Effizientes Pfannenheizen mit Oxy-Fuel-Brennern
Von Josef Weschenbach, Bielefeld
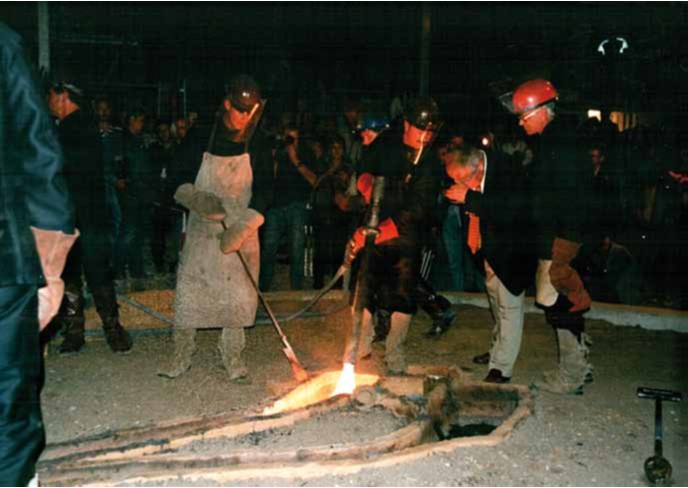
Der Domvorplatz kurz vor dem öffentlichen Abguss der großen Glocke des Halberstädter Dom-Geläutes im September 1999. Auch hier kamen Oxy-Fuel-Brenner zum Aufheizen der Rinnen zur unterirdischen Gießform zum Einsatz.
Erschienen in GIESSEREI 06/2013
Die Einsatzgebiete von Oxy-Fuel-Brennern sind Eisen- und Stahlgießereien sowie Stahlwerke. Erdgas-Sauerstoffbrenner oder Oxy-Fuel-Brenner haben gegenüber Erdgas-Luftbrennern den energetischen Vorteil, dass der Brennstoffbedarf im Vergleich zu Erdgas-Luftbrennern deutlich geringer ist. Zudem sind kurze Aufheizzeiten der Pfannen, Öfen, Konverter und Rinnen (u. a. bei Netz- und Mittelfrequenzöfen) möglich, was mit einer Steigerung der Produktivität einhergeht. Je nach Brennerausführung und Feuerfestzustellung können in etwa 50 bis 60 min Pfannentemperaturen zwischen 1250 und 1450 °C erreicht werden. Die Temperaturdifferenzen zwischen aufgeheizter Pfanne und Schmelzgut sind dabei sehr gering. Darüber hinaus verbessert sich durch die höheren Pfannentemperaturen die Produktqualität. Schließlich ist aufgrund des Mischungsverhältnisses von 1:2 beim Erdgas-Sauerstoff-Brenner gegenüber 1:10 beim Erdgas-Luftbrenner auch der Geräuschpegel beim Einsatz der Anlage deutlich niedriger.
Industrielle Nutzung von Oxy-Fuel-Brennern
Bis etwa in die 1980-er Jahre wurden Pfannen überwiegend mit Klopfmassen (Knüppeln/ Patschen) oder mit Schamotte zugestellt oder auch je nach Größe mit Schamottesteinen gemauert. Auf diese Zeit gehen auch die ersten Aufheizversuche mit Oxy-Fuel-Brennern zurück. Hierbei gab es viele Rückschläge, da diese Pfannen nicht für so hohe Temperaturen geeignet waren, wie sie Oxy-Fuel-Brenner erreichen. Hinzu kam auch, dass die ersten Brenner konstruktionsbedingt zu hohe Strömungsgeschwindigkeiten hatten und bei höheren Leistungen fast wie Schneidbrenner wirkten. Diese Brennerflammen waren oft nicht neutral über die Regelanlagen mit einem Erdgas-Sauerstoffverhältnis 1:2 einstellbar. Häufige Folge waren deshalb Oberflächenbeschädigungen der Pfannen. Heute herrschenhohe Sicherheitsstandards beim Betrieb von Oxy-Fuel-Brennern, u. a. bei der Versorgung mit Sauerstoff, dennoch werden in Gießereien weiterhin überwiegend Holzkohle- oder Erdgas-Luftbrenner eingesetzt. Auch das umstrittene und kostenaufwendige Aufheizen von Pfannen mit Flüssigeisen ist noch gebräuchlich. In Stahlwerken wurde der Einsatz von Oxy-Fuel-Brennern schneller als in Gießereien realisiert, da dort schon hochwertigere Massen, bedingt durch die höheren Eisentemperaturen gegenüber Gusseisen mit Lamellengraphit, eingesetzt wurden. Ab den 1980-er Jahren wurden in Gießereien, bedingt durch höhere Schmelztemperaturen und Qualitäten, die ersten hochwertigeren Betone und Trockenmassen eingesetzt. Die Gussqualitätsanforderungen auf dem Markt sind mittlerweile sehr hoch. Damit verbunden sind auch immer höhere Temperaturen. Oxy-Fuel-Brenner zum Aufheizen von Pfannen und Öfen können einen umweltfreundlichen wirtschaftlichen Beitrag beim energieeffizienten Betrieb von Gießereien leisten. Die neue Brennergeneration ist den technischen Herausforderungen angepasst und kann bis ca. 1250 °C selbstkühlend durch den Sauerstoffstrom und bis ca. 1450 °C und darüber hinaus mit Wasserkühlung eingesetzt werden.
