefäßes unterschieden werden. Wie bereits in Teil 1* ausgeführt, kommen Verfahren zur Förderung und Dosierung des flüssigen Metalls mittels elektromagnetischer Kräfte gegenwärtig nicht zum Einsatz.
Die erstgenannte Kategorie kann eingeteilt werden in Stopfengießeinrichtungen, die drucklos und solche, die druckbetätigt arbeiten. Der zweitgenannten Kategorie ist das Gießen durch Kipp- oder durch Drehbewegung des Gefäßes zugeordnet. Auch hinsichtlich der Geometrie der Gießgefäße unterscheiden sich die Aggregate dieser beiden Grundtypen deutlich: Bei den Stopfengießeinrichtungen ohne Druckbeaufschlagung hat das Gießgefäß eine Wannenform (Bild 1). Die druckbetätigte Ausführung ist an die Bauform eines Gießofens angelehnt (Bild 2) und in einigen Fällen auch fast baugleich mit einem Gießofen – allerdings ohne Induktor.
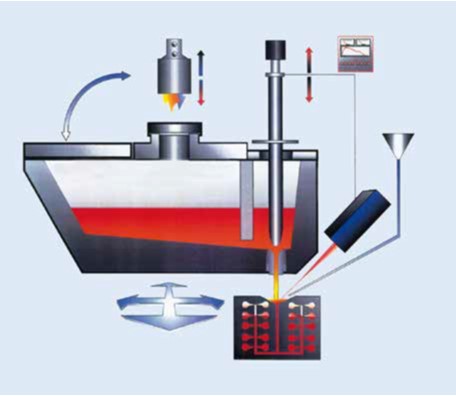
Bild 1: Stopfengießeinrichtung, drucklos.
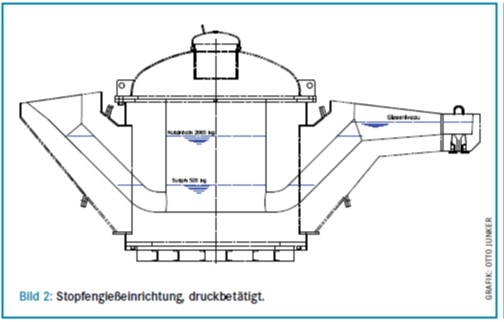
Bild 2: Stopfengießeinrichtung, druckbetätigt.
Bei der zweitgenannten Kategorie war die normale Gießpfanne Ausgangspunkt für die Form des Gießgefäßes. Daher werden diese auch als Pfannengießeinrichtungen bezeichnet (Bild 3). Allerdings wurde die Form in Hinblick auf eine gute Regelbarkeit der Gießleistung in Abhängigkeit vom Kippwinkel der Pfanne optimiert, sodass teilweise Gefäße mit einem fast rechteckigen Querschnitt auf dem Markt sind (Stichwort Segmentbauweise).
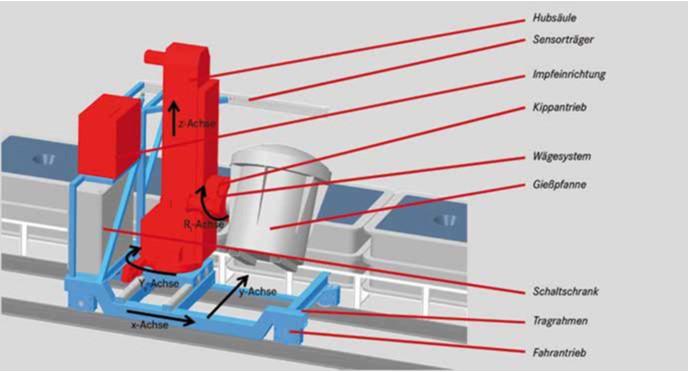
Bild 3: Pfannengießeinrichtung, Prinzipdarstellung der Bauart InduPour (Induga).
