Smart Melting: Steigerung der Energieeffizienz in der Schmelzerei von Aluminium-Schmelz- und Druckgussbetrieben
Von Matthias Henninger, Wolfgang Schlüter, Dominik Jeckle und Jörg Schmidt, Ansbach
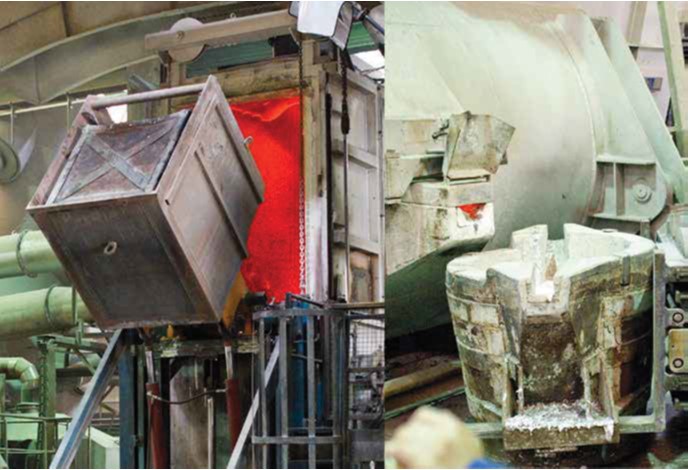
Das Kompetenzzentrum für industrielle Energieeffizienz der HS Ansbach untersucht die Auswirkungen der Ofenbeschickung auf die Leistungsdaten von Aluminiumschmelzöfen mittels Simulation (links: Beschickung, rechts: Entnahme Schmelzofen).
Erschienen in GIESSEREI 03/2017
Um am Weltmarkt bestehen zu können, ist es insbesondere für energieintensive Unternehmen wie zum Beispiel Schmelz- und Druckgussbetriebe überlebensnotwendig, einen hohen Automatisierungsgrad und eine hohe Energieeffizienz zu erreichen. Dies gilt auch für die Nichteisenmetall-Gießerei-Industrie, welche im Fokus der vorliegenden Studie steht. In Deutschland werden jährlich ungefähr 5,9 Mio. t Metall eingeschmolzen und vergossen, davon sind ca. 20 % Nichteisenmetall-Werkstoffe. Bei einem abgeschätzten Energieeinsatz von 2000 kWh pro Tonne gutem Guss ergibt sich dafür ein jährlicher Energieverbrauch von 2,2 Mrd. kWh [1]. Nach Angaben des Bundesverbandes der Deutschen Gießerei-Industrie (BDG) betragen die Kosten für Energie in der Gießerei-Industrie 25 % der Bruttowertschöpfung [2]. Davon entfallen ungefähr 50 % des Energiebedarfs auf den Schmelzbereich [1]. Aufgrund des hohen Kosten- und Energieaufwandes wurde ebenfalls vom BDG eine Liste mit Empfehlungen für eine energieeffiziente Betriebsweise von Schmelzöfen erarbeitet [3].
Der effiziente Umgang mit Ressourcen – und speziell der Energie – ist durch den Klimawandel und die Energiewende verstärkt in den Fokus der Forschung gerückt. Das Verbundforschungsprojekt Green Factory Bavaria ist in diesem Forschungsfeld angesiedelt [4]. Im darin enthaltenen Teilprojekt „Smart Melting“ werden neue Wege zur Steigerung der Energieeffizienz in der Aluminium-Druckgussindustrie untersucht. Der Schwerpunkt des Projektes liegt auf einer Verringerung des Energieverbrauchs von gasbetriebenen Schmelzöfen durch eine verbesserte Abstimmung zwischen den Teilbereichen Schmelzen und Druckgießen und einer daran gekoppelten intelligenten Betriebsweise der Schmelzanlagen und Aluminiumdistribution.
