Anlagenverfügbarkeit und Energieeffizienz – ein Tandem
Energieverbrauch reduzieren und Kosten senken mit der richtigen Strategie
Von Patrick Reichen, Uzwil/Schweiz
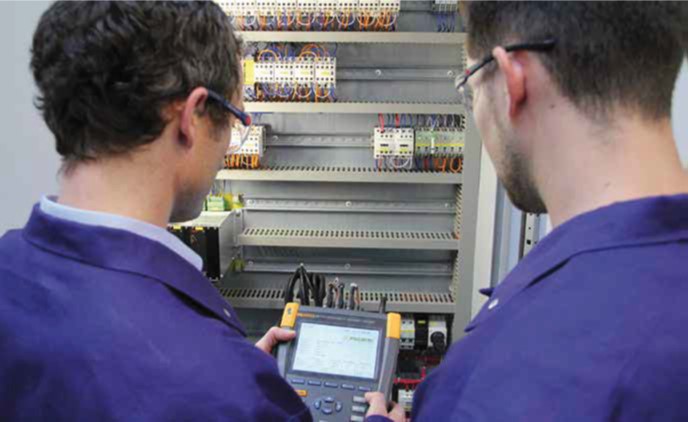
Bühler-Mitarbeiter während der Energiemessung an einer Druckgießanlage.
Erschienen in GIESSEREI 12/2015
Steigende Energie- und Rohstoffpreise verschärfen den ohnehin großen Kostendruck auf europäische Gießereien. Deshalb sind Lösungen gefragt, wie der Energieeinsatz vermindert und die Ressourcennutzung optimiert werden können. Die Tatsache, dass auch die Verfügbarkeit der Druckgießmaschine einen erheblichen Einfluss auf die Energiekosten je produziertem Bauteil hat, wird dabei noch häufig übersehen. Dabei ist die Verbesserung der Gesamtanlageneffektivität (GAE) und damit der Verfügbarkeit einer Druckgießzelle häufig der größere Stellhebel zur Kosteneinsparung im Prozess.
Der zunehmende Kostendruck und der globale Wettbewerb beschäftigen die Verantwortlichen in den Unternehmen und stellen die komplette Gießereibranche vor große Herausforderungen. Mit innovativen Bauteilkonstruktionen und modernen Druckgießverfahren lassen sich der Materialeinsatz reduzieren und damit Kosten sparen. Anstrengungen zur Verringerung des Energieverbrauchs im Produktionsprozess stehen jedoch zusehends im Fokus (Bild 1). Dies geschieht vor dem Hintergrund allgemein steigender Energiepreise, aber auch aufgrund politischer Regularien, nach denen zukünftig in vielen Ländern stromintensive Unternehmen im Rahmen der Energiewende erhöhte Umlagen tragen müssen.
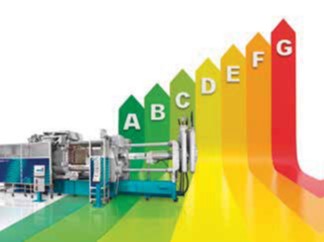
Die Suche nach dem idealen Modell zur Energie- und damit Kostenreduktion ist aufwendig, denn sehr viele Parameter beeinflussen die Energieeffizienz von Systemen – und mitunter auch einander. Insbesondere stellt sich die Frage nach der Vergleichbarkeit der möglichen zu treffenden Maßnahmen oder der im Prozess beteiligten Druckgießmaschine in Bezug auf eine gewünschte Energieeinsparung.
