Induktionsofentechnologie und Energieeffizienz
Von Erwin Dötsch, Dortmund
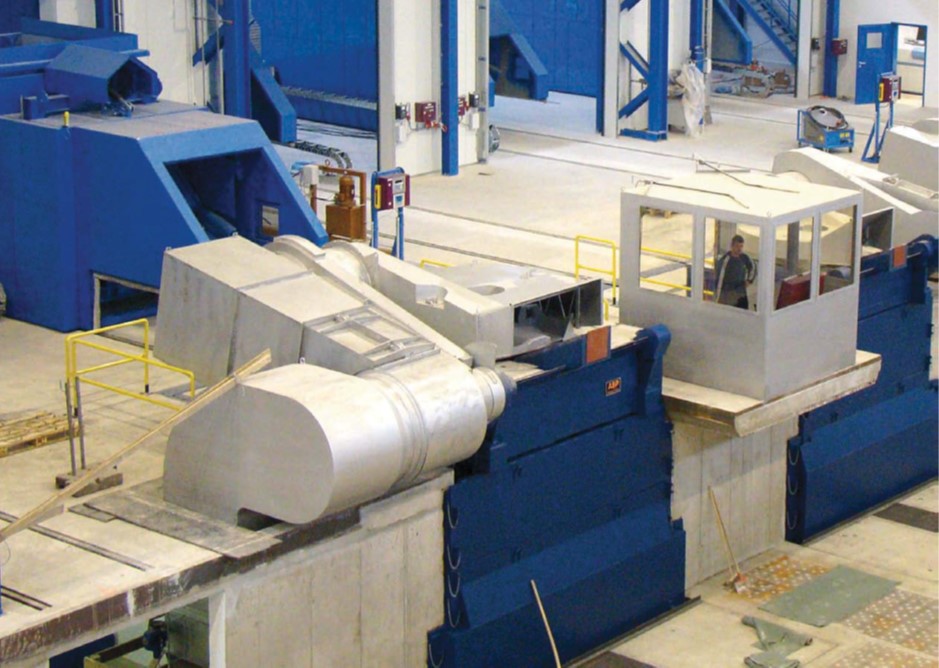
Erschienen in GIESSEREI 06/2011
Die Anwendung des induktiven Schmelzens befindet sich im Zustand einer raschen Entwicklung“, schrieb Karl-Heinz Brokmeier 1966 im Vorwort seines seinerzeit zum Standardwerk gewordenen Buches „Induktives Schmelzen“. Tatsächlich hat sich diese vergleichsweise junge Schmelztechnologie nach dem rasanten Wachstum in den 1960er Jahren basierend auf der Netzfrequenztechnik, dann mit der Entwicklung der Mittelfrequenz-Stromversorgung in den 1980er Jahren als Standardlösung in Eisen- und Nichteisengießereien etabliert. Maßgebend dafür sind zunächst die anwendungstechnischen Merkmale des Induktionsverfahrens:
Direkte Energieübertragung ohne Übertemperatur. Die Wärme wird mit hohem Wirkungsgrad direkt im Schmelzgut „erzeugt“, so dass im Unterschied zu anderen Schmelzverfahren keine Emissionen anfallen, die aus der Verbrennung des Energieträgers oder Hochtemperaturreaktionen entstehen. Daraus ergeben sich Vorteile für die Schmelzmetallurgie und die Umweltverträglichkeit.
Exakte Dosierung der Energiezufuhr. Der Schmelzablauf lässt sich mit geringem Personalaufwand exakt und reproduzierbar mit zielsicherer Einstellung der Abstichtemperatur und Sollzusammensetzung führen. Die Prozesse sind weitgehend automatisierbar.
Intensives Rühren der Schmelze durch elektromagnetische Kräfte. Die induktive Badbewegung führt zur Homogenität von Temperatur und chemischer Zusammensetzung der Schmelze sowie zu intensivem Stoffaustausch zwischen Gas- , Flüssig- und Festphasen an der Oberfläche und im Innern des Schmelzbades. Das schafft besonders günstige Bedingungen für das Schmelzen von spezifisch leichtem Schmelzgut wie Spänen oder Blechabfällen sowie für das Aufkohlen und Legieren.
Hohe Umwelt- und Arbeitsplatzverträglichkeit sowie niedriger Entsorgungsaufwand. Das Prinzip der direkten Energieübertragung führt zu geringer Staubemission und Schlackenbildung, die um mehr als eine Zehnerpotenz unter den Werten vergleichbarer brennstoffbeheizter Schmelzaggregate liegen. Auch schädliche Abgaskomponenten wie SO2 oder NOx entstehen nicht. Die Lärmbelästigung wird in zulässigen Grenzen unter 85 bis 83 dB(A) gehalten. Auch die relativ niedrige Hitzebelastung der Arbeitsumgebung macht den Induktionsofen zu einem arbeitsplatzfreundlichen Schmelzaggregat. Auf Basis dieser anwendungstechnischen Vorteile mit ständigen Verbesserungen bei der Energieeffizienz zeichnet sich derzeit ein weiterer Wachstumsschub für das induktive Schmelzen ab, der aus den Forderungen zur CO2-Reduktion resultiert.