Um die Steuerungsmaßnahmen entwickeln zu können, müssen zunächst die Betriebsabläufe und Zusammenhänge innerhalb des kompletten Schmelz- und Druckgussbetriebes erfasst und verstanden werden. Dies erfolgt einerseits durch die Aufnahme und Analyse von Messdaten und andererseits durch die Entwicklung eines Simulationsmodells, welches insbesondere für die Untersuchung von Zusammenhängen, Schwachstellen und sich ändernden Rahmenbedingungen große Vorteile besitzt.
Grundlagen
Aufbau des Schmelz- und Druckgussbetriebes
Die Grundlage, um ein Simulationsmodell entwickeln oder Schwachstellen im Betriebsablauf aufdecken zu können, ist immer eine zielgerichtete und realistische Analyse des zu betrachtenden Problems. Um garantieren zu können, dass mit der Verbesserungsmaßnahme das beste Ergebnis für den Gesamtbetrieb erreicht wird und keine relevanten Kopplungen vernachlässigt werden, ist es wichtig, den Betrieb in seiner Gesamtheit zu erfassen [5].
Die wichtigsten Anlagen und Zusammenhänge in einem Schmelz- und Druckgussbetrieb werden anhand von Bild 1 beschrieben. Die Anlieferung des Aluminiums erfolgt in fester (Masseln) beziehungsweise flüssiger Form. Das angelieferte Flüssigaluminium kann direkt an die Druckgießmaschinen weiterverteilt werden. Das feste Aluminium hingegen muss vor der Weiterverarbeitung zunächst betriebsintern in Schmelzöfen aufgeschmolzen werden. Für den Aufschmelzvorgang wird das angelieferte Masselmaterial in der Regel mit sogenanntem Ausschussbzw. Rücklaufmaterial, welche Abfallprodukte des Gießprozesses bzw. der Bauteilnachbearbeitung sind, im Verhältnis 50 : 50 gemischt. Der Transport des festen bzw. flüssigen Aluminiums erfolgt mit Staplern.
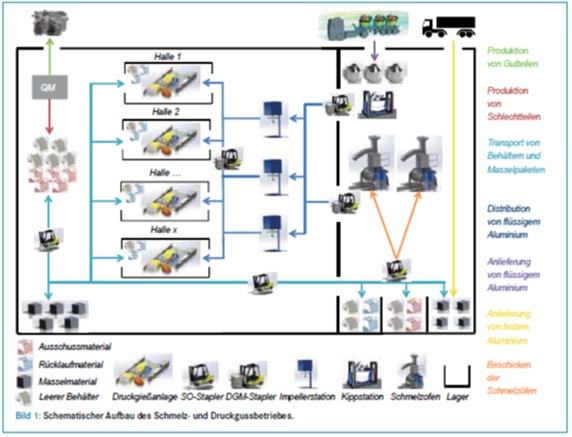
In den Druckgießmaschinen erfolgt die Urformung der Bauteile. Die Anzahl der produzierten Teile und der Verbrauch an flüssigem Aluminium sind in besonderem Maße abhängig von Taktzeit und Schussgewicht der Anlage. Die Druckgießmaschinen sind die einzigen Aluminiumsenken und geben somit die Nachfrage an Flüssigaluminium vor. Produktionsschwankungen der Druckgießmaschinen in Kombination mit ungenauer Datenlage zum Aluminiumverbrauch und den hochkomplexen Vorgängen im Schmelzofen machen es für den Produktionsleiter der Schmelzerei nahezu unmöglich, eine intelligente und ideal an die Situation angepasste Betriebsweise der Schmelzöfen zu gewährleisten. Dies hat zur Konsequenz, dass die Schmelzöfen häufig ebenfalls nicht gleichmäßig in einem idealen Betriebspunkt, sondern fluktuierend betrieben werden. Daraus resultiert ein erhöhter spezifischer Energieverbrauch infolge von Aufheiz- und Abkühlvorgängen des Ofens und energetisch ungünstigeren Wärmeübergangssituationen bei geringeren Ofenauslastungen.