Leistungsaufnahme im Normzyklus
In der Consumer-Branche seit langem verbreitet sind die Energieverbrauchskennzeichnungen von Geräten, die sogenannten „Energielabel“. In der Zwischenzeit konnten sich auch in der Gießereibranche Kennzahlen zur Energieeffizienz etablieren: Unter der Führung des Verbandes Deutscher Maschinen- und Anlagenbau (VDMA) haben sich Bühler, Uzwil, Schweiz, und weitere Vertreter aus der Industrie zusammengefunden und im VDMA-Normenblatt 24499 einen standardisierten Prozess beschrieben, nach dem sich der Energieverbrauch von Druckgießmaschinen vergleichen lässt. Gemessen und angegeben wird dieser auf Basis eines prozessnahen Zyklus, welcher definierte Wartezeiten für die Funktionen der Peripherie bzw. der Zusatzaggregate der Gießzelle abbildet. Eine Vergleichbarkeit unterschiedlichster Maschinentypen von verschiedenen Herstellern ist auch dadurch gewährleistet, dass die „Wartezeiten“ als Funktion der Zuhaltekraft der Druckgießmaschine und der Prozessverlauf mit klar umrissenen Verfahrbedingungen beschrieben sind (Bild 2).
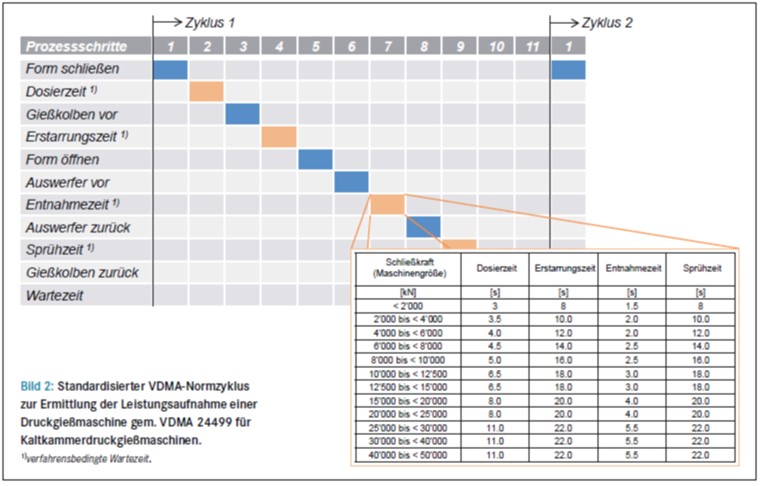
Der VDMA-Normzyklus folgt exakten Vorgaben und bietet damit eine zuverlässige Grundlage, anhand derer sich leicht die Leistungsaufnahme und damit die Energieeffizienz verschiedener Druckgießmaschinen bewerten lässt (Bild 3). Das Resultat einer VDMA-Messung umfasst nebst den technischen Kennwerten einer Maschine den ausgewiesenen Energieverbrauch einer Druckgießmaschine pro Normzyklus. Dieses „Energie-Zertifikat“ gibt damit der Gießerei noch weitere Sicherheit im Rahmen eines Investitionsentscheids.
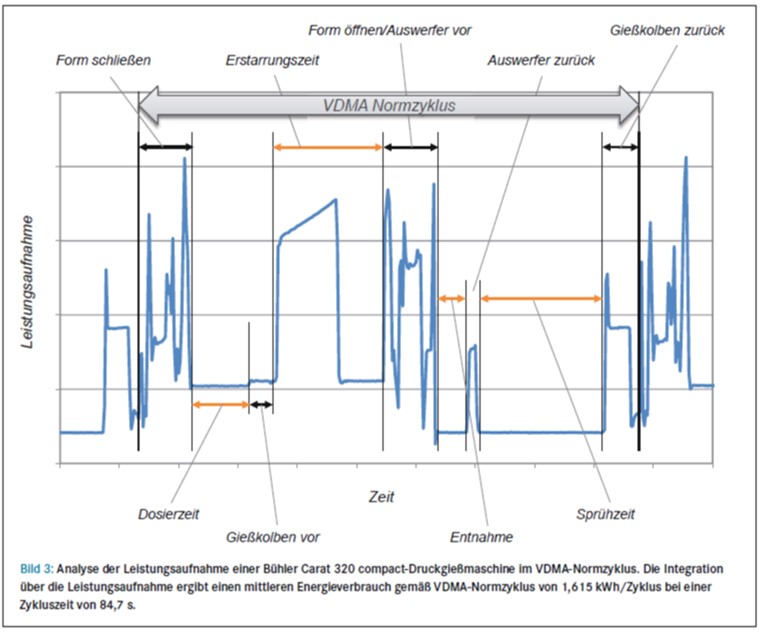
Energieeinsparung im realen Produktionsumfeld
Neben diesen Vergleichskennzahlen zur eingesetzten Maschine stellt sich für den Druckgießer natürlich immer die Frage nach dem Gesamtressourcenverbrauch und damit auch nach den Kosten pro produziertem Bauteil in der realen Fertigung. Dies ist der eigentliche Benchmark im Wettbewerb der Gießereien. In der Gesamtoptimierung des Energieverbrauchs zählt dabei deshalb nicht nur die Reduktion der benötigten elektrischen Energie der Maschine, sondern auch jene zur Aufschmelzung des Metalls oder zur Bereitstellung der weiteren Ressourcen wie der Druckluft oder des Kühlwassers. Verschiedene Untersuchungen zeigen auch, dass insbesondere der Sprühprozess aufgrund des hohen Verbrauchs an Druckluftenergie einen überproportional hohen Anteil am Gesamtenergieverbrauch einnehmen kann (Bild 4 und Tabelle 1). Dies wird häufig bei rein elektrischen Energiemessungen in der Gießzelle unterschätzt.