Daraus resultiert die grundsätzliche Feststellung, dass bei den Gießeinrichtungen mit Stopfenentleerung die Regelung der Gießleistung durch den Stopfenhub einfach und reproduzierbar ist. Auch die Form des Gießstrahls ist durch den Düsendurchmesser und den Stopfenhub eindeutig definiert. Hinzu kommt, dass der Gießstrahl genau senkrecht in den Eingusstrichter trifft. Dagegen hängt bei den Pfannengießmaschinen die Gießleistung von der Kippgeschwindigkeit der Pfanne ab. Daraus ergibt sich die Konsequenz, dass die Anforderungen an die Automatisierung des Formfüllprozesses bei den Pfannengießmaschinen wesentlich komplexer sind.
Allgemein ist anzumerken, dass die Einstellung der jeweiligen Gießleistung entsprechend der vorgegebenen Gießkurve durch Nachfahren (Teach-in), nach dem Gewicht, der Zeit oder der Erfassung des Niveaus im Eingusstrichter erfolgen kann. Auch eine Kombination ist möglich, z. B. von gespeicherter Gießkurve und Gewicht.
Pfannengießeinrichtungen
Charakterisierung
Bei den Pfannengießeinrichtungen wird das Gefäß über die Gießschnauze soweit gekippt, bis das flüssige Metall in den Einguss der Gießform fließt. Hierbei wird die Gießschnauze kurz oberhalb des Eingusstrichters fixiert und die Pfanne um diesen Punkt gedreht. Dabei ist es wichtig, dass der Drehpunkt so gewählt wird, dass es zu keinem Auswandern der Gießschnauze kommt. Dieser Gießvorgang entspricht dem des Abgießens mit der Hand, allerdings wird der Formfüllprozess je nach Automatisierungsgrad in Bezug auf die Reproduzierbarkeit und Genauigkeit deutlich verbessert.
Der Markt an Pfannengießeinrichtungen unterteilt sich in halbautomatische und vollautomatische Einrichtungen.
Bei den halbautomatischen Einrichtungen regelt der Bediener mittels eines Joysticks die motorisierte Kippbewegung und damit die Gießleistung. Damit ist das Gießergebnis individuell unterschiedlich. Der Gießvorgang wird auch nicht automatisch beendet, sondern erfolgt durch den Bediener. Allerdings verfügen viele halbautomatisierte Systeme über eine Schnittstelle zur Formanlage, sodass die Position des Eingusstrichters selbständig angefahren wird. Auch das Ankippen der Pfanne bis zu dem Niveau, bei dem die Schmelze gießbereit in der Gießschnauze steht, ist bei hochwertigen Systemen automatisiert. Der Pfannenwechsel wird durch den Bediener angefordert und wird bei einigen Systemen automatisch durchgeführt.
Vollautomatische Pfannengießeinrichtungen minimieren die Eingriffe des Bedieners durch die zusätzliche Integration verschiedener Sensorsysteme. Die Sensorik überwacht hauptsächlich das Niveau der Schmelze im Eingusstrichter und das Gewicht der Pfanne und damit die Gießleistung und das Abgussgewicht.
Der automatisierte Gießvorgang wird heutzutage sehr unterschiedlich eingestellt, einfachere Einrichtungen füllen gesteuert den Trichter mittels eines Teachin-Verfahrens. Das Ende des Gießvorgangs wird vorwiegend über die integrierte Waage geregelt. Moderne Gießeinrichtungen überwachen das Trichterniveau mittels eines Kamera- oder Lasersystems. Dieser Messwert wird in einem Regelalgorithmus verarbeitet, und durch Veränderung der Gießleistung wird das vordefinierte Niveau eingehalten. Die Qualität der Automation zeigt sich in der Dynamik der Niveauregelung des Trichters und in der Gießgewichtsgenauigkeit. Dabei ist die Rückverfolgbarkeit des Prozesses sichergestellt, da moderne Pfannengießmaschinen alle relevanten Prozessparameter, u. a. Gießgewicht, Gießzeit, Impfzeit, Impfmenge, Gießtemperatur, Pfannennummer, Art des Gießprozesses (automatisch, manuell) etc., dokumentieren.