CO2-Reduktion – ein Kriterium für die Elektrowärme
Die anwendungs- und umwelttechnischen Vorteile der elektrothermischen Prozesstechnik im Vergleich zur direkten Nutzung fossiler Brennstoffe sind unumstritten und haben in den letzten zehn Jahren zu einem um etwa 4 % höheren Anteil der Elektrowärme an der industriellen Prozesswärme geführt. Beispiele dafür sind die Elektrostahlerzeugung, deren Anteil an der Gesamtstahlerzeugung in den EU-Ländern in den letzten 20 Jahren von etwa 30 auf über 40 % gestiegen ist sowie das induktive Schmelzen in Eisengießereien, das bei der Gusseisenerzeugung mit etwa 40 % weltweit einen ähnlichen Anteil als Alternative zum koksbeheizten Kupolofen erreicht hat.
Dieser Trend erfährt einen zusätzlichen Auftrieb durch den wachsenden Anteil der regenerativen Stromproduktion, der als Prognose in Europa für 2020 im Vergleich zu 2007 in Bild 1 dargestellt ist. Aus Bild 2 lässt sich die daraus abzuleitende CO2-Reduktion für das induktive Schmelzen von einer Tonne Gusseisen entnehmen: Bereits in 2007 war die die Stromerzeugung einschließende spezifische CO2-Emission des Mittelfrequenz-Tiegelofens mit ca. 300 kg/t deutlich geringer als die des Kupolofens mit fast 500 kg/t. Mit dem für 2020 in Deutschland prognostizierten Regenerativ-Stromanteil liegt dann die spezifische CO2-Emission mit ca. 200 kg/t bei ca. 40 % der CO2-Emission des Kupolofens. Somit erfüllt das induktive Schmelzen die klimatechnische Forderung nach konsequenter Umstellung auf „saubere“ Energieträger in energieintensiven Industriebetrieben. bekanntlich wird diese Forderung vom Handel mit CO2-Emissionsrechten begleitet, was derzeit den Betrieb von Industrieöfen noch nicht betrifft, in Zukunft aber nicht auszuschließen ist.
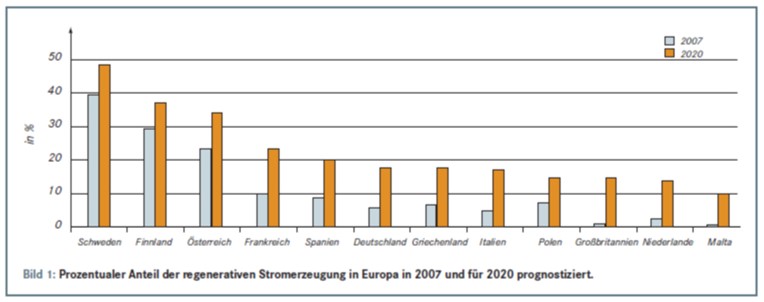
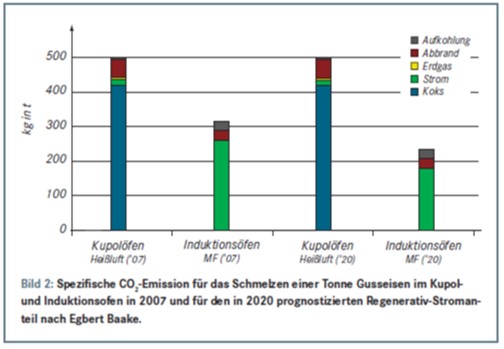
Energieeffizienz durch moderne Anlagenund Prozesstechnik
Auch beim Einsatz „grüner“ Energie ist natürlich im Sinne der Ressourcenschonung in erster Priorität die effiziente Nutzung der Elektroenergie gefordert. Dabei haben die Anlagen- und die Prozesstechnik gleiche Bedeutung.
Bei der modernen Anlagentechnik besteht inzwischen für alle Anwendungen des Induktionsverfahrens die Stromversorgung aus einer Frequenzumrichtereinheit, die die Induktionsspule fürdie geforderte Leistung mit Strom einer an die Schmelzbedingungen angepassten Frequenz versorgt. In Bild 3 ist als Beispiel das Schema der Induktionstiegelofenanlage dargestellt. Sie besteht im Wesentlichen aus dem Tiegelofen selbst, schematisch dargestellt in Bild 4, dem elektrischen Teil mit Transformator, Umrichter und Kondensatorbatterie sowie der Peripherie mit der Chargiereinrichtung und dem Wasserkühlsystem für Elektrik und Ofenspule. Für die Energiebilanz einer solchen Anlage sind beispielhaft für das Schmelzen von Gusseisen folgende Werte relevant: Die elektrischen Verluste im Transformator (1,5 %), im Umrichter (3 %) in Kondensator und Leitungen (2,5 %) sowie als Hauptanteil in der Spule ca. 15 %; dazu kommen ca. 3 % thermische Verluste, so dass bei einer spezifischen Enthalpie von 390 kWh/t für das Schmelzen und Überhitzen von Gusseisen auf 1500 °C der Energiebedarf am Netz bei 520 kWh/t liegt. Somit wird ein Gesamtwirkungsgrad von 75 % erreicht.
