Energieeffizienz im induktiven Schmelzbetrieb – Einfluss der leistungsoptimierten Fahrweise
Von Erwin Dötsch, Robert Ibach, Marco Rische und Yilmaz Yildir, Dortmund
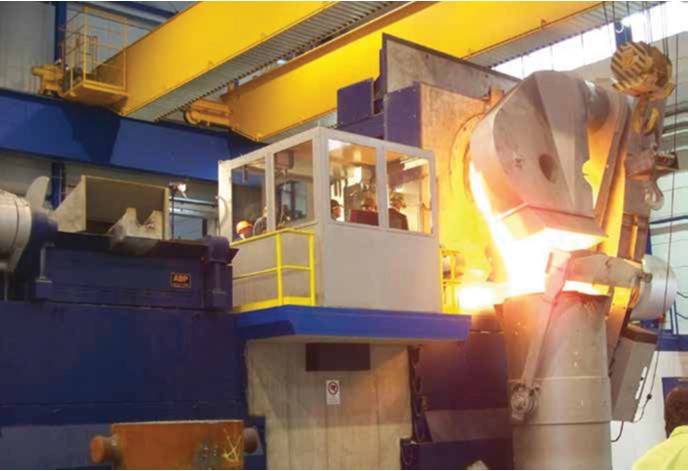
ABP-MFInduktions-Schmelzanlage, Typ IFM
Erschienen in GIESSEREI 02/2016
Mittelfrequenz-Schmelztechnik
In Bild 1 ist das Schema einer modernen Induktions-Schmelzanlage dargestellt. Demnach erfolgt die Stromversorgung über einen Frequenzumrichter, der die Induktionsspule für die geforderte Leistung mit Strom einer geeigneten Frequenz versorgt. Zusammen mit der parallel geschalteten Kondensatorbatterie und der Induktionsspule bildet er einen Schwingkreis mit variablen Größen von Strom, Spannung und Frequenz, die sich automatisch an die in Form des Schmelzgutes innerhalb der Spule vorliegende Last anpassen. Diese Charakteristik der Umrichter-Stromversorgung führt zu den Hauptvorteilen gegenüber dem konventionellen NF-Ofen mit starrer Netzfrequenz: Die variable und höhere Frequenz macht es zusammen mit den variablen Strom- und Spannungswerten möglich, dass der MF-Ofen bei gleichem Fassungsvermögen mit einer mehrfach höheren Leistung ausgerüstet und ohne Einbuße bei der Schmelzleistung im Chargenbetrieb, das heißt, ohne Sumpf mit festen Einsatzstoffen, betrieben werden kann.
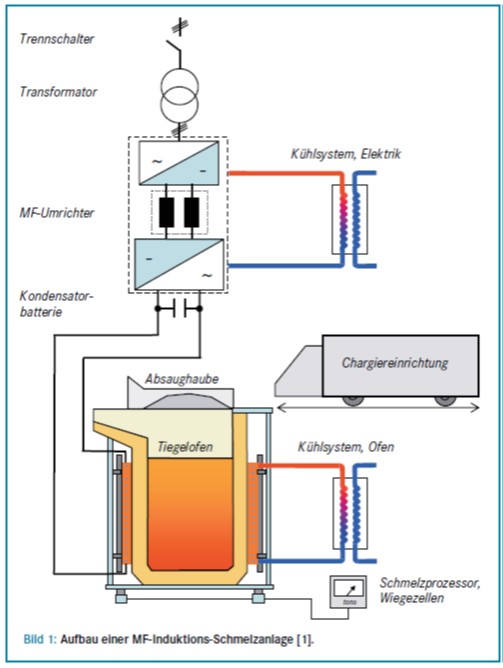
Dieser satzweise Betrieb erfordert zur optimalen Leistungsbeaufschlagung des Ofens eine quasikontinuierliche Chargierung [2]. Dazu werden die Einsatzstoffe in vorgegebener Reihenfolge meist per Magnetkran in eine fahrbare Beschickungs einrichtung geladen, die auf der Ofenbühne in Chargierposition fährt (Bild 2) und das Schmelzgut möglichst in der in Bild 3 dargestellten Reihenfolge in den Tiegelofen chargiert. Der Chargier- und Schmelzprozess wird dann über den so genannten Schmelzprozessor gesteuert. Dazu werden der aktuelle Inhalt des Tiegelofens über Druckmessdosen erfasst und die zum Schmelzen der Teilchargen bei einer vorgegebenen Temperatur benötigte Energie vom Schmelzprozessor berechnet und freigegeben. Der aktuelle Inhalt und die aus dem jeweiligen Energieeintrag berechnete mittlere Temperatur werden auf dem Bildschirm des Schmelzprozessors als kennzeichnende Größen für die Ofenbedienung angezeigt.
