Kaltwind-Kupolofen
Der Kaltwind-Kupolofen hat nach Literaturangaben einen Koksverbrauch von ungefähr 130 bis 150 kg/t Flüssigeisen.
Unter der Annahme eines Heizwertes von 8,5 kWh/kg, Europäische Kohle, gelangt man zu einem Energieeinsatz von 1105 bis 1275 kWh/t Flüssigeisen.
Der Koksbedarf zum Schmelzen von 1000 kg Eisen im Kaltwind-Kupolofen, dessen Innendurchmesser größer als 750 mm ist, wird nach [7] wie nachfolgend dargestellt angegeben.
Tabelle 1: Koksbedarf zum Schmelzen von 1000 kg Flüssigeisen in einem Kaltwind-Kupolofen
Abstichtemperatur [°C] | Koksbedarf [kg/t Flüssgeisen] |
1.400 | 95 |
1.426 | 110 |
1.454 | 125 |
1.482 | 140 |
1.510 | 155 |
1.538 | 170 |
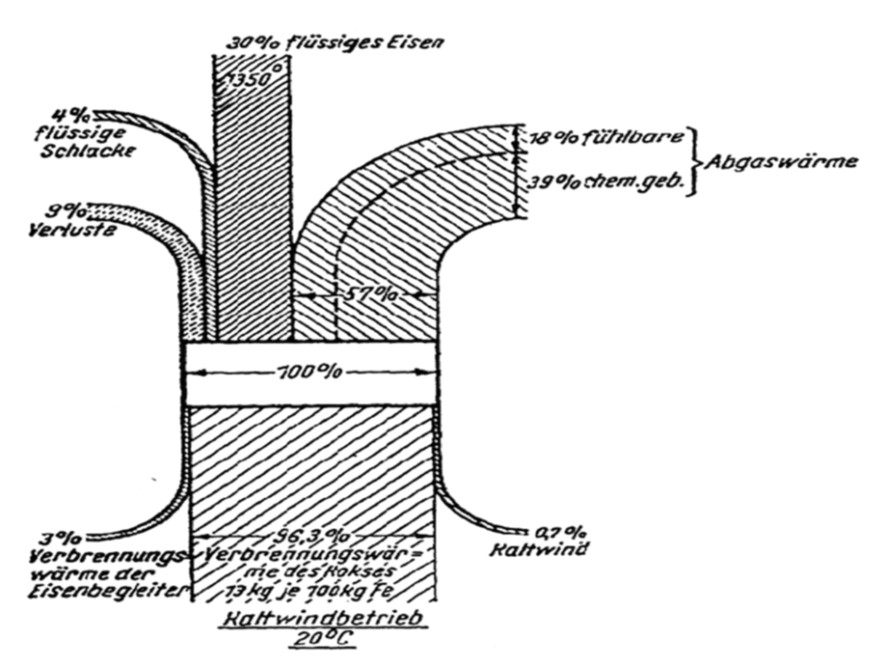
Nach [2] wird die an das Eisen abgegebene Nutzwärme auf 30 % bis 40 % beziffert. Die Wärmeverluste, die sich durch die Verbrennungsgase (1/3 durch fühlbare Wärme; 2/3 durch latente Wärme in Form von CO) ergeben, werden auf 45 % bis 55 % beziffert.
Sonstige Wärmeverluste ergeben sich durch die Ofenwand und die Schlacke und belaufen sich nach [2] auf 10 % bis 20 %. Der Energienutzungsgrad kann nach [2] bis auf 50 % bis 60 % gesteigert werden, wenn der Satzkoks gesenkt wird, die Chargenvorwärmung im Ofenschacht sehr wirksam ist (ausreichend bemessene Schachthöhe oder Erweiterung des Ofendurchmessers oberhalb der Schmelzzone), kein Stahlschrott eingesetzt und der Kupolofen gut geregelt wird, zum Beispiel auf eine Rinnentemperatur von nicht mehr als 1400 °C, wenn große Gussstücke gegossen werden sollen.