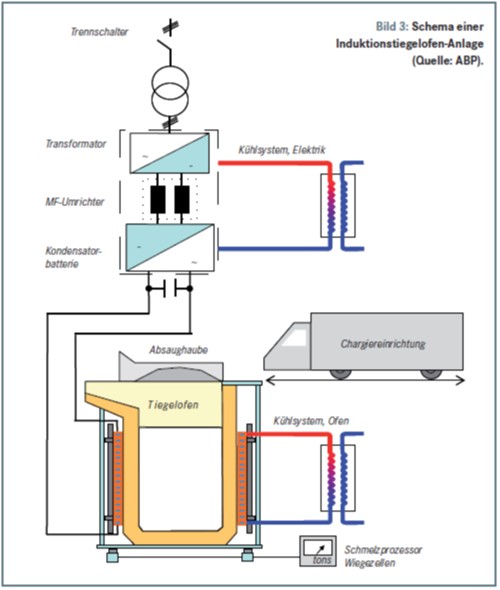
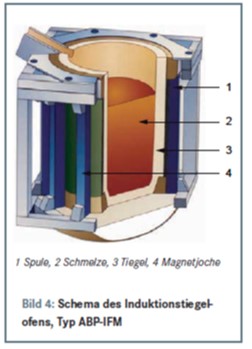
Marginale Verbesserungspotentiale für eine noch höhere Energieeffizienz liegen im Spulenaufbau, wo sich vor allem durch Optimierung der mittleren Spulentemperatur und des Spulenprofils sowie der Kühlspule die Verluste um 1 bis 3 Prozentpunkte senken lassen. Beim Umrichter liegen vergleichbare Möglichkeitenv vor durch Einsatz neuer Leistungselektronikkomponenten wie IGBT oder IGLT. Moderne IGBT-Umrichter stehen inzwischen zu wirtschaftlichen Kosten mit Leistungen bis 6000 kW zur Verfügung. Die derzeit maximale Ausgangsleistung eines Umrichters auf Thyristorbasis liegt bei 18 000 kW. Das größte Potential zu verbesserter Energieeffizienz beim Induktionstiegelofen liegt in der Nutzung der Abwärme, die mit bis zu 20 % der Ofenleistung greifbar im Kühlwasser der Spule vorliegt, allerdings auf einem Temperaturniveau von bisher maximal 80 °C. Unter dieser Voraussetzung gibt es Erfahrungen mit den beiden folgenden Systemen:
- Nutzung der warmen Luft, wie sie beim Autokühlerprinzip anfällt, zur Schrotttrocknung oder zur Hallenheizung. Bei der Schrotttrocknung müssen für einen effektiven Wärmeübergang in der Schrottschüttung große Luftmengen mit Druck bewegt werden; dazu wird Energieaufwand benötigt, der die Energiebilanz verschlechtert. Bei der Hallenheizung wirken sich die großen bewegten Luftmengen als Zugluft aus, was zusätzliche Maßnahmen notwendig macht. Demnach ist die Abwärmenutzung in Form von warmer Luft noch wenig effektiv und verbesserungsfähig.
- Nutzung von warmem Wasser zum Duschen oder Heizen. Diese Art der Abwärmenutzung ist energetisch effizient, erfordert aber einen hohen Investitions- und Regelaufwand, da Heiz- und Kühlsystem im Verbund, aber auch unabhängig voneinander funktionieren müssen.
Derzeit wird an weiteren Nutzungsmöglichkeiten gearbeitet, indem beispielsweise durch Einkopplung anderer Gießereiabwärmen die Temperatur des austretenden Ofenkühlwassers erhöht wird.
Es ist zu erwarten, dass diese laufenden Entwicklungen zu brauchbaren Ergebnissen führen.
Dem genannten optimalen Energiebedarf von 520 kWh/t stehen im gut geführten praktischen Schmelzbetrieb Werte von 560 bis 650 kWh/t gegenüber. Einflussgrößen für diesen zusätzlichen Energiebedarf bis zum Eingießen der Schmelze in die Form sind die Ofenfahrweise und die Integration der Schmelzanlage in den Gesamtprozess, worauf anschließend eingegangen wird.
Bild 5 zeigt den spezifischen Energiebedarf des MF-Tiegelofens im Vergleich zu dem des Kupolofens. Aufgrund des hohen Anlagenwirkungsgrades ergibt sich ein deutlich niedrigerer Energieverbrauch des Induktionsofens vor Ort, was sich aber bei Betrachtung des Primärenergiebedarfs aufgrund des Kraftwerkswirkungsgrads zu Gunsten des Kupolofens umkehrt.
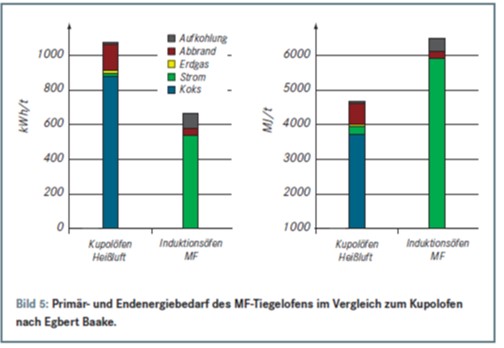
Ähnlich verhält es sich beim Schmelzen von Aluminium im Induktionsrinnenofen im Vergleich zum gasbeheizten Ofen, wie aus Bild 6 hervorgeht. Hier spielt allerdings der unterschiedliche Metallabbrand eine große Rolle, dessen Berücksichtigung bei herkömmlichen gasbeheizten Aluminium-Schmelzöfen ohne induktive Rührer die Energiebilanz auch in Bezug auf die Primärenergie zu Gunsten des induktiven Schmelzens ausfallen lässt.