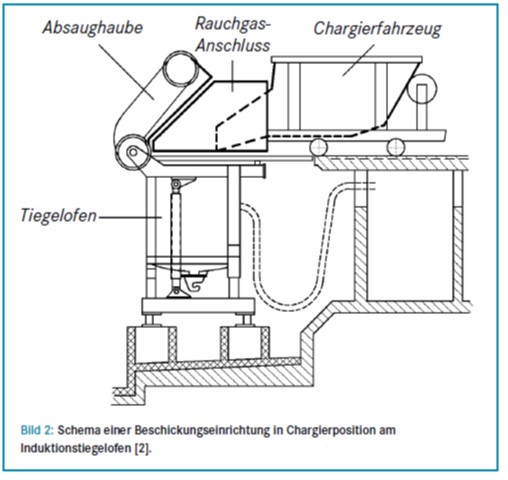
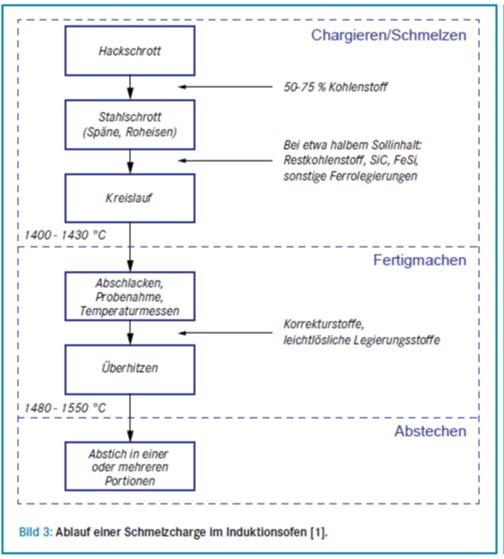
Energieverbrauch in Theorie und Praxis
Auf Basis der physikalisch vorgegebenen Enthalpie des Schmelzgutes ergibt sich der Energiebedarf einer Schmelzanlage aus dem technischen Stand und der Fahrweise der jeweiligen Öfen. Die spezifische Enthalpie von Gusseisenschmelzen beträgt 396 kWh/t bei 1500 °C [3], die Anlagenverluste eines modernen MF-Ofens liegen entsprechend den Werten in Bild 4 bei etwa 130 kWh/t [4], sodass sich für das Schmelzen von Gusseisen ein Energiebedarf von 525 kWh/t ergibt. Bis zur Bereitstellung der gießfertigen Schmelze entsteht über den Schmelzprozess hinaus zusätzlicher Energiebedarf für das Warmhalten und andere Manipulationen. In einem gut geführten MF-Schmelzbetrieb liegt dann der durchschnittliche Energieaufwand bei 560 bis 600 kWh/t.
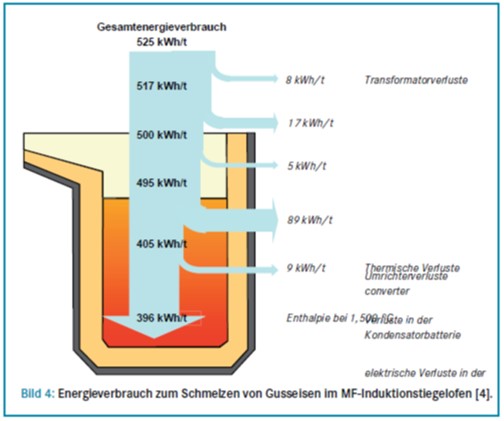
In der Praxis werden diese Werte oft um mehr als 100 kWh/t überschritten [5]. Grund dafür sind meistens höhere Prozessverluste, beispielsweise durch:
- Setzen von sandbehaftetem Kreislaufmaterial,
- Warmhalten mit offenem Ofendeckel,
- ungedrosselte Absaugung beim Warmhalten,
- längeres Warmhalten durch mangelhafte Logistik und
- nicht sachgemäßes Chargieren.
