Mit Leidenschaft für eine leichtere Zukunft
Ein Bericht von GF Casting Solutions
Aus Alt mach Neu! Und aus Neu wird später einmal wieder Alt - und so weiter. Ein ewiger Kreislauf! Nicht nur Recycling macht Guss wertvoll für die Zukunft. Autos sterben auf dem Schrottplatz!?! Ab in die Presse. Quadratisch, praktisch, gut und weg den Schrott?! … Denkste! Der Kreislauf des Materials startet dort, wo sein vorheriges Leben endet.
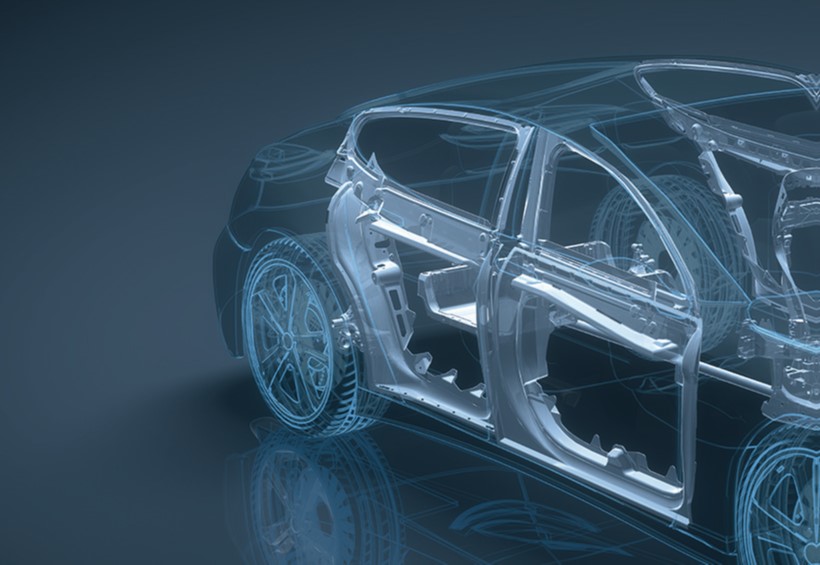
Aus Bahnschiene mach Kurbelwelle! Recycling macht‘s möglich. Aluminium, Magnesium oder Eisen, ganz egal, Gussteile von GF Automotive sind alle wiederverwertbar. Der Eine nennt es Schrott, die Gießereien nennen es Rohstoff. Eisen und Aluminium können nach ihrem Gebrauchsende wieder zum Rohstoff, als Eisenschrott oder Sekundäraluminium, für neuen Guss verwendet werden. Wie oft? Ganz egal! Metalle lassen sich immer wieder einschmelzen und erneut vergießen, und das ohne Nachteile!
Gussteile schonen die Umwelt, der Wiederverwertung sei Dank.
Die Politik fordert aufgrund des Klimawandels, den CO2-Ausstoß zu senken. Autohersteller und deren Lieferanten wie Gießereien arbeiten mit Nachdruck daran den CO2-Ausstoß zu reduzieren. Doch wie? Durch Leichtbau. Und warum? Weil ein leichteres Auto weniger Kraftstoff verbraucht und weniger Kraftstoff heißt weniger CO2-Ausstoß. Bei GF Automotive heißt es deshalb: „Kampf den Pfunden!“ Wir gießen Teile, die leicht und gleichzeitig stabil sind.
Neue Autos sollen leichter werden, also müssen wir unseren Kopf anstrengen! Jedes Teil muss gecheckt werden. Zu schwer? Mach‘s leichter! Ein Beispiel: unser leichtes Schwenklager, ein Teil des Fahrwerks, mit bionischem Design. Biowas? Bionisches Design, sprich bei Mutter Natur gespickt, denn die hat zigtausend Jahre Erfahrung in Sachen Leichtbau. Bäume und Skelette sind Grundgerüste, optimal im Verhältnis
von Gewicht zu Stabilität. Gussteile, die im Fahrwerk stark beansprucht werden, damit Du in Zukunft richtig Gas geben kannst, müssen gleichzeitig absolut sicher und zuverlässig sein. Leicht, stabil und sicher in einer Form zu verbinden ist eine ganz schön große Herausforderung.