Aufbau des Schachtschmelzofens
Die Funktion des simulierten und untersuchten Schachtschmelzofens mit kurzem Schacht kann in vier Teilfunktionen unterteilt werden (Bild 2). Durch die hargiereinrichtung wird das feste Aluminium in den Schmelzschacht eingebracht (Funktion 1). Im Schmelzschacht wird das Aluminium durch die mit Erdgas befeuerten Schmelzbrenner erwärmt und geschmolzen (Funktion 2). Dabei wird durch die Brenner heißes Rauchgas erzeugt, welches das Aluminium umströmt und dabei einen Großteil seiner Energie an das Aluminium abgibt. Je mehr Energie von diesem an das Aluminium übertragen wird, desto höher ist der Wirkungsgrad des Schmelzofens. Sowohl das erzeugte Rauchgas wie auch das geschmolzene Aluminium verlassen den Schmelzschacht in Richtung Warmhaltebereich (Ofenwanne). In dieser wird das flüssige Metall überhitzt und auf einer definierten Temperatur gehalten (Funktion 3). Für diesen Vorgang wird zum einen das Rauchgas der Schmelzbrenner und zum anderen, falls dieses nicht ausreicht, das Rauchgas der Warmhaltbrenner verwendet. Die Entnahme des Aluminiums erfolgt über den Entnahmestutzen durch Kippen des Ofens (Funktion 4).
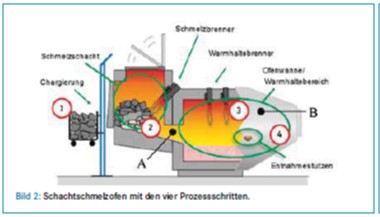
Maßnahmen zur Steigerung der Energieeffizienz im Schmelzbetrieb
Betriebsweise und Energieverbrauch
des Schachtschmelzofens Eine energieeffiziente Betriebsweise des Schmelzofens erfordert eine kontinuierliche Betriebsweise in einem geeigneten Betriebspunkt und einen hohen Aluminiumfüllstand im Schmelzschacht. Für die Untersuchung des Ist-Zustandes wurden Messungen in einem Referenzbetrieb durchgeführt. Die im Folgenden beschriebenen Abbildungen und Tabellen beziehen sich alle auf eine charakteristische Messreihe.
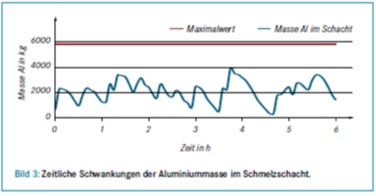
In Bild 3 sind der Maximalwert und der gemessene Wert für die Aluminiummasse im Schmelzschacht dargestellt. Der reale Schachtfüllstand ist immer deutlich geringer als der maximal mögliche Schachtfüllstand und fluktuiert sehr stark zwischen einem Minimalwert von 400 kg und einem Maximalwert von 4200 kg. Mit der immer wieder auftretenden Abnahme der Aluminiummasse ist eine Abnahme der wärmetauschenden Oberfläche und der treibenden Temperaturdifferenz zwischen Rauchgas und Aluminium verbunden. Daraus resultieren eine Abnahme des Wärmestroms vom Rauchgas an das Aluminium und somit eine erhöhte Rauchgasaustrittstemperatur des Ofens. Die Abnahme des Wärmestroms an das Aluminium verringert den thermischen Wirkungsgrad und erhöht den spezifischen Energieverbrauch des Ofens. Übersteigt die Rauchgasaustrittstemperatur einen definierten Grenzwert, wird die interne Brennersteuerung aktiv und verringert die Brennerleistung. Dies führt zu einer Abkühlung der Ofenwand, welche bei steigender Auslastung wieder aufgeheizt werden muss. Daher ist zu erwarten, dass die in Bild 3 dargestellte fluktuierende Betriebsweise die Leistungskennwerte negativ beeinflusst. Die genannten negativen Auswirkungen werden durch einen Vergleich der gemessenen Leistungsdaten mit den Herstellerangaben bestätigt (Tabelle 1). So liegen der spezifische Energieverbrauch 25 % über und die Schmelzleistung mit 3,68 t/h im unteren Bereich der Herstellerangabe. Dabei muss berücksichtigt werden, dass im realen Betrieb Vorteile in Bezug auf die Wärmeübertragung aufgrund einer höheren spezifischen Oberfläche und Temperatur des eingebrachten Aluminiums gegenüber den Herstellerangaben vorliegen. Da die Herstellerangaben trotz dieser Vorteile nicht erreicht werden, müssen zusätzliche negative Einflüsse vorhanden sein. Die beschriebene diskontinuierliche Betriebsweise mit stark fluktuierendem Schachtfüllstand wird als signifikanter negativer Einfluss im Folgenden detailliert betrachtet.