Beim klassischen Kaltwind-Kupolofen ist die Überhitzung nur schwer unter Inkaufnahme eines deutlichen Abfalls des Wärmewirkungsgrades zu erreichen. Aus Abbildung 4 geht hervor, dass für die Überhitzung von 1400 °C auf 1500 °C ein Abfall der Energienutzung auf unter 30 % zu verzeichnen ist.
Die Aussage mit einem möglichst geringen Koksverbrauch auskommen zu wollen muss jedoch im Hinblick auf die Wirtschaftlichkeit relativiert werden. Wird die in den Kupolofen eingebrachte Energie in Form von Koks über ein bestimmtes Maß gesenkt, ist zu bedenken, dass sich der Ofen die notwendige Energie aus den Begleitelementen holt.
1 Verfahrensmodifikationen beim Kaltwind- Kupolofen
1.1 Zugabe von Sekundärwind
Ein Kaltwind-Kupolofen ohne Sekundärwind-Einrichtung gilt heute als veraltet und stellt nicht mehr den Stand der Technik dar.
Die thermische Effizienz kann beim Kaltwind-Kupolofen durch den Einbau einer zweiten Düsenreihe gesteigert werden. Durch das Einblasen von Sekundärwind kann das Kohlenmonoxid, das durch die endotherme Reduktion von CO2 durch Kohlenstoff (Koks) entstanden ist, oxidiert werden.
Die Wärme, die durch Verbrennung des Kohlenmonoxids frei wird, kann direkt von den Bestandteilen der Gattierung aufgenommen werden.
Die Zugabe von Sekundärwind verbessert die Brennstoffausnutzung und vermindert den erforderlichen Kokssatz. Der Koksverbrauch wird mit 105 bis 125 kg/t Flüssigeisen durch die Zugabe von Sekundärwind angegeben.
Unter der Annahmen eines Heizwert europäischer Kohle von 8,5 kWh/kg beträgt der Energiebedarf 893 kWh/t bis 1063 kWh/t.
Ein Kupolofen mit Sekundärwindbetrieb ist mit zwei Düsenreihen ausgestattet. Im Vergleich zu einem herkömmlichen Kupolofen mit nur einer Blasformreihe ermöglicht der Kupolofen mit Sekundärwindbetrieb:
- eine höhere Abstichtemperatur und eine größere Kohlenstoffaufnahme bei einem gegebenen Koksverbrauch
- eine Reduktion des Koksverbrauches und, wenn erforderlich, eine Erhöhung der Schmelzrate unter Beibehaltung einer bestimmten Abstichtemperatur
- eine gezielte Einstellung einer Verbrennungszone in der das gebildete Kohlenmonoxid gezielt nach verbrannt wird, wobei eine erhebliche Wärmemenge frei wird.
Um einen optimalen Nutzen aus dem Betrieb mit Sekundärwind zu ziehen, sollte die Teilung 25 % - 50 % oben und 75 % - 50 % unten betragen. Die beiden Reihen sollten bei Kaltwind etwa 1 m und bei Heißwind etwa 0,5 m auseinander liegen.
Unter der Annahme, dass eine Reduzierung des Koksgehaltes eine Erhöhung der Energie-nutzung verspricht, verbessert sich die Energienutzung im Falle des Sekundärwind-Betrieb, gleiche Eisentemperatur vorausgesetzt, um ca. 30 %.