Induktionsöfen in Eisengießereien unverzichtbar
Für die Herstellung von Eisenguss sind Induktionsöfen als Schmelz-, Speicher- und Gießaggregate unverzichtbar geworden; besonders der Mittelfrequenztiegelofen wurde zum Standardschmelzaggregat. Seine Vorteile gegenüber dem Kupolofen liegen in der Flexibilität für die Herstellung unterschiedlicher Legierungen, der besonderen Eignung für das Erschmelzen von Basiseisen für duktile Werkstoff e, dem hohen Ausbringen der Einsatzstoff e und nicht zuletzt in der geringen CO2-Emission.
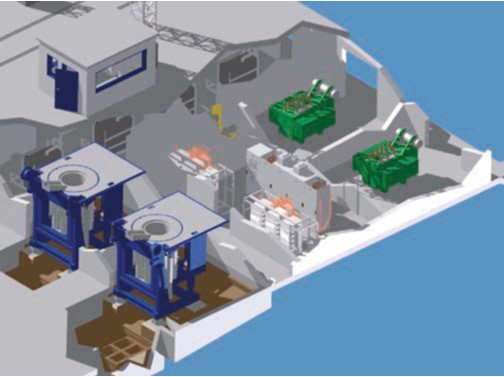
Solche modernen Anlagen wie in Bild 7 im Modell beispielhaft dargestellt, arbeiten mit
- stufenloser Leistungsaufteilung eines Umrichters auf zwei Öfen im Tandembetrieb zur kontinuierlichen Versorgung von Form anlagen ohne zusätzlichen Puffer;
- fahrbaren Beschickungseinrichtungen, meist mit Vibrationsförderung, die in der Gattierhalle mit Magnetkran anforderungsgerecht beladen werden;
- Absaughauben, die an die Chargiereinrichtung andocken (Bild 8) und die Rauchgase bei allen Arbeitsgängen wirkungsvoll absaugen, auch beim Abstich mit Magnesiumbehandlung in der Pfanne (Bild 9);
- rückkippbaren Öfen zum zügigen Abschlacken (Bild 10) als Alternative zum Einsatz von Schlackebaggern;
- hydraulischer Vorrichtung zum Ausdrücken des verschlissenen Feuerfesttiegels;
- Prozessoren zur Steuerung des Gattier-, Chargier- und Schmelzablaufs.
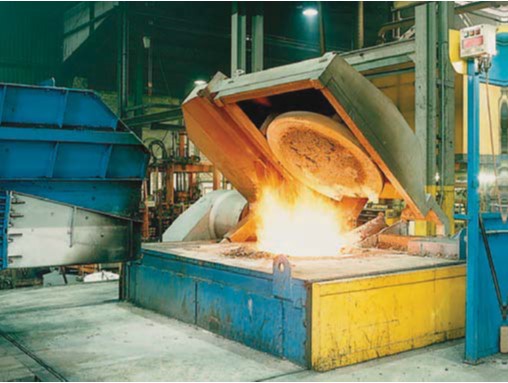
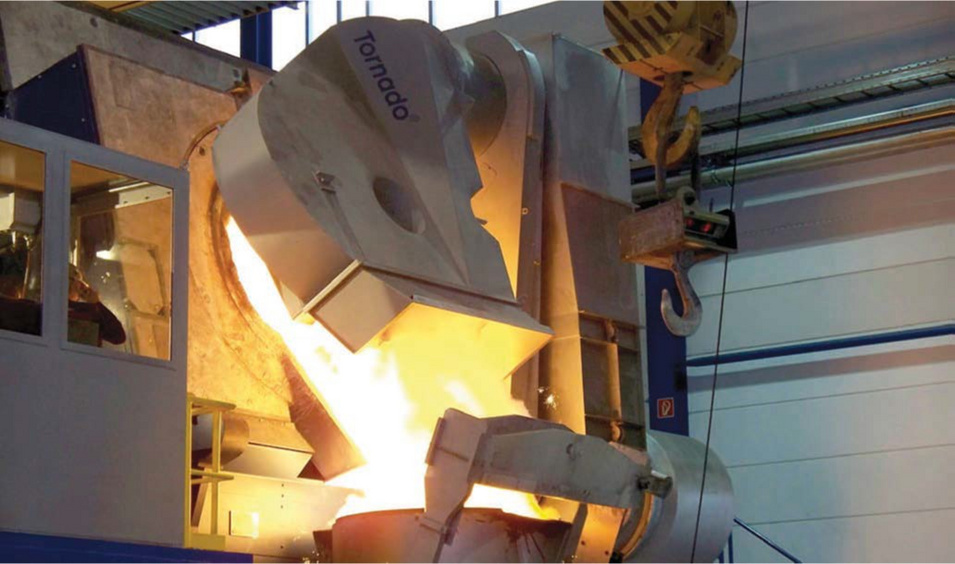
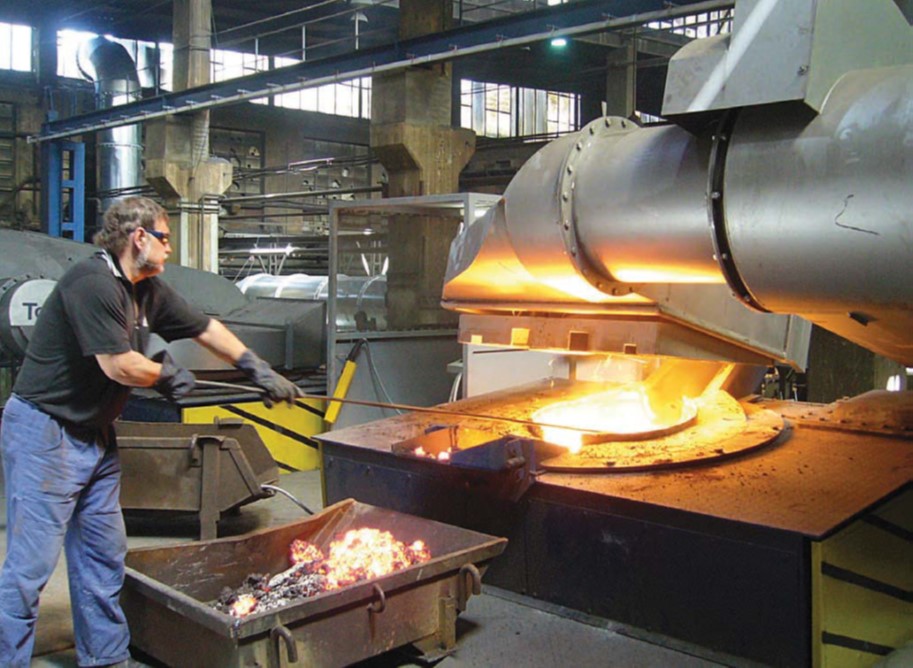
Der gut geführte Schmelzablauf
Auf die Energieeffi zienz haben alle Einzelschritte des gesamten Schmelzprozesses Einfl uss: Es beginnt mit der Chargenvorbereitung, wo der richtige Mix von grobem und kleinerem Stückgut zum mehr oder weniger guten Ankoppeln des elektromagnetischen Feldes an das Schmelzgut führt. Bei ungünstiger Schüttdichte mit wesentlich mehr Luftvolumen als Metall- im Spulenbereich des Tiegels würde die Schmelzzeit entsprechend verlängert und damit die Energieeffizienz verschlechtert. Bei Bedarf ist hier der Einsatz eines Kreislauf- und Schrottbrechers sinnvoll. Ein zweites energierelevantes Kriterium der Einsatzstoffbeschaffenheit ist der Sandanteil des Kreislaufmaterials. Der Energiebedarf für das Schmelzen des