Tabelle 1: Vergleich der Leistungsdaten zwischen realem Betrieb und Herstellerangabe.
Spez. Energieverbrauch in kWh/t | Schmelzleistung in t/h | |
Herstellerangabe | +25 % | 3,5-4,5 |
Gemessene Werte | +25 % | 3,68 |
Verbesserte Betriebsführung
Ziel der verbesserten Betriebsführung ist eine kontinuierliche Betriebsweise des Ofens mit maximaler Brennerleistung und gleichmäßig hoher Aluminiummasse im Schmelzschacht. Daraus sollen sich eine Verringerung des spezifischen Energieverbrauchs und eine Erhöhung der Schmelzleistung bei gleichbleibender Qualität des geschmolzenen Aluminiums ergeben. Bei einer angepassten Beschickungsstrategie (Bild 4) befindet sich die Masse immer im Bereich zwischen 3200 kg und 4800 kg. Der hohe Schachtfüllstand führt zu einer großen Wärmeübertragungsfläche und einer daraus resultierenden niedrigeren Abgastemperatur am Schachtaustritt. Kombiniert man diese Effekte mit der konstanten Brennerleistung, sind eine Annäherung der Schmelzleistung und eine Verringerung des spezifischen Energieverbrauchs an die Herstellerangaben zu erwarten.
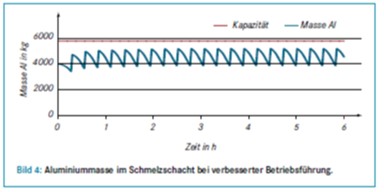
Abgastemperaturen
Der Wirkungsgrad der Wärmeübertragung im Schmelzofen liegt je nach Betriebssituation zwischen 25 und 50 %. Die Austrittstemperatur des Rauchgases aus dem Ofen ist besonders gut geeignet, um eine Aussage über die Energieeffizienz zu treffen. Dies liegt daran, dass diese ein Ergebnis aller Wärmeübergangsvorgänge innerhalb des Schmelzofens ist. Pauschal kann gesagt werden, dass die Effizienz mit abnehmender Rauchgastemperatur zunimmt. In Bild 5 sind die Rauchgastemperaturen am Schachtende und Ofenaustritt eingetragen. Die Positionen dieser Messpunkte sind in Bild 2 mit A und B gekennzeichnet. Am Schachtende sind deutlich die Auswirkungen der Schwankungen des Aluminiumfüllstandes im Schmelzschacht (vgl. Bild 3) auf die Rauchgastemperatur erkennbar. So ist diese nach einem Beschickungsvorgang immer am niedrigsten und steigt mit zunehmendem zeitlichen Abstand zu diesem an. Die Rauchgastemperatur am Ofenaustritt verläuft wesentlich gleichmäßiger und bewegt sich im Korridor zwischen 850 °C und 1000 °C. Dies zeigt, dass im Rauchgas am Ofenaustritt noch ein hoher Energiegehalt vorhanden ist, welcher für eine Verbesserung des thermischen Gesamtwirkungsgrades des Ofens genutzt werden kann.
