Gemeinschaftsprojekt erforscht Energieeffizienz von Aluminiumschmelzöfen
Von Christina Gassel, München
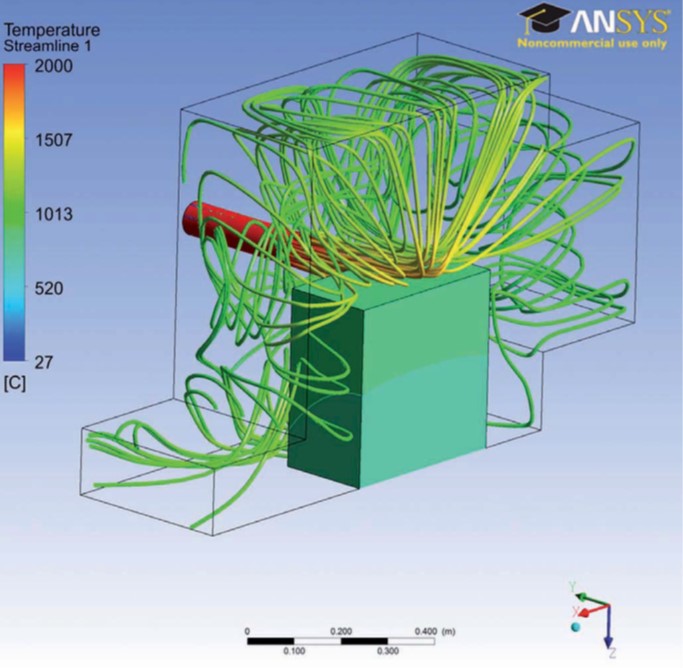
Die Strömungsverteilung in der Brennkammer des Ofens ist einer von vielen Faktoren in den Untersuchungen. Wirkliche Effizienzsteigerungen lassen sich nur durch Optimierungen in allen Bereichen erzielen.
Erschienen in GIESSEREI 04/2011
Die Entwicklung einer neuen, gasbeheizten Ofengeneration, die in Energiebilanz und Standzeit des Feuerfestmaterials die derzeit üblichen Anlagen übertrifft – das ist das Ziel eines Projektes des Schmelzofenbauers ZPF Therm und einer Forschungsgruppe um Prof. Dr. Klaus Eigenfeld von der Technischen Universität Bergakademie Freiberg. Der Direktor des Gießerei-Instituts prüft zusammen mit Kollegen anderer Fachbereiche Möglichkeiten, Gasverbrauch und Stillstandzeiten zu verringern und gleichzeitig die Schmelzequalität zu verbessern. Laut ZPF Therm sind Energieeinsparungen von etwa 15 % möglich.
Die Untersuchungen wurden von der ZPF Therm Maschinenbau GmbH, Siegelsbach, initiiert und werden von dem Unternehmen auch praktisch unterstützt. Das bis Oktober dieses Jahres angelegte Forschungsprojekt wird durch das Bundesministerium für Wirtschaft und Technologie BMWi gefördert und vom Projektträger Jülich betreut. Letzterer kontrolliert die fachliche und sachliche Projektdurchführung und unterstützt die beteiligten Firmen.