Diese zusätzlichen Verlustquellen lassen sich größtenteils durch relativ einfache Maßnahmen abstellen. Dagegen ist der letzte Punkt, nämlich die Nutzung der Potenziale des optimierten Chargierens, ein komplexer Vorgang, der hauptsächlich durch folgende drei Kriterien bestimmt wird:
Es beginnt mit der Chargenvorbereitung, wo der richtige Mix von grobem und kleinerem Stückgut Voraussetzung für das mehr oder weniger gute Ankoppeln des elektromagnetischen Feldes an das Schmelzgut ist. Bei ungünstiger Schüttdichte mit wesentlich mehr Luftvolumen als Metall im Spulenbereich des Tiegels wird die Schmelzzeit entsprechend verlängert und damit die Energieeffizienz verschlechtert. Bei Bedarf ist hier der Einsatz eines Kreislauf- und Schrottbrechers sinnvoll.
Ein zweites energierelevantes Kriterium ist das leistungsoptimierte Chargieren mit Hilfe des Schmelzprozessors. Er ermöglicht die Prozesskontrolle so, dass einerseits keine Unterbrechungen im Schmelzablauf entstehen und dass andererseits das Schmelzgut rechtzeitig nachchargiert wird, sodass der Spulenraum immer gefüllt ist und das eventuell feuchte Material nicht in den flüssigen Sumpf eintaucht. Demnach sollte der Schmelzer den Anweisungen des Prozessors folgen und auf diese Weise den Ofen ständig mit der vollen verfügbaren Leistung fahren.
Drittes Kriterium ist dann die Bauweise des Frequenzumrichters, die die anlagentechnische Voraussetzung für den optimalen Chargier- und Schmelzablauf darstellt, worauf im Folgenden näher eingegangen wird.
Entwicklung des Frequenzumrichters für den satzweisen Betrieb
Wie eingangs beschrieben, arbeitet der aus Umrichter, Kondensatorbatterie und Induktionsspule bestehende Schwingkreis lastgeführt, das heißt, die Leistungsaufnahme des Ofens hängt vom Schmelzgutzustand ab, der sich während der Schmelzzeit in Bezug auf elektrische und magnetische Leitfähigkeit sowie Spulenfüllgrad und Anteil fest/flüssig ändert. Dementsprechend ändert sich auch die Leistungsaufnahme – wie in Bild 5 gezeigt, wo Ofeninhalt und Leistung eines 6-t-Ofens mit einem Umrichter erster Bauart (Baujahr 1984) über der Schmelzzeit aufgetragen sind. Der Umrichter war seinerzeit mit einer Spannung von 2500 V, einem Wirkstrom von 1720 A und einer Frequenz von 230 Hz für eine Leistung von 3500 kW ausgelegt. In Bild 5 ist zu erkennen, dass beim Anfahren der Charge mit ferromagnetischem Schrott das Schmelzgut aufgrund der hohen magnetischen Leitfähigkeit (Permeabilität) so niederohmig ist, dass bei Nennspannung ein hoher Strom und damit eine hohe Leistung erzeugt werden.

