Von der Simulation zum optimierten Ofen
Bis zu 15-prozentige Energieeinsparung durch Prozessoptimierung bei einem Aluminiumschmelzofen
Von Bettine Kuhnert, München
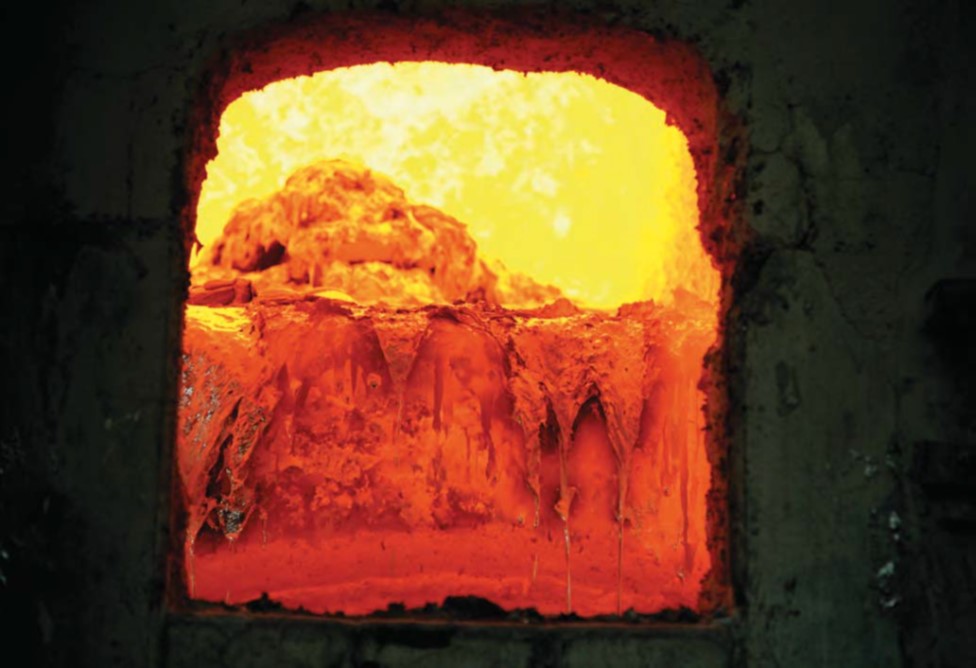
Die Sensorische Erfassung des Schmelzgutes erlaubt effiziente Ausrichtung eines schwenkbaren Brennersystems.
Erschienen in GIESSEREI 05/2017
Um das Energiesparpotenzial bei Aluminiumschmelzprozessen zu ermitteln, den Abbrand zu minimieren und die Grundlagen für ein modernes Wärmerückgewinnungssystem zu schaffen, haben Forscher in einem Verbundprojekt von Industrie und Wissenschaft ein System zur Überwachung und Steuerung des Schmelzprozesses entwickelt (Bild 1). Konsortialführer war dabei der Schmelzofenbauer ZPF GmbH aus Siegelsbach, der auch den Anstoß für das Vorhaben gegeben hatte. Die Untersuchungen im Rahmen des BMWi-geförderten Projekts, das nach einer Laufzeit von insgesamt vier Jahren 2016 abgeschlossen wurde, ermöglichten eine deutliche Verkürzung der Einschmelzzeit. So konnte eine Energieeffizienzsteigerung von bis zu 15 Prozent realisiert werden.
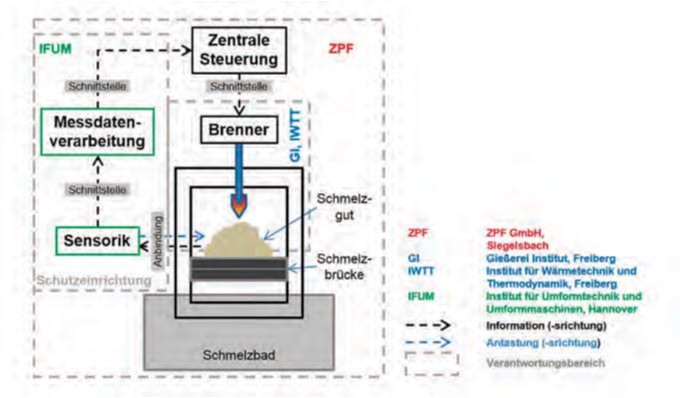
„Um nachhaltige Verbesserungen zu erzielen, muss das gesamte Ofensystem optimiert werden. Das war die wesentliche Erkenntnis aus dem 2011 abgeschlossenen Vorgängerprojekt, das sich hauptsächlich mit neuen Brenneranordungen und alternativem Feuerfestmaterial befasste“, berichtet Sven-Olaf Sauke, der das Projekt planerisch begleitete. „Mit dem Anfang 2012 gestarteten Forschungsvorhaben und Ende 2013 wieder aufgenommenen Projekt Edusal II sind wir einen weiteren Schritt in diese Richtung gegangen“. Der Fokus lag dabei einerseits auf der Entwicklung einer Messtechnik zur sensorischen Erfassung des Ofenraums. Dadurch sollte die örtliche Lage des Restmaterials auf der Schmelzbrücke nachgewiesen und mengenmäßig bestimmt werden. Zum anderen galt es herauszufinden, wie ein dynamisches Brennersystem anhand der Messdaten auf das Schmelzgut ausgerichtet werden kann und ob sich dadurch die Effizienz des Gesamtsystems steigern lässt (Bild 2).