Bei dem Projekt geht es um Effizienzfaktoren, wie Chargiermethodik, Reinigungsintervalle, und Abbrandverlust. Faktoren, die jeden Gießereibetreiber interessieren sollten, es aber selten tun, wie Eigenfeld feststellt. „Nur wenn der Leidensdruck groß genug ist“, ergänzt er. Ansonsten bliebe es häufig nur beim Blick auf den Gaszähler. Rund 0,6 kWh werden benötigt, um 1 kg einer herkömmlichen Aluminiumlegierung zu schmelzen. Bei einer Aluminiumproduktion in Deutschland von 1,1 Mio. t im Spitzenjahr 2008 entspricht das 380 Mio t CO2. Da die Emissionen direkt von der Menge an verfeuertem Erdgas abhängen, würden von effizienterer Technik beide Seiten profitieren: die Wirtschaft durch geringere Energiekosten und die Umwelt durch weniger Treibhausgase. „Den hauptsächlich klein- und mittelständisch strukturierten Gießereibetrieben fehlt es allerdings meist an den nötigen Forschungs- und Entwicklungskapazitäten“, so Eigenfeld. „Deshalb ist es uns wichtig, in diesem Projekt immer die ökonomischen Voraussetzungen im Auge zu behalten und Ergebnisse zu finden, die direkt in die Praxis umgesetzt werden können.“
Praxistests und Computersimulationen ermitteln Verbesserungspotentiale
Außer Eigenfeld und seinem Kollegen Dr. Uwe Richter vom Gießerei-Institut der TU Bergakademie Freiberg, die die Möglichkeiten der Gießtechnik untersuchen, arbeitet Dr. Volker Uhlig vom Freiberger Institut für Wärmetechnik und Thermodynamik an Verbesserungen der Brennertechnik und der Wärmeströme. Dipl.-Ing. Steffen Dudczig vom Institut für Keramik, Glasund Baustofftechnik befasst sich darüber hinaus mit der Belastbarkeit und Lebensdauer des Feuerfestmaterials. Die Konstruktion und Fertigung von Demonstrationsanlagen, die Durchführung der Feldversuche und die Analyse der verwendeten Schmelzöfen betreut ZPF Therm. Der Aluminiumschmelzofenbauer (Bild 1) kooperiert schon länger mit der TU Freiberg und stellt sein Know-how sowie Material und Vergleichswerte zur Verfügung. Sven-Olaf Sauke, Leiter der Technik bei ZPF Therm, sieht großes Potential in der Studie: „In den ersten Ansätzen gehen wir von einer Energieeinsparung von etwa 15 % aus.“
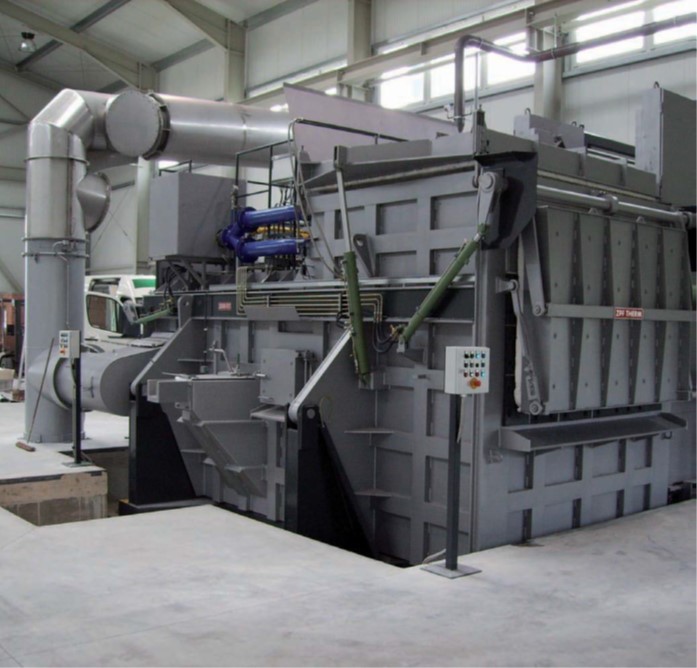
Bild 1: Aluminiumschmelzofen von ZPF Therm: Bei dem Forschungsprojekt, an dem die Firma beteiligt ist, geht es um verbesserte Energieeffizienz und längere Standzeiten des Feuerfestmaterials.
Bislang wurden bereits theoretische und praktische Untersuchungen zu Schmelzverhalten, Infiltration und Strömungsverteilung in einem Schmelzofen durchgeführt. Versuchsträger war ein Schmelz- und Warmhalteofen mit 300 kg/h Schmelzleistung und 700 kg Warmhaltekapazität. „Einige Bereiche, zum Beispiel das Feuerfestmaterial, werden direkt am konkreten Objekt betrachtet und etwa in Langzeittests erprobt“, erklärt Eigenfeld. „Wo es sinnvoll ist, werden auch Computermodelle erstellt und durch Messtechnik validiert (Bild 2).“ Dafür wird die Ofengeometriein Berechnungseinheiten zerlegt, die die reale Anlage abbilden. Allein das Gitter, das im Modell die Schichten an den Gas-Feststoff-Grenzflächen darstellt, umfasst circa 1 Mio. Zellen. Mittels dieses virtuellen Ofens können Szenarien unter verschiedenen Bedingungen simuliert werden, um so zum Beispiel mehr über die Strömungsentwicklung oder die Temperaturen in der Brennkammer zu erfahren (Bild S. 84). „Vor allem die Verteilung der Stromlinien der Brenngase hat uns überrascht“, sagt Eigenfeld. Wenn die Gaswege bekannt sind, lassen sich daraus Konstruktionsmerkmale für den Ofeninnenraum bleiten. Wird z. B. der Gasstrom länger über das Schmelzgut geführt, lässt sich ein besseres Abschmelzverhalten und damit eine Verkürzung der Schmelzzeit erreichen. Grundlage der Konstruktion effizienterer Aluminiumschmelzöfen sind aber auch Prozessparameter, die vom Betreiber bestimmt werden, etwa das Chargiergut sowie Chagierzeiten und -mengen.