Mit der Originalspannung von 2500 V wurde dadurch der Umrichter mit Anfahrleistungen von über 4000 kW so überlastet, dass es zu häufigen Thyristorausfällen kam. Dementsprechend wurden die Spannung auf 2250 V und damit die Nennleistung auf 2900 kW reduziert. Mit diesen Werten erhält man den in Bild 5 dargestellten Leistungsverlauf: Nach dem hohen Leistungseintrag zu Chargenbeginn wird nach wenigen Minuten bei Überschreiten der Curie-Temperatur (768 °C) das Schmelzgut in Abhängigkeit von der Schüttdichte mehr oder weniger hochohmig, sodass der Strom und damit die Leistungsaufnahme erheblich absinken. Mit weiterem Nachchargieren von ferromagnetischem Schmelzgut steigt die Leistungsaufnahme wieder über Nennleistung an, um sich dann bei etwa zu 3/4 gefülltem Ofen auf den konstant bleibenden Wert von 2900 kW einzupendeln. Somit liegt die durchschnittliche Leistungsaufnahme etwa bei 2800 kW und damit bei nur 80 % der ursprünglichen Nennleistung. In der weiteren Umrichterentwicklung wurde anstelle der generellen Spannungsbegrenzung als Verbesserungsmaßnahme der Ofen nur beim Anfahren und beim Nachchargieren mit reduzierter Spannung beaufschlagt. Bild 6 zeigt als Beispiel dafür den Leistungsverlauf von vier Chargen einer 10-MW-Anlage, deren Leistungsaufnahme beim Anfahren auf 5 MW und beim Nachchargieren auf 2 MW begrenzt ist. Hier ist es wichtig, noch einmal an das Ziel der optimierten Leistungsbeaufschlagung zu erinnern: Der Ofen soll möglichst über die gesamte Schmelzzeit mit der vollen Nennleistung gefahren werden, dann erreicht man die kürzeste Schmelzzeit und damit den geringsten Energieaufwand und die höchste Produktivität. Gleichzeitig kann zum Vorteil des Strompreises mit dem niedrigsten Strom-Maximum gearbeitet werden. Es ist selbsterklärend, dass mit der Gesamt- und Teilreduzierung der Umrichterspannung dieses Ziel nicht erreicht wird. Dazu wurde der Umrichter mit Konstantleistungsregelung entwickelt.
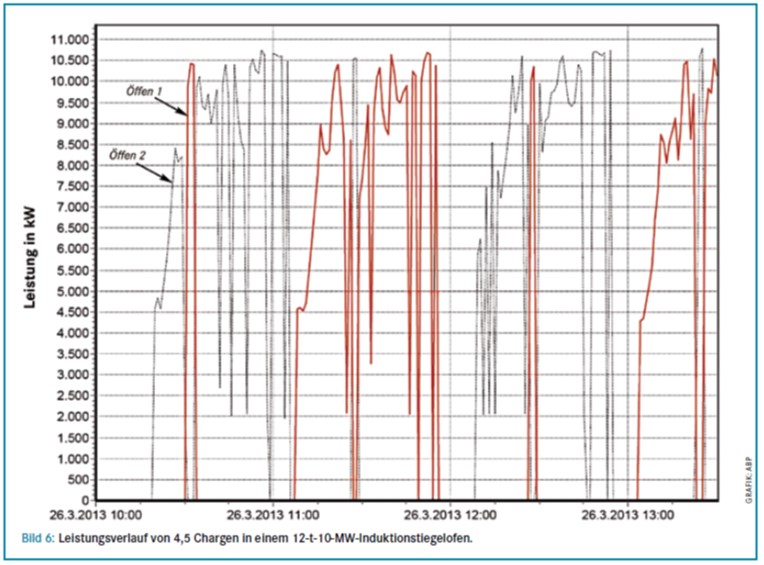
Umrichter mit Konstantleistungsregelung
Entsprechend Bild 7 ist der Konstantleistungsumrichter in Bezug auf Strom und Spannung nicht auf einen Arbeitspunkt ausgelegt, sondern er verfügt über einen Strom- und Spannungsbereich von jeweils 70 bis 100 %, der entsprechend der eingetragenen Lastkennlinie in Abhängigkeit vom elektromagnetischen Widerstand des Schmelzgutes abgefahren wird [6].