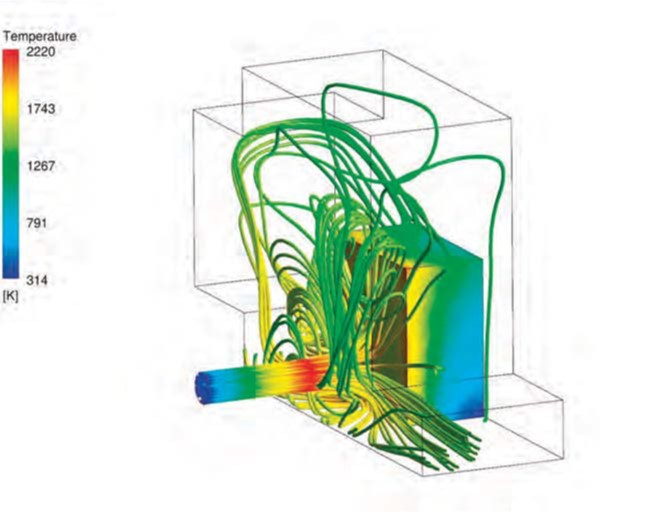
Optisches Messverfahren zur Erfassung des Ofeninnenraums
Die Projektpartner haben jeweils zu einem Teilvorhaben in ihrem Bereich geforscht. So wurden am Institut für Umformtechnik und Umformmaschinen der Leibniz Universität Hannover (IFUM) grundlegende messtechnische Untersuchungen zur Energieeinsparung und Automatisierung bei Al-Schmelzprozessen durchgeführt. Dazu musste zunächst eine entsprechende Sensortechnik entwickelt werden, die den thermischen Bedingungen im Ofenumfeld standhält. Als dafür am besten geeignet erwies sich ein optisches Kameraverfahren. „Die darauf beruhende, eigens für das Projekt umgerüstete Kamera ermöglichte erstmals eine Überwachung und Bewertung des laufenden Schmelzvorgangs (Bild 3). Allerdings limitiert die Leistungsfähigkeit der technischen Elemente derzeit noch die Anwendbarkeit“, erläutert Sauke.
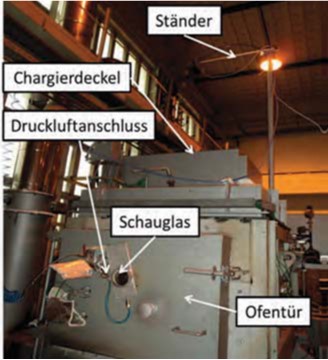
Da die Geschwindigkeit bei der Analyse der Messdaten entscheidend, diese jedoch bei der verwendeten Bildverarbeitungssoftware unzureichend war, entwickelten die Forscher einen speziellen Auswertungsalgorithmus. Dieser importiert im ersten Schritt die von der Kamera erstellten Daten und erzeugt daraus eine Tabelle, in der die Informationen aus allen drei während eines Aufnahmezeitpunkts erzeugten Bildaufnahmen festgehalten sind. Alle Koordinaten, die sich außerhalb der Grenzbereiche des Aluminium-Masselpakets befinden, werden vom Programm automatisch gelöscht und die verbliebene Oberfläche im dritten Schritt in neun definierte Regionen eingeteilt. So lässt sich das Fließverhalten der Schmelze und die Lage der verbliebenen Aluminiumreste systematisch bestimmen.
Simulationen zur Fahrweise des dynamischen Brennersystems
Für die weitere Verarbeitung wurden die zyklisch erhobenen Messdaten mit Hilfe einer speziellen Software in ein 3-D-Modell umgewandelt. Dieses wurde in ein Koordinatensystem umgewandelt, welches zur Ansteuerung des beweglichen Brennersystems benötigt wurde. Der Einfluss der Badfüllung auf die Abgasaustrittstemperatur und die Einschmelzzeit des Blocks stellte sich als gering heraus. Weiterhin wurde untersucht, inwiefern sich das Schwenken des Brenners und die damit verbundene Vergrößerung des Wirkbereichs auf die Temperaturverteilung auf der Schmelzbrücke auswirken (Bild 4). Dabei konnte im Vergleich zu einer statischen Positionierung eine starke Steigerung der Schmelzleistung nachgewiesen werden. „Somit ist deutlich weniger Zeit für das Aufschmelzen der Aluminiumreste erforderlich, was in Summe eine erhebliche Verbesserung der Energieeffizienz bedeutet“, resümiert Sauke das Ergebnis der Simulationen.
