Innovatives Technologie- und Anlagenkonzept für eine nachhaltige Prozessgestaltung in Gießereien
Von: Stefan Scharf, Marc Kujath, Bastian Sander, Holger Seidel, Eric Riedel, Wolfgang König, Chris Michealis, Magdeburg, Jochen Volkert, Jörg tom Felde, Nürnberg und Norbert Stein, Hagen Stein, Bad Langensalza
Erschienen in GIESSEREI 01/2019
Mit Blick auf das gesteigerte Bewusstsein für planetare Grenzen und die Verantwortung für die Lebensgrundlagen kommender Generationen gilt es heute mehr denn je, anforderungsgerechte Prozesse und Lösungen zu entwickeln, die sich durch einen ressourcenschonenden Materialeinsatz sowie eine effiziente Nutzung der zur Verfügung stehenden Energieträger auszeichnen. Zusätzlich gewinnt die Frage nach einer nachhaltigen Produktion auch aus ökonomischer Sicht zunehmend an Bedeutung. Gerade im Bereich der energieintensiven Gießerei-Industrie sind sowohl technologische Innovationen als auch eine fortlaufende Optimierung der bestehenden Prozessabläufe unerlässlich, um die Wettbewerbsfähigkeit insbesondere von klein- und mittelständischen Unternehmen (KMU) auch künftig zu sichern. Mit dem vorgestellten Forschungsvorhaben „Entwicklung neuartiger Technologien, Anlagenkomponenten und Logistik zu einer energieeffizienten Fertigung in Leichtmetall-Gießereien“ (ETAL) verfolgen die Projektpartner das Ziel, basierend auf sowohl konzeptionellen als auch technologischen Innovationen, den erforderlichen Primärenergieeinsatz und damit auch die emittierten Schadstoffe in der Prozesskette der Leichtmetallgusserzeugung signifikant zu reduzieren. Gleichzeitig werden die Gussqualität und die Fertigungsflexibilität deutlich erhöht. Das entwickelte Konzept zur dezentralen Schmelzeversorgung in NE-Gießereien ermöglicht eine komplette Reorganisation der Materialflüsse. Dadurch werden der Primär-Energieeinsatz sowie die emittierten Schadstoffe signifikant reduziert und gleichzeitig die Gussqualität sowie die Fertigungsflexibilität deutlich erhöht. Möglich wird dies durch den Einsatz neuartiger Heiz-Dockingstationen („heat dock“) und mobiler Tiegelpfannen („mpot“) sowie durch eine innovative Brennertechnologie, die anfallende Abwärme thermisch wiederverwerten kann.
1 Einleitung
Die Fragestellung nach einer energieeffizienten und nachhaltigen Fertigung ist für die künftige Wettbewerbsfähigkeit von klein- und mittelständischen Unternehmen der metallverarbeitenden Industrie von elementarer Bedeutung. Dies gilt insbesondere am Standort Deutschland, einem der weltweiten Vorreiter in Hinblick auf die energieeffiziente und umweltschonende, gleichzeitig aber auch kostenintensive Nutzung erneuerbarer Energiequellen. Vor dem Hintergrund der global stetig steigenden Energiepreise sowie drohender Strafzahlungen für die Emission von Schadstoffen, gleichwohl aber auch vor dem Hintergrund einer scheinbar unaufhaltsam zunehmenden Erderwärmung und einem wachsenden ökologischen Verantwortungsbewusstsein, gilt es heutzutage daher mehr denn je, anforderungsgerechte Lösungen zu entwickeln, die einen ressourcenschonenden Materialeinsatz sowie eine nachhaltige Nutzung der zur Verfügung stehenden Energieträger ermöglichen und dabei die Summe der klimaschädigenden Schadstoffemissionen (insbesondere CO2) auf ein Minimum reduzieren. Politische Restriktionen, sowohl global als auch auf Bundesebene, verknüpfen dabei bewusst ökologische und ökonomische Aspekte, um die avisierten Zielstellungen zu erreichen. In diesem Kontext bekommt der Produktionsfaktor Energie auch aus wirtschaftlicher Sicht eine immer bedeutsamere Rolle.
Jährlich werden in deutschen Gießereien über 5 Mio. t (1,67 Mio. t NE-Guss) hochwertiger Bauteile und Komponenten hergestellt. Offiziellen Auswertungen des Statistischen Bundesamtes zufolge fallen dabei Energiekosten an, die inzwischen ca. 25 % der Bruttowertschöpfung (13 Mrd. € / a) entsprechen. Allein die NE-Gusserzeugung verursacht dabei ca. 1,01 Mio. t CO2 / a [1].
In diesem Kontext zeigt Bild 1 die typische Prozesskette der am Produktionsstandort Deutschland stark forcierten Aluminiumgusserzeugung sowie das (vorläufige) Ergebnis durchgeführter Verbrauchserfassungen beim Projektpartner, der Leichtmetallgießerei Bad Langensalza GmbH (LGL), zur Ermittlung der prozessbezogenen Energiebedarfe. Bei der Auswertung der prozentualen Energieverteilung wird schnell ersichtlich, dass eine Effizienzsteigerung innerhalb einer Gießerei vorrangig über eine nachhaltige Gestaltung der einzelnen Prozessschritte zur Metallbereitstellung zu realisieren ist.