Energieeffizienzsteigerung durch externe Masselvorwärmung
Eine Möglichkeit dieses Potenzial zu nutzen, ist die Einführung einer externen Vorwärmkammer. Diese wird direkt neben dem Schmelzofen angebracht und verwendet den aus dem Ofen austretenden Abgasstrom für die Erwärmung von Masselmaterial. Dies führt zu einer weiteren Energieabgabe des Rauchgases und somit zu einer besseren Ausnutzung der durch die Brenner eingebrachten thermischen Energie. Durch die Energieübertragung werden die mit Raumtemperatur eingebrachten Aluminiummasseln auf eine definierte Temperatur erwärmt. Die Masseln mit erhöhter Temperatur werden anschließend in den Schmelzofen eingebracht. Im Schmelzschacht muss aufgrund der bereits zugeführten Energie weniger Energie übertragen werden, was zu einer höheren Schmelzleistung und einem geringeren spezifischen Energieverbrauch führt. Die externe Masselvorwärmung bietet sich bei den Schachtschmelzöfen mit kurzem Schacht aufgrund der dort auftretenden hohen Rauchgastemperaturen am Ofenaustritt besonders an.
In Tabelle 2 sind die Ergebnisse einer Überschlagsberechnung zum Einsparpotenzial durch Vorwärmung der Aluminiummasseln aufgelistet. Mit zunehmender Vorwärmtemperatur erhöht sich die Kosteneinsparung linear. Dies liegt an der idealisierten Berechnung, in der davon ausgegangen wird, dass immer alle Masseln vorgewärmt werden können. Des Weiteren werden mögliche negative Effekte der Vorwärmung, wie die daraus resultierende geringere treibende Temperaturdifferenz zwischen Rauchgas und eingebrachtem Aluminium im Schmelzschacht, vernachlässigt. Die Kosteneinsparung bezieht sich ausschließlich auf die Einsparung aufgrund des geringeren Gasverbrauches. Die anfallenden Anschaffungs- und Betriebskosten der Vorwärmkammer werden nicht betrachtet.
Tabelle 2: Einsparpotenziale bei Integration einer Masselvorwärmung.
Vorwärmtemperatur in °C | Masselverbrauch in kg/d | Ideale Energieeinsparung2) in kWh/d | Kosteneinsparung2) in €/d | Kosteneinsparung2)3) in €/a |
100 | 40 000 | 2400 | 83,04 | 24 912 |
200 | 40 000 | 5400 | 186,84 | 56 052 |
300 | 40 000 | 8400 | 290,64 | 87 192 |
1)Annahme eines mittleren Wärmeübertragungswirkungsgrades des Ofens von 33 %; 2) als Gaspreis für Industriekunden wurden 3,46 Cent/kWh verwendet [6]; 3) für die Berechnung wurden 300 Produktionstage angesetzt
Simulationsmodell
Um die Zusammenhänge der Prozessparameter, wie die Auswirkung der Ausfallzeiten und der Nachfragesituation der Druckgießmaschinen auf die Schmelzöfen, besser zu verstehen, wird der in Bild 1 dargestellte Schmelz- und Druckgussbetrieb mit einem Simulationsmodell abgebildet. Nach erfolgter Validierung kann dieses dazu genutzt werden, unterschiedliche Betriebszustände zu untersuchen. Aus den Ergebnissen können dann Handlungsalternativen für die Aluminiumdistribution, die Betriebsweise der Druckgießanlagen und der Schmelzöfen generiert werden. So kann zum Beispiel die optimale Reaktion auf einen Ausfall eines Schmelzofens oder die Verspätung eines Flüssigaluminiumtransports abgeleitet werden. Mithilfe des Simulationsmodells können Verbesserungsmaßnahmen wie zum Beispiel die verbesserte Beschickung und die Vorwärmung kostengünstig und risikofrei in einer virtuellen Umgebung analysiert werden, ohne in den realen Betrieb eingreifen zu müssen. Das entwickelte Simulationsmodell setzt sich aus einem Materialflussmodell und einem Energiemodell, welches die energetischen Vorgänge in den Schmelzöfen detailliert abbildet, zusammen.