Vom Pfannenbeheizen bis zum Schlackeentleeren
Josef Weschenbach und sein gleichnamiges Ingenieurbüro waren und sind maßgeblich an der Entwicklung neuer Oxy-Fuel-Brenner beteiligt. Seit 18 Jahren ist der Bielefelder Unternehmer, der auf über 40 Jahre Stahl- und Gießereierfahrung zurückblicken kann, selbstständig und trotz seines Alters von 75 Jahren immer noch im Einsatz. Schon früh arbeitete er mit der Martin Renz GmbH, Altena, bei der Installation, beim Anlagenbau und bei der Inbetriebnahme zusammen. Über 150 Projekte in unterschiedlichen Bereichen wurden durchgeführt, z. B. das Sintern von Warmhalte- und E-Öfen bis zu 100 t Inhalt. Hinzu kommen das Aufheizen von Kupolöfen (Zünden) sowie das Aufheizen von Pfannen mit Kapazitäten von 0,5 bis 100 t, was je nach Größe und Feuerfestzustellung zwischen 40 und 70 min dauert. Lösungen wurden auch für das Aufheizen von Siphons, Vorherden, Rinnen, Pfannen, Kokillen und Konvertern entwickelt. Des Weiteren verfügt Weschenbach über Know-how für das schnelle Schlackeentleeren von Pfannen und Kokillen etc.
Wie der Ingenieur ermittelt hat, sind angesichts niedrigerer Aufheizzeiten und damit einhergehendem geringerem Brennstoffbedarf die Abgasemissionen bei Oxy-Fuel-Brennern rund 80 bis 85 % geringer als bei Erdgas-Luftbrennern. Die Anschaffungskosten der Anlage sollen sich je nach Einsatzmöglichkeiten in einem Jahr amortisieren.
Ursachen der Wirksamkeit von Oxy-Fuel-Brennern
Bei jeder Feuerung dient der zu 21 % in der Luft enthaltene Sauerstoff dem Brennstoff (z. B. Erdgas) als Reaktionspartner. Der Effekt der Feuerung ist am größten, wenn mit reinem Sauerstoff gearbeitet wird und der in der Luft enthaltene Stickstoff nicht mit aufgeheizt werden muss – wie beim Oxy-Fuel-Brenner. Der Stickstoff, der mit 79 % der Hauptbestandteil der Luft ist, vergrößert die Abgasverluste und Abgasvolumina. Bei dem Aufheizen von Öfen und Pfannen sollten die Pfannendeckel wegen der geringen
Abgase nahezu aufgelegt werden, um nach dem Aufheizen die Temperatur zu halten. Bei Erreichen der gewünschten Pfannentemperatur, z. B. von ca. 1250 °C, kann über ein Zeitrelais die Anlage automatisch abschalten. Bild 1 zeigt den Energieeinsatz und die Kosten für das Aufheizen einer 8-t-Pfanne bei Erdgas-Luft- und Erdgas-Sauerstoff-Brennern (Bild 2) im Vergleich.