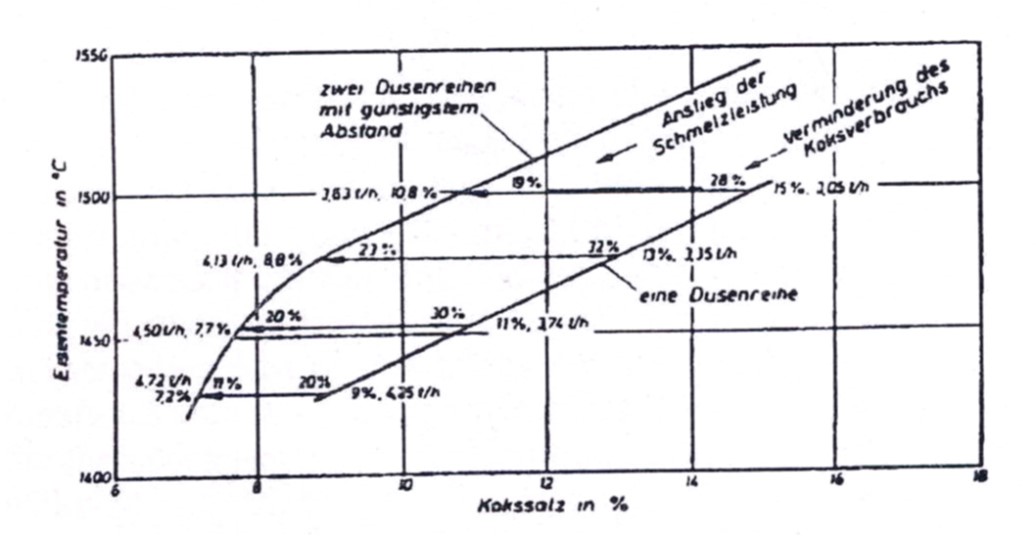
1.2 Anreicherung des Windes mit Sauerstoff
Die Anreicherung des Windes mit Sauerstoff ist Stand der Technik, wodurch die thermische Effizienz des Kaltwind-Kupolofens verbessert wird. Durch die Anreicherung des Windes mit Sauerstoff lassen sich höhere Verbrennungstemperaturen erzielen, die eine verbesserte Nutzung der angebotenen Energien bewirken.
Bei optimaler Ofenauslegung und abgestimmter Sauerstoff-Zugabe lassen sich im Dauerbetrieb Abstichtemperaturen von 1520 °C bis 1550 °C erreichen.
Die kontinuierliche Anreicherung des Windes mit Sauerstoff realisiert nachfolgend genannte Verbesserungen:
- höhere Metalltemperatur, höhere Kohlenstoffaufnahme und geringerer Siliziumschmelzverlust bei gleichen Koksverbrauch
- geringerer Koksverbrauch bei einer gegebenen Metalltemperatur ohne Anstieg der Kohlenstoffaufnahme oder Reduktion des Siliziumschmelzverlustes oder
- höhere Ausbringung eines bestehenden Kupolofens als Ergebnis einer gesteigerten Schmelzrate
Ein weiterer Vorteil liegt in der Möglichkeit gewisse Unregelmäßigkeiten, die mit der Herkunft und Beschaffenheit des verwendeten Gießereikokses zusammenhängen, auszugleichen. Diese Unregelmäßigkeiten können trotz der großen Sorgfalt, mit der auch der Gießereispezialkoks, wie beispielsweise BR6, hergestellt wird, durchaus vorkommen.
Wird im Durchschnitt für eine Tonne Eisen 10 m³ Sauerstoff zugesetzt, dessen Primärenergie rd. 12 MJ/m³ beträgt, so werden dadurch 20 kg Koks mit einem Heizwert von rd. 30 MJ/kg eingespart. Unter Berücksichtigung nachfolgender Gleichung beläuft sich der Gewinn auf 20kg * 30MJ/kg – 10m³ * 12MJ/m³ = 480 MJ/t Eisen.
Günstig ist die Zufuhr von Sauerstoff, wenn er kurzfristig und zeitweise zugegeben wird, d.h. nach prozessbedingten Veränderungen wie beispielsweise in der Anfahrperiode und nach Ofenstillständen.
Die Methode, mit der Sauerstoff in den Ofen eingebracht wird, hat Einfluss auf die Abstichtemperatur.
Tabelle 2: Erhöhung der Eisentemperaturen im Vergleich zu normalen Kaltwindöfen durch verschiedene Arten der Sauerstoffzuführung
Art der Sauerstoffzufuhr | Temperaturveränderung |
Anreicherung im Gebläsewind | + 15 K |
Einbringen in die Düsen | + 40 K |
Einbringen in den Herd des Ofens | |
230 mm unter den Düsen | + 50 K |
610 mm unter den Düsen | + 85 K |
951 mm unter den Düsen | + 85 K |
In Abhängigkeit des Sauerstoffeinbringens in den Ofen kann die Eisentemperatur gegenüber dem Normalbetrieb um 15 °C bis 85° C erhöht werden.