Materialflusssimulation
Im Materialflussmodell werden der Aluminiumtransport und die Verarbeitung des Aluminiums in den Druckgießmaschinen auf der Grundlage von Bild 1 abgebildet. Das Modell erfasst unter anderem die Stapler, deren Steuerung sowie die Druckgießmaschinen. Die Staplersteuerung beinhaltet sowohl die Strategie der Verteilung des flüssigen Aluminiums an die Druckgießmaschinen wie auch die gewählte Reihenfolge der Beschickung der Schmelzöfen. Dieses Modell bildet somit die Einund Ausgänge des Energiemodells und nimmt somit Einfluss auf die Betriebsweise des Schmelzofens im Simulationsmodell. Damit lassen sich in der Simulation die Auswirkungen unterschiedlicher Nachfragesituationen und Beschickungsstrategien der Schmelzöfen untersuchen [7].
Energiemodell der Schmelzöfen
Im Schmelzofen finden die Verbrennung von Erdgas durch Brenner, der Phasenübergang des Aluminiums sowie Wärmeund Stofftransportvorgänge (Leitung, Konvektion, Strahlung) statt. Zur exakten Erfassung und Abbildung der Problematik müsste auf Strömungssimulationen (CFD) zurückgegriffen werden. Diese führen jedoch zu sehr komplexen Modellen mit hohem Rechenaufwand und geringer Flexibilität hinsichtlich sich ändernder Rahmenbedingungen. Für die Simulation von längeren Zeitabschnitten mit permanent
wechselnden Rahmenbedingungen wird
daher das mathematische Modell auf einen
Satz gewöhnlicher Differenzialgleichungen
vereinfacht.
Um die Güte des erarbeiteten Modells
zu erhöhen, werden unterstützende Simulationen
von verschiedenen stationären
Fällen mit einem CFD-Programm
durchgeführt. Wegen der Vereinfachungen
und zusätzlicher Annahmen kommt
der Validierung des Modells anhand von
Messdaten große Bedeutung zu. Detaillierte
Angaben zum Energiemodell sind
unter [8] zu finden.
Validierung des Materialflusses
Beim Vergleich der kompletten Materialflusssimulation
mit realen Betriebsdaten
ergab sich über eine Kalenderwoche bei
der Zahl der produzierten Gussteile eine
Abweichung von 14,5 %. Die Abweichung
ist im Wesentlichen auf die durch einen
statistischen Ansatz in der Simulation berücksichtigten
ungeplanten Stillstände
der Druckgießmaschinen zurückzuführen.
Durch den statistischen Ansatz, der nur
von einer normalverteilten mittleren Ausfallzeit
der Druckgießmaschinen (ermittelt
aus realen Ausfallzeiten im Betrieb
des Kooperationspartners) ausgeht, wird
keine genaue Differenzierung der Ausfälle
vorgenommen und es kommt zu Abweichungen
zwischen den simulierten
und den tatsächlichen unvorhergesehenen
Stillständen.
Validierung des Energiemodells
Da das Energiemodell des Schmelzofens
unter starken Vereinfachungen und zahlreichen
Annahmen entwickelt wird,
kommt der Validierung hier große Bedeutung
zu. Bei einem Vergleich mit Messwerten,
die im Betrieb des Kooperationspartners
erhoben wurden, zeigt sich eine
gute Übereinstimmung beim zeitlichen
Verlauf der festen Aluminiummasse im
Schmelzschacht (Bild 6a). Die Masse an
flüssigem Aluminium in der Ofenwanne
ist direkt daran gekoppelt und kann somit
auch gut abgebildet werden. Der Vergleich
bei der Abgastemperatur des
Rauchgases zeigt, dass der zeitliche Verlauf
der Wärmeübertragung vom Rauchgas
auf das feste Aluminium in der Simulation
richtig abgebildet wird (Bild 6b).
Damit kann davon ausgegangen werden,
dass der Materialfluss mit dem Phasenübergang
fest-flüssig im Schmelzofen in
der Simulation ausreichend genau wiedergegeben
werden kann.