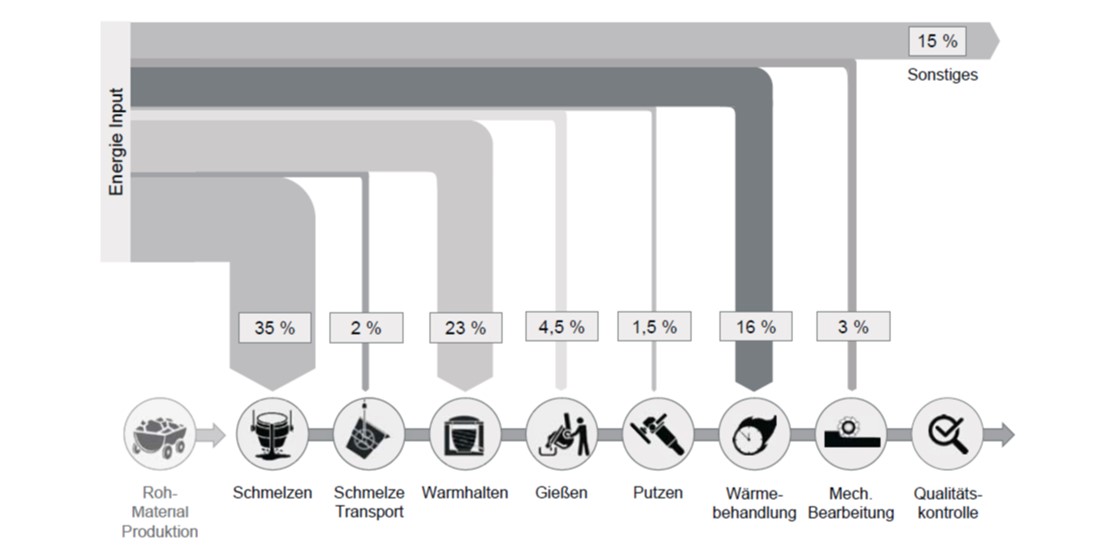
2 Stand der Technik
2.1 Energiequelle
Gemäß aktuellen Erhebungen hinsichtlich der in der deutschen Gießereiindustrie eingesetzten Energieträger für die primär benötigte Wärmebereitstellung beträgt der Anteil des Energieträgers Strom in den NE-Gießereien, die zurzeit mit 336 von 610 Betrieben den Großteil der Branche darstellenden, ca. 50 %. Die restliche benötigte Wärmeenergie wird weitestgehend durch gasbeheizte (offenflammige) Brennersysteme erzeugt. Bezogen auf die besonders energieintensiven Prozessschritte zur Metallbereitstellung (Schmelz- und Warmhaltebetrieb) lässt sich der IST-Stand am Standort Deutschland aktuell derart charakterisieren, dass in hier fokussierten NE-Gießereien der Schmelzbetrieb zu etwa gleichen Teilen durch gas- oder strombeheizte Ofenkonzepte realisiert wird, wohingegen der Warmhaltebetrieb nahezu ausschließlich durch strombasierte Ofenanlagen erfolgt [2], [3].
Vergleicht man jedoch die zur Wärmebereitstellung eingesetzten Energieträger Gas und Strom, so sind bezogen auf eine kWh Energie sowohl die anfallenden Bezugskosten als auch die emittierten CO2-Äquivalente (Hochrechnung auf Basis des aktuellen deutschen Strommixes) bei Gas deutlich vorteilhafter (Bild 2), [4], [5], [6]. Dass zum gegenwärtigen Stand dennoch zu einem Großteil elektrische Beheizungslösungen zur Anwendung kommen, begründet sich in der Tatsache, dass die bisher bekannten offenflammigen Brennersysteme entscheidende Nachteile sowohl im Hinblick auf die Temperaturregelbarkeit als auch auf die erzielbare Temperaturhomogenität aufweisen. Die resultierenden lokalen Überhitzungen lassen sich deshalb momentan nur in großen Anlagen als adäquat nutzbar einschätzen. Darüber hinaus beschränkt sich der Einsatz von brennstoffbeheizten Industrielösungen momentan im Wesentlichen auf Öfen für den Schmelzprozess.