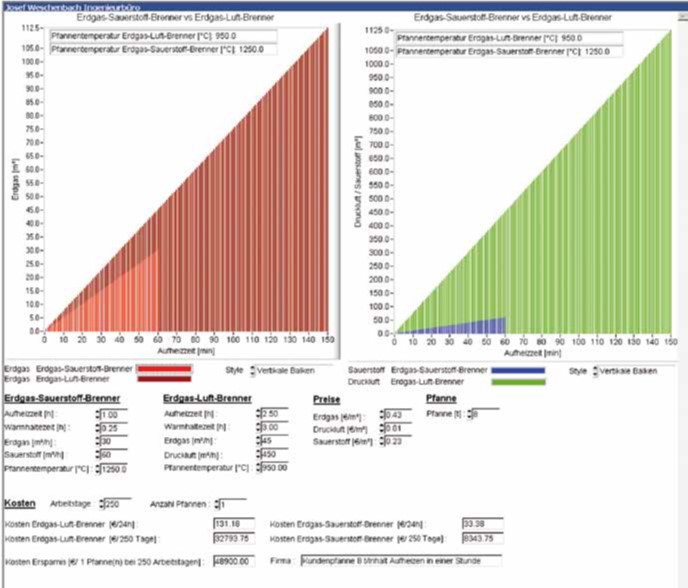
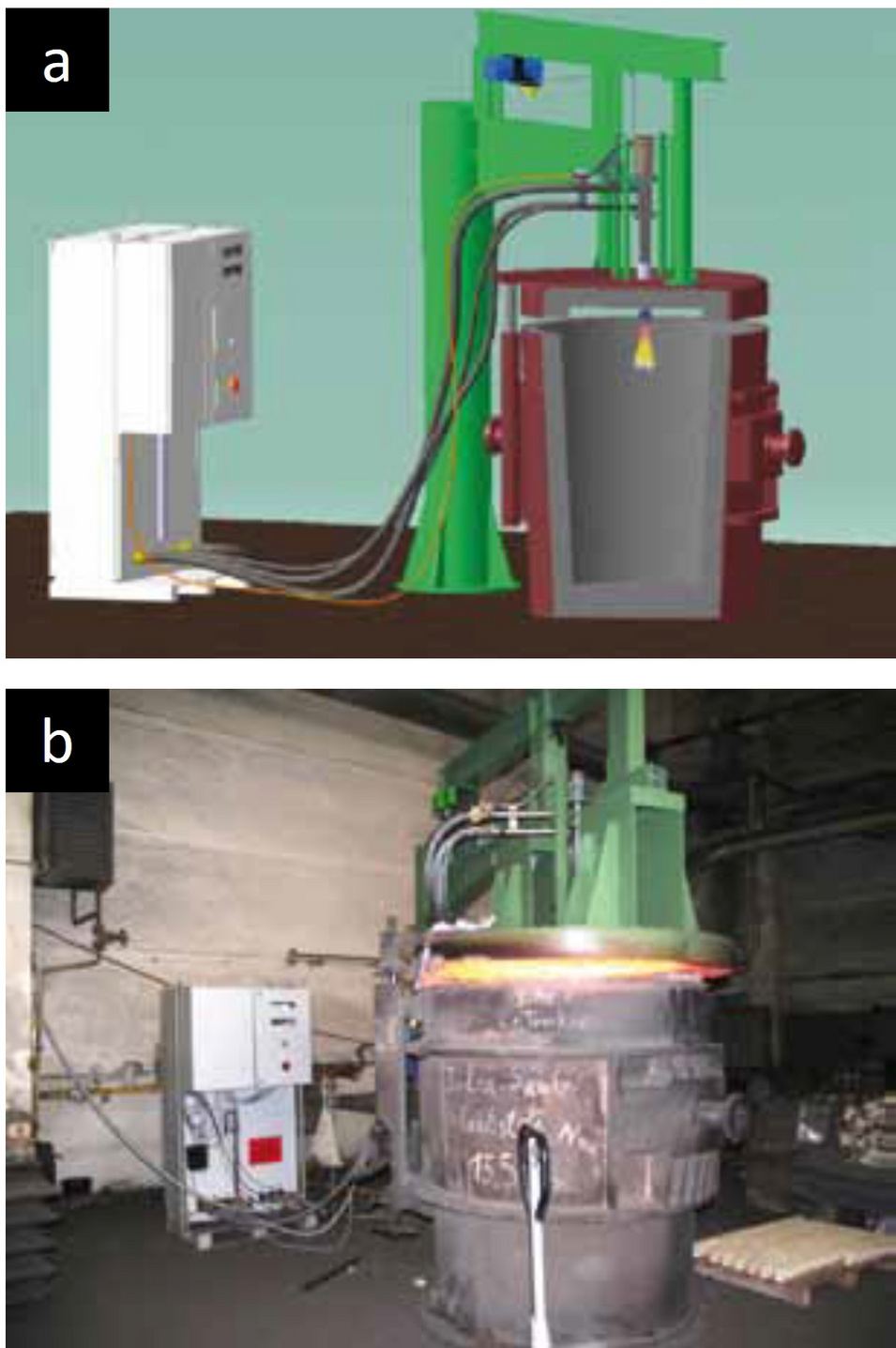
Beispielrechnung nach Bild 1
Erdgas-Luftbrenner
Das Aufheizen der 8-t-Pfanne bis auf ca. 950 °C dauert ca. 2,5 h bei einem Erdgasverbrauch von insgesamt etwa 125 m3 sowie Verbrennungsluft mit ca. 79 % Stickstoff von etwa 1250 m3. Es werden Emissionen von 1250 m3 frei. Die Gesamtkosten für das Aufheizen und Warmhalten einer solchen Pfanne betragen ca 131,18 Euro.