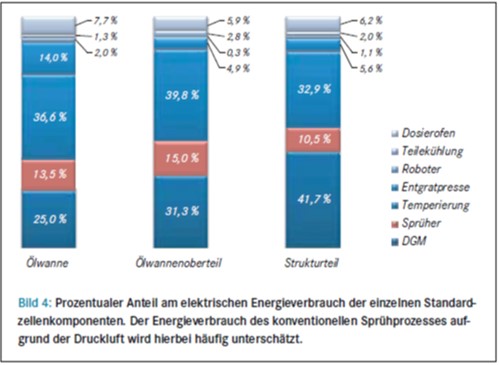
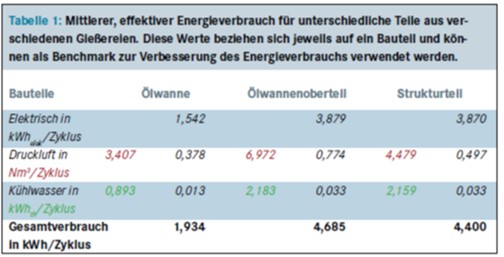
Energiemessprotokoll zeigt Potenziale auf
Konkrete Aussagen kann dazu ein Energiemessprotokoll liefern, welches die im realen Produktionsumfeld erfassten Daten und deren Bezug zu einem spezifisch produzierten Bauteil darstellt. Unternehmen wie Bühler, welche über das notwendige Know-how und die entsprechende Messtechnik verfügen, bieten dies als Dienstleistung für Gießereien an. Während die benötigte elektrische Energie relativ einfach über ein Energiemessgerät zu erfassen ist, stellen die Messung von Druckluftverbrauch und Kühlwasseraufbereitung erhebliche Anforderungen an den Messaufbau. Zur exakten Bestimmung des Druckluftverbrauches eignen sich insbesondere kalorimetrische Messgeräte, die hohe Gasgeschwindigkeiten über einen großen Messbereich bei gleichzeitig hoher Prozessdynamik abbilden können. Dabei ist die korrekte Positionierung der Messgeräte unter Berücksichtigung der benötigten Beruhigungsstrecken entscheidend für die Qualität der Messresultate. Eine Messung der thermischen Energie ohne Produktionsunterbrechung bedingt außerdem in vielen Fällen eine zusätzliche mobile Messstrecke mit kalibrierten Temperatursensoren und exakter Durchflussmessung.
Zur Beschreibung des Gesamtenergieverbrauchs lassen sich die erhaltenen Einzelwerte in einen äquivalenten, elektrischen Energieverbrauch umrechnen. Dazu werden gießereispezifisch die Umrechnungsfaktoren für Druckluft und Kühlwasser aus den örtlichen Gegebenheiten errechnet. Diese Faktoren beschreiben die benötigte elektrische Energie zur Bereitstellung von einem Normkubikmeter Druckluft respektive einer Kilowattstunde thermischer Energie. Sie sind zudem stark von den installierten Kompressoren wie auch von der Art der Kühlwasseraufbereitung abhängig. Die Resultate einer spezifischen Druckgießzelle können in einem Energiemessprotokoll (Bild 5) im Detail aufgeschlüsselt werden und ergeben in Summe den benötigten Energieverbrauch eines bestimmten Bauteils.