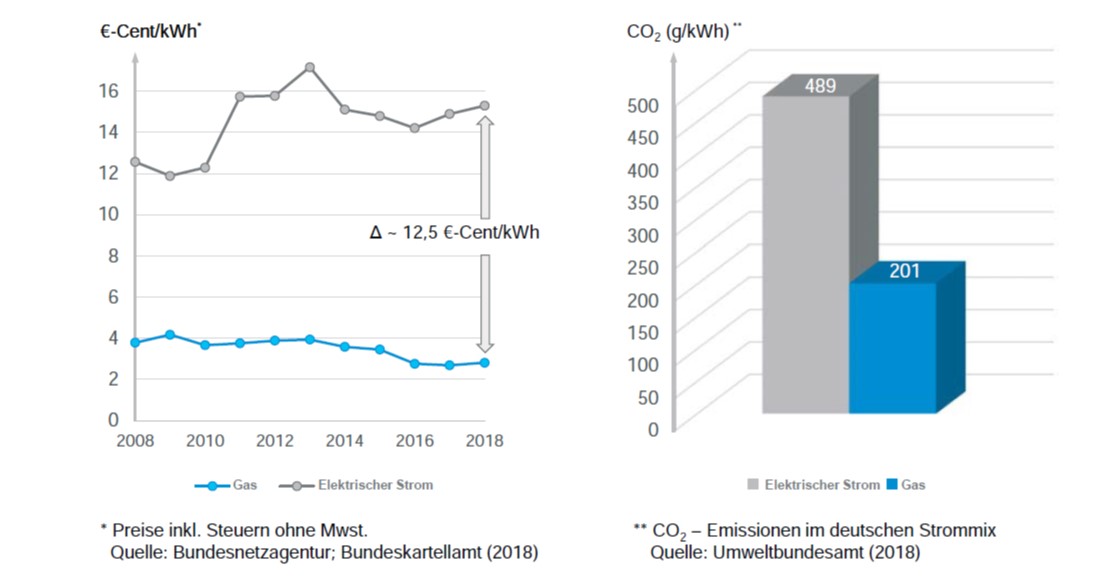
Für den Einsatzbereich Warmhalten kommen gemäß aktuellen Erhebungen des Bundesverbandes der Deutschen Gießerei-Industrie (BDG) [7] lediglich bei sehr großen Ofenvolumina, und auch hier nur vereinzelt 2-stufige oder modulierende Kaltluftbrenner bzw. Mantelrohr- oder Rekuperator-Warmluftbrenner, zur Anwendung. Einem Einsatz von durch Vorwärmung der Verbrennungsluft effizienteren Brennern in KMU-typischen Ofengrößen steht der erhöhte, kaum zu skalierende gerätetechnische Aufwand sowie die notwendige hohe und gleichmäßige Auslastung (dies gilt insbesondere auch für moderne Flox-Brenner) entgegen, die für einen effektiven Betrieb bzw. Wirkungsgrad erforderlich sind. Deshalb werden diese Ofenanlagen zumeist bequem und einfach elektrisch beheizt. Alternativ kommen Öfen zum Einsatz, die mit günstigen, jedoch sehr ineffizienten Gasbrennern ausgestattet sind. Flammenfreie Vormisch-Brenner (z.B. Porenbrenner) weisen diese Nachteile nicht auf und haben sich inzwischen als bessere Alternative. Vor allem in kleineren Schmelz- und Warmhalteöfen, etabliert [8]. Gleichwohl können letztere aber, anders als offenflammige Brenner, bisher nicht mit vorgewärmter Verbrennungsluft betrieben werden. Die gezielte Wiederverwertung von Abwärme in Form vorgewärmter Verbrennungsluft in flammenfreien Brennern stellt daher ein zentrales Entwicklungsziel des vorgestellten Projektes dar, um eine noch wirtschaftlichere gasbasierte Wärmebereitstellung auch in KMUtypischen Anlagengrößen zu ermöglichen und entsprechend die Grundlage eines insgesamt revolutionären Prozess- und Anlagenkonzeptes zu schaffen.
2.2 Prozessführung
Die zum gegenwärtigen Zeitpunkt in deutschen KMUs vorherrschende konventionelle Prozessgestaltung der Leichtmetallgusserzeugung lässt sich, wie schematisch auch in Bild 3 dargestellt, in folgende Prozessschritte untergliedern:
- Stationär Metall schmelzen und in eine (hoffentlich) vorgewärmte Transportpfanne umgießen,
- Transport der Schmelze und Umgießen in einen stationären Warmhalteofen,
- Schöpfen aus dem Warmhalteofen und Gießen des zu erzeugenden Bauteils.
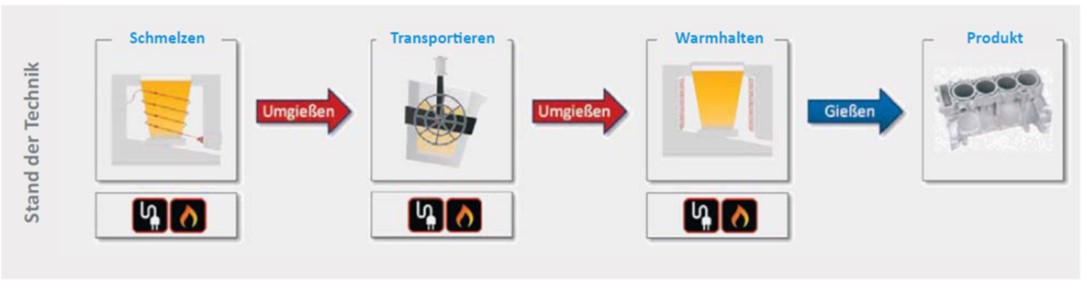
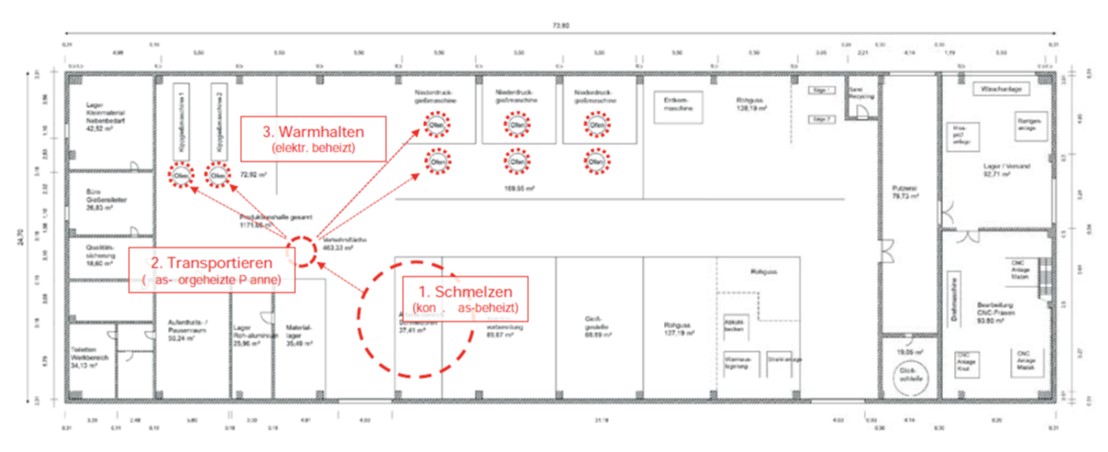
Neben dem hohen energetischen Aufwand durch eine individuelle Beheizung an jedem einzelnen Prozessschritt und die zwangsweise Überhitzung der Schmelze zur Kompensation der mit jedem Umfüllvorgang einhergehenden Wärmeverluste wirkt sich die aktuell verfolgte Prozessführung jedoch auch, insbesondere aufgrund der erforderlichen Umschöpfprozesse und dem damit einhergehenden Einbringen von Oxiden und Porosität in die Schmelze, nachteilig auf die Qualität der erzeugten Gussteile aus. Um die geforderten Qualitäten dennoch erzielen zu können, muss die zu vergießende Schmelze während des Warmhalteprozesses arbeits- und energieintensiv aufbereitet werden. Bei weiterer Betrachtung der für eine KMU-Leichtmetallgießerei typischen Anordnung der Produktionsanlagen beim Verbundpartner LGL fällt ferner die räumlich zentrale Schmelzeversorgung (hier zwei gasbeheizte Schmelzöfen) ins Auge (Bild 4), die über kranbahnverfahrene, separat vorzuwärmende Transportpfannen insgesamt 8 elektrisch widerstandsbeheizte Warmhalteöfen versorgt. Erst hier werden die schmelzflüssigen Al-Legierungen produktspezifisch in die wertschöpfenden Kokillen vergossen.