Erdgas-Sauerstoffbrenner
Das Aufheizen der 8-t-Pfanne bis auf ca. 1250 °C dauert hier nur etwa 1 h bei einem Erdgasverbrauch von ca. 30 m3 und ca. 60 m3 Sauerstoff. Die Gesamtemissionen betragen ca. 90 m3 – eine beachtliche Abgasreduzierung. Hier summieren sich die Gesamtkosten einschließlich Warmhalten der Pfanne auf ca. 33,38 Euro pro Pfanne.
Anwendungsbeispiele
25-t-Pfanne mit Spezialisolierung Die Oxy-Fuel-Brenner haben unterschiedliche Einsatzmöglichkeiten. Die Anlage in Bild 3 ist eine fahrbare Oxy-Fuel-Brennerregelanlage, die überall im Betrieb eingesetzt werden kann. Sie verfügt über 2 Massenstromregler, eine elektronische Steuerung und digitale Leistungsanzeigen.
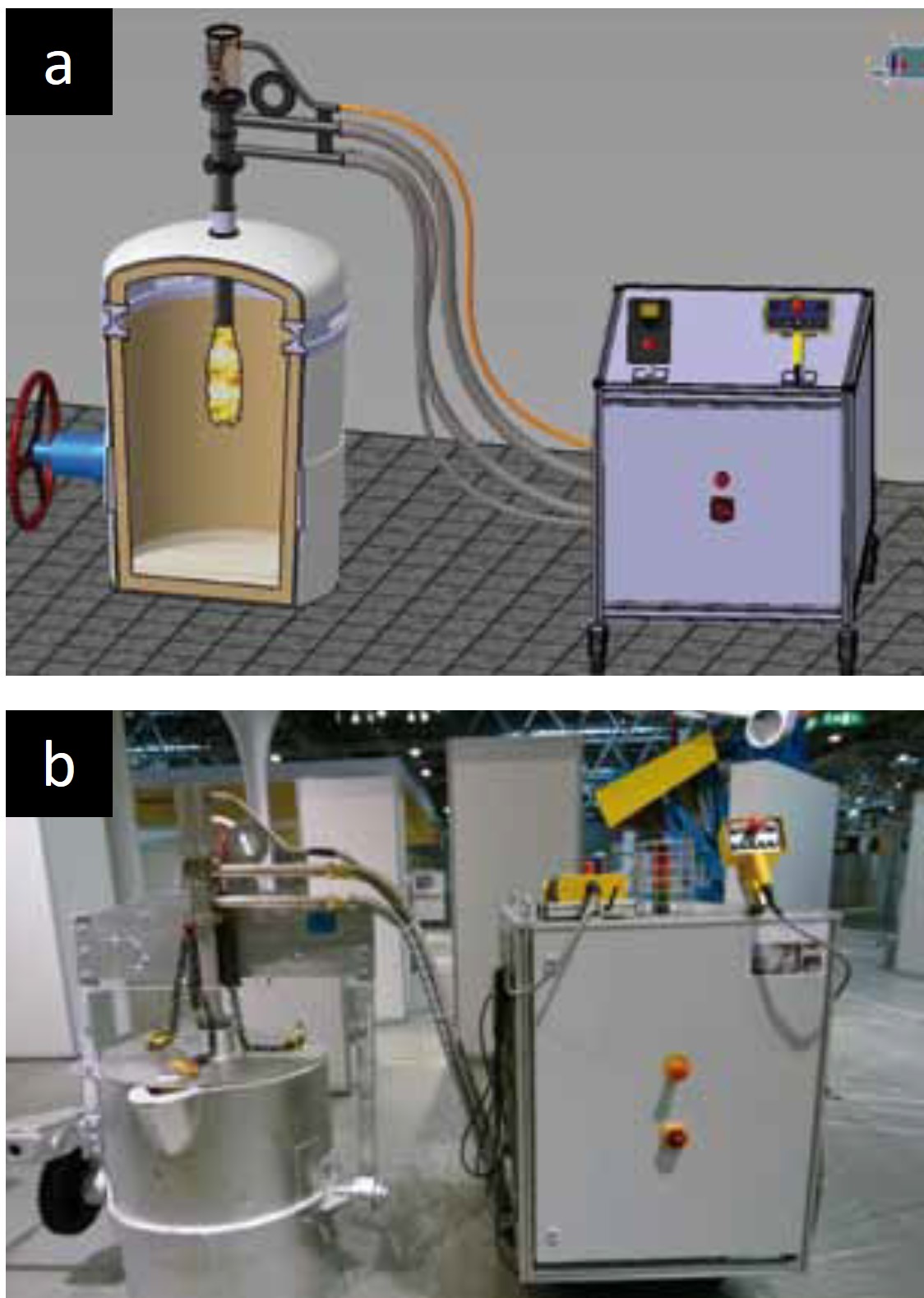
Hier kommt der Erdgas-Sauerstoff-Brenner zum Sintern von Öfen und zum Aufheizen von Pfannen zum Einsatz. Die Anlage kann für jeden Leistungsbereich ausgelegt werden und auf Wunsch unter gewissen Bedingungen auch für Fernabfragen ausgestattet werden. Eine Besonderheit sind die hohen Kosten- und Energieeinsparungen beim Sintern und Aufheizen durch die langen vorgegebenen Zeiten. Vorgabe des Kunden war es, eine 25-t-Pfanne in 3 Tagen und 4 h auf 1200 °C aufzuheizen. In diesem Fall liegt der Energieverbrauch je Pfanne durch