Nutzung von Kupolofenabwärme zur Trocknung von Wasserlack und Einleitung ins Fernwärmenetz
Bezug zum BREF Gießerei, Ausgabe Mai 2005
In Kapitel 4.5.2.2 wird die Nachverbrennung von Abgasen von Heißwindkupolöfen und in Kapitel 4.7.3 die Nutzung der Abwärme eines Heißwindkupolofens unter Verwendung von Thermalöl zur Kerntrocknung dargestellt.
Zur Steigerung des Umweltschutzes in einer Gießerei stellt die Abwärmenutzung eines Heißwindkupolofens zur Wasserlacktrocknung eine neue Anwendungsmaßnahme dar.
Beschreibung
Die Erhöhung des thermischen Wirkungsgrades beim Kupolofen selbst ist begrenzt, da in den letzten Jahren vielen Möglichkeiten zur Optimierung ausgeschöpft wurden. So werden bereits heute schon viele Kupolöfen in der Nähe des verfahrenstechnischen Optimums betrieben.
Weitere Verbesserungen sind vor allem dadurch zu erzielen, dass eine kontinuierliche Fahrweise ermöglicht wird und Betriebszustände vermieden werden, welche eine Reserve an Schmelzkoks erfordern. Potenzial ergibt sich daher aus Nutzung der abgeführten Wärme.
Technische Beschreibung
Im Beispiel wird eine Tauch- und Spritzgrundieranlage wird unter Einsatz/Verwendung von Wasserlack betrieben. Die Grundieranlage verfügt über 4 Tauchbecken, 2 Spritzstände und einen Trocknungstunnel, der sich in eine Abdunstzone mit einer Kapazität von 13 Fördertraversen bei einer Umlufttemperatur von ca. 50°C und einem eigentlichen Trocknungsbereich mit einer Kapazität von 46 Fördertraversen bei einer Umlufttemperatur von ca. 140°C unterteilt.
Die Durchlaufzeit durch den Trocknungstunnel beträgt 1 Stunde. Im Anschluss daran erfolgt die Kühlung der Teile in einem entsprechenden Tunnel durch Frischluftzufuhr von außen bei einer Durchlaufzeit von 40 Minuten.
Gegenüber der ehemaligen Lackieranlage, die mit lösemittelhaltigen Lacksystemen arbeitete, entstand jedoch durch die Einführung der vorstehend beschriebenen Wasserlacksysteme ein zusätzlicher nicht unerheblicher Energiebedarf zur Lacktrocknung.
Der gesamte Trocknungsbereich wurde mit fünf Erdgasgebläsebrennern und einer installierten Leistung von 2.250 KW ausgelegt.
- Nutzung der Abwärme des Kupolofens zur Wasserlacktrocknung: Am Kupolofen wurde in 2009 eine Thermalöl-Wärmerückgewinnungsanlage installiert, mit der die im Gichtgas der Kupolofen-Schmelzanlage enthaltene Abwärme genutzt werden kann.
- Zur Nutzung dieser Abwärme wurde ein Sekundärkreislauf (= Nutzkreislauf), welcher am oberen Ende des Nulldruck-Sammlers des Primärkreislaufes (= Kühlkreislauf am Kupolofen) ansetzt und der mittels einer Ringleitung in DN-125 mm über das Dach bis in den Bereich der Lackieranlage verläuft, aufgebaut.
- In die Ringleitung wurden bereits zusätzliche Stutzen für potentiell zukünftige Abnehmer integriert.
- Im Sekundärkreis-Vorlauf erreicht das Thermalöl eine Temperatur von ca. 210°C. Zur Nutzung eines Teils dieser Abwärme für eine Lackieranlage wurden 5 Thermalöl-Luft-Wärmetauscher in den Trocknungstunnel der Lackieranlage eingebaut.