Das Schmelzen mit erhöhtem Sauerstoffanteil bewirkt nicht nur eine verbesserte Energienutzung des Kupolofen-Betriebes, sondern eröffnet auch beim Heißwindbetrieb eine deutliche Erweiterung des optimalen Bereichs der Schmelzleistung.
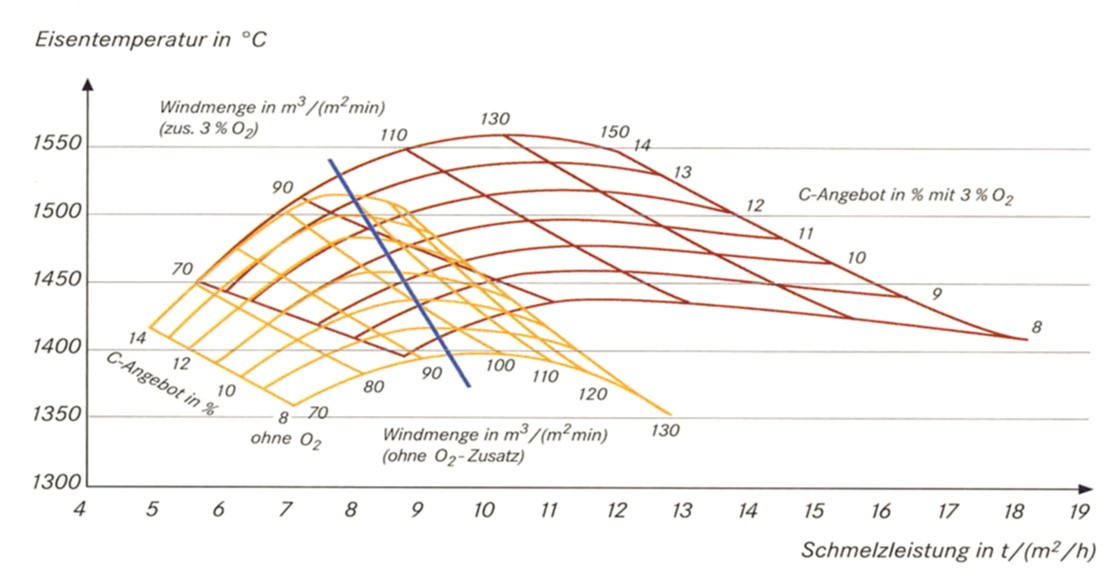
Abbildung 4 zeigt, wie sich für 3 % Sauerstoffzusatz das schmelztechnische Optimum sowohl zu höherer Temperatur als auch zu einer höheren Schmelzleistung verschiebt.
Bei einem gegebenen Kohlenstoffangebot steigt die Eisentemperatur mit zunehmender Windmenge an, bis sie ein Maximum erreicht und wieder abfällt, Abbildung 10. Maximale Eisentemperatur bedeutet eine maximale Löslichkeit von Kohlenstoff im Eisen und gemäß dem Boudouardschen Gleichgewicht ein maximales Reduktionspotential, was zu minimalen Abbränden führt.
Dies kennzeichnet das Optimum des Ofens. Falls der Kupolofen allein mit Wind betrieben wird (gelbes Netz) bewirkt schon eine geringe Veränderung der Windmenge ein starkes Abfallen der Eisentemperatur.
Bei Zusatz von 3 % Sauerstoff zum Ofenwind (rotes Netz) ist der Verlauf der Eisentemperatur im Bereich des Maximums flacher. Bei Variation der Windmenge weicht die Eisentemperatur nicht wesentlich vom Maximum ab, so dass der Ofen über einen großen Schmelzleistungsbereich wirtschaftlich arbeitet.
Durch den Sauerstoffeinsatz steigt, neben der erreichbaren Schmelzleistung des Ofens, auch die maximale Schmelztemperatur, was zu Einsparungen bei Koks und Legierungselementen führt.
1.3 Sauerstoff-Direktinjektion
Zur Leistungssteigerung von Kaltwind-Kupolöfen gelten als Stand der Technik die Verfahren der Anreicherung des Windes mit Sauerstoff und die Sauerstoff-Direktinjektion. Bei der Sauerstoff-Direktinjektion ist es wichtig, dass der technische Sauerstoff weit in das Koksbett eindringt und die Mitte des Schmelzofens erreicht. Dadurch wird der ganze Schmelzofenquerschnitt genutzt und eine hohe Effektivität und Wirtschaftlichkeit des Schmelzprozesses erreicht.