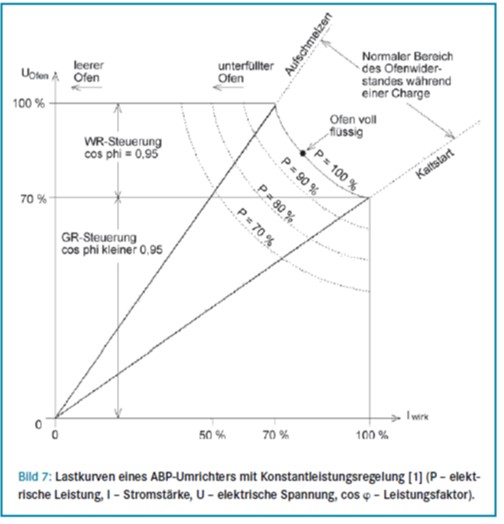
Das Ergebnis wird am Leistungsverlauf in Bild 8 deutlich, der als signifikantes Beispiel die Verhältnisse an dem inzwischen mit modernem Konstantleistungsumrichter ausgerüsteten 6-t-Ofen von Bild 5 darstellt: Beim Anfahren mit dem ferromagnetischem Schrott wird die Nennleistung in Höhe von 3500 kW mit sich automatisch einstellender niedriger Spannung erzeugt. Bei Erreichen der Curie-Temperatur steigt die Umrichterspannung auf die Grenzspannung von 3000 V an, um die Leistungsaufnahme auf dem Nennwert zu halten. Wegen mangelnder Schüttdichte des inzwischen aufgeheizten Schrotts ist das bei ca. 2 t Ofeninhalt kurzzeitig nicht mehr möglich, bis ferromagnetischer Schrott nachchargiert wird und die Leistung wieder auf den Nennwert ansteigt, wo sie bis zum Chargenende mit 6 t Inhalt gehalten wird. Die durchschnittliche Leistungsaufnahme liegt somit bei über 95 % der Nennleistung und die Schmelzzeit verkürzt sich um 9 min gegenüber der Schmelzzeit von 62 min mit dem alten Umrichter (s. Bild 5).
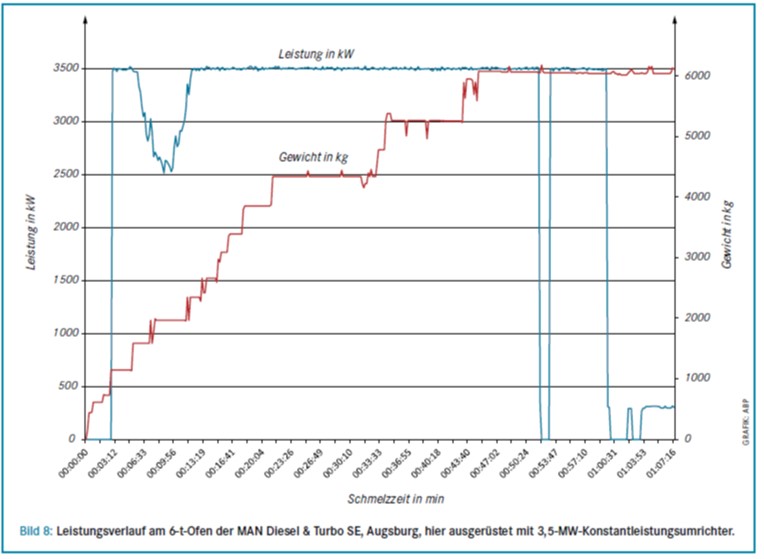
Ein weiteres Beispiel für die anforderungsgerechte Funktionsweise des Konstantleistungsumrichters stellt der Betrieb von zwei 8400-kW-12-t-Tiegelöfen dar, wobei gleichzeitig der Einfluss der Schüttdichte des Schmelzgutes sichtbar wird [7]. Beim Beladen der Chargierwagen für das in Bild 9 abgebildete 12-t-Ofen-Tandem wird die Reihenfolge der Einsatzstoffe so eingestellt, dass zur Schonung der Feuerfestauskleidung zunächst leichter Stanzschrott in den leeren heißen Tiegel gelangt und dann aber möglichst bald kleinstückiges Kreislaufmaterial chargiert wird, um eine hohe Packungsdichte der Schmelzgutschüttung und damit ein gutes Ankoppeln des elektromagnetischen Feldes beim Anfahren zu erreichen.