Bautypen und -größen
Die Temperaturverluste in den unbeheizten Pfannen grenzen in Bezug auf die vertretbare Temperaturtoleranz die Chargendauer und damit die maximale Baugröße der angebotenen Pfannengießeinrichtungen ein. Wie Tabelle 1 zeigt, resultiert hieraus, dass Pfannengießeinrichtungen mit einem Fassungsvermögen bis max. 3,2 t angeboten werden. Es gibt aber auch eine Vielzahl von Ausführungen mit einem wesentlich kleineren Fassungsvermögen, teilweise enden die verschiedenen Baugrößen einzelner Anbieter bei maximal 1,2 bzw. 1,3 t (Sinto, Ziheng). Da es sich bei den aufgeführten Herstellern vorwiegend um Lieferanten von Formanlagen handelt, könnte hier ein Zusammenhang mit der Art der angebotenen Formanlagen bestehen. Dabei ist noch anzumerken, dass die Anlagen teilweise so ausgelegt sind, dass mit verschiedenen Pfannengrößen gearbeitet werden kann.
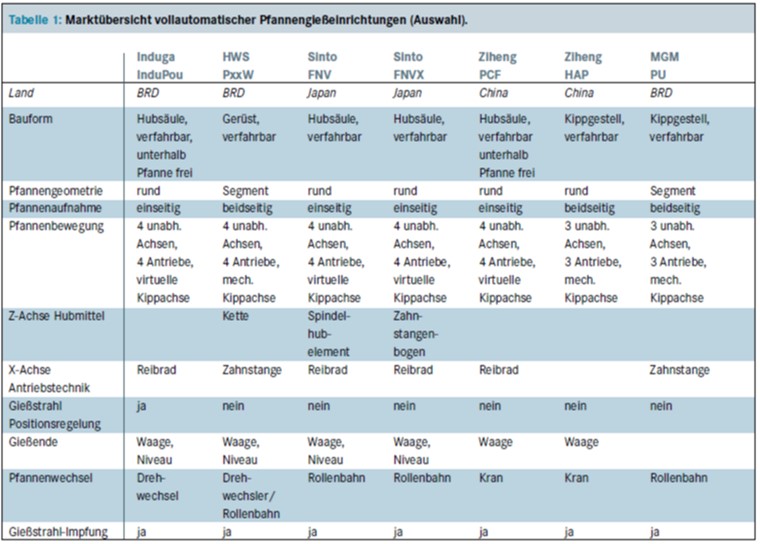
Hinsichtlich der Form der Pfanne überwiegt die Ausführung mit einem kreisförmigen Querschnitt, nur in zwei Fällen (HWS und MGM) kommen rechteckige Formen zum Einsatz. Letztere Variante, auch als Segmentbauweise bezeichnet, soll, wie bereits oben erwähnt, dafür sorgen, dass sich die Gießleistung proportional mit dem Kippwinkel ändert [1]. Dies wird bei Gießeinrichtungen mit zylindrischem Pfannenkörper über die Maschinensteuerung realisiert.
Der Ausguss ist häufig als Siphon ausgeführt, um ein schlackenfreies Gießen zu ermöglichen.
Der erforderliche Pfannenwechsel wird mittels Rollenbahn oder mit Hilfe eines Drehwechselsystems vorgenommen. Der Pfannentransport zur Aufnahmeposition der Gießeinrichtung erfolgt per Kran oder Stapler.
Die Pfannengießeinrichtungen können längs der Formline verfahren werden.
Generell gilt es, die Pfannenwechselzeit so kurz wie möglich zu halten, um die Anzahl nichtabgegossener Formen zu minimieren, da die Formanlage nicht angehalten wird. Die Pfannengießeinrichtung fährt mit der frisch gefüllten Pfanne entlang der Formlinie soweit nach vorn, dass die nichtabgegossenen Formen nacheinander abgegossen werden können. Dies setzt allerdings voraus, dass die Gießzeit kürzer als die Taktzeit ist und genügend Zeit bleibt, um nicht nur alle nichtabgegossenen Formen abzugießen, sondern auch in dem normalen Taktbetrieb arbeiten zu können. Das wird dann zu einem Problem, wenn sich Gießzeit und Taktzeit nicht wesentlich unterscheiden. Im Extremfall besteht die Lösung im Einsatz zweier parallel arbeitender Pfannengießeinrichtungen, wodurch der Pfannenwechsel komplett kompensiert werden kann.