Design ist das Eine, der Werkstoff ist aber auch sehr wichtig. Wir von GF Automotive haben den Eisengusswerkstoff „SiboDur“ entwickelt. SiboDur verbunden mit bionischem Design plus eine Verbesserung in der Herstellung sparen 20 % Gewicht bei Schwenklagern und Radträgern. In der neuesten Studie der Entwickler wurden beim Schwenklager in Eisen sogar ganze 32 % Gewichtseinsparung erzielt – das wären 2,82 kg pro Fahrzeug. Das ist nicht viel!? Du fragst dich sicherlich, was das schon bringen soll. Für ein Fahrzeug senkt dies den CO2-Ausstoß nur wenig, aber es gibt ja nicht nur das Eine.
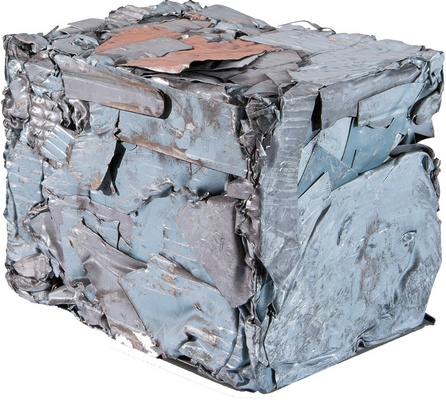
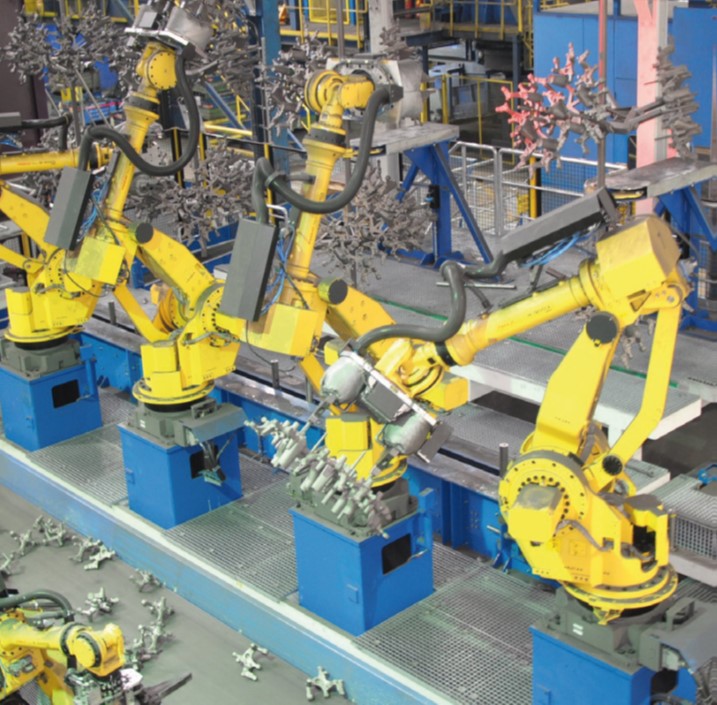
Bei 1,6 Millionen Fahrzeugen ist das eine ganze Menge, genau gesagt 11.600 Tonnen CO2 weniger pro Jahr. Daher hat diese Studie im Oktober 2012 den „ÖkoGlobe“ von der Uni Duisburg-Essen bekommen. Das Schwenklager wird bereits in Serie, sprich in großen Massen produziert. Solche bionischen Schwenklager und Radträger werden für VW und deren „Modulare Querbaukasten-Plattform“ gegossen, die man sich als einen Steckbaukasten für Motor und Co. vorstellen kann. Und wo werden diese Teile eingesetzt? Zum Beispiel im neuen Audi A3 oder dem Golf VII sind sie verbaut und helfen, die Umwelt zu schonen.
Wir legen in all unseren Gießereien großen Wert auf Nachhaltigkeit. So entstehen zum Beispiel bei unserer Produktion in Herzogenburg im Jahr rund 18.000 Tonnen Altsand.