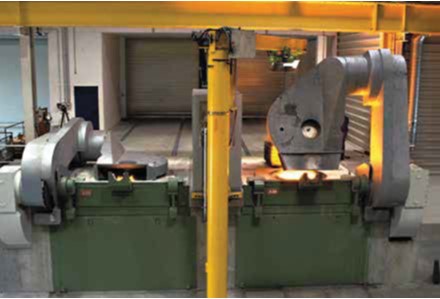
Der in Bild 10 dargestellte zeitliche Leistungsverlauf zeigt, dass von Beginn der Schmelzzeit an bis zu ihrem Ende der Ofen mit der vollen Nennleistung in Höhe von 8400 kW beaufschlagt wird. Somit wird bei diesem Beispiel das Ziel der minimalen Schmelzzeit mit maximaler Energieeffizienz voll erreicht, indem die drei oben genannten Kriterien erfüllt werden:
- Einsatz eines Umrichters mit Konstantleistungsbereich,
- Schmelzgutmischung aus kleinstückigem Kreislauf, Stanzabfällen uns Spänen mit hoher Schüttdichte von ca. 2,5 t/m³ und
- sachgerechtes Chargieren , prozessorgeführtes Nachchargieren auf festesSchmelz gut unter Berücksichtigung der optimierten Leistungsaufnahme.
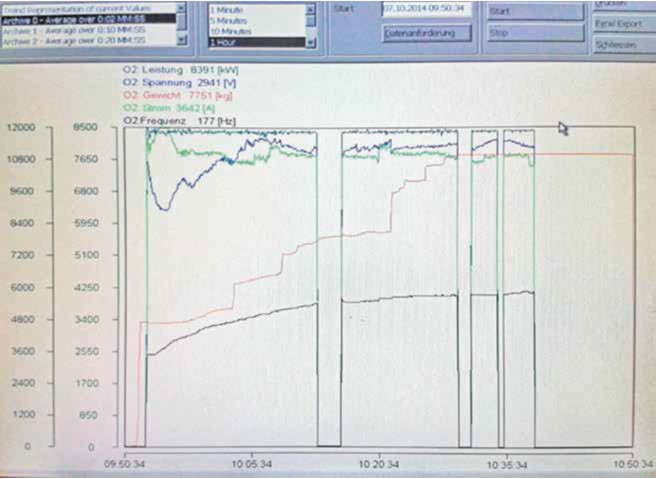
Zusammenfassung
Der Energiebedarf von Induktions-Schmelzanlagen ergibt sich aus dem technischen Stand und der Fahrweise der Öfen. Stand der Technik moderner MF-Induktionstiegelöfen für das Schmelzen von Gusseisen bei 1500 °C ist ein Wirkungsgrad von 75 % und dementsprechend ein Energiebedarf von 525 kWh/t. Dazu kommt in prozesstechnisch bedingter Energieaufwand für das Fertigmachen der gießfertigen Schmelze, der stark vom Chargier- und Schmelzablauf beim satzweisen Betrieb der umrichtergespeisten Tiegelöfen abhängig ist. Einen wichtigen Einfluss hat dabei der vom Zustand des Schmelzgutes abhängige Leistungseintrag während der Schmelzperiode. Es wird eine konstante Leistungsaufnahme angestrebt, die zur kürzesten Schmelzzeit und damit zum geringsten Energiebedarf bei niedrigstem Strom-Maximum sowie zur höchsten Produktivität führt. Erreicht wird dieses Ziel durch die Verwendung eines Umrichters mit Konstantleistungsregelung und den Einsatz von Schmelzgut hoher Schüttdichte, das in einem prozessorgeführten Verfahren in den Tiegelofen chargiert wird. Im auf diese Weise gut geführten MF-Schmelzbetrieb liegt der durchschnittliche Energiebedarf bei 560, maximal bei 600 kWh/t.
Dr.-Ing. Erwin Dötsch, Dipl.-Ing. Robert Ibach, Dr. Marco Rische und Dipl.-Ing. Yilmaz Yildir, ABP Induction Systems GmbH, Dortmund
Literatur:
[1] Dötsch, E.: Induktives Schmelzen und Warmhalten. 2. Aufl. Vulkan-Verlag Essen, 2013.
[2] Giesserei 87 (2000), [Nr. 8], S. 64-66.
[3] Giesserei 88 (2001), [Nr. 10], S. 25-29.
[4] Gießerei-Praxis (2013), [Nr. 6], S. 237-240.
[5] Giesserei 98 (2011), [Nr. 6], S. 158-170.
[6] Giesserei 99 (2012), [Nr. 6], S. 20-25.
[7] Giesserei 101 (2014), [Nr. 5], S. 112-117.