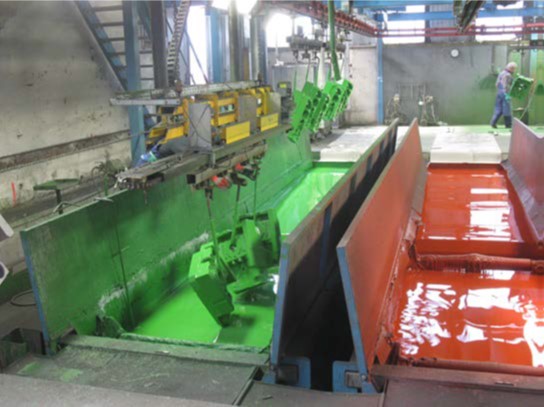
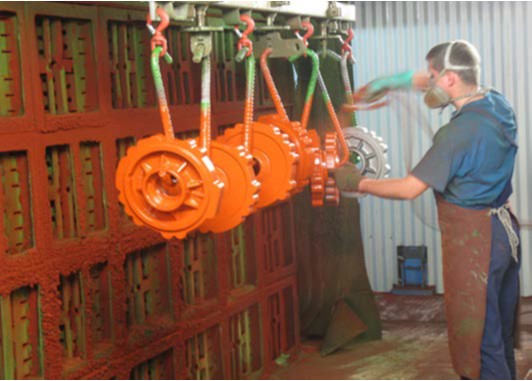
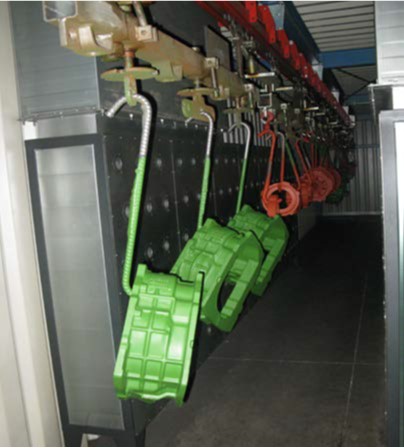
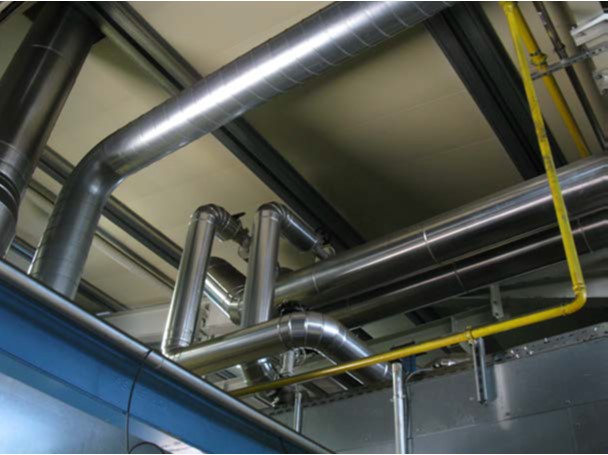
Tabelle: Betriebsdaten
Hersteller | Heimer Lackieranlagen GmbH & Co.KG 2009 (eigentliche Anlage) 2010 (Erweiterung Abwärmenutzung) |
Betriebszeiten | Montag bis Freitag im Drei-Schichtbetrieb |
Flächenbedarf | 1.700 m² |
Leistung - Durchsatz Gussteile | ca. 6.500 kg /h |
Installierte elektrische Leistung | 335 KW |
Installierte Brennerleistung Erdgas | 2.250 KW |
Stromverbrauch | 1.728.028 KWh in 2010 |
Gasverbrauch | 118.078 m³/a bzw. 1.315.400 KWh in 2010 |
Erreichter Umweltnutzen
- Im Falle einer nachträglich eingebauten Wärmerückgewinnungsanlage lässt sich der Gasverbrauch für die Wasserlack-Trocknung von durchschnittlich ca. 25,5 m³/h auf ca. 18,2 m³/h, d. h. um ca. 30 % reduzieren. Zu berücksichtigen ist, dass der Kupolofen zweischichtig und die Grundieranlage dreischichtig betrieben werden. Ein dreischichtiger Betrieb des Kupolofens führt zu einer höheren Nutzungsdauer der Abwärmenutzung und damit zu einem zusätzlichen Einsparpotenzial
- Durch Einführung der Wasserlacksysteme reduzierte sich der Lösemittelverbrauch von 107 VOC-to in 2008 (= Komplettproduktion mit lösemittelhaltigen Lacken) auf 14,1 VOC-to in 2010 (= Komplettproduktion mit Wasserlack-systemen)
- Nachdem der C-Gesamt-Ausstoß den Grenzwert von 5 mg-C/m³ unterschreitet, unterliegt die Anlage keiner eigenständigen Emissionsmessverpflichtung
Verlagerungseffekte
- Gegenüber den konventionellen lösemittelhaltigen Lacksystemen entsteht ein nicht unerheblicher zusätzlicher Energiebedarf zur Lacktrocknung
- Da dieser zusätzliche Energiebedarf nicht vollständig durch die Nutzung von Abwärme abgedeckt werden kann, steigt der CO2-Ausstoß der Erdgasbrenner
- Kosten für die Beschaffung der Wasserlacksysteme liegen um ca. 1/3 über den Einkaufskosten der lösemittelhaltigen Grundierungen
- Deutlich stärkerer Materialverbrauch aufgrund einer höheren Schichtdicke
- Verlagerung der Gesundheitsgefahr: Wasserlack kann über die Haut aufgenommen werden
Anwendbarkeit
Folgende Aspekte zu den Wasserlacksystemen müssen bei der Einführung beachtet werden:
- Besondere kundenspezifische Anforderungen an den Grundierungsaufbau (z. B. Salzsprüheigenschaften und Steinschlagabfederung)
- Oberflächen der Gussteile müssen frei von Fett- und Ölverschmutzungen sein
- Vorgaben zu Schichtdicken sind nicht zuletzt aufgrund der Rauhtiefen der Gussoberflächen einzuhalten