das Sintern anfangs bei 3 m3/h Erdgas und steigt dann entsprechend der Sinterkurve bis auf 48 m3/h Erdgas an. Beim Sauerstoff liegt der Verbrauch zunächst bei 6 m3/h und steigert sich dann bis auf 96 m3/h (Bild 4).
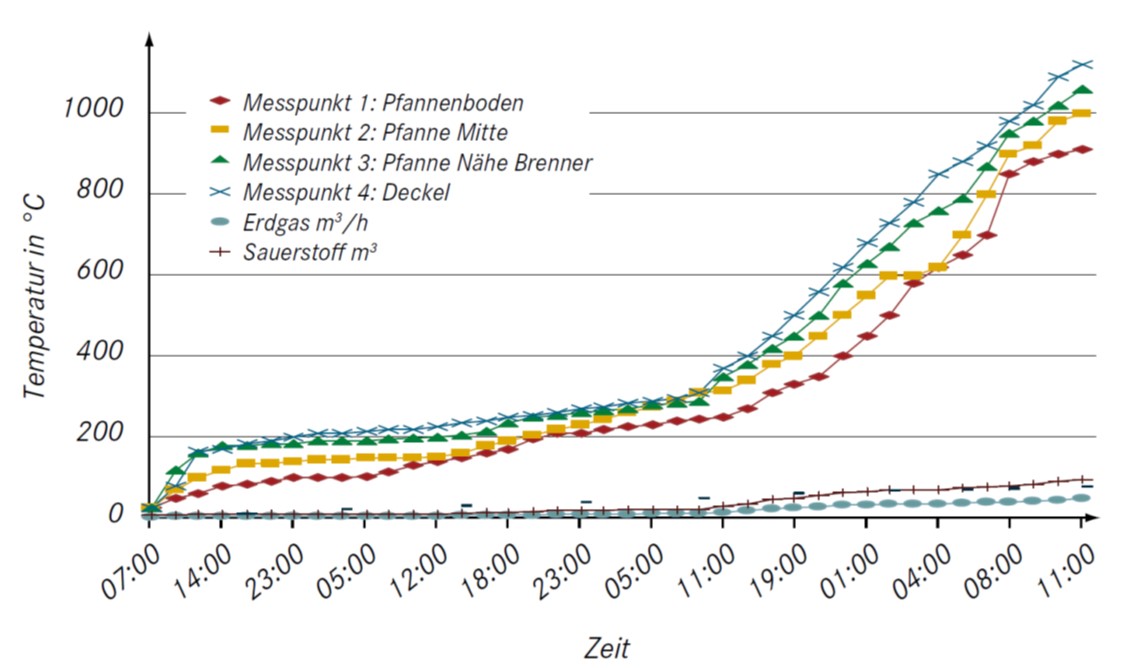
Aufheizen liegender Pfannen
25- und 80-t-Pfannen können auch liegend vor einer Wand aufgeheizt werde. Dabei wird der über eine 3-stufige Regelanlage gesteuerte Brenner in der Wand befestigt (Bild 5). Früher wurden in dieser Gießerei 25- und 50-t-Pfannen mit Erdgas-Luftbrennern aufgeheizt, sodass ein Vergleich beider Systeme bei der Energieeffizienz und der Belastung durch Abgase möglich ist. Der Oxy-Fuel-Brenner heizt die 25-t-Pfanne in ca. 3,45 h auf rund 1240 °C auf und die 80-t-Pfanne in ca. 3,5 h auf rund 1230 °C. Bei der kleineren Pfanne werden für diesen Prozess 180 m3 Erdgas und 360 m3 Sauerstoff eingesetzt, bei der größeren 438 m3 Erdgas und 876 m3 Sauerstoff. Für das Aufheizen beider Pfannen fallen also insgesamt 618 m3 Erdgas und 1236 m3 Sauerstoff an. Wenngleich die Pfannenkapazitäten, die heute und in der Vergangenheit aufgeheizt wurden, voneinander abweichen, war der Energieeinsatz des Erdgas-Luftbrenners doch deutlich höher – bei längeren Aufheizzeiten und geringeren Spitzentemperaturen: Die beiden 25- und 50-t-Pfannen wurden in 8 bis 12 h bis auf 900/950 °C aufgeheizt. Hierfür wurden 2600 m3 Erdgas und 26 000 m3 Luft benötigt. Analog zum höheren Energieverbrauch fielen früher auch deutlich mehr Emissionen in Form von CO2 und NOx an. Der Oxy-Fuel-Brenner verursacht 1854 m3 Abgase, der Erdgas-Luft-Brenner 26600 m3. Schließlich ist auch noch die niedrige Kostenbelastung durch Oxy-Fuel-Brenner zu nennen: Die Kosten für das Aufheizen der beiden Pfannen betragen heute 531 Euro, früher waren es 1352 Euro.
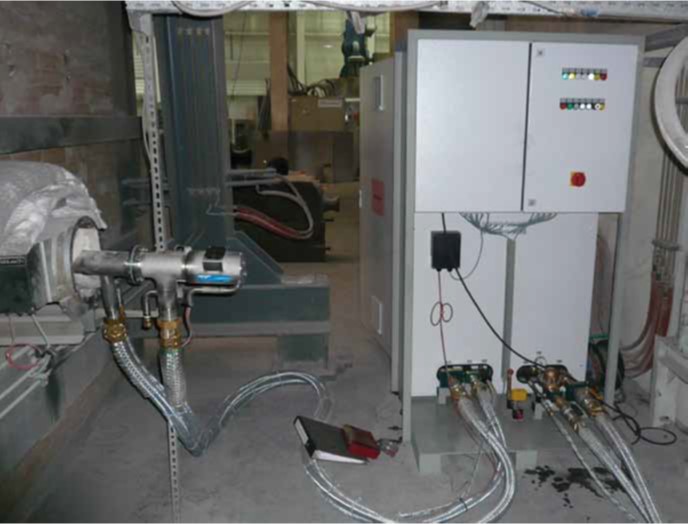
90 t-Warmhalteofen
Die Oxy-Fuel-Brenner können auch für das Sintern und Aufheizen von Warmhalteöfen, in diesem Fall mit einer Kapazität von 90 t, eingesetzt werden (Bild 6). Stellt man den Energieverbrauch von Erdgas-Luftbrennern erneut dem von Oxy-Fuel-Brennern gegenüber, treten deutliche Kostenvorteile bei letzterem zutage: Während der Erdgas-Luftbrenner bei einer Aufheizzeit von 7 Tagen 14 728 m3 Erdgas und 147 280 m3 Luft benötigt, liegt der Verbrauch beim Oxy-Fuel-Brenner nur bei ca. 6720 m3 Erdgas und ca. 13 440 m3 Sauerstoff. Dadurch sinken die Kosten mit der neuen Heizanlage um ca. 79 %, die Abgasbelastung sinkt von 162 008 m3 auf 20 160 m3.
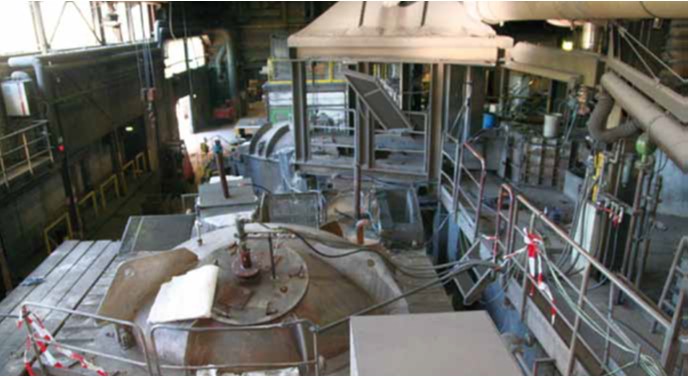
Der Glockenguss zu Halberstadt
Der Oxy-fuel-Brenner spielte auch bei einem aufsehenerregenden Ereignis am 3. September 1999 eine wichtige Rolle – dem öffentlichen Abguss der großen Glocke des Halberstädter Dom-Geläutes. Als Vorlage diente die Schilderung des Glockengusses in Friedrich Schillers Gedicht „die Glocke“ von 1799. Die sogenannte Domina wurde unter den Augen von rund 20 000 Menschen auf dem Domplatz in Halberstadt abgegossen (Bild 7). Anschließend kühlte die Glocke 4 Wochen ab. Weitere 4 Wochen dauerte es, das 8,5 t schwere Gussteil zu putzen. Die Glocke war im zweiten Weltkrieg zur Herstellung von Waffen eingeschmolzen worden. An dem historischen Ereignis in Halberstadt waren auch die beiden Brüder Fritz-Georg und Hans-Martin Rincker von der Glockenund Kunstgießerei in Sinn und Lauchhammer sowie zwei Gießereien und ein Feuerfestmassenhersteller aus der Region beteiligt.
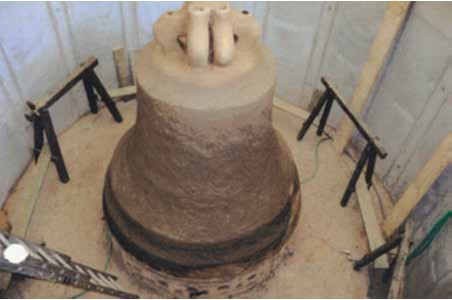
Die Domina hat einen Durchmesser von 2,26 m und einen 6 Zentner schweren Klöppel. Ziel des Projektes war es, dem Dom sein vollständiges mittelalterliches Geläut wiederzugeben, das zur Jahrtausendwende an Silvester 1999 wieder erklingen sollte. Mit dem Oxy-Fuel-Brenner wurde die große Transportpfanne nach der Zustellung in Staßfurt gesintert. Anschließend wurde die Pfanne in Blankenburg für die Schmelze bis auf ca. 1350°C aufgeheizt und dann – gefüllt mit flüssiger Bronze – per Lkw nach Halberstadt gebracht. Vor dem Abguss der Glocke wurden auch die Gießrinnen mit Oxy-Fuel-Brennern auf Temperatur gebracht (Bild S. XXX). Ohne Einsatz des Brenners wäre es schwierig gewesen, Pfanne und Rinnen aufzuheizen oder warmzuhalten. Die Alternative wäre ein Holzofen zur Herstellung der Schmelze gewesen - was im Vergleich zum Oxy-Fuel-Brenner eine deutlich höhere Umweltbelastung zur Folge gehabt hätte.
Josef Weschenbach, Gründer des Josef Weschenbach Ingenieurbüros, Bielefeld