Aus materialflusstechnischer Sicht ist dieser einem „PUSH-System“ zuzuordnende Produktionsablauf als denkbar ungünstig zu bewerten. Die Schmelzöfen schränken nicht nur die legierungsspezifische Variabilität und somit das realisierbare Bauteilspektrum stark ein, sondern stellen auch, speziell in Verbindung mit dem zum Transport benötigten Hallenkran, die produktionsbestimmende Engstelle der Wertschöpfung dar. Um an den Gießplätzen dennoch bedarfsgerecht produzieren zu können, sind individuell beheizte Warmhalteöfen als Materialpuffer zwingend notwendig. Neben der hohen Energieintensität zur aktiven Beheizung dieser Vielzahl an relevanten Komponenten (Schmelzofen, Vorwärmstation, Warmhalteofen) ergeben sich aufgrund der fehlenden energetischen Flexibilität lange, nicht wertschöpfende und dennoch energieintensive Prozesszeiten.
2.3 Prozessüberwachung
Nicht zuletzt ist auch dem Punkt einer effektiven Prozessüberwachung besonderes Augenmerk zu schenken, um eine nachhaltige und dabei hochwertige Produktion zu gewährleisten. Bei der Erzeugung von qualitativ hochwertigem Guss kann in diesem Kontext insbesondere eine durchgehend stabile und homogene Fahrweise der einzelnen (Hochtemperatur-) Prozessschritte entlang der Fertigungskette als essenziell herausgehoben werden. Beginnend bei einer exakten Temperaturführung im Schmelzofen, entscheiden neben einer möglichst homogenen Vorwärmung und Temperierung der Transportpfannen vor allem auch eine möglichst gleichmäßige Temperierung der Schmelze in den Warmhalteöfen in erheblichem Maße über die Qualität der hergestellten Gussteile. Aufgrund der relativ niedrigen Schmelztemperaturen sowie der hohen Legierungsvielfalt, nicht zuletzt aber auch aufgrund der stetig zunehmenden Qualitätsanforderungen, sind die tolerierbaren Prozessfenster im Bereich der Aluminiumgusserzeugung dabei als besonders eng zu charakterisieren.
Obwohl aus einer Vielzahl wissenschaftlicher Abhandlungen (z.B. [9], [10], [11], [12]) hinreichend bekannt ist, dass eine ungenaue Temperaturführung sowohl in Schmelz- als auch in Warmhalteöfen zu einem signifikanten Abfall der Schmelzequalität führen, wird die Schmelzetemperatur im betrieblichen Produktionsablauf vor allem in kleinen und mittleren Betriebsgrößen vielfach nur rudimentär, meist mittels Thermoelementen oder unter mobiler Infrarot-Wärmemessgeräte, ermittelt. Während diese Fehlerquellen in den zu großen Teilen automatisierten Gießanlagen der massenproduzierenden OEM- und OEM-nahen Gießwerke durch entsprechend aufwendig ermittelte Prozesstaktungen weitestgehend auf ein Minimum reduziert werden können, bereiten sie KMU-typischen Betrieben speziell vor dem Hintergrund steigender Qualitätsanforderungen und immer komplizierter werdender, dünnwandiger Gussgeometrien zunehmend Probleme.
3 Entwickelte Technologielösungen
Im Sinne der beabsichtigten und dringend erforderlichen Effizienzsteigerung verfolgt das vorliegende Forschungsvorhaben ETAL das Ziel, über die gesamte Prozesskette der Leichtmetallgusserzeugung hinweg den erforderlichen Primärenergieeinsatz und damit auch die emittierten Schadstoffe signifikant zu reduzieren und gleichzeitig sowohl Gussqualität als auch Fertigungsflexibilität deutlich zu erhöhen. Dies entspricht letztlich einer Reduktion des spezifischen Energieeinsatzes und hilft somit sowohl die Fertigungskosten zu senken als auch die Umwelt zu schonen. Dabei beinhaltet das zwischen der promeos GmbH, Nürnberg, der LGL Leichtmetallgießerei Bad Langensalza GmbH, dem Bereich Ur- und Umformtechnik am Institut für Fertigungstechnik und Qualitätssicherung der Otto-von-Guericke-Universität Magdeburg (OVGU) sowie dem Fraunhofer-Institut für Fabrikbetrieb und -automatisierung Magdeburg (IFF) konzipierte Projekt gleich mehrere als revolutionär einzustufende
Technologieentwicklungen.