- Vernetzung des Lacks kann durch unzureichende Verarbeitungstemperaturen und -Zeiten stark beeinträchtigt bzw. behindert werden
- Zur Auslegung der nominalen Ofenleistung muss auf Basis des Gussprogramms eine Ofenkurve erarbeitet werden - Hintergrund ist hierzu die Relation der Umluft- zur Objektoberflächentemperatur (z. B. Objektoberflächen-temperatur lt. Spezifikation = min. 100°C für 20 Minuten Haltezeit bedeutet 140°C Umlufttemperatur für 45 Minuten Haltezeit)
- Nachrüstbarkeit von vorhandenen Anlagen aufgrund der vorstehend genannten Punkte nur bedingt möglich
Wirtschaftliche Aspekte
- Bei der Einleitung von Abwärme ins Fernwärmenetz kann die sonst ungenutzte Abwärme wirtschaftlich vorteilhaft genutzt werden, z. B. durch feste Abnahmepreise
- Die zusätzlichen Investitionskosten für die Integration einer Abwärmenutzung zur Lacktrocknung beliefen sich auf ca. 1,4 Mio. EUR. Hierbei wurden die Kosten nur anteilsmäßig berücksichtigt
- Im Vergleich zur Beschichtung mit lösemittelhaltigen Lacksystemen sind die Produktionskosten für die Verarbeitung von Wasserlacksystemen aufgrund der deutlich höheren Materialkosten und des -verbrauches sowie des enormen zusätzlichen Energiebedarfs ohne Abwärmenutzung um ca. 75 % höher
- Durch die Abwärmenutzung zur Lacktrocknung können die Produktionskosten im Vergleich zu einer Lacktrocknung unter ausschließlicher Verwendung von Erdgasbrennern um ca. 20 bis 25 % reduziert werden
- Trotz diverser Energieabnehmer steht weitere Wärmeenergie in der Eisengießerei ungenutzt zur Verfügung. In einem Forschungsvorhaben will die Gießerei Heunisch zusammen mit Partnern diese Energie durch Speicherung nutzbar machen.
Gründe für die Anwendung dieser Technik
- Um einen Teil des deutlich höheren Energiebedarfs zu decken wurde die Abwärmenutzung am Kupolofen zur Lacktrocknung implementiert
- Aufgrund von gesetzlichen Vorgaben (VOC-Verordnung) wurde die Umstellung von lösemittelhaltigen Grundierungen auf Wasserlacksysteme vonnöten
Referenzanlagen
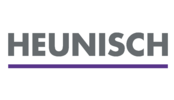
Gießerei Heunisch GmbH, Bad Windsheim
Informationsquellen
- Blank, S. (2012): Mollig warme Klassenzimmer dank Energie aus Gießerei, www.nordbayern.de/region/bad-windsheim/mollig-warme-klassenzimmer-dank-energie-aus-giesserei-1.2385027/kommentare-7.1580339, Abruf März 2013
- Enzenbach, T. (2009): Abwärmenutzung bei Kupolofen - Schmelzanlagen mit dem Einsatz von Thermalöl als Wärmeträger. In: Giesserei, Nr. 10, S. 68-74
- Ebert, C. (2014): Pressemeldung Heunisch GmbH: Gießerei forscht an thermischer Energiespeicherung, Bad Windsheim