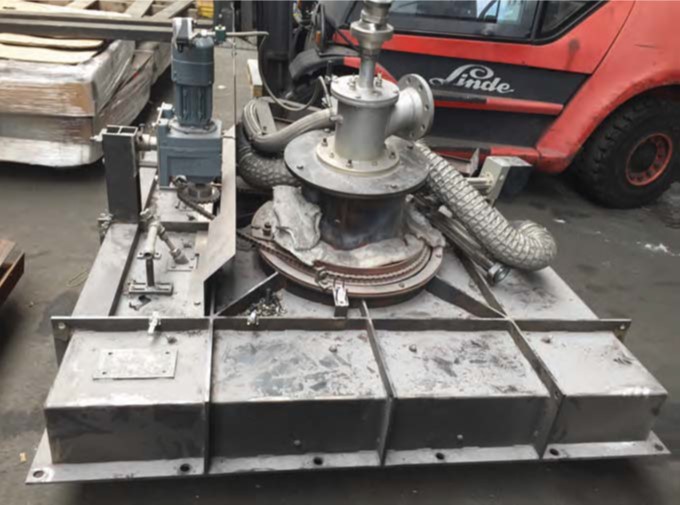
Die Simulationen wurden ausnahmslos am Institut für Wärmetechnik und Thermodynamik (IWTT) der TU Bergakademie Freiberg durchgeführt. Bei den zur Optimierung eingesetzten numerischen Simulationen zur Fahrweise des dynamischen Systems wurden sowohl der Warmhalte- als auch der Schmelzbetrieb berücksichtigt. Darüber hinaus wurden am IWTT Untersuchungen zum eingesetzten Brennersystem durchgeführt sowie Möglichkeiten zur Reduzierung des Gasverbrauchs untersucht. Ergänzend hierzu wurden am Gießereiinstitut (GI) der TU Bergakademie Freiberg Untersuchungen zur Abbrandminimierung und ein Großteil der Heißversuche unter Laborvoraussetzungen durchgeführt.
Annahmen unter realen Industriebedingungen bestätigt
ZPF unterstützte das Verbundprojekt bei Grundlagenfragen, kümmerte sich um die Softwareentwicklung sowie den Aufbau und die Erprobung einzelner Systemkomponenten. Auch die Testphase mit einem Demonstrator und die industrielle Umsetzung und Erprobung übernahm das Unternehmen aus Siegelsbach. „Für die Feldversuche wurde ein Demonstrator aufgebaut, der stark an eine Serienanlage angelehnt war. Der Schmelzofen vom Typ SG 1,5T5 mit einer Schmelzleistung von 1,5 t/h und einem Warmhaltebadinhalt von 5 t wurde aber projekttypisch mit einer großen Anzahl an Sonderbauteilen ausgestattet, etwa den benötigten Messmitteln“, so Sauke. Über zwei Stellmotoren konnte das System anhand der Koordinaten, die vom Messsystem an die Brennersteuerung übermittelt wurden, in die gewünschte Lage geschwenkt werden. Die Schmelzzeiten konnten dadurch ‒ ohne Beeinträchtigung der Qualität ‒ bei niedrigerem Gasverbrauch verkürzt werden.
„Unsere ursprünglichen Erwartungen einer 10 bis 15-prozentigen Energieeinsparung haben sich erfüllt, wobei die Messdaten des beweglichen Brenners den Schluss zulassen, dass diese Effizienzsteigerung auf einer Verkürzung der Einschmelzzeit beruht“, freut sich Sauke über den Erfolg des Projekts. Mit der Bestätigung der Annahmen unter realen Industriebedingungen ist der Grundstein für eine neue Verfahrensweise gelegt. Um weitere Schlussfolgerungen zu einer optimierten Fahrweise ziehen zu können, gilt es jedoch noch einiges zu verbessern und weitere Langzeitversuche zu unternehmen.
„In einem weiteren F+E-Projekt, das nach Möglichkeit 2017 starten soll, wird das Hauptaugenmerk auf den variablen Brennerpositionen und der Identifizierung von Verbesserungsmöglichkeiten bei der Messsensorik liegen“, gibt Sauke einen Ausblick auf die Zukunft. So soll unter anderem eine Online-Überwachung eingesetzt werden, um die Systemsicherheit zu erhöhen. Das mittel- bis langfristige Ziel ist, dass die Erkenntnisse in die Entwicklung von Ofenanlagen ‒ nicht nur bei ZPF ‒ einfließen sollen. „Wenn die Technik serienreif ist, können alle Betreiber von Aluminiumschmelzöfen davon profitieren. Auch ein Einsatz in anderen Industriezweigen, in denen eine Prozessüberwachung für den Heißbereich benötigt wird, ist denkbar“.