Die Neuentwicklung von Induga (Indu- Pour) setzt vor allem auf eine vollständige Automation des gesamten Gießprozesses und eine ausgefeilte Maschinentechnik. Ein Novum ist die dreidimensionale Gießstrahlpositionsregelung. Dabei kann in Bezug auf die Niveauerfassung im Eingusstrichter auf die weitreichende Erfahrung beim Regeln des Gießprozesses mit einem kamerabasierenden System an einem Gießofen zurückgegriffen werden. Zusätzlich ist die Optimierung der Wägetechnik und der damit verbundenen Gießgewichtsgenauigkeit von Bedeutung. Hierbei werden neuartige Systeme mit höchster Genauigkeit eingesetzt. Eine Neuheit ist, dass in dem Gießgefäß auf der Basis der induktiv beheizten Pfannentechnik des Unternehmens Induladle ein Temperaturverlust des flüssigen Metalls vermieden und unter Umständen auch eine Temperaturerhöhung vorgenommen werden kann. Damit kann z. B. bei einem Stillstand der Formanlage der Pfanneninhalt auf einem separaten Heizstand auf Gießtemperatur gehalten bzw. erwärmt werden und muss nicht vermasselt oder in den Schmelzofen zurückgeführt werden.
Stopfengießeinrichtungen
Stopfengießeinrichtungen, drucklos
Anhand der automatisch dosierenden Stopfengießeinrichtung Bauart Otto Junker (siehe Bild 1) soll das Grundprinzip dieser Bauart erläutert werden:
Die Einrichtung besteht aus einem wannenförmigen Gefäß, welches mit einer keramischen Gießmasse ausgekleidet ist und ein Nutzfassungsvermögen von 0,5 bis 3,0 t hat. Die Abdeckung mit keramisch zugestellten Deckelsegmenten reduziert die Abstrahlverluste deutlich. Der Deckel besitzt eine Öffnung zum Befüllen und Reinigen sowie eine Vorrichtung für die Aufnahme eines Gasbrenners zum Aufheizen des Gefäßes. Im vorderen Teil der Wanne befindet sich die Gießkammer, die mit einer am Boden offenen Wand von der Hauptkammer abgetrennt ist. Über einen Düsenstein im Boden der Gießkammer wird mittels einer Stopfeneinrichtung der Formkasten gefüllt. Ein Düsenreinigungssystem sorgt dafür, dass mögliche Ansätze an der Düse entfernt werden können.
Die Anlage ist genau wie ein Gießofen in zwei Richtungen verfahrbar und dann zum Dosieren mit einer automatischen Gießleistungsregelung (Kamera oder Laser) ausgerüstet werden.
Der Wärmeverlust in der Gießeinrichtung bewegt sich aufgrund der sehr guten Isolierung und der gewählten Konstruktion auf einem sehr niedrigen Niveau – er ist aber grundsätzlich nicht vermeidbar. Somit sinkt die Temperatur des flüssigen Eisens ab, sodass zur Einhaltung hoher Qualitätsanforderungen und weitgehend gleicher Gießparameter das Abgießen der im Gefäß gespeicherten Eisenmenge nach 15-20 min beendet sein sollte und ein erneutes Befüllen erfolgen muss. Allerdings kann das Befüllen mit frischem Eisen auch während des laufenden Abgießprozesses vorgenommen werden. Davon ausgehend hat sich für die überschlägige Auslegung die Faustformel ergeben, dass das Nutzfassungsvermögen einer unbeheizten Gießeinrichtung ein Viertel des stündlichen Flüssigeisendurchsatzes betragen soll. Bild 4 zeigt eine derartige Gießeinrichtung mit einem Fassungsvermögen von 2,0 t mit Stopfeneinrichtung und Gasbrenner zum Aufheizen.
