Kostenersparnis durch energieeffiziente Abluftfiltersysteme
Von Parisa Javadian Namin, Königswinter
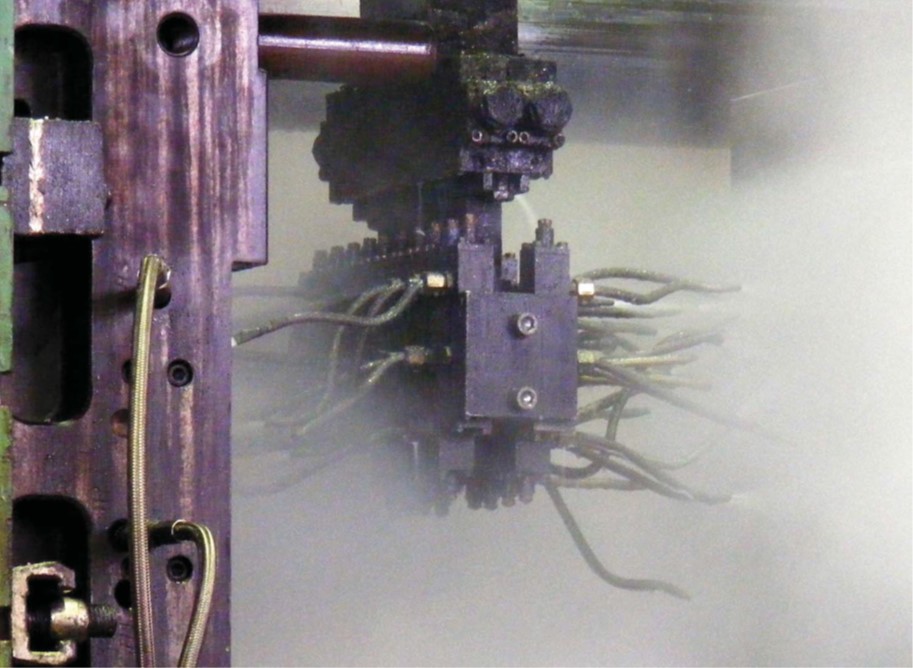
Formsprühen beim Druckguss – Rauch und Nebel machen eine Abluftfiltration zwingend erforderlich.
Erschienen in GIESSEREI 11/2012
Die Steigerung der Energieeffizienz ist in vielen Branchen zu einer Managementaufgabe höchster Priorität aufgestiegen. Denn gerade in energieintensiven Produktionsprozessen bestehen häufig erhebliche Einsparpotentiale, die entscheidende Auswirkungen auf die Wettbewerbsfähigkeit des Unternehmens haben können. Das gilt insbesondere auch in Gießereien, denn die Energiekosten bilden hier stets einen hohen Anteil an den Gesamtkosten der Produktion. Neben dem Energieeinsatz zum Schmelzen und Gießen des Metalls fällt an zweiter Stelle der Energieverbauch für Abluft- und Zuluftanlagen ins Gewicht. Hier kann der Einsatz energieeffizienter Abluftfiltersysteme die Energiekosten und damit den CO2-Ausstoß erheblich senken und so gleichermaßen für eine Verbesserung des Unternehmenserfolgs wie auch des Carbon Footprint sorgen.
Reine Luft am Arbeitsplatz ist in modernen Produktionsbetrieben ein Muss. Produkt-, Arbeitsplatzqualität und Zertifizierungsanforderungen machen Maßnahmen zur Luftreinhaltung zwingend erforderlich. Die an Gießereimaschinen erzeugte Abluft setzt sich aus öligen und häufig auch pastösen Rauch- und Aerosolsubstanzen zusammen. Beim Dauereinsatz der Maschinen entstehen hohe Rauchbelastungen, die abgeschieden werden müssen. Dabei ist auch heute noch die konventionelle Abluftführung ins Freie weit verbreitet. Hier wird die belastete Abluft mittels Ablufthauben erfasst und (häufig ungefiltert) nach draußen transportiert. Das schafft zwar reine Luft in der Halle, bedeutet jedoch einen Abtransport der Luftschadstoffe ins Freie. Hinzu kommt, dass die einfache Beförderung der Abluft nach außen in den kalten Wintermonaten hohe Folgekosten nach sich zieht, denn die ins Freie transportierte Luft muss zwingend durch die gleiche Menge an frischer Außenluft ersetzt werden. Die Erwärmung der kalten Außenluft auf Raumtemperatur führt zu immensen Betriebskosten für das Unternehmen und belastet die Umwelt durch einen hohen Ausstoß an CO2. Die KMA Umwelttechnik GmbH aus Königswinter ist seit langem auf energiesparende Methoden zur Abluftbehandlung spezialisiert und ermöglicht durch innovative Filtertechnik kostensparende Alternativen zur konventionellen Ablufttechnik. Das derzeit energieeffizienteste Verfahren der Abluftbehandlung ist der Umluftbetrieb. Hierbei wird durch den Einsatz leistungsstarker Filtertechnik eine so hohe Reinluftqualität ermöglicht, dass die gefilterte Abluft am Filterausgang wieder zurück in den Arbeitsbereich geführt werden kann. Das heißt, die Luft zirkuliert in der Halle und weist damit keine Wärmeverluste durch Abluft auf. Dementsprechend ist bei dieser Methode das größte Energieeinsparpotential vorhanden. Bei neuen Gießereien findet dieses Verfahren daher vielfach Anwendung. Dennoch besteht auch bei modernen Gießereien häufig der Bedarf nach einem Abluftbetrieb, denn bestimmte Produktionsverfahren oder auch die Unternehmensphilosophie im Allgemeinen können einen permanenten Austausch von Abluft mit frischer Außenluft erforderlich machen. KMA Umwelttechnik hat für diese Einsatzfälle ein energieeffizientes Abluftfiltersystem entwickelt, das dem Gießereibetrieb erlaubt, etwa 85 % seiner im Abluftbetrieb verlorenen Energiekosten wiederzugewinnen (Bild 1). Es handelt sich hierbei um die Kombination von bewährter Abluftfiltertechnik des Unternehmens mit einem neuen integrierten Wärmerückgewinnungssystem, bestehend aus Wärmetauscher und hocheffizienter Abluftwärmepumpe.
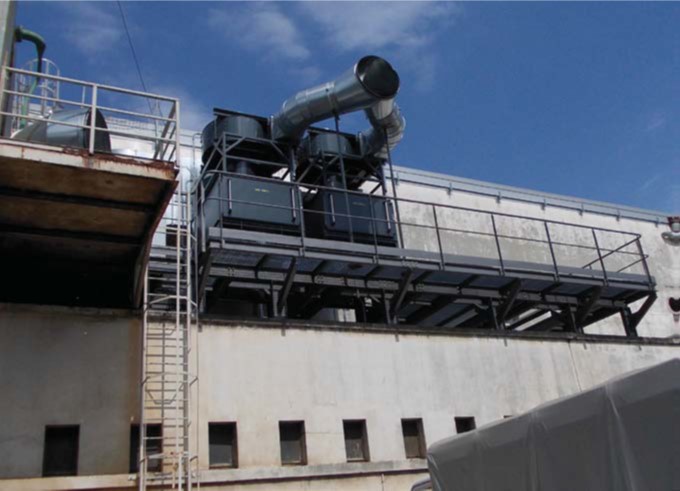
Anhand eines Fallbeispiels soll nachfolgend die Auswirkung eines derartigen Systems näher erläutert werden. Angenommen wird eine Gießerei mit Sitz in Süddeutschland mit 10 Druckgießmaschinen von jeweils 1100 t Kapazität, die zusammen eine Abluftmenge von etwa 80 000 m3/h erzeugen. Am Abluftausgang beträgt die durchschnittliche Ablufttemperatur 25 °C. Die mittlere Hallentemperatur wird für die Wintermonate mit 18 °C angesetzt. In Süddeutschland wird von einer sechsmonatigen Heizperiode (Anfang Oktober bis Ende März) ausgegangen. Basierend auf diesen Daten ergibt sich in 25 Wochen im Jahr eine durchschnittliche Außenlufttemperatur von etwa 2,9 °C (Quelle: Klimakarte Nürnberg). Das bedeutet, dass an 3600 h im Jahr eine Beheizung der Außenluft (ΔT = 15,1 °C) erfolgen muss, damit die Luft mit 18 °C in die Halle geführt werden kann. Die Beispielgießerei hat nun 3 Konzepte zur Auswahl:
Das erste Konzept ist der konventionelle Abluftbetrieb, bei dem die Abluft durch angepasste Hauben über den Maschinen abgesaugt und mittels eines einfachen Demisters gefiltert und anschließend durch einen Ventilator ins Freie getragen wird. Demisterfilter bestehen aus Drahtgeflechten, die grobe Partikel sowie Tröpfchen aus der Abluft filtern. Der Energieverbrauch bei diesem Konzept setzt sich aus dem Stromverbrauch der Ventilatoren im Abund Zuluftbereich sowie dem Energieverbrauch der Heizungsanlage zusammen. Bei einem Gaspreis von 0,50 Euro/m3 und einem Strompreis von 15,5 Cent/kWh ergeben sich in unserer fiktiven Gießerei während der Heizperiode Betriebskosten in Höhe von 152 000 Euro, verbunden mit einem durch Lüftung bedingten CO2-Ausstoß von 592 t.
Beim zweiten Konzept wird die Absauganlage um ein hocheffizientes Filtersystem mit integriertem Wärmetauscher erweitert (Bild 2). Das Filtersystem setzt sich aus Demister und Elektrofilter zusammen. Der Elektrofilter ist in diesem Fall von großer Bedeutung, da er die hochgradige Abscheidung von öligen und fettigen Emissionen
wie Rauch, Staub und Nebel erlaubt. Diese Filtermethode erhöht gegenüber der vorher beschriebenen Demisterfilteranlage nicht nur deutlich die Reinheit der gefilterten Luft, sondern sichert auch den Wirkungsgrad des Wärmetauschers dauerhaft. Mithilfe des Wärmetauschers wird der warmen Abluft die Energie entzogen und durch einen Direktverbund auf die einströmende Außenluft übertragen. Der Wirkungsgrad bei diesem Direktverbund beträgt über die Heizperiode im Mittel etwa 40 %. In der Beispielgießerei bedeutet das eine Energierückgewinnung von durchschnittlich 173,6 kW/h und etwa 625 000 kW während einer Heizperiode. Durch den reduzierten Gasverbrauch entspricht das einer jährlichen Energieeinsparung von über 73 000 m3 Gas. Zieht man den Energieeigenverbrauch der Wärmerückgewinnungsanlage (Umwälzpumpe) von der eingesparten Energiemenge ab, so ergibt das eine Reduzierung der Betriebskosten um fast 36 000 Euro und eine Senkung der CO2-Emissionen um über 141 t im Jahr. Die Amortisationszeit für die Investition dieser Anlage beträgt etwa 2 Jahre.
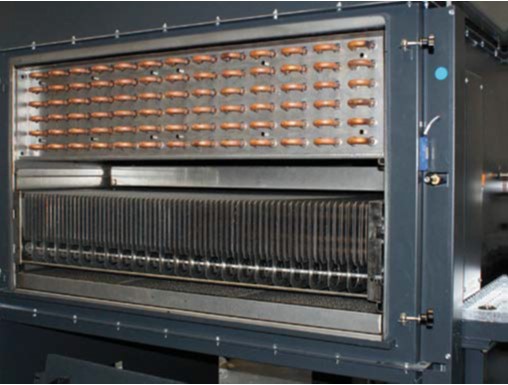
Obwohl das zweite Konzept bereits eine wirksame Möglichkeit zur Verbesserung der ökologischen und wirtschaftlichen Kennzahlen bietet, hat KMA Umwelttechnik das Konzept noch durch eine hocheffiziente Wärmepumpe erweitert (Bild 3). Abluftwärmepumpen beziehen ihre Energie aus der auch an kalten Tagen stets relativ warmen Hallenabluft. Daher erzielt dieses Prinzip extrem hohe Leistungszahlen von über 6 (d. h. aus 1 kW elektrischem Strom werden 6 kW thermische Energie gewonnen).
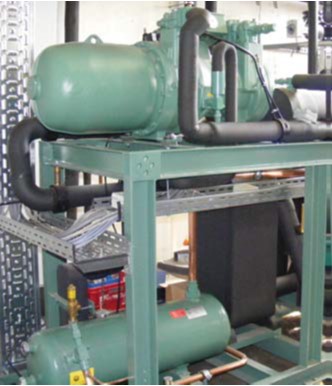
Wärmepumpe können etwa 85 % der im Abluftbetrieb verlorenen Energiekosten wiedergewonnen werden.
Eine derartige Anlage ist deutlich wirtschaftlicher als vergleichbare Heizsysteme und ermöglicht eine direkte Energieübertragung an die zu erwärmende Zuluft. Angelehnt an die hohe Leistungszahl und einem Wirkungsgrad von 85 % gewinnt die Gießerei bei Einsatz einer KMA-Abluftfilteranlage mit integriertem Wärmetauscher und Wärmepumpe fast doppelt so viel Energie zurück wie mit einem einfachen Wärmetauscher (Bild 4). Das entspricht einer Energierückgewinnung von etwa 370 kW in der Stunde (~1 332 000 kW im Jahr) und damit einer jährlichen Energieeinsparung von 185 000 m3 Gas. Bei Abzug des Energieeigenverbrauchs der Anlage summiert sich die jährliche Ersparnis auf über 53 000 Euro. Damit einhergehend reduziert sich der CO2-Ausstoß um über 225 t im Jahr. Bei diesem dritten Modell rentiert sich die Investition nach einer Amortisationszeit von etwa 3 Jahren.
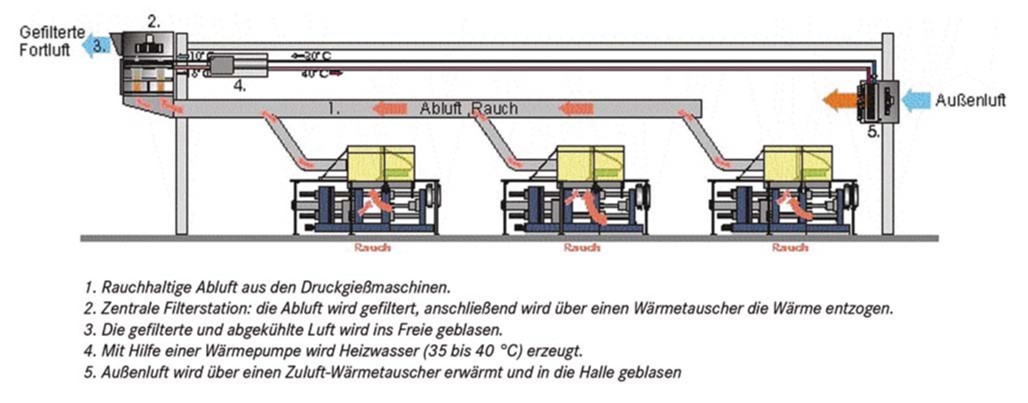
Wie das Fallbeispiel verdeutlicht, ist ein Umdenken bezüglich energieeffizienter Abluftfiltersysteme in Gießereien für das Unternehmen lohnenswert. Es zeigt auf, dass Umweltverträglichkeit und Wirtschaftlichkeit keine Gegensätze bilden, sondern sich bei Auswahl der passenden Technik sogar gegenseitig ergänzen und verstärken. Die Investition in ein energieeffizientes Abluftsystem rentiert sich schon nach kurzer Zeit. Sie verschafft der Gießerei erhebliche Einsparungen und damit Wettbewerbsvorteile und verbessert den ökologischen Fußabdruck des Unternehmens durch erhebliche Reduzierungen des CO2-Ausstoßes (Bild 5).
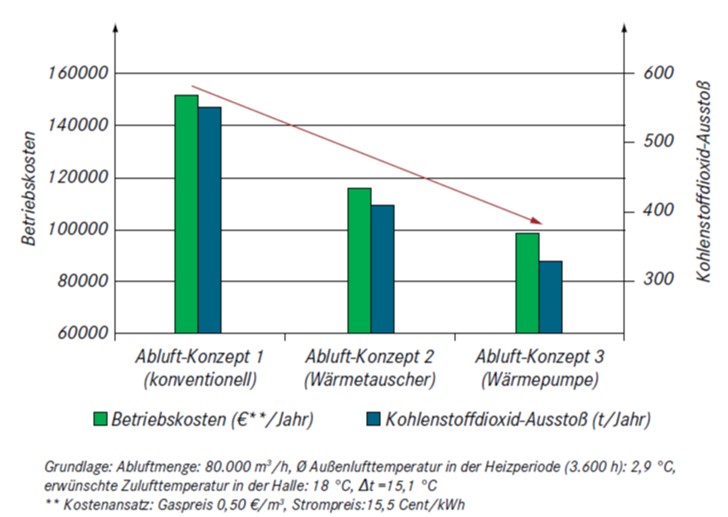