anhaftenden Sandes zu Schlacke liegt mit ca. 500 kWh/t in der gleichen Größenordnung wie der für das Schmelzen des Eisens. Für das Herstellen einer 10 t-Gusseisenschmelze aus 50 % Kreislauf mit 10 % Sandanteil werden somit 250 kWh zusätzlich für das Sandschmelzen benötigt. Dazu kommt der Aufwand für das Abschlacken der großen Schlackenmengen. Für ein effizientes induktives Schmelzen ist es daher sinnvoll, das Kreislaufmaterial sandzustrahlen oder zumindest durch Rütteln zu reinigen.
Das leistungs- und damit energieoptimierte Chargieren erfolgt mit Hilfe des Schmelzprozessors: Er ermöglicht die Prozesskontrolle so, dass einerseits keine Unterbrechungen des Schmelzprozesses entstehen, drei bis fünf Minuten Unterbrechung bedeuten 25 bis 50 kWh/t zusätzlichen Energieverbrauch, und dass andererseits das Schmelzgut rechtzeitig nachchargiert wird, so dass es nicht in den flüssigen Sumpf eintauchen kann. Demnach sollte der Schmelzer den Anweisungen des Prozessors folgen und den Ofen ständig mit der vollen verfügbaren Leistung fahren. Dazu steht am Bedienpult ein Terminal mit Bildschirm zur Verfügung, wie in Bild 11 anhand einer Maske für ein Tiegelofentandem dargestellt.
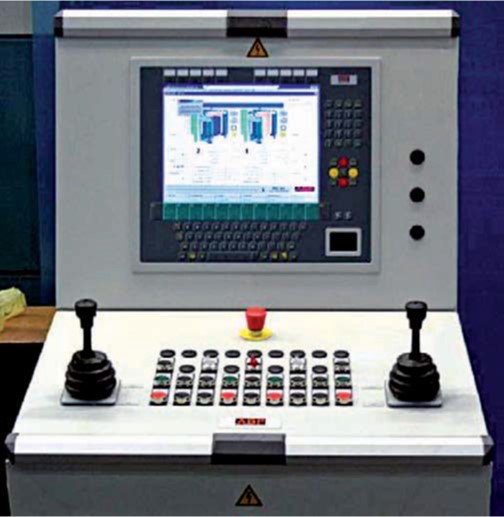
Die für die Herstellung der meisten Gusseisensorten zu empfehlende Chargierreihenfolge lässt sich aus Bild 12 ablesen. Demnach sollten in den leeren heißen Tiegel zunächst leichter Stahlschrott oder Späne in der Menge chargiert werden, dass der Boden bedeckt ist und somit der Tiegel gegen mechanischen Verschleiß geschützt wird. Dann erfolgt die Zugabe von 50 % bis 75 % der Kohlenstoffmenge, die für die Endzusammensetzung der Schmelze berechnet wurde sowie die Zugabe von Stahlschrott, gegebenenfalls gemischt mit Spänen und/oder Roheisen bis zur Oberkante der Aktivspule. Anschließend werden Stahlschrott plus Kreislauf/Gussbruch auf Knopfdruck so nachchargiert, dass die Aktivspule gefüllt, der Ofen aber nicht überfüllt wird. Nach der Eingabe von etwa der Hälfte der Gesamtcharge sollten Silicium in Form von SiC und/oder FeSi sowie die restliche Kohle und eventuell andere Legierungsstoffe eingegeben werden. Nach Erreichen der vollen Ofenfüllung und der theoretischen Soll-Temperatur erfolgen Temperaturmessung und Probenahme sowie das Abschlacken.
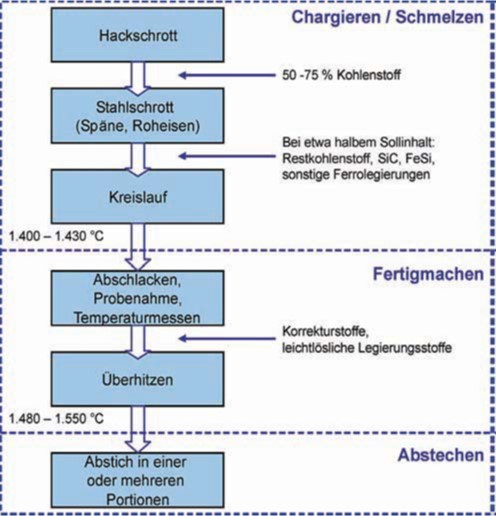
Das beschriebene und in Bild 12 schematisch dargestellte Chargier- und Schmelzverfahren ist weitgehend reproduzierbar, so dass die Zusammensetzung der Schmelze beim Abschluss des Aufschmelzens auf 1400 bis 1430 °C nahe der Sollzusammensetzung liegt, die Legierungsstoffgehalte jedoch geringfügig unter den Sollwerten bleiben. Die Endzusammensetzung wird dann durch Nachsetzen von geringen Mengen Kohlenstoff und Silicium bzw. anderen Legierungselementen vor dem Wiedereinschalten des Ofens zum Hochheizen der Schmelze auf bstichtemperatur exakt erreicht. Somit entfällt zusätzliche Heizzeit für das Legieren, die zu Lasten des Energieverbrauchs und der Produktivität der Schmelzanlage gehen würde.
Am Schluss des Schmelzzyklusses sorgt der Prozessor ohne Überschwingen für die exakte Einstellung der angestrebten Abstichtemperatur zur gewünschten Abstichzeit. Neben der Energieverbrauchsminimierung leistet der Schmelzprozessor somit einen Beitrag für die Sicherheit im Schmelzbetrieb und für die Treff sicherheit der Gusseigenschaften im reproduzierbaren Schmelzablauf, für deren Optimierung das schnelle Schmelzen im Chargenbetrieb mit einmaliger Überhitzung die beste Voraussetzung bietet.
Während des Schmelzens sollte der Ofendeckel wenn immer möglich geschlossen sein. Das gilt besonders am Ende der Schmelzperiode bei mit Schmelze voll gefülltem Tiegel. Dann betragen die zusätzlichen Wärmeverluste beispielsweise eines 12 t-Tiegelofens bei off enem Deckel ca. 600 kW, so dass in einer Zeit von 5 Minuten mit offenem Deckel 50 kWh zusätzliche Verluste entstehen. Die Rauchentwicklung während dieser Schmelzphase ist sehr gering. Dementsprechend wird die Absaugleistung der Haube reduziert, so dass die mit der Absaugung ausgetragene Wärmemenge klein gehalten wird.
Das richtige Anlagenkonzept
Für den Energieaufwand bei der weiteren Verarbeitung der Schmelze haben Auslegung und Konzept der Schmelz- und Gießanlage wichtige Bedeutung. Beispielsweise führt beim kontinuierlichen Flüssigeisenbedarf einer automatisierten Formanlage die Tandemanordnung der Schmelzanlage zu hoher Energieeffizienz bei gleichzeitig niedrigem Leistungsmaximum. Bei einem solchen Tandem speist ein Umrichter mit stufenloser elektronischer Leistungsaufteilung zwei Tiegelöfen so, dass der eine Ofen im Schmelz-, der andere im Warmhalte-/Gießbetrieb arbeitet (Bild 13). Damit ist die kontinuierliche Schmelzeversorgung ohne zusätzlichen Puff er sichergestellt. Gegenüber der herkömmlichen Lösung mit einem Speicherofen spart man das Umfüllen der Schmelze in diesen Puffer und damit neben dem Handling die dafür benötigte Energie; das sind bei einem Temperaturabfall von 30 bis 50 K pro Umfüllvorgang 15 bis 20 kWh/t.
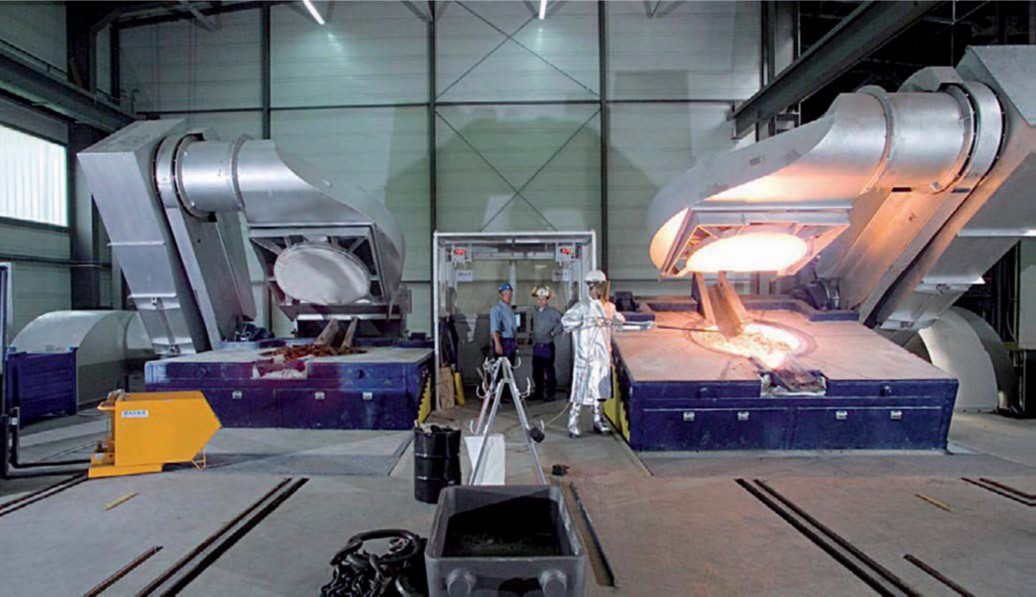
Ein weiteres Potential zur Energieeinsparung auf dem Weg zur kontinuierlich zu versorgenden Formanlage bietet der Gießofen. In Bild 14 sind zwei alternative Anlagenkonzepte dargestellt: a) Das Versorgen einer unbeheizten Gießeinrichtung mit relativ kleinen Schmelzeportionen in Taktzeiten von 10 bis 15 Minuten; b) die Beschickung eines Gießofens mit vergleichsweise großen Portionen in großem Zeitabstand. Im Fall der unbeheizten Gießeinrichtung muss die Schmelze im Schmelzofen um 50 bis 70 K überhitzt werden, um die Wärmeverluste während des Transports und des Gießvorgangs zu kompensieren. Der entsprechende Energiebedarf beträgt 50 bis 70 kWh/t. Beim Einsatz des Gießofens werden nur ca. 20 K für die Überhitzung im Schmelzofen benötigt. Die Transportverluste sind in größerer Pfanne geringer, und die Wärmeverluste während des Gießens werden im Gießofen mit besserem Wirkungsgrad gedeckt. Darüber hinaus führt das beim Gießofenkonzept mögliche schnellere Entleeren des Schmelzofens zur optimalen Leistungsnutzung des Tandems mit nahezu 100 %.
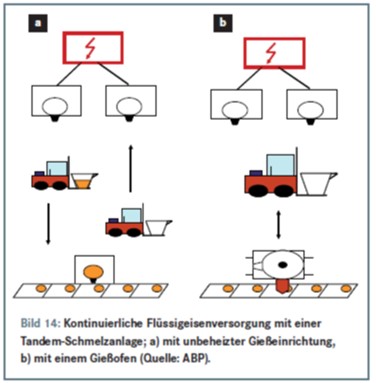
Induktionsrinnen- und -tiegelofen für das Schmelzen von NE-Metallen
Wegen des um 15 bis 20 Prozentpunkte höheren elektrischen Wirkungsgrades und des daraus folgenden geringeren Energieverbrauches wird für das induktive Schmelzen von NE-Metallen der Rinnenofen bevorzugt. Allerdings bietet der Tiegelofen die Vorteile der stärkeren Badbewegung und des problemlosen Anfahrens mit festen Einsatzstoffen. Dementsprechend wird er trotz des höheren Energieverbrauches immer dann eingesetzt, wenn unter Nutzung der Rührwirkung kleinstückige Teile wie Blechabfälle oder Späne mit gutem Ausbringen zu schmelzen sind oder wo häufiger Legierungswechsel der herzustellenden Schmelze gefordert ist.
Letzteres ist häufig bei der Aluminium-Formgussherstellung der Fall, so dass in Al-Gießereien meist der Induktionstiegelofen das geeignete Schmelzaggregat darstellt. In Standardausführung lassen sich die MF-Tiegelöfen analog zur Eisengießerei betreiben, beispielsweise in Tandemanordnung.
In Aluminium-Halbzeugwerken steht der Induktionsrinnenofen in starker technologischer Konkurrenz zum gasbeheizten Schmelzofen. Den Ausschlag für die höhere Wirtschaftlichkeit des Elektro- oder des Brennstoffverfahrens geben im Einzelfall letztendlich die lokalen Energiekosten und die Effizienz der Induktoren, die in Doppelkanalform mit zwei Spulen ausgeführt sind. Die Schmelzleistung beträgt bei Anschlussleistungen bis 1500 kW bis über 3 t/h pro Induktor mit Feuerfesthaltbarkeiten von durchschnittlich neun Monaten. Der Ofenkessel mit Fassungsvermögen bis 55 t bei 45 t Nutzfassung ist meist in Wannenform ausgeführt und am Ofenboden mit bis zu vier Induktoren bestückt. Bild 15 zeigt schematisch einen solchen Ofen mit vier Hochleistungsinduktoren.
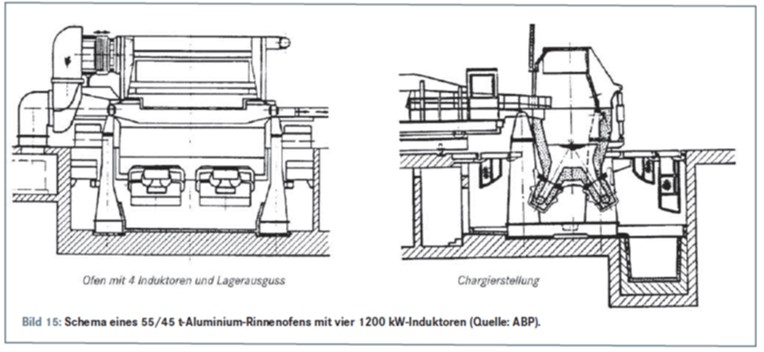
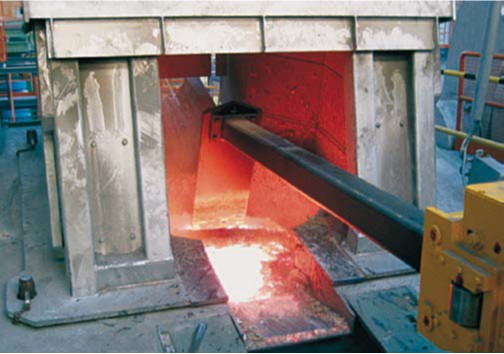
Auch in Halbzeugwerken für Kupferwerkstoffe werden Rinnenöfen dieser in Bild 15 dargestellten Bauart als Schmelzaggregat betrieben. Dazu wurden Mitte der 1990er Jahre effiziente Induktoren mit Leistungen bis 2400 kW entwickelt. Durch Einsatz von mit Kupferblech ausgekleideten Induktorgehäusen erreicht man elektrische Wirkungsgrade von 91 % für Kupfer und 86 % für Messing. Entsprechende Induktionsschmelzanlagen in Halbzeugwerken bestehen aus einem oder mehreren Rinnenöfen mit einem oder mehreren dieser Induktoren für das Schmelzen von grobstückigem Schmelzgut sowie einem oder mehreren Tiegelöfen für das Schmelzen von Spänen. Die auf diese Weise mit hoher Wirtschaftlichkeit erzeugte Schmelze wird über Rinnen in einen Speicher- und Gießofen überführt, der in mehrstündigen Taktzeiten eine Stranggussanlage versorgt
Analog zu der oben beschriebenen Schmelzführung in der Eisengießerei erfolgt auch das Erschmelzen von Kupferwerkstoffen mit hoher Energieeffizienz. Beispielhaft für die fortschrittliche Bedienung solcher Hochleistungsanlagen zeigt Bild 16 das mechanisierte Abkrätzen an einem 30 t-MF-Tiegelofen zum Schmelzen von Messingspänen.
Induktives Schmelzen hat Zukunft
Das induktive Schmelzverfahren hat sich auf breiter Front in der Gießerei-Industrie vor allem für die Herstellung von Eisenwerkstoffen, aber auch in Metallwerken für NE-Anwendungen durchgesetzt. Maßgebend dafür sind zunächst die anwendungstechnischen Vorteile: Die direkte Energieübertragung ohne Übertemperatur und die aus den elektromagnetischen Kräften resultierende Badbewegung ermöglichen einen reproduzierbaren und automatisierbaren Schmelzprozess mit metallurgischen Vorteilen, hoher Umwelt- und Arbeitsplatzverträglichkeit sowie geringem Entsorgungsaufwand.
Mit Hilfe fortschrittlicher Anlagen- und Prozesstechnik arbeitet die Induktionstechnologie mit hoher Energieeffizienz. Die Wirkungsgrade von 97 bis 98 % bei der Umrichter-Stromversorgung und bis zu 85 % bei der Induktionsspule werden durch den prozessorgeführten Schmelzablauf optimal genutzt. Der weitere Energiebedarf in der Verarbeitung der Schmelze bis zur Formanlage wird durch die Tandemanordnung der Schmelzöfen minimiert, indem zwei Tiegelöfen mit der Stromversorgung aus einem Umrichter mit stufenloser Leistungsaufteilung die kontinuierliche Flüssigeisenversorgung ohne zusätzlichen Puffer sicherstellen. Der Gesamtenergiebedarf solcher fortschrittlichen Induktionsanlagen liegt mit 560 bis 600 kWh/t weit unter dem vergleichbarer brennstoffbeheizter Schmelzöfen. Laufende Entwicklungsarbeiten zur Nutzung der im Ofenkühlwasser gebundenen Abwärme werden die Energiebilanz des Indusktionsofens weiter verbessern.
Bei der aktuellen Diskussion über die CO2-Reduzierung wachsen die Vorteile des induktiven Schmelzens mit dem wachsenden Anteil der regenerativen Stromerzeugung. Bereits jetzt beträgt die spezifische CO2-Emission des MF-Schmelzofens einschließlich dem Anteil aus der Stromerzeugung beim Gusseisenschmelzen mit ca. 300 kg/t etwa 60 % der Emission des Kupolofens. Nach derzeitiger Prognose der Entwicklung der regenerativen Stromerzeugung wird sich die Emission des Induktionsofens in den nächsten 10 Jahren auf 200 kg/t verbessern.
Bei allen Fortschritten in der Energieeffizienz bleibt die besondere Bedeutung des Strompreises bestehen. Die Frage seiner Entwicklung im Vergleich zum Preis der fossilen Energieträger ist derzeit schwierig zu beantworten. Um so wichtiger ist die Nutzung eines intelligenten Energiemanagements in jeder Gießerei, wo sich in Abhängigkeit von lokalen Bedingungen vertragliche Vergünstigungen mit dem Stromlieferanten aushandeln lassen. Die sich abzeichnenden Änderungen bei den Netzlastverhältnissen sollten hier neue Möglichkeiten bieten, da die induktive Schmelzanlage häufig mit relativ hoher Flexibilität im Strombezug bei trotzdem voller Produktivität betrieben werden kann.
Dr. Erwin Dötsch, ABP Induction Systems GmbH, Dortmund