Diese müssen eigentlich teuer entsorgt werden, aber unsere Ingenieure waren clever. Um die Umwelt zu schonen, überarbeiten wir diese Altsande und machen sie für die Zementindustrie als Sekundärrohstoff, quasi das zweite Leben des Rohstoffs, nutzbar. Und damit sind wir wieder beim Recycling.
Gießereien schmelzen Metalle bei sehr hohen Temperaturen, das ist klar. Dadurch wird aber nicht nur das Metall heiß, sondern zum Beispiel auch die Luft. In Singen hatten wir die Idee, diese Wärme weiter zu nutzen. Aber das ist viel mehr Abwärme, als wir selbst nutzen können. Wie praktisch, dass die Firma MAGGI nebenan ihre Ravioli und die berühmte MAGGIWürze herstellt und dafür Wärme benötigt.
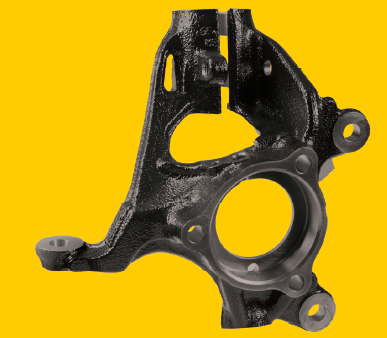
Mit Hilfe eines Wärmetauschers machen wir mit unserer heißen Abluft ein Thermoöl heiß und das nutzt MAGGI in Kombination mit einem Dampfkessel um reinen Wasserdampf herzustellen. Und damit arbeiten sie in ihrer Produktion. Somit sparen sie teures Erdgas, was gleichzeitig wieder den Ausstoß an CO2 senkt und das in der Menge, die allen Autos einer Kleinstadt entspricht. Zusammenarbeit für unsere Umwelt – eine gute Sache!
600.000 t Eisen, Aluminium und Magnesium werden jährlich bei GF Automotive in 100 Millionen Bauteile vergossen. Solche Zahlen setzen ein hohes Maß an Verantwortung voraus. Und wir stellen uns dieser Verantwortung.
Ach ja, und wenn eines der Autos in denen unsere Teile stecken, irgendwann auf den Schrottplatz kommt … Na ja, ihr wisst ja, wie’s dann weitergeht!
Deine Chance
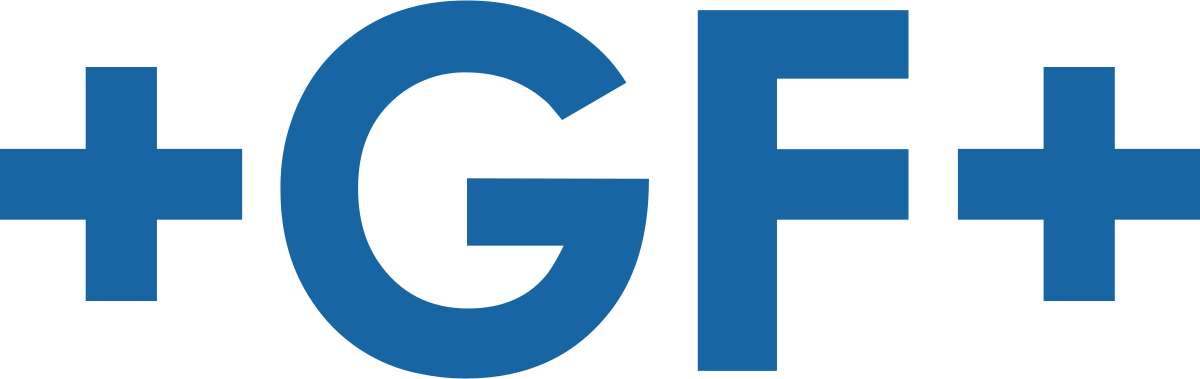
Das klingt spannend? Dann schau doch direkt mal in unsere Ausbildungsbörse oder auf der Website von GF Castings Solutions vorbei und starte mit Leidenschaft in eine leichte Zukunft.