Air Liquide berichtet in [28] über das ALJET™-CSI System, bei dem technischer Sauerstoff über Laval-Düsen auf Überschallgeschwindigkeit beschleunigt und in das Koksbett von Kalt- oder Heißwind-Kupolofen eingebracht wird.
Aufgrund der durch die Überschallgeschwindigkeit verbundenen möglichen hohen Eindringtiefe in das Koksbett wird der Sauerstoff gut genutzt was zu einer Erhöhung von Schmelzleistung und Flexibilität, einer Verkürzung der Anfahrphase und einer Einsparung von Koks und Legierungselementen führt.
Tabelle 3: Betriebsergebnisse des Gleichdruckgeregelten Aljet CSIVerfahrens
Ursprünglicher Betriebszustand | ALJETTM-System | |
Windmenge (prim./sek.) in m3/h | 6.700 / 600 | 6.700 / 600 |
Schmelzleistung in tEisen/h | 11,5 | 14 |
Koksverbrauch in kg/tEisen | 120 | 115 |
Sauerstoffverbrauch in m3/ tEisen | 35 | 29 |
Tabelle 2 zeigt einen Vergleich zwischen den Ergebnissen, resultierend aus den Ergebnissen des Gleichdruckgeregelten ALJET™-CSI System und den Werten im ursprünglichen Betriebszustand.
Bei ansonsten gleichbleibenden Bedingungen stieg die Schmelzleistung von 11,5 tEisen/h auf 14,0 tEisen /h. Der Koksverbrauch konnte von 120 kg/tEisen auf 115 kg/ tEisen reduziert werden. Ebenfalls konnte der Sauerstoffverbrauch von 35 m³/ tEisen auf 29 m³/ tEisen gesenkt werden.
1.4 Abhängigkeit der thermischen Effizienz von der Ofenschachthöhe
Die thermische Effizienz eines Kaltwind-Kupolofens kann durch Erhöhung der Schachthöhe verbessert werden. Im Allgemeinen gilt nach Aussage von [30]: Je höher der Ofenschacht, desto länger bleiben die Verbrennungsgase in Kontakt mit der Beschickung und desto mehr Wärme kann an die Beschickung abgegeben werden. Die optimale Schachthöhe folgt im Allgemeinen der Faustformel:
„Höhe = 5 mal Durchmesser auf Höhe der Blasform“
Nachfolgend dargestellt sind Beispieldaten für veränderten Koksverbrauch durch Vergrößerung der Schachthöhe:
Tabelle 3: Beispieldaten für veränderten Koksverbrauch durch Vergrößerung der Schachthöhe
Kupolofen vor dem Umbau | Kupolofen nach dem Umbau | |
Durchmesser | - | - |
Schmelzzone | 1,4 | 1,4 |
Obere Zone | 1,4 | 1,7 |
Höhe über Blasform [m] | 5 | 6,5 |
Koksmenge [kg/t] | 140 | 115 |
Ratsam ist, die Optimierung der Ofenhöhe während der Planungsphase vorzunehmen. Ansonsten erfolgt eine Vergrößerung der Schachthöhe normalerweise nur bei wesentlichen Umbaumaßnahmen am Ofen.
Die Motivation für die Implementierung der Modifikation der Schachthöhe liegt nach [30] in der Steigerung der Effizienz des Ofenbetriebes.
Quellen:
[2] Ernst Brunhuber; Gießerei-Praxis; Energiecharakteristik und Senkung des spezifischen Energieverbrauches in der Gießerei_ Fachverlag Schiele und Schön GmbH_ März 1978
[20] St. Hasse; Merkmale, Wirtschaftlichkeit und Entwicklungstendenzen des Kupol- und Induktionsprozesses in Eisengießereien; Gießerei-Rundschau; 1991; 11/12 November/Dezember
[30] Merkblatt über Beste Verfügbare Techniken in der Gießereiindustrie; Umweltbundesamt; Juli 2004