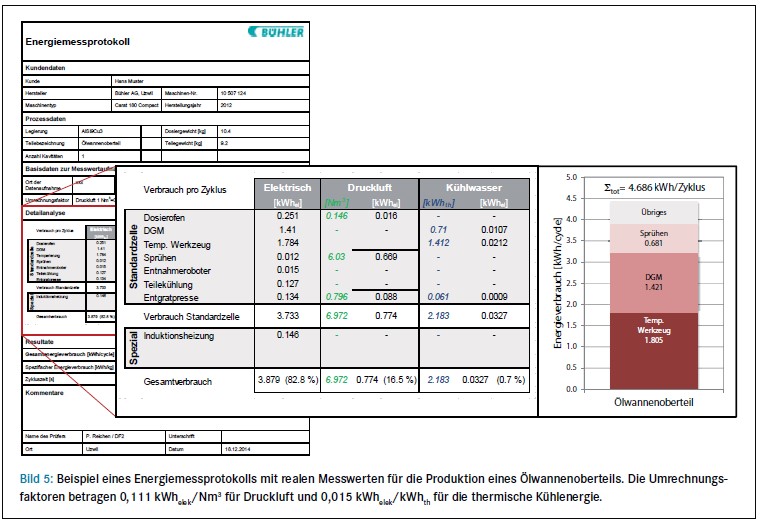
Anhand dieser Ergebnisse ist es dann möglich, gezielte Optimierungen der Maschineneinstellung, der Sprühtechnik oder des Zellenkonzeptes einfließen zu lassen – und so den Energieeinsatz und damit die Kosten je produziertem Bauteil zu reduzieren.
Verfügbarkeit beeinflusst Energieeffizienz
Neben den obigen Überlegungen lohnt sich für den Gießer der Blick auf die Gesamtanlageneffektivität (GAE) seiner Gießzelle, denn diese schlägt sich unmittelbar auf die Wirtschaftlichkeit der Anlage nieder. Sie wird als Produkt aus der Verfügbarkeit der Druckgießzelle, dem Ausbringungsgrad und der Qualität der Gussteile berechnet. Verluste durch den Stillstand der Maschine, durch längere Zykluszeiten sowie der Ausschuss werden in dieser Rechnung ebenfalls berücksichtigt.
In diesem Zusammenhang von besonderem Interesse sind die Stillstandzeiten der verwendeten Zellenkomponenten. Um den Unterschied zwischen möglicher und tatsächlicher Produktionszeit aufzuzeigen, bedarf es ihrer fundierten Auswertung. Zu den Stillstandzeiten zählen neben den Zeiten für ungeplante Wartungs-, Instandhaltungs- oder Reparaturarbeiten nach technischen Ausfällen auch organisatorische Leerläufe, beispielsweise durch Bedienfehler sowie fehlendes Material oder Personal. Mit spezialisierten Softwarepaketen, wie z. B. dem Bühler Event Analyzer, können entsprechende Statusreports der Druckgießmaschine einem Expertenteam zur Verfügung gestellt und ausgewertet werden.
Stillstandzeiten erhöhen den Energieverbrauch je Bauteil
Auch wenn die Maschine vorübergehend steht, muss das Schmelzgut weiterhin warm und alle benötigten Aggregate in einem Standby-Zustand gehalten werden. Bis zu 60 % der Leistungsaufnahme während der regulären Produktion fallen heutzutage an, obwohl die Maschine nicht produziert. Die Folge davon ist, dass alle gefertigten Gutteile kostenmäßig diese „Stand-by-Verluste“ mittragen müssen. Oder mit anderen Worten: Eine höhere Gesamtanlageneffektivität reduziert den Energieverbrauch pro Bauteil. Dabei wird deutlich, dass sich die Verbesserung der GAE ungleich stärker auf die Stückkosten auswirkt als die ausschließliche Optimierung der Energiekosten der produzierenden Druckgießzelle selbst. Ein vereinfachtes Berechnungsmodell zeigt den prozentualen Einfluss einer verbesserten GAE auf den Energieverbrauch respektive der Herstellkosten (Bild 6a). Zum Vergleich dient die identische Berechnung bei einer Verbesserung der Energieeffizienz.
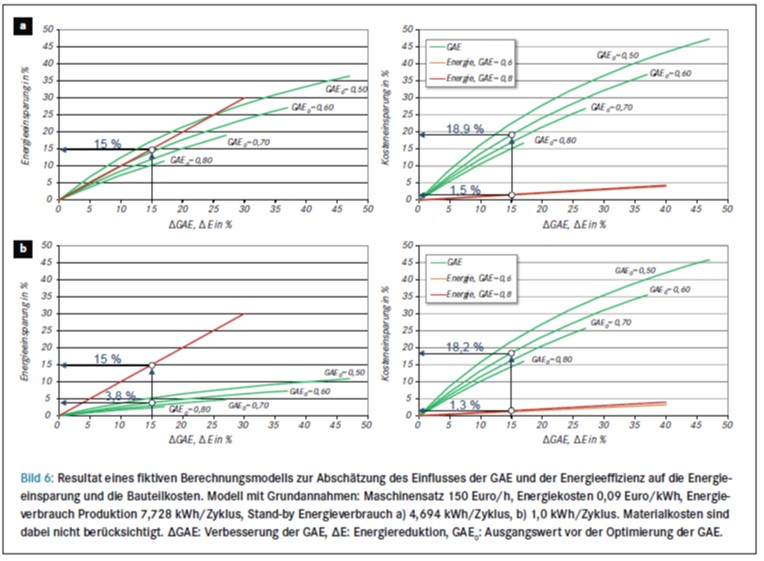
Modellierung liefert Entscheidungsgrundlagen
Ausgehend von einem Maschinenstundensatz, welcher die zu erwartenden Fix kosten und die tatsächlichen Energiekosten berücksichtigt, zeigt das Modell, wie sich die Gesamtkosten eines zu produzierenden Bauteils mit zunehmender Anlagenverfügbarkeit reduzieren: Die Verbesserung der GAE um rund 15 % hat im vorliegenden Beispiel einen um das Zehnfache höheren Einfluss auf die Herstellkosten als die bloße Reduktion der Energiekosten um 15 %. Durch Variation der Modellparameter kann der Einfluss einer deutlichen Reduktion des Stand-by-Energieverbrauchs simuliert werden (Bild 6b). Der Einfluss einer höheren Anlagenverfügbarkeit auf den reduzierten Energieverbrauch nimmt dadurch ab. Das Verhältnis bei den Kosteneinsparungen bleibt jedoch erhalten.
Mit einer solchen Modellierung lässt sich auch die Frage beantworten, ob mit dem Ziel der Kostenreduktion in neue, weniger energieverbrauchende Anlagenteile investiert werden soll oder alternativ in Maßnahmen zur Erhöhung der Verfügbarkeit einer vorhandenen Installation.
Verfügbarkeit und Energieeffizienz
Der stetig wachsende Kostendruck verlangt kontinuierlich nach Innovation, auch beim Druckgießen. Der Einsatz energieeffizienter Produktionsmaschinen leistet dabei einen wichtigen Beitrag zur Kostensenkung. Mit dem VDMA-Normzyklus für Druckgießmaschinen werden diese vergleichbar. Die Verbesserung der Gesamtanlageneffektivität hat darüber hinaus einen noch entscheidenderen Einfluss auf die Gesamtkostenbilanz je gefertigtem Gutteil. Mit einem richtig abgestimmten, präventiv wirkenden Servicepaket lässt sich bei niedrigeren Kosten die Produktivität entscheidend steigern. Die Experten von Bühler bieten sich bei diesen Fragen als kompetente Partner an.
Patrick Reichen, Project Manager R&D, Bühler AG, Uzwil, Schweiz