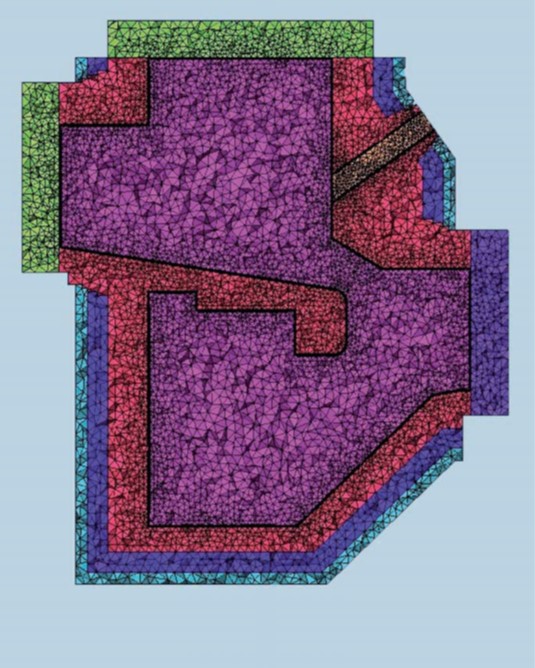
Bild 2: Computermodell eines Schmelzofens (Grün: Schachtdeckel, Beschickungstüre, Türkis: Stahlmantel, Blau: Feuerfestbeton, Rot: Feuerfestauskleidung, Lila: Reinigungstüre, Orange: Brenneröffnung, Magenta: Ofenraum).
Die Ergebnisse haben nicht nur Einfluss auf die Ofeneffizienz, sondern auch auf die Schmelzequalität. Untersuchungsgegenstand ist deshalb auch die Entstehung von Korund (Bild 3) bei bestimmten Prozessparametern. Korund in Gussstücken führt zu erheblichen Problemen, besonders bei der spanenden Bearbeitung. Daher soll auch durch eine verbesserte Führung der Prozessparameter, wie zum Beispiel Temperatur oder Sauerstoffgehalt, die Korundbildung in neuen Ofensystemen minimiert werden.
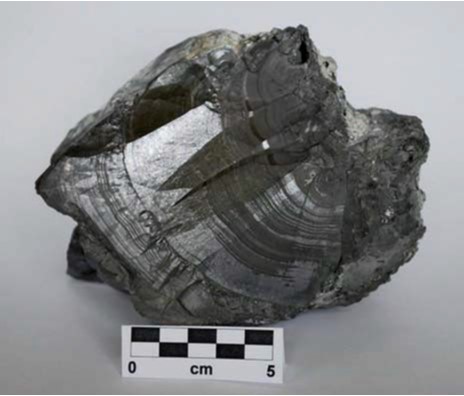
Bild 3: Das Projekt befasst sich auch mit der Schmelzequalität. So wird etwa die Entstehung von Korund bei bestimmten Prozessparametern untersucht.
Nur umfassende Optimierung erhöht die Effizienz nachhaltig
Zu den weiteren Fragestellungen, die das Projekt behandelt, zählen die Auswirkungen von Anzahl, Ort und Strahlrichtung der Brenner, der Einfluss der Beschickungsart und die Bedeutung, die diese Faktoren für die Schmelze haben. Dabei soll auch die Relation zwischen Anschaffungs- und Betriebskosten zum Gesamtaufwand für Schmelzen und Warmhalten betrachtet werden. „Wir konnten aber bereits feststellen, dass die Veränderung einzelner Komponenten nicht ausreicht. Um nachhaltige Verbesserungen zu erzielen, muss das gesamte Ofensystem optimiert werden“, betont Eigenfeld. „Was die Lebensdauer des Feuerfestmaterials betrifft, ist klar geworden, dass dafür der gesamte Prozess – von der Einbringung über das Sintern bis zur Nutzung – Relevanz hat.“ Als nächste Schritte werden die bisherigen Gesamtergebnisse ausgewertet und daraus die Konfiguration für den Demonstrator abgeleitet, den ZPF konstruieren und fertigen wird.
Christine Gassel, Pressebüro Gebhardt-Seele, München