Stopfengießeinrichtungen, druckbetätigt
Diese Bauart unterscheidet sich bis auf die fehlende Beheizung nur unwesentlich von den Induktionsgießöfen, sodass hier nur auf die Unterschiede eingegangen wird. Ist die Bauart fast identisch, hat das den Vorteil, dass ein Nachrüsten mit einem Induktor ohne große Umbauarbeiten erfolgen kann, wie es bei der Ausführung aus dem Hause Otto Junker der Fall ist. Andere Hersteller [2] sehen den Vorteil in einem günstigen Verhältnis von Gesamt- zu Nutzfassungsvermögen und haben sich daher für eine flachere Bauform entschieden, bei der die Siphonmündungen nur in einer Rinne im Boden enden. Dies erleichtert den Legierungswechsel, da die Sumpfmenge relativ klein ist. Auch die Reinigung der Siphons ist einfacher durchzuführen. Allerdings entfällt dafür die Möglichkeit einer späteren Induktornachrüstung.
Zu erwähnen ist noch, dass die in Teil 1 des Beitrages erwähnte Schnellwechseleinrichtung für Gießöfen von Otto Junker auch für die unbeheizte Stopfengießeinrichtung eingesetzt werden kann.
Aufgrund des geringeren Temperaturverlustes im Vergleich zu den anderen Gießeinrichtungen ist eine längere Chargendauer möglich. Demzufolge kann damit auch das Fassungsvermögen der Einrichtungen erhöht werden – es liegt im Bereich von 2,4-7,0 t [3] (Bild 5) bzw. 1,5- 5,5 t [4].
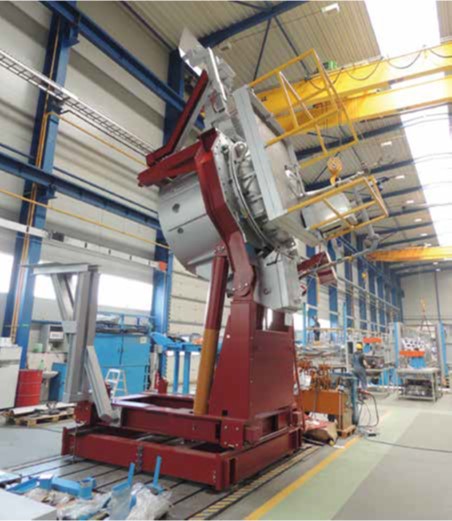
Bild 5: Druckbetätigte Stopfengießeinrichtung, Fassungsvermögen 2,4 t bei der Werksmontage.
Vergleich der verschiedenen Gießeinrichtungen
Anhand wichtiger technischer Merkmale (Tabelle 2) sollen eine Bewertung der einzelnen Gießeinrichtungstypen erfolgen und die Einsatzkriterien erläutert werden. Teilweise wurde dabei eine eigene Bewertung vorgenommen, da nicht in jedem Fall Werte bzw. Angaben vorlagen.
Tabelle 2: Bewertung der verschiedenen Gießeinrichtungen.
Gießeinrichtung | ||||
Pfannengießeinrichtungen | Stopfengießeinrichtungen druckbetätigt | drucklos | |||
Fassungsvermögen in t | 0,6-3,2 | 2,4-7,0** 1,5-5,5 t* | 0,5-3,0 t ** | |
Chargendauer in min | 5-10 | 30 | 15-20 | |
Temperaturverlust in °C/min | 5-10 | 1-1,5 * | 2,5 ** | |
Temperaturgenauigkeit in K | 25-50 | 30-45 | 25-50 | |
Gießleistung in kg/s | 2-20 | 1-40 | 1-40 | |
Legierungswechsel in min | 1 | 15-20 | 10-15 | |
Gefäßwechsel | 1 min | 2-4 h | 20-30 min | |
Gleichzeitiges Befüllen und Abgießen | nein | ja | ja | |
Einsatz als Zwischenspeicher | nein | begrenzt | nein | |
Automatisches Dosieren und Abgießen | ja | ja | ja | |
Schlackenfreies Abgießen | ja | ja | ja | |
Speicherung von Mg-behandeltem Gusseisen | nein | ja | nein | |
Einsatzkriterien Formanlagen | ||||
Abgussgewicht | klein bis mittel | mittel bis groß | mittel | |
Taktzeiten | lang bis mittel | kurz bis mittel | mittel |
*ABP, **Otto Junker
Die Pfannengießeinrichtungen sind durch den schnellen und einfachen Legierungswechsel sowie die hohe Anwendungsflexibilität charakterisiert, dagegen steht die Tatsache, dass jeder Pfannenwechsel Zeit kostet und einige Formen während der Wechselzeit nicht abgegossen werden können. Der höhere Temperaturverlust erfordert einen schnellen Pfannenwechsel und damit auch ein kleineres Fassungsvermögen der Gefäße.
Zudem muss festgestellt werden, dass das automatische Abgießen und Dosieren bei den Pfannengießeinrichtungen ein doch aufwendiges Sensor- und Regelsystem bedingt. Zweifellos besteht ein Vorteil darin, dass im Gießgefäß vor dem Einschleusen in die Gießeinrichtung auch metallurgische Maßnahmen wie das Impfen oder eine Mg-Behandlung vorgenommen werden können. In diesen Fällen ist die Behandlungspfanne gleichzeitig auch die Gießpfanne. Damit entfällt das mit einem Temperaturverlust verbundene Umfüllen der Schmelze, und unter Umständen kann statt der Gießstrahlimpfung mit einer Pfannenimpfung gearbeitet werden.
Bei kleineren bis mittleren Abgussgewichten und längeren Taktzeiten stellen Pfannengießeinrichtungen eine gute Alternative dar. Bei sehr kurzen Taktzeiten und damit Hochleistungsformanlagen kann durch die Installation von zwei Pfannengießeinrichtungen eine Lösung erreicht werden.
Vorteilhaft ist auch die Tatsache, dass teilweise in einer derartigen Gießeinrichtung unterschiedliche Pfannengrößen zum Einsatz kommen können.
Für die druckbetätigten Stopfengießeinrichtungen sprechen der niedrige Temperaturverlust, das gleichzeitige Befüllen und Abgießen, die gute Automatisierung sowie die längere Chargendauer. Nachteilig ist, dass ein Legierungswechsel zeitaufwendig ist. Druckbetätigte Stopfengießeinrichtungen sind prädestiniert für den Einsatz an Hochleistungsformanlagen mit kurzen Taktzeiten sowie mittleren bis großen Abgussgewichten. Die drucklos arbeitenden Stopfengießeinrichtungen unterscheiden sich von den druckbetätigten darin, dass das Niveau des flüssigen Metalls mit zunehmenden Abgüssen sinkt und damit auch der metallostatische Druck. Zur Gewährleistung konstanter Gießparameter sind daher eine exakte Erfassung des Niveaus im Eingusstrichter und eine feinfühlige und zeitgerechte Regelung der Gießleistung notwendig, um die wechselnden Druckverhältnisse auszugleichen.
Fazit
Die verschiedenen Grundtypen und Bauformen der Gießeinrichtungen stellen eine gute Ergänzung zu den Gießöfen dar und sind in bestimmten Einsatzfällen eine gute Alternative. Das Entwicklungspotenzial liegt in der Verbesserung der Automatisierung des Gießvorgangs sowie in der der Optimierung des Gesamtfertigungsprozesses und damit auch in der Online-Kopplung zu dem Schmelz- und Formprozess.
Dipl.-Ing. Thomas Voss und Dipl.-Ing. Marc Onder de Linden, Induga GmbH & Co.KG, Simmerath-Lammersdorf, Dr.-Ing. Dietmar Trauzeddel, Otto Junker GmbH, Simmerath-Lammersdorf
Literatur:
[1] Heinrich Wagner Sinto Maschinenfabrik GmbH. Prospekt Gießautomaten, Gießmaschinen.
[2] Dötsch, E.: Induktives Schmelzen und Warmhalten. 2. Aufl., Vulkan-Verlag, 2013.
[3] ABP Induction Systems GmbH. Prospekt Druckgasbetätigte, unbeheizte Gießeinrichtung Pouromat Typ OCU.
[4] Otto Junker GmbH. Prospekt UGD.