3.1 Innovative modulare Brennertechnologie
Zunächst ist hier das Herzstück der Anlage, ein vollkommen neu entwickeltes gasbasiertes, modulares Brennerkonzept zu nennen. Im Gegensatz zu bisher bekannten Lösungen ermöglicht dieses erstmalig, den günstigen und ökologisch sinnvollen Energieträger Gas in elektrischer Regelgüte zur Erzeugung der benötigten Wärme zu nutzen und dabei vorgewärmte Luft sicher und exakt kontrollierbar zu verarbeiten. Somit wird künftig die prozessintern anfallende Abwärme zielführend wiederverwertet werden können.
Vollvormischende Brenner der Firma promeos arbeiten bisher als Kaltluftbrenner und zeichnen sich durch die Abstinenz raumgreifender Diffusionsflammen aus. Die flächige und flammenfreie Verbrennung des Gas-Luft-Gemisches erlaubt es, Wärme als homogene IR-Strahlung und mit gleichmäßiger Konvektion zur Verfügung zu stellen. Aufgrund folgender Merkmale vereinen promeos-Brenner auch bisher schon die ökonomischen und ökologischen Vorteile des Energieträgers Gas mit der Prozess- und Regelgüte elektrischer Heizelemente:
- Keine Hot-Spots, weil keine freien Flammen,
- Stufenlose Regelbarkeit der Wärmeleistung,
- Beliebige geometrische Anpassung der Brennergeometrie durch modularen Aufbau,
- Beliebige modulare Skalierung der Brennerleistung durch modularen Aufbau,
- Hohe Leistungsdichte von bis zu 4 MW/m2.
Die Erweiterung dieser Attribute um den Effekt der direkten Abwärmenutzung durch Vorwärmung der Verbrennungsluft ist zentraler Gegenstand des hier entwickelten Brennerkonzeptes.
Aufgrund der Zündbedingungen der industriell verwendeten Brenngase (Erd- und Flüssiggase) ist eine Vollvormischung von Luft hoher Temperatur mit Brenngas ausgeschlossen. Um dennoch die oben genannten Vorteile auch mit vorgewärmter Luft hoher Temperatur realisieren zu können, entwickelte promeos das Konzept eines multi-zellularen Flächenbrenners, welcher durch Parallelschaltung einzelner Verbrennungszellen mit dezentraler Gemischaufbereitung die Realisierung beliebig 2-D-skalierbarer Brennermodule für Hochtemperaturprozesse erlaubt. Wichtige Entwicklungsinhalte umfassen dabei die sichere, modulare Medienversorgung der einzelnen Brenner-Zellen sowie die Materialauswahl und -verarbeitung der 3-D-strukturierten Brennerzellen selbst. Ermöglicht wird diese Verfahrensentwicklung u.a. durch moderne Simulationstechniken sowie den Einsatz generativer Fertigungsverfahren. Bild 5 zeigt den ersten Prototypen des neuartigen Brennerkonzeptes. Die Abmessungen und Flächenleistungsdichten entsprechen denen aller bisherigen flammenfreien Brenner von promeos, was u.a. eine Erweiterung der bisherigen Kaltluftsysteme um die Luftvorwärmung erlauben wird. Es ist geplant, in einem ersten Entwicklungsschritt Verbrennungslufttemperaturen von bis zu 500 °C sicher verwerten zu können.
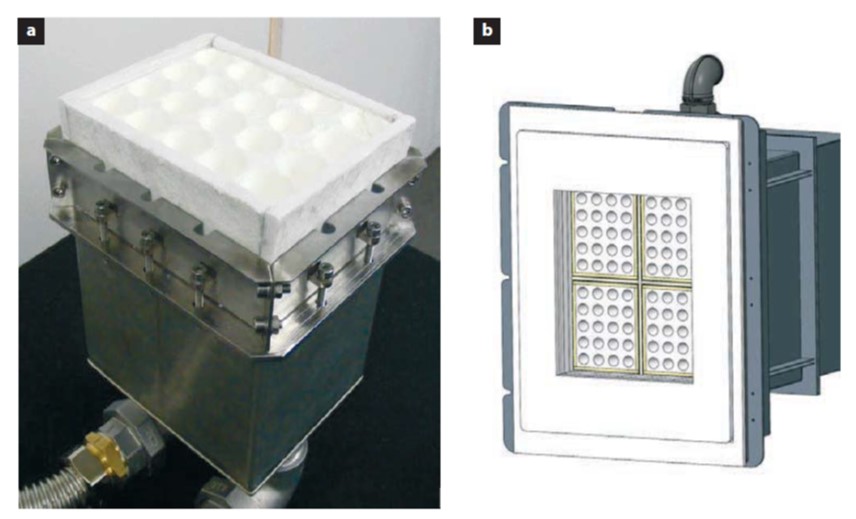
3.2 Revolutionäres Prozess- und Anlagenkonzept
Diese Brennerentwicklung wiederum stellt die grundlegende Voraussetzung für ein erfolgreiches Gelingen des Prozessund Anlagenkonzeptes dar, das den konventionell üblichen Prozessablauf künftig massiv verkürzt und erheblich vereinfacht. Das Metall wird künftig in vollkommen mobilen Tiegelpfannen, sog. „mpots“ (Bild 6), eingeschmolzen, transportiert und warmgehalten, wodurch die qualitätsbeeinträchtigenden Umschöpfvorgänge komplett entfallen und der gesamte Prozess deutlich effizienter gestaltet wird.
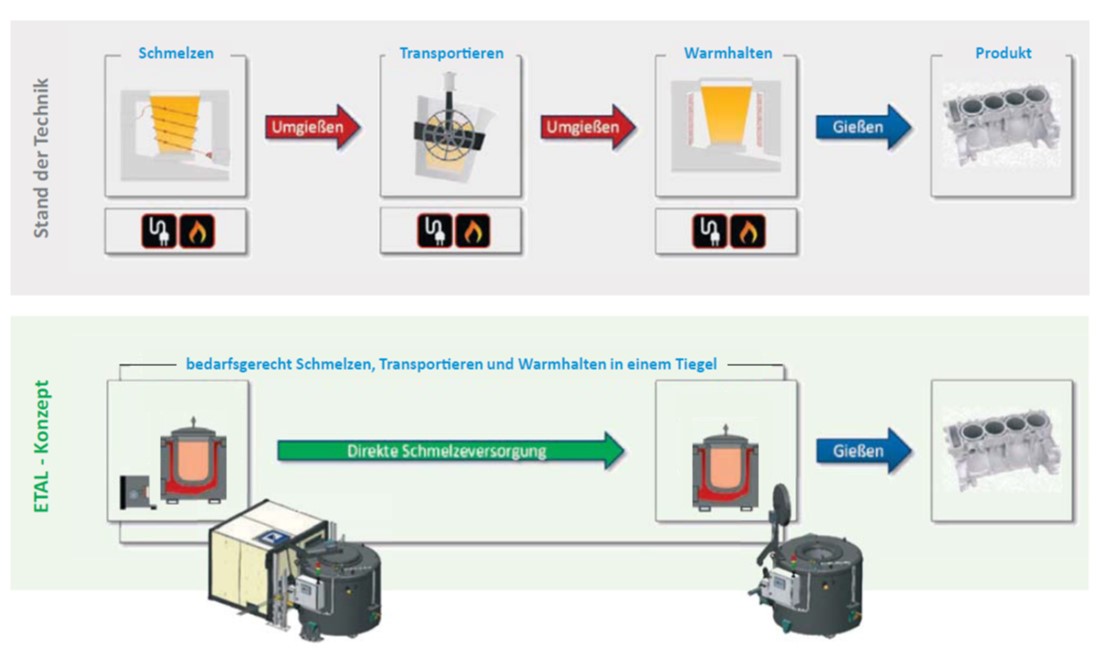
Das Besondere dabei ist, dass diese „mpots“ keine feste Beheizungslösung beinhalten. Vielmehr beziehen sie die zum Schmelzen benötigte Energie an innovativen Docking-Stationen (heat docks), die mit Hilfe der vorstehend genannten effizienten Brennerlösung arbeiten. Je nach erforderlicher Schmelzkapazität können mehrere heat docks gekoppelt werden. In diesem Fall besteht die Möglichkeit, die anfallende Abwärme zusätzlich auch kaskadenartig an die Partnerstation weiterzugeben, um somit zusätzliche Effizienzpotenziale zu heben.
Nach dem Einschmelzen verfahren die „mpots“ an die wertschöpfenden Gießplätze und versorgen diese entsprechend bedarfsgerecht mit flüssigem Metall. Dabei funktionieren sie ähnlich einer Thermoskanne und nutzen die zuvor bezogene Heißluft gezielt als Wärmeisolationspolster. Sofern erforderlich können an den Gießplätzen optional (z.B. wenn beim Abgießen kleinvolumiger Bauteile der „mpot“ übermäßig lange am Gießplatz verbleiben muss) weitere, entsprechend kleiner dimensionierte heat docks mögliche Wärmeverluste des Metalls ausgleichen, was den systemischen spezifischen Energieverbrauch senkt. Bei Bedarf können auch in einer beliebigen Anzahl solcher mpots komplett unterschiedliche Legierungen verarbeitet werden, wodurch der zunehmenden Herausforderung einer stetig steigenden Produktdiversität Rechnung getragen wird.
Durch den Einsatz eines solchen volltransportablen Schmelzund Warmhaltesystems, in dem die für die Gusserzeugung vorzuhaltende Metallmenge jeweils direkt in einem einzigen Tiegel eingeschmolzen, veredelt, warmgehalten und geschöpft wird, entfallen mindestens zwei Umfüllprozesse. Dadurch wird die Bildung der für die Gussqualität äußerst schädlichen Oxide signifikant reduziert und die mit der Schlackebildung einhergehenden Materialverluste werden minimiert. Dies resultiert in einer deutlichen Reduzierung des Produktionsausschusses und wird außerdem die indirekten Energieverbräuche senken. Ferner könnten durch das neue Konzept künftig sogar aufwendige Schmelze-Aufbereitungsverfahren, wie z.B. das Impellern, deutlich reduziert oder gänzlich überflüssig werden. Für eine finale Beurteilung sind jedoch zunächst die geplanten Untersuchungen in der praktischen Anwendung abzuwarten. Neben den energietechnischen Vorteilen eröffnen sich durch den innovativen Konzeptansatz und die damit einhergehende Loslösung von den bislang vorrangig krangebundenen Transportwegen der Schmelze, insbesondere auch aus Sicht der Produktionsplanung und Fertigungslogistik, komplett neue Möglichkeiten für die Gestaltung der innerbetrieblichen Materialflüsse. Hier ist eine erhebliche Senkung der Kreislaufmaterialquote und damit des indirekten Energieverbrauches zu erwarten. In diesem Zusammenhang sollen die Bereiche der eigentlichen Wertschöpfung, also die Gießplätze, im Sinne einer vollvernetzten Anlagentechnik die benötigte Schmelzlegierung künftig bedarfsgerecht („PULL“-Prinzipien) und jederzeit transparent an den heat docks anfordern und anschließend direkt aus den bereitgestellten mpots für den Gießprozess schöpfen. Projiziert auf die LGL GmbH könnten somit konkret die zwei gasbeheizten Schmelzöfen, die drei mittels Gasbrenner vorgeheizten Transportpfannen sowie die acht elektrisch beheizten Warmhalteöfen durch zwei bis drei effizient beheizte „heat docks“ und einer der Produktionsauslastung angepassten Anzahl an „mpots“ substituiert werden (Bild 7).
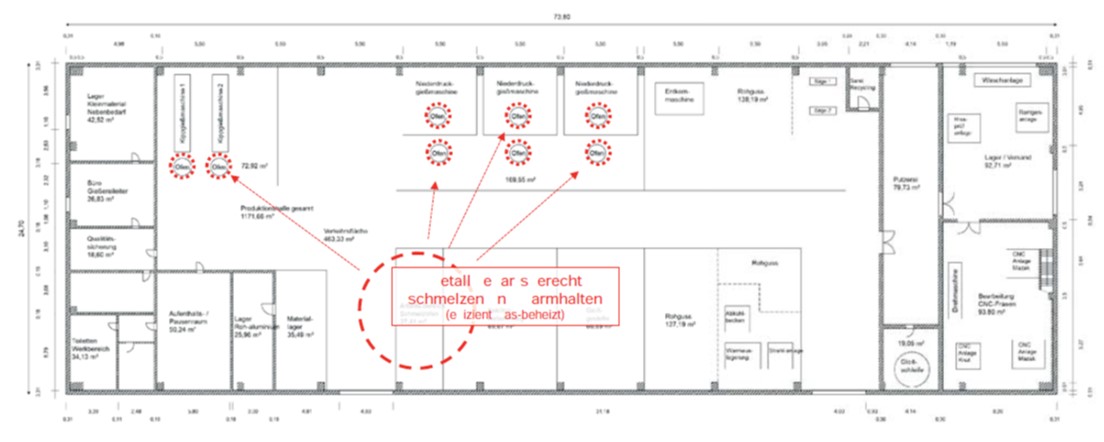
Neben der Sicherstellung planbarer Warenverkehre durch eine anforderungsgerechte Technik (z.B. führerlose Transportsysteme) bietet diese Form der intelligenten Materialabrufe die Möglichkeit der Routenoptimierung in der Logistik durch flexiblere Prozessabfolgen bzw. Produktreihen und erfüllt so die Ansprüche einer nachhaltigen, energieeffizienten und hochflexiblen Lösung.
3.3 Neue Sensortechnologie für eine kontinuierliche Prozessüberwachung
Nicht zuletzt ermöglicht eine ebenfalls im Projekt entwickelte sensorbasierte Monitoring-Technologie sowohl eine kontinuierliche Überwachung der Temperaturen und Füllstände als auch eine zielführende Kommunikation zwischen mpot und heat docks. Dies bildet die Basis für eine künftig vollkommen automatisierte Prozessführung und demonstriert ein konkretes Anwendungsszenario für die digitalisierte Produktion der Zukunft.
Diese vollvernetzte Monitoring-Technologie (einschließlich sensorgestützter Hardware) soll künftig eine universelle, standardisierte, objektorientierte Echtzeit-Erfassung sowie eine Bewertung und Überwachung der Hochtemperaturprozesse ermöglichen. Die Herausforderung besteht dabei darin, künftig sämtliche produktionsrelevanten Prozessinformationen unter den extremen Bedingungen einer Gießerei berührungslos und direkt in Form einer In-Situ-Analyse zuverlässig zu erfassen, sofort weiterzugeben und im Sinne einer Steigerung der operativen Effizienz zu verarbeiten.
Die Nutzung dieser Informationen lässt die Ableitung vielfältiger betriebstechnischer Zusammenhänge wie den Ereignisund Zustandsbezug der Anlagen, die Identität, Ortung und Qualitätsermittlung von Prozessen, Produkten und Betriebsmitteln sowie die Bewertung des damit verbundenen energetischen Zustands zu. Sie bietet damit eine intelligente und nachhaltige Entscheidungsgrundlage, kurzum die Grundvoraussetzung für eine künftig vollautomatisierte Prozesssteuerung.
4 Zusammenfassung und Ausblick
Wie vorstehend dargestellt, beinhaltet das Projektvorhaben ETAL gleich mehrere neuartige Technologieentwicklungen, die einen radikalen Umbruch in der künftigen Prozessgestaltung moderner Gießereien ermöglichen können. Dabei haben sich die Projektpartner das ambitionierte Ziel gesetzt, den erforderlichen Primärenergieeinsatz und damit auch die emittierten Schadstoffe in der Prozesskette der Leichtmetall-Gusserzeugung signifikant zu reduzieren, um auch in einer zunehmend globalisierten Zukunft eine wirtschaftliche, wettbewerbsfähige und gleichwohl nachhaltige Produktion am Standort Deutschland zu ermöglichen.
Das Gesamtkonzept aus technischer Lösung und Prozessoptimierung ist dabei hochinnovativ und weltweit einzigartig. Die technologische Entwicklung sogenannter heat docks, also dezentraler Wärmestationen und das Tiegelpfannenkonzept Impot im Sinne einer volltransportablen Schmelz- und Warmhaltelösung zur Metallversorgung sind zum Schutzrecht angemeldet. Als Voraussetzung für ein erfolgreiches Gelingen des beschriebenen Prozess- und Anlagenkonzeptes ermöglicht dabei ein neu entwickeltes, gasbasiertes modulares Brennerkonzept erstmalig den Einsatz des günstigen und ökologisch sinnvollen Energieträgers Gas zur Erzeugung der benötigten Wärme in elektrischer Regelgüte. Die Besonderheit dabei ist, vorgewärmte Luft sicher und exakt kontrollierbar zu verarbeiten, sodass die prozessintern anfallende Abwärme zielführend und effizient wiederverwertet werden kann.
Nicht zuletzt ermöglicht eine sensorbasierte, vollvernetzten Monitoring-Technologie die kontinuierliche, berührungslose Überwachung sowohl der Schmelzetemperatur als auch der Füllstände sowie eine zielführende Kommunikation zwischen mpots und heat docks. Dies wiederum bildet entsprechend die Basis für eine künftig vollkommen automatisierte Prozessführung, die sich durch geeignete Logistikkonzepte nach dem Push-Prinzip zu einer bedarfsgerechten Metallbereitstellung als wesentlicher Bestandteil des Gesamtkonzeptes auszeichnet.
Die Vorteile auf einen Blick:
- Reduzierung der CO2-Emissionen um bis zu 80 %,
- Senkung der Energiekosten um bis zu 60 %,
- Reduzierung des Primärenergieverbrauches bei NE-Gussteilenu m bis zu 25 %,
- Verringerung der Schlackebildung um bis zu 20 %, äquivalent einer Rohmaterial- und Schmelzenergieeinsparung von mehr als 2 MWh/t im Gießprozess,
- erhebliche Verbesserung der Gussqualität durch homogen erwärmte Werkzeuge und Entfall der Umschöpfprozesse,
- Signifikante Verkürzung der Durchlaufzeiten durch Flexibilitätssteigerung der Schmelzgutbereitstellung und damit effizientes Auftragsmanagement.
Die Autoren danken dem Bundesministerium für Wirtschaft und Energie (BMWi) für die Förderung des Projektes ETAL auf Grundlage des Rahmenprogramms „6. Energieforschungsprogramm“ zum Thema „Energieeffizienz in der Industrie“.
Stefan Scharf, Marc Kujath, Bastian Sander und Holger Seidel, Fraunhofer-Institut für Fabrikbetrieb und –automatisierung IFF, Magdeburg, Jochen Volkert und Jörg tom Felde, promeos GmbH, Nürnberg, Norbert Stein und Hagen Stein, Leichtmetallgießerei Bad Langensalza GmbH, Bad Langensalza, Eric Riedel, Wolfgang König und Chris Michealis, Otto-von-Guericke-Universität Magdeburg, Institut für Fertigungstechnik und Qualitätssicherung IFQ, Magdeburg
Literatur
[1] Bundesverband der Deutschen Giesserei-Industrie (BDG) (Hrsg.): Die Gießerei-Industrie: Eine starke Branche in Zahlen.
[2] Stephan, W. ; Zitzmann, K. ; Pröbstle, G. ; Kapischke: Effiziente Energieverwendung in der Industrie.
[3] Bosse, M. ; Frost, E. ; Hazrat, M. ; Rhiemeier, J. ; Wolff, H.: Ermittlung von branchenspezifischen Potentialen zum Einsatz von erneuerbarer Energien in besonders energieintensiven Industriesektoren am Beispiel der Gießerei-Industrie. 2013.
[4] Bundesnetzagentur: Gewerbe- und Industriestrompreise in Deutschland bis 2018 | Statistik. URL https://de.statista.com/statistik/daten/studie/154902/umfrage/strompreise-fuer-industrie-und-gewerbe-seit-2006/ – Überprüfungsdatum 2019-02-27.
[5] Bundesnetzagentur: Gaspreise für Gewerbe- und Industriekunden in Deutschland bis 2018 | Statistik. URL https://de.statista.com/statistik/daten/studie/168528/umfrage/gaspreise-fuer-gewerbe--und-industriekunden-seit-2006/ – Überprüfungsdatum 2019-02-27.
[6] Petra Icha, Gunther Kuhs: Entwicklung der spezifischen Kohlendioxid-Emissionen des deutschen Strommix in den Jahren 1990-2017. 2018.
[7] Bosse, M.: Energieaspekte bei Brennersystemen für brennstoffbeheizte Gießereiöfen (NE) : Der energieeffiziente Gießereibetrieb 2.0. 2013.
[8] www.promeos.com (Stand 19.02.2019)
[9] Canadian Metallurgical Quarterly 18 (2013), [Nr. 3], S. 251–266.
[10] Metallurgical and Materials Trans-actions A 38 (2007), [Nr. 6], S. 1303–1316
[11] International Journal of Thermal Sciences 51 (2012), S. 145–154
[12] International Journal of Thermal Sciences